Технология литья под давлением, технико-экономические показатели.
Литьем под давлением получают отливки в металлических формах (пресс-формах), при этом заливку металла в форму и формирование отливки (затвердевание) осуществляют под давлением с холодной или горячей камерой прессования, расположенной горизонтально или вертикально.
На машинах с горизонтальной холодной камерой прессования (рис. 3.15 а) заданную порцию расплавленного металла заливают в камеру 2 подготовленной к заливке и закрытой пресс-формы, а плунжером 1 под давлением 40…100 МПа расплав подают в пресс-форму. Прилагаемое давление способствует улучшению жидкотекучести заливаемого расплава.
Пресс-форма состоит из неподвижной 5 и подвижной 6 полуформ. В подвижной полуформе установлен металлический стержень 4 и выталкиватели 3, с помощью которых из раскрытой пресс-формы удаляют отливку после ее затвердевания и охлаждения. Перед заливкой рабочие поверхности пресс-формы обдувают воздухом и смазывают специальными материалами для предупреждения адгезии (прилипания) металла отливки к пресс-форме, а затем нагревают до температуры 120…320˚С. Во время заливки пресс-форму охлаждают водой. Воздух и газы из объема пресс-формы удаляют через каналы глубиной 0,05-0,15 мм и шириной 15 мм, расположенных в плоскости разъема пресс-формы, или вакуумированием рабочей полости перед заливкой расплавленного металла.
Схема литьевой машины с горячей вертикальной камерой поршневого действия показана на рис. 3.15 г. Из обогреваемого тигля 1 расплав под давлением поршня подается по металлопроводу 2 в закрытую пресс-форму 3. После затвердевания металла в пресс-форме давление снимают, поршень движется вверх, форму раскрывают и отливку выталкивают толкателями. Машины с горячей камерой более производительны и расходуют меньше металла, однако их нельзя применять для литья сплавов с температурой плавления более 500˚С из-за быстрого изнашивания поршня. В машинах с горячей камерой получают отливки на основе цинка, олова и свинца.
|
|
Машины с холодной камерой используют для производства отливок на основе меди, алюминия и магния.
Литье под давлением является одним из самых высокопроизводительных специальных методов литья (200-400 отливок в час); процесс осуществляется на машинах и может быть полностью автоматизирован. Применяется в массовом и крупносерийном производствах отливок сложной конфигурации с минимальной толщиной стенок 0,8 мм и отверстиями диаметром до 1 мм преимущественно из цветных сплавов массой от нескольких граммов до десятков килограммов (~ 50 кг). За счет точной обработки и тщательного полирования рабочей полости пресс-формы обеспечивается точность отливок 8…13 квалитетов, а шероховатость поверхности Ra = 25…0,32 мкм; припуски на механическую обработку минимальны или не предусматриваются, что резко сокращает трудоемкость механической обработки отливок. Ускоренная кристаллизация металла в металлической пресс-форме под давлением обуславливают образование мелкозернистой структуры, отливки характеризуются высокими механическими свойствами (табл. 3.1). Отсутствие формовочных материалов улучшает условия труда и снижает загрязнение окружающей среды. Литье под давлением относят к малооперационным и безотходным технологическим процессам.
|
|
Недостатками литья под давлением являются: высокая стоимость пресс-форм и оборудования; ограниченность габаритных размеров и массы отливок, а также номенклатуры металлов и сплавов; наличие газовой пористости в массивных частях отливок, снижающей прочность и эксплуатационные свойства деталей.
Технология литья по выплавляемым моделям, технико-экономические показатели.
Сущность процесса заключается в заполнении расплавленным металлом неразъемной керамической оболочковой формы, получаемой из жидких формовочных смесей по точной разовой модели из легкоплавких пластичных материалов (воска, парафина, канифоли, стеарина, жидких кислот, церезина и др.) В производстве используют готовые легкоплавкие модельные составы ПС (50% парафина и 50% стеарина), ПВ, КЦП и др.
|
|
Изготовление разъемных прессформ:
Формовочными материалами для оболочковых форм служат суспензия и кварцевый песок. Керамическую суспензию приготовляют тщательным перемешиванием огнеупорных материалов (пылевидного кварца, электрокорунда, магнезита и др.) со связующим – гидролизованным раствором этилсиликата, жидкого стекла и др.
