НОРМИРОВАНИЕ ТОЧНОСТИ ГЛАДКИХ ЦИЛИНДРИЧЕСКИХ СОЕДИНЕНИЙ
Предисловие
Учебное пособие, переработанное и дополненное, посвящается светлой памяти Артемия Николаевича Спасского, кандидата технических наук, доцента кафедры «Технология машиностроения», длительное время читавшего лекции по дисциплинам «Технология машиностроения» и «Взаимозаменяемость, стандартизация и технические измерения».
Первая рукописная редакция справочно-методического пособия была составлена доцентом А.Н. Спасским и ассистентом Т.М. Ионовой при участии старшего преподавателя С.Ф. Магницкой. Пособие имело все необходимые данные для выполнения курсовой работы по «Взаимозаменяемости, стандартизации и техническим измерениям» и пользовалось большим спросом у студентов.
В 1992 г. оно было переиздано под общей редакцией профессора Л.А. Болдина в виде светокопий. Так как пособие не потеряло актуальности и получило признание многих поколений студентов, преподавателями кафедры принято решение издать его в новой редакции с учетом требований действующих стандартов, дополнив поясняющими текстами из теории.
Первое издание, подготовленное коллективом авторов кафедры, вышло в 2001году. Первая глава составлена Т.Н. Гребневой и С.Ф. Магницкой. Вторая разработана В.Н. Кайновой и Г.И. Лебедевым, так как нормирование требований к точности формы и расположения поверхностей особенно актуально в настоящее время. Третья и четвертая главы составлены С.Ф. Магницкой, пятая глава −Т.Н. Гребневой, шестая глава − В. Н. Кайновой и Т.Н. Гребневой.
|
|
Во втором издании переработаны все шесть глав с учетом изменений в области стандартизации и добавлены новые главы −7 и 8, которые рассматривают вопросы, решаемые в курсовой работе.
Глава седьмая подготовлена В.Н. Кайновой и Г.И. Лебедевым, а восьмая глава − С.Ф. Магницкой и И.Н. Фроловой.
Авторы приносят глубокую благодарность за ценные предложения и замечания по улучшению содержания учебного пособия всем преподавателям кафедры «Технология машиностроения» НГТУ и лично профессору, кандидату технических наук, Л.А. Болдину, кандидату технических наук, доценту А.А.Симонову, кандидату технических наук, доценту И.Н.Фроловой, а также рецензентам: зав. кафедрой «Технология металлов и машиноремонта» доктору технических наук, профессору А.С. Курникову, главному технологу, кандидату технических наук, доценту АО НАЗ «Сокол» П.М. Королеву.
Все замечания и предложения, которые будут с признательностью восприняты коллективом авторов, могут быть направлены по адресу:
603950, г.Н. Новгород, ул. Минина, д. 24; НГТУ, корпус 2, кафедра «Технологии машиностроения».
ВВЕДЕНИЕ
Конструкторская документация является основным видом документов, которые используются для проектирования технологических процессов обработки и сборки, контрольно-измерительных операций, а также при выполнении работ по сертификации. При разработке конструкторской документации необходимо соблюдать требования действующих стандартов. Точность существенно влияет на качество изделий, на трудоемкость их изготовления, а, следовательно, и на себестоимость.
|
|
Студенты большинства конструкторских специальностей выполняют курсовую работу, в которой осваивают нормирование точности основных соединений, применяемых в различных отраслях машиностроения. Цель данного учебного пособия − помочь студентам в решении указанных задач. Пособие состоит из восьми глав, в которых приводятся сведения из теории, а также справочные таблицы из стандартов. Номенклатура рассматриваемых параметров ограничена предлагаемыми вариантами заданий к курсовой работе.
Первая глава содержит материалы по выбору и расчету допусков и посадок, методы расчета размерных цепей и требования к точности угловых размеров.
Вторая глава дополнена новыми требованиями к шероховатости поверхностей, а также даны рекомендации, позволяющие нормировать точность формы и расположения поверхностей деталей машин.
|
|
Третья глава содержит сведения по призматическим шпонкам и прямобочным шлицам. Даны примеры выполнения рабочих чертежей со шпоночными и шлицевыми соединениями.
