Технология выгрузки насыпных грузов
Из специализированных вагонов-хопперов
Выгрузка насыпных грузов из специализированных вагонов-хопперов
осуществляется самотёком, т. е. без механизации. Поэтому себестоимость такой
технологии выгрузки насыпных грузов меньше.
Здесь имеются четыре технологии:
1-я технология. По этой технологии при выгрузке насыпных грузов из
специализированных вагонов бункерного типа (хоппер-цементовоз) целесооб-
разно выгрузку осуществлять на повышенном пути малой высоты (до 2.5 м)
самотёком в приемный бункер конвейера, который подает груз в автомобили.
2-я технология. По этой технологии выгрузку насыпных грузов из специа-
лизированных вагонов бункерного типа осуществляют на высоких эстакадах с
подъездом автомобиля под разгрузочный путь и непосредственным высыпани-
ем груза из вагона в автомобили.
В отдельных случаях могут использоваться перегрузочные бункера вме-
стимостью до 60…120 м3.
3-я технология. По этой технологии при выгрузке пылевидных грузов из
вагонов-хопперов в автомобили-цистерны целесообразны схемы непосредст-
венной перегрузки с использованием пневмооборудования.
Выгрузку грузов из вагонов-хопперов и цистерн обслуживает бригада из
1-2 чел.
4-я технология. В зависимости от рода выгружаемого груза, условий орга-
низации работ и применяемого оборудования при выгрузке грузов, склонных к
сводообразованию, на вагонах-хопперах устанавливают вибраторы.
|
|
Параметры этих вибромашин, которые генерируют вынуждающую силу,
не должны в соответствии с п. 1.7 ГОСТ 22235-76 «Вагоны грузовые магист-
ральных железных дорог колеи 1520 мм. Общие требования по обеспечению
сохранности при производстве погрузочно-разгрузочных и маневровых работ»
превышать по амплитуде: 6.4 кН при установке вибраторов на штатные скобы в
нижней части бункеров; 36 кН (3.7 тс) при установке вибраторов на нижнюю
обвязку хоппера или прижиме устройства к нижней обвязке и стойкам. При
каждой разгрузке вагона допускается периодическое выключение вибромаши-
ны общей продолжительностью не более одной минуты.
Для сокращения затрат времени на разгрузку вагонов должна быть обеспе-
чена четкая подача автомобилей с интервалом подъезда к вагону 3 – 7 мин. в
зависимости от интенсивности потока выдачи грузов. В процессе загрузки ав-
томобилей водитель автомобиля должен находиться в кабине и выполнять пе-
редвижения по указанию рабочих комплексной бригады.
123
Технология выгрузки насыпных грузов
Из открытого подвижного состава
The technology of unloading of embankments cargoes
|
|
From open top rolling stock
Технология выгрузки насыпных грузов из полувагонов
Существуют шесть технологий выгрузки насыпных грузов и грузов нава-
лом из полувагонов:
1-я технология. По данной технология, как исключение в соответствии с п.
1.2.10 ГОСТа 22235-76, допускается грейферная разгрузка при перегрузке гру-
зов, перевозимых в железнодорожно-водном сообщении, при условии обеспе-
чения сохранности вагонов. В других случаях разгрузка грейфером допускается
по разрешению федерального органа исполнительной власти железнодорожно-
го транспорта, т. е. такой способ является способом ограниченного применения.
Он используется в исключительных случаях. Например, такая технология ис-
пользуется при вынужденной выгрузке насыпных грузов в стеснённых услови-
ях, и при этом нет других решений. По этой причине для широкого применения
не рекомендуется. Эта технология реализуется с использованием козловых кра-
нов с грейферными захватными органами. Механизированный способ выгрузки
осуществляется при
n сут. = 10 ваг./сут.
Схема механизации выгрузки из вагонов грузов, перевозимых насыпью и
навалом с применением козловых кранов, оснащенных грейфером, показана на
|
|
рис. 5.16.
124
Рис. 5.16. Схема механизации выгрузки из вагонов грузов,
перевозимых насыпью и навалом с применением
козловых кранов с грейфером:
1 – гидравлический грейфер ГЭГ 2.0 вместимостью 2.0 м3;
2 – бункерная установка; 3 – автомобиль;
4 – штабель; 5 – козловой кран
Параметры канатных грейферов, предназначенных для погрузки-выгрузки
грузов, перевозимых насыпью и навалом, из вагонов должны соответствовать
ГОСТ 24599.
