Сравнительные данные по крекингу на шариковых и пылевидных
Катализаторах
Показатели
Температура, °С....................................................
Кратность циркуляции катализатора, кг/кг . Выход продуктов, % (масс.)
газ (включая С4)............................................
в том числе:
изобутилен ..........................................
бутилены ...............................................
бензин (фракция С5 — 195 °С)....................
легкий газойль (фракция 195 —350 °С)
тяжелый газойль (фракция выше 350 °С)
кокс .........................................................
потери . ................................................
Катализатор цеокар-2
шариковый | пылевидный |
480 | 490 |
2,5 | 7,0 |
20,90 | 19,00 |
«5.28 | 6,04 |
2,68 | 3,16 |
47,2 | 47,1 |
21,1 | 24,4 |
4,7 | 4,2 |
5,1 | 4,3 |
1,0 | 1,0 |
229
Бензин имеет плотность 0,72—0,77, октановое число по исследовательскому методу от 87 до 91. По химическому составу бензин каталитического крекинга отличается от прямогонных бензинов и бензинов термических процессов. В нем содержится 9— 10% (масс.) непредельных углеводородов и от 20 до 40% (масс.) ароматических углеводородов. Непредельные и парафиновые углеводороды не менее, чем на две трети состоят из углеводородов изомерного строения.
Легкий газойль (фракция 195—350°С) имеет плотность 0,89—0,94 и состоит на 40—80% из ароматических соединений. Цетановое число колеблется от 45 до 24. Легкий газойль с высоким цетановым числом используется как компонент дизельного топлива, с низким цетановым числом — как разбавитель мазута. И бензин, и легкий газойль, полученные из сернистого сырья, нуждаются в очистке от серы.
|
|
Тяжелый газойль (фракция выше 350°С) — остаточный жидкий продукт каталитического крекинга — используется как компонент топочного мазута или в качестве сырья установок коксования. Содержание серы в нем выше, чем в исходном сырье.
Высокое содержание ароматических углеводородов полициклического строения (40—60%) делает газойли каталитического крекинга ценным источником получения индивидуальных ароматических углеводородов (нафталина, фенантрена), одновременно фракцию 280—420 °С применяют для выделения из нее высокоаро-матизированного концентрата — сырья для производства сажи. Для этой цели применяют селективный растворитель — фурфурол (см. § 67, § 69), разделяя фракцию 280—420 °С на деароматизиро-ванный рафинат, направляемый в дизельное топливо и экстракт, который и является сырьем для производства сажи.
§ 47. УСТАНОВКА КАТАЛИТИЧЕСКОГО КРЕКИНГА С ШАРИКОВЫМ КАТАЛИЗАТОРОМ
Установки каталитического крекинга с алюмосиликатным катализатором можно разделить на три типа:
1) со стационарным слоем таблетированного катализатора и реакторами периодического действия;
2) с плотным слоем циркулирующего шарикового катализатора, реактором и регенератором непрерывного действия;
|
|
3) с кипящим слоем циркулирующего микросферического или пылевидного катализатора, реактором и регенератором непрерывного действия.
Установка первого типа предназначена для периодического процесса. В ней имеется несколько реакторов, в каждом из которых за 30 мин происходит весь рабочий цикл: реакция крекинга, удаление нефтяных паров, регенерация катализатора, удаление воздуха и продуктов сгорания.
Установки каталитического крекинга со стационарным катализатором не получили большого распространения. Установки с дви-
230
жущимся катализатором, наоборот, имеются повсеместно. Вначале
был разработан процесс с шариковым катализатором, но в настоя
щее время гораздо шире применяют более прогрессивный процесс
каталитического крекинга с кипящим слоем пылевидного или ми
кросферического катализатора. i
Технологическая схема. Технологическая схема установки ката-литического крекинга с движущимся шариковым катализатором приведена на рис. 51. Установка с плотным слоем циркулирующего шарикового катализатора имеет два основных аппарата: реактор для непрерывного каталитического крекирования сырья и регенератор для непрерывного удаления кокса с поверхности катализатора.
|
|
Катализатор в виде шариков 0 3—5 мм пересыпается из бункера-сепаратора С-2 пневмоподъемника в бункер реактора Р-1 и равномерно проходит плотным слоем реакционную зону, зону отделения продуктов крекинга и зону отпарки. После этого катализатор выводится из реактора, поступает в загрузочное устройство пневмоподъемника А-2 и по стояку поднимается дымовыми газами в бункер-сепаратор С-3. Здесь дымовые газы отделяются и выбрасываются в атмосферу, а катализатор пересыпается в бункер регенератора Р-2. Катализатор проходит через секции, регенератора сверху вниз. В каждую секцию подается воздух для выжига кокса. Секции регенератора снабжены змеевиками для отвода теплоты регенерации за счет образования водяного пара. Регенерированный катализатор ссыпается в загрузочное устройство пневмоподъемника А-1 и поднимается по катализаторопроводу в бункер-сепаратор С-2. Катализаторная крошка отвеивается в сепараторе С-4. Воздух в регенератор и транспортирующий дымовой газ в пневмо-подъемник подаются при помощи воздуходувок и печей под. давлением (на схеме показаны только одна печь П-2 и одна воздуходувка ПК-2). Пар, получаемый в регенераторе, поступает в паросборник С-5, а далее расходуется на нужды установки.
|
|
Сырье подается насосом Н-1 через теплообменники Т-1, Т-2 в печь П-1, где нагревается до температуры реакции и испаряется. Пары сырья поступают в реакционную зону реактора Р-1, где контактируют с катализатором, перемещаясь сверху вниз. Пары продуктов крекинга и водяные пары, подаваемые в реактордля отпарки катализатора, выводятся из реактора через специальное устройство и направляются в нижнюю часть ректификационной колонны К-1-
С верха К-1 уходят пары бензина, водяные пары и жирный газ. Эта смесь после конденсации и охлаждения в конденсаторе-холодильнике ХК-1 разделяется в сепараторе С-1 на бензин, воду и жирный газ. Газ при помощи компрессора ПК-1 выводится на установку газофракционирования, бензин частично подается насосом Н-6 на орошение колонны К-1, балансовое количество бензина направляется на установку стабилизации. Легкий газойль (фракция 195—350 °С) поступает из колонны К-1 в отпарную колонну К-2, где отпаривается водяным паром, после чего через холодильник
231
|
L---- 1-|---------- !Ы_I—J h-s |
УК-1
Рис. 51. Техкологическая схема установки каталитического кре / — сырье; II- жирный газ; III — бензин; /V —фракция 195-350 °С; V —ф
мовые газы; IX — водяно
Х-1 выводится с установки. Тяжелый газойль (фракция выше350 °С) откачивается с низа колонны К-1 насосом Н-4 и после охлаждения в теплообменнике Т-2 и холодильнике Х-2 также выводится с установки.
мж, |
Тепловой режим в колонне К-1 поддерживается с помощью жидкостного орошения, которое циркулирует по замкнутому контуру: колонна К-1 — насос Н-5 — теплообменник Т-1 — колонна К-1- В результате из колонны выводится избыточное тепло. В качестве рециркулята крекинга применяется фракция промежуточного состава, которая выводится из колонны К-1 на 4—■ 5 тарелок ниже, чем легкий газойль, и подкачивается насосом Н-3 к свежему сырью перед печыо П-1.
Аппаратура.Реактор отечественной установки каталитического крекинга производительностью 800 т/сут по свежему сырью представляет собой цилиндрический аппарат из углеродистой стали с внутренней об- 1 \А кладкой из легированной стали диаметром около 4 м и объемом реакционной зоны 30-50 м3 (рис. 52). Днища реактора эллиптические. В центре верхнего днища имеется штуцер для подачи катализатора из бункера, смонтированного над реактором. Высота реактора с бункером 41 м. Штуцер соединяется с верхним распределительным устройством, которое посредством переточных труб равномерно распределяет катализатор по всему сечению реактора.
Рис. 52. Реактор установки каталитического крекинга с шариковым катализатором: / — днище реактора; 2 — шту |
В верхнюю часть реактора через штуце
ры вводятся пары сырья. Они равномерно
контактируют с катализатором, двигаясь
сверху вниз через реакционную зону. Под
реакционной зоной находится сепарацион-
чое устройство для вывода продуктов реак
ции— гирлянда патрубков с прорезями, за
щищенными колпачками от попадания ката
лизатора. Все патрубки нижним открытым
концом соединяются со сборной камерой,
из которой через штуцеры пары продукта
удаляются из реактора. Ниже имеется зона
отпарки адсорбированных на катализа
торе ПарОВ уГЛеВОДОрОДОВ ВОДЯНЫМ ПарОМ, тализатора.
подаваемым через специальный штуцер. Закоксованный катализатор выводится из реактора через выравниватель потока.
