Определение положения паза под пластину или нож у сборных зенкеров.
Для обеспечения заданных параметров режущей части (φ, γ и λ) у зенкеров, оснащенных пластинками из твердого сплава или сборных зенкеров со вставными ножами необходимо определить угол наклона ω и смещение Е относительно диаметральной плоскости паза под пластинку или нож на торце зенкера.
Для определения ω и Е необходимо знать значения торцевого γт и осевого γо передних углов.
tg γт= tg γ ∙ cos φ – tg λ ∙ sin φ
tg γо= tg γ ∙ sin φ + tg λ ∙ cos φ
tg ω = tg γо∙ cos γт
E = L ∙ tg ω + D/2 ∙ sin γт
Расстояние Н от оси зенкера до дна паза под пластину твердого сплава зависит от диаметра инструмента и ширины пластины в:
Н = D/2 – в + 0,5 δ , где
δ = 0,2…0,4 мм – припуск на шлифование инструмента по диаметру.
Зенковки
Зенковка – многолезвийный режущий инструмент, предназначенный для обработки цилиндрических углублений под головки винтов; конических углублений, для центрования отверстий, отверстий под винты с потайной головкой, снятия фасок, обработки поверхностей бобышек, выступов.
2φ = 60° , 75°, 90°, 120°
γ – обычно равен нулю
α = 8…10°
Для направления в процессе работы зенковки снабжают цапфами.
Профиль канавок зенкера
Тип I– выполняют аналогично профилю канавки сверла, режущая кромка
прямолинейная. Перо имеет ленточку f. Такой профиль делают у
|
|
спиральных трех- или четырехзубых хвостовых зенкеров.
Тип II– криволинейный профиль канавки применяют для четырехзубых
насадных зенкеров. Обеспечивает хороший отвод стружки, но
требуются для фрезерования его специальные фасонные фрезы.
Тип Ш – профиль ограничен по затылку прямыми линиями. Для насадных
зенкеров, особенно оснащенных твердым сплавом, фрезеровать
можно или специальными фасонными фрезами, или обычными
угловыми фрезами.
Развертки.
Развертки разделяют:
1. по способу закрепления: хвостовые и насадные;
2. по способу применения: ручные, машинные;
3. по форме обрабатываемого отверстия: цилиндрические, конические;
4. по конструкции: цельные, сборные, жесткие и регулируемые.
Для ручных и машинных разверток диаметром 3…50 мм ориентировочно число зубьев:
z = 1,5 · √d + (2…4)
для машинных сборной конструкции:
z = 1,2 · √d
Большинство разверток изготавливают с прямым зубом.
Окружной шаг может быть равномерным или неравномерным, но всегда зуб против зуба (для удобства измерения).
Для обработки поверхности с пазами применяют развертки с винтовым зубом. Направление винтовых зубьев обратно направлению резания.
|
|
Диаметр калибрующей части зависит от диаметра отверстия. При его определении необходимо учитывать разбивку (или усадку) отверстия, допуск на её изготовление, изнашивание.
|
ΔА изг принимают равным 1/3 ΔА.
ΔАразб.мах = ΔА изг = ΔА/3;
Запас на изнашивание ΔА изг ≈ 0,6ΔА при Н5; ΔА изг ≈ 0,55 ΔА при Н7;
ΔА изг ≈ 0,45ΔА – Н8.
|
Твердосплавные развертки маленьких размеров диаметром меньше 12 мм делают с цельной твердосплавной частью, диаметром от 11 до 30 с впаянными в корпус пластинками, диаметром 18…70 – со вставными ножами закрепленными клиньями или механическим путем, диаметром 70…300 мм применяют двухлезвийные ножи.
Конические развертки.
Для получения конических отверстий обычно применяют комплекты разверток (ГОСТ 10082-71) их трех или двух штук.
Развертка №1 имеет ступени на зубьях, расположенных по винтовой линии, направление которой совпадает с направлением резьбы.
|
Развертка №2 прямоугольная резьба имеет направление обратное направлению предыдущей развертки.
|
|
|
Развертка №3 имеет гладкие зубья заточенные по всей длине.
Расточные инструменты.
Применяются на токарных, револьверных станках, автоматах, полуавтоматах, автоматических линиях и расточных станках.
