Назначение режимов резания для рассматриваемых маршрутов обработки
В курсовой работе назначаются режимы резания: на две разнохарактерные операции расчет ведется по формулам теории резания металлов, на остальные – по нормативам.
Расчет режимов резания с использованием аналитических формул выполняется по справочнику [4].
Для выбора режимов резания по нормативам можно пользоваться справочником [5].
Расчет режимов резания для всех операций начинается с описания исходных условий обработки, которые включают:
– номер и наименование операции;
– краткое содержание операции;
– наименование и модель станка;
– наименование режущего инструмента, его размеры, марка материала режущей части.
Далее определяется глубина резания для диаметральных размеров: с учетом величины припуска и маршрутной технологии (черновая обработка, чистовая окончательная) обработки поверхности. При этом на чистовую и отделочную обработку оставляют, как правило, 20–30% общего припуска; на линейные размеры принимается на основе решения размерных цепей.
Подача на оборот So (подача на зуб Sz при фрезеровании) выбирается в зависимости от глубины резания по [5]. Справочные значения подачи корректируются и принимаются окончательно по паспортным данным станка выбранной модели.
Скорость резания Vp рассчитывается по формулам теории резания или нормативам. По полученному значению скорости определяется расчетная частота вращения шпинделя
|
|
(5.25)
где D – диаметр детали или инструмента.
Полученное значение частоты вращения корректируется (принимается меньшее) по паспорту станка. По принятой частоте вращения определяется действительная скорость резания
………. . (5.26)
Рассчитанные режимы резания записываются в сводные таблицы режимов резания (таблица 5.6). В эти же таблицы записывается основное время, рассчитанное с использованием установленной величины минутной подачи.
Таблица 5.6 – Сводная таблица режимов резания
Номер опера-ции | Наименова-ние операции, перехода | Глуби-на резания t, мм | Дли-на реза-ния lрез, мм | Подача Sо, мм/об | Скорость V, м/мин | Частота вращения, мин-1 | Минут-ная подача Sм,, мм/ми | Основ-ное время t0, мин | |||
рас- четная | при-нятая | рас-четная | при- нятая | рас-четная | при- нятая | ||||||
005 | Токарная с ЧПУ 1 Точение черновое Æ40 Æ50 | 2,0 1,5 | 25 40 | 0,4 0,4 | 0,36 0,36 | 118 118 | 100 98,9 | 939 751 | 800 630 | 288 227 | 0,1 0,19 |
010 | Сверлильная 1 Сверление отв. Æ10 | 5 | 16 | 0,18 | 0,16 | 19 | 18,2 | 605 | 580 | 92,8 | 0,24 |
В заключение рассчитывается эффективная мощность резания Ne и проверяется возможность обработки по мощности привода главного рабочего движения станка Nст. При этом учитывают кпд станка, который в этом случае принимается равным 0,85–0,90.
|
|
Расчет норм времени
Расчет норм времени выполняется также для всех операций в соответствии с методикой, представленной в [2].
В крупносерийном и массовом производстве рассчитывается норма штучного времени
tшт = tо + tв + tобс + tотд , (5.27)
где tо – основное время;
tв – вспомогательное время;
tобс – время на обслуживание рабочего места;
tотд – время на отдых.
В мелко- и среднесерийном производстве рассчитывается норма штучно – калькуляционного времени
(5.28)
где tп. з – подготовительно – заключительное время;
п – размер партии деталей.
Основное время рассчитывается по формуле
|
|
(5.29)
где Lрез – длина резания ;
y – величина врезания и перебега;
i – количество рабочих ходов.
Вспомогательное время tв состоит из затрат времени на отдельные приемы:
(5.30)
где tус. – время на установку и снятие детали;
tз.о. – время на закрепление и открепление детали;
tуп. – время на приемы управления станком;
tиз. – время на измерение детали.
Оперативное время рассчитывается по формуле
. (5.31)
Время на обслуживание рабочего места и время на отдых tобс и tотд в серийном производстве по отдельности не определяются. В нормативах дается сумма этих двух составляющих в процентах от оперативного времени tоп [2].
В массовом производстве время на отдых tотд задается в процентах от оперативного времени [2].
Время на обслуживание tобс в массовом и крупносерийном производстве слагается из времени на организационное обслуживание tорг и времени на техническое обслуживание tтех:
. (5.32)
|
|
Подготовительно-заключительное время состоит из ряда составляющих:
– время на получение инструментов и приспособления до начала работы на станке;
– время на наладку станка и установку инструментов и приспособления;
– время перемещений и поворотов рабочих органов станка, на настройку цепей рабочих движений станка;
– время на установку, выверку и регулировку положений упоров;
– время на снятие и сдачу инструментов и приспособлений после окончания обработки партии деталей на станке.
