Системы безопасности, радиосвязь, скоростемеры , контрольно-измерительные приборы
15.8.1 Ремонт скоростемеров и их приводов производится в соответствии с инструкцией по эксплуатации и ремонту локомотивных скоростемеров и приводов к ним (приложение 15 к настоящему Руководству).
15.8.2 Ремонт систем безопасности производится в соответствии с действующими инструкциями.
15.8.3 Производится поверка контрольно-измерительных приборов в соответствии с требованиями, установленными федеральным органом исполнительной власти в области стандартизации, метрологии и сертификации.
15.8.4 Проверка устройств поездной радиосвязи производится в соответствии с инструкциями и технологическим процессом обслуживания аппаратуры поездной радиосвязи.
15.8.5 Монтажные провода и кабели, клеммные сборки проверяются в объеме общих требований настоящего Руководства с замером сопротивления изоляции по нормам соответствующего рабочего напряжения.
Регулятор напряжения генераторов
Электронный регулятор напряжения демонтируется и направляется в цех электроники для ремонта, регулировки и проведения испытаний.
Проверка и испытания регулятора напряжения производятся в соответствии с Программой и методикой испытаний Э2411.00.00 ПМ и Руководством по эксплуатации регулятора напряжения Э2411.00.00РЭ.
Пульт управления УНИКАМ ПУ2РК
Выполняются работы, приведенные в п. 14.12 настоящего Руководства.
Установка пожаротушения УП-ТПС
|
|
Выполняются работы, приведенные в п. 14.13 настоящего Руководства.
Установка пожарной сигнализации УПС-ТПС
Выполняются работы, приведенные в п. 14.14 настоящего Руководства.
Бортовая подсистема контроля температуры подшипниковых узлов электровоза
Выполняются работы, приведенные в п. 14.15 настоящего Руководства.
Микропроцессорная система управления локомотивам МСУЛ, единая система автоведения и управления тяговым приводом ЕСАУП
Выполняются работы, приведенные в п. 14.16 настоящего Руководства.
Преобразователь напряжения в код ПНКВ-1 и блоки БИВМ
Выполняются работы, приведенные в п. 14.17 настоящего Руководства.
Стабилизированный преобразователь напряжения электропневматического тормоза модернизированный СПН ЭПТ М
Преобразователь снимается с локомотива, проверка его технических характеристик проводится на контрольно – испытательном стенде КИС СПН-Д НКРМ.468211.004 или на «Стенде для испытаний источников питания и блоков управления ЭПТ» А1970.100.00 в комплекте со специальной приставкой МК СПН НКРМ.424911.002 в соответствии с Руководством по эксплуатации к указанным стендам.
Система кондиционирования
|
|
Ремонт кондиционеров производится в соответствии с инструкцией завода–изготовителя.
Система отопления
15.18.1 Электропечи, калориферы и обогреватели разбираются, детали очищаются. Проверяется сопротивление элементов в соответствии с техническими данными. Элементы, имеющие обрыв выводов, коробление и вмятины, заменяются.
Кожухи печей и калориферов надежно заземляются с помощью установочных винтов на металлических стенках или на бобышках, приваренных к корпусу электровоза.
Проверяется исправность блокировочных устройств калориферов.
15.18.2 В случае оборудования локомотива жидкостной системой отопления, выполняются работы, указанные в п.14.20.5, 14.20.6, и, кроме того, тэны снимаются, очищаются, проверяются их электротехнические характеристики.
Проверка положения кузова и тележек
После посадки кузова на тележки проверяются на прямом нивелированном участке пути:
высота осей автосцепок;
разница высот автосцепок по концам электровоза;
высота путеочистителей от головки рельсов;
зазоры между вертикальными и горизонтальными ограничителями рамы кузова и тележек;
зазоры между рамой тележки и буксами;
вертикальный перекос продольных балансиров и рессор.
|
|
Испытание и приемка электровоза
15.20.1 После окончания текущего ремонта ТР-3 электровоза на ремонтном стойле производятся следующие проверки по его оборудованию:
измерение сопротивления изоляции цепей напряжением до 380 В включительно мегаомметром на 500 В;
измерение сопротивления изоляции цепей напряжением свыше 380 В мегаомметром на 2500 В;
работу и последовательность срабатывания электрических аппаратов с пульта управления машиниста из обеих кабин при номинальных значениях напряжения в цепях управления, давления воздуха;
проверку работы аварийных схем;
испытание тормозной рычажной передачи при давлении воздуха в тормозных цилиндрах 0,6 МПа (6 кгс/см2).
15.20.2 Проверка действия оборудования электровоза после текущего ремонта ТР-3 под напряжением контактной сети производится под руководством мастера или бригадира.
Перед проверкой выполняются следующие работы:
контролируется отсутствие на крыше электровоза, в высоковольтных камерах, под электровозом исполнителей работ, а также посторонних предметов и инструмента;
проверяется действие и регулируется работа звуковых сигналов и стеклоочистителей, предохранительных клапанов.
Проверяется действие защиты силовых и вспомогательных цепей и защиты от боксования.
|
|
Проверяется работа всех аппаратов, машин и схем при опущенном и поднятом токоприемнике.
Производится испытание тормозного оборудования в соответствии с требованиями инструкции по техническому обслуживанию, ремонту и испытанию тормозного оборудования локомотивов и моторвагонного подвижного состава (приложение 15 к настоящему Руководству).
Проверяется работа системы подачи песка, действие АГС.
Проверяется соответствие вращения колесных пар положению реверсивной рукоятки контроллера машиниста.
15.20.3 По окончании проверки действия оборудования электровоза на ремонтном стойле, под напряжением контактной сети и обкаточных испытаний на электрифицированном участке под рабочим напряжением, производятся записи о выполненном ремонте в книге ремонта локомотива ТУ-28, паспорте электровоза и технических паспортах оборудования.
При проведении всех видов испытаний электровоза должны соблюдаться требования правил и инструкций по технике безопасности при ремонте и эксплуатации электроподвижного состава.
15.20.4 После указанных испытаний производится обкатка электровозов на электрифицированном участке.
До выезда на главные пути проверяются:
правильность положения кранов пневматических магистралей;
исправность действия тормозов;
действие сигнальных фар, прожекторов и звуковых сигналов;
работа систем безопасности, радиосвязи, систем МСУЛ или ЕСАУП.
Во время обкатки производится проверка работы основного и вспомогательного оборудования электровоза на всех рабочих и аварийных режимах.
По окончании обкатки проверяется состояние:
тяговых электродвигателей, вспомогательных машин, а также электрических аппаратов;
подшипников редукторов и букс (по нагреву);
ходовых частей и деталей рессорного подвешивания;
корпусов тяговых редукторов и подвесок тяговых двигателей, редукторов.
Проверяется и окончательно регулируется положение кузова и тележек.
15.20.5 После обкаточных испытаний производится проверка и регулирование нагрузок от колес электровоза на рельсы путем вывешивания электровоза по осям и колесам с помощью специального устройства. Регулированию продольной развески подлежат оси, имеющие отклонения от среднего значения статической нагрузки всех осей более ± 3%, поперечной развески ± 4%. Вывешивание и регулирование нагрузок от колес на рельсы выполняется в соответствии с технической документацией, разработанной ПКБ ЦТ ОАО «РЖД».
Приложение 1. | |||||
НОРМЫ ДОПУСКОВ И ИЗНОСОВ МЕХАНИЧЕСКОГО ОБОРУДОВАНИЯ | |||||
1.1. Нормы допусков и износов механической части электровозов ЧС2, ЧС2Т, ЧС2К | |||||
| |||||
№ п/п |
Наименование деталей и размеров | Размер, мм | |||
чертежный | допускается при выпуске из ремонта
|
браковочный в эксплуатации | |||
капитального | текущего ТР-3 | ||||
1 | 2 | 3 | 4 | 5 | 6 | |
1. Рамы тележки и кузова | ||||||
1.1 | Расстояние между осями стаканов под направляющие букс в одной боковине рамы | 680 ± 0,3 | 680 ± 0,3 | – | – | |
