Технологический процесс, составные части ТП.
Технология машиностроения. Изделия машиностроения.
Технология машиностроения – это наука об изготовлении машин требуемого качества, в нужном количестве и в заданные сроки при наименьших затратах живого и овеществленного труда. В настоящее время эта отрасль знаний настолько развита, что многие виды технологических процессов изучаются в специальных курсах: литейного производства, теории обработки металлов давлением, теории резания металлов, сварки и т.д. Все эти науки и существующие на их основе производства тесно связаны с современной технологией машиностроения, находят приложение на всех этапах от проектирования до производства и выпуска продукции машиностроения.
Современные направления развития технологии машиностроения основаны на результатах исследований в области математики, электронной и вычислительной техники, кибернетики, робототехники, металлофизики, искусственного интеллекта и других современных разделов фундаментальных и прикладных наук.
Результатом деятельности любого предприятия является выпуск продукции установленного качества. В соответствии с ГОСТ любая продукция машиностроительного производства называется изделием. Изделие – это любой предмет или набор предметов, подлежащих изготовлению на предприятии. Изделием являются различные машины, механизмы, агрегаты, устройства и детали.
Изделия, изготовленные для реализации (поставки, продажи), называют изделием основного производства.
Изделия, изготовляемые для нужд самого предприятия, например, оснастка – приспособления, специальные виды инструмента и др. называют изделиями вспомогательного производства. В отдельных случаях изделия основного производства могут использоваться для нужд предприятия – изготовителя, а изделия вспомогательного производства – реализовываться другим машиностроительным предприятиям.
В зависимости от сложности и назначения изделия подразделяются на специфицированные (имеющие спецификацию – сборочные единицы, комплексы, комплекты) и детали.
|
|
В соответствии с ГОСТ установлено четыре вида изделий:
· детали – изделия, изготовленные из однородного по наименованию и марке материала без применения сборочных операций; (например, валик из однородного металла, литая заготовка, ножовочное полотно и др.);
· сборочные единицы – изделия, составные части которых подлежат соединению между собой на предприятии-изготовителе путем сборочных операций (сочленение, свинчивание, сварка, пайка, клейка, склеивание и т.п.). Например, автомобиль, станок, электродвигатель, сварной корпус, авторучка и т.д.;
· комплекты – два и более специфицированные изделия, не соединенных на предприятии-изготовителе сборочными операциями, но предназначенных для выполнения взаимосвязанных эксплуатационных функций. Например, гибкий производственный модуль, цех-автомат, бурильная установка;
|
|
· комплекты – два и более изделия, не соединенных на предприятии-изготовителе сборочными операциями и представляющих набор изделий, которые имеют общее эксплутационное назначение вспомогательного характера. Например, комплект запасных частей, комплект инструмента и принадлежностей и т.п.
Изделие – деталь, агрегат, машина является технической системой, которая создается для выполнения определенных функций, т.е. имеет определенное служебное назначение.
Основные (или исполнительные) элементы машины – это те элементы, функции которых совпадают с функцией машины.
Технологические требования на изделия. Классификация ТТ, признаки классификации деталей.
Функции изделия (машины, детали) отражены в технических требованиях (ТТ) – системе качественных показателей с установленными на них количественными значениями. Для любого показателя качества следует различать заданное действительное и измеренное значения. Точность изготовления изделия или его элементов характеризуется степенью приближения действительных значений показателей качества к заданным. Точность измерения показателя качества определяется степенью приближения измеренного значения к действительному.
|
|
Допуском называют всякое ограничение любого показателя качества.
Все технические требования можно разбить на следующие группы: функциональные требования –ТТ1; требования к взаимодействию машины и человека – ТТ2; требования к взаимодействию машины и окружающей технической среды – ТТ3; требования к взаимодействию машины и окружающей физической среды –ТТ4. Функциональные требования ТТ1 представляют собой чаще всего самую важную и многочисленную группу, всегда присутствующую в полном списке технических требований.