Для расточных операций применяют следующие типы инструментов:
1. стержневые резцы с одной режущей кромкой;
2. двусторонние пластинчатые резцы (резцы-блоки) с двумя или более режущими кромками;
3. расточные головки с одной или несколькими режущими кромками.
Стержневые резцы крепят или в суппорте станка или в оправке.
Державки различной формы – круглые, квадратные, прямоугольные.
Установка расточных резцов в оправках может быть прямой и наклонной, при которой можно обрабатывать торцы деталей и точнее проводить регулировку вылета резца.
Необходимо учитывать, что вершина резца оказывается смещенной относительно оси оправки и относительно оси детали при выполнении паза по центру (что проще).
Отсюда применяются углы α и γ.
Закрепление может быть регулируемым и нерегулируемым. Регулирование обычно с помощью винтов. Для примера:
1- резец
2- втулка
3- дифференциальный винт
|
|
4- винты для крепления втулки
5- винт для закрепления винта.
Недостаток: малая размерная стойкость резцов; деформации оправки.
Для устранения деформаций применяют двусторонние резцы. При этом силы резания уравновешиваются. Двусторонние стержневые резцы применяют редко, т.к. при износе необходимо регулировать на размер. Вместо них применяют пластинчатые резцы. При переточках сохраняется диаметральный размер.
|
Также существует сборная конструкция таких резцов из двух пластин, которая позволяет регулировать рабочий размер резца.
|
Расточные блоки состоят из корпуса с одной или несколькими парами регулируемых на необходимый размер резцов.
Блоки можно удобно настраивать на размер перед установкой в оправку.
|
Расточные головки имеют большую производительность.
Имеют корпус с посадочной поверхностью в котором устанавливают режущие элементы.
Фрезы.
Классификация фрез:
1. по виду и назначению: цилиндрические, дисковые, концевые, торцовые, фасонные.
2. по направлению зубьев фрезы: прямозубые, косозубые и с винтовыми зубьями.
3. по конструкции: цельные, составные, сборные, наборные.
4. по форме зуба: острозаточенные и затылованные.
5. по способу крепления на станке: насадные с отверстием под оправку, концевые с коническим и цилиндрическим хвостовиком.
|
6. по материалам: быстрорежущие стали, твердосплавные; оснащенные минералокерамической и композиты
фрезы с затылованным профилем задней поверхности используются в основном для фасонных фрез. Для остальных случаев наиболее распространены фрезы с острозаточенной задней поверхностью.
К общим конструктивным элементам всех фрез относится:
· диаметр фрезы
· посадочные размеры
· число зубьев и их форма
Наружные диаметры фрез стандартизованы. Ряды диаметров составлены по геометрической прогрессии со знаменателем φ=1.26; 1,58
dф.п. = dф(n-1) · φ , где
n – порядковый номер диаметра. (dф от 3 до 1000).
Диаметр посадочного отверстия - в зависимости от наружного диаметра, но не более 60 мм и округляется до стандартного ряда: 16, 22, 27, 32, 40, 50, 60 мм.
Определение наружного диаметра и диаметра посадочного отверстия.
Диаметр фрезы следует выбирать минимально возможный с целью снижения машинного времени обработки:
У насадных фрез dф должен обеспечивать прочность фрезы в сечении между окружностью впадин и посадочным отверстием, а также достаточную жесткость оправки. Исходя из этого dф для цилиндрических, дисковых, концевых фрез определяют по формулам, полученным опытном путем.
При выборе dф для торцовых фрез необходимо учитывать, что при заданной ширине заготовки врезании зуба должно происходить при толщине среза больше радиуса округления режущего лезвия.
Надо отметить также, что диаметр фрезы оказывает влияние на шероховатость поверхности при определенной подаче на зуб.
Расчетные диаметры округляют до ближайшего стандартного размера.
Диаметр посадочного отверстия:
d=dф /2,25
округляют до стандартного. Точность обычно Н7.
Число зубьев фрезы.
Число зубьев фрезы выбирают из условия равномерности фрезерования с учетом эффективной мощности оборудования.
