Развитие нефтеперерабатывающей промышленности в СССР. 16 страница
Основная аппаратура установок ЭЛОУ. Главным аппаратом установки является электродегидратор — емкость, снабженная электродами, к которым подводится переменный ток высокого напряжения. В эксплуатации на промысловых и заводских установках ЭЛОУ находятся электродегидраторы различных конструкций: вертикальные, шаровые и горизонтальные.
Вертикальный электродегидратор (рис. 10) представляет собой цилиндрический сосуд диаметром 3 м, высотой 5 м и объемом
115
30 м3. Внутри находятся электроды — металлические пластины, подвешенные на фарфоровых изоляторах. Напряжение подается к электродам от двух повышающих трансформаторов мощностью по 5 кВ-А. Напряжение между электродами от 15 до 33 кВ.
Сырье вводится в электродегидратор через вертикальную, вмонтированную по оси аппарата трубу, которая на половине высоты дегидратора заканчивается распределительной головкой. Головка устроена так, что через ее узкую кольцевую щель эмульсия нефти и воды вводится в виде тонкой веерообразной горизонтальной струи. Обработанная нефть выводится в центре верхнего
Рис. 12. Горизонтальный электродегидратор типа ЭГ.
днища электродегидратора, а отстоявшаяся вода — через нижнее днище.
Недостатком вертикальных электродегидраторов, приведшим к их вытеснению более современными конструкциями, является низкая производительность, недостаточно высокая температура обес-соливания. Из-за низкой производительности на установках ЭЛОУ приходилось соединять лараллельно 6—12 аппаратов. На мощных электрообессоливающих установках, построенных в 1955—1970 гг., применяются шаровые электродегидраторы вместимостью 600 м3 с диаметром 10,5 м. Производительность такого дегидратора (рис. 11) равна 300—500 м3/ч. Принцип его действия тот же, что и вертикального аппарата, но вместо одного стояка с распределительной головкой для ввода сырья и одной пары электродов в шаровом электродегидраторе их по три.
|
|
Строящиеся в настоящее время установки обессоливания оснащаются горизонтальными электродегцдраторами. Конструкция этих аппаратов позволяет проводить обессоливание при давлении до 1,8 МПа и температуре до 160°С. Горизонтальные электродегидраторы (рис. 12) имеют диаметр 3—3,4 м и объем 80 и 160 м3. Повышение расчетного давления и температуры позволяет проводить глубокое обессоливание трудно обессоливаемых нефтей.
Электроды в горизонтальном электродегидраторе расположены почти посредине аппарата. Они подвешены горизонтально друг над другом. Расстояние между ними составляет 25—40 см.
116
Ввод сырья в горизонтальный электродегидратор осуществляется через расположенный вдоль аппарата горизонтальный маточник. Поступая в аппарат, нефть попадает в слой отстоявшейся воды, а затем — в зону под электродами, в межэлектродное пространство, и, наконец, в зону над электродами. В верхней части дегидратора располагаются выкидные коллекторы обработанной нефти. Достоинством этой конструкции является большой путь движения нефти и время ее пребывания в аппарате, так как ввод сырья расположен значительно ниже, чем в других электродегид-раторах. При этом значительно улучшаются условия отстаивания воды.
|
|
Кроме того, в горизонтальном электродегидраторе крупные частицы воды выпадают из нефти еще до попадания в зону сильного электрического поля, расположенную в межэлектродном пространстве. Поэтому в нем можно обрабатывать нефть с большим содержанием воды, не опасаясь чрезмерного увеличения силы тока между электродами.
Режим обессоливания. Температура и давление процесса обес-соливания во многом обусловливаются конструкцией аппарата. Большое значение имеют свойства обессоливаемой нефти. Легкие нефти с низкой вязкостью, не образующие устойчивых эмульсий, обессоливаются при 80—100°С, но для большинства нефтей, таких, например, как ромашкинская, арланская, мангышлакская, оптимальной считается температура 120—130 °С. Следует иметь в виду, что повышение температуры обессоливания увеличивает электрическую проводимость и силу тока, усложняет условия работы изоляторов.
|
|
Важное значение имеет равномерная подача в нефть деэмуль-гатора. Расход деэмульгаторов на НПЗ колеблется от 10 до 30 г/т и зависит от устойчивости образующейся эмульсии воды и нефти. Промышленность выпускает деэмульгаторы в виде растворов в органических растворителях, из которых перед применением приготавливают 1—5% водные растворы.
Иногда в нефть также подается щелочь, которая необходима для подавления коррозии в случае содержания в нефти свободного сероводорода, а также для нейтрализации неорганических кислот, попавших в нефть при кислотной обработке скважин. В качестве промывной воды применяется свежая речная вода, паровой конденсат и вода из систем оборотного водоснабжения. Перед подачей в нефть воду подогревают.