1.2 | Смещение осей отверстий под направляющие букс в боковине рамы | ± 0,2 | ± 0,2 | – | – | |
1.3 | Расстояние между осями отверстий стаканов направляющих букс правой и левой стороны одной оси | 2070 ± 0,3 | 2070 ± 1 | – | – | |
1.4 | Продольное смещение осей буксовых направляющих правой и левой стороны оси относительно друг друга | Не более 0,3 | Не более 0,7 | – | – | |
1.5 | Внутренний диаметр стаканов под направляющие букс: а) верхней части б) нижней части | 70 +0,03 110 +0,054 | 70 +0,5 110 +0,5 | – – | – – | |
1.6 | Натяг запрессовки направляющей буксы в раму | 0,013 – 0,089 | 0,013 – 0,089 | 0,013 – 0,089 | – | |
1.7 | Внутренний диаметр втулки в кронштейне рамы под валик для крепления подвески рессоры тележки | 65 +0,19 | 65 +0,3 | 65 +0,7 | – | |
1.8 | Натяг запрессовки втулки подвески в кронштейн рамы | 0,013 – 0,062 | 0,013 – 0,062 | 0,013 – 0,062 | – | |
1.9 | Внутренний диаметр втулки в кронштейне рамы под валик для крепления балансира рессорного подвешивания тележки | 80 +0,19 | 80 +0,2 | 80 +0,2 | – | |
1.10 | Натяг запрессовки втулки балансира в кронштейне рамы | 0,036 – 0,093 | 0,036 – 0,093 | 0,036 – 0,093 | – | |
1.11 | Расстояние между внутренними поверхностями боковины рамы | 1840 ± 1 | 1840 ± 2 | – | – | |
1.12 | Диаметр резьбы в отверстиях шкворневой балки для крепления тягового двигателя | М45 ´ 3 | М45 ´ 3 | М45 ´ 3 | – | |
1.13 | Расстояние от передних упоров фрикционного аппарата в буферном брусе рамы кузова до передней плоскости бруса | 390 ± 3 | 390 ± 3 | ![]() | _ | |
1.14 | Расстояние между передними и задними упорами фрикционного аппарата в буферном брусе | 625 -3 | 625 -3 | 625 ± 3 | – | |
| ||||||
1.15 | Диаметр стержня направляющей буксы | ![]() | ![]() | 105 – 104 | – | |
2. Шкворневое соединение тележки | ||||||
2.1 | Диаметр шкворня | ![]() | 187 – 190* | 185 – 190 | Менее 183 | |
2.2 | Диаметр верхнего посадочного пояса шкворня | ![]() | 200 – 206 | 200 – 206 | – | |
2.3 | Диаметр нижнего посадочного пояса шкворня | ![]() | 240 +0,15 | 240 – 240,3 | – | |
2.4 | Натяг запрессовки шкворня в гнездо рамы кузова | 0,03 – 0,105 | 0,03 – 0,105 | 0,03 – 0,105 | – | |
2.5 | Изгиб шкворня | 0 | 0 | 0 | – | |
2.6 | Суммарный зазор между шкворнем и отверстием в шаровом подшипнике | 0,12 – 0,253 | 0,12 – 0,3 | 0,12 – 0,6 | Более 1,5 | |
2.7 | Диаметр шарового подшипника (по шару) | ![]() | 270 – 272 | 268 – 273 | – | |
2.8 | Местный износ отверстия в шаровом подшипнике (по диаметру) | 0 | 0 – 0,1 | 0 – 0,3 | – | |
2.9 | Суммарный зазор между шаровым подшипником и его вкладышем | 0,21 – 0,464 | 0,21 – 0,6 | 0,21 – 0,9 | Более 1,6 | |
2.10 | Зазор посадки верхней половины вкладыша в нижнюю (не более) | 0,048 | 0,1 | 0,25 | – | |
2.11 | Размер собранных вкладышей (по высоте) | 200 –0,25 | 200 –1 | 200 –2 | Менее 196 | |
2.12 | Размер гнезда в шкворневой балке рамы тележки (по продольной оси электровоза) | 316 +0,36 | 316 – 318 | 316 – 320 | – | |
2.13 | Суммарный зазор между поверхностями скольжения гнезда шкворневой балки рамы и наличниками вкладышей в сборе | 0,2 – 0,96 | 0,2 – 1,0 | 0,2 – 1,6 | – | |
2.14 | Некруглость отверстия в шаре под шкворень, не более | 0,05 | 0,05 | 0,25 | Более 1 | |
2.15 | Наибольший суммарный зазор между вкладышами (в сборе) и гнездом шкворневой балки тележки (по перечной оси) | 60 | 60 | 60 | – | |
2.16 | Зазор между вкладышами в сборе и опорой гнезда главного шкворня (в продольном направлении) | 0,5 – 0,95 | 0,5 – 0,95 | 0,5 – 0,95 | – | |
3. Боковые опоры кузова | ||||||
3.1 | Наибольший износ шаровой поверхности опоры (с восстановлением смазочных канавок) | 0 | 0,5 | 1,5 | 2 | |
3.2 | Наименьшая толщина скользуна (с восстановлением смазочных канавок) по центру шаровой поверхности | 24 | 22 | 20 | – | |
3.3 | Ширина шарового скользуна | 177 +0,5 | Не менее 176,6 | Не менее 175,5 | – | |
3.4 | Толщина плиты скользуна | 12 ± 0,2 | Не менее 11 | Не менее 10 | Менее 9 | |
3.5 | Наибольшее расстояние между наличниками на боковых стенках масляной ванны | 181 +0,5 | 181 +0,8 | 181 +1,1 | – | |
3.6 | Наибольший зазор между шаровым скользуном и боковым наличником (в мм на сторону) | 2 | 2,4 | 3,0 | Более 3,5 | |
3.7 | Вертикальный зазор между кузовом и упором на раме тележки | ![]() | ![]() | ![]() | Менее 25 | |
4. Муфта соединения между тележками | ||||||
4.1 | Диаметр пальца | ![]() | 120 –119 | 120 – 117 | Менее 115 | |
4.2 | Натяг запрессовки пальца в ступицу | 0,122 - 0,172 | 0,122 - 0,172 | 0,122 - 0,172 | - | |
4.3 | Зазор между шейкой пальца и отверстием в шаровой втулке | 0,12 - 0,48 | 0,12 - 0,5 | 0,12 - 1,0 | Более 3 | |
4.4 | Зазор между поверхностью втулки и подшипником (по шару) | 0,145 - 0,645 | 0,145 - 0,65 | 0,145 - 1,0 | Более 2* | |
4.5 | Диаметр цапфы толкателя | ![]() | 80 - 79 | 80 - 78 | Менее 77 | |
4.6 | Местный износ отверстия в шаровом подшипнике (по диаметру) | 0 | 0 - 0,1 | 0 - 0,3 | - | |
4.7 | Натяг запрессовки втулок в кронштейны | 0,010 - 0,070 | 0,010 - 0,070 | 0,010 - 0,070 | – | |
4.8 | Зазор между втулкой кронштейна и цапфой толкателя | 0,5 - 1,19 | 0,5 - 1,5 | 0,5 - 1,5 | Более 2,5 | |
4.9 | Толщина наличников подшипника муфты и накладок направляющих | 6,5 ± 0,2 | 6,5 - 6,1 | 6,5 - 5,8 | Менее 5,0 | |
4.10 | Наибольший суммарный зазор между наружной торцевой плоскостью подшипника и торцом цапфы болта (толкателя) | 12 | 12 | 12 | Более 17 | |
4.11 | Суммарный вертикальный зазор между наличниками подшипника и накладками направляющих | 0,6 - 1,0 | 0,6 - 1,0 | 0,6 - 2,0 | Более 3,5 | |
4.12 | Суммарный горизонтальный зазор между наличниками и накладками | 1,0 - 1,47 | 1,0 - 1,5 | 1,0 - 2,0 | Более 3,5 | |
5. Колесные пары | ||||||
5.1 | Диаметр шеек оси под буксовые подшипники | 180 –0,08 | 180 –0,20 | 180 –0,30 | – | |
5.2 | Наибольшее допустимое биение шеек оси под буксовые подшипники | 0,02 | 0,03 | 0,03 | - | |
5.3 | Толщина бандажей по кругу катания при скорости: до 120 км/ч свыше 120 км/ч | 90 90 | 85 - 100 85 - 100 | – *1 – *1 | Менее 45 Менее 55 | |
5.4 | Разница диаметров бандажей по кругу катания: а) у комплекта колесных пар электровоза б) у одной колесной пары | 0 - 2 0 - 0,5 | 0 - 5 0 - 0,5 | 0 - 5 0 - 0,5 | Более 12 Более 1*2 | |
5.5 | Биение бандажа по кругу катания | 0 - 0,4 | 0 - 0,5 | 0 - 0,5 | Более 0,5*2 | |
5.6 | Местное увеличение ширины бандажа | 0 - 0,5 | 0 - 1 | 0 - 1 | Более 3 | |
5.7 | Равномерный наплыв по наружной грани бандажа | 0 | 0 | 0 | Более 5 | |
5.8 | Расстояние между внутренними гранями бандажей у ненагруженной колесной пары: | |||||
до 120 км/ч | 1440 -1 | ![]() | ![]() | Более ![]() | ||
свыше 120 км/ч | 1440 -1 | 1440 ± 1 | 1440±1 | Более ![]() | ||
5.9 | Разность расстояний между внутренними гранями бандажей у одной неподкаченной колесной пары | 0 - 1,0 | 0 - 1,0 | 0 - 1,0 | – | |
5.10 | Расстояние от торца оси до торца ступицы центра колесной пары | 300 ± 0,2 | 300 ± 0,2 | – | – | |
6. Буксовый узел | ||||||
6.1 | Диаметр внутренней цилиндрической части буксы под роликоподшипник | ![]() | ![]() | ![]() | - | |
6.2 | Некруглость внутренней цилиндрической части корпуса буксы, не более: а) при расположении большого диаметра по вертикали б) то же по горизонтали | 0,03 0,03 | 0,20 0,15 | 0,33 0,25 | - - | |
6.3 | Конусообразность внутренней цилиндрической части корпуса буксы, не более | 0,03 | 0,08 | 0,15 | - | |
6.4 | Диаметр отверстий в корпусе буксы под амортизаторы направляющих | 175 +0,04 | 175 +0,1 | – | – | |
6.5 | Расстояние между осями отверстий под амортизаторы | 680 ± 0,3 | 680 ± 0,3 | 680 ± 0,3 | – | |
6.6 | Натяг запрессовки втулки амортизатора в буксу | 0,018 – 0,085 | 0,018 – 0,085 | 0,018 – 0,085 | – | |
6.7 | Внутренний диаметр втулки амортизатора | 120 +0,04 | 120 +0,1 | – | – | |
6.8 | Натяг запрессовки стакана направляющей во втулку амортизатора | 0,035 – 0,095 | 0,035 – 0,095 | 0,035 – 0,095 | – | |
6.9 | Зазор между стаканом и направляющей буксы, не более | 0,39 | 0,6 | 1,4 | – | |