Ширина двухчелюстного грейфера, независимо от назначения размаха, не
должна превышать 2.5 м, а номинальный вес порожнего грейфера должен быть
не более 80 кН. Наличие зубьев, клыков, перекрытие ножей в нахлестку, а так-
же острые режущие кромки на ножах не допускаются. Кромки ножей закрытого
грейфера должны плотно прилегать друг к другу. Допускается относительное
смещение кромок по высоте в сомкнутом положении в пределах 20 % толщины
ножа.
Режим работы выгрузочных комплексов с козловым краном при выгрузке
грузов грейфером, перевозимых насыпью и навалом из полувагонов, должен
обеспечивать сохранность конструкции вагонов, их узлов и деталей. В частно-
сти, не допускается свободное «бросание» грейфера.
|
|
Грейфер на груз должен опускаться вертикально. Опирание грейфера на
элементы конструкции вагона не допускается. Грейфер при зачерпывании груза
не должен касаться пола вагона. Допускаемая посадочная скорость опускания
грейфера на груз в зависимости от его массы не должна превышать скорости,
указанной в табл. 5.1.
Таблица 5.1
Допускаемая посадочная скорость опускания грейфера на груз
Наименование параметра
Вес грейфера, кН
Допускаемая посадочная ско-
18
20
Величина
25 30
35
40
рость опускания грейфера на груз,
м/с
0.36 0.33 0.28 0.24 0.22 0.20
Преимуществами такой технологии выгрузки грузов являются возможности:
– применения прямого варианта выгрузки груза из вагона грейфером пря-
мо в автомобиль;
– выгрузки с глуходонного вагона или с вагона с нижними люками.
Недостатками являются:
– вероятность повреждения обшивок вагонов грейфером;
– необходимость зачистки вагонов от остатков грузов (примерно остается
до 30 кН (3 тс) груза) или вручную или с применением специальных способов;
– низкая производительность такой схемы механизации выгрузки грузов;
125
– трудности при выгрузке смерзающихся насыпных грузов в зимнее время,
поскольку в этом случае требуется использование рыхлителей.
2-я технология, которая применяется на крупных пунктах. По этой техно-
логии применяется повышенный путь в комплексе с тракторным погрузчиком
(экскаватором) с ковшом, например, ТО-18А для погрузки грузов из штабеля в
автомобили, зачистки габаритов и отвалки грузов в штабеля (рис. 10.4). Здесь
вагоны подаются на повышенный путь и груз выгружается через нижние люки.
При этом рабочие открывают крышки нижних люков вручную, используя
вспомогательные мостики. Схематически выгрузка сыпучего груза из полува-
гона показана на рис. 5.17.
Рис. 5.17. «Повышенный путь» для выгрузки сыпучих грузов:
1 − «повышенный путь»; 2 − вспомогательный мостик;
3 − полувагон; 4 − тракторный погрузчик; 5 − автомобиль;
6 − склад (штабель) оперативного хранения груза
Ширина от оси повышенного пути до крайней внутренней точки штабеля
груза равна ∼16 м.
Грузы, выгружаемые на повышенных путях, как правило, обезличиваются,
и вагоны с грузами должны подаваться на специально отведенные для данного
рода груза участки у повышенного пути. С этой целью при подаче вагонов на
станции должна быть соответствующая подборка вагонов.
Технология выгрузки насыпных грузов следующая. Вагоны подают манев-
ровым локомотивом группами на повышенный путь. Затем их закрепляют
башмаками. Вначале поворачивают секторы, затем вручную ударом молотка
освобождают люковую закидку, открывая при этом люки вагона (рис. 5.18).
Четырёхосный полувагон имеет 14 люков, по 7 люков с каждой стороны.
На каждом люке по 2 сектора и по 2 люковых закидки. Значит, надо поворачи-
вать 28 секторов и освобождать в общем случае 28 люковых закидок. Высыпа-
ние насыпных грузов в отвал происходит самотёком, затем тракторным погруз-
чиком, оборудованным ковшом, груз загружается в автомобили или перемеща-
ется в штабель. Очистка полувагона производится вручную с применением ло-
паты со скребком посредством ломов. Крышки люков весят ∼ 1 кН. Как видно,
работа носит тяжёлый характер. После закрытия крышки разгрузочных люков
фиксируются люковыми закидками, а последние, в свою очередь, секторами.