233
Регенератор — аппарат квадратного сечения 3X3 м, высотой 27 м, выполнен из углеродистой стали, с внутренней обмуровкой огнеупорным кирпичом. Регенератор имеет 8 зон, в каждой зоне находятся устройства для подвода воздуха, вывода дымовых газов и змеевики для отвода теплоты. В змеевиках циркулирует вода, которая частично превращается в пар. Все змеевики соединены с общим котлом-утилизатором. Максимальная температура
:\" |
III |
\£ |
/, |
выжига 720°С наблюдается в средней части аппарата. На входе и выходе катализатора, так же как и в реакторе, имеются распределитель и выравниватель потока. Производительность регенератора характеризуется величиной коксосъема в кг/(ч-м3) — количеством кокса, выжигаемого в единицу времени на единицу реакционного объема. Для установок с шариковым катализатором эта величина равна 12—14 кг/(ч-м3).
II |
|
Рис. 53. Дозатор пневмо-подъсмника: / — первичный воздух; // — вторичный воздух; /// — катализатор; /—корпус; 2— стояк пнепмо-подъемника; 3 — штуцер для ввода катализатора; 4 — направляющая; 5—штуцер для подвода воздуха. |
Из реактора в регенератор катализатор перемещается при помощи дымового газа, а из регенератора в реактор — при помощи горячего воздуха. Нижняя часть пневмо-подъемника (рис. 53), называемая дозатором, служит для попадания катализатора в поток газа. Из дозатора поток газа с катализатором поднимается по стояку, верхняя часть которого входит в бункер-сепаратор. Резкое увеличение поперечного сечения ведет к выпаданию частиц катализатора из потока. Из бункера-сепаратора воздух или дымовой газ выбрасывается в атмосферу, а катализатор по катализатрропроиоду ссыпается в бункер соответственно реактора или регенератора. Скорость газовой струи с катализатором 14—20 м/с. Кроме того, в систему пневмоподъема входят воздуходувки и топки, которые служат для подогрева воздуха и получения дымового газа посредством сжигания топлива под давлением.
Контроль и регулирование процесса. При установившемся режиме на определенном виде сырья необходимо контролировать и поддерживать постоянными целый ряд технологических параметров: расход сырья на установку, температуру в реакторе и на выходе сырья из печи, степень закоксованности катализатора и др. Температура на выходе паров сырья из печи регулируется подачей топлива в печь, температура в реакторе и степень закоксованности катализатора — кратностью циркуляции катализатора, температура выжига кокса в каждой секции регенератора — подачей воды в змеевики секций и подачей воздуха в каждую секцию. Важное значение имеет контроль уровня катализатора в бункерах
т
реактора, -регенератора и пневмотранспорта, который основан на измерении диэлектрической постоянной катализатора.
гл |
Пуск установки.Пуск реакторного блока начинают с горячей циркуляции катализатора. Разогрев катализатора ведут постепенно во избежание его растрескивания. Одновременно выводят на горячую циркуляцию погоноразде-лительную часть, после чего принимают па установку сырье. Далее реактор постепенно включается на поток паров сырья из печи, и уста-
Рис. 54. Узел ввода тяжелого сырья;
/ — корпус реактора; 2 —напорный стояк; Л —трубопровод для сырья; 4 — выравнивающий катализаторопровод; 5 — диффузор; 6 — тяги; 7 —отбойная тарелка.
Рис. 55. Технологическая схема установки с движущимся шариковым катализатором после реконструкции:
/--сырье; // — водяной пар; /// —воздух; IV — дымовые газы; V —продукты реакции; / — совмещенный реактор-регенератор (реактор над регенератором); 2 —пневмотранспорт однократного подъема.
новка начинает работать в соответствии с технологическим регламентом.
Техника безопасности.Для установки каталитического крекинга наиболее серьезными авариями являются аварии реакторного блока и пневмотранспорта. В случае отключения электроэнергии остановится циркуляция катализатора и не будет подачи воздуха в регенератор. В связи с этим необходимо немедленно прекратить подачу сырья в реактор. С прекращением подачи воды на охлаждение змеевиков регенератора повысится температура в секциях регенератора. В этом случае следует прекратить подачу воздуха в регенератор, в змеевики пустить водяной пар, снизить
235
производительность установки по сырью. Прекращение подачи водяного пара приведет к прекращению отпарки паров продукта с катализатора. Пары углеводородов, попадая с катализатором в катализаторопровод, могут вызвать пожар. В этом-случае необходимо остановить установку.
Реконструкция установки. Впоследние годы установки с движущимся шариковым катализатором, спроектированные и построенные для аморфного алюмосиликатного катализатора, переведены на значительно более активные и селективные цеолитсо-держащие катализаторы, на которых, во-первых, получается значительно больше бензина, во-вторых, кокса. Если установки не реконструировать, то их приходится эксплуатировать в более мягком режиме или при сокращенной производительности. Для полного использования возможностей, заложенных в цеолитсодержа-щих катализаторах, осуществляется несколько вариантов реконструкции установок. Например, в одном варианте реконструирован ввод тяжелого сырья (рис. 54); сокращен объем реакционной зоны до 30—40 м3; увеличен на 2—3 секции регенератор; увеличена охлаждающая поверхность конденсаторов верхнего продукта ректификационной колонны.
На рис. 55 приводится технологическая схема еще одного варианта реконструкции, позволившая поднять производительность пневмотранспорта пример'но в четыре раза, а производительность установки в целом — в полтора раза.
§ 48. УСТАНОВИЛ КАТАЛИТИЧЕСКОГО КРЕКИНГА С ПЫЛЕВИДНЫМ КАТАЛИЗАТОРОМ
Установки каталитического крекинга в кипящем слое эксплуатируются с начала 1940-х гг. Как и на установках с шариковым катализатором, реакция крекинга осуществляется в реакторе, а выжиг кокса—в регенераторе. Отличительная особенность установок— применение пылевидного или микросферического катализатора, способ его транспортирования и наличие кипящего слоя в реакторе и регенераторе. Катализатор изготовляют в виде мел- _ ких шариков (20—80 мкм) или частиц неправильной формы размером 10—120 мкм.
В последнем случае катализатор получил название пылевидного. Для установок с кипящим слоем используют то же сырье, что и для установок с движущимся шариковым катализатором. Качество получаемых продуктов соответствует качеству продуктов сустановок с движущимся слоем катализатора.
Технологическая схема.Технологическая схема установки каталитического крекинга с кипящим слоем катализатора приведена на рис. 56.
Сырье насосом Н-1 через теплообменники Т-1, Т-2, Т-3, Т-4 подается в печь П-1. Нагретое сырье смешивается с циркулирующим газойлем, поступающим с низа ректификационной колонны. Смесь сырья и рециркулята подается вподъемный стояк катализаторо-
226
провода, по которому катализатор, сырье и рециркулят поднимаются в реактор Р-1. Процесс каталитического крекирования начинается еще в стояке и заканчивается в кипящем слое реактора.
Пары продуктов реакции и водяной пар, подаваемый в отпар-ную зону реактора, уходят через верхний штуцер реактора и поступают в нижнюю часть ректификационной колонны К-1. С верха колонны К-1 газ, пары бензина и водяные пары поступают в конденсатор-холодильник ХК-1, а оттуда после конденсации — в сепаратор С-1, где разделяются на водяной слой, бензиновый слой и
Рис. 56. Технологическая схема установки <: кипящим слоем микросферического катализатора:
/ — сырье; // —катализатор; /// — бензин; Л7 — жирный газ; V — фракция 195—350 °С;
VI — фракция выше 350 °С; VII — вода; VIII — воздух; IX — водяной Пар; X — дымо-
вь(е газы; XI — топливный газ; XII — циркуляционное орошение колонны /?-/.
газ. Газ компрессором ПК-1 подается на газофракционирование, а бензин насосом п-2 частично направляется на орошение верха колонны К-1, а балансовое количество — на стабилизацию- Боковые погоны колонны К-1 (фракции 195—350 °С и выше 350 °С) поступают в соответствующие отпарные секции колонны К-2, где отпариваются водяным паром. Фракция 195—350 °С забирается насосом Н-3, охлаждается в сырьевом теплообменнике Г-7; холодильнике Х-1 и выводится с установки. Фракция выше 350 °С забирается насосом Н-4, охлаждается в сырьевом теплообменнике Т-3 и холодильнике Х-2 и также выводится с установки. С низа К-1 насосом Н-5 в реактор Р-1 откачивается шлам — тяжелый газойль со взвешенной в нем катализаторной пылью.
Катализатор из кипящего слоя реактора медленно опускается в отпарную зону, куда подается водяной пар. Нефтяные пары, адсорбированные поверхностью катализатора, удаляются с помощью водяного пара. Далее катализатор поступает вкатализаторопровод
237
И спускается в узел смешения с воздухом. Воздушный поток поднимает катализатор в регенератор Р-2 по восходящей линии катализаторопровода. Основная часть воздуха для выжига кокса подается непосредственно в регенератор. В змеевики регенератора подводится пар или вода для съема избыточной теплоты. Дымовые газы, образовавшиеся при выжиге кокса, поступают в котел-утилизатор A-J, отдают свое тепло и направляются в электрофильтр А-2
*- iv |
для улавливания катализаторной пыли, после чего выбрасываются в атмосферу. Для подогрева воздуха под давлением применяется топка 17-2.