6.10 | Диаметр отверстия в проушине корпуса буксы (под втулку) для подвески рессоры тележки | 75 +0,03 | 75 +0,1 | 75 +0,5 | – | |
6.11 | Расстояние между проушинами буксы | 210 ± 2 | 210 ± 2 | 210 ± 2 | – | |
6.12 | Неперпендикулярность переднего и заднего торцов корпуса буксы к оси отверстия под подшипник, не более | 0,05 | 0,07 | – | – | |
6.13 | Натяг посадки лабиринтного кольца на предступичную часть оси | 0,07 – 0,145 | 0,05 – 0,145 | 0,04 – 0,145 | – | |
6.14 | Некруглость и конусообразность посадочной поверхности лабиринтного кольца буксы, не более | 0,03 | 0,05 | 0,07 | – | |
6.15 | Внутренний диаметр стяжной втулки | ![]() | ![]() | – | – | |
6.16 | Усилие запрессовки стяжной втулки в кН(тс) | 400+20 (40+2) | 400+20 (40+2) | 400+20 (40+2) | – | |
6.17 | Продвижение стяжной втулки при запрессовки усилием 400–420 кН (40+2тс) | 0,75 – 1,35 | 0,75 – 1,35 | 0,75 – 1,35 | – | |
6.18 | Зазоры между торцами крышек и кольцом подвижного подшипника, не более | 3 | 3 | 3 | – | |
6.19 | Зазор между передней крышкой и торцом наружного кольца неподвижного подшипника, не более | 0,2 | 0,2 | 0,5 | – | |
6.20 | Размер по ширине хвостовика стопорной планки (предохранителя) торцевой гайки | 21 –0,2 | 21 –0,2 | 21 –0,5 | – | |
6.21 | Внутренний диаметр стакана направляющей буксы | 105 +0,22 | 105 +0,3 | 105 +0,7 | 105,8 | |
6.22 | Диаметр выточки в буксе под предохранительное кольцо амортизатора | 180 +1,0 | 180 +1,0 | – | – | |
7. Токоотводящее устройство | ||||||
7.1 | Толщина контактной шайбы на оси колесной пары | 35 ± 0,1 | ![]() | ![]() | – | |
7.2 | Высота контактного кольца | 40 | 40 – 38 | 40 – 32 | Менее 24 | |
7.3 | Размер от опорной поверхности корпуса под крышку до контактной поверхности шайбы | 80 ± 0,2 | 80 ± 0,2 | ![]() | – | |
7.4 | Износ паза держателя контактного кольца | – | – | – | 4 | |
7.5 | Суммарная слабина (люфт) между шпонкой (упором) и пазом держателя контактного кольца | – | – | – | 2 | |
7.6 | Наибольшая толщина резинового амортизатора | – | 8 | 8 | 10 | |
7.7 | Глубина утопания сигнализатора износа контактного кольца от торцевой поверхности крышки корпуса заземлителя | – | – | – | 16 | |
7.8 | Натяг посадки контрольного штифта в стакан заземляющего устройства | 0,002 – 0,048 | 0,002 – 0,048 | 0,002 – 0,048 | – | |
8. Рессорное подвешивание тележек и кузова | ||||||
8.1 | Стрела прогиба листовой рессоры в свободном состоянии: а) рессора буксы б) рессора кузова для ЧС2 до № 304 для ЧС2т и ЧС2 с №305 | 51,5 +5 58 +5 83 +5 | 51,5 - 56,5 58 - 63 83 - 88 | 56,5 - 46,5 63 - 53 88 - 78 | Обратный прогиб под нагрузкой Менее 48 Менее 72 | |
8.2 | Износ стенок хомута рессоры, не более | - | 1 | 2 | Более 3 | |
8.3 | Наименьший зазор между верхней частью буксы и плоскостью упора на боковине рамы тележки | 35 +15 | 35 +15 | 35 +15 | Менее 30 | |
8.4 | Диаметр цапфы серьги буксовой рессоры | ![]() | ![]() | 62 | 61 | |
8.5 | Натяг посадки втулки в проушину буксы | 0,005 - 0,065 | 0,005 - 0,065 | 0,005 - 0,065 | – | |
8.6 | Суммарный зазор между цапфой серьги рессоры и втулкой проушины буксы | 0,1 – 0,5 | 0,1 – 0,5 | 0,1 – 0,5 | – | |
8.7 | Диаметр валика подвески рессоры тележки | ![]() | 64,5 - 63,5 | 64,5 - 62,5 | – | |
8.8 | Диаметры валиков рессорного подвешивания: а) кузова б) поводка поперечной балки |
![]() ![]() ![]() ![]() |
![]() ![]() ![]() ![]() | 38–36 50-48 30–29 35–34 | – – – – | |
8.9 | Диаметр валика балансира | ![]() | ![]() | ![]() | – | |
8.10 | Суммарный зазор между валиком и втулкой рессорного подвешивания, имеющими номинальный диаметр, мм: 30 38 50 64,5 79,5 | 0,025-0,083 0,17-0,51 0,17-0,51 0,7-1,1 0,7-1,13 | 0,025-0,1 0,17-0,51 0,17-0,51 0,7-1,3 0,7-1,4 | 0,025-1,0 0,17-1,0 0,17-1,5 0,7-1,5 0,7–1,6 | Более 2 Более 3 Более 3 Более 4 Более 5 | |
8.11 | Износ опорной части рессорной подвески кузова (ремонт, изготовление подвесок по черт. Э290.33.14.00) | 0 | 0-0,4 | 0-0,8 | Более 4 | |
9. Тормозная рычажная передача | ||||||
9.1 | Диаметр цапфы тормозной поперечной балки | ![]() | 53,5–54,5 | 51,5–54,3 | Менее 49 | |
9.2 | Выход штока тормозного цилиндра | 75–100 | 75–100 | 75–100 | Менее 75 Более 100 | |
9.3 | Допускаемые отклонения диаметров валиков и отверстий втулок рычажной передачи от номинального значения, мм: а) для отверстий диаметром от 30 до 50 б) то же свыше 50 в) для валиков диаметром от 30 до 50 г) то же свыше 50 | +0,17 +0,2 –0,34 –0,4 | +0,4 +0,5 –0,5 –0,7 | +0,75 +1,0 –1,8 - 2,0 | Более 2 Более 3 2,5 3,0 | |
9.4 | Зазор между стержнем тормозной тяги и предохранительной скобой по вертикали – с внутренней стороны – « наружной « | – – | Не менее 3 Не менее 10 | Не менее 3 Не менее 10 | Менее 3 Более 10 | |
10. Кронштейны подвески тормозных башмаков | ||||||
10.1 | Отклонения по толщине ушков (верхнее/нижнее) | ±0,5 | +0,5/–1,0 | +0,5/–2,0 | – | |
10.2 | Наибольшее отклонение по ширине зева проушин | +1,5 | +2,0 | +3,5 | – | |
11. Башмаки и колодки | ||||||
11.1 | Диаметр отверстия втул-ки под валик серьги | 45+0,17 | 45+0,17 | 45–46 | – | |
11.2 | Толщина тормозной колодки, не менее | 66 | 66 | 66 | Менее 15 | |
12. Головка штока поршня тормозного цилиндра | ||||||
12.1 | Толщина тела головки | 50 | Не менее 49 | Не менее 48 | Менее 47 | |
12.2 | Наибольший износ штока тормозного цилиндра по диаметру | – | 2 | 3 | Более 4 | |
13. Монтажные допуски по рычажной передаче тормоза | ||||||
13.1 | Наибольшие суммарные зазоры по диаметру между валиком и втулкой в шарнирных соединениях, мм: а) для диаметров от 30 до 50 б) для диаметров свыше 50 | 0,34 0,4 | 0,8 1,0 | 1,5 1,8 | Более 3 Более 4 | |
13.2 | Суммарный зазор вдоль оси валика в проушинах: а) в сочленении кронштейнов с подвесками б) в сочленении тяг между собой и с рычагами | 1–2 1–2 | 1–2 1–2 | 1–3 1–3 | Более 4 Более 6 | |
14. Ударно-сцепные устройства | ||||||
14.1 | Высота горизонтальной оси автосцепки от головок рельсов | ![]() | 1000–1080 | 990–1080 | Менее 980 Более 1080 | |
14.2 | Вертикальный зазор между хвостовиком автосцепки и ударной розеткой | 30±5 | 25–35 | 25–35 | Менее 25 Более 40 | |
14.3 | Расстояние от упора головы автосцепки до ударной розетки | 75±5 | 75±5 | 80±10 | Менее 70 Более 90 | |
14.4 | Высота нижней кромки путеочистителя от головки рельсов | 150±10 | 140–160 | 120–160 | Менее 100 Более 165 | |
15. Тяговый редуктор | ||||||
15.1 | Толщина зуба венца зубчатого колеса, измеренная на расстоянии 12,1 мм от вершины зуба | ![]() | Не менее 17,3 | Не менее 15,8 | Менее 15 | |
15.2 | Наибольшее торцевое биение зубчатого колеса на колесной паре, не более | – | 0,25 | 0,25 | – | |
15.3 | Радиальное биение окружности выступов венца зубчатого колеса, не более | 0,19 | 0,25 | 0,3 | – | |
15.4 | Толщина зуба шестерни, измеренная на расстоянии 12,17 мм от вершины зуба | ![]() | 17,4 | 16 | Менее 15 | |
15.5 | Торцевое биение шестерни, не более | 0,1 | 0,1 | 0,15 | – | |
15.6 | Радиальное биение окружности выступов венца шестерни, не более | 0,080 | 0,1 | 0,12 | – | |
16. Роликовые подшипники редуктора | ||||||
16.1 | Диаметр ступицы колесного центра под подшипники | ![]() | ![]() | ![]() | – | |
16.2 | Натяг посадки подшипников на ступицу центра | 0,04–0,09 | 0,04–0,09 | 0,04–0,09 | – | |
16.3 | Диаметр посадочной части корпуса на наружное кольцо опорного подшипника с допуском | ![]() | ![]() | ![]() | – | |
16.4 | Диаметр ступицы шестерни под подшипник | ![]() | ![]() | ![]() | – | |
16.5 | Натяг на посадку роликового подшипника шестерни | 0,035-0,065 | 0,035-0,065 | 0,035-0,065 | - | |
16.6 | Диаметр отверстия в корпусе под подшипник со стороны тягового двигателя | ![]() | ![]() | ![]() | - | |
16.7 | Диаметр отверстия втулки под подшипник шестерни со стороны колеса | ![]() | ![]() | ![]() | - | |
16.8 | Наружный диаметр втулки подшипника шестерни со стороны колеса | 266 -0,02 | 266 -0,03 | 266 -0,05 | - | |
16.9 | Диаметр отверстия в кольце под втулку подшипника шестерни со стороны колеса | 266 +0,02 | 266 +0,05 | 266+0,10 | – | |
