Развитие нефтеперерабатывающей промышленности в СССР. 20 страница
149
флегмы, которого было бы достаточно не только для данной колонны, но и для колонн, расположенных ниже. Таким образом, вышележащие секции оказываются перегруженными жидкостным потоком, величина которого значительно превышает необходимое для данной секции орошение. При переходе на комбинированную схему в виде острого орошения вводится только то количество
Рис. 32. Пароэжекторные агрегаты — одноступенчатые (а) и двухступенчатые (б):
/ — отсасываемая смесь; Л —выхлоп; III — водяной пар;
IV — вода;
/ — паровое сопло; 2 —головка; 3 — диффузор; 4 — эжектор
I ступени; 5 — эжектор 2-й ступени; 6 — конденсатор смешения;
7 —барометрическая труба.
флегмы, которое необходимо для верхней секции колонны. В остальных секциях флегма создается с помощью циркулирующего орошения, которое забирается с нижележащей тарелки соответствующей секции, охлаждается и подается на верхнюю тарелку этой секции. В атмосферных колоннах современных установок первичной перегонки имеется 2—3 циркулирующих орошения. Число промежуточных орошений, как правило, на единицу меньше числа отводимых боковых погонов.
Внедрение промежуточных циркулирующих орошений позволяет улучшить условия регенерации тепла на установке, так как температура отводимого циркулирующего орошения выше температуры острого орошения и дает возможность значительно разгрузить верхнюю часть атмосферной колонны и конденсаторы-холодильники. В многосекционных вакуумных колоннах орошение создаетсяисключительно с помощью потоков циркулирующих орошений.
|
|
150
Способы создания вакуума. Вакуум в колоннах создается с помощью вакуум-насосов или пароструйных эжекторов. Вакуум-насосы по принципу действия аналогичны компрессорам. Существуют поршневые, ротационные и водокольцевые вакуум-насосы.
Принцип работы пароструйных эжекторов (рис. 32)—использование кинетической энергии водяного пара. Струя пара с большой скоростью вытекает из сопла, захватывает отсасываемую газожидкостную смесь и вместе с ней выбрасывается в атмосферу.
Рис. 33. Схемы конденсации паров, уходящих из вакуумной
колонны;
а — с конденсатором смешения; 6 — с поверхностным конденсатором; / — водяной пар; // — вода; Ш-уловленный нефтепродукт; /V-вода, загрязненная нефтепродуктами; V — несконденсировавшиеся газы (выхлоп эжектора); / — колонна; 2 —барометрический конденсатор; 3 — барометрическая труба; 4 — эжекторы; 5—промежуточный конденсатор пароэжекторного агрегата; в —барометрический колодец; 7 —поверхностный конденсатор; 8—газосепаратор; 9—отстойник-сепаратор.
Чтобы создать небольшой вакуум (до 90 кПа), используют одноступенчатые эжекторы. Если требуется более глубокий вакуум, применяют многоступенчатые пароэжекторные агрегаты, снабженные промежуточными конденсаторами (см. рис. 32,6). В конденсаторах рабочий пар и газы, выходящие из предыдущей ступени, охлаждаются и конденсируются.
|
|
Эжекторами и вакуум-насосами из вакуумных колонн отсасываются газы разложения, водяной пар, подаваемый в колонны для улучшения ректификации, а также воздух, попавший в аппаратуру вследствие ее недостаточной герметичности. Схемы конденсации паров, уходящих из вакуумных колонн, изображены на рис. 33.
В схеме на рис. 33, а основным аппаратом, применяемым для конденсации, является барометрический конденсатор смешения. Он представляет собой цилиндрический аппарат с каскадными ситча-тьши тарелками, под нижнюю из которых поступают пары с верха
151
вакуумной колонны. Охлаждающая вода подается на верхнюю тарелку. Сконденсировавшиеся нефтяные пары и вода сливаются по трубе 3 в барометрический колодец 6, а газ с верха барометрического конденсатора отсасывается паровыми эжекторами или вакуум-насосами 4. Существенный недостаток схемы а состоит в том, что при непосредственном, смешении с нефтяными парами охлаждающая вода сильно загрязняется сероводородом и нефтепродуктами. Экспериментально установлено, что в воде конденсаторов содержится до 5% от получаемой на АВТ дизельной фракции. Вода, загрязненная нефтепродуктами, попадает затем в сточные воды завода, загрязняя почву и водоемы.
