Технология литья в оболочковые формы, технико-экономические показатели.
Сущность способа заключается в заливке расплава в тонкую оболочковую форму, состоящую из двух предварительно скрепленных полуформ; затвердевший и охлажденный металл или сплав воспроизводит конфигурацию модели, по которой изготовлялись полуформы. Изготовление оболочковой формы исключает потребность в опоках, резко снижает расход формовочной смеси, легко механизируется и автоматизируется.
Формовочные смеси, применяемые при литье в оболочковые формы на 92-95% состоят из мелкого кварцевого, магнезитового или циркониевого песка и 4-6% связующего, в качестве которого используют термореактивную смолу фенолформальдегидную (пульвербакелит) или мочевиноформальдегидную (карбамид). Такой состав смеси обеспечивает малую шероховатость поверхности и более высокую точность отливок, чем изготовленных в ПГФ, так как оболочка твердеет на модели и сохраняет ее размеры. Чтобы исключить разделение песка и смолы и устранить пылеобразование в процессе приготовления, в смеси добавляют увлажнители: керосин, спирт, ацетон и др.
Модельная оснастка состоит из моделей отливок, модельных плит, стержневых ящиков, моделей литниковой системы и механизмов для съема оболочек.
Выбивка и очистка отливок при литье в оболочковые формы нетрудоемки, так как на отливках отсутствует пригар, а литники и прибыли имеют малые размеры. К моменту полной кристаллизации металла отливки смола из смеси выгорает, форма и стержни легко разрушаются, освобождая отливку при выбивке. Отработанную смесь и упрочняющую засыпку регенерируют, освежают и вновь возвращают для изготовления форм.
|
|
Литье в оболочковые формы наиболее рационально применять в условиях крупносерийного и массового производства для получения ответственных фасонных мелких и средних отливок толщиной стенок 3-15 мм и массой 0,25-100 кг из различных сплавов.
Процесс является высокомеханизированным и автоматизированным.
Преимуществами литья в оболочковые формы является высокая точность отливок (до 12…13 квалитета), с сравнительно низкой шероховатостью поверхностей 40…2,5 (в результате в 2 раза снижаются припуски на механическую обработку по сравнению с литьем в ПГФ). Повышается производительность труда; снижение брака в 1,5…2 раза. Высокая прочность оболочек позволяет изготовлять их тонкостенными, что значительно снижает расходы формовочных материалов.
Основными недостатками этого вида литья являются сравнительно большая стоимость песчано-смоляных смесей и токсичность смол при их выгорании, что требует применения эффективной вытяжной вентиляции.
Технология литья в металлические формы, технико-экономические показатели.
|
|
Кокилем называют металлическую форму заполняемую расплавом под действием гравитационных сил.
Сущность способа заключается в применении многократно используемой металлической литейной формы, которая формирует конфигурацию и свойства отливки. При этом способе литья практически исключается применение, либо расходуется малое количество песчаных смесей для изготовления разовых стержней. Полости в отливках оформляют песчаными, оболочковыми или металлическими стержнями.
По конструкции кокили бывают простыми и сложными, различают неразъемные вытряхные и разъемные с горизонтальным, вертикальным или комбинированным (сложным) разъемом (рис. 3.13).
Изготовляют кокили из серого чугуна (преимущественно), стали, а также из цветных сплавов.
Кокили небольших размеров либо отливают, либо получают обработкой резанием из поковок. Рабочие полости и элементы литниковой системы в последнем случае формируют электрофизической или электрохимической обработкой. Крупные кокили изготовляют литыми.
Разъемные кокили (рис. 3.13 б, в) состоят из двух половин 6, соединяемых центрирующими штырями 10. Для повышения жесткости и предупреждения коробления у кокилей предусматривают ребра жесткости 5, либо делают коробчатые формы. На наружной поверхности кокиля для ускоренного его охлаждения иногда отливают пальцы 8. Внутреннюю полость или отверстие в отливке образуют за счет песчаного 1 или металлического 9 стержня. Металл заливают в литниковую чашу 3, откуда по стояку 4 и питателям 7 он заполняет полость формы 2. Так как металлические стержни неподатливы, то во избежание образования в отливке трещин их удаляют из формы после заливки и образования достаточно прочной корки в отливке, т.е. до начала усадки металла. Если внутренняя полость отливки имеет сложную форму, то металлические стержни делают составными или применяют песчаные. Литниковую систему располагают в полости разъема кокиля. Для удаления воздуха из формы при заливке из формы и повышения газопроницаемости при охлаждении в плоскости разъема по всей высоте кокиля прорезают щели глубиной 0,3-0,5 мм.
|
|
Технология изготовления отливок в кокиле включает операции:
· очистка кокиля от старой облицовки;
· нанесение огнеупорного защитного покрытия или покраска рабочей поверхности кокиля;
· сборка формы с установкой стержней;
· заливка кокиля;
· выдержка отливки в форме;
|
|
· раскрытие и удаление из него отливки.
