Развитие нефтеперерабатывающей промышленности в СССР. 17 страница
Жидкая фаза опускается по тарелкам нижней (отгонной) части секции и при этом из нее отгоняются легкие фракции.
Паровая фаза поднимается по тарелкам верхней концентрационной части секции /, постепенно облегчаясь по составу, и затем поступает в секцию 2. Секция / представляет собой полную ректификационную колонну, ректификат которой служит сырьем секции 2. В секции 2 от смеси отделяется фракция, которая частично перетекает в секцию /, а частично поступает в отдельно расположенную отгонную часть. Здесь фракция дополнительно ректифицируется. Ректификат секции 2 является сырьем секции 3.
В секциях 3 н 4 отделяются в виде боковых погонов еще две фракции. Как секция 2, так и секции 3 и 4 представляют концентрационные части' простых колонн. Отгонные части этих колонн выделены в самостоятельные колонны, которые обычно именуются
123
отпарными или стриппингами. Готовые продукты отбираются с низа отгонных секций, а отогнанные легкие фракции отводятся в основную колонну, с верха которой уходит самый легкий дистиллят.
Сложные колонны применяются в тех случаях, когда не требуется особенно высокой четкости разделения продуктов. Для четкого и сверхчеткого фракционирования (при вторичной перегонке бензинов, газоразделении) обычно устанавливается несколько простых ректификационных колонн, в каждой из которых выделяется один или два целевых компонента.
|
|
Перегонка нефти до мазута и гудрона.Первичная перегонка нефти на трубчатых установках осуществляется при атмосферном давлении и под вакуумом. При перегонке нефти на трубчатых установках, работающих при атмосферном давлении, из нефти выделяют светлые дистилляты — бензиновый, керосиновый, дизельный. Остатком от перегонки при атмосферном давлении является мазут —фракция, перегоняющаяся выше 330—350 °С. Эти установки носят название атмосферная трубчатая установка (AT).
Для того чтобы выделить более высококипящие нефтяные фракции, мазут подвергается перегонке на установках, работающих с применением вакуума. Остатком от перегонки мазута является гудрон.
В зависимости от общей схемы НПЗ и свойств поступающей для переработки нефти сооружаются либо установки атмосферной перегонки, либо установки, сочетающие атмосферную и вакуумную перегонку, — атмосферно-вакуумные трубчатые установки (АВТ). Различные варианты технологических схем НПЗ рассматриваются в § 86.
В тех случаях, когда на заводе необходимо получить максимальное количество светлых продуктов, перегонку ведут до гудрона. Выделенные из мазута темные дистиллятные фракции и гудрон затем используются для получения более легких нефтепродуктов методами крекинга, коксования и др. Перегонку до гудрона проводят и в том случае, если на заводе организуется производство нефтяных масел, кокса, битума. Если же. требуется получить максимальное количество котельного топлива, то ограничиваются перегонкой до мазута.
|
|
Ассортимент продуктов атмосферных и атмосферно-вакуумных установок. Врезультате первичной перегонки нефти при атмосферном давлении получаются следующие продукты.
1. Сжиженный углеводородный газ, состоящий в основном из пропана и бутана. Количество продукта зависит от того, насколько глубоко была стабилизирована нефть на промысловых установках. При переработке нефти с большим содержанием газа пропан-бутановая фракция выводится с перегонной установки не только в жидком, но и в газообразном виде. После очистки от сернистых соединений прямогонный сжиженный газ может использоваться какбытовое топливо. Прямогонный газ является также сырьем газофракционирующих установок.
124
2. Бензиновая фракция. Перегоняется в пределах 30—180 °С. Используется в качестве компонента товарного автобензина, как сырье установок каталитического риформинга.
3. Керосиновая фракция. Перегоняется в пределах 120—315°С. Используется в качестве топлива реактивных авиационных двигателей, для освещения, как горючее тракторных карбюраторных двигателей. Подвергается дополнительной обработке на установках гидроочистки, щелочной очистки или демеркаптанизации с целью очистки от сернистых соединений и улучшения эксплуатационных качеств, в частности термической стабильности.
|
|
4. Дизельная фракция. Перегоняется в пределах 180—350 °С. Ранее дизельную фракцию называли атмосферным газойлем. Фракция используется как топливо для дизельных двигателей, установленных на автомобилях, тракторах, тепловозах, судах морского и речного флота. Дизельная фракция, полученная из сернистых нефтей, нуждается в очистке от серы, которая проводится с применением гидрогенизационного метода (см. § 56).
