Автоматизация работы ТСК и управления ПРМ и механизмами
![]() |
Многие транспортно-грузовые системы перерабатывают большие грузопотоки, в том числе одинаковых или подобных грузов. В этих условиях высокая экономическая эффективность лигистических систем доставки грузов может быть достигнута посредством широкой автоматизации погрузочно-разгрузочных работ, транспортных и складских(ПРТС) работ, подъемно-транспортных машин и переработки информации, складского документооборота и учета грузов.
Сущность автоматизации состоит в том, что производственные процессы, в том числе операции основного технологического процесса производства и связанные с ними ПРТС работы выполняются без участия человека (или с минимальным участием человека - в зависимости от степени автоматизации операций) автоматическими машинами и механизмами. В промышленности автоматизируются основные технологические процессы производства продукции и связанные с ними ПРТС работы, как часть комплексной технологии производства. В торговле и на транспорте автоматизируются перегрузочные, комплектовочные, сортировочные операции, транспортировка и складирование грузов, формирован ие транспортных пакетов и т.д.
Устройство и принцип действия вил у погрузчика.
К числу наиболее простых и распространенных захватных приспособлений относятся вилы, используемые для захвата тарно-штучного груза, уложенного на поддон или прокладки. В зависимости от типа погрузчиков и перерабатываемого груза вилы имеют длину от 0,5 до 2,5 м. Вилочный подхват состоит из вил Г-образной формы. Вилы можно передвигать на поперечной балке каретки, устанавливая между ними нужное расстояние.
|
|
При перемещении крупногабаритных легких грузов, не размещающихся на вилах стандартной длины, применяются надеваемые на эти вилы удлинители, которые увеличивают длину вил в пределах устойчивости погрузчика. При
работе погрузчика с грузами, упакованными в тюки, пакеты, кипы, применяются сталкиватели грузов.
Универсальным вилочным захватом можно перемещать различные тарно-штучные грузы в ящиках, кипах, бочках в непакетированном и пакетированном виде(отдельными грузовыми местами) в складских помещениях, вагонах, трюмах судов и на открытых площадках. Отличительная особенность его - крепление вил к подвижным кареткам, что позволяет поворачивать их на 45°,90° и 180° вокруг горизонтальной оси. При повороте вил на 45° можно перегружать катно-бочковые грузы, а при повороте на 90° - пакеты из ящиков, кип и др. Поворот на 180° увеличивает высоту подъема груза с 2,75м до 3,3м.
С помощью погрузчиков, оборудованных вилами, перегружают отдельные места грузов большой массы, пакеты на поддонах, грузы в мягкой таре. Для грузовых мест больших размеров используют удлинители вил.
|
|
Чтобы предотвратить падение груза с вил и разрушение пакетов, применяют прижимы. Прижим повышает производительность автопогрузчиков в 1,5 раза, так как надежно удерживать груз, а это позволяет увеличить скорость транспортирования.
В зависимости от требуемой высоты подъема груза одни и те же электропогрузчики могут иметь разные грузоподъемные механизмы. Грузоподъемные механизмы с разной высотой подъема различаются длиной рам, цилиндров и цепей. Все они оснащены телескопической рамой, кареткой, на которую устанавливают сменные грузозахватные приспособления, цилиндром подъема, двумя цилиндрами наклона, траверсой с направляющими блоками или звездочками и грузовыми цепями.
Устройство грузоподъемного механизма рассмотрено на примере базового электропогрузчика ЭП-103-УКП. Он имеет наружную и внутреннюю рамы в виде вертикальных стоек корытообразного сечения, выполненных из листовой стали штамповкой и соединенных между собой поперечными связями. В нижней части внутренней рамы с наружной стороны и в верхней части
наружной рамы с внутренней стороны установлены кронштейны с роликами и для ограничения поперечного перемещения внутренней рамы.