Довольно сложной задачей является конструкторско-технологическая классификация деталей машин. Решение этой задачи было начато еще в 1937 г. А.П. Соколовским. Однако разработка детального общемашиностроительного классификатора пока считается невозможной (хотя и существует в соответствии с ЕСКД в машиностроении и приборостроении классификатор, в котором установлены шесть классов от 71 до 76). Задача становится реальной, если классификацию проводить в пределах отрасли машиностроения, а еще проще – в пределах предприятия.
|
|
Как правило, классификацию выполняют по четырем признакам:
1) функционально-геометрическому; 2) размерному; 3) точностному;
4) по применяемому материалу.
Следует отметить, что в каждой отрасли машиностроения применяются группы деталей оригинальной формы и функционального назначения, которые редко или совсем не встречаются в машинах других отраслей (например, диски и лопатки турбин или компрессоров, станины и шпиндели металлорежущих станков и т.п.). Но, с другой стороны, очень многие детали являются универсальными или типовыми, т.е. применяются в самых разных машинах.
По второму признаку (габаритным размерам) все детали делят на четыре группы: мелкие, средние, крупные и особо крупные. В некоторых случаях деление делают по массе. Границы между группами, как правило, условны и нечетки.
По третьему признаку (наиболее высокому квалитету точности, установленному на какой-либо размер детали) все детали делят на четыре группы: высокоточные (максимальная точность размеров соответствует 4JT, 5JT – четвертому и пятому квалитетам); точные (6JT, 7JT); средней точности (8JT…..10JT); неточные (11….17-й квалитеты).
По четвертому признаку (применяемому материалу) детали условно делят на группы: 1) из сталей углеродистых конструкционных; 2) из сталей легированных; 3) из чугунов; 4) из алюминиевых сплавов; 5) из медных сплавов; 6) из пластмасс; 7) из прочих материалов. Могут выделятся подгруппы. Например, механические свойства и обрабатываемость резанием стали существенно изменяется в результате термической обработки. Поэтому в первой и второй группах выделяют следующие подгруппы деталей: 0) из стали в состоянии поставки; 1) из улучшаемой стали; 2) из цементируемой стали; 4) из закаливаемой стали.
3. Производственный процесс предприятия.
Готовые изделия получают из материалов и полуфабрикатов в результате осуществления отдельных процессов, совокупность которых образует производственный процесс. По ГОСТ производственный процесс определяется как совокупность всех действий людей и орудий труда, необходимых на данном предприятии для изготовления или ремонта продукции.
Состав цехов и служб предприятия с указанием связей между ними определяют производственную структуру. Элементарной единицей структуры предприятия является рабочее место. На рабочем месте размещены исполнители работы, обслуживаемое технологическое оборудование, часть конвейера, на ограниченное время оснастка и предметы труда.
Производственный процесс необходимо рассматривать как сложную систему взаимодействий отдельных структур предприятия .
Производственный участок представлят собой группу рабочих мест, организованных по предметному, технологическому или предметно-технологическому принципу.
Совокупность производственных участков образует цех (ГОСТ 14.004-83).
Приведенная упрощенная (без энергетических потоков) функциональная схема машиностроительного предприятия содержит подсистемы: управления – УПР; складирования – СКЛ; изготовления заготовок – ЗГ; обработки заготовок – ОБ; сборки машин – СБ; материально-технологической подготовки производства – МТПП; информационно-технологической подготовки производства – ИТПП. Функции подсистем определяются их наименованием. В заготовительной, обрабатывающей и сборочной подсистемах реализуются в основном рабочие функции предприятия, а в остальных – обеспечивающие, которые необходимы для реализации рабочих функций.
Функции предприятия реализуются в производственном процессе, где выделяют ряд процессов технологического характера, во время выполнения которых качественное изменение объекта производства (формы, размеров, механических свойств, состояния поверхности и т.п.).
Технологический процесс, составные части ТП.