5. Мазут — остаток, получаемый при атмосферной перегонке нефти. Температура начала кипения 330—350 °С. Используется в качестве котельного топлива, является сырьем установок термического крекинга.
Ассортимент продуктов вакуумной перегонки мазута зависит от варианта переработки нефти. Существуют две схемы переработки мазута: масляная и топливная. При масляной схеме получают несколько фракций — вакуумных дистиллятов, при топливной — одну.
|
|
Число вакуумных дистиллятов при масляной схеме переработки мазута определяется типом перерабатываемой нефти и равно 2—3. Каждый из дистиллятов затем подвергается очистке (см. гл. X), очищенные продукты смешиваются в различных соотношениях для получения тех или иных сортов масел.
Вакуумный дистиллят, вырабатываемый при топливной схеме переработки мазута, перегоняется при 350—500°С и используется как сырье каталитического крекинга или гидрокрекинга. Эту фракцию иногда называют вакуумным газойлем.
6. Гудрон — остаток от перегонки нефти, перегоняется при
температуре выше 500 °С. Это — высоковязкий продукт, застыва
ющий при 30—40 °С. Он используется как сырье установок терми
ческого крекинга, коксования, производстпа битума и высоковяз
ких масел.
§ 26. ТЕХНОЛОГИЧЕСКИЕ СХЕМЫ УСТАНОВОК ПЕРВИЧНОЙ ПЕРЕГОНКИ НЕФТИ
Типы установок.Атмосферные и вакуумные трубчатые установки существуют независимо друг от друга или комбинируются в составе одной установки.
Атмосферные трубчатые установки подразделяются в зависимости от их технологической схемы на установки с однократным и двукратным испарением нефти.
125
Принципиальная схема установки с однократным испарением приводится на рис. 15, а. Нефть пропускается сырьевым насосом через теплообменники и трубчатую печь в ректификационную колонну. В эвапорационном пространстве происходит однократное испарение нефти. Пары нефти затем разделяют ректификацией на целевые фракции, а из жидкости также с применением процесса ректификации удаляют легкокипящие фракции.
Схема установки с двукратным испарением приводится на рис. 15,6. Нагретая в теплообменнике нефть подается в так на-
Рис. 15. Схема атмосферной перегонки с однократным (а) и двукратным (б)
испарением нефти: I — нефть; // —газ; /// — бензин; /I/ —керосин; V— Дизельная фракция; VI — мазут.
зываемую отбензинивающую колонну. В эвапорационном пространстве этой колонны происходит испарение нефти. Поскольку нефть нагрета только до 200—240 °С, количество образующихся паров невелико и в них в основном содержатся бензиновые фракции. На ректификационных тарелках концентрационной части колонны бензин отделяется от более тяжелых фракций и в виде паров уходит из колонны. Вместе с парами бензина удаляются пары воды, поступившей на установку первичной перегонки с нефтью, и газы.'
Полуотбензиненную нефть забирают насосом и через трубчатую печь подают в основную, атмосферную колонну, где происходит повторное испарение нефти и ректификация паров с выделением тяжелого бензина (смешиваемого затем с бензином, получаемым в отбензинивающей колонне), керосиновой и дизельной фракции. Остатком является мазут.
Достоинством схемы с однократным испарением является то, что легкие и тяжелые фракции испаряются совместно. Это спо-
126
собствует более глубокому отделению тяжелых компонентов при относительно низких (300—325°С) температурах подогрева нефти. Установки однократного испарения компактны, имеют малую протяженность трубопроводов, требуют меньше топлива, чем другие установки.
Недостатки схемы с однократным испарением следующие:
1) при перегонке нефтей с повышенным (выше 15%) содержанием бензиновых фракций значительно увеличивается давление в теплообменниках и трубах печного змеевика, что приводит к необходимости применять более прочную и металлоемкую аппаратуру, увеличивать давление в линии нагнетания сырьевого насоса;
2) если на перегонку подается нефть, из которой плохо удалена вода, то это также приводит к повышению давления в печи и может вызвать повреждение фланцевых соединений печных труб;
3) если перегоняемая нефть недостаточно хорошо обессолена, то при ее нагреве в трубах печи будут отлагаться минеральные соли, из-за этого происходят местные перегревы в змеевиках печей, что в конечном итоге может приводить к аварии — прогару труб.
При двукратном испарении газ, вода и значительная часть бензина удаляются из нефти до ее поступления в печь. Это обстоятельство облегчает условия работы как печи, так и основной ректификационной колонны и является основным преимуществом схемы с двукратным испарением. Схема с двукратным испарением особенно удобна в тех случаях, когда часто происходит изменение типа перерабатываемой нефти. На установках Двукратного испарения устранены недостатки, характерные для установок однократного испарения.