126
Рис. 5.18. Полувагон с открывающимися люками
Помимо этого, крышки разгрузочных люков ещё и увязываются за запор-
ные угольники отожжёнными проволоками диаметром не менее 4 мм в один
оборот с закруткой концов проволоки в три витка при помощи металлической
пластинки (для проволочных закруток), чтобы на пути передвижения поезда
исключить самопроизвольное их открывание. Концы проволоки должны быть
не более 90…100 мм и загнуты внутрь к люку вагона.
Преимущества такой технологии выгрузки насыпных грузов следующие:
– выгрузка грузов происходит самотёком, отсутствуют расходы на топливо
или электроэнергию;
– высыпание грузов происходит за несколько минут.
Недостатки такой технологии выгрузки насыпных грузов:
– нерационально используются складские площади, поскольку с каждой
стороны склада имеются места для работы тракторных погрузчиков;
– присутствует тяжёлый ручной труд при открывании и закрывании люков;
– в каждом вагоне остатки насыпных грузов очищаются вручную;
– затруднена выгрузка смёрзшихся грузов;
– отсутствует прямой вариант выгрузки грузов;
– нельзя выгружать вагоны с глухим дном, т. е. глуходонные вагоны.
3-я основная технология. По этой технологии схема комплексной выгрузки
из полувагонов грузов (через люки), перевозимых насыпью и навалом, включает:
повышенный путь высотой 2.4 м, козловой кран (например, КДКК-10), оснащён-
ный фермой–мостом с площадками для грузчиков и люкоподъёмниками для за-
крывания крышек люков полувагонов, а также сменным рабочим оборудованием
(накладным вибратором для очистки кузовов полувагонов, выброрыхлителем
127
смёрзщихся грузов, который навешивается на кран посредством быстросъёмного
устройства и поворотной головки). Такая технология используется при
30 ваг./сут. Схема комплексной механизации приведена на рис. 5.15.
n сут. =
При применении этой схемы рекомендуется следующая технология выпол-
нения операций выгрузки. После подачи вагонов на повышенный путь маневро-
вым локомотивом двое рабочих с мостиков, укреплённых на дополнительной
ферме крана, с обоих сторон вагонов срезаются проволоки Ш4 мм, которыми
были увязаны разгрузочные люки за запорные угольники вагона. Затем рабочие
последовательно вручную поворачивают сектора и с помощью лома люковые
закидки. Так открываются разгрузочные люки полувагона. Рабочие совместно с
дополнительной фермой крана передвигаются вдоль повышенного пути по ме-
ре открывания люков полувагона.
Процесс выгрузки грузов по основной технологии (рис. 5.19) предусматри-
вает участие машиниста крана (крановщика) и двух грузчиков, одновременно
открывающих или закрывающих крышки люков полувагонов.
Рис. 5.19. Схема комплексной механизации выгрузки сыпучих грузов из
полувагонов на повышенном пути, перекрытым козловым краном:
1 – ферма-приставка; 2 – накладной вибратор (виброрыхлитель);
3 – вибрационный гидравлический грейфер;
4 – бункерная установка; 5 – автомобиль; 6 – козловой кран;
7 – повышенный путь; 8 – вагон; 9 – автодорога.
128
Машинист крана (крановщик) включает механизмы передвижения крана
по сигналам каждого из грузчиков с нижней площадки дополнительной фермы-
моста крана для обеспечения согласованной работы по открыванию крышек
люков. Аналогично подаются сигналы при заключительном проходе крана для
выполнения операций закрывания крышек разгрузочных люков с использова-
нием люкозакрывателей. Повышение производительности труда при выгрузке
достигается, если пульт управления передвижения крана расположен на одной
из нижних площадок. Тогда на выгрузке заняты только два работника ком-
плексной бригады, а сигнал о возможности дальнейшего продвижения крана
подаёт рабочий с площадки, не имеющей пульта управления.
При обратном движении крана для очистки полувагона от остатка груза на
верхний обвязочный пояс полувагона опускают накладной вибратор, навешан-
ный тросами на козловой кран, т. е. очистка вагона осуществляется механизи-
рованным способом.
При следующем передвижении крана производится закрывание крышек
разгрузочных люков полувагонов люкоподъёмниками, установленными на мос-
тиках, т. е. механизированным способом. Схема работы люкоподъёмника пока-
зана на рис. 5.20.
Рис. 5.20. Схема работы люкоподъёмника:
1− полувагон; 2 − трос с крюком для подъёма крышек люков
полувагона; 3 − лебёдка, установленная на монорельсе 4,
укреплённом на стойки 5.
