Коническая форма задней поверхности сверла.
В этом случае задняя поверхность является участком конической поверхности, ось которой параллельна проекции главной режущей кромки на торцовую плоскость.
1) Для образования задних углов вершина конуса должна быть смещена относительно оси сверла на величину, равную или больше радиуса перемычки.
2) Для обеспечения заданных величин α, φ, ψ:
a) ось качания SOнавертывают на угол δ по отношению к образующей шлифовального круга
δ = φ – σ ,
σ – зависит от конструкции станка;
b) устанавливают определенную величину «f» (вылет сверла условный, определяется расчетным путем). Чем больше α, тем меньше f.
c) находится величина «К». Чем больше «К», тем больше α.
Недостатком является, что поперечная кромка близка к прямой линии, а также технологический недостаток: необходимость поворота при заточке на 180°.
Винтовая форма задней поверхности.
Шлифовальный круг имеет два движения за один оборот сверла.
V – общая скорость круга относительно сверла
Vосц– скорость осциллирующего движения
Vз– скорость затылования
Со– размер характеризует положение сверла относительно круга, при формировании режущей кромки.
tgαх= Vз / ω ∙ rх , где
rх– радиус точки режущей кромки
Два движения, вращательное и поступательное, дают винтовую линию.
αх– угол подъема винтовой поверхности
В некоторые моменты времени вершина сверла выходит за угловую кромку круга. Вследствие этого происходит заострение поперечной кромки.
|
|
Заточка позволяет получить более рациональное распределение значений задних углов и более выпуклую поперечную кромку ( что улучшает центрирование).
У сверл с винтовой задней поверхностью увеличиваются значения задних углов на поперечной кромке, что уменьшает осевые нагрузки.
Большим преимуществом является возможность автоматизировать процесс заточки.
Особенности сверл для обработки различных материалов.
1. Универсальные сверла
2φ = 118…120°, α = 9…12°, обратная конусность 0,08…0,12 мм на 100 мм длины.
Ширина пера равна примерно ширине канавки
Для улучшения условий резания часто применяют разные методы:
– Д – двойную заточку (улучшение условий работы уголков сверла)
– П – с подточкой перемычки
– Л – с подточкой ленточки
2. Для материалов повышенной и высокой прочности HRCдо 45,
σвдо 125 кг/мм² ; особо высокой – HRCдо 52, σвдо 150 кг/мм²
ω = 30…35°, но переднюю поверхность затачивают специально
Основная беда – большой крутящий момент. Для его уменьшения увеличивают 2φ до 150°, двойную заточку не применяют, сверла делают как можно короче.
|
|
Перо сверла выполняют шире, чем канавка, а ленточку едва заметной за счет увеличения диаметра спинки.
dс= до 0,5 d с обязательной подточкой перемычки.
Для облегчения отвода стружки сверло снабжается стружкоделительными канавками (для сверл большого диаметра).
Для более мелких – полирование и хромирование канавок, подвод СОЖ через канал в тело сверла.
Для уменьшения трения делают больше обратную конусность (в 2 раза) и уже ленточки (примерно в 2 раза).
Сверла снабжают усиленным хвостовиком.
3. Сверла для мягких, легких сплавов, дающих сливную стружку (мягкие, слоистые пластмассы).
Увеличенный ω до 45°; 2φ до 140°; α до 20°
Ширина канавки больше ширины пера
4. Для хрупких цветных металлов (бронза, твердые пластмассы – эбонит, вулканит).
ω = 10…20°; 2φ = 130…160°; α = 12…15°
Соотношение сечений как в обычных сверлах, но канавки несколько шире.
Твердосплавные сверла.
Применяют для обработки отверстий в твердых материалах небольшой прочности (чугун, цветные металлы, пластмассы, мрамор, гранит и др.).
Мелкие сверла Ø 1,0…12 мм делают целиком из твердого сплава (ГОСТ 17273 – 71, ГОСТ 17274 – 71) и со стальным хвостовиком, в который впаивают твердосплавную рабочую часть (ГОСТ 17275 – 71).
|
|
Сверла диаметром от 5 до 30 мм оснащают пластинами из твердого сплава (ГОСТ 22735 – 77, 22736 – 77).
Недостаток: ослабляется корпус в месте расположения пластины.
Дата добавления: 2018-06-27; просмотров: 470; Мы поможем в написании вашей работы! |
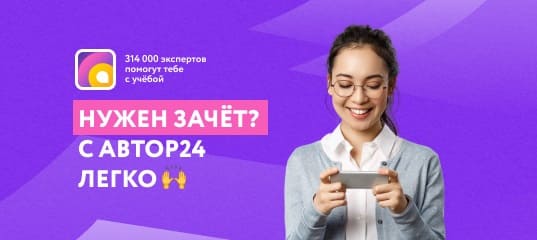
Мы поможем в написании ваших работ!