Техника безопасности. При обслуживании электрообессоливаю-щих установок персонал имеет дело с аппаратами, в которых поддерживается высокое напряжение электрического тока. Это обстоятельство создает повышенную опасность установок ЭЛОУ. Верхняя площадка на электродегидраторах, где расположены трансформаторы и реактивные катушки, имеет сетчатое и решетчатое ограждение. На лестнице, служащей для подъема на электродегидратор, предусматривается блокировочное устройство, отключающее главную цепь электропитания при открытии дверцы
|
|
117
лестницы. Устройства для отключения напряжения при понижении уровня нефти в электродегидраторс имеет каждый из этих аппаратов.
Ремонт оборудования, установленного на верхней площадке и внутри электродегидратора, можно проводить только после снятия напряжения, тщательного вентилирования помещения дегидрато-ров (если они размещены в здании).
При возникновении пожара на электрооборудовании напряжение должно быть немедленно снято.
Экономические показатели обезвоживания и обессоливания нефти.Содержание воды в нефти при ее подготовке на промыслах снижается с 10—50% до 0,5—1,5%, степень обессоливания зависит от с емы подготовки нефти на промысле. В нефти, поступающей на ЭЛОУ, содержится от 40—60 до 3000 мг/л солей. При обес-соливании на заводских ЭЛОУ содержание солей снижается до 3—20 мг/л, а воды — до 0,1%.
Глубокое обессоливание нефти позволяет значительно продлить безостановочный пробег установок переработки нефти, снизить расход металла на замену оборудования, уменьшить энергетические расходы. Экономия от переработки нефти с содержанием 5 мг/л солей по сравнению с нефтью, содержащей 20 мг/л солей, составляет около 40 млн. руб. на каждые 100 млн. т. перерабатываемой нефти. Необходимо стремиться к тому, чтобы содержание солей в обессоленной нефти перед подачей на первичную перегонку не превышало 2—3 мг/л. Однако добиться этого можно, если на заводы будет поступать нефть, содержащая не более 40— 60 мг/л солей, т. е. на промыслах будет проводиться не только обезвоживание, но и частичное обессоливание нефти.
На промысловых обессоливающих установках из нефти удаляются наиболее крупные и легкоразрушаемые глобулы эмульсий. При перекачках и хранении нефти водо-нефтяная эмульсия дополнительно стабилизируется и становится трудноразру-шаемой, что усложняет решение проблемы обессоливания нефти на НПЗ.
При обессоливании на промыслах гораздо проще, чем на НПЗ, решается задача очистки сточных вод обессоливания. Воду после несложной и недорогой подготовки можно направить обратно в скважины на самом промысле. На заводе же для очистки воды приходится сооружать специальные очистные сооружения, так как эта вода должна сбрасываться в водоем. Кроме того, следует учитывать, что при транспортировке необессоленной и необезвожен-ной нефти затрачиваются большие средства на перевозку балласта (воды и солей).
Значительным резервом снижения себестоимости подготовки нефти к переработке на НПЗ является объединение (комбинирование) установок обессоливания с первичной перегонкой нефти. При комбинировании теплота отходящих продуктов перегонной установки используется для подогрева нефти перед обессолива-нием.
118
§ 23. СОРТИРОВКА И СМЕШЕНИЕ НЕФТЕИ
Нефти различных месторождений отличаются по своему химическому составу и товарным свойствам. Из некоторых нефтей можно получить без дополнительной обработки высокооктановый бензин; другие, в частности, мангышлакские, содержат в большом количестве парафиновые углеводороды, являющиеся ценным нефтехимическим сырьем.
Схема переработки нефти на заводе, выбор тех или иных технологических процессов зависят от качества нефти. Например, при переработке сернистых нефтей в состав завода включаются установки по очистке продукции от серы, при переработке парафини-стых нефтей — установки депарафинизации.
Но вводить раздельную перекачку нефтей в зависимости от их сортов нерационально, так как это усложнит нефтепромысловое хозяйство, увеличит размеры резервуарного парка, приведет к созданию сложной системы нефтепроводов. Поэтому на практике нефти смешиваются в районах добычи и направляются на переработку в виде смеси.
Смешивать нефти рекомендуется после проведения комплекса исследовательских работ. Иначе может произойти обесценивание получаемой продукции. Например, если смешать сернистую и малосернистую нефть, то не удастся получить малосернистый нефтяной кокс, являющийся особо ценным и дефицитным продуктом.