16.10 | Некруглость и конусообразность посадочных поверхностей шестерни под подшипник, не более | – | 0,019 | 0,025 | – | |
17. Корпус редуктора | ||||||
17.1 | Диаметр отверстия в полуфланце под корпус осевых роликовых подшипников | 420 +0,06 | 420 +0,12 | 420 +0,25 | – | |
17.2 | Наибольший суммарный зазор между посадочными поверхностями полуфланца и корпуса осевых роликовых подшипников | 0,1 | 0,2 | 0,3 | – | |
17.3 | Диаметр отверстия в боковине под корпус роликового подшипника шестерни со стороны тягового двигателя | 560 +0,07 | 560 +0,12 | 560 +0,25 | – | |
17.4 | Некруглость отверстия в боковине | – | – | 0,25 | – | |
17.5 | Наибольший суммарный зазор между посадочной частью корпуса роликового подшипника шестерни и боковиной корпуса со стороны тягового двигателя | 0,07 | 0,125 | 0,15 | – | |
17.6 | Диаметр отверстия в боковине корпуса под кольцо подшипника шестерни со стороны колеса | 340 +0,05 | 340 +0,06 | 340 +0,08 | – | |
17.7 | Наибольший суммарный зазор между посадочной частью кольца роликового подшипника шестерни и боковиной корпуса со стороны колеса: ЧС2 ЧС2т | 0,01 0,06 | 0,01 0,06 | 0,02–0,025 0,07 | – – | |
17.8 | Натяг на посадку лабиринтного кольца на ступицу шестерни | 0,003–0,068 | 0,003–0,068 | 0,003–0,068 | – | |
17.9 | Диаметр отверстия втулки кронштейна подвески редуктора | 80 +0,046 | 80 – 80,05 | 80 – 80,4 | 82 | |
17.10 | Суммарный зазор между втулкой и валиком подвески редуктора | 0,1–0,24 | 0,1–0,35 | 0,2–0,6 | Более 2,0 | |
17.11 | Диаметр отверстия в подвеске редукторов под втулку амортизатора | 146 +0,068 | 146 +0,08 | 146 +0,09 | – | |
17.12 | Натяг посадки амортизатора в подвеску | 0,037–0,140 | 0,037–0,140 | 0,037–0,140 | – | |
17.13 | Зазор между валиком и отверстием амортизатора | 0,1–0,24 | 0,1–0,3 | 0,1–0,5 / 0,42 | – | |
18. Тяговый привод | ||||||
18.1 | Диаметр цапфы карданной крестовины | ![]() | ![]() | ![]() | – | |
18.2 | Диаметр отверстия корпуса игольчатого подшипника | ![]() | ![]() | ![]() | – | |
18.3 | Суммарный окружной зазор между иглами в корпусе подшипника | 0,5 | 0,6 | 0,8 | Более 1.0 | |
18.4 | Глубина вмятин на рабочих поверхностях цапф крестовин и корпусов подшипников, не более | – | 0,08 | 0,08 | Более 0,1 | |
18.5 | Разница в диаметре игл при подборе их в подшипник, не более | 0,002 | 0,004 | 0,004 | – | |
18.6 | Толщина зуба торцевых шлицев на высоте 3,6 мм от головки зуба | 10 +0,02 | 10±0,02 | ![]() | – | |
18.7 | Высота зуба торцевого шлица | ![]() | ![]() | ![]() | – | |
18.8 | Зазор между вершиной зуба поводка и впадиной зуба шестерни, не менее | 1,2 | 1,0 | 0,6 | – | |
18.9 | Размер паза в поводке шестерни карданного вала |
![]() ![]() |
![]() ![]() |
![]() ![]() | – – | |
18.10 | Размер шипа (каблучка) корпуса игольчатого подшипника | 25-0,033 | 25-0,033 | 25-0,033 | – |
1.2. Нормы допусков и износов механической части электровозов ЧС7
№ п/п | Наименование деталей и размеров | Серия и индекс электро-воза | Размер, мм | |||
Чертеж-ный | Допускается при выпуске из ремонта | Брако-вочный в эксплу-атации | ||||
капиталь-ного | теку-щего ТР-3 | |||||
1 | 2 | 3 | 4 | 5 | 6 | |
1. Рамы тележки, кузова | ||||||
1.1. | Расстояние между осями стаканов под направляющие буксы в одной боковине рамы | ЧС7 | 680±0,3 | 680±0,3 | 680±0,3 | – |
1.2. | Смещение осей отверстий стаканов направляющих букс в боковине рамы | « | ±0,2 | ±0,2 | ±0,2 | – |
1.3. | Расстояние между осями отверстий стаканов направляющих букс правой и левой стороны | « | 2100±0,3 | 2100±0,3 | – | – |
1.4. | Продольное смещение осей буксовых направляющих правой и левой стороны оси относительно друг друга | « | ±0,3 | ±0,7 | – | – |
1.5. | Расстояние между осями стаканов направляющих цапф в перекрестном направлении | « | ![]() | ![]() | – | – |
1.6. | Разность диагоналей между осями стаканов направляющих цапф для одной кол. пары | « | 0,7 | 0,9 | 1,2 | – |
1.7. | Внутренний диаметр стаканов под направляющие буксы: | « | ||||
а) верхней части | 70+0,03 | 70+0,5 | – | – | ||
б) нижней части | 110+0,035 | 110+0,5 | – | – | ||
1.8. | Натяг запрессовки направляющей цапфы буксы в раме тележки | « | ||||
а) верхней части | 0,013–0,062 | 0,013–0,062 | 0,013–0,062 | – | ||
б) нижней части | 0,019–0,076 | 0,019–0,076 | 0,019–0,076 | – | ||
1.9. | Внутренний диаметр втулки в кронштейне рамы под валик для крепления подвески | « | 60+0,19 | 60,5 | 61,0 | Более 62 |
1.10 | Натяг запрессовки втулки валика подвески в кронштейн рамы | « | 0,013–0,062 | 0,013–0,062 | 0,013–0,062 | – |
1.11. | Диаметр стержня направляющей цапфы буксы | « | ![]() | 104–105*1 | 104–105*1 | – |
1.12. | Расстояние от передних упоров фрикционного аппарата в буферном брусе рамы кузова до передней плоскости бруса | « | 390±3 | 390±3 | ![]() ![]() | – |
1.13 | Расстояние между передними и задними упорами фрикционного аппарата в буферном брусе | « | 625–3 | 625–3 | ![]() ![]() | – |
2. Шкворневое соединение | ||||||
2.1. | Диаметр шкворня | « | ![]() | 138–140*2 | 138–140*2 | – |
2.2. | Шаровая втулка шкворня | « | 140+0,063 | 140+0,1 | 141*2 | Более 141,5 |
2.3. | Суммарный зазор между шкворнем и отверстием в шаровом подшипнике | « | 0,085–0,211 | 0,085–0,3 | 0,085–1,0 | Более 1,5 |
2.4. | Диаметр верхнего посадочного пояса шкворня | « | ![]() | 135–136*3 | 135–136*3 | – |
2.5. | Диаметр нижнего посадочного пояса шкворня | « | ![]() | 165–166*3 | 165–166*3 | – |
2.6. | Натяг запрессовки шкворня в гнездо рамы тележки по верхнему и нижнему поясу | « | 0,035–0,095 | 0,035–0,095 | 0,035–0,095 | – |
2.7 | Изгиб шкворня | « | 0 | 0 | 0 | – |
2.8. | Диаметр шаровой втулки (по шару) | « | ![]() | ![]() | 229–230*4 | Менее 228 |
2.9. | Диаметр вкладыша подшипника (по шару) | « | ![]() | 230,4*4 | 231*4 | Более 231*4 |
2.10 | Суммарный зазор между шаровой втулкой и его вкладышем | « | 0,37–0,585 | 0,37–0,6 | 0,37–1,0 | Более 1,5 |
2.11 | Зазор в посадке верхней половины вкладыша в нижнюю | « | 0–0,075 | 0–0,1 | 0–0,15 | – |
2.12 | Размер собранных вкладышей (по высоте) | « | 175–0,25 | 175–1 | 173–175 | Менее 172 |
2.13 | Размер гнезда в шкворневой балке рамы кузова (по продольной оси электровоза) | « | 280+0,32 | 278–280 | 276–280 | – |
2.14 | Суммарный зазор между поверхностью гнезда скольжения шкворневой балки и плитой скольжения шарового вкладыша | « | 0,2–1,12 | 0,2–1,21 | 0,2–1,4 | – |
2.15 | Допуск круглости отверстия в шаре под шкворень | « | 0,05 | 0,05 | 0,25 | Более 1 |
2.16 | Наибольший суммарный зазор между вкладышами (в сборе) и гнездом шкворневой балки тележки (по поперечной оси) | « | 120 | 120 | 120 | – |
2.17 | Толщина плиты скольжения | « | 8–0,2 | 7,7*1 | 7,5*1 | – |
2.18 | Внутренний диаметр втулки в кронштейне гнезда под валик поводка | « | 45+0,039 | 45,5 | 45,8 | 46 |
2.19 | Натяг втулки в гнезде кронштейна | « | 0,013–0,062 | 0,013–0,062 | 0,013–0,062 | – |
3. Колесная пара | ||||||
3.1. | Диаметр шейки оси под буксовые подшипники | « | ![]() | ![]() | ![]() | – |
3.2. | Допуск радиального биения шеек оси под буксовые подшипники | « | 0,018 | 0,02 | – | – |
3.3. | Допуск конусообразности шеек оси | « | 0,03 | 0,04 | 0,04 | – |
3.4. | Допуск круглости шеек оси | « | 0,015 | 0,03 | 0,035 | – |
3.5. | Диаметр предподступичной части оси | « | ![]() | ![]() | ![]() | – |
3.6. | Допуск круглости и конусообразности предподступичной части оси | « | 0,03 | 0,05 | 0,07 | – |
3.7. | Допуск круглости и конусообразности посадочного отверстия лабиринтного кольца | « | 0,03 | 0,05 | 0,07 | – |
3.8. | Натяг на посадку внутренних колец роликовых подшипников | « | 0,035–0,065 | 0,035–0,065*1 | 0,035–0,065*1 | – |
3.9 | Натяг посадки лабиринтного кольца | « | 0,084–0,159 | 0,05–0,16 | 0,04–0,16 | – |
3.10 | Перекос торцевой поверхности лабиринтного кольца относительно шейки | « | 0,03 | 0,05 | 0,05 | – |
3.11 | Толщина бандажей по кругу катания | « | 90 | 80–100 | 70–100 | Менее 45*2 |
