Экономическое обоснование принятого варианта технологического процесса
В курсовом проекте сравниваются два возможных варианта изготовления детали. При этом применяется методика, изложенная в [2].
Все расчеты настоящего раздела выполняются с использованием цен и тарифных ставок, действующих в Республике Беларусь на момент выполнения расчетов.
При оценке эффективности того или иного варианта техпроцесса наиболее выгодным признается тот, у которого сумма текущих и приведенных капитальных затрат на единицу продукции будет минимальной.
Расчеты приведенных затрат и технологической себестоимости выполняются для всех изменяющихся операций технологического процесса.
Приведенные затраты для двух сравниваемых вариантов техпроцесса рассчитываются по формуле
З = С+Ен(Кс+Кзд), (5.39)
где С – технологическая себестоимость, р.;
Ен – нормативный коэффициент экономической эффективности капитальных вложений (Ен = 0,1);
Кс, Кз – удельные капитальные вложения в станок и здание соответственно.
Расчет основной и дополнительной зарплаты выполняется по формуле
С3 = Сч× Кд × Зн × Ко.м., (5.40)
где Сч – часовая тарифная ставка рабочего (принимается по установленным тарифным ставкам), р./ч;
Кд – коэффициент, учитывающий дополнительную зарплату и начисления (Кд = 1,7);
|
|
Зн – коэффициент, учитывающий оплату наладчика (Зн = 1,0);
Ко.м. – коэффициент, учитывающий оплату рабочего при многостаночном обслуживании (Ко.м. = 1,0)
Расчет часовых затрат по эксплуатации рабочего места выполняется по формуле
Сэксп.= Сч.з.× Км , (5.41)
где Сч.з – часовые затраты на базовом рабочем месте (принимаются по данным базовых предприятий), р./ч;
Км – коэффициент, показывающий, во сколько раз затраты, связанные с работой данного станка, больше, чем аналогичные расходы у базового станка (принимается по данным [2]).
Удельные капитальные вложения в станок рассчитываются по формуле
(5.42)
где Цс – отпускная цена станка, р.;
Км – коэффициент, учитывающий затраты на транспортировку и монтаж (Км = 1,1);
Сп – принятое число станков на операцию (Сп = 1,0);
N – годовой объем выпуска деталей.
Удельные капитальные вложения в здание рассчитываются по формуле
(5.43)
|
|
где Спл – стоимость 1 м2 производственной площади (принимается по материалам производственной практики), р./м2;
Пс – площадь, занимаемая станком с учетом проходов, м2;
Сп – принятое число станков на операцию (Сп = 1,0).
Площадь, занимаемая станком Пс , определяется по формуле
(5.44)
где f – площадь станка в плане (длина к ширине), м2;
Кс – коэффициент, учитывающий дополнительную производственную площадь (К = 3,5 при f = 2–4м2; К = 3 при f = 4–6м2; К = 4 при f < 2м2).
Технологическая себестоимость рассчитывается для всех операций по формуле
. (5.45)
Экономический эффект от внедрения принятого варианта технологического процесса рассчитывается по формуле
(5.46)
где Збаз – приведенные затраты по базовому варианту техпроцесса;
Зпр – приведенные затраты по проектируемому варианту.
Результаты расчетов приведенных затрат сводятся в таблицу 5.10.
|
|
Таблица 5.10 – Расчет приведенных затрат
Операция | Модель станка | tшт, мин | Сз, р. | Сэксп, р. | Кс, р. | Кзд.,р. | С, р. |
Базовый вариант | |||||||
010. Токарная | 16К20 | 7,8 | (6.40) | (6.41) | (6.42) | (6.43) | (6.45) |
025.Сверлильная | 2Н55 | 6,4 | (6.40) | (6.41) | (6.42) | (6.43) | (6.45) |
Итого S S S S | |||||||
Проектируемый вариант | |||||||
05.Токарная с ЧПУ | 16К20Т1 | 2,3 | (6.40) | (6.41) | (6.42) | (6.43) | (6.45) |
20. Сверлильная с ЧПУ | 2Р135Ф2 | 3,4 | (6.40) | (6.41) | (6.42) | (6.43) | (6.45) |
Итого S S S S | |||||||
Примечание – В таблице в скобках указаны номера формул, по которым выполняются расчеты |
5.13 Расчет наладочных размеров маршрута обработки
При настройке инструмента перед обработкой партии деталей методом автоматического получения размеров центр рассеивания размеров должен быть расположен в той части установленного допуска, чтобы иметь возможность использования всего поля допуска для компенсации размерного износа инструмента и для сокращения количества подналадок за период стойкости инструмента. Например, если настроить при точении резец на середину поля допуска, то для компенсации износа резца можно будет использовать лишь половину допуска на размер. Если же настроечный размер расположен на расстоянии примерно в 1/3 ТD от нижнего предельного размера, то на компенсацию износа инструмента можно будет использовать почти две трети поля допуска. В соответствии с рекомендациями [10, 11] уровень настройки Х0 определяется по одной из следующих формул:
|
|
- при смещении уровня настройки в процессе обработки к верхнему предельному отклонению ESA поля допуска на обработку (при наружном точении):
- при смещении уровня настройки в процессе обработки к нижнему предельному отклонению EIA поля допуска на обработку (при растачивании):
Где ESA и EIA – верхнее и нижнее отклонения размера А обрабатываемой поверхности, мм; - смещение уровня настройки за период стойкости инструмента (между настройками инструмента), мм;
- среднее квадратическое отклонение размеров при обработке в малой выборке, мм;
- поле допуска на настройку, мм.