В ближайшее время на переработку начнут поступать искусственные сорта нефтей с заданным качеством, приготавливаемые в соответствии с определенной рецептурой. Смеси будут готовить таким образом, чтобы добавлением более высококачественных сортов компенсировать недостатки менее качественных нефтей. Например, смешением высокосернистых и сернистых нефтей Вол-го-Уральского района и Западной Сибири с бессернистой, но высо-копарафинистой нефтью Мангышлакского полуострова будут получать смесь, близкую по качеству к татарской нефти типа ромашкинскон. Благодаря такому приготовлению искусственной нефтесмеси, перерабатывающие предприятия будут получать стабильное сырье, заранее знать, какого выхода товарных продуктов следует ожидать.
Глава V ПЕРВИЧНАЯ ПЕРЕГОНКА НЕФТИ
§ 24. НАЗНАЧЕНИЕ ПЕРВИЧНОЙ ПЕРЕГОНКИ
Нефть, как уже было указано, представляет собой чрезвычайно сложную смесь взаимно растворимых органических веществ. Разделить ее нацело на составляющие компоненты практически невозможно, но этого для промышленного применения нефтепродуктов и не требуется. На практике нефть делят на фракции, отличающиеся по пределам выкипания. Это разделение проводится на установках первичной перегонки нефти с применением процессов дистилляции и ректификации.
Полученные фракции служат сырьем для дальнейшей переработки или используются как товарные продукты. Первичная перегонка — первый технологический процесс переработки нефти. Установки первичной перегонки имеются на каждом НПЗ.
Дистилляция. Дистилляцией или перегонкой называется процесс разделения смеси взаимно растворимых жидкостей на фракции, которые отличаются по температурам кипения как друг от друга, так и от исходной смеси. При перегонке смесь нагревается до кипения и частично испаряется. Получаемые пары отбираются и конденсируются. Перегонкой получают дистиллят и остаток, которые по составу отличаются от исходной смеси.
Перегонка может быть осуществлена однократным, многократным или постепенным испарением.
При однократном испарении в течение всего времени нагревания смеси продуктов до определенной конечной температуры образующиеся пары не выводятся из системы и остаются в контакте с жидкостью. После того как сообщение тепла заканчивается, вся парожидкостная смесь выводится в сепаратор. Здесь образовавшиеся пары в один прием (однократно) отделяются от жидкости.
При многократном осуществлении процесса разделение фаз проводится в несколько приемов. Многократное испарение состоит из повторяющегося несколько раз процесса однократного испарения. Первоначально происходит отделение паров от жидкости, а затем—на второй ступени — жидкая фаза, оставшаяся при отделении паров в первой ступени, вновь испаряется и т. д.
При постепенном испарении образующиеся пары по мере их образования непрерывно выводятся из перегонного аппарата. Постепенное испарение примеяяется при лабораторной перегонке
120
нефти из колбы, а в промышленной практике прежде использовалось при перегонке на кубовых установках.
Процесс однократного испарения обладает преимуществами перед постепенным испарением. При однократном испарении низ-кокипящие фракции, перейдя в пары, остаются в аппарате, снижают парциальное давление испаряющихся высококипящих фракций, что дает возможность вести перегонку при более низких температурах.
При постепенном испарении, наоборот, легкие фракции отгоняют сначала, а тяжелые — в конце. Поэтому легкие фракции, которые превратились в пары и были выведены из аппарата, не влияют на температуру кипения тяжелых фракций. Благодаря влиянию легких фракций, применяя однократное испарение, можно снизить конец кипения перегоняемого сырья на 50—100 °С по сравнению с постепенным испарением.
На современных установках перегонка нефти проводится с применением однократного испарения.
Как известно, в составе нефти имеются углеводороды, кипящие при атмосферном давлении в интервале температур 400— 500СС и выше в то время как термическая стабильность углеводородов сохраняется только до 380—400 "С. При более высокой температуре начинается процесс разложения — крекинга углеводородов, причем наиболее высококипящие углеводороды нефти обладают наименьшей термической стабильностью.
Для того чтобы избежать разложения углеводородов, надо понизить температуру их кипения. Это достигается перегонкой нефти под вакуумом. Нефтяная фракция, выкипающая при атмосферном давлении в интервале температур 450—500°С, может быть перегнана под вакуумом (остаточное давление 3—5 кПа) при 200—250 °С.
Для понижения температуры кипения в практике нефтепереработки применяют также перегонку с водяным паром, который снижает парциальное давление углеводородов.
Ректификация.При однократном испарении взаимно растворимых жидкостей и последующей конденсации паров получают две фракции: легкую, в которой содержится больше низкокипящих фракций, и тяжелую, в которой содержится меньше низкокипящих фракций, чем в исходном сырье. Следовательно, при перегонке происходит обогащение одной фазы низкокипящими, а другой — высококипящими компонентами. Однако достичь требуемого разделения компонентов нефти и получить конечные продукты, кипящие в заданных температурных интервалах, с помощью перегонки нельзя. Поэтому после однократного испарения нефтяные пары подвергаются ректификации.
