Развитие нефтеперерабатывающей промышленности в СССР. 19 страница
сводом; з — двухпоточнля двухкамерная печь с наклонным 1'нодом. 1 — горелки {форсунки); 2—радиаитпый змеевик; 3 — конвекционный змеевик; 4 — дымоход; 5 — перевальная стенка; 6 — панельные горелки.
30—60, при вакуумной перегонке мазута 25—35, при термическом крекинге 25—50, при каталитическом риформинге 30—35.
Коэффициентом полезного действия нечи называется отношение полезно используемой теплоты к общему количеству теплоты, выделенной при сгорании топлива. Перед конструкторами печей стоит задача добиться повышения к. п. д. печи. В печах установок первичной перегонки, строившихся до 1970 г., этот показатель не превышал 60—65%. На новых установках AT и АВТ используются печи с более высоким к. п. д. — 80% и выше.
На НПЗ широко распространены одно- и двухскатные трубчатые печи шатрового типа. Схематический разрез двухскатной печи приведен на рис. 25. Печь состоит из двух радиантных камер и одной конвекционной. Конвекционная камера отделена от радиантных стенками из огнеупорного кирпича. Эти стенки называются перевальными. Дымовые газы удаляются из печи через дымоход
141
(боров), который начинаетсй в нижней части конвекционной камеры, и дымовую трубу.
Трубы змеевика крепятся к стенкам радиантной камеры печи при помощи подвесок и кронштейнов из жаропрочной стали, а в конвекционной камере укладываются на специальные решетки. Между собой они соединяются сварными калачами или разъемными переходами-двойниками. В радиантной камере имеются две группы труб —нижняя (подовый экран) и верхняя (потолочный экран).
|
|
Шатровые печи, несмотря на их универсальность, простоту в эксплуатации, в настоящее время не сооружаются. Их основной
Рис. 25. Двухскатная трубчатая печь шатровсго типа:
/ — выходящим продукт; // — входящий продукт; /// — газы в дымоиую
трубу.
недостаток — низкие технико-экономические показатели. Коэффициент полезного действия этих печей не превышает 50—60%, "так как почти нигде не используется тепло дымовых газов. Эти печи работают с большим коэффициентом избытка воздуха, что также сказывается на к. п. д. печи. Шатровые печи требуют много места, для их сооружения расходуется большое количество легированной стали.
Недостатки печей шатрового типа устраняются в конструкциях новых печей. К печам нового типа относятся трубчатые печи с излучающими стенками из панельных горелок, печи объемно-настильного пламени, вертикально-факельные печи, разработанные институтом ВНИИнефтемаш, а также вертикальные трубчатые печи, сконструированные в институте Ленгипронефтехим.
Особенностью вертикальных печей является вертикальное расположение труб в радиантных змеевиках этих печей. Вертикальные трубчатые печи подразделяются на вертикальные цилиндрические и вертикальные секционные, Вертикальные цилиндрические печи
|
|
142
|
имеют тепловую производительность от 2 до 15 МВт, а вертикальные секционные от 12 до 150 МВт. Устройство вертикальной секционной печи показано на рис. 26. Печи этого типа состоят из ряда секций одинаковой теплопроизводительности и размеров, причем число секций зависит от теплопроизводительности печи.
Каждая секция состоит из радиантной и конвекционной камер, причем радиантные части всех секций печи объединяются в общий металлический сварной футерованный изнутри корпус.
Радиантная часть печи имеет в плане форму прямоугольника. В днище радиантных камер расположены форсунки. Чтобы улучшить обслуживание форсунок, печь приподнимается над землей на металлических стойках каркаса. Трубы змеевика располагаются внутри камеры, причем если печь состоит из одной секции, то все трубы змеевиков расположены у стен печи. Если в печи имеется несколько секций, то наряду с однорядными экранами появляются двухрядные, расположенные между топочными пространствами секций.