Принцип работы люкоподъёмника следующий. Рабочий зацепляет крюком
крышку разгрузочного люка вагона и включает электродвигатель лебёдки. При
этом крюк поднимет крышку разгрузочного люка вагона, после чего рабочие
фиксируют её люковыми закидками.
После окончания операций по выгрузке и очистке полувагонов вибратор
заменяется на грейфер для погрузки грузов в автомобили, в промежуточные
бункера или отвалки в штабеля оперативного хранения.
Режим работы кранов при выгрузке сыпучих грузов из полувагонов дол-
жен обеспечивать сохранность конструкции вагонов. В частности, не допуска-
ется свободное «бросание» грейфера с высоты на груз без подтормаживания.
Преимущества такой технологии:
– высокая производительность выгрузочных операций;
– механизированный способ закрывания разгрузочных люков;
129
– механизация процесса зачистки полувагона;
– возможность рыхления затвердевших насыпных грузов рыхлителями.
4-я технология. По этой технологии применяется повышенный путь, пере-
крытый мостовым краном грузоподъёмностью 100 кН, оснащённым грейфером,
накладным вибратором и люкоподъёмником. Мостовой кран более производи-
тельный, чем козловой. Такая технология используется при n сут. = 40 ваг./сут.
Схема комплексной механизации, технология выгрузки груза, преимущества и
недостатки такие же, как и у 3-й технологии.
5-я технология. Эта технология применяется при
n сут. = 50 ваг./сут. Для
выгрузки насыпного груза используется ковшово-элеваторный разгрузчик кон-
струкции инж. Ш.С. Хабибулина ТР-2 (С-492), конструкция (рис.10.25) и прин-
цип работы которого будут изучены на практических занятиях 10.10.
Технология выгрузки насыпных грузов следующая. Элеватор устанавливают
над грузом рядом с торцевой стенкой разгружаемого вагона. После этого последо-
вательно включают отвальный и поперечный конвейеры, а затем и ковшовый эле-
ватор. Постепенно ковшовый элеватор опускается в вагон, ковши зачёрпывают
груз и, освобождаясь от него вверху, передают груз на поперечный ленточный
конвейер. Затем груз следует на отвальный конвейер и далее в штабель.
После того как ковшовый элеватор опустится в нижнее предельное поло-
жение, включают механизм передвижения портала. Перемещаясь вместе с пор-
талом относительно вагона, этот элеватор своими ковшами продолжает черпать
груз, осуществляя разгрузку вагона.
Преимущества технологии: возможность зачерпывания груза одновре-
менно по всей ширине вагона благодаря значительной ширине ковшей элевато-
ра. Поэтому разгрузчик ТР-2 (С-492) отличается высокой производительностью
– 1800…2000 кН/ч.
Недостатки технологии:
– значительные остатки груза в вагоне – до 35 кН и более, что вынуждает
выполнять целый ряд вспомогательных операций;
– не приспособлена для выгрузки груза размером кусков более 80 мм и
смёрзшихся в вагоне;
– необходимость установки с противоположной стороны на опорной балке
портала противовеса с весом 36 кН при одностореннем навешивании отвально-
го конвейера.
6-я технология. Эта технология применяется при
n сут. = 100 ваг./сут. и
выше. Для выгрузки насыпного груза используются вагоноопрокидыватели,
конструкция (рис. 5.21 и 10 24) и принцип работы которых будут изучены на
практических занятиях 10.9. Вагоноопрокидыватели являются самыми высоко-
производительными машинами (у ВРС-2 − 18000 кН/ч., а у ВРС-125 − 17000
кН/ч.
130
Рис. 10.24. Вагоноопрокидыватель ВРС-125.
1 − ротор; 2 − вибраторы для рыхления груза; 3 − верхние балки;
4 − трубчатые фермы; 5 − роликовая балансирная опора; 6 − привод
Дата добавления: 2020-04-08; просмотров: 1165; Мы поможем в написании вашей работы! |
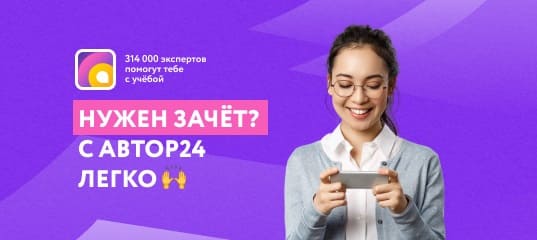
Мы поможем в написании ваших работ!