3.12 | Разница диаметров бандажей по кругу катания | « | ||||
у комплекта колесных пар электровоза | 0–2 | 0–5 | 0–5 | Более 12 | ||
у одной колесной пары | 0–0,5 | 0–0,5 | 0–0,5 | Более 1*3 | ||
у одной тележки | 0–2 | 0–2 | 0–2 | Более 3 | ||
3.13 | Радиальное биение бандажа по кругу катания относительно осевых шеек | « | 0–0,4 | 0–0,5 | 0–0,5 | Более 2*3 |
3.14 | Разница в замерах по ширине одного бандажа | « | 0–3 | 0–3 | 0–3 | Более 6 |
3.15 | Расстояние между внутренними гранями бандажей у ненагруженной колесной пары: | « | 1440±1 | 1440±1 | 1440±1 | Более 1443 Менее 1437 |
3.17 | Расстояние от торца оси до торца ступицы центра кол. пары | « | 280±0.2 | 280±0.2 | – | – |
4. Буксовый узел | ||||||
4.1 | Диаметр внутренней цилиндрической части буксы под роликоподшипник | « | ![]() | ![]() | ![]() | – |
4.2 | Допуск круглости внутренней цилиндрической части корпуса буксы | « | ||||
при расположении большего диаметра по вертикали | 0,04 | 0,2 | 0,33 | – | ||
то же по горизонтали | 0,04 | 0,15 | 0,25 | – | ||
4.3 | Допуск конусности внутренней цилиндрической части корпуса буксы | « | 0,035 | 0,08 | 0,15 | – |
4.4. | Допуск перпендикулярности переднего и заднего торцов корпуса буксы к оси отверстия под подшипник | « | 0,05 | 0,07 | – | – |
4.5. | Расстояние между осями отверстий под амортизаторы | « | 680±0.3 | 680±0.3 | 680±0.3 | – |
4.6. | Диаметр отверстий в корпусе буксы под амортизаторы направляющих стаканов | « | 175+0.04 | 175+0.5 | 175+0.5 | – |
4.7 | Наружный диаметр втулки амортизатора | « | ![]() | *1 | *1 | – |
4.8. | Натяг запрессовки втулки амортизатора в буксу | « | 0,028–0,093 | 0,028–0,093 | 0,028–0,093 | – |
4.9 | Внутренний диаметр втулки амортизатора (сайлентблока) буксы | « | 120+0,04 | 120+0,1 | 120+0,1 | – |
4.10 | Наружный диаметр стакана | « | ![]() | *1 | *1 | – |
4.11 | Натяг запрессовки стакана во втулку амортизатора | « | 0,039–0,101 | 0,039–0,101 | 0,039–0,101 | – |
4.12 | Внутренний диаметр стакана направляющей оси | « | ![]() | 105,5*2 | 105,2*2 | Более 106 |
4.13 | Зазор между стаканом и направляющей цапфы буксы | « | 0,272–0,39 | 0,6 | 1,4 | – |
4.14 | Радиальный зазор роликовых подшипников (в свободном состоянии) | « | 0,15–0,215 | 0,14–0,3 | 0,14–0,4 | – |
4.15 | Посадочный радиальный зазор (измеряется по шейке оси в случаях, когда при разборке не снимаются внутренние кольца подшипников) | « | – | – | 0,08–0,37 | – |
4.16 | Разность посадочных радиальных зазоров парных подшипников | « | 0,03 | 0,03 | 0,03 | – |
4.17 | Зазор плавания сепаратора | « | ||||
при центровании по бортам | 0,5–1,1 | 0,5–1,3 | 0,5–1,8 | Более 2,2 | ||
при центровании по роликам | 1,2–2,5 | 0,8–2,5 | 0,5–2,5 | Более 2,5 | ||
4.18 | Осевой зазор (разбег) двух парных цилиндрических подшипников для одной буксы колесной пары с фирменными подшипниками с отечественными « | « | 10,4–12,6 11,38–12,97 | 10,4–12,8 11,38–13,17 | 10,4–13 11,38–13,17 | – |
4.19 | Зазор между торцовыми поверхностями внутренних колец подшипников и дистанционных колец, а также буртом внутреннего кольца заднего подшипника и лабиринтным кольцом на 1/3 окружности | « | 0,05 | 0,05 | 0,05 | – |
4.20 | Зазор между фланцем передней крышки и торцом корпуса буксы | « | 1–3 | 1–3 | Не менее 0,5 | – |
5. Рессорное подвешивание тележки и кузова | ||||||
5.1 | Зазор между верхней частью буксы и плоскостью упора на боковине рамы тележки | ЧС7 (82Е1,2,3) (82Е4,5) (82Е6,7,8) | ![]() | ![]() | ![]() | ![]() ![]() |
5.2 | Вертикальный зазор между рамой кузова и рамой тележки | ЧС7 | ![]() | ![]() | 40–55 | – |
5.3 | Горизонтальный зазор между рамой кузова и рамой тележки | « | 50±5 | 50±5 | 45–55 | – |
5.4 | Высота пружин (тележки) в свободном состоянии наружной внутренней | ЧС7 (82Е1–5) | 295±4 278±4 | 291–299 274–282 | 289–301 277–284 | – – |
Высота пружины (тележки) в свободном состоянии | ЧС7 (82Е6,7,8) | ![]() | 319–329 | 317–331 | – | |
5.5 | Высота пружин тележки: | ЧС7 (82Е1–5) | ||||
наружной под рабочей нагрузкой 27911Н | ||||||
для 1 группы | 216–220 | 216–220 | 216–220 | – | ||
для II группы | 220–224 | 220–224 | 220–224 | – | ||
внутренней под рабочей нагрузкой 16674Н | ||||||
для 1 группы | 207–210 | 207–210 | 207–210 | – | ||
для II группы | 210–213 | 210–213 | 210–213 | – | ||
5.6 | Высота пружин тележки под рабочей нагрузкой 45800Н для 1 группы | ЧС7 (82Е6,7,8) | 259–262 | 259–262 | 259–262 | – |
5.7 | Высота пружин (кузова) в свободном состоянии | ЧС7 (82Е1–8) |
![]() | 465–480 | 462–480 | – |
5.8 | Высота пружин (кузова) под рабочей нагрузкой: –50200Н для: 1 группы пружин II группы пружин | ЧС7 (82Е1–8) | 349–355 355–361 | 349–355 355–361 | 349–355 355–361 | – – |
5.9 | Внутренний диаметр втулки камня подвески | ЧС7 | 60+0,19 | 60+0,5 | 61 | 62 |
5.10 | Толщина камня подвески по впадине радиуса 32 мм | « | 55 | 54 | 52 | менее 51 |
5.11 | Высота шейки подвески | « | 80 | 79 | 77 | 76 |
5.12 | Диаметр валика подвески | « | ![]() | ![]() | 58 | 57 |
5.13 | Высота седла (износ по валику R25) | « | 35 | 35 | 33 | 32 |
5.14 | Высота нижней опоры (износ по валику R25) | « | 25 | 25 | 23,5 | 23 |
5.15 | Высота верхней опоры (износ по валику R25) | « | 25 | 25 | 23,5 | 23 |
5.16 | Диаметр валика амортизатора кузова | « | ![]() | 39,7 | 39,5 | 39,2 |
5.17 | Диаметр валика амортизатора кузова | « | ![]() | 34,7 | 34,5 | 34,2 |
5.18 | Диаметр валика буксового амортизатора | « | ![]() | 34,7 | 34,5 | 34,2 |
5.19 | Диаметр валика буксового амортизатора | « | ![]() | 29,8 | 29,7 | 29,6 |
5.20 | Диаметр валика поводка | « | ![]() | 44,8 | 44,2 | 43 |
5.21 | Суммарный зазор по валикам Æ30 Æ35 Æ40 Æ45 Æ60 | « | 0,025–0,083 0,03–0,115 0,03–0,115 0,08–0,231 0,1–0,48 | 0,025–0,1 0,03–0,2 0,03–0,2 0,08–0,3 0,1–0,6 | 0,025–0,5 0,03–0,5 0,03–0,5 0,08–0,8 0,1–0.8 | 1,0 1,5 1,5 1,5 2,0 |
6. Тяговый редуктор зубчатая передача | ||||||
6.1 | Толщина зуба венца зубчатого колеса, измеренная на расстоянии от вершины зуба: 7,82мм | « |
![]() | 13,77 | 12,27 | 11,8 |
6.2 | Наибольшее торцевое биение зубчатого колеса на кол.паре | « | 0,25 | 0,25 | 0,25 | – |
6.3. | Толщина зуба шестерни, измеренная от вершины зуба на расстоянии: 10,07 мм | « |
![]() | 15,5 | 14,0 | 13,5 |
6.4 | Торцевое биение шестерни | « | 0,1 | 0,1 | 0,15 | – |
6.5 | Наибольший износ зуба по толщине от полного профиля на обе стороны зубчатого колеса или шестерни | « | – | 1,5 | 3,0 | 3,5 |
6.6 | Зазор между ступицей зубчатого колеса и венцом зубчатого колеса | « | 0,16 | 0,25 | 0,3 | – |
6.7 | Натяг посадки призонных болтов крепления зубчатого колеса к ступице | « | 0,006–0,035 | 0,02–0,04 | – | – |
Опорно-осевой узел тягового редуктора | ||||||
6.8 | Диаметр ступицы зубчатого колеса под подшипник | « | ![]() | ![]() | – | – |
6.9 | Допуски на диаметр ступицы зубчатого колеса, не более круглость конусообразность биение | « | 0,02 0,03 0,03 | 0,03 0,04 0,05 | – – – | – – – |
6.10 | Натяг посадки внутреннего кольца роликоподшипника на шейку ступицы | « | 0,056–0,123 | 0,056–0,123 | 0,056–0,123 | – |
6.11 | Диаметр отверстия опоры (стакана) под наружное кольцо осевого подшипника | « | ![]() | ![]() | ![]() | – |
6.12 | Допуск круглости и конусообразности отверстия опоры под наружное кольцо осевого подшипника | « | 0,03 | 0,045 | 0,06 | – |
6.13 | Диаметр отверстия в полуфланцах корпуса под опору (стакан) осевого подшипника - со стороны ТЭД - со стороны колеса | « | 520+0,07 540+0,07 | 520+0,12 540+0,12 | 520+0,25 540+0,25 | |
6.14 | Наибольший суммарный зазор между посадочными поверхностями полуфланцев корпуса и опоры (стакана) осевых подшипников | « | 0,17 | 0,2 | 0,3 | – |
Опорно-осевые роликовые подшипники | ||||||
6.15 | Радиальный зазор (в свободном состоянии) | « | 0,195–0,28 | 0,19–0,45 | – | – |
6.16 | Зазор плавания сепараторов при центрировании по бортам наружных колец (в свободном состоянии) | « | 1–1,45 | 1–1,9 | 1–2,3 | – |
6.17 | Осевой разбег (в свободном состоянии) | « | 0,25–0,5 | 0,25–0,7 | 0,25–1 | – |