В четвертой главе приводится структура обозначения подшипников, а также требования к точности подшипников, посадочных поверхностей вала и корпуса под установку подшипника. Дан пример выполнения части сборочного чертежа с посадками подшипника на валу и в корпусе и примеры рабочих чертежей посадочных мест под подшипник вала и корпуса с указанием требований по точности размеров, формы и расположения.
Существенно переработаны главы пятая и шестая: пятая глава дополнена требованиями к точности резьбы с натягами и по переходным посадкам; в шестой главе обращено внимание на выбор степеней точности зубчатых передач и видов сопряжений и контрольного комплекса.
Седьмая глава определяет факторы, влияющие на выбор средств и методов измерений, приведены рекомендации по выбору средств измерений в зависимости от контролируемых параметров и точности универсальных средств.
Восьмая глава содержит необходимые сведения для проектирования гладких калибров для контроля валов и отверстий.
|
|
Во все главы внесены изменения и дополнения согласно вновь изданным нормативным документам.
ГЛАВА 1. НОРМИРОВАНИЕ ТОЧНОСТИ ЛИНЕЙНЫХ
И УГЛОВЫХ РАЗМЕРОВ
НОРМИРОВАНИЕ ТОЧНОСТИ ГЛАДКИХ ЦИЛИНДРИЧЕСКИХ СОЕДИНЕНИЙ
1.1.1. Основные понятия и термины
Качество изделий машиностроения зависит от геометрической точности деталей, входящих в них.
Точность есть понятие совокупное, и может быть оценена точностью размеров элементов детали, точностью формы поверхностей и их взаимным расположением, волнистостью и шероховатостью. Нормирование точности размеров осуществляется стандартами Единой системы допусков и посадок (ЕСДП) через систему ГОСТов (Государственных стандартов) [1,4,6,12].
Размер – числовое значение линейной величины (диаметр, длина и т.п.) в выбранных единицах измерения. Под размером элемента в цилиндрических соединениях понимается диаметр, в плоских – расстояние между параллельными плоскостями по нормали к ним. Числовые значения размеров в машиностроении задаются в миллиметрах (мм).
Различают размеры:
· номинальный – размер, относительно которого определяются предельные размеры и который служит началом отсчета отклонений (нулевая линия), назначается из числа стандартных по ГОСТ 6636.
· предельные (наибольший и наименьший) – два предельно допустимых размера, между которыми должен находиться или которым может быть равен действительный размер годной детали;
· действительный – размер, установленный измерением с допускаемой погрешностью.
В соединении элементов двух деталей один из них является внутренним (охватывающим), другой – наружным (охватываемым). В ЕСДП всякий наружный элемент называется валом, всякий внутренний элемент – отверстием. Термины «отверстие» и «вал» применяются и к несопрягаемым элементам.
Допуск Т – разность между наибольшими и наименьшими предельными размерами или алгебраическая разность между верхним и нижним отклонениями.
Стандартный допуск IT – любой из допусков, устанавливаемый системой ЕСДП.
Квалитет – совокупность допусков, соответствующих одинаковой степени точности для всех номинальных размеров.
Отклонением размера называется алгебраическая разность между размером (действительным, предельным) и номинальным размером.
Основное отклонение (рис. 1.1) – одно из двух предельных отклонений размера (верхнее или нижнее), определяющее положение поля допуска относи-
тельно нулевой линии (номинального размера). В данной системе ЕСДП основным отклонением является ближайшее к нулевой линии.
Поле допуска – поле, ограниченное наибольшим и наименьшим предельными размерами и определяемое величиной допуска и его положением относительно номинального размера (рис. 1.1).
Принятые обозначения:
D (d) – номинальный размер отверстия (вала);
Dmax(dmax), Dmin (dmin), D(d)e, Dm(dm ) – размеры отверстия (вала), наибольший (максимальный), наименьший (минимальный), действительный, средний.