Аппаратура.Реактор представляет собой цилиндрический аппарат, выполненный из углеродистой стали с внутренней защитной футеровкой. В реакторе можно выделить три основные зоны: реакционную, отпарную и отстойную.
Реакционная зона заполнена псев-доожиженным слоем катализатора высотой 5—6 м и плотностью 400—-450 кг/м3.
Для создания кипящего слоя в нижней части секции имеется распределительная решетка.
Рис. 57. Схема регенератора: /—эакоксопанный катализатор и воздух; 11 — водяной пар; /// — воздух; IV — дымовые газы; V — вода; VI — регенерированный катализатор; / — корпус; 2,6 — воронки; 3 — циклоны; 4—короба н маточники; 5 — змеевики охлаждения; 7 — распределительная решетка; 8—каталиэаторопровод. |
Отпарная секция расположена ниже кипящего слоя, имеет меньший диаметр, чем весь реактор, и снабжается перегородками в виде уголков, приваренных в шахматном порядке для улучшения контакта пара и катализатора. Время пребывания катализатора в отпарной секции примерно 3 мин. Отпарная секция может быть также выносной.
Отстойная зона расположена над кипящим слоем. Здесь происходит отделение паров продукта от унесенного катализатора. В верхней части отстойной зоны располагаются циклонные сепараторы. Пары продуктов крекинга, покидая реактор, проходят циклонные сепараторы, окончательно освобождаясь от катализатора. Из циклонов унесенный катализатор возвращается под кипящий слой.
Регенератор — цилиндрический аппарат диаметром 12 м и высотой 30 м, с коническими днищами. Полезный объем 680 м3. Высота кипящего слоя 6 м. Корпус внутри футерован огнеупорным кирпичом (рис. 57).
На каждый килограмм кокса, выжигаемого с поверхности катализатора, в регенераторе расходуется 12—15 кг воздуха. Примерно 20% воздуха подается вместе с катализатором по пневмоподъем-
238
нику, остальной воздух, необходимый для сжигания кокса, подается непосредственно под решетку кипящего слоя. Сжигание кокса ведут с недостатком воздуха, поэтому в дымовых газах содержится большое количество окиси углерода. Этот прием дает возможность увеличить скорость выжига, сократить подачу воздуха в регенератор, снизить выделение тепла при сгорании кокса, улучшить отвод избыточной теплоты и уменьшить площадь поперечного сечения аппарата.
Процесс горения происходит в кипящем слое, и заканчивается за 5—7 мин. Величина коксосъема составляет 20—45 кг кокса в час на 1 т катализатора.
Над кипящим слоем расположена отстойная зона с циклонами. Дымовые газы, проходя сквозь циклоны, освобождаются от унесенного катализатора. Тепло дымовых газов, а также тепло, полученное в результате сгорания СО до С02, используется в котле-утилизаторе для получения водяного пара.
Ректификационная колонна не имеет отпарной зоны. В нижней части колонны-расположены каскадные тарелки. Пары из реактора, поступающие в колонну под каскадные тарелки, охлаждаются и промываются от катализатора тяжелым газойлем. В нижней части колонны накапливается взвесь катализатора в тяжелом газойле — шлам, возвращаемый в реактор вместе с сырьем установки. Избыточное тепло отводится из колонны при помощи двух потоков циркуляционного орошения.
Контроль и регулирование процесса.Основные параметры регулируются автоматически. Температура в реакторе зависит от температуры сырья, температуры и количества циркулирующего катализатора. Чтобы стабилизировать работу всей аппаратуры, поддерживают постоянными количество сырья, подаваемого на установку, и температуру на выходе сырья из печи, регулируя расход топлива в печь. Температура в кипящем слое катализатора определяется расходом катализатора из регенератора в реактор.
Режим в регенераторе зависит от температуры, давления, количества воздуха, подаваемого в регенератор, степени закоксованно-сти катализатора. Повышение температуры в регенераторе может привести к пережогу катализатора, а понижение температуры ниже заданной приведет к неполному выжигу кокса. Температура в регенераторе поддерживается постоянной путем изменения подачи в змеевики регенератора-насыщенного водяного пара, из которого получают перегретый пар определенной температуры. Расход воздуха поддерживается постоянным. Давление в реакторе и регенераторе должно быть постоянным, хотя и не одинаковым, иначе нарушается циркуляция катализатора. Давление в регенераторе поддерживается клапаном на линии вывода дымовых газов в котел-утилизатор, давление в реакторе — на линии вывода углеводородных газов реакции из бензинового сепаратора (ректификационной колонны).
Пуск установки.Пуск установки начинается с налаживания кипящего слоя в реакторе и регенераторе при помощи горячего
т
воздуха и разогрева катализатора за счет впрыска топлива в регенератор. После достижения нормальной высоты слоя и температуры 480 °С в регенераторе кипящий слой и транспортные линии реактора переводят с воздуха на перегретый водяной пар. Когда температура сырья во фракционирующей части установки достигнет 400 °С, его можно подать в реактор и вывести установку на режим.
Техника безопасности.При эксплуатации установок каталитического крекинга с кипящим слоем могут возникать аварийные ситуации, в первую очередь при нарушении циркуляции катализатора. Например, падение уровня катализатора в реакторе приведет к попаданию воздуха в реактор из регенератора по транспортной линии, а это может быть причиной возникновения пожара или взрыва. Падение уровня катализатора в регенераторе может вызвать проникновение в регенератор паров сырья, что приведет к загоранию в регенераторе. Поэтому при падении уровня катализатора в одном из этих аппаратов необходимо выключить пневмотранспорт, добавить катализатор в реактор или регенератор и лишь после этого-снова восстановить циркуляцию.
Примерные технико-экономические показатели установки каталитического крекинга в кипящем слое на 1 т сырья
Топливо жидкое, кг................................................................. 6,72
Топливо газообразное, кг.......................................................... 9,50
Электроэнергия, МДж............................................................... ....... 320
Катализатор микросферический, кг.......................................... ....... 1,9
Потребление водяного пара давлением 0,8 МПа, кг ... 270 -
Выработка водяного пара, кг
4,7 и 3,8 МПа...................................................................... ....... 635
0,12 МПа.............................................................................. ........ 50
Реконструкция установки.Замена аморфного катализатора на цеолитсодержащий ,в установках каталитического крекинга с кипящим слоем привела к дооборудованию реактора и регенератора. В реакторе на распределительную решетку устанавливается «стакан», резко (примерно в 5 раз) сокращающий реакционный объем. Стакан является продолжением транспортной линии. Вместо стакана может быть также установлен конус высотой 5 м и диаметром в верхней части 2 м с закругленными наружу краями и шестью рассекателями потока катализатора (рис. 58).
Перспективы развития процесса.Для увеличения средней активности катализатора предложен метод контактирования фаз в «полусквозном» * потоке. В отличие от кипящего слоя, где частицы катализатора совершают многократное движение в различных направлениях реакционной зоны, в полусквозном потоке они движутся в основном снизу вверх, вместе с парами реагирующей смеси. Продукты реакции отделяются от катализатора в отдельном аппарате большего объема или в расширенной верхней части реак-
* Полусквозиой поток имеет скорость до 2,5 м/с, сквозной — выше 2,5 м/с,
240
тора. Способ контактирования частиц катализатора с парами сырья и газами в полусквозном потоке позволяет избежать проскока реагирующей смеси в колонну. Полусквозной поток уменьшает среднюю закоксованность катализатора (т. е. повышается его активность) и уменьшает вероятность вторичных превращений. Принципиальная конструкция реакторного узла с полусквозным потоком
|
|
Рис. 58. Схема реконструи- • Рис. 59. Конструкция реактор-
рованного реактора: ■ лого узла с полусквозным по-
/ —корпус реактора; 2 — подво- током катализатора:
дящий катализаторопровод; / — сырье; // — водяной пар; Ш-воз-
3 — рассекатель. дух; /у_ дымовые газы; V — про-
дукты реакции. / — щ;клоиы; 2 — объемный сепаратор; 3, в — стояки; 4 — регенератор; 5 —реактор; 7 —решетка; S —распылитель.
катализатора приведена на рис. 59. Подобный реактор имеет общую высоту около 30 м. Однако для каталитического крекинга в полусквозном потоке желательно раздельное крекирование менее стойких и более стойких компонентов сырья, которое можно проводить в оптимальном режиме для каждого из этих компонентов. Благодаря очень простому устройству полусквозного реактора, вполне осуществимо иметь два реактора, т. е. фактически иметь двухступенчатый каталитический крекинг.
§ 49. МЕХАНИЗМ ПРОЦЕССОВ КАТАЛИТИЧЕСКОГО РИФОРМИНГА
Исследование каталитических реакций нафтеновых и парафино вых углеводородов привело советских ученых к замечательным открытиям. Н. Д. Зелинским и его школой была подробно изучена
241
реакция дегидрирования циклогексановых углеводородов в ароматические. Эта реакция стала классической.
