Глава 1. СПОСОБЫ РЕШЕНИЯ ЗАДАЧ
МНОГОКРИТЕРИАЛЬНОГО ВЫБОРА ВАРИАНТОВ
1.1. Уровни распределённых систем управления и задачи выбора вариантов по уровням.
Современные системы управления являются распределёнными по уровням и интегрированными по функциям АСУ ТП И АСУП [1 - 7]. Каждому уровню соответствуют определённые функции, реализованные соответствующими техническими средствами автоматизации и программным обеспечением (рис.1.1).
Основой первого уровня распределённых систем управления являются оконечные устройства, в основном это датчики и исполнительные устройства, расположенные непосредственно на объектах контроля и управления. Основными задачами при проектировании данного уровня являются:
· математическое описание процедуры выбора процессорных измерительных средств (ПрИС) и исполнительных устройств;
· формирование множества параметров и признаков технологического процесса, определяющих выбор датчиков и исполнительных уст-ройств;
· формирование показателей эффективности для выбора датчиков и исполнительных устройств;
· обоснование структурной модели процесса выбора вариантов датчи-ков, исполнительных устройств и программного обеспечения;
· выбор уравнения и структуры процессорных измерительных средств;
· выбор оптимального варианта процессорных измерительных средств на множестве показателей эффективности;
· определение числа ПрИС;
|
|
· выбор промышленной сенсорной сети для подключения датчиков и исполнительных устройств;
· выбор программного обеспечения для интеллектуальных датчиков и исполнительных устройств;
· разработка алгоритма и программного обеспечения для решения за-дач выбора вариантов ПрИС и исполнительных устройств.
Второй уровень распределенной системы относятся к уровню низо-вой автоматизации. Основными техническими средствами этого уровня яв-ляются промышленные контроллеры и промышленные контроллерные сети для подключения контроллеров к операторским станциям. Основная задача данного уровня – непосредственное управление объектом, обработка измерительной информации, поступающей от датчиков и формирование управляющих сигналов, подаваемых на исполнительные устройства.
Контроллеры |
Универсальная
сеть
|
|
Уровень управления производством |
Сервер |
Контроллерная сеть |
Универсальная сеть |
Датчики |
Исполнительные устройства |
Операторские станции |
Компью- теры |
Вычислитель- ная сеть |
Уровень управления участками и технологическими процессами |
Уровень низовой автомати- зации |
Уровень датчков и испол- нитель ных уст- ройств . |
Сенсорная сеть |
Технологический объект управления (ТОУ) (технологический процесс, технологические операции, технологическое оборудование) |
Рис. 1.1. Уровни распределенных систем управления.
Объём информационного кадра для данного уровня составляет порядка 1– 2 байта, время цикла порядка 10 мс. Основными задачами при проектировании уровня низовой автоматизации являются:
· обоснование структурной модели процесса выбора промышленных контроллеров, контроллерной сети и программного обеспечения; формирование показателей эффективности для выбора оптимальных вариантов промышленных контроллеров и промышленной контрол - лерной сети;
|
|
· математическое описание процедуры выбора промышленных контролеров и контроллерной сети;
· определение числа каналов модулей ввода-вывода;
· выбор модулей ввода-вывода промышленных контроллеров;
· выбор вариантов процессорной части промышленных контроллеров;
· выбор вариантов контроллерной сети;
· выбор программного обеспечения для технических средств второго уровня распределенных систем управления (РСУ);
· разработка алгоритма и программного обеспечения для решения задач выбора вариантов промышленных контроллеров и контроллерной сети.
Основной задачей третьего уровня распределённых систем является управление технологическими участками и технологическими процесса-ми. Основой уровня являются операторские станции, промышленные ком-пьютеры и универсальные промышленные сети. Информационный кадр составляет десятки байтов, время цикла 100–1000 мс. Для управления тех-нологическими участками и технологическими процессами должен быть спроектирован соответствующий уровень операторского интерфейса для визуального контроля процессов на участках и технологических операциях и воздействия на второй уровень системы и в итоге на объекты управления. Основными задачами для проектирования данного уровня являются:
|
|
· обоснование структурной модели выбора вариантов технических средств и программного обеспечения третьего уровня РСУ;
· математическое описание выбора технических средств и программ-ного обеспечения;
· формирование показателей эффективности для выбора операторских станций, промышленных компьютеров и промышленной универса- льной сети;
· выбор вариантов операторских станций, промышленных компьютеров и промышленной сети на множестве показателей эффективности;
· выбор программного обеспечения для технических средств третьего уровня РСУ;
· разработка алгоритма и программного обеспечения для решения за-
дач выбора вариантов технических средств и программного обес-печения.