|
|
В схеме на рис. 33, б опасность загрязнения воды устранена. Пары с верха вакуумной колонны поступают в поверхностный конденсатор 7, где конденсируется основная часть водяных паров и унесенных нефтяных фракций. В качестве поверхностного конденсатора применяются кожухотрубчатые теплообменники с плавающей головкой или аппараты воздушного охлаждения. Затем конденсат и пары поступают в газоеепаратор 8, из которого не-сконденсировавшиеся пары отсасываются эжекторами. Конденсат по барометрической трубе поступает в отстойник-сепаратор 9. Сюда также подаются паровые конденсаты из межступенчатых конденсаторов эжектора. Вода из отстойника сбрасывается в канализацию, а нефтепродукт, отделенный от воды, возвращается в линию дизельной фракции. Выхлопные газы из эжектора сжигаются в трубчатой печи. На всех действующих АВТ система с использованием конденсаторов смешения заменяется системой с поверхностными конденсаторами.
|
|
Современные схемы создания вакуума обеспечивают поддержание в колоннах установок АВТ остаточного давления 5—9 кПа.
§ 29. МЕРЫ БОРЬБЫ С КОРРОЗИЕЙ
Причины коррозии при переработке нефти.При переработке нефти происходит разрушение металла, из которого выполнена аппаратура, оборудование и трубопроводы, вызываемое коррозией. Коррозию на установках первичной перегонки могут вызывать:
1) минеральные соли, которые содержатся в нефтях, поступающих на переработку; при нагреве нефти соли — в основном хлориды — разлагаются и образуется хлористый водород, который в присутствии влаги обладает высокой коррозионной активностью;
2) сернистые соединения, которые присутствуют в большинстве перерабатываемых в настоящее время нефтей; при переработке сернистых нефтей выделяется большое количество коррозионноак-тивных веществ — сероводорода и меркаптанов;
3) нефтяные кислоты, содержание которых в ряде нефтей достигает 1,9%.
Скорость коррозии черных металлов в присутствии влажного хлористого водорода составляет 5—20 мм/год, а совместное присутствие сероводорода и хлористого водорода усиливает коррозию
152
в 3—4 раза. Наиболее интенсивно процессы коррозии протекают 6 конденсаторах-холодильниках, верхней части ректификационных колонн, печных трубах, трубопроводах горячих остатков (мазута и гудрона). Показателем интенсивности коррозии конденсаторов-холодильников и ректификационных колонн служит содержание ионов железа в воде, удаляемой из рефлюксных емкостей, а также рН этой воды.
Меры борьбы с коррозией.Для уменьшения коррозии на установках первичной перегонки нефти применяются следующие методы: 1) глубокое обезвоживание и обессоливание нефти; 2) использование коррозиоиностойких материалов; 3) введение нейтрализующих веществ и ингибиторов коррозии.
Чтобы увеличить срок службы оборудования, на наиболее опасных его участках применяются стойкие против коррозии материалы— легированные стали Х5М, 0X13, латунь, сплав никеля и меди, называющийся монель-металлом. Для снижения стоимости аппаратуры ее изготавливают из двухслойного металла: внутренняя поверхность, подверженная действию вредных соединений, делается из легированных металлов, наружная — из углеродистой стали.
Применение коррозиоиностойких материалов позволяет в несколько раз снизить скорость коррозии оборудования, однако наибольший эффект в борьбе с коррозией дает применение нейтрализующих веществ и ингибиторов коррозии. В качестве нейтрализующих веществ используются содо-щелочной раствор и аммиак. В результате скорость коррозии снижают до 0,1—0,2 мм/год. Более эффективное уменьшение коррозии достигается применением специальных веществ — ингибиторов коррозии. Ингибиторы (замедлители) коррозии представляют собой органические вещества, которые образуют на поверхности металла тонкую защитную пленку.
В нашей стране разработаны и внедряются на нефтезаводских установках ингибиторы коррозии — ИКБ-2, ИКБ-4, за рубежом широко применяются ингибиторы кронокс, налко и др.
§ 30. ОСНОВЫ ЭКСПЛУАТАЦИИ ПЕРЕГОННЫХ УСТАНОВОК
Контроль и регулирование работы установок.Работу установок первичной перегонки, как и любых других технологических установок, регулирует производственный персонал с помощью контрольно-измерительных приборов, а также путем непосредственного контроля за состоянием аппаратуры, оборудования, коммуникаций, лабораторных анализов качества сырья и получаемой продукции.
Установки первичной перегонки оснащены большим числом приборов для измерения и автоматического регулирования расхода, температуры, давления и уровня продуктов в аппаратах и трубопроводах. На современной установке АВТ имеется более 2 тыс. приборов автоматического контроля и регулирования.
153
Нормальная эксплуатация установки первичной перегонки во многом зависит от технологического режима печей. Схема регулирования трубчатой печи приводится на рис. 34. Основной регулируемый параметр в трубчатой печи — температура нагреваемого продукта на выходе из печи. Необходимо, чтобы температура эта поддерживалась постоянной.