В 1936—1937 гг. Молдавский и Камушер над окисным хромовым катализатором при 450—470 °С превратили парафиновые углеводороды в ароматические; того же результата достигли Казанский и Платэ при 310 °С над платинированным углем, а Каржев, Северьянова и Снова — при 500—550 °С над меднохромовым катализатором. Эта реакция получила название дегидроциклиза-ции алканов или С6-дегидроциклизации.
Как было показало с помощью меченых атомов, над окисно-хро-мовым катализатором, механизм этой реакции заключается в том, что парафиновый углеводород с числом углеродных атомов не менее шести постепенно дегидрируется до триена.Триен замыкается в циклогексадиеновыи углеводород, а последний дегидрируется до соответствующего ароматического углеводорода:
СгаН2п + 2 __н ' СпНгя (алиф) _н ' СПН2П —2 (алиф) ~__н *
циклизация
----- *- СгаН2п-4 (алиф) * CrtH_>n-i (цикл) _н * СгаП2/г-6
Суммарная реакция:
СгаН2/г + 2 —> СПН2П_(| + 4Н2
Интересно отметить, что все стадии дегидрирования являются реакциями каталитическими, а стадия циклизации чисто термическая реакция.
Таким путем из гексана получается бензол, из гептана — толуол, из октанов и нонанов— смесь изомерных ароматических углеводородов, так как при содержании в цепи более семи атомов углерода возможны различные варианты замыкания цепи в цикл.
Дальнейшие исследования показали (Казанский, Либерман и другие, 1954 г.), что алканы над платинированным углем могут замыкаться и в пятичленное циклопентановое кольцо (Cs-дегидро-циклизация).
Термодинамическая вероятность дегидроциклизации с образованием шестичленных колец значительно выше, чем вероятность Сб-дегидроциклизации. Однако энергия активации этой последней реакции, наоборот, ниже чем для Св-дегидроциклизации, поэтому в конечном итоге обе реакции конкурентоспособны и протекают параллельно.
Другие исследования показали, что в реакции ароматизации могут вовлекаться и олефиновые, и циклопентановые углеводороды. Олефины циклизуются, а алкйлциклопентаны изомеризуются до соответствующих циклогексанов, которые затем дегидрируются. Алкйлциклопентаны и алкилциклогексаны над платинированным углем при 310 °С (Ал. А. Петров, 1971 г.) могут также циклодеги-дрироваться с образованием бициклов. Н
"СНг*—-СН^ |
I______ ^,, ^г, —н,
242
Если расположить углеводороды разных классов в порядке убывания их склонности к ароматизации при высокой температуре над окисными и металлическими катализаторами, то получится следующий ряд:
циклогексеновые; циклогексановые; циклопентановыс; олефиновые;
парафиновые
При разработке промышленных процессов каталитической ароматизации, или, как их в дальнейшем стали называть, каталитического риформинга, встретились большие трудности. Главная из них заключалась в быстром закоксовывании гсатализаторов вследствие развития побочных реакций уплотнения и конденсации. Для торможения этих нежелательных реакций и удлинения срока службы катализаторов ароматизацию стали проводить в атмосфере водорода. Из уравнения реакции дегидрирования и дегидроциклизации . видно, что по принципу Ле-Шателье и по закону действующих масс увеличение давления водорода должно смещать равновесие этих реакций справа налево:
CGH12 ч=* С6Н6 + ЗН2 С6Н14 5=* CGH6 + 4Н2
Вместе с тем опыты показали, что чем выше давление водорода, тем меньше отложения кокса. Этими двумя противоречивыми обстоятельствами и диктуется выбор парциального давления водорода в том или ином варианте промышленного процесса.
Среди процессов каталитического риформинга одним из первых был освоен так называемый гидроформинг. Этот процесс осуществлялся при 480—550 °С под давлением водорода 1,5—2,5 МПа в присутствии алюмомолибденового катализатора (MoOa/Al203). В настоящее время _все 'установки каталитического риформинга работают на платиновомкатализаторе,. а .сам процесс получил название платформинга, или риформинга на алюмоплатиновом катализаторе. ~
Алюмоплатиновый катализатор представляет собой окись алюминия, на которую нанесено не более 0,6% платины. Этот катализатор является бифункциональным. С точки зрения теории катализа в бифункциональных катализаторах существуют активные центры веществ, содержащие как неспаренные, так и спаренные электроны. Первые способствуют активации окислительно-восстановительных реакций. В данном случае это платина, являющаяся (так же, как и другие металлы VIII группы) типичным гидрирующим-дегидрирующим катализатором. Поэтому на алюмоплатиновом катализаторе развиваются реакции дегидрирования шести-членных нафтенов и дегидроциклизации алканов. Окись алюминия— вещество со спаренными электронами имеет кислотный характер. Поэтому на алюмоплатиновом катализаторе активируются реакции изомеризации, протекающие по карбоний-ионному механизму. Для усиления этой функции катализатор промотируется хлором или фтором. В качестве промоторов, увеличивающих
24а
активность, селективность и термическую стабильность катализатора предложены также редкие элементы иттрий и церий.
Эффективным оказалась и частичная замена платины на другие металлы, например рений, иридий, кадмий, свинец, палладий. Такие полиметаллические катализаторы более стойки к спеканию, срок их службы значительно выше. На этих катализаторах несколько снижается роль побочных реакций распада и наоборот увеличивается значение реакции дегидроциклизации парафинов. При работе на этих катализаторах понижается скорость закоксо-вывания, повышается продолжительность межрегенерационных пробегов.
Процесс платформинга осуществляется при температуре порядка 500°С под давлением водородсодержащего газа 2—4 МПа. Содержание водорода в циркулирующем газе от 75 до 90%. Коксообразование при этом сильно тормозится. Платиновый катализатор весьма чувствителен к сернистым соединениям. Дезактивация катализатора происходит и под влиянием азотистых соединений, а также соединений свинца и мышьяка. Особенно велики требования к чистоте сырья при использовании полиметаллических катализаторов, которые исключительно чувствительны к воздействию каталитических ядов.
Механизм риформинга над платиновым катализатором очень сложен, так как в этом процессе сказывается совместное влияние высокой температуры, давления водорода и бифункционального катализатора.
Рассмотрим основные реакции, протекающие в условиях каталитического риформинга.
Дегидрирование шестичленных нафтенов. Эта реакция термодинамически наиболее вероятна при температуре процесса.
Изомеризация пятичленных нафтенов в шестичленные с дальнейшим их дегидрированием до ароматических углеводородов. В целом этот вид ароматизации получил название дегидроизоме-ризации. Например:
су ^0**0+8Ha
Эта реакция при температуре процесса термодинамически маловероятна. Действительно, расчеты показывают, что равновесная концентрация метилциклопентана при 500°С равна 95%, а цикло-гексана — только 5%. Однако поскольку циклогексан с большой скоростью сразу превращается в бензол, то равновесие реакции изомеризации даже при неблагоприятной температуре все время смещается вправо.
Дегидроциклизация алканов:
СяН2п+2 4=^ С„Над-б + 4Н2— Q
В отсутствие катализаторов эта реакция невозможна, так как значительно скорее произойдет распад алканов. Наличие катали-
244
затора меняет дело. Даже при неблагоприятных с точки зрения термодинамической вероятности температурах порядка 500°С реакция становится возможной. Это, так же как и в случае дегидро-изомеризации, объясняется тем, что образующиеся на промежуточной стадии, хотя и с малыми равновесными концентрациями, шестичленные нафтены, сразу же с большими скоростями дегидрируются до соответствующих ароматических углеводородов. Циклодегидрирование олефинов:
СпНгп —> СгаН2п-б + ЗН2
Циклизация непредельных углеводородов идет со значительно большими скоростями, чем циклизация предельных углеводородов. Однако протекающие параллельно реакции распада и конденсации приводят к быстрому отравлению катализатора, поэтому в качестве сырья следует применять фракции, не содержащие непредельных углеводородов.
Наряду с перечисленными реакциями, приводящими к накоплению ароматических углеводородов, под влиянием алюмопла-тинового катализатора и в атмосфере водорода большое развитие получают гидрокрекинг и изомеризация парафиновых углеводородов, а также гидрирование остаточных сернистых соединений. Механизм гидрокрекинга и гидрообессеривания будет рассмотрен в § 54. Обе реакции полезны, так как приводят к облегчению фракционного состава и разрушению агрессивных сернистых соединений. В условиях риформинга на алюмоплатиновом катализаторе изомеризация алканов нормального строения в разветвленные происходит в основном только для низкомолекулярных углеводородов С4—Сб.
Образующиеся ароматические углеводороды частично могут деалкилироваться и изомеризоваться с перераспределением боковых цепей, как и при каталитическом крекинге.
Побочными нежелательными реакциями при каталитическом риформинге являются: уплотнение и конденсация непредельных и ароматических углеводородов, а также глубокий гидрокрекинг алканов и цикланов с образованием газообразных углеводородов. Что касается кинетики основных реакций, то с наибольшей скоростью протекает дегидрирование нафтенов. Значительно медленнее идет дегидроциклизация алканов и еще медленнее — их изомеризация.