Четвертый уровень относится к уровню управления производством и в большей степени относится к системам управления производством (АСУП) в тесной интеграции с системами автоматизации технологических процессов (АСУ ТП). На этом уровне осуществляется: управление произ-водственным циклом, автоматизация работ по планированию, контролю исполнения, сбору статистики и анализу производственного цикла предп-риятий с непрерывным, циклическим и поточным производством, организация профилактического и технического обслуживания производственного оборудования, автоматизация управления персоналом. Технической основой уровня являются компьютеры, коммуникационные устройства и серверы, объединенные в вычислительные сети с соответствующими автоматизированными рабочими местами (АРМ). Основными задачами при проектировании данного уровня являются:
- обоснование структурной модели выбора технических средств и программного обеспечения четвертого уровня РСУ;
- математическое описание процесса выбора технических средств и программного обеспечения четвертого уровня РСУ;
- формирование показателей эффективности для выбора варианта то-пологии (компоновки) вычислительной сети;
- выбор вариантов компьютеров и серверов на множестве показателей эффективности;
· выбор программного обеспечения для технических средств вычис-лительной сети с учетом интеграции системы управления производ-ством с системой управления технологическим процессом в реаль-ном времени;
· разработка алгоритма и программного обеспечения для решения за-дач выбора вариантов на данном уровне распределенной системы управления.
Пример сетевого взаимодействия уровней распределённой системы управления показан на рис.1.2. Датчики и исполнительные устройства под-ключены к сенсорной промышленной сети «АS-интерфейс» (разработчик AS-I Consortium), позволяющей подключать простые, бинарные датчики и интеллектуальные датчики с возможностью подключения к промышлен-ной сети более высокого уровня, PROFIBUS – Dp (разработчик Siemens) с протоколом физического уровня, соответствующего стандарту физическо-го интерфейса RS – 485. Промышленная сеть PROFIBUS-Dp обеспечивает высокоскоростной обмен данными с оконечными устройствами. Подклю-чение сети AS – интерфейс к сети PROFIBUS-Dp осуществляется через мо-дуль связи 1 фирмы Siemens (Dp/AS – I - Link). Сеть PROFIBUS-РА применяется в опасных производствах, реализует стандарт IES 61158 2 (с внутренней защитой данных).
Internet /
Intranet
TCP /IP
Вычислитель- ная сеть |
Уровень управления производством |
Сервер |
Технологический объект управления (ТОУ) (технологический процесс ТП, участки ТП, технологическое оборудование) |
2 1 |
AS-и н т е р ф е й с |
Датчики |
Исполнительные устройства |
IES 6158 - 2 |
RS - 485 |
PRO FIBUS - DP |
PROFIBUS - РА |
К о н т р о л л е р ы |
RS - 485 |
PROFIBUS -FMS |
Операторские станции |
TC/ IP/ Ethernet |
Компью- теры |
Уровень управления участками и технологическими процессами |
Уровень низовой автомати- зации |
Уровень датчков и испол- нитель ных уст- ройств . |
1 |
Рис. 1.2. Сетевое взаимодействие уровней распределённой системы управления
Сегмент сети PROFIBUS-Dp подключается к сети PROFIBUS-РА через разделительный мост 2. Промышленные контроллеры (уровень низовой автоматизации) подключаются к датчикам и исполнительным устройствам, в данном случае с помощью сети PROFIBUS-РА и физического интерфейса RS – 485. Для подключения промышленных контроллеров к операторским станциям (уровень управления участками и технологическими процессами) используется промышленная сеть PROFIBUS-FMS, предназначенная для передачи больших объемов данных с физическим интерфейсом RS – 485. Для связи операторских станций с вычислительными сетями (уровень управления производством) используется универсальная промышленная сеть Ethеrnet (разработчик DEC, Xerox, Intel) cо стековым протоколом стандарта Ethernet TCP/IP (Transmission Control Protokol/ Internet Protokol), протокол управления и передачи/протокол Интернета. Для связи вычислительной сети управления производством с уровнем интегрированных систем управления типа ERP (Enterprise Resourse Plauning) используются универсальные сети Internet/Intranet с протоколом TCP/IP. Для создания таких распределенных систем управления необходимы интегрированные системы проектирования, обеспечивающие работу АСУ ТП и АСУП в реальном времени, интеграцию информационных