Е S (es) – верхнее отклонение отверстия (вала);
EI (ei) – нижнее отклонение отверстия (вала);
S , Smax, Smin,Sm – зазоры, наибольший (максимальный), наименьший (минимальный), средний соответственно;
N, Nmax, Nmin, Nm – натяги, наибольший (максимальный), наименьший (минимальный), средний соответственно;
TD, Td, TS, TN, TSN - допуски отверстия, вала, зазора, натяга, зазора-натяга (в переходной посадке) соответственно;
IT1, IT2, IT3…….. ITn ……. IT18. – допуски по квалитетам обозначаются сочетанием букв IT с порядковым номером квалитета.
При обработке каждая деталь приобретает свой действительный размер и может быть оценена как годная, если он находится в интервале предельных размеров, или забракована, если действительный размер вышел за эти границы. Условие годности деталей может быть выражено следующим неравенством:
Dmax(dmax) ³ D(d)e ³ Dmin (dmin).
Допускявляется мерой точности размера. Чем меньше допуск, тем меньше допустимое колебание действительных размеров, тем выше точность детали и, как следствие, увеличивается трудоемкость обработки и ее себестоимость:
TD = Dmax – Dmin = | ES – EI | – для отверстия;
Td = dmax – dmin = | es – ei | – для вала.
Отклонения могут быть действительными или предельными, а предельные – верхним ES(es) и нижним EI (ei):
для отверстия ES = Dmax – D ; EI = Dmin – D ; для вала es = dmax – d ; ei = dmin – d ..
Отклонения могут принимать значения:
• положительные (со знаком плюс), если Dmax (dmax), Dmin (dmin) > D (d),
• отрицательные (со знаком минус), если Dmax (dmax ), Dmin (dmin) < D (d)
• равные нулю, если Dmax (dmax) = D (d) или Dmin (dmin) = D (d).
На рис. 1.1 изображены схемы расположения полей допусков отверстия и вала, а также указаны предельные размеры отверстия и вала, определяемые верхним и нижним отклонениями относительно номинального размера (нулевой линии).
Посадка - это соединение двух деталей, в результате чего образуется зазор или натяг. Разность размеров отверстия и вала до сборки определяет характер соединения деталей. Различают посадки с зазором, посадки с натягом и переходные посадки.
Зазор − разность между размером отверстия и вала до сборки S = D – d, если размер отверстия больше размера вала D > d. Зазор характеризует большую или меньшую свободу относительного перемещения деталей в соединении. Посадки c зазором применяются в подвижных соединениях, в которых детали в процессе работы перемещаются в продольном (осевом) направлении или вращаются относительно друг друга.
Натяг − разность размеров вала и отверстия до сборки N = d – D, если действительный размер вала больше действительного размера отверстия d > D . Натяг характеризует степень сопротивления взаимному смещению деталей в соединении. Посадки с натягом предназначены для получения неразъемных соединений, в которых неподвижность деталей обеспечивается за счет сил трения на контактных поверхностях. Посадки с натягом преимущественно выполняются тепловым способом (нагрев втулки или охлаждение вала), а при малых натягах используется силовой способ ( сборка под прессом).
В переходных посадках может получиться или зазор или натяг в зависимости от действительных размеров отверстия и вал. Они обеспечивают точное центрирование (соосность) втулки относительно вала, применяются для неподвижных (вдоль оси) соединений с дополнительным креплением.
![]() ![]() ![]() ![]() ![]() ![]() ![]() ![]() ![]() ![]() ![]() ![]() ![]() |
а) б)
Рис. 1.1. Схемы расположения полей допусков:
а – отверстия (ES и EI – положительные); б – вала (es и ei – отрицательные)
Дата добавления: 2019-02-22; просмотров: 1169; Мы поможем в написании вашей работы! |
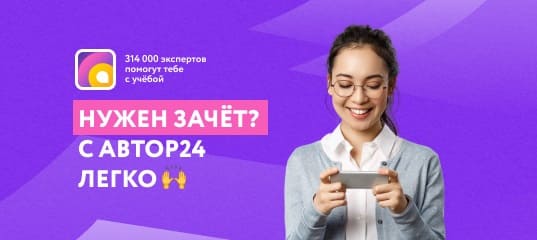
Мы поможем в написании ваших работ!