§ 50. СЫРЬЕ, ПАРАМЕТРЫ И ПРОДУКТЫ ПРОЦЕССА КАТАЛИТИЧЕСКОГО РИФОРМИНГА
Каталитический риформинг на платиновом катализаторе (плат-форминг)—один из важнейших процессов нефтеперерабатывающей и нефтехимической промышленности. Процесс занимает ведущее место как в производстве высокооктановых бензинов, так и в производстве ароматических углеводородов — бензола, толуола, ксилолов.
245
Следует также отметить, что использование водородсодержа-щего газа — побочного продукта риформинга — способствовало
|
о4. |
kj |
- ^ 3
■о о
03 Q
^| 80 1^ 75
75 80 85 30 95 100 Октановое число
Рис. 60. Связь между окта
новым числом бепзииа-ри-
формата из ромашкинской
нефти, его выходом и вы
ходом водорода:
/ — фракция 6Э —180 °С; 2 — фрак
ция 85-180 °С; 3 — фракция
105-180 °С.
90 | ^-2 | ||
85 | У^^ | ||
80 | - yS, | ||
75 7Л | 1 1 | i i I | 1 1 |
30 JS 40 45 50 55 60 Содержание ароматических и нафтеновых углеводородов в сырье, % (масс.)
Рис. 61. Зависимость выхода бензина риформинга с октановым числом 95 от
углеводородного состава сырья: /-фракция 85-180 °С; 2 — фракция'105-180 °С:
широкому внедрению в промышленность процессов гидроочистки нефтепродуктов.
На установках каталитического риформинга получают углеводородный газ, ароматизированный бензин, водородсодержащий газ.
Выход и состав продуктов каталитического риформинга зависит от свойств катализатора и исходного сырья и взаимосвязанных параметров процесса: температуры, давления, объемной скорости подачи сырья, кратности циркуляции во-дородсодержащего газа по отношению к сырью.
ю |
Сырье. Вкачестве сырья каталитиче-
20 30 40 so ского риформинга применяют бензино-
CtTeoaoV^T<Z^ вые фракции с началом кипения 60 °С и
выше и концом кипения не выше 180 °С.
Рис. 62. Зависимость выхода Бензины с началом кипения ниже 60 °С
водорода от содержания нафтеновых углеводородов в сырье: I — фракция 85-180 °С; 2— фракция 105-180 °С. |
нет смысла подвергать риформированию, так как во фракции н. к. — 60 °С не содержится ни цикланов, ни алканов, способных превратиться в ароматические углеводороды, а есть только углеводороды с числом атомов углерода менее шести, превращающиеся в углеводородный газ. Это балластные фракции, повышающие нагрузку установки, увеличивающие выход газа, причем на газообразование расходуется водород,
246
Утяжеление фракционного состава сырья выше 180 °С приводит к большим отложениям кокса на катализаторе, вследствие чего сокращается срок службы в режиме реакции.
В зависимости от назначения установки применяют бензиновые фракции с различными пределами выкипания. Для получения высокооктанового бензина используют фракции 85—180 °С и 105— 180°С;, для получения индивидуальных углеводородов: бензола фракцию .60—85 °С, толуола — фракцию 85—105 °С, ксилолов — фракцию 105—140°С; для получения смеси бензола, толуола, ксилолов— фракцию 62—140 °С, а при одновременном получении и ароматических углеводородов и высокооктанового бензина— фракцию 62—180 °С,
При производстве высокооктановых бензинов, особенно с октановым числом 95—100, каталитическому риформингу целесообразнее подвергать сырье утяжеленного фракционного состава с начальной температурой 105 °С, так как это позволяет увеличить выход бензина риформинга' и одновременно водорода (рис. 60).
Углеводородный состав сырья оказывает влияние на выход бензина риформинга и содержание в нем ароматических углеводородов, а также на выход водорода в процессе риформинга и на тепловой эффект реакции. Чем больше цикланов и ароматических углеводородов содержится в сырье, тем выше выход бензина риформинга (рис. 61). Качество сырья и бензина риформинга представлены в табл. 11, зависимость выхода водорода от содержания нафтеновых углеводородов -показана на рис. 62.
Катализаторы.Стационарные таблетированные катализаторы
платформинга АП-56 и АП-64 имеют следующую характери
стику: Г- С\
АП-56 АП-64
Насыпная плотность, т/м3............................................ 0,6 0,6—0,65
Содержание платины, % (масс.).................................. 0,58 0,6—0,65
Промотор...................................................................... Фтор Хлор
Эти катализаторы проявляют высокую активность и селективность в условиях процесса и могут стабильно работать без регенерации от 6 месяцев до 1 года. При потере активности вследствие значительных отложений кокса катализатор регенерируется окислительным методом (см. § 51). Катализатор АП-64 более активен и селективен, чем АП-56 (табл. 12).
Как уже отмечалось выше, соединения серы, азота, металлов, а также вода, поступающие вместе с сырьем, ухудшают селективность и сокращают срок службы платиновых катализаторов. Поэтому сырье платформинга подвергают гидроочистке и осушке. В качестве катализаторов гидроочистки применяют алюмокоб'альт молибденовый катализатор и катализатор АП-15 со сниженным содержанием платины. Степень удаления сернистых и азотистых соединений зависит от чувствительности катализаторов: для АП-56 — остаточное содержание серы в сырье 0,001%, катализатор АП-64 требует более тщательной подготовки сырья, и особенно жесткие требования предъявляют к качеству сырья и вспомогательных
847
ТАБЛИЦА 11
Свойства и состав сырья продуктов риформинга фракций
86—180 "С и 106—180 °С различных нефтей для получения
бензина с октановым числом 96
Фракция 85-180 °С
Фракция 105- 180 °С
Показатели
Арлан-ская нефть
Усть-ба-
лыкская
нефть
Ром аш-
кинокая
нефть
Арлан-ская нефть
Ромаш-
кинская
нефть
Котурте-
пипская
нефть
Сырье
Плотность р^° . . . Углеводородный состав сырья. % (масс.)
ароматические нафтеновые . . . паряфчновые . . Октановое число . .
Бензин риформинга
Плотность р^° . . .
Углеводородный со
став бензина, %
(масс.)
непредельные . .
ароматические
предельные . . .
Выход % (масс.)
стабильного бен
зина ........................
водорода . . . .
0,738
6,5 26,0 67,5 37,0
0,785
1,2 64,5 34,5
75,0 1,2
0,736
7,4 27,4 65,2
0,789
0,9 64,7 34,4
76,5 1,2
0,742
10,0 27,0 63,0 39,5
0,796
0,8 65,5 33,7
77,7 1,3
0,750
7,4 23,1 69,5 25,5
0,798
0,9 65,4 33,7
76,0 1,3
0,750
12,2 26,0 61,8 39,0
0,795
0,7 67,5 31,8
81,0 1,6
0,772
11,0 48,0 41,0 55,0
0,804
0,5 68,5 31,0
88,3 2,2
ТАБЛИЦА 12
Режим, материальный баланс и свойства продуктов каталитического риформинга фракции 85—180 °С на катализаторах АП-56 и АП-64
|
Показатели
АП-64
Давление, МПа..........................................
Выход продуктов, % (масс.)
дебутанизированный бензин . . .
газ........................................................
в том числе водород .....................
потери ................................................
Свойства бензина риформинга
плотность при 20 СС, кг/м3 . . . . углеводородный состав, % (масс.)
непредельные ...........................
ароматические .............................
парафины + нафтены .............
октановое число
моторный метод.............................
исследовательский метод . . . .
3,5
82,5
10,5
1,0
1,0
766
1,4 55 48,1
80 85
78,5
20,0
1,1
1,5
790
1,5 64,0 34,5
85 95
2,0
83,5
15,0
1,7
1,5
793
0,8 66,0 33,2
85 95
249
материалов полиметаллические многофункциональные катализаторы (остаточное содержание серы и азота в сырье 0,0001—0,0005%).
Промотор катализатора АП-64—-хлор — легко гидролизуется в присутствии даже небольших количеств воды. Поддержание оптимального содержания хлора в катализаторе возможно, во-первых, за счет снижения влажности циркуляционного газа, во-вторых, восполнением потерь хлора подачей хлорорганического соединения в зону реакции. Например, дихлорэтан подается вместе с сырьем во все три ступени риформинга пропорционально распределению катализатора в реакторах из расчета 5%о на сырье.
100 |
|
|
Совершенствование процессов платформинга с длительными циклами реакции связано с разработкой и внедрением полиметаллических многофункциональных катализаторов, более эффективных и стабильных, чем алюмоплатпновые, особенно при пониженном давлении (см. стр-. 244).