Для дисковых фрез всех типов для улучшения равномерности:
z=360·к/ψ , где
к- коэффициент равномерности фрезерования;
ψ- угол контакта фрезы с заготовкой.
Соsψ=1-2t/dф
При проектировании стандартных фрез для черновой обработки:
z=(Сz·dф )/(√Sz·t)
где Сz =0,2 – для цилиндрических и дисковых фрез;
Сz =0,6 - для торцовых фрез.
Эта формула получена из условия оптимального размещения стружки.
Для стандартных фрез для чистовой обработки:
nn –число переточек
хn = 0,15…0,25 мм - слой, снимаемый при первой переточке.
Для достижения равномерности фрезерования зубья выполняют по винтовой линии с углом наклона ω, обеспечивающим постоянство сечения срезаемой стружки в каждый момент времени.
Где к=1, 2, 3 – целое число.
Максимальное число зубьев фрезы определяют в зависимости от эффективной мощности оборудования по эмпирическим формулам.
Геометрические параметры фрез выбирают в зависимости от обрабатываемого материала.
Профиль зубьев фрезы.
Шаг зубьев зависит от dф, условий работы (черновая, чистовая), свойство материала.
Для черновой обработки применяют фрезы с крупным зубом Рt >10 мм.
Для чистовой обработки – фрезы с мелким зубом.
В зависимости от шага применяют три типа профилей зубьев. Для фрез с мелким зубом принята трапециидальная форма профиля. Угол тела зубьев η=47…52º
Н=(0,5…0,65)·Рz
У фрез с винтовыми зубьями η рассматривают в нормальном сечении.
Крупнозубые фрезы имеют профиль зубьев либо криволинейный либо двухугловой.
|
Н= (0,3…0,45)Рt
|
R= (0,3…0,45)dф
r1 =(0,4…0,75)Н
Расчет положения зуба в корпусе торцевой фрезы.
|
Расчет выполняется аналогично как для зенкера, но с учетом того как обозначен угол φ. Угол ω паза под нож и его смещение Е рассчитывают так, чтобы обеспечить получение заданного переднего угла γ на вершине лезвия и угла наклона режущей кромки λ без дополнительной заточки плоского ножа при выбранном угле в плане φ.
tgγт=tgγ·Sinφ+tgλ·Cosφ
tgγo=tgγ·Cosφ-tgλ·Sinφ
tgω=tgγo·Cosγт
Е=e- L·tgω, e= (dф/2)·Sinγт
Е=(dф/2)·Sinγт -L·tgω
Широкое распространение получили сборные фрезы оснащенные твердосплавными многогранными пластинами. Конструкции таких фрез отличаются большим многообразием.
При проектировании торцевых фрез, оснащенных многогранными пластинами, угол наклона пластины ω и смещение Е паза под пластину или державку ножа рассчитывают так, чтобы получить на режущих лезвиях заданные главный α и вспомогательный α1 задние углы.
tgω=tgγo·Cosγт
tgγт=tgμ·Sinψ
tgγo=tgμ·Cosψ
|
Смещение вершины зуба А относительно оси фрезы:
e= (dф/2)·Sinγт
Е1=Н-b·Sinω-e
Н-высота державки
Если пластину устанавливают в корпусе инструмента, то смещение паза относительно оси корпуса:
Е=e-с·Соsω, где
e-толщина пластины.
Фасонные фрезы.
Имеют фасонную производящую поверхность, на которой расположены зубья. Фасонные фрезы обрабатывают сразу весь контур детали, поэтому они имеют высокую производительность.
Фасонные фрезы применяют как затылованные, так и острозаточенные.
Фрезы с затылованными зубьям.
Эти фрезы затачиваются по передней поверхности при этом форма задней поверхности должна обеспечивать постоянство профиля режущей кромки при повторных заточках.
Фрезы могут быть со шлифованным и нешлифованным профилем. Первые применяют при высоких требованиях к точности профиля детали.
На практике применяют три способа затылования:
· радиальное, при котором затыловочный резец перемещают перпендикулярно оси фрезы;
· угловое, при котором резец перемещают под некоторым углом к оси фрезы;
|
· осевое, при котором резец перемещают параллельно оси фрезы.
Наибольшее применение имеют два первых способа затылования:
Один оборот за 1/z поворота фрезы. Спад спирали обычно на угле 60º.