|
|
Эти ролики посажены на эксцентрические оси, поворачивая которые можно регулировать боковой зазор между рамами. Для уменьшения трения при перемещении внутренней рамы внутри наружной в каждую ее стойку вварены две оси с установленными на них катками, вращающимися на подшипниках. Цилиндр подъема закреплен корпусом на шаровой пяте основания наружной рамы, а на телескопической головке его плунжера установлен направляющий блок. Через блок перекинута цепь, один конец которой прикреплен к грузовой каретке, а другой к корпусу цилиндра. Телескопическая головка обеспечивает подъем плунжера на высоту 100 мм без увеличения габаритной высоты погрузчика, что соответствует подъему каретки на 200 мм. Каретка грузоподъемника неразборная. Она представляет собой плиту с вырезами. К средней ее части прикреплены кронштейны с вваренными в них цапфами, на которых смонтированы направляющие катки на шарикоподшипниках. К тем же кронштейнам болтами закреплены обоймы с боковыми роликами, воспринимающими боковые усилия. К плите каретки приварен также кронштейн, предназначенный для закрепления тяговой цепи с устройством для ее натяжения. Вилы, устанавливаемые на плите каретки, перемещаются по ширине и фиксируются в необходимом положении пружинными фиксаторами. На каретке может быть установлено и другое сменное рабочее приспособление—различные захваты, штыри, крановая стрела и т. д. Наружная рама шарнирно прикреплена к кронштейнам корпуса погрузчика.
|
|
С помощью двух гидроцилиндров грузоподъемник может наклоняться вперед на 3°и назад на 10°. Гидроцилиндры наклона поршневого типа двустороннего действия, их крепят шарнирно одним концом к корпусу электропогрузчика, а другим к кронштейнам наружной рамы. Синхронность работы гидроцилиндров регулируют изменением длины штоков, ввертывая их в головку.
Заключение
В первом разделе курсовой работы были рассчитаны объемы работ для каждого вида груза. Для тарно-штучных грузов ∑Qгод = 560тыс т/год, для КТК ∑Qгод = 2310тыс.т/год, для леса круглого ∑Qгод = 2520тыс т/год.
В остальных разделах мной была выполнена работа по расчету основных характеристик заданных типов ПРМ, выгодных для них складов, а также были учтены наиболее рациональные пути переработки грузов.
Во втором разделе я выбирала наиболее эффективное средство КМАПРР для каждого вида груза. Таким образом получилось, что для переработки тарно-штучного груза наиболее выгодным средством является вилочный электропогрузчик ЭП-103-УКП и кран-штабелер мостового типа;для переработки лес круглый - козловой кран ККУ-10; для переработки КТК - мостовой кран.
В третьем разделе я рассчитывала основные параметры склада. Для тарно-штучного груза при переработке электропогрузчиком ЭП-103 длина склада с учетом пожарных выходов составила Ьскл=126м, емкость склада Е=1608,552т, площадь склада F=3217,044 м2, мостовым краном емкость склада составила Е= 1608,552т, площадь склада F=3217,044 м2, длина склада с учетом пожарных выходов Lскл=282м.
В четвертом разделе я определяла производительность и количество ПРМ. Таким образом получилось, что для переработки тарно-штучных грузов необходимо 3 электропогрузчика и 4 мостовых кранов.
Сменную производительность мостового крана я взяла из ЕНВ, она численно равна нормам выработки. Нвыр=Псм=196 т/см., а эксплуатационную и техническую рассчитала и получилось, что Пэ=28 т/ч, Птех=35т/ч.
Чтобы рассчитать техническую, эксплуатационную и сменную производительности для электропогрузчика я должна была рассчитать время одного цикла. Рассчитав время цикла, я получила, что Птех=45т/ч, Пэ=7,2т/ч,
Псм=50,1 т/см.
В пятом разделе я рассчитала основные технико-экономические характеристики ПРМ и выбрала наиболее рациональный вариант для переработки тарно-штучного груза. Рассчитав заданные мне параметры, я убедилась, что для моего варианта наиболее выгодным будет являться электропогрузчик ЭП-103-УКП, так как его основные характеристики значительно лучше, чем у второго варианта - мостового крана, данные показатели также были подтверждены экономическими показателями.