з «Г 1,0 |
s i |
J |
JL |
0,1 |
443 475 507 539 Температура, С |
'411 |
Рис. 63. Зависимость отношения равновесных концентраций ароматических и нафтено-ных углеводородов от температуры при различном парциальном давлении водорода. |
Параметры процесса. Тепловой эффект реакции зависит главным образом от содержания в сырье' нафтеновых углеводородов, так как именно реакции дегидрирования нафтенов сопровождаются интенсивным поглощением тепла. Если для парафинистого сырья отрицательный тепловой эффект составляет 295—364, то для нафтенового 410—670 кДж на 1 кг сырья.
Поскольку тепло реакции отнимается от газо-сырьевой смеси, температура последней падает. Поэтому к реакционной смеси необходимо подводить тепло. Это обстоятельство вынуждает распределять катализатор в несколько реакторов, и между реакторами подогревать газосырьевую смесь в секциях печи. В первых реакторах поглощение тепла наиболее велико, так как содержание нафтенов в/ сырье наибольшее, в последних — наоборот. Чтобы сделать подвод тепла более, равномерным, катализатор размещают в нескольких реакторах неравномерно: в первом по ходу сырья реакторе — наименьшее количество катализатора, в последнем — наибольшее. В конечном итоге общая глубина ароматизации зависит от правильного распределения катализатора между реакторами. Соотношение загрузки катализатора по реакторам может быть 15:35:50; 1:2:4; 1 : 3 : 7 и др.
Температура процесса лежит в пределах 470—525 °С. Понижение температуры при неизменных объемной скорости и давлении ведет к увеличению выхода бензина, снижению выхода газа, уменьшению коксообразования, но одновременно и к уменьшению количества ароматических углеводородов в получаемом бензине (рис. 63).
249
Объемная скорость составляет обычно 1—2 ч-1. Снижение объемной скорости при прочих равных условиях дает тот же эффект, что и повышение температуры: уменьшение выхода ри-формата, повышение содержания ароматических углеводородов в нем, увеличение выхода газа и коксовых отложений на катализаторе. Слишком низкие объемные скорости неэкономичны, так как при этом необходимо увеличивать объем реактора. Влияние объемных скоростей на выход и качество катализата при риформинге фракции 120—180СС при 495 СС иллюстрируется следующими данными:
Объемная скорость, ч-1 . . . | 0,5 | 1,0 | 1,5 | 2,0 |
Выход стабильного катализата, | ||||
% (масс.)................................... -. | 64,5 | 78,2 | 81,0 | 83,0 |
Плотность катализата р4° . . | 0,788 | 0,787 | 0,786 | 0,784 |
Содержание ароматических | ||||
углеводородов, % (масс.) . . | 66,8 | 65,2 | 62,5 | 60,0 |
Роль давления водородсодержащего газа в процессе каталитического риформинга очень велика, так как при повышении давления (2—4 МПа) резко снижается скорость газо-и коксообра-зования. Одновременно повышение давления приводит к уменьшению выхода ароматических углеводородов. При более низком давлении выход ароматических углеводородов выше, но выше кок-сообразование, следовательно, катализатор быстрее теряет активность.
Для получения бензола давление снижают до 2 МПа, при этом значительного коксообразования не наблюдается, так как рифор-мированию подвергается легкое сырье. Влияние давления на результаты каталитического риформинга широкой фракции 62— 180°С из восточных нефтей СССР (в присутствии катализатора АП-64)показано ниже:
Давление процесса, МПа......................................................... 3,7 2,0
Ваход стабильного катализата, % (масс.).............................. 78,8 84,0
Выход ароматических углеводородов, % (масс.) . . . 38,9 48,5
Соотношение между объемом' водородсодержащего газа при 0°С и 0,1МПа и объемом сырья при 20 °С, поступающих в реактор, называется кратностью подачи (или кратностью циркуляции) водородсодержащего газа. Разбавление паров сырья водородом благоприятно влияет на продолжительность работы катализатора. Кратность циркуляции колеблется в пределах 1300—1800м3/м3. Увеличение кратности циркуляции связано с увеличением эксплуатационных расходов на топливо, воду, электроэнергию.
Технологический режим.Режим работы установки платфор-минга производительностью 1 млн. т/год при производстве компонента автобензина АИ-95 из фракции 85—180 С и ароматизиро-
250
ванного концентрата АИ-86из фракции 62—140°С (для получениябензола, толуола, ксилола) приводятся ниже:
Пределы выкипания сырьевой фракции, °С . . . 85—180 62—140
Температура, °С
гидроочистка......................................................... ..... 350-400 350-400
риформинг............................................................. ..... 480-530 480-530
Давление в реакторе, МПа
гидроочистка .................................................. .... 2,7 2,7
риформинг *......................................................... ..... 3,0 2,5
Объемная скорость, ч-1
гидроочнсткн........................................................ .... 2,5 2,5
риформинг............................................................ .... 1,2 1,2
Кратность циркуляции, м3/м3
гидроочистка......................................................... .... 150 130
риформинг............................................................. 1800 1500
Соотношение загрузки по реакторам риформипга 1:3:7 1:3:7
Концентрация водорода в водородсодержащем газе, % (об.)
гидроочистка......................................................... ... 75—55 82—72
риформинг............................................................. 70—60 79—69
* Значения давления приведены для последнего реактора.
Материальный баланс.Материальный баланс установок плат-форминга с предварительной гидроочисткой сырья при получении
бензола (I), 90-(II) и 95-октанового бензина (III)приводится
ниже [в % (масс.)]:
i it ш
Поступило:
Фракция 62-85 °С........................................ 100,00 — —
Фракция 85-180 °С...................................... — 100,00 100,00
Получено:
Сухой газ..................................................... 3,20 3,28 8,25
Стабильная головка.................................... 7,90 11,10 4,73
Стабильней ка.тализат................................ 83,30 82,70 77,84
Водородсодержащий газ ...................... 2,40 1,31 6,78
(Водород).................................................... (2,04) (1,11) (1,2)
Сероводород................................................ — 0,21 0,04
Потери.......................................................... 3,20 1,40 2,36
г
Итого . . . 100,00 100,00 100,00/-
Водородсодержащий газ с содержанием водорода 60—90% применяется при гидроочистке топлив и масел. Его состав, в °/о(об.), при производстве 95-октанового бензина (I), и производстве бензола, толуола (II) примерно следующий:
i п i и
Водород............ 70,1 87,5 Пропан................... 4,9 2,6
Метан.............. 13,3 4,2 Бутан.................. 1,5 2,4
Этан.......................... 9,1 3,3 Пентан и выше .... 1,1 1,0
Сухой газ направляется в топливную сеть завода, на установки пиролиза или в производство водорода. Стабильная головка, представляющая смесь пропана, бутана и изобутана, подвергается фракционированию для дальнейшего использования в качестве нефтехимического сырья.
251
§ 61. УСТАНОВКА ПЛАТФОРМИНГА
Установка платформинга состоит из трех блоков: 1) предварительная гидроочистка бензина: 2) платформинг гидроочищенного бензина (гидрогенизата); 3) стабилизация бензина платформинга.
Если на установке получают индивидуальные ароматические углеводороды, то в ее состав включается еще и блок выделения ароматических углеводородов, который будет рассмотрен в § 53.
Технологическая схема.Технологическая схема установки для получения высокооктановых бензинов приводится на рис. 64.
Исходное сырье подается насосом Н-1 на смещение с циркулирующим газом гидроочистки и избыточным водородом риформинга-Полученная газо-сырьевая омесь после нагрева в теплообменнике Т-1 и печи П-1 поступает в реактор гидроочистки Р-1. Далее смесь газа и гидроочищенного бензина отдает свое тепло в кипятильнике Т-3, теплообменнике Т-1, холодильнике Х-1 и направляется в сепаратор высокого давления гидроочистки С-1, где газ отделяется от гидрогенизата. В водородсодержащем газе присутствует сероводород, выделяющийся при гидроочистке. Из сепаратора газ поступает в колонну К-3, где сероводород отмывается 15% раствором моноэтаноламина.
Очищенный газ разделяется на две неравные части: большая— циркуляционный газ гидроочистки — поступает на прием циркуляционного компрессора ПК-1 и вновь смешивается с сырьем, меньшая — избыточный водород — выводится с установки. Жидкая фаза в сепараторе С-1 содержит гидроочищенный бензин с растворенными снем сероводородом, углеводородным газом и водой. Поэтому гидрогенизат поступает через теплообменник Т-2 в отпар-ную" колонну К-1, где происходит отпарка газа, воды и сероводорода от бензина за счет тепла потока из реактора Р-1, подводимого в кипятильник Т-3. Стабильный гидрогенизат с низа колонны К-1 проходит теплообменник Т-2 и насосом Н-2 направляется на Смешение с циркулирующим водородом блока платформинга. Сме1\ бензина и газа нагревается в теплообменнике Т-4 и в первой секций печи П-2, а затем последовательно проходит реактор Р-2, вторую секцию печи П-2, реактор Р-3, третью секцию печи П-2 и реактор Р-4.