6.18 | Разность радиальных зазоров парных подшипников (в свободном состоянии) | « | Не более 0,05 | Не более 0,05 | Не более 0,05 | – |
6.19 | Радиальный зазор подшипников в собранном редукторе | « | 0,1–0,25 | 0,1–0,42 | 0,1–0,5 | – |
6.20 | Осевой разбег (зазор), контролируемый в собранном редукторе | « | 0,25–0,5 | 0,25–0,7 | 0,25–1 | – |
Опорный узел малой шестерни | ||||||
6.21 | Диаметр отверстия шестерни по посадке на вал поводка | ЧС7 (82Е4,5,6) (82Е7,8) | 165+0,025 199+0,029 | 165+0,025*ййй 199+0,029* | 165+0,025* 199+0,029* | – – |
6.22 | Диаметр шейки вала поводка под шестерню | ЧС7 (82Е4,5,6) (82Е7,8) | ![]() ![]() ![]() | ![]() ![]() | ![]() ![]() | – – |
6.23 | Натяг посадки шестерни на вал поводока | ЧС7 (82Е4,5,6) (82Е7,8) | 0,227-0,277 0,255–0,313 | 0,227-0,277 0,255–0,313 | 0,227-0,277 0,255–0,313 | – – |
6.24 | Диаметр ступицы шестерни под подшипник | ЧС7 (82Е1,2,3) | ![]() | ![]() | ![]() | – |
6.25 | Диаметр поводка шестерни под подшипник со стороны ТЭД со стороны колеса | ЧС7 (82Е4,5,6) (82Е7,8) ЧС7 (82Е4,5,6) (82Е7,8) |
![]() ![]() ![]() ![]() |
![]() ![]() ![]() ![]() |
![]() ![]() ![]() ![]() | – – – – |
6.26 | Допуск круглости и конусообразности шеек поводка (шестерни) под подшипники | ЧС7 | 0,015 | 0,02 | 0,025 | – |
6.27 | Натяг посадки подшипников на шейки поводка (шестерни) | « | 0,027–0,077 | 0,02–0,07 | 0,02–0,07 | – |
6.28 | Диаметр отверстия опоры (стакана) шестерни под наружное кольцо подшипника со стороны ТЭД | ЧС7 (82Е1,2,3) (82Е4,5,6) (82Е7,8) |
250+0,046
![]() ![]() |
250+0,08
![]() ![]() |
250+0,15
![]() ![]() | – – – |
со стороны колеса | ЧС7 (82Е1,2,3) (82Е4,5,6) (82Е7,8) |
250+0,052
![]() ![]() |
250+0,08
![]() ![]() |
250+0,15
![]() ![]() | – – – | |
6.29 | Допуск круглости на диаметр отверстия опоры (стакана) | ЧС7 | 0,023 | 0,03 | 0,035 | – |
6.30. | Посадка наружного кольца роликоподшипника в опоре (стакане) | « | Зазор 0,088 Натяг 0,02 | Зазор 0,105 Натяг 0,02 | Зазор 0,15 Натяг 0,02 | – – |
6.31 | Диаметр отверстия в боковине редуктора под опору (стакан) подшипника шестерни со стороны ТЭД со стороны колеса | ЧС7 ЧС7 (82Е1,2,3) (82Е4,5,6) (82Е7,8) | 568+0,07 310+0,052 350+0,057 450+0,063 | 568+0,12 310+0,1 350+0,1 450+0,1 | 568+0,25 310+0,15 350+0,15 450+0,15 | – – – – |
6.32 | Допуск круглости отверстия в боковине редуктора под опоры (стакан) | ЧС7 | 0,035 | 0,1 | 0,2 | – |
6.33 | Допуск перпендикулярности привалочных поверхностей к общей оси расточки | « | 0,03 | 0,05 | 0,06 | – |
6.34 | Диаметр посадочного места опоры (стакана) подшипника шестерен в корпус редуктора со стороны ТЭД | ЧС7 (82Е1-6) (82Е7-8) |
![]() |
![]() |
![]() | |
со стороны колеса | ЧС7 (82Е1,2,3) (82Е4,5,6) (82Е7,8) |
310–0,1
![]() ![]() | 310–0,2* 350–0,25* 450–0,35* | 310–0,3* 350–0,3* 450–0,4* | ||
6.35 | Наибольший суммарный зазор между посадочными поверхностями расточек боковины редуктора и опоры (стакана) подшипника шестерни со стороны ТЭД со стороны колеса | ЧС7 (82Е1–6) (82Е7,8) ЧС7 (82Е1,2,3) (82Е4,5,6) (82Е7,8) | 0,1–0,27 0–0,23 0–0,152 0,1–0,257 0,1–0,363 | 0,3 0,3 0,2 0,3 0,4 | 0,4 0,4 0,3 0,4 0,5 | |
Роликовые подшипники шестерни | ||||||
6.36 | Радиальный зазор (в свободном состоянии) со стороны ТЭД со стороны колеса со стороны ТЭД со стороны колеса со стороны ТЭД со стороны колеса | ЧС7 (82Е1,2,3) (82Е4,5,6) (82Е7,8) | 0,105–0,16 0,18–0,24 0,125–0,165 0,115–0,15 0,14–0,18 0,14–0,18 | 0,1–0,25 0,14–0,4 0,11–0,25 0,11–0,25 0,135–0,3 0,135–0,3 | 0,1–0,4 0,24–0,45 0,11–0,35 0,11–0,35 0,135–0,4 0,135–0,4 | |
6.37 | Зазор плавания сепараторов (в свободном состоянии) при центрировании по роликам при центрировании по бортам наружных колец | ЧС7 | 1,0–2,5 0,5–1,1 | Не менее 0,7 0,5–1,3 | Не менее 0,5 0,5–1,8 | – Более 0,5 |
6.38 | Разность радиальных зазоров парных подшипников (в свободном состоянии) не более | « | 0,1 | 0,1 | 0,12 | |
6.39 | Радиальный зазор подшипников в собранном редукторе со стороны ТЭД со стороны колеса со стороны ТЭД со стороны колеса со стороны ТЭД со стороны колеса | ЧС7 (82Е1,2,3) (82Е4,5,6) (82Е7,8) | 0,07–0,13 0,09–0,16 0,075–0,15 0,07–0,135 0,09–0,16 0,09–0,16 | 0,07–0,23 0,09–0,25 0,07–0,25 0,07–0,25 0,09–0,25 0,09–0,25 | 0,07–0,38 0,09–0,38 0,07–0,38 0,07–0,38 0,09–0,38 0,09–0,38 | |
6.40 | Осевые разбеги (зазоры) по цилиндрическим подшипникам шестерни, контролируемые в собранном состоянии | ЧС7 (82Е4,5,6) | 0,4–0,6 | 0,4–0,8 | 0,4–1,2 | |
7. Подвеска редуктора | ||||||
7.1 | Диаметр отверстия втулки подвески редуктора | ЧС7 | 80+0,054 | 80+0,1 | 80+0,5 | 82 |
7.2 | Суммарный зазор между валиком и втулкой сайлентблока | « | 0,1–0,228 | 0,1–0,35 | 0,1–0,5 | 1,5 |
7.3 | Диаметр валика подвеса редуктора | « | ![]() | ![]() | ![]() | 78* |
7.4 | Диаметр отверстия в подвеске редуктора под сайлентблок | « | 160+0,063 | 160+0,08 | 160+0,09 | – |
7.5 | Натяг посадки сайлентблока в подвеску | « | 0,026–0,089 | 0,026–0,089 | 0,026–0,089 | – |
8. Тяговый привод | ||||||
8.1 | Диаметр цапфы карданной крестовины | ЧС7 (82Е1–6) ЧС7 (82Е7,8) |
![]() ![]() |
![]() ![]() |
![]() ![]() | – – |
8.2 | Диаметр гнезда в корпусе подшипника под иглы | ЧС7 (82Е1–6) | ![]() | 61,6+0,08 | 61,6+0,15 | – |
8.3 | Диаметр гнезда в буксе под установку обоймы с игольчатым подшипником | ЧС7 (82Е7,8) | 65+0,019 | 65+0,05 | 65+0,1 | – |
8.4 | Разница в диаметре игл при подборке их в подшипник | ЧС7 | 0,002 | 0,004 | 0,004 | – |
8.5 | Суммарный окружной зазор между иглами в корпусе подшипника | ЧС7 (82Е1–6) | 0,53 | 0,6 | 0,8 | – |
8.6 | Радиальный зазор между цапфой и иглами | « | – | – | 0,01–0,05 | – |
8.7 | Глубина вмятин на рабочих поверхностях цапф крестовин и корпусов подшипников | ЧС7 | – | 0,08 | 0,08 | Более 0,1 |
8.8 | Толщина зуба торцевых шлицев на высоте 3,6 мм от головки зуба | ЧС7 (82Е1,2,3) | 10+0,02 | 10±0,02 | ![]() | – |
8.9 | Высота зуба торцевого шлица | « | 8,4–0,1 | ![]() | ![]() | – |
8.10 | Зазор между вершиной зуба, поводка и впадиной зуба шестерни | « | 1,2 | 1,0 | 0,6 | – |
9. Токоотводящее устройство | ||||||
9.1 | Высота токосъемного диска | ЧС7 (82Е1–6) | 32 | 31,5 | 30,5 | – |
9.2 | Высота щетки | « | 50±0,8 | 45 | 28 | 20 |
9.3 | Диаметр токосъемного цилиндра | ЧС7 (82Е6-8) | ![]() | 104 | 103 | – |
10. Тормозная рычажная передача | ||||||
10.1 | Допускаемые отклонения диаметров валиков и отверстий втулок рычажной передачи от номинального значения, мм для отверстий диаметром до 30 от 30 до 50 свыше 50 | ЧС7 | +0,14 +0,17 +0,2 | +0,25 +0,4 +0,5 | +0,6 +0,75 +1 | Более 1,0 Более 1,0 Более 1,5 |
для валиков диаметром до 30 от 30 до 50 свыше 50 | –0,42 –0,5 –0,6 | –0,8 –1 –1,2 | –1,0 –1,5 –1,8 | Более –1,5 Более –2,0 Более –2,5 | ||
10.2 | Суммарный зазор по диаметру между валиком и втулкой (или отверстием) в шарнирных соединениях для валиков диаметром, мм: от 18 до 30 от 30 до 50 от 50 до 65 | « | 0,3–0,56 0,32–0,64 0,34–0,72 | 0,3–0,7 0,32–1,1 0,34–1,2 | 0,3–1,2 0,32–1,2 0,34–1,5 | Более 2,5 Более 2,5 Более 3,5 |
10.3 | Натяг втулок в деталях рычажной передачи | « | 0,01–0,05 | 0,01–0,05 | 0,01–0,05 | – |
10.4 | Увеличение диаметра отверстия под втулку от номинального размера в деталях рычажной передачи | « | – | 1 | 2 | 3 |
10.5 | Суммарный зазор вдоль оси валика в проушинах: в сочленении кронштейнов с | « | 2 | 2–2,2 | 2–3 | Более 4 |
подвесками в сочленении тяг между собой и с рычагами в сочленении рычагов и головками тяг авторегуляторов в сочленении рычагов с корпусом авторегуляторов | 2 2,6 2 | 2–2,2 2–3 2–2,2 | 2–3 2–4 2–3 | Более 4 Более 5 Более 4 | ||
10.6 | Отклонения по толщине головок тяг | « | –1 | –1...–2 | –1...–2 | – |
10.7 | Отклонения по толщине щек тяг | « | ±0,5 | ![]() | ![]() | – |
10.8 | Отклонения в расстояниях между центрами соседних отверстий в рычагах, тягах и балансирах при их длине, мм: до 500 свыше 500 до 1000 свыше 1000 до 2000 свыше 2000 до 4000 | « | – – – – | ±1 ±1,5 ±2 ±3 | ±1 ±1,5 ±2 ±3 | – – – – |
