Принципы построения системы допусков и посадок для типовых соединения машин
Системой допусков и посадок называется совокупность рядов допусков и посадок, закономерно построенных на основе опыта, теоретических и экспериментальных исследований и оформленных в виде стандарта. Система предназначена для того, чтобы можно было выбрать (самые) необходимые для практики варианты допусков и посадок типовых соединений деталей машин. Она делает возможной стандартизацию режущих инструментов и калибров, облегчает конструирование и достижение взаимозаменяемости соединений, повышает качество изделий.
Системы допусков и посадок построены по единым принципам для всех типов соединений, которые рассматриваются ниже на примере гладких цилиндрических соединений.
Системой посадок основного отверстия (системой отверстия) называется совокупность посадок, в которых при одной и той же степени точности и одном и том же номинальном размере предельные отклонения отверстий одинаковы для любых посадок, а различные посадки достигаются изменением предельных отклонений валов (рис. 1.5,а).
Системой посадок основного вала (системой вала) называется совокупность посадок, в которых при одной и той же степени точности и одном и том же номинальном размере предельные отклонения валов одинаковы для любых посадок, а различные посадки достигаются изменением предельных отклонений отверстий (рис. 1.5, б).
Для всех посадок в системе отверстия нижнее отклонение отверстия равно нулю (EJ = 0), т.е. нижняя граница ноля допуска отверстия, называемого основным отверстием, всегда совпадает с нулевой линией.
|
|
Для всех посадок в системе вала верхнее отклонение вала es = 0, т.е. верхняя граница поля допуска вала, называемого основным валом, всегда совпадает с нулевой линией.
Поле допуска основного отверстия откладывают вверх, а основного вала - вниз от нулевой линии, т.е. в материал детали. Такую систему допусков называют односторонней предельной. Характер одноименных посадок (т.е. предельные величины зазоров и натягов) в системе отверстия и в системе вала примерно одинаковы. Выбор той или иной системы определяется конструктивными, технологическими и экономическими соображениями.
В машиностроении преимущественное распространение получила система отверстия, т.к. точные отверстия обрабатываются дорогостоящим инструментом (зенкерами, развертками, протяжками). Каждый из них применяют для обработки только одного размера с определенным полем допуска. Валы же, независимо от их размера, обрабатывают одним и тем же резцом или шлифовальным кругом. В системе отверстия различных по предельным размерам отверстий будет меньше. Это позволяет изготовлять режущий инструмент на специализированных предприятиях, с меньшими затратами и высоким качеством.
|
|
Однако в некоторых случаях по конструктивным соображениям приходится применять систему вала, когда требуется чередовать соединения нескольких отверстий одинакового номинального размера, но с различными посадками на одном валу.
Рисунок - 1.5 Расположение полей допусков:
а) при системе отверстия, б) при системе вала
Рисунок - 1.6 Шарнирное соединение вилки с тягой:
а) узел в сборе; б) поля допусков в системе отверстия;
в) поля допусков в системе вала
Так, в соединении, показанном на рисунке 1.6, а, должна быть обеспечена подвижная посадка вилки 1 с тягой 3 и неподвижная его посадка с вилкой 2. Если выполнить это соединение в системе отверстия (рис. 1.6, б), то валик придется делать ступенчатым, причем крайние ступени будут иметь больший диаметр, чем средняя. Монтаж такого узла затруднен (валик, проходя утолщенной ступенью через отверстие в вилке, испортит поверхность отверстия). Следовательно, в этом случае целесообразно выбрать систему вала (рис. 1.6, в). Систему вала применяют и тогда, когда детали типа тяг, осей, валиков изготовляют из точных холоднотянутых прутков без механической обработки их наружных поверхностей. При выборе системы посадок следует учитывать также допуски на стандартные изделия (например, подшипники качения).
|
|
Для построения системы допусков устанавливают единицу допуска i, которая отражает влияние на точность технологических, конструктивных и метрологических факторов, выражает зависимость допуска от номинального размера и является мерой точности. На основании исследований и систематизации опыта механической обработки цилиндрических деталей из металла была установлена единица допуска для размеров от 1 до 500 мм
(1.9)
где D - среднее геометрическое крайних размеров интервала.