АВ=(π·dф)/z
К=(π·dф·tgα)/z
К- округляют до значений стандартного ряда.
Величину К рассчитывают для точки максимального диаметра фрезы и откладывается во всех сечениях профиля фрезы перпендикулярных её оси.
Для произвольного радиуса фрезы rх радиальный задний угол αrx рассчитывают по формуле:
tgαrx = (dф/2·tgα)/drx/2=rф/rх · tgα
tgα=tgαrx · Sinφх или
|
tgαx =rф/rх · tgα · Sinφх , необходимо чтобы αx>2º это может быть выполнено, если φх>5º. Минимальные задние углы можно увеличить или уменьшить разность задних углов для различных участков профиля, если применить угловое затылование.
К1 = К· Sinτ
|
К2 =К·Cosτ
Конструктивные элементы.
Выполняют главным образом насадными.
|
Для дисковых фасонных фрез:
1. диаметр посадочного отверстия: d0=5,28·h0,48·В0,15, где h- глубина фрезерования; В- ширина фрезерования.d0- округляют до ближайшего стандартного.
2. наружный диаметр фрезы: dф=2,5·d0, округляют до большего оканчивающегося на 0 или 5 размера при dф<100 мм
3. число зубьев: z=(π·dф)/(А·h1), где
А=1,8…2,5 – для черновых фрез
А=1,3…1,8 – для чистовых фрез.
h1- высота профиля фрезы.
z- округляют до ближайшего целого, лучше четного.
4. радиус закругления дна впадины: r1 =(dф/2- h1-К)/Sinψ/2;
. К-величина затылования.
5. высота зуба: Н=h1+К+r1
6. уголвпадины: θ = ψ + μ , где μ=15…20º - угол обеспечивающий прочность максимально переточенного зуба.
Ψ = ε/5; ε = 2π/z
7. ширину фрезы В определяют в зависимости от характера профиля фрезы.
Фрезы с положительным передним углом.
Применяются в тех случаях, когда необходимо увеличить стойкость фрезы или уменьшить шероховатость обработанной поверхности.
Применение положительного переднего угла γв при вершине зуба вызывает необходимость производить корреляционный расчет профиля. При этом определяют высоту профиля hfх для произвольного радиуса rх в плоскости передней поверхности и высоту hх в осевом сечении.
Первый расчет необходим для контроля точности профиля, второй – для изготовления фрезы.
Размеры зуба по ширине фрезы применяются.
|
tgγх(N-N) = (dф/2·rх)·tgγв · Sinφх
При шлифовании профиля диаметр круга не должен быть меньше 80 мм. Чтобы круг не срезал профиль следующего зуба, шлифуют не на всю ширину зуба.
|
Для устранения седловины, фрезы подвергают двойному затылованию. К1=(1,2…1,5)К.
Фасонные острозаточенные фрезы.
Острозаточенные фрезы по сравнению с затылованными обеспечивают более высокие производительность и стойкость, вследствие большего числа зубьев и отсутствие обезуглероженного слоя, удаляемого при переточках по задней поверхности.
При переточках затылованных фрез с передней поверхности удаляется в 4-5 раз больший слой, чем при заточке острозаточенных по задней поверхности.
Однако изготовление и переточки довольно сложны, так как требуются перемещения шлифовального круга по специальной кривой , для чего применяют шлифование по копиру и станки с программным управлением.
|
Инструменты для образования резьбы.
Основными способами получения резьбы являются:
· вырезание профиля резьбы режущим инструментом;
· выдавливание профиля резьбы;
· накатывание профиля резьбы.
Обработку резанием осуществляют: резьбовыми резцами; гребёнками; метчиками; резьбовыми плашками; резьбонарезными головками; резьбовыми фрезами; шлифовальными кругами.
При выдавливании инструмент с деталью работают по принципу пары скольжения без зазора.(бесстружечные метчики).
При накатывании – пары качения, что уменьшает силы трения (резьбонакатные ролики, резьбонакатные плоские и сегментные плашки и др.).
Наиболее распространенным и дешёвым являются метчики и плашки-лёрки. Они применяются во всех видах производства.
Метчики.