ресурсов от уровня низовой автоматики до уровня планирования и управления производством и доступности этой информации на всех уровнях принятия решений. К таким системам относится система TRACE MODE 6+T-FAKTORY 6 (компания AdАstra Research Group, Россия) [7], структура и функции системы представлены на рис. 1.3, 1.4. Управление производством в реальном времени в интегрированной системе TRACE MODE 6 + T - FAKTORY 6 представлено на рис.1.5. TRACE MODE 6 даёт набор средств для программирования промышленных контроллеров (Softlоgik), создания систем телемеханики и операторского интерфейса (SCADA) для цифрового управления технологическим процессом (АСУ ТП). T – FAKTORY – 6 решает задачи: контроль исполнения производственных заданий, учет производственных затрат, сырья, энергии, производственных и людских ресурсов, расчет себестоимости выпускаемой продукции, материальных балансов, учёт и техническое обслуживание производственного оборудования, учёт персонала. В иерархии информационных систем предприятия T – FAKTORY – 6 заполняет пробел между SCADA и ЕRР уровнями. Модули T – FAKTORY – 6 интегрированы с программами TRACE MODE – 6. Разрабатывая проект методом от «технологии» проектировщик одновременно создает основу автоматизации управления финансово-экономическими процессами предприятия. Данные реального времени поступают в T – FAKTORY – 6 с мониторов реального времени (МРВ) TRACE MODE – 6. Для хранения данных T – FAKTORY – 6 используется система управления базой данных реального времени SIAD 6. Модули Т – FAKTORY – 6 представляют набор средств автоматизации финансово-экономических процессов производства (АСУП) и включают: систему управления исполнением производственных заданий – МЕS – система (Маna-facturing execution system); cистему учета и технического обслуживания оборудования ЕАМ – система (Euterprise assets management); cистему управления человеческими ресурсами HRM – система (Human recourses management). Вместе они образуют полную информационную систему директора по производству и подчиненного ему персонала рис. 1.5. Система МЕS является основным модулем, в ней концентрируется вся информация из АСУ ТП (TRACE MODE – 6) и из модулей ЕАМ и НRМ. Основные задачи, решаемые МЕS – системой:
· генерирование производственных заданий или их получение из ЕRР систем предприятия;
ERP |
SCADA TRACE MODE Микро TRACE MODE 6 Цифровое управление технологическим процессом |
снабжение, маркетинг и т. д.
СУБД ERP |
MES, EAM, HRM |
Операторское
СУБД РВ SIAD 6 |
техпроцессом
ТЕХНОЛОГИЧЕСКИЙ ПРОЦЕСС |
Рис. 1.3. Структура интегрированной системы TRACE MODE – 6 + T – FACTORY – 6: MES – система исполнения производственных заданий. EAM – система учета и технологического обслуживания оборудования. HRM – управление человеческим ресурсом.
· планирование материальных, технологических, организационных и человеческих ресурсов, необходимых для исполнения производственных заданий;
· планирование материальных, технологических, организационных и человеческих ресурсов, необходимых для исполнения производственных заданий;
· контроль исполнения заданий по стадиям;
· ведение статистики исполнения производственных заданий;
· выполнение текущей себестоимости;
· создание материальных балансов;
· расчет времени исполнения производственных заданий и сравнение его с нормативами;
· расчет стоимости исполнения производственных заданий и сравнение его с нормативами;
· сохранение истории производственных заданий, прослеживание пути товара в технологии;
· передачу в реальном времени информации о производственном задании в ЕRР – систему предприятия;
TRACE MODE – 6 |
T – FACTORY – 6 |
Softlogic |
АСУ ТП |
Цифровое управление технологическим процессом |
SCADA |
Программирование контроллеров |
Управление производственным бизнесом в реальном времени – набор средств автоматизации финансово – экономических процессов производств |
АСУП |
Создание систем телемеханики и операторского интерфейса |
Система управления исполнением производственных заданий |
Система учета и технического обслуживания оборудования |
EAM |
MES |
Управление человеческими ресурсами |
HRM |
Рис. 1.4. Функции интегрированной системы TRACE MODE – 6 + T – FAKTORY – 6
На основе Т – FAKTORY – 6 - MES создаются автоматизированные рабочие места (АРМ) руководителей предприятия: директора по производству, главного технолога, директора по качеству и т.д.