Продукт риформинга из реактора Р-4 направляется в теплообменнике Т-4 и холодильник Х-2, охлаждается и поступает в сепаратор высокого давления платформинга С-3, 'где происходит разделение газа и бензина. Газ поступает на прием компрессора ПК-2. Большая часть его возвращается на смешение с гидрогенизатом, а избыточный водород платформинга направляется в блок гидроочистки. Жидкий продукт из сепаратора С-3 попадает в сепаратор низкого давления С-4, где из платформата выделяется растворенный углеводородный газ. Окончательно илатформат стабилизируется в колоннах К-4 и К-5. Углеводородный газ гпдроочистки и риформинга из сепараторов С-2 и С-4 смешивается и подается во фракционирующий абсорбер К-4.
252
Рис. 64. Технологическая схема установки 7 —сырь?; И—избыточный водород; ///—сухой углеводородный гаа; IV — стаби бензин; VI — 15%-ный раствор мояоэтаиоламина, насыщенный сероводородом; /
Нестабильный бензин из сепаратора С-4 двумя потоками поступает в абсорбер К-4: часть холодного бензина подается на верх адсорбера, другая часть нагревается и теплообменнике Т-6 и подается в низ абсорбера. С верха абсорбера К-4 уходит сухой углеводородный газ, с низа — бензин в колонну стабилизации К-5 после предварительного нагрева в теплообменнике Т-5 за счет стабильного бензина. С верха колонны К-5 с установки выводит-. ся стабильная головка, с низа колонны К-5 через теплообменники Т-5~'к~Т^6 ~~йГ "холодильник Х-3 — стабильный бензин. Подвод тепла в низ колонн К-4 и К-5 осуществЖётся""методом горячей струи через двухкамерную печь П-3. При полном выделении из бензина этана (режим деэтанизации) в верху колонны К-5 поддерживается 70 °С, при полном удалении пропана (режим депро-панизации)—45 °С. В обоих случаях температура низа колонны 220 °С, давление 11,5 МПа.
В настоящее время в схему включаются также осушители циркулирующего водородсодержащего газа, наполненные цеолитовым поглотителем или активной окисью алюминия, а также емкости, мерники и дозировочный насос для подачи дихлорэтана в количестве 5• 10-5% (масс.) на сырье.
Регенерация катализатора. По окончании никла реакции катализатор теряет активность вследствие отложения на нем кокса. Процесс регенерации осуществляется поэтапно. Сначала прекращается прием сырья на установку. Блок гидроочистки и блок стабилизации отключаются. Циркуляция водородсодержащего газа в блоке платформинга продолжается для промывки системы от углеводородов. Далее постепенно сокращается подача топлива в форсунки печи платформинга до полного отключения. Система постепенно охлаждается до 200°С, и циркуляция водородсодержа-. щего газа прекращается. Водородсодержащий газ сбрасывается через редукционные клапаны в топливную сеть. Из реакторов остаток паров углеводородов отсасывается вакуумным насосом. Затем система продувается инертным газом в атмосферу. После продувки система заполняется инертным газом до давления 1 МПа, включается циркуляционный компрессор и реакторный блок постепенно разогревается при постоянной циркуляции инертного газа. При 250 °С к инертному газу добавляется воздух в таком количестве, чтобы концентрация кислорода в инертном газе не превышала 0,5% (об.) в начале регенерации и 2% (об.) в конце регенерации. Выжигание кокса проводится в две ступени: первая ступень при 250—300°С, вторая при 380—400°С. После окончания выжигания кокса катализатор прокаливают при 500 °С. Затем систему охлаждают, циркуляцию инертного газа прекращают и сбрасывают его в атмосферу. После этого снова продувают систему водородсодержащим газом.
Пуск установки. Если на заводе имеется установка, риформин-га, дающая избыточный водородсодержащий газ, при пуске установки платформинга вначале систему гидроочистки и платформинга заполняют водородом до максимально возможного давле-
254
нйя 3—4 МПа. Включают циркуляционный компрессор, начинается холодная газовая циркуляция. Затем включают форсунки печей и, постепенно поднимая температуру, переводят установку на горячую газовую циркуляцию. Одновременно разогревают отделение стабилизации гидрогенизата. Затем на установку принима; ют сырье и начинают понемногу подавать сырье в реакторы, постепенно доводя подачу до нормальной. При отсутствии водорода возможен пуск установки на смеси сырья и инертного газа при производительности, составляющей 25% от нормы.
Контрольи регулирование процесса.Устойчивый режим работы установки контролируется приборами и поддерживается при помощи автоматических регуляторов. Расход сырья на установку и количество циркулирующего водородсодержащего газа поддерживаются постоянными. Подача топлива в реакторные печи регулируется в соответствии с поступлением нагреваемого продукта в печь и корректируется по температуре продукта на выходе из ' печи в реактор. Давление в блоке гидроочистки автоматически поддерживается постоянным регулированием расхода водородсодержащего газа с установки, а давление в блоке платформинга — регулированием расхода избыточного водорода на гидроочистку. Уровень в сепараторах С-1 и С-3 регулируется отводом жидкого продукта.
Аварийные блокировки.На установках платформинга имеется ценное оборудование — циркуляционные компрессоры, а в реакторы загружен дорогой катализатор. Поэтому предусматривается система автоматических блокировок для предотвращения порчи оборудования и катализатора в аварийных ситуациях. Если падает давление газа, повышается его температура на приеме компрессора или прекращается подача воды на охлаждение в компрессоры, то компрессор и сырьевой насос автоматически останав- . ливаются, одновременно прекращается подача топлива в печь. При повышении температуры газо-сырьевой смеси на входе в реактор до 525 °С автоматически отключается сырьевой насос и установка переводится на горячую циркуляцию водородсодержащего газа.
Экономическиепоказатели. На 1 т стабильного катализата при переработке фракции 85—180°С расходуется:
Электроэнергия, МДж .... 86,4 Топливо, кг................................... 95,8
Водяной пар, МДж................... , 570 Вода оборотная, м3..................... 15,5
Перспективы развития процесса.Изучение работы катализатора в реакторах платформинга со стационарным катализатором показало, что фактически реакции образования ароматических углеводородов из шестичленных, пятичленных нафтенов и парафинов происходят неодновременно. Сначала превалирует реакция дегидрирования шестичленных нафтенов и лишь затем происходит де-гидроизомеризация пятичленных нафтенов и далее дегидроцикли-зация парафинов. Поэтому для углубления ароматизации большое преимущество имеет процесс риформинга с одновременным
255
Дифференцированием температуры и парциального давления водорода по реакторам. Такой процесс получил название магнафор-мипга. *
Высокоселективный алюмоплатиновый катализатор РД-150, про-мотированный хлором, имеет длительный межрегенерационныи пробег, что позволяет вести процесс при 1,4 МПа. Температура и соотношение водородсодержащего газа и сырья для первых трех реакторов ниже, объемная скорость выше, чем в обычном процессе. Такие условия углубляют дегидрирование нафтенов в первых трех реакторах, одновременно значительно уменьшается гидрокрекинг сырья. Наоборот, в последнем реакторе повышение температуры в отсутствие нафтенов усиливает дегидроциклизацию парафинов. Коксообразование подавляется увеличением соотношения водород: сырье в последнем реакторе. Соответственно этому размещение катализатора в реакторах находится в отношении 17: 17: 16:50. Мольное отношение водород: сырье в начале 2,5: 1, в конце 9:1, температура повышается до 525 °С. Процесс позволяет получить бензин с октановым числом 94—98 (по исследовательскому методу), а выход его на 2—4% (°б.) выше, чем на обычной установке.
Соответствующие исследования для катализатора АП-64 при 2,0 МПа позволили рекомендовать для отечественных установок риформинга, перерабатывающих бензольно-толуольную фракцию, следующий технологический режим: при распределении катализатора 1:2:4 или 1:2:6 в головных реакторах кратность циркуляции водородсодержащего газа должна быть (450 ч- 600) : 1, в последнем (1300-=- 1600) : 1. Температура в реакторах соответственно 475—490 °С; 490—505 °С; 505—530 °С.
Большие преимущества имеет также процесс с движущимся катализатором, непрерывно регенерируемым в специальном аппарате.
§ 62. АППАРАТУРА И ОБОРУДОВАНИЕ УСТАНОВОК ПЛАТШОРМИНГА
Наиболее сложной по устройству на установках платформинга является аппаратура реакторного блока: реакторы, печи, теплообменники, кипятильники, холодильники. Вся аппаратура реакторного блока работает в условиях высокого давления в среде водорода, большинство аппаратов — при высокой температуре. Производительность установок 200—1000 тыс. т/год.
Реактор представляет собой цилиндрический аппарат, выполненный из стали. В верхней части имеется штуцер для ввода газосырьевой смеси. Применяют реакторы как с аксиальным (осевым) вводом газо-сырьевой смеси, так и с радиальным вводом. -В первом случае газо-сырьевая смесь проходит через катализатор сверху вниз (рис. 65). Входной штуцер снабжается устройством для равномерного распределения потока по всему сечению аппарата. Во втором случае от штуцера вниз по центру аппарата спускается
* Разработан в США.