В шестом разделе уже для выбранного средства переработки, а именно электропогрузчика я составляю контактный технологический график грузового пункта по определенным расчетам: работы автотранспорта, интервала подачи вагонов на грузовой пункт, числа погрузок в автотранспорт, затрат механизмо-часов при переработке одной подачи, числа плдач,имеющих долю прямой переработки, количества груза,перерабатываемого по прямому варианту, затрат механизмо-часов на подачу по прямому варианту, затрат механизмо-часов для подач, имеющих прямой вариант, но при переработке груза в склад, общих затрат механизмо-часов, пр переработке из склада в автотранспорт.
В седьмом разделе я отражаю основные положения безопасности при работе на ж.д. станциях и грузовых пунктах; требования безопасности при выполнении ПРР; требования безопасности при переработке тарно-штучного груза; экологические мероприятия на станциях и в ГРС.
В восьмом разделе разделе описываю организацию технического обслуживания ПРМ. Указываю периодичность и продолжительность всех видов технического обслуживания и ремонтов для выбранного мною электропогрузчика ЭП-103-УКП.
В девятом раздел план-разрез крытого склада для тарно-штучных грузов, стреловой кран и грузозахватное устройство у ЭП-103-УКП - вилы.
Все произведенные мною расчеты укладываются в общепринятые нормы и соответствуют всем железнодорожным стандартам.
Список использованных источников
1. Журавлев Н.П., Маликов О.Б. Транспортно-грузовые системы: Учебник для вузов ж.-д. транспорта. - М.: Маршрут, 2006.-368с.
2. Гундорова Е.П. Технические средства железных дорог: Учебник для техникумов и колледжей ж.-д.транспорта. - М.: Маршрут, 2003. - 496с.
3. Гриневич Г.П. Комплексная механизация и автоматизация погрузочно-разгрузочных работ на железнодорожном транспорте: Учебник для вузов ж.-д. трансп. 4-е издан., переработ, и доп. - М.: Транспорт,
1981. - 343с.
4. Падня В.А. Погрузочно-разгрузочные машины: Справочник. - 4-е изд., перераб. и доп. - М.:Транспорт, 1981. - 448с., ил., табл.
5. Единые нормы выработки и времени на вагонные, автотранспортные и складские погрузочно разгрузочные работы. - М.:Транспорт, 1977.
6. Киреев B.C. Механизация и автоматизация погрузочно-разгрузочных работ: Учебник для техникумов. - М.: Транспорт, 1992. - 352с.
7.Игнатов А.П. Погрузочно-разгрузочные машины на железнодорожном транспорте: Учебник для техникумов и колледжей железнодорожного транспорта. - М.: УМК МПС России, 2002. - 384с.
8. Методические и справочные материалы по «организации и механизации грузовой работы» :методическое пособие для дипломного и курсового проектирования. Часть 1.: Екатеринбург- 1996.
9. Политов В.В., Брагин A.M. Комплексная механизация и автоматизация погрузочно-разгрузочных работ: учебно-методическое пособие.Екатеринбург, 1999.
10. Плахович С.А., Фролова И.С. Складское хозяйство. Часть 2. Учебно-методичиское пособие для студентов. УрГУПС. Екатеринбург. 2008.
И.Тимошин А.А., Мачульский И.И.
Дата добавления: 2018-06-27; просмотров: 331; Мы поможем в написании вашей работы! |
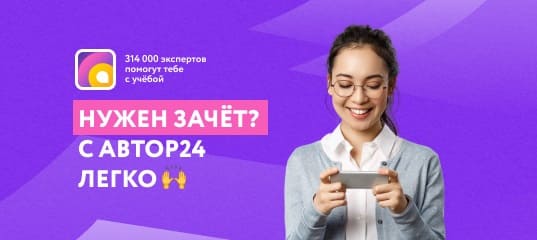
Мы поможем в написании ваших работ!