КЛИЕНТ
ЗАКАЗ |
ERP |
Директор по производству |
ЗАДАНИЕ НА ПРОИЗВОД-СТВО |
ВЫПОЛНЕНИЕ ЗАДАНИЯ |
СЕБЕСТОИМОСТЬ ПРОДУК ЦИИ |
ПЛАНОВОЕ ВРЕМЯ И СТОИМОСТЬ ИСПОЛНЕНИЯ ЗАКАЗА |
ПЛАНИРОВАНИЕ РАБОТ |
МАТЕРИАЛНЫЕ И ЭНЕРГЕТИЧЕСКИЕ БАЛАНСЫ |
МЕS |
SCADA |
SOFTLOGIC |
EAM |
CYБД |
Анализ |
УПРАВЛЕНИЕ ТЕХНОЛОГИЧЕСКИМ ПРОЦЕССОМ |
ОБ СЛУЖИВАНИЕ ОБОРУДОВАНИЯ |
СОХРАНЕ- НИЕ ИСТО- РИИ |
ПРИЧИ- НЫ БРАКА |
ОКЛОНЕНИЕ ОТ НОРМА- ТИВОВ |
HRM |
ПРОСТОИ ОБОРУДО- ВАНИЯ |
ЗАГРУЗКА ОБОРУДОВА-НИЯ |
ЧЕЛОВЕЧЕСКИЕ РЕСУРСЫ |
ЕАM |
ИСПОЛНЕНИЕ ЗАДАНИЯ |
Рис. 1.5. Управление процессом в реальном времени в интегрированной системе
TRACE MODE – 6 + T – FAKTORY – 6
Основные задачи, решаемые в ЕАМ – системе:
· учет и техническое обслуживание производственного оборудования;
· получение информации для расследования причин отказов оборудо-вания;
· отладка материально-технического снабжения;
· планирование людских, материальных и энергетических ресурсов;
· учет финансовых затрат на техобслуживание оборудования;
· создание для каждой единицы оборудования регламента профилак-тического и аварийного технического обслуживания с программиро-ванием документооборота исполнения;
· генерирование отчетов штатным серверам документирования TRA-CE MODE – 6 или генераторам отчетов СУБД.
Информация об использовании, производительности и выработке оборудования поступают в ЕАМ – систему в режиме реального времени из МРВ TRACE MODE – 6 или непосредственно из контроллеров через Микро TRACE MODE. База данных оборудования формируется уже при разработке АСУ ТП в TRACE MODE – 6 методом «от технологии».
На основе Т – FAKTORY – 6 – ЕАМ создаются АРМ сотрудников производственных служб предприятия: начальник служб технического об-
служивания; мастер цеха, бригадиры службы технического обслуживания; рабочие служб технического обслуживания; менеджеры по закупкам оборудования; складские работники и т.д.
Основные задачи, решаемые в НRМ – системе:
· формирование информации об административной структуре и кад-
рах предприятия, необходимую для организации производства и ре-
шения задач МЕS и ЕАМ – системами;
· создание штатного расписания, прописываются организационные структуры цеха, отдела, участка, смены и т.д.;
· создание личных карточек сотрудников;
· выдача руководителю информации в реальном времени о наличии и доступности трудовых ресурсов предприятия, необходимых для вы-полнения производственных заданий.
Из изложенного выше следует, что во всех случаях возникает задача выбора вариантов из исходного множества вариантов, удовлетворяющих заданным показателям эффективности, и что для решения задачи интегрированного проектирования для распределенных систем управления необ-ходимы единые:
· метод автоматизированного выбора вариантов;
· математическое описание процесса выбора вариантов технических средств и программного обеспечения;
· структурная модель выбора вариантов;
· вычислительная процедура выбора вариантов;
· алгоритм выбора вариантов;
· программное обеспечение процесса выбора вариантов для всех уров-ней распределенных систем управления;
· интегрированная среда разработки проектов распределенных систем управления на базе современных SCADA – систем, включающих ин-струментальную систему и исполнительные программные модули, мониторы реального времени, систему управления базой данных ре-ального времени для группового проектирования АСУ ТП и АСУП с выходом на ЕRР – систему предприятия.
Дата добавления: 2018-04-05; просмотров: 305; Мы поможем в написании вашей работы! |
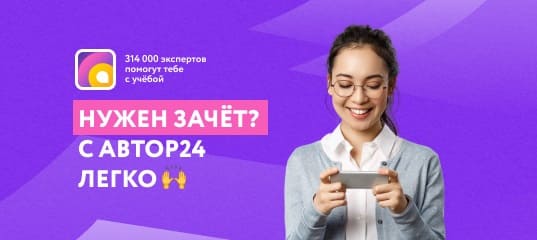
Мы поможем в написании ваших работ!