256
перфорированная труба, конец которой заглушён. Поток газа и сырья движется через катализатор от стенок аппарата к центру по радиусам (рис. 66).
Реакторы с радиальным вводом имеют значительно меньшее гидравлическое сопротивление, чем реакторы с аксиальным вводом. Обычно первым по ходу сырья устанавливают реактор с аксиальным вводом, чтобы задержать в верхнем слое катализатора
|
7 «п*
Рис. 65. Реактор риформинга с аксиальным вводам газо-сырьевой смеси: 1 — корпус;; 2— футеровка; 3—фарфоровые шары; 4—штуцер для, термопары; 5 — штуцер для ввода газо-сырьевой смеси; 6 — распределитель; 7— днище; Я —катализатор; S—перфорированный стакан с сеткой; 10—штуцер для вывода газо-продуктовой смеси. |
Рис. 66. Реактор риформинга с радиальным вводом газо-сырьевой смеси: /—корпус реактора; 2 —футеровка; 3—перфорированный стакан с сеткой; 4-г- днище; 5 — штуцер для термопары; 6 — штуцер для вывода газо-продуктовой смеси; 7— штуцер для п со да газо-сырьевой смеси; 8 —распределитель; 9 — перфорированная труба с сеткой; 10—катализатор; Л —фарфоровые шары.
продукты коррозии. Остальные реакторы имеют радиальный ввод для того, чтобы снизить общее гидравлическое сопротивление системы реакторного блока. Водород при 525 °С и 2—4 МПа вызывает водородную коррозию металла. Поэтому изнутри металлическая стенка реактора защищена футеровкой из торкрет-бетона. Кроме того, внутри реактора устанавливают стальной перфорированный стакан, между стенкой которого и стенкой аппарата имеется газовый слой. Нарушение футеровки приводит к перегреву и разрушению стенки реактора. Поэтому необходимо постоянно . контролировать с помощью наружных термопар температуру внешней поверхности металла (должна быть не более 150 °С). Для изготовления корпуса и днищ реактора применяют сталь марки 09Г2ДТ со специальной закалкой поверхности аппарата или сталь 12ХМ.
9 . Закь 380
257
Катализатор размещается в стальном стакане реактора сплошным слоем. Над и под слоем катализатора находятся фарфоровые шары диаметром 16 и 20 мм для предотвращения уноса катализатора. Нижний слой фарфоровых шаров лежит на решетке, дополнительно перекрытой металлической сеткой. Шары, решетка и сетка защищают выводной штуцер реактора от попадания в него катализатора вместе с продуктами реакции. Внутренние детали реактора выполняются из легированной хромоникелевой стали. Сверху в реактор вводится шестизонная термопара, контролирующая температуру внутри реактора. Диаметр реактора 2200—3000 мм, высота 9500—11500 мм.
На проектируемых и строящихся установках корпус и днища реактора выполняются из двухслойной стали J.2XM + 0X18Н1 ОТ и не нуждаются в защитной футеровке.
Рис. 67. Теплообменник реакторного блока риформинга с сильфонным компенсатором:
/ — штуцер для ввода газо-продуктовой смеси; 2— крышка; 3 —корпус; 4 — дисковая перегородка; 5 — штуцер для ввода газс~сырьевой смеси; 6 — крышка плавающей головки; 7—силь-фон; 8 — штуцер вывода газо-продуктовой смеси; 9—кольцевая перегородка; 10 — трубки; 11 — штуцер для вывода газо-сырье-вой смеси; 12—трубная решетка.
Печь риформинга на платиновом катализаторе вертикальная, многокамерная, многопоточная. Отличительной особенностью является змеевик из жаропрочной стали марки Х5МУ диаметром 100—200 мм. Во избежание потерь водорода змеевик выполняется цельносварным. В конвекционных секциях печей устанавливают ошипованные трубы, резко увеличивающие коэффициент теплопередачи от дымовых газов к продукту.
Теплообменники, применяемые в реакторном блоке, ко-жухотрубчатые, но с рядом особенностей. Во-первых, горячий поток из реактора, наиболее активный в отношении коррозионного воздействия, направляется не в межтрубное, как обычно, а в трубное пространство. Во-вторых, эти теплообменники для повышения температурного напора конструируют по принципу строгого противотока: аппараты имеют один ход по трубному и один ход по межтрубному пространству. Это связано с определенными конструктивными трудностями, поскольку необходимо компенсировать тепловое расширение трубок относительно корпуса. В настоящее время существует три типа таких аппаратов: 1) с сальниковым уплотнением, 2) с внутренней трубой и 3) с сильфонным компенсатором (рис. 67).
258
Недостаток теплообменников с сальниковым уплотнением в том, что нериформированный продукт может попадать в продукты ри-форминга. В теплообменниках с внутренней трубой недостаточно эффективно используется поверхность теплообмена. Аппарат третьего типа лишен этих недостатков. На установках большой производительности, где число последовательно включенных теплообменников больше четырех и, следовательно, температурный напор близок к максимальному, применяют кожухотрубчатые теплообменники, с плавающей головкой, одноходовые по межтрубному и двухходовые по трубному пространству. Корпус аппарата выполняется из биметалла марки 12МХ + ЭИ496, а трубный пучок, из стали марки Х5М. Поверхность теплообмена одного аппарата 350— 900 м2. Общая поверхность теплообмена реакторного блока для крупных установок может составлять 1000—3000 м2. Коэффициент теплопередачи примерно равен 230—400 Вт/(м2-°С).
Холодильники реакторного блока могут быть как водяными, так и воздушными. Первые — обычные кожухотрубчатые аппараты, двухходовые по трубному и одноходовые по межтрубному пространству. Вода подается в трубки, продукт — в межтрубное пространство. Аппараты воздушного охлаждения такие же, как и на установке АВТ, но трубки выполняются из легированной стали и рассчитаны на давление 5 МПа. Коэффициент оребрения равен 22.
К наиболее сложному оборудованию реакторного блока относятся сырьевой насос и циркуляционный компрессор. Для подачи сырья применяется центробежный 8-ступенчатый насос, приводимый в движение электродвигателем. Сырьевой насос развивает давление в нагнетательном трубопроводе 5—6 МПа, имеет торцевое уплотнение.
Для циркуляции вбдородсодержащего газа применяют поршневые и центробежные компрессоры. Поршневые компрессоры на оппозитной базе марок 2М16М-20/42-60, 4М16М-45/35-55, 4М16-56/15-30 обеспечивают перепад давления между всасывающим и нагнетающим трубопроводами 1,5—2^0 МПа и подачу до 22,2 м3/с при 0°С и 0,1 МПа. Центробежные компрессоры могут приводиться в движение как от электропривода, так и от паровой турбины. Центробежный турбокомпрессор обладает тем преимуществом, что легко поддается регулированию подачи изменением частоты вращения. Турбокомпрессор для установок производительностью 109 кг/год имеет расчетный перепад давления 1,2—1,5 МПа, подачу 88,8 м3/с при 0°С и 0,1 МПа, мощность 6900 кВт.
§ 53. ВЫДЕЛЕНИЕ АРОМАТИЧЕСКИХ УГЛЕВОДОРОДОВ ИЗ ПРОДУКТОВ КАТАЛИТИЧЕСКОГО РИФОРМИНГА
Продукт, получаемый в результате каталитического риформиро-вания прямогонного бензина, содержит от 30 до 60% (масс.) ароматических углеводородов; остальное составляют цикланы и алканы нормального и изостроения,
9*
269
Получить из этой смеси ароматические углеводороды обычной ректификацией невозможно, так как они образуют с алканами и цикланами нераздельнокипящие (азеотропные) смеси. Для выделения ароматических углеводородов в настоящее время применяют экстракцию.
Сырьем' установки экстракции ароматических углеводородов служат катализаты после риформирования фракций 62—85 °С (28,5% ароматических углеводородов), 62—105°С (37% ароматических углеводородов) и 105—140 °С (45,5% ароматических углеводородов). В качестве растворителей применяют полиэтиленгли-коли, сульфолан, диметилсульфоксид, jV-метилпирролидон.
На отечественных установках для извлечения ароматических углеводородов из катализата платформинга наиболее распространенным экстрагентом является водный раствор диэтиленгликоля (ДЭГ), но его повсеместно заменяют более эффективным три- и тетра этиленгликолями (ТЭГ и тетраЭГ).
Основные свойства полиэтиленгликолей приведены в табл. 13.
ТАБЛИЦА 13
Дата добавления: 2018-04-04; просмотров: 1004; Мы поможем в написании вашей работы! |
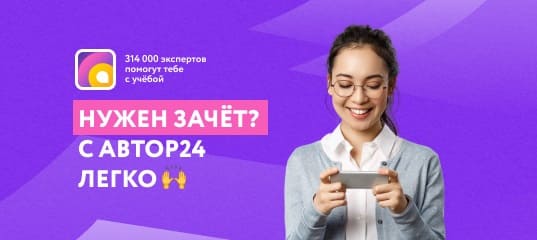
Мы поможем в написании ваших работ!