(1.10)
где Dmax; Dmin - максимальное и минимальное значение размера интервала, для которого определяется допуск.
Квалитеты (степени точности для резьбовых соединений, зубчатых передач и др.). В каждом изделии детали различного назначения изготовляют с различной точностью. Для нормирования требуемых уровней точности установлены квалитеты (степени точности) изготовления деталей и изделий. Под квалитетом понимают совокупность допусков, характеризуемых постоянной относительной точностью, определяемой коэффициентом а для всех номинальных размеров данного диапазона (например, от 1 до 500 мм). Точность в пределах одного квалитета изменяется только в зависимости от номинального размера.
|
|
Число квалитетов определяется потребностью различных отраслей промышленности, перспективами повышения точности изделий, границами достижимой точности, функциональными и технологическими факторами и принятым значением знаменателя j геометрической прогрессии, по которой изменяется величина допуска при переходе от одного квалитета к другому. Квалитет определяет величину допуска на изготовление, а следовательно, и соответствующие методы и средства обработки деталей машин.
Ряды допусков и интервалы размеров. Используя единицу допуска и коэффициент a, для каждого квалитета построили ряды допусков всех размеров, охватываемых данной системой допусков. В настоящее время в России и ряде других стран действует система допусков и посадок для размеров:
до 1 мм, от 1 до 500 мм, свыше 500 до 3150 мм, свыше 3150 до 10000 мм.
Для упрощения таблиц полей допусков и посадок каждый из диапазонов размеров, в свою очередь, разбит на несколько интервалов и величины допусков приняты одинаковыми для всех размеров, объединенных в один интервал (например, свыше 6 до 10 мм, свыше 10 до 18 мм и т.д.).
Диаметры по интервалам распределены таким образом, чтобы допуски, подсчитанные по крайним значениям в каждом интервале, отличались от допусков, подсчитанных по среднему значению диаметра в том же интервале, не более чем на 5-8 процентов.
Нормальная температура. Допуски и отклонения указаны в таблицах стандартов для деталей, размеры которых определены при нормальной температуре +20°С. Такая температура принята как близкая к температуре рабочих помещений машиностроительных и приборостроительных заводов. При этой температуре осуществляется градуировка и аттестация линейных и угловых мер измерительных приборов и инструментов и должны производиться измерения.
В производстве принято соблюдать следующие условия нормального температурного режима:
- температура детали и измерительного средства в момент контроля должна быть одинаковой, что может быть достигнуто при совместной выдержке детали и измерительного средства в одних условиях (например, на чугунной плите);
- желательно, чтобы коэффициенты линейного расширения материала детали и измерительного средства были примерно одинаковыми.
Следует указать, что погрешность измерения возникает также от местного нагрева. Например, под действием тепла руки контролера в течение 15 минут размер скобы для проверки валов диаметром 175 мм изменяется на 8 мкм, а скобы для проверки валов диаметром 280 мм - на II мкм. Это свидетельствует о необходимости применять тепловую изоляцию, например, термоизолирующие накладки и ручки у скоб или термоизолирующие перчатки.
Дата добавления: 2018-04-15; просмотров: 1095; Мы поможем в написании вашей работы! |
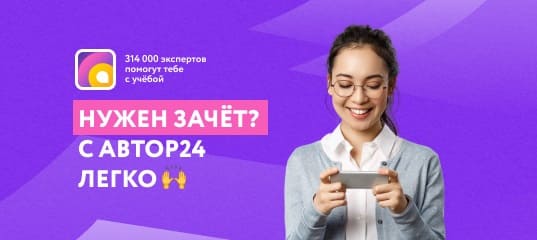
Мы поможем в написании ваших работ!