По принципу работы их подразделяют:
· метчики, образующие профиль путем снятия стружки;
· метчики, образующие профиль без снятия стружки – бесстружечные;
· метчики, образующие резьбу комбинированным способом.
По конструкции и применению метчики делят на следующие типы:
· машинно-ручные
· машинные
· гаечные
· конические
· метчики для круглой резьбы
· метчики сборной конструкции, нерегулируемые и регулируемые
· специальные, комбинированные, ступенчатые и др.
Конструктивные элементы метчиков.
К основным конструктивным элементам метчиков относят:
|
· режущая (заборная) часть (1);
· калибрующая часть (2);
· хвостовик (3) с элементами крепления (4,5);
· форма зуба (6);
· форма стружечной канавки (7) и её направление;
· геометрические параметры режущей и калибрующей частей;
· профили резьбы метчика и её размеры.
Основную работу резания выполняет режущая часть.
Схемы резания при нарезании резьбы метчиком.
1. В большинстве случаев режущая часть срезает слои металла по генераторной схеме резания. Конструкция проста, но кромки трутся о металл, что может привести к срыву вершины резьбы.
|
Режущую часть по заборному конусу затылуют.
К=(π·d)/z · tg α
α - задний угол на наружном диаметре.
α=4…20º и выбирается по справочной литературе.
2. применяют также и профильную схему резания.
|
Изготовление такого метчика значительно сложнее, т.к. режущие кромки с трех сторон, а значит и задние углы должны быть со всех сторон, поэтому затылование проводят по всему профилю.
При этом ухудшается его затягивание в отверстие.
3. применяют также в особенности при обработке ТОМ генераторную корригированную схему.
|
α1=55º при α=60º
В этом случае уменьшается трение:
|
Высота выступов на профиле резьбы зависит от а.
Основные конструктивные элементы метчика.
Диаметр по торцу метчика: dт =d1 (0,1…0,35).
Во многих случаях длину режущей части от торца до калибрующей части задают и тогда угол заборного конуса φ уточняют по формуле:
tg φ=(d - dт)/2·l1
l1 назначают в зависимости от вида отверстия (глухое, сквозное), типа метчика (машинный, гаечный) и номера метчика в комплекте.
Число режущих кромок:
N = (l2 ·z)/р, где
l2 - длина режущей части, участвующая в резании.
l2 = (d - dN)/2 ·tgφ;
dN- диаметр отверстия под резьбу (dN> d1 ).
|
z - число зубьев; р – шаг резьбы.
Подъем на зуб: аz=(hз ·Cosφ)/n
аz оптим.= 0,02…0,15 мм
для стали: аz опт= 0,02…0,05 мм
чугуна: аz опт= 0,06…0,07 мм
Значение переднего угла γ на режущей и калибрующей частях принимают одинаковым. Его величина зависит от материала заготовки. (γ=5…30º).
|
Метчики по калибрующей части могут без затылования по профилю, с затылованием на 2/3 ширины пера и с затылованием по всей ширине пера. К=0,01…0,02мм.
Метчики d<10 мм не затылуют. Гаечные затылуют на 2/3 ширины пера. Затылование уменьшает трение. Так же мерой по снижению трения является выполнение обратной конусности (0,04…0,08 на 100 мм длины).
Для лучшего направления и устранения подрезания резьбы острыми кромками калибрующих зубьев метчики иногда выполняют с бочкообразными зубьями.
|
При нарезании резьбы в заготовках из пластичных материалов рекомендуется применять с вырезанной в шахматном порядке ниткой.
|
Форма стружечных канавок.
Стружечные канавки должны обеспечивать достаточно хороший отвод стружки, не создавать концентратов напряжений, обеспечивать достаточно высокую прочность зуба и метчика в целом, отсутствия среза стружки при выворачивании.(число канавок равно 2-6 при применении d в пределах 2…52 мм).
Основными параметрами профиля канавки являются: передний угол γ, диаметр сердцевины dс, радиус у основании зуба R, радиус по спинке зуба r, ширина пера F, и угол не рабочей кромки μ.
|
dс и F назначают в зависимости от числа зубьев z. Угол μ=80…85º, что позволяет устранить защемление стружки и возможность среза обработанной поверхности.