Основной причиной смещения настройки является размерный износ инструмента. При односторонней обработке (точение торца, обработка плоскости и т.п.)
При двусторонней обработке (обработка поверхности вращения, одновременная обработка двух поверхностей и т.п.)
где - относительный износ инструмента, мкм/км [12]; l – путь резания за период стойкости инструмента м. [12]
Число деталей обработанных за период стойкости инструмента, может быть определено по формуле:
где T – период стойкости инструмента, мин; Т0 - основное время обработки одной детали, мин.
Среднее квадратическое отклонение размеров в малой выборке может быть определено по формуле:
где - значение поля рассеивания размеров в выборке [12].
Допустимая в разных условиях обработки погрешность настройки при распределении ее значений по нормальному закону может быть определена по формуле:
где ITA – поле допуска на обработку, мм; Δн.у – абсолютное значение погрешности контроля точности настройки, мм; δизм – погрешность измерения, мм.
Значение Δн.у представляет собой погрешность метода расчета среднего арифметического значения или медианы в малой выборке и может быть вычислено следующим образом:
где n – объем выборки.
Допустимая для данных условий погрешность измерений δизм принимается по [13]. В соответствии с δизм по [14] выбираются средства измерений. Результаты расчетов сводят в таблицу 5.11
Таблица 5.11 – Наладочные размеры обработки ступени вала Ø18-0,02
Операция | Содержание перехода | Технологический размер | Наладочный размер | Средства контроля |
010 | Точение черновое | Ø18.26+0,13 | Ø18.3 | … |
015 | Точение чистовое | … | … | … |
025 | Шлифование | … | … | … |
Заключение
Этот раздел такой же короткий, как и введение. В нем содержатся общие выводы по проекту, приводятся наиболее существенные отличия принятого варианта технологического процесса от других возможных вариантов. Отражается использование новых высокопроизводительных методов обработки, нового оборудования, инструмента и приспособлений. Даются сведения о возможности получения экономического эффекта и его величине.
Список литературы
1 Справочник технолога–машиностроителя: в 2 т. / Под ред. А. Г. Косиловой и Р. К. Мещерякова. – М.: Машиностроение, 1985. – Т.1 656 с.
2 Технология машиностроения. Курсовое и дипломное проектирование: учеб. пособие / М. Ф. Пашкевич [и др.]; под ред. М. Ф. Пашкевича. – Минск: Изд-во Гревцова, 2010. – 400 с.
3 Технология машиностроения: учеб. пособие / М. Ф. Пашкевич [и др.]; под ред. М. Ф. Пашкевича. – Минск: Новое знание, 2008. – 478 с.
4 Справочник технолога–машиностроителя: в 2 т. / Под ред. А. Г. Косиловой и Р. К. Мещерякова. – М.: Машиностроение, 1985. Т.2 – 496 с.
5 Режимы резания металлов: Справочник / Под ред. Ю. В. Барановского. – М.: Машиностроение, 1972. – 408 с.
6 Технологическая оснастка: учебник для студентов машиностроит. специальностей вузов / М. Ф. Пашкевич [и др.] – Минск.: Адукацыя i выхаванне, 2002. – 320 с.
7. Матвеев, В.В., Бойков, Ф.И., Свиридов Ю.П. Проектирование экономичных технологических процессов в машиностроении.- Челябинск: Южно.-Уральское кн. изд-во, 1979.- 112 с.
8. Махаринский, Е.И., Горохов, В.А. Основы технологии машиностроения: учебник.- Мн.: Выш. шк., 1997 – 432 с.
9. Пузанова, В.П. Размерный анализ и простановка размеров в рабочих чертежах.- М.-Л.: Машгиз, 1958.-196 с.
10. Маталин, А.А. Технология машиностроения: учебник для вузов.- Л.: Машиностроение, 1985.- 496 с.
11. Лабораторный практикум по технологии машиностроения/ В.В. Бабук [и др.]; под ред. В.В. Бабука. – Мн.: Выш. шк., 1983. – 220 с.
12. Дипломное проектирование по технологии машиностроения: учебное пособие для вузов/ В.В. Бабук [и др.]; Под общ. ред. В.В. Бабука – Мн.: Выш. шк., 1979.-464 с.
13. ГОСТ 8.051-81 (СТ СЭВ 303-76). Государственная система обеспечения единства измерений. Погрешности допускаемые при измерении линейных размеров до 500 мм.
14. РД 50-98-86. Методические указания. Выбор универсальных средств измерений линейных размеров до 500 мм (по применению ГОСТ 8.051-81).
Дата добавления: 2018-05-12; просмотров: 296; Мы поможем в написании вашей работы! |
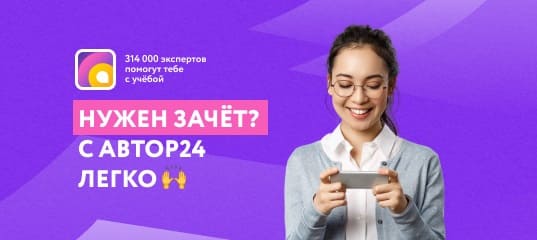
Мы поможем в написании ваших работ!