В колонну
Рис. 34. Принципиальная схема регулирования трубчатой печи:
/, 7—клапаны; 2, 3— регуляторы; 4, 5—термопары; 6 — диафрагма; в—регулирующий блок.
В настоящее время на НПЗ применяется схема связанного регулирования температурного режима трубчатых печей. В системе имеются два регулятора 2 и 3. Один из них 2 поддерживает постоянной температуру дымовых газов над перевальной стенкой печи. При отклонении температуры от заданного значения регулятор с помощью клапана 1 изменяет подачу топлива в печь.
При постоянстве температуры, состава и расхода нагреваемого продукта и при неизменном состоянии змеевика печи температура продукта на выходе из печи будет постоянной. Однако эти параметры могут изменяться, а следовательно, будет меняться и температура продукта на выходе. Чтобы стабилизировать температуру продукта, на выходе его из печи установлен регулятор 8, соединенный с термопарой 5, который при изменении температуры меняет задание регулятору 2 и, следовательно, изменяет в допу-
154
стимых пределах температуру дымовых газов над перевалом за счет изменения подачи топлива.
На температурный режим печей влияет также равномерность
подачи продукта. Поскольку при частом изменении расхода про
дукта меняется температура в печи и уменьшается продолжитель
ность безаварийной эксплуатации труб змеевика, расход продукта
в печи следует поддерживать постоянным. Для этого на выходной
линии насоса устанавливается диафрагма в, связанная с регистри
рующим прибором и регулирующим блоком 8. Регулирующий
блок в соответствии с установленным заданием действует на
клапан 7. , .
Задача регулирования ректификационной колонны — обеспечение заданной четкости разделения при условии максимально экономичной работы аппарата. Поскольку ректификационные колонны используются в разных условиях эксплуатации, схемы их регулирования могут быть различными. При разделении многокомпонентных смесей в колоннах вручную или автоматически регулируются расход и состав питания, температура верха и низа колонны, давление, уровень остатка в нижней части колонны.
Температуру верха колонны поддерживают на заданном уровне, изменяя расход орошения. Температуру низа регулируют, изменяя количество теплоносителя, подаваемого в кипятильник, или подачу топлива в трубчатую печь, которая служит для подогрева «горячей струи».
- Давление в колонне регулируется: 1) изменением количества сбрасываемого из рефлюксной емкости неконденсирующегося продукта (газа); 2) изменением количества подаваемой на охлаждение продукта воды (применяется для вакуумных колонн); 3) с помощью клапана-регулятора на линии вывода паров из колонны.
Однако и температура, и давление являются лишь косвенными параметрами, позволяющими судить о процессе и качестве получаемых продуктов. Четкость разделения можно заметно повысить, если в схемах регулирования применить разработанные в последние годы анализаторы качества. Так, в колоннах стабилизации бензина применяются схемы поддержания постоянства упругости паров стабильного бензина изменением подачи теплоносителя в рибойлер стабилизатора. В отпарных колоннах АВТ используется схема регулирования температуры вспышки выходящего из них продукта подачей пара.
На рис. 35 приводится схема регулирования работы отбензи-нивающей колонны. Для обеспечения постоянства загрузки колонны и стабилизации ее работы расход нефти регулируется специальным регулятором в зависимости от уровня отбензиненной нефти в нижней части колонны.
Температура верха колонны зависит от того, какой конец кипения должен иметь отбираемый в колонне бензиновый погон. Она поддерживается постоянной за счет подачи определенного количества острого орошения и корректируется автоматическим
155
анализатором конца кипения. При стабильных условиях работы и конец кипения бензина, и температура верха, и количество ороше-
Рис. 35. Принципиальная схема регулирования отбензинивающей колонны:
I — нефть; //—газ; /// — бензин на стабилизацию; IV—полуотбензиненпая нефть в атмосферную колонну.
ния остаются постоянными. Если качество бензина по каким-либо причинам меняется, например за счет изменения состава сырья, то с помощью автоматического анализатора конца кипения изменяется температура верха. Чтобы поддержать эту новую температуру верха, в колонну подается нужное количество орошения.
156
Расход отбензиненной нефти и «горячей струи» поддерживают постоянным, а температуру «горячей струи» и, следовательно, температуру низа колонны регулируют изменением подачи топлива в печь.
Лабораторный контроль качества сырья ипродукции. Благодаря лабораторному контролю персонал установок получает дополнительные сведения, позволяющие правильно вести технологический процесс.