Обычно канавки делают прямыми. Для глухих отверстий для лучшего отвода стружки применяют винтовые канавки с одноименным направлением наклона. Для сквозных – обратное направление – стружка вперед.
Допуски на профиль резьбы метчика.
|
Метчик должен быть значительно точнее обрабатываемой детали.
Допуски на элементы резьбы метчиков назначают по стандартам. Для машинноручных ГОСТ 3266-71. для гаечных ГОСТ 1604-71. Размеры допусков зависят от точности резьбы: метчики класса точности Н1 предназначены для резьб с классом точности 4Н, 4Н5Н, 5Н, 6Ст;
2-й (Н2) – 5Н6Н, 6Н, 6Ст, 7Ст;
3-й (Н3) – 6Н;
4-й (Н4) – 6Н, 7Н.
d2- является основной величиной , характеризующей степень точности метчика.
Назначают допуск – с учетом погрешностей на изготовление и гарантированного запаса на изнашивание и разбивку.
|
|
Верхнее отклонение можно было бы не ограничивать, т.к. d не может быть больше предельного. Однако в этом случае заостряется зуб и ускоряется его износ. Для р≤0,75 верхнее отклонение не ограничивают, в остальных случаях его назначают как для метрических резьб по ГОСТ 16425-71.
Внутренний диаметр d1 не должен срезать стружку, поэтому верхнее отклонение меньше или равно нулю. Нижнее отклонение не ограничивают, т.к. у шлифовального круга всегда есть радиус.
|
Допуск на половину угла профиля при р=0,25…5,0 мм для метчиков 1, 2, 3 класса точности колеблется в пределах ±(40´…15´) и ±(80´…20´) для 4 класса точности.
Шаг резьбы метчика имеет также очень жесткие допуски.
Для метрических резьб на длине 25 витков предельные отклонения равны ± 0,05 мм (Н4) для нешлифованных метчиков. Для шлифованных - ± 0,06…0,012 мм (Н1, Н2, Н3).
Плашки.
Предназначены для нарезания наружных резьб.
Основные конструктивные элементы круглых плашек:
· режущая часть;
· калибрующая часть;
· число, диаметр и расположение стружечных отверстий;
· ширина пера и его форма;
· наружный диаметр;
· ширина плашки;
· элементы крепления.
|
l1 =l2 – режущие части (l1=(3…4)р).
Угол конуса φ и длина режущей части зависят от материала заготовки. (2φ=25…90º).
d - наружный диаметр;
d1 - внутренний диаметр.
Режущую часть затачивают по передней и задней поверхностям.
Угол γ (передний) задают в зависимости от материала заготовки (10…30º) на внутреннем диаметре.
Задний угол также задают на внутреннем диаметре d=6…9º. Его определяют по величине затылования:
К=(π·d1)/z · tg α
Длина калибрующей части lк принимают равной (3…5)р, отсюда Н=(6…10)р.
По профилю резьбы плашки не затылуют и не шлифуют. Они нарезают резьбы не выше 6, 8 степеней точности.
Оптимальным отношением ширины пера к расстоянию между перьями считают F/с=0,65…0,8.
Число перьев z назначают в зависимости от диаметре резьбы (3…12).
Централизованно выпускаемые плашки имеют цилиндрическую форму стружечных канавок, образуемых сверлением. Диаметр их dс определяют в зависимости от ширины пера и расстояния между перьями.
Наружный диаметр D=d1 + 2dс + 2Е.
По наружному диаметру и ширине плашки унифицированы.
Плашки закрепляют или в воротке или в патроне. Для чего выполняют три или четыре конических углубления.
Дата добавления: 2018-06-27; просмотров: 392; Мы поможем в написании вашей работы! |
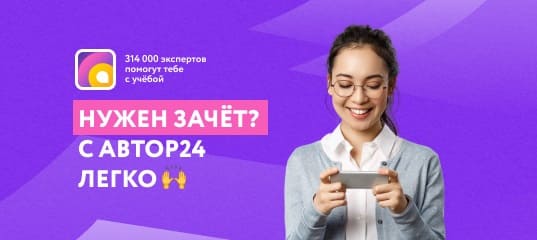
Мы поможем в написании ваших работ!