Составляющие норм штучного или штучно-калькуляционного времени по всем операциям двух вариантов технологических процессов сводятся в таблицу 5.7
Таблица 5.7 – Сводная таблица норм времени
В минутах
Но-мер опе-ра-ции | Наиме-нова-ние опера-ции | Основ-ное время t0 | Вспомогатель-ное время tв | Опе-ратив-ное время tоп | Время обслужива-ния | Вре-мя на от-дых tотд | Штучное время, tшт | Под-гото-вит. закл. время tп.з.
| Вели-чина пар-тии п | Штуч-но-калькуляци-он. время tшт-к | |||
tуст | tупр | tизм | tтехобс | tоргобс | |||||||||
Уточнение типа производства
Тип производства в соответствии с ГОСТ 3.1121-84 характеризуется коэффициентом закрепления операций, который показывает число различных операций, закрепленных в среднем по цеху (участку) за каждым рабочим местом в течение месяца.
Для расчета коэффициента закрепления операций следует использовать нормы времени tшт или tшт-к, взятые из принятого варианта технологического процесса. Расчет следует вести в табличной форме (таблица 5.9). В первую графу таблицы записываются все операции технологического процесса, во вторую – нормы времени tшт или tшт-к.
Определяется расчетное количество станков mp для каждой операции по формуле (5.33) и записывается в третью графу таблицы.
(5.33)
где N – годовой объем выпуска деталей, шт.;
tшт.(шт-к) – штучное или штучно- калькуляционное время, мин;
Fд – действительный годовой фонд времени, ч, принимаемый при двухсменной работе по таблице 5.8;
hз.н. – нормативный коэффициент загрузки оборудования (для расчетов в курсовом проекте принимается hз.н. = 0,75–0,85).
Принятое число рабочих мест Р (четвертая графа таблицы 5.9) устанавливают округлением значений mp (третья графа) до ближайшего большего целого числа.
Таблица 5.8 – Фонд времени работы оборудования
Оборудование | Номинальный годовой фонд времени, ч | Действительный годовой фонд времени, ч |
Металлорежущие станки 1–30 категорий ремонтной сложности | 4154 | 4029 |
Металлорежущие станки свыше 30 категории ремонтной сложности | 4154 | 3904 |
Автоматические линии | 4154 | 3738 |
Поточные линии | 4154 | 3987 |
Рабочие места без сложного оборудования (верстаки, столы) | 4154 | 4154 |
Таблица 5.9 – Расчет коэффициента закрепления операций
Операция | tшт-к,мин | mp | Р | hз.ф. | О |
005.Токарная | 4,2 | 0,087 | 1 | 0,087 | 9,20 |
010.Протяжная | 1,2 | 0,025 | 1 | 0,025 | 32,00 |
015.Зубофрезерная | 8,6 | 0,181 | 1 | 0,181 | 4,42 |
020. Зубошевинговальная | 3,4 | 0,071 | 1 | 0,071 | 11,27 |
025.Внутришлифовальная | 4,1 | 0,086 | 1 | 0,086 | 9,30 |
030.Плоскошлифовальная | 3,6 | 0,076 | 1 | 0,076 | 10,53 |
SR=6 SO=76,72
Далее, для каждой операции вычисляют значение фактического коэффициента загрузки оборудования:
. (5.34)
Количество операций (последняя графа), выполняемых на рабочем месте, определяется по формуле
. (5.35)
Коэффициент закрепления операций рассчитывается по формуле
(5.36)
По ГОСТ 3.1121-84 приняты следующие коэффициенты закрепления операций кз.о.:
– массовое производство кз.о ≤ 1;
– крупносерийное производство 1 < кз.о ≤10;
– среднесерийное производство 10 < кз.о ≤20;
– мелкосерийное производство 20 < кз.о ≤40;
– единичное производство кз.о > 40.
Для серийного производства рассчитывается размер партии деталей по формуле
(5.37)
где а – количество дней запаса деталей на складе;
Ф – количество рабочих дней в году.
Рекомендуется принимать а = 2–3 дня – для крупных деталей; а = 3–5 дней для средних; а = 5–10 дней для мелких.
Для массового и крупносерийного производства рассчитывается такт выпуска по формуле
(5.38)
где Fд – годовой фонд времени работы оборудования, ч.
Дата добавления: 2018-05-12; просмотров: 273; Мы поможем в написании вашей работы! |
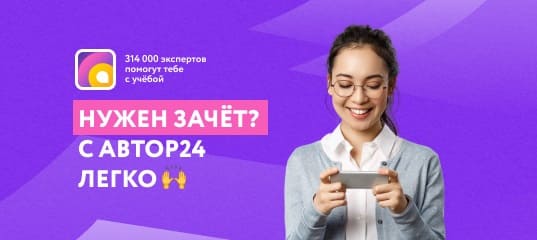
Мы поможем в написании ваших работ!