Себестоимость заготовки (детали).
Факторы, влияющие на себестоимость производства в машиностроении, условно делят на три группы :
· конструктивные факторы, т.е. конструктивное решение самой детали, выбор марки материала и технических условий, обеспечивающих приемлемость ее для изготовления обработкой давлением, литьем, сваркой и т.д.;
· технологические факторы, характеризующие способ формообразования заготовки, выбор самой заготовки, оборудования и технологического процесса получения детали;
· производственные факторы, т.е. характер и культура производства, технологическая оснащенность, технологический и организационный уровни производства.
Все три группы факторов взаимосвязаны и оказывают существенное влияние на себестоимость изделий, так как способ получения заготовки в значительной мере предопределяется конструкцией детали, ее материалом, а также характером производства, его технологическим и организационным уровнем. И то, насколько полно в заготовке учтено влияние факторов первой и третьей групп, позволяет судить о "технологичности" заготовки. Под технологичностью заготовки принято понимать, насколько данная заготовка соответствует требованиям производства и обеспечивает долговечность и надежность работы детали при эксплуатации. Выпуск технологичной заготовки в заданных масштабах производства обеспечивает минимальные производственные затраты, себестоимость, трудоемкость и материалоемкость.
|
|
Как правило, заготовки деталей могут быть получены одним или несколькими способами литья или обработки давлением. Однако при литье структура металла, а следовательно, и механические свойства детали ниже, чем при обработке металлов давлением. Кроме того, в отливках, особенно получаемых литьем под давлением или в кокиль, большая вероятность возникновения литейных напряжений и наличия пористости. Наоборот, при штамповке, создавая направленную структуру (макроволнистость), можно в значительной степени увеличить эксплуатационные свойства детали. В то же время заданный параметр шероховатости поверхности и точность размеров могут быть обеспечены и в том, и в другом случаях. Из сказанного следует, что при выборе способов получения заготовки для данных деталей в первую очередь необходимо учитывать основные факторы (требования к качеству и себестоимость), ориентироваться на то, что является определяющим в данном конкретном случае.
Оптимальное решение при выборе заготовки может быть найдено только при условии комплексного анализа влияния на себестоимость всех факторов, при обязательном условии положительного влияния способа получения заготовки на качество изделия.
|
|
Если представить себестоимость изготовления детали формулой
С= М+3 + О,
где М - стоимость материалов на деталь;
З - расходы на заработную плату при изготовлении детали;
О - расходы, учитывающие стоимость оснастки,
используемой при изготовлении детали;
и учесть, что такие процессы формообразования, как литье, ковка, штамповка, весьма трудоемки, то даже в этом случае значительная доля затрат падает на материал (в некоторых случаях затраты на материал составляют 60% себестоимости детали). Поэтому пути снижения себестоимости деталей, а следовательно, и изделий наиболее целесообразно искать в снижении расхода материала, т.е. в выборе наиболее экономичной, рациональной заготовки.
В настоящее время ГОСТом для оценки технологичности детали в группе дополнительных показателей предусмотрен коэффициент использования металла (Ки.м), который оценивают как отношение массы готовой детали к массе исходного металла, т.е.
Ки.м = Мд/Мз .
Коэффициент использования металла является наиболее часто употребляемым для оценки рентабельности выбранной заготовки, так как зависит от конструкции детали и от конструкции и массы заготовки.
Следует отметить, что доля применения точных заготовок, получаемых прогрессивными способами пластической деформации составляет в отечественном машиностроении всего 15%, тогда как в США - 50…60%; доля производства отливок из высокопрочного чугуна у нас составляет 2…5%, в США – 20…25%, в Японии – 26…27%; в то же время удельный вес поковок в объеме кузнечных заготовок у нас в стране составляет до 30%, а в США – 5…7%.
Дата добавления: 2018-05-12; просмотров: 402; Мы поможем в написании вашей работы! |
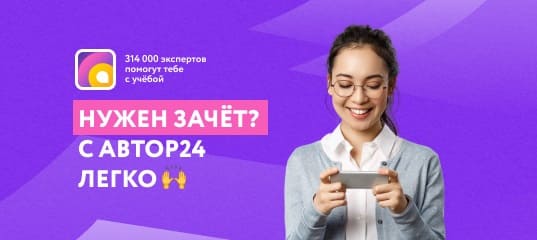
Мы поможем в написании ваших работ!