Рис. 2G.
|
труб- |
Вертикально-секционная чатая печь: |
I — каркас-кожух; 2 — футеровка; 3 —рлдмант- иая ча^ть змеевика; 4 — конвекционная часть змееппка; 5 — горелка. |
Сверху каждой радиантной камеры помещается конвекционная камера, которая также имеет прямоугольную форму, футерована легким жаростойким бетоном и содержит пакет горизонтальных ошипованных труб. Конвекдионная камера заканчивается сборником продуктов сгорания, имеющим форму усеченной пирамиды. Продукты сгорания затем уходят в дымовую трубу. Дымовые трубы могут быть сооружены для каждой секции отдельно или быть общими для нескольких секций.
из
В вертикально-секционных печах с дымовыми газами теряется большое количество тепла, которое следует утилизировать, используя, например, для получения водяного пара. Испарительные секции котлов-утилизаторов располагаются над конвекционным змеевиком в каждой конвекционной камере. Корпусом котла-утилизатора служит нижняя прямоугольная часть сборника продуктов сгорания.
Преимущества вертикальных трубчатых печей перед печами других типов заключаются в следующем:
1) уменьшение расхода легированного металла на подвески и опоры труб змеевика, поскольку число креплений уменьшено и они вынесены за пределы обогреваемой зоны;
|
|
2) значительное уменьшение габаритов и площади, занимаемой печами;
3) повышение к. п. д. до 80—85% за счет утилизации теплоты и некоторого уменьшения потерь ее через наружные стены;
4) значительное снижение расхода футеровочного материала, благодаря применению легкого жаростойкого бетона.
Ректификационные колонны.Классифицируются по технологическому назначению, давлению, способу осуществления контакта между паром и жидкостью, числу получаемых при разделении смесей продуктов. В зависимости от назначения ректификационные аппараты делятся на колонны атмосферной перегонки нефти, от-бензинивающие, вакуумной перегонки мазута, стабилизации,и т. д. В зависимости от давления — на атмосферные, вакуумные, работающие под давлением.
В качестве контактных устройств используются ректификационные тарелки и насадки. На большинстве технологических установок по переработке нефти применяются только тарельчатые колонны.
Существуют ректификационные тарелки различных типов — колпачковые (рис. 27), бесколпачковые, струйно-направленные и др.
Колпачковая тарелка представляет собой металлический диск, в котором имеется множество отверстий для прохода паров. По периметру отверстий закреплены бортики определенной высоты, называемые стаканами, благодаря которым на тарелке поддерживается определенный слой жидкости. Сверху стаканы накрываются колпачками. Между верхним срезом стакана и колпачком имеется зазор для прохода паров, поступающих с нижележащей тарелки. При работе колпачки погружены в слой жидкости, и вследствие этого образуется гидравлический затвор, через который барботи-руют пары.
Уровень жидкости на тарелках поддерживается сливными перегородками {сливными карманами), нижняя часть которых доходит до следующей тарелки. Избыток жидкости по сливным карманам спускается на нижележащую тарелку. Положение колпачков можно регулировать, изменяя размер зазора между колпачком и верхним срезом стакана. Очень важно, чтобы тарелки размещались в
144
колонне строго горизонтально и чтобы все колпачки были одинаково погружены в жидкость на тарелке. Если эти требования не выполнены, то в какой-либо части тарелки толщина слоя жидкости будет меньше. Через эту часть тарелки начнет проходить большее количество жидкости, и многие колпачки на остальной части тарелки перестанут работать.
Наиболее распространены колпачковые тарелки желобчатого типа, тарелки с S-образными элементами, с круглыми колпачками и тарелки клапанного типа.
t t t t t t \
|
t t \ \ |
1
Щ
mm
Vnzazzzzzzpz/
.V
Рис. 27. Схема работы колпачковой тарелки:
/—патрубок; 2—колпачок: 3 — диск тарелги; 4 — сливная труба: 5 —сливная перегородка; И — высота уровня жидкости в сливном стакане, h ~высота стакана, h л—высота подпора при сливе жидкости, I п — высота выступающей над тарелкой части сливной перегородки или труби.
Желобчатые тарелки имеют простую конструкцию и весьма легко монтируются. Схема тарелки приводится на рис. 28. Основной недостаток желобчатых тарелок заключается в малой площади барботажа (до 30% от площади тарелки), что способствует увеличению скорости паров и уносу флегмы.