Технологический процесс представляет собой совокупность различных операций, в результате выполнения которых изменяются размеры, форма, свойства предметов труда, выполняется соединение деталей в сборочные единицы и изделия, осуществляется контроль требований чертежа и технических условий.
Законченную часть технологического процесса, выполняемую на одном рабочем месте, называют технологической операцией. Она является основным элементом производственного планирования и учета. На выполнение операций устанавливают нормы времени и расценки. По операциям определяют трудоемкость процесса, необходимое количество производственных рабочих, количество и вид оборудования и технологической оснастки, себестоимость изготовления и т.п. На операцию разрабатывается вся учетная и технологическая документация.
Основными технологическими частями операции являются переходы. Технологический переход – законченная часть технологической операции, выполняемая одними и теми же средствами технологического оснащения при постоянных технологических режимах и установке. При выполнении перехода режимы работы иногда изменяются без воздействия рабочего, т.е. автоматически, например, при выполнении перехода на станках с программным управлением. Переходы могут выполняться путем удаления одного или нескольких слоев материала за один или несколько рабочих ходов.
Рабочий ход – законченная часть технологического перехода, однократное перемещение инструмента относительно заготовки, которое сопровождается изменением ее размеров, качества и свойств. Однократное же перемещение инструмента относительно заготовки, необходимое для подготовки рабочего хода называют вспомогательным ходом.
Все действия рабочего, совершаемые им при выполнении технологического перехода, разделяются на отдельные приемы. Приемом называют законченную совокупность действий человека, применяемых при выполнении перехода или его части и объединенных одним целевым назначением.
Установка и закрепление заготовок в приспособление, смену инструмента, открепление и снятие заготовки, и другие, законченные части технологической операции, которые состоят из действий человека и (или) оборудования и не сопровождаются изменением свойств предмета труда, но необходимы для технологического перехода, называют вспомогательными переходами.
Установом называют часть операции, выполняемую при неизменном закреплении заготовок или собираемой сборочной единицы.
При одном установе заготовка может занимать различные позиции. Позиция – это фиксированное положение, занимаемое неизменно закрепленной заготовкой и собираемой сборочной единицей совместно с приспособлением относительно инструмента или неподвижной части оборудования при выполнении определенной части операции.
Наладкой называют подготовку технологического оборудования и технологической оснастки к выполнению технологической операции. К наладке относится установка приспособления на станок, установка на размер комплекта режущего инструмента и т.п.
Совокупность орудий производства, необходимых для выполнения технологического процесса, называют средствами технологического оснащения.
Технологическое оборудование – это средства технологического оснащения, в которых для выполнения определенной части технологического процесса размещают материалы или заготовки, средства воздействия на них, а также технологическую оснастку (например, металлорежущие станки, литейные машины, печи, испытательные стенды и т.п.).
В технологическую оснастку включаются средства технологического оснащения для выполнения определенной части технологического процесса (режущий инструмент, штампы, приспособления и т.п.).
Количество времени, затраченное на выполнение технологического процесса или его части, называют трудоемкостью. Единицей трудоемкости служит нормо-час. Для нормирования труда и планирования производственного процесса используется норма времени, которая измеряется в единицах времени (часах, минутах) с указанием квалификации рабочего.
Часто вместо нормы времени устанавливают обратную величину – норму выработки. Единицей измерения нормы выработки является количество деталей или изделий, которое обрабатывается в единицу времени с указанием квалификации рабочего.
Дата добавления: 2018-05-12; просмотров: 786; Мы поможем в написании вашей работы! |
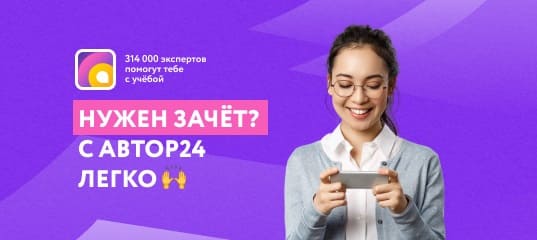
Мы поможем в написании ваших работ!