10.9 | Отклонения по толщине ушков, кронштейнов подвески тормозных башмаков | « | ±0,5 | ![]() | ![]() | – |
10.10 | Отклонение по ширине зева проушины кронштейна подвески башмаков | « | +1,5 | +2,5 | +3,5 | – |
10.11 | Диаметр отверстия во втулке башмака под цапфу тормозного вала | « | 60+0,19 | 60+0,25 | 60+0,25 | – |
10.12 | Износ шейки (цапфы) тормозной поперечины по диаметру | « | – | 0–0,7 | 0–1 | 1,2 |
10.13 | Износ пружины тормозного цилиндра по диаметру витка | « | – | 1,5 | 2 | 3 |
10.14 | Выход штока тормозного цилиндра | « | 75–100 | 75–100 | 75–100 | Менее 75 Более 100 |
10.15 | Наибольший износ штока тормозного цилиндра по диаметру | « | – | 2 | 2 | 4 |
10.16 | Толщина тормозной колодки | « | 55 | 55 | 55 | Менее 15 |
11. Ударно-сцепные устройства | ||||||
11.1 | Высота горизонтальной оси автосцепки от головок рельсов | « | ![]() | 1000–1080 | 990–1080 | Менее 980 Более 1080 |
11.2 | Вертикальный зазор между хвостовиком автосцепки и ударной розеткой | « | 30±5 | 25–35 | 25–35 | Менее 25 Более 40 |
11.3 | Расстояние от упора головы автосцепки до ударной розетки | « | 75±5 | 75±5 | 80±10 | Менее 70 Более 90 |
11.4 | Высота нижней кромки путеочистителя от головки рельсов | « | 150±10 | 140–160 | 120–160 | Менее 100 Более 165 |
1.3. Нормы допусков и износов механического оборудования электровозов ЧС6, ЧС200 | ||||||
Размер, мм
| ||||||
№ п/п |
Наименование деталей и размеров |
Серия электро-воза |
Чертеж-ный | допускаемый при выпуске из ремонта |
Браковоч-ный в эксплуа-тации | |
капиталь-ного | текущего ТР-3 | |||||
1 | 2 | 3 | 4 | 5 | 6 | 7 |
1. Рамы тележки, кузова | ||||||
1.1 | Расстояние между направляющими в одной боковине рамы | ЧС6, ЧС200 | 680±0,3 | 680±0,3 | – | – |
1.2 | Смещение осей отверстия гнезд под направляющие буксы в одной боковине рамы | « | ±0.2 | ±0,2 | – | – |
1.3 | Расстояние между осями направляющих правой и левой сторон одной оси | « | 2100±0,3 | 2100±0,3 | – | – |
1.4. | Расстояние между осями стаканов направляющих цапф в перекрестном направлении | « | ![]() | ![]() | – | – |
1.5 | Разность диагоналей между направляющими букс одной колесной пары | « | 0–0,7 | 0–0,9 | 0–1,2 | – |
1.6 | Продольное смещение осей буксовых направляющих правой и левой сторон относительно друг друга | « | не более 0,3 | не более 0,7 | – | – |
1.7 | Диаметр стержня направляющей буксы | « | ![]() | 105–104*1 | 105–104*1 | – |
2. Шкворневое соединение тележки | ||||||
2.1 | Натяг запрессовки шкворня в гнездо рамы тележки | « | 0,03–0,105 | 0,03–0,105 | 0,03–0,105 | – |
2.2 | Общий зазор между шкворнем и отверстием в шаровом подшипнике | « | 0,085–0,211 | 0,085–0,3 | 0,085–0,6 | Более 1,5 |
2.3 | Диаметр шарового подшипника (по шару) | « | ![]() | ![]() | 229–230*2 | – |
2.4. | Местный износ отверстия шарового подшипника (по диаметру) | « | 0 | 0–0,1 | 0–0,3 | – |
2.5 | Суммарный зазор между шаровым подшипником и его вкладышами | « | 0,47–0,485 | 0,47–0,65 | 0,47–0,9 | Более 1,6 |
2.6 | Зазор в посадке верхнего вкладыша в нижний | « | 0–0,075 | 0–0,1 | 0–0,15 | |
2.7 | Размер собранных вкладышей по высоте | « | 175–0,25 | 175–1 | 173–175 | Менее 172 |
2.8 | Суммарный зазор между поверхностями скольжения гнезда шкворневой балки и наличниками вкладышей в сборе | « | 0,6–1,12 | 0,6–1,2 | 0,6–1,2 | – |
2.9 | Некруглость отверстия в шаре под шкворень | « | 0,05 | 0,05 | 0,25 | более 1 |
2.10 | Суммарный зазор между вкладышами (в сборе) и гнездом шкворневой балки вдоль поперечной оси тележки | « | 120 | 120 | 120 | |
2.11 | Диаметр шкворня | « | ![]() | 138–140 | 138–140 | |
3. Колесные пары | ||||||
3.1 | Диаметр шейки оси под буксовые подшипники качения | « | ![]() | ![]() | ![]() | – |
3.2 | Диаметр предподступичной части оси | « | ![]() | ![]() | ![]() | – |
3.3 | Уменьшение диаметра средней части оси против чертежного размера | « | – | 3,0 | 3,0 | Более 3,0 |
3.4 | Некруглость шейки оси под буксовые подшипники | « | 0,015 | 0,03 | 0,03 | |
3.5 | Конусообразность шейки оси под буксовые подшипники | « | 0,03 | 0,04 | 0,04 | |
3.6 | Радиальное биение поверхности буксовых предподступичных шеек относительно оси при проверке в центрах | « | 0,03 | 0,03 | 0,03 | |
3.7 | Толщина бандажей по кругу катания | ЧС6 | 90 | 80–100 | 70–100 | Не менее 50*2 |
3.8 | Диаметр цельнокатаных колес | ЧС200 | 1250+1 | 1250+2 | 1250+2 | Менее 1160 |
3.9 | Разница диаметров бандажей (ободов) по кругу катания: у одной колесной пары в одной тележке | ЧС6, ЧС200 | 0–0,5 – | 0–0,5 0–2,0 | 0–0,5 0–3,0 | Более 1,0 Более 3,0 |
3.10 | Разница диаметров бандажей по кругу катания у комплекта колесных пар электровоза | « | 0–2 | 0–5 | 0–8 | Более 12 |
3.11 | Радиальное биение бандажей по кругу катания относительно осевых шеек | « | 0–0,4 | 0–0,5 | 0–0,5 | Более 2 |
3.12 | Толщина гребней колес обточки | « | – | 33-0,5 | 28–33-0,5 | – |
3.13 | Глубина местных выбоин (ползунов) на поверхности катания | « | 0 | 0 | 0 | Более 0,7 |
3.14 | Разница в замерах по ширине одного бандажа | « | 0–3 | 0–3 | 0–3 | Более 3 |
3.15 | Наименьшая толщина бурта бандажа под бандажное кольцо | ЧС6 | 12 | 5 | 5 | Менее 5 |
3.16 | Расстояние между внутренними гранями бандажей у неподкаченной колесной пары а)при освидетельствовании б) при полном освидетельствовании новых бандажей и цельнокатаных колес в) при обточке старых колес | ЧС6, ЧС200 | 1440±1 1440±1 1440±1 | 1440±1 1440±1 1440±1 | 1440±1 1440±1 1440±1 | Менее 1437 Более 1443 « « |
3.17 | Отклонение диаметра посадочной поверхности обода колесного центра от чертежного размера | ЧС6 | –0,3 | +3...–6 | – | – |
3.18 | Отклонение ширины обода колесного центра против чертежного размера | « | –0,3 | +2...–5 | – | – |
3.19 | Расстояние от торца оси до торца ступицы центра колесной пары | ЧС6, ЧС200 | 280±0,2 | 280±0,2 | – | |
4. Зубчатые передачи | ||||||
4.1 | Наибольший износ зуба по толщине от полного профиля на обе стороны зубчатого колеса или шестерни | « | – | 1,5 | 3,0 | Более 3,5 |
4.2 | Толщина зубьев венца зубчатого колеса, измеренная на расстоянии 9,58 мм от вершины головки зуба | ЧС6 |
![]() | 14,95 | 13,5 | – |
4.3 | То же на расстоянии 10,08 мм | ЧС200 | ![]() | 15,32 | 13,8 | |
4.4 | Длина общей нормали на 5 зубьях у импортных шестерен | ЧС6 ЧС200 | ![]() ![]() | – | ||
4.5 | Толщина зуба шестерни, измеренная на расстоянии: 14,74 мм 14,20 мм | ЧС6 ЧС200 |
![]() ![]() | 18,72 18,33 | 17,2 16,9 | |
4.6 | Зазор между ступицей зубчатого колеса и венцом зубчатого колеса | ЧС6, ЧС200 | 0,16 | 0,25 | – | |
4.7 | Диаметр призонных болтов крепления зубчатых колес | « | 25 | 25–29 | – | |
4.8 | Натяг посадки призонных болтов | « | 0,006–0,035 | 0,01–0,04 | – | |
4.9 | Радиальное биение окружности выступов шестерни | « | 0–0,08 | 0–0,1 | 0–0,12 | – |
4.10 | Торцевое биение зубчатого венца | « | 0–0,25 | 0–0,25 | 0–0,25 | – |
4.11 | Радиальное биение окружности выступов зубчатого венца | « | 0–0,115 | 0–0,25 | 0–0,3 | – |
5. Опорно-осевой узел тягового редуктора и подшипники шестерни | ||||||
5.1 | Диаметр ступицы шестерни под подшипник | « | ![]() | ![]() | ![]() | |
5.2 | Некруглость и конусообразность шеек ступицы шестерни | « | 0,015 | 0,020 | 0,025 | |
5.3 | Диаметр отверстия опоры под наружное кольцо подшипника | « | 250+0,046 | 250+0,08 | 250+0,15 | |
5.4 | Некруглость не более | « | 0,023 | 0,03 | 0,035 | |
5.5 | Диаметр удлиненной части ступицы зубчатого колеса | « | ![]() | ![]() | – | – |
5.6 | Некруглость посадочного места шейки под внутреннее кольцо роликоподшипника, не более | « | 0,02 | 0,03 | – | – |
5.7 | Конусообразность посадочного места шейки под внутреннее кольцо роликоподшипника, не более | « | 0,03 | 0,04 | – | – |
5.8 | Диаметр посадочного места опоры под наружное кольцо подшипника | « | ![]() | ![]() | ![]() | – |
5.9 | Некруглость и конусообразность посадочного места под наружное кольцо подшипника | « | 0,03 | 0,045 | 0,06 | – |