В отличие от желобчатых тарелок н тарелках с S-образными элементами (рис. 29) жидкость, направляясь к сливному устройству, движется поперек колпачков, а сами колпачки представляют одно целое с желобом. Каждый S-образный элемент состоит из колпачковой и желобчатой части. При сборке их располагают таким образом, чтобы колпачковая часть одного элемента перекрывала желобчатую часть другого, образуя гидравлический затвор.
Тарелки из S-образных элементов предназначены для колонн, работающих при атмосферном или невысоком давлении, для них характерна устойчивая равномерная работа при изменении нагрузок. Производительность тарелок на 20% выше, чем желобчатых.
145
Еще более эффективны для колонн, работающих при переменных нагрузках по пару и" жидкости, а также для колонн, в которых требуется добиться повышенной четкости разделения, клапанные прямоточные тарелки. Основной элемент такой тарелки — клапан
Рис. 28. Колпачковая тарелка желобчатого типа:
/ — корпус колонны; 2 —глухие сегменты; 3 — карманы; 4, 7 —сливные перегородки; 5 —колпачок; в — желоб.
(рис. 30), который под действием паров приподнимается над полотном тарелки на различную высоту. В отличие от прочих колпач-ковых тарелок, работающих в статическом режиме, для клапанных тарелок характерен динамический, переменный режим работы.
Подвижные клапаны в зависимости от паровой нагрузки поднимаются или опускаются, регулируя площадь свободного сечения тарелки. Благодаря такой конструкции, в широком пределе нагрузок, определяемом возможной длиной хода клапана, скорость паров существенно не меняется.
146
Из бесколпачковых тарелок в последние годы нашли применение решетчатые тарелки провального типа и ситчатые тарелки с отбойными элементами.
|
Рис. 29. Тарелка с S-образными элементами:
/ — S-образкый элемент; 2 — плоский сегмент; 3 — кармаЕг,
4 — сливная перегородка; 5 — onopEian полоса; 6 — струб-
циЕ1а-скоба; 7—первый элемент; 8 — колпачок.
Основным показателем для тарелок с переливами является скорость паров в свободном сечении колонны. Скорость паров в колоннах установок первичной перегонки зависит от типа тарелки,
а 8
Клапан закрыт '///!>,■ <>/т Клапан полуоткрыт У//77/////А Клапан открыт |
Клапан открыт
Y//////////7Z |
|
/г |
VZZZ. |
;.■■:■.■"•'■•'/'.': J |
2
I Клс
(7-шшшшшШ Ст>'
У//////Ш////Л у;);/;;/>77777\ |
Клапан закрыт |
'Ш/////Л У/У7777?,
Рис. 30. Клапанные колпачки — прямоугольный (а) и круглый (б): /—клапан; 2— удерживающая скоба.
расстояния между тарелками, нагрузки тарелки по жидкости, физических свойств разделяемых продуктов и других факторов. Она составляет (в м/с): в атмосферной колонне 0,6—0,9, в отбензини-вающей 0,2—0,3, в стабилизаторе 0,15—0,2, в вакуумной 2—3.
Поскольку на установках первичной перегонки нефть требуется разделить на большое число фракций, на них широко применяются
147
сложные колонны. Сложными являются основная атмосферная колонна и колонна вакуумной перегонки мазута. Атмосферная Коломна состоит из 3—4 секций, и в ней отбирается 2—3 боковых погона — керосиновый, легкий и тяжелый дизельные. В вакуумных колоннах отбирается 1—3 боковых погона. Отбензннивающая и стабилизационная колонна относятся к простым колоннам. Характеристика ректификационных колонн установок прямой перегонки приводится ниже:
АВТ ABT
мощностью мощностью
2 млн. т/год 6 млн. т/год
Отбензинивающая колонна
Диаметр, мм............................................ 4200 5000
Число тарелок, шт.................................. 15 24
Тип тарелок............................................ ...... Желобчатые Клапанные
Скорость паров, м/с................................ .............. 0,231 0,266
Высота подпора на сливе, мм ... 26 40
Атмосферная колонна
Диаметр, мм............................................ 4200 5000/7000
Число тарелок, шт.................................. 43 43
Тип тарелок............................................. Желобчатые Клапанные
Скорость паров в верхнем сечении,
м/с........................................................ 0,34 0,96
Высота подпора на сливе, мм . . . 16 35
Вакуумная колонна
Диаметр, мм............................................ .... 5000/8000/6000 6400/9000
Число тарелок, шт.................................. ................ 12 18
Тип тарелок............................................ Желобчатые Клапанные
Скорость Паров, м/с............................... ................ — 2,1—3,5
Способы создания орошения. Чтобы обеспечить нормальное проведение процесса ректификации, в колонне необходимо создать поток орошения (флегмы). В промышленной практике применяются три основных способа создания орошения: с применением поверхностного парциального конденсатора; холодным, испаряющимся (острым) орошением; циркуляционным, неиспаряющимся орошением.