Однако, чтобы достичь такой же глубины отбора дистиллятов, как при однократном испарении, нефть на установках двукратного испарения приходится нагревать до более высокой температуры (360—370 °С). На установке с двукратным испарением удваивается количество ректификационных колонн, загрузочных насосов, растут размеры конденсационной аппаратуры.
На установках и блоках вакуумной перегонки также применяются схемы однократного и двукратного испарения (рис. 16). Наиболее распространены блоки с однократным испарением мазута (рис. 16, а). Они построены на большинстве отечественных НПЗ. Но, как показал опыт эксплуатации, на таких блоках не удается получить хорошо отректифицированные вакуумные дистилляты с четкими пределами перегонки, необходимые для получения высококачественных масел. Среднее значение «налегания» температур выкипания смежных вакуумных дистиллятов составляет 70—130 °С.
Добиться улучшения четкости вакуумных дистиллятов можно за счет увеличения числа ректификационных тарелок. Однако такое решение не всегда приемлемо, поскольку при увеличении числа тарелок в колонне снижается вакуум, повышается температура
127
*nt
V |
lit |
£Г
к-i
YVM^-
/7-J |
K-2
^
■if
-d
-@------- ► VI
-<Э------ *■ vn
-®------- +1K
Рис. 16. Схемы вакуумной перегонки мазута с однократным (а) и двукратным (б, в) испарением:
/ — мазут; // — водяной пар; /// — пары с верха вакуумных колонн; IV — вакуумный дистиллят (фракция 350-500°С); V, VI, VII — масляные погоны; VIII — полугудрон; IX — гудрон.
на нижних тарелках, может уменьшиться глубина отбора и ухудшиться качество дистиллятов. Более рациональный путь улучшения качества вакуумных дистиллятов — перегонка по схеме двукратного испарения (рис. 16,б, а).
Схема, приведенная на рис. 16,6, предусматривает отбор в первой вакуумной колонне широкой масляной фракции, которая после нагрева в печи разделяется во второй колонне на фракции с более узкими пределами перегонки. По варианту, изображенному на рис. 16, в, в первой вакуумной колонне от мазута отделяется в виде бокового погона легкий масляный дистиллят. Остаток — полугудрон вновь нагревается в печи и подается во вторую колонну, в которой отбираются остальные дистилляты.
При двухступенчатой вакуумной перегонке расходуются дополнительные количества топлива, пара, электроэнергии. Однако достигаемое улучшение качества масляных дистиллятов, а в конечном итоге, товарных масел компенсирует эти затраты. Среднее значение налегания температур выкипания снижается до 30—60 °С.
Схемы установок. На НПЗ применяются все описанные выше схемы перегонки нефти и мазута, строятся отдельно стоящие установки атмосферной и вакуумной перегонки, комбинированные атмосферно-вакуумные трубчатые установки.
В 1947—1953 гг. в нашей стране строились AT и АВТ мощностью 0,5—0,6 млн. т в год. В последующие годы были сооружены установки мощностью 1—3 млн. т. Начиная с 1967 г. вводят в эксплуатацию мощные установки по перегонке нефти, перерабатывающие 6—8 млн. т в год. На многих установках, построенных в последние 10—15 лет, атмосферно-вакуумную перегонку нефти комбинируют с обессоливанием сырья и вторичной перегонкой бензина.
На рис. 17 приводится технологическая схема комбинированной установки ЭЛОУ-АВТ производительностью 6 млн. т нефти в год, рассчитанной на переработку сернистых нефтей и построенной на ряде заводов.
Нефть, поступающая на установку, забирается насосом Н-1 и двумя потоками проходит через сырьевые теплообменники, в которых нагревается до 130—140 °С. Первый поток нефти подогревается за счет теплообмена с первым (в Т-1) и вторым (в Т-2) циркулирующими орошениями колонны К-2. Второй поток проходит через теплообменники Т-3, где подогревается фракцией 350— 500 °С, и Т-4— средним циркулирующим орошением вакуумной колонны К-6. Затем оба потока нефти смешиваются и поступают на блок обессоливания.