Очищенный кокиль подогревают до температуры 140-180˚С и с помощью пульверизатора или кисти на рабочие поверхности наносят облицовочные теплозащитные покрытия для предохранения от воздействия высоких температур заливаемого металла, улучшения заполняемости кокиля, облегчения извлечения отливок и др.
Теплозащитные покрытия приготовляют из огнеупорных материалов (пылевидного кварца, молотого шамота, графита, мела и др.) связующего (жидкого стекла и др.) и воды. Облицовка может состоять из нескольких слоев, толщина покрытия 0,3-0,8 мм. Для уменьшения шероховатости поверхности на облицовку наносят краску, имеющую тот же состав, что и облицовка, но более жидкую.
При сборке кокиля в определенной последовательности устанавливают металлические или песчаные стержни, проверяют точность их установки и закрепления, соединяют половинки кокиля с помощью механизма запирания.
Заключительная операция подготовки кокиля – нагрев его до рабочей температуры, значение которой (обычно 150…350˚С) определяется толщиной стенок и размерами, а также задаваемыми свойствами металла отливки.
Заливку металла осуществляют разливочными ковшами или автоматическими заливочными устройствами. После достижения до достаточной прочности отливки при ее затвердевании металлический стержень частично извлекают из отливки, чтобы избежать чрезмерного обжатия его усаживающейся отливкой и возникновения в ней по этой причине трещин. Охлаждают отливки до температуры выбивки, составляющей 0,6-0,8 температуры солидуса сплава.
Открывают кокиль, из отливки окончательно удаляют металлический стержень, а затем с помощью толкателей извлекают отливку из кокиля. (Песчаные стержни выбивают из отливок после из извлечения из кокиля). После этого отливки подвергают обрубке – обрезают литники, прибыли и выпоры, очистке и при необходимости – термической обработке. Отливки проходят контроль.
Технологический процесс литья в кокиль дает возможность создавать высокоэффективные автоматизированные литейные комплексы, используют одно- и многопозиционные автоматические кокильные линии изготовления отливок. Этот вид литья применяют в условиях крупносерийного и массового производства для изготовления отливок из чугуна, стали и цветных сплавов с толщиной стенок 3…100 мм массой от десятков граммов до сотен килограммов. Точность отливок соответствует 12…15 квалитетам, а шероховатость поверхности Rа25…2,5 мкм, что снижает припуски на механическую обработку вдвое по сравнению с литьем в ПГФ. Обладая по сравнению с песчано-глинистыми формами более высокой теплопроводностью (~ в 60 раз), кокили обеспечивают мелкозернистую структуру отливок, что повышает плотность металла и механические свойства.
Литье в кокиль относится к трудо- и материалосберегающим, малооперационным и малоотходным технологическим процессам. Оно способствует улучшению условий труда в литейном производстве и уменьшает воздействие на окружающую среду.
К недостаткам кокильного литья следует отнести: высокую стоимость кокиля; трудность получения тонкостенных отливок в связи с быстрым отводом теплоты от расплава металлическим кокилем; чугунные отливки в кокиле получают отбеленными и требуют длительного отжига, что удорожает их производство; опасность образования трещин в отливках из-за неподатливости металлической формы и стержней; сравнительно небольшую стойкость кокиля (небольшое число заливок) при изготовлении в нем стальных и чугунных отливок (табл. ).
Во избежание отбеливания чугунных отливок подбирают химический состав чугуна, обеспечивающий графитизацию в условиях повышенной скорости охлаждения, а также подогревают кокиль перед заливкой до температуры 250-300˚С и до минимума сокращают время выдержки отливок в кокиле.
Дата добавления: 2018-05-12; просмотров: 986; Мы поможем в написании вашей работы! |
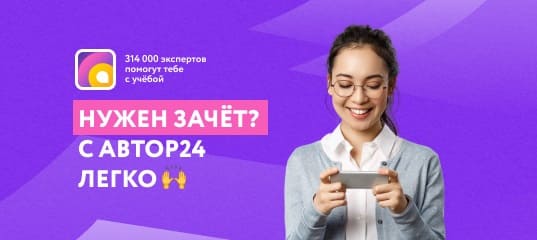
Мы поможем в написании ваших работ!