В лаборатории исследуют качество нефти, поступающей на перегонную установку, и продукции, уходящей с установки. При анализе нефти определяют ее плотность, содержание солей, воды, светлых фракций. Анализ бензиновых фракций состоит в определении октанового числа, наличия или отсутствия активных сернистых соединений (проба на медную пластинку). Проводят также фракционную разгонку бензина. Для средних дистиллятов — керосиновой и дизельной фракции — анализируют фракционный состав, вязкость, температуры вспышки, застывания или помутнения.
Если в результате лабораторного анализа выясняется, что продукция не соответствует нормам, оператор должен немедленно определить причину этого и в случае необходимости изменить режим работы установки или отдельных аппаратов.
На лабораторный анализ затрачивается много времени, его результаты поступают на установку через 1,5—2 ч после отбора пробы, т. е. когда оператор уже не может исправить качество выпущенной за это время продукции. Кроме того, лабораторным контролем занимается большое число людей. Поэтому основное направление технического прогресса и совершенствования установок первичной перегонки состоит в значительном увеличении степени автоматизации, переходе к автоматическому контролю качества продукции.
Разработанные в последние годы анализаторы качества на потоке позволяют не направлять отбираемые пробы сырья и продукции в цеховую или заводскую лабораторию, а получать результат анализа сразу же, непосредственно на установке. В перспективе, связав анализаторы качества с регуляторами технологического режима, можно будет добиться полной автоматизации технологического процесса. Анализаторы качества, определяющие фракционный состав, температуру вспышки, плотность продукта, уже работают на многих установках прямой перегонки.
Организация и учет работыустановки. С помощью регистрирующих и показывающих приборов, а также руководствуясь данными лабораторных анализов, оператор имеет возможность непрерывно следить за эксплуатацией установки, соблюдением технологического режима.
Основным документом, в котором определены требования к процессу, является технологический регламент. В регламенте приводится характеристика изготавливаемой продукции, сырья и полуфабрикатов, описание технологического процесса, нормы режима,
157
описываются возможные неполадки, причины и способы их устранения.
Оперативный документ, находящийся на установке и содержащий основные требования по поддержанию режима технологического процесса, носит название технологической карты. Технологическая карта вывешивается на видном месте в операторной установке и служит для старшего оператора и всех работающих на установке основным руководством. Карту для каждой установки пересматривают ежегодно. Обычно в технологических картах приводятся пределы регулирования различных параметров технологического режима.
Текущую работу оператор анализирует с помощью записей о технологическом режиме и качестве сырья и продукции. Запись показателей режима производится с интервалом в два часа в специальном режимном листе. В режимный лист заносят также данные лабораторных анализов. Другим важным документом является вахтенный журнал, куда записывают сведения о регулировке режима в связи с переходом на отбор других нефтепродуктов, о возникающих в ходе вахты нарушениях режима и неполадках в работе установки. На основе вахтенного журнала и режимного листа заступающая на вахту смена знакомится с работой установки в предшествующий период. Соблюдение норм технологического режима контролирует отдел технического контроля (ОТК) завода.
Остановка установки. Плановая остановка на ремонт установки первичной перегонки ведется следующим образом. Постепенно Снижают температуру на выходе нефти из печи и уменьшают до 50% производительность установки. После того как температура на выходе из печи снизится до 320 СС, установку переводят на горячую циркуляцию — прием сырья и вывод продуктов прекращается. Затем приостанавливают подачу острого водяного пара в колонны, перекрывают линии перетока боковых фракций из атмосферной колонны в отпарные секции, откачивают оставшиеся в отпарных секциях нефтепродукты в резервуар «некондиции» (некачественного продукта), находящийся в промежуточном пар ке установки.
Далее останавливают насосы циркулирующих орошений, но подачу острого орошения продолжают еще некоторое время, чтобы постепенно охладить колонну. Прекращение подачи острого орошения и отключение всех насосов и вентиляторов воздушных холодильников проводят после того, как исчезнет уровень жидкости в рефлюксных емкостях.
После снижения температуры на выходе из печи до 250 °С тушат все форсунки и перекрывают задвижки на линиях подачи топлива. Когда температура низа колонны К-1 и К-2 снизится до 150—160 °С, горячая циркуляция прекращается.
После того как установка остановлена, проводят тщательную подготовку аппаратуры к ремонту. Аппараты и трубопроводы
158
Дата добавления: 2018-04-04; просмотров: 440; Мы поможем в написании вашей работы! |
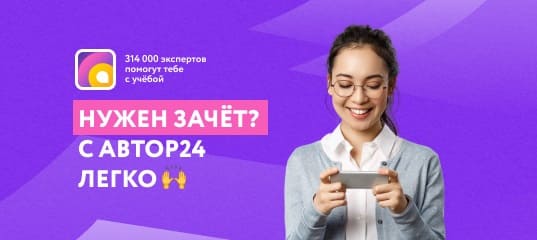
Мы поможем в написании ваших работ!