Для получения моделей отливок и литниковой системы используют разъемные пресс-формы. Одноместные пресс-формы изготовляют из гипса, дерева, пластмасс, сплавов алюминия и др. (мелкосерийное производство); многоместные прессформы – из алюминиевых сплавов и стали (серийное и массовое производство. Полость пресс-формы точно воспроизводит конфигурацию и размеры будущей детали с учетом усадки модельного состава.
Модельный состав в пастообразном состоянии запрессовывают в разъемную пресс-форму (б), в данном случае для четырех отливок деталей (а). После затвердевания модельного состава пресс-форму раскрывают и модель выталкивают в ванну с холодной водой. В результате получают модельный блок из четырех моделей 1, соединенных в центре элементами литниковой системы (в). В специальной пресс-форме получают модель литниковой системы, к которой крепят модельные блоки 1 и образуют «гроздевидный» блок 2 (г). Легкоплавкая модель в отличие от обычной является точной копией изготовляемой детали: она неразъемна, имеет все внутренние полости, отверстия, резьбу и не имеет стержневых знаков.
|
|
Формы по выплавляемым моделям изготовляют погружением модельного блока 2 в керамическую суспензию 3, налитую в емкость (г) с последующей обсыпкой кварцевым песком в специальной установке (д). Затем модельные блоки сушат 2-2,5 ч. на воздухе или 20-40 мин. в специальном шкафу в среде аммиака. На модельный блок наносят четыре-шесть слоев огнеупорного покрытия с последующей сушкой каждого слоя. Для обсыпки первого слоя суспензии, нанесенного на блок моделей, применяют мелкозернистый кварцевый песок, а для последующих слоев – более крупный. Таким образом получают прочные оболочковые формы.
Модельную массу из формы удаляют в процессе выдержки в сушильном шкафу при температуре более 100˚ или погружением в ванну с горячей водой (е). Затем формы промывают водой и сушат в шкафах в течение 1,5-2 ч. при температуре 200˚С. Для выжигания остатков модельного состава, а также для упрочнения оболочки полученную литейную форму в металлическом ящике засыпают металлической дробью или крупным огнеупорным кварцевым песком и др. и помещают в печь для обжига при температуре 800-900˚С в течение 2 ч. При обжиге частички связующего спекаются с частичками огнеупорного материала, испаряется влага, выгорают остатки модельного состава. Сразу после обжига в горячие формы заливают расплавленный металл (ж), что дает возможность получать тонкостенные отливки сложной конфигурации.
После затвердевания и охлаждения отливок форму разрушают, отливки очищают от остатков керамической оболочковой формы и отрезают от них литники. Для окончательной чистки отливки подвергают обработке в 45%-ном водном растворе едкого натра при температуре 150˚С. После травления отливки промывают проточной водой, сушат, подвергают термической обработке и контролю.
В настоящее время литье по выплавляемым моделям является хорошо отработанным высокомеханизированным и автоматизированным процессом современного машиностроения. Заливка металла в горячие формы обеспечивает возможность получать сложные по конфигурации и тонкостенные (до 0,3 мм), с отверстиями до 2 мм; отливки массой от нескольких граммов до десятков килограмм из любых сплавов. Керамическая суспензия позволяет точно воспроизвести контуры модели, а неразъемная литейная форма с малой шероховатостью поверхности способствует получению отливок с высокой точностью геометрических размеров (9…10 квалитета) и малой шероховатостью поверхности (Ra=25…1,25 мкм). Припуск на механическую обработку составляет 0,2…0,7 мм, объем механической обработки отливок уменьшается на 80-100%.
Литье по выплавляемым моделям относится к прогрессивным материало- и трудосберегающим технологическим процессам обработки металлов. Процесс экономически выгоден для любых типов производства; характеризуется уменьшенным расходом формовочных материалов, улучшенными условиями труда и меньшим воздействием на окружающую среду.
Недостатками литья по выплавляемым моделям являются: значительная трудоемкость изготовления формы и трудности изготовления крупных отливок; снижение механических свойств металла вследствие применения предварительно нагретых форм.
Дата добавления: 2018-05-12; просмотров: 521; Мы поможем в написании вашей работы! |
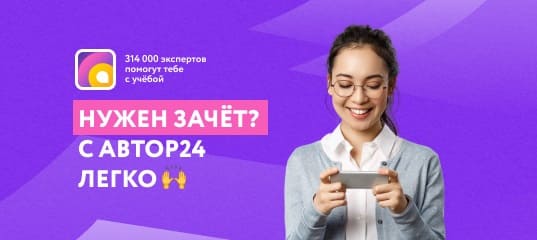
Мы поможем в написании ваших работ!