Ректификацией называется диффузионный процесс разделения жидкостей, различающихся по температурам кипения, за счет про-тивоточного многократного контактирования паровижидкости.
Контактирование паров и жидкости осуществляется в вертикальных цилиндрических аппаратах—ректификационных колоннах,
121
снабженных специальными устройствами — ректификационными тарелками или насадкой, — позволяющими создать тесный контакт между паром, поднимающимся вверх по колонне, и жидкостью, стекающей вниз (рис. 13).
|
В среднюю часть в виде пара, жидкости или парожидкостной смеси подается сырье, которое необходимо разделить на две части — высококипящую и низкокипящую. Зона, в которую подается сырье, носит название эвапорационной, так как в ней происходит эвапорация — однократное испарение нагретой в печи или теплообменнике смеси на паровую и жидкую фазы. В некоторых случаях эвапораци-онная зона отделена от колонны, и эвапорация производится в самостоятельном аппарате. Однако у большинства колонн, в частности на установках первичной перегонки, однократное испарение и ректификация совмещаются.
В работающей ректификационной колонне через каждую тарелку проходят четыре потока: 1) жидкость — флегма, стекающая с вышележащей тарелки; 2) пары, поступающие с нижележащей тарелки; 3) жидкость — флегма, уходящая на нижележащую тарелку; 4) пары, поднимающиеся на вышележащую тарелку.
Рис. 13. Схема ректификационной колонны: / — холодное орошение; II — ректификат; III — циркулирующая горячая струя; IV — остаток; V—сырье. |
Пары и жидкость, поступающие на тарелку, не находятся в состоянии равновесия, однако, вступая в соприкосновение, стремятся к этому состоянию. Жидкий поток с вышележащей тарелки поступает в зону более высокой температуры, и поэтому из него испаряется некоторое количество низкокипящего компонента, в результате чего концентрация последнего в жидкости уменьшается. С другой стороны, паровой поток, поступающий с нижележащей тарелки, попадает в зону более низкой температуры и часть высококипящего продукта из этого потока конденсируется, переходя в жидкость. Концентрация высококипящего компонента в парах таким образом понижается, а низкокипящего — повышается. Фракционный состав паров и жидкости по высоте колонны непрерывно изменяется.
Часть ректификационной колонны, которая расположена выше ввода сырья, называется концентрационной, а ниже — отгонной. В обеих частях колонны происходит один и тот же процесс ректификации. С верха концентрационной части в паровой фазе выводится целевой продукт необходимой чистоты — ректификат, а с низа — жидкость, еще в заметной степени обогащенная низкоки-пящим компонентом. В отгонной части из этой жидкости окончательно отпаривается низкокипящий компонент. В виде жидкости
122
с низа этой части колонны выводится второй целевой компонент— остаток.
Для нормальной работы ректификационной колонны необходимо, чтобы с верха колонны на нижележащие тарелки непрерывно стекала жидкость (флегма). Поэтому часть готового продукта (ректификата) после конденсации возвращается на верхнюю тарелку колонны в виде так называемого орошения. С другой стороны, для нормальной работы колонны необходимо, чтобы с низа колонны вверх непрерывно подымались пары. Чтобы создать в колонне паровой поток, часть уходящего из колонны остатка подогревается, испаряется и возвращается обратно в колонну.
На рис. 13 изображена схема так называемой простой колонны, состоящей из концентрационной и отгонной частей и имеющей два вывода продуктов — с верха и низа. Существуют колонны, в которых имеется только концентрационная часть, когда сырье вводится под нижнюю тарелку колонны, или только отгонная, когда сырье подается на верхнюю тарелку.
*-vr |
Рис. 14. Схема сложной ректификационной колонны с выносными отгонными секциями: / — сирье; // — ректификат: ///, IV, V — боковые погоны; VI— остат< к; VII — водяной пар. |
' На современных установках по переработке нефти наряду с простыми колоннами широкое распространение получили сложные колонны, в которых как бы совмещается несколько простых колонн (рис. 14). Сырье в таких колоннах поступает в среднюю часть одной из секций (см. рис. 14, секция /) и разделяется на жидкую и паровую фазы.
Дата добавления: 2018-04-04; просмотров: 406; Мы поможем в написании вашей работы! |
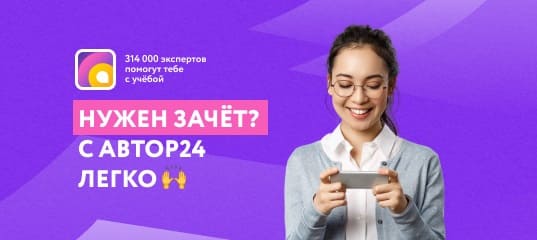
Мы поможем в написании ваших работ!