Обезвоженная и обессоленная нефть после электрообессолива-ния вновь делится на два потока и поступает в теплообменники. Первый поток нефти нагревается в Т-5 и Т-6 гудроном, второй — в Т-7 — нижним циркулирующим орошением К-6 и в Т-8 — гудроном. Нагретая до 220—240°С нефть поступает затем в отбензини-вающую колонну К-1-
Верхний продукт К-1 конденсируется и охлаждается в воздушном и водяном конденсаторах-холодильниках ХК-1 и ХК-2, после
5 Зак, ЗВО
129
If |
ХК-3 ХК |
|
J K-2 |
Ш |
н-з |
хш
7-7 7-8
•-©-©-
7-5 7-6
Блок ЭЛОУ
7-3 7-4
XK-1 \XK-2
to
П{1 |
V2
Рис. 17. Технологическая схема атмосферно-вакуу / — нефть; // — газ; Я/ —головка стабилизации; /V, V, VI, VII — узкие бензинов 230-280 °С; X — фракция 280-350 °С; XI — фракция 350-500 °С; XII — гудрон
XIV — водяной пар.
чего поступает в рефлюксную емкость Е-1, из которой часть бен
зина возвращается насосом в К-1 в качестве орошения (флегмы),
а балансовое количество под собственным давлением поступает в
емкость Е-3.
j Нижний продукт К-1— частично отбензиненная нефть заби-
/ рается насосами Н-2 и Н-3 и направляется в трубчатую печь П-1.
^ Из печи выходят два потока нагретой до 360 °С нефти, один из ко-
j торых возвращается в колонну К-1, внося дополнительное количе-
-* ство теплоты, необходимой для ректификации.
.^Ч Второй поток нагретой полуотбензиненной нефти поступает
J5» в атмосферную колонну К-2, где разделяется на несколько фрак
ций. Температура'нефти на выходе из печи П-1 составляет 360 °С.
^ Для снижения температуры низа колонны и более полного из-
J влечения из мазута светлых нефтепродуктов ректификация в К-2 <. проводится в присутствии водяного пара. Пар подается в нижнюю "2 часть колонны в количестве 1,5—2% на остаток.
С верха колонны К-2 уходят пары бензиновой фракции с концом кипения 180°С, а также водяной пар. Пары поступают в воздушный и водяной конденсаторы-холодильники ХК-3 и ХК-4; после конденсации продукт попадает в емкость-водоотделитель Е-2. .Отстоявшийся от воды тяжелый бензин подается насосом в Е-3. Часть бензина из Е-2 возвращается в К-2 в качестве острого орошения. Из колонны К-2 выводятся также три боковых погона — фракции 180—230 °С, 230—280 °С, 280—350 °С. Эти погоны поступают первоначально в отпарные колонны К-3, К-4, К-5. В отпарных колоннах из боковых погонов в присутствии водяного пара удаляются легкие фракции. Освобожденные от легких фракций целевые продукты в жидком виде выводятся с установки, а пары легких фракций возвращаются в колонну К-2.
Фракция 180—230 °С перед выходом с установки проходит через теплообменник Т-7 и холодильник Х-1. Фракции 230—280°С и 280—350°С также охлаждаются в соответствующих теплообменниках и концевых холодильниках.
Для улучшения условий работы колонны К-2 и съема избыточной теплоты в колонне предусмотрен вывод двух циркулирующих орошений: верхнее (с 11-й тарелки) проходит через теплообменник Т-1 и возвращается в К-2 на 10-ю тарелку; нижнее (с 21-й тарелки) проходит через теплообменник Т-2 и возвращается на 20-ю тарелку.
Остаток из атмосферной колонны — мазут — насосом Н-4 подают в трубчатую печь П-3. Мазут, нагретый в печи до 410°С, поступает в вакуумную колонну К-6. В колонне поддерживается остаточное давление 6,6 кПа. Для снижения температуры низа и облегчения условий испарения из гудрона легких компонентов в низ К-6 вводят водяной пар.
С верха К-6 выводят водяные пары, газы разложения, воздух и некоторое количество нефтепродукта (дизельной фракции), которые поступают в конденсатор ХК-5. Несконденсировавшиеся газы отсасываются многоступенчатым эжектором А-1.
5*
131
|
|
А 4 |
со й . < 5 с |
|
ж
Дата добавления: 2018-04-04; просмотров: 362; Мы поможем в написании вашей работы! |
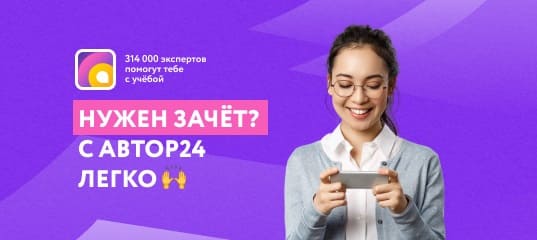
Мы поможем в написании ваших работ!