Схемы создания орошения приводятся на рис. 31. Парциальный конденсатор представляет собой трубчатый теплообменный аппарат, устанавливаемый непосредственно на колонне. В трубки аппарата подается вода или холодное сырье. Конденсат, образующийся в межтрубном пространстве, стекает обратно в колонну в виде флегмы.
При съеме тепла острым орошением на верх колонны подается насосом холодная жидкость, соответствующая по составу ректификату. Эта жидкость, контактируя на верхней тарелке с парами, поднимающимися с нижних тарелок, испаряется. Поднимающиеся снизу пары охлаждаются, частично конденсируются. Образовавшийся конденсат стекает на следующую тарелку в качестве орошения. Пары орошения и испарившегося на верхней тарелке продукта уходят в конденсатор-холодильник 3. После конденсации продукт
148
собирается в емкости 4, откуда ректификат отводится в качестве товарного продукта, а орошение вновь возвращается в колонну.
С помощью циркулирующего, неиспаряющегося орошения тепло отводится как из верхней части колонны, так и из промежуточных сечений. Схема съема тепла циркулирующим орошением следующая: жидкость забирается насосом 5 с какой-либо тарелки, прокачивается через холодильник или теплообменник 6 и возвращается в колонну на вышележащую тарелку.
Сравнивая различные методы создания орошения, следует отметить, что применение парциального конденсатора связано с большими неудобствами. При высокой производительности установок
А 5 в
|
ш
-W
я
п М
___ I w
^—г~"
£
S-5
Рис. 31. Схемы орошения ректификационных колонн с применением
парциального конденсатора (а), холодного (острого) орошения (б) и
циркулирующего орошения (в):
I — пары из колонны; // — орошение; /// — охлаждающий агент (вода, воздух, холодное сырье); IV — ректификат; / — колонна; 2 — парциальный конденсатор; 3 — конденсатор-холодильник; 4—ре-флюксная емкость; 5 — насос; 6 — теплообменник (холодильник).
размеры парциальных конденсаторов растут и становится трудно размещать их над колонной. Кроме того, возникают сложности в регулировании температуры колонны, так как быстро изменить количество подаваемого из парциального конденсатора орошения невозможно.
При' отводе тепла острым орошением конденсатор можно размещать на любой высоте, сооружение и эксплуатация конденсаторов в этом случае много проще. Однако применение острого орошения требует установки специального насоса для подачи орошения и затраты электроэнергии.
На современных установках по перегонке нефти используются комбинированные схемы орошения. Так, в сложных атмосферных колоннах сочетается острое и циркулирующее орошение. В сложных колоннах масса ректификата при переходе от первой (нижней) простой колонны (секции) к верхней сокращается, а масса флегмы (если в колонну подается только острое орошение) должна в той же последовательности увеличиваться. Дело в том, что через секции, расположенные выше, должно проходить такое количество
Дата добавления: 2018-04-04; просмотров: 377; Мы поможем в написании вашей работы! |
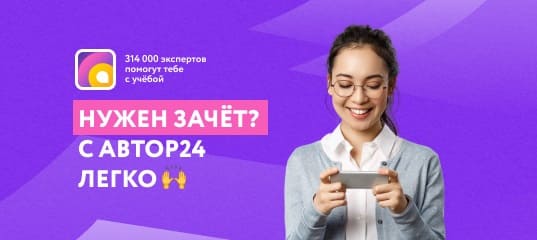
Мы поможем в написании ваших работ!