5.10 | Натяг посадки внутреннего кольца роликоподшипника на шейку ступицы зубчатого колеса | « | 0,056–0,123 | 0,056–0,123 | – | – |
5.11 | Радиальный зазор опорных подшипников в свободном состоянии | « | 0,195–0,28 | 0,19–0,45 | – | – |
5.12 | Разность радиальных зазоров парных роликоподшипников, не более | « | 0,05 | 0,05 | – | – |
5.13 | Радиальные зазоры опорных подшипников в собранном редукторе | « | 0,1–0,25 | 0,1–0,42 | 0,1–0,5 | |
5.14 | Осевой разбег по цилиндрическим подшипникам опоры | « | 0,25–0,5 | 0,25–0,5 | 0,25–0,1 | |
5.15 | Посадка наружного кольца роликоподшипника в корпусе | « | от зазора 0,088 до натяга 0,02 | от зазора 0,105 до натяга 0,02 | от зазора 0,15 до натяга 0,02 | |
6. Корпус редуктора | ||||||
6.1 | Диаметр отверстия в редукторе под стакан осевых роликоподшипников | « | 540+0,07 520+0,07 | 540+0,12 520+0,12 | 540+0,25 520+0,25 | |
6.2 | Наибольший суммарный зазор между посадочными поверхностями корпуса редуктора и стаканом осевых роликоподшипников | « | 0,1 | 0,2 | 0,3 | – |
6.3 | Диаметр отверстия в боковине редуктора под корпус подшипника шестерни со стороны тягового двигателя | « | 555+0,063 | 555+0,12 | 555+0,25 | |
6.4 | Некруглость отверстия | « | 0,035 | 0,1 | 0,2 | – |
6.5 | Наибольший суммарный зазор между посадочной частью корпуса роликоподшипника шестерни и боковиной со стороны тягового двигателя | « | 0,26 | 0,37 | 0,55 | |
6.6 | Диаметр посадочного места корпуса подшипников со стороны тягового двигателя | « | ![]() | ![]() | ![]() | – |
6.7 | Некруглость посадочного места корпуса подшипника | « | 0,1 | 0,25 | 0,35 | – |
6.8 | Диаметр отверстия в боковине корпуса под стакан роликоподшипника шестерни со стороны колеса | « | 310+0,052 | 310+0,1 | 310+0,15 | |
6.9 | Овальность отверстия | « | 0,035 | 0,1 | 0,2 | – |
6.10 | Наружный диаметр стакана подшипника шестерни со стороны колеса | « | 310–0,1 | 310–0,15 | 310–0,2 | |
6.11 | Овальность посадочного места | « | 0,1 | 0,25 | 0,35 | |
6.12 | Радиальный зазор подшипников шестерни в свободном состоянии: NU 2228 МА/СЗ, 80-32528М 22228 А/СЗ 22228 М/С4, 40-3528А | « | 0,105–0,16 0,145–0,19 0,18–0,24 | 0,1–0,25 0,14–0,4 0,14–0,4 | 0,1–0,4 0,14–0,45 0,14–0,45 | – |
6.13 | Разность радиальных зазоров парных подшипников шестерни, не более | « | 0,1 | 0,1 | 0,12 | – |
6.14 | Натяг посадки подшипников на цапфы шестерни | « | 0,027–0,077 | 0,02–0,07 | 0,02–0,07 | – |
6.15 | Радиальные зазоры подшипников в собранном редукторе: NU 2228 МА/СЗ, 80-32528М 22228 М/СЗ 22228 М/С4, 40-3528А | « | 0,07–0,13 0,09–0,16 0,13–0,21 | 0,07–0,23 0,09–0,25 0,12–0,3 | 0,07–0,38 0,09–0,38 0,12–0,4 | – |
6.16 | Центровка валов редуктора и тягового двигателя затяжка верхней пары амортизаторов « нижней « | « | – – | – – | 98±1 93±1 | – – |
7. Тяговый привод | ||||||
7.1 | Диаметр цапфы карданной крестовины | « | ![]() | ![]() | ![]() | |
7.2 | Диаметр отверстия корпуса игольчатого подшипника | « | ![]() | ![]() | ![]() | |
7.3 | Разница в диаметре игл при подборе в подшипник | « | – | 0,004 | 0,004 | – |
7.4 | Суммарный окружной зазор между иглами в корпусе подшипника | « | 0,53 | 0,6 | 0,8 | Более 1 |
7.5 | Толщина зуба торцевого шлица на высоте 3,6 мм от головки зуба | « | 10+0,02 | ![]() | ![]() | – |
7.6 | Высота зуба шлица | « | 8,4–0,1 | 8,4–0,2 | 8,4–0,6 | – |
7.7 | Отклонение поводка по вертикали по обеим сторонам после установки его на шестерню или на конец карданного вала, не более | « | 0,3 | 0,3 | 0,3 | |
7.8 | Зазор между вершиной зуба поводка и впадиной зуба шестерни, не менее | « | 1,2 | 1,0 | 0,6 | – |
8. Буксовый узел | ||||||
8.1 | Диаметр отверстия корпуса буксы под роликоподшипники | « | ![]() | ![]() | ![]() | |
8.2 | Конусообразность отверстия | « | 0,035 | 0,08 | 0,15 | |
8.3 | Диаметр отверстий в корпусе буксы под сайленблок | « | 175+0,04 | 175+0,5 | – | |
8.4 | Некруглость отверстия при расположении большой оси (большого диаметра): а) по вертикали б) по горизонтали | « | 0,04 0,04 | 0,2 0,15 | 0,33 0,25 | – – |
8.5 | Натяг посадки заднего лабиринтного кольца на предподступичную шейку оси | « | 0,084–0,159 | 0,05–0,16 | 0,04–0,16 | – |
8.6 | Внутренний диаметр втулки сайлентблока буксы | « | 120+0,04 | 120+0,1 | – | – |
8.7 | Натяг запрессовки втулки амортизатора в буксу | « | 0,018–0,085 | 0,018–0,085 | 0,018–0,085 | – |
8.8 | Внутренний диаметр стакана направляющей буксы | « | ![]() | 105,5* | 105,7* | – |
8.9 | Радиальный зазор роликовых подшипников (в свободном состоянии) | « | 0,15–0,215 | 0,14–0,3 | 0,14–0,4 | – |
8.10 | Разность радиальных зазоров парных подшипников (в свободном состоянии) | « | 0,03 | 0,03 | 0,03 | – |
8.11 | Зазор между стаканом и направляющей буксы | « | 0,39 | 0,6 | 1,4 | – |
8.12 | Зазор плавания сепаратора при центрировании по наружному кольцу при центрировании по телам качения | « | 0,5–1,1 1,2–2,5 | 0,5–1,3 0,8–2,5 | 0,5–1,8 0,5–2,5 | более 2,2 более 2,5 |
8.13 | Натяг внутренних колец подшипника | « | 0,035–0,065* | 0,035–0,065* | 0,035–0,065* | – |
8.14 | Перекос торцевой поверхности лабиринтного кольца относительно шейки, не более | « | 0,03 | 0,05 | 0,05 | – |
8.15 | Зазор между торцевыми поверхностями внутренних колец подшипников и дистанционных колец, а также бортом внутреннего кольца заднего подшипника и лабиринтным кольцом на 1,3 окружности, не более | « | 0,05 | 0,05 | 0,05 | – |
8.16 | Зазор между фланцем передней крышки и торцом корпуса буксы | « | 1–3 | 1–3 | не менее 0,5 | |
8.17 | Разбег собранной буксы на оси колесной пары: – с импортными подшипниками; – с отечественными подшипниками | « | 10,4–12,6 11,38–12,97 | 10,4–12,8 11,38–13,17 | 10,4–13,0 11,38–13,37 | |
9. Рессорное подвешивание | ||||||
9.1 | Высота пружин рессорного подвешивания кузова | « | 466±6 | 460–472 | 458–474 | – |
9.2 | Высота пружин буксового подвешивания: а) наружной б) внутренней | « | 295±4 278±4 | 291–299 274–282 | 289–301 272–284 | – – |
9.3 | Износ рессорной подвески по толщине | « | – | 0–1 | 0–2 | Более 3 |
9.4 | Диаметр валиков рессорного подвешивания | « | ![]() | ![]() | 58–60 | – |
9.5 | Диаметр валиков поводков вторичного подвешивания | « | ![]() | ![]() | ![]() | 43 |
9.6 | Диаметр валиков гидроамортизаторов | ЧС6 ЧС200 | ![]() ![]() | ![]() ![]() | 39,5–40 39,5–40 | – – |
9.7 | Зазор между валиком и втулкой рессорного подвешивания, име-ющих номинальный диаметр, мм: 32 35 40 45 60 | ЧС6, ЧС200 | 0,08–0,181 0,025–0,115 0,03–0,181 0,09–0,181 0,1–0,48 | 0,08–0,2 0,025–0,2 0,03–0,2 0,09–0,2 0,1–0,6 | 0,08–0,5 0,025–0,5 0,03–0,5 0,09–0,8 0,1–0,8 | 2 2 2 2 2,5 |
10. Тормозная рычажная передача | ||||||
10.1 | Суммарные зазоры по диаметру между валиком и втулкой (или отверстиями) в шарнирных соединениях для валиков диаметров, мм 29,5 30 39,5 40 44,5 45 49,5 50 59,5 | « | 0,62–0,94 0,3–0,56 0,58–0,9 0,31–0,63 0,63–0,95 0,31–0,63 0,63–0,95 0,31–0,63 0,84–1,22 | 0,62–1,1 0,3–0,7 0,58–1,1 0,31–0,8 0,63–1,1 0,31–0,8 0,63–1,1 0,31–0,8 0,84–1,25 | 0,62–1,5 0,3–1,2 0,58–1,5 0,31–1,2 0,63–1,5 0,31–1,2 0,63–1,5 0,31–1,2 0,84–1,5 | |
10.2 | Наибольшие допускаемые отклонения от номинального размера диаметров валиков и отверстий деталей рычажной передачи: а) для отверстий диаметром,мм до 30 вкл. свыше 30 до 50 вкл. « 50 « 70 « б) для валиков диаметром до 30 вкл. свыше 30 « 50 « « 50 « 70 « | « | +0,14 +0,17 +0,2 –0,42 –0,5 –0,6 | +0,25 +0,4 +0,5 –0,7 –0,8 –1,25 | +0,6 +0,75 +1,0 –1,2 –1,2 –1,5 | Более +1,5 Более +1,5 Более +2 Более –2 Более –2,5 Более –3 |
10.3 | Увеличение диаметра отверстия под втулку от номинального размера в деталях рычажной передачи, не более | « | – | 1 | 2 | Более 2 |
10.4 | Отклонения в расстояниях между центрами отверстий в тягах, рычагах и траверсах длиной, мм до 500 вкл. свыше 500 до 1000 вкл. « 1000 « 2000 « « 2000 « 4000 « | « | – – – – | ±1 ±1,5 ±2 ±3 | ±1 ±1,5 ±2 ±3 | – – – – |
10.5 | Отклонение по толщине головок тяг | « | –1 | –1 ... –2 | –1 ... –2 | – |
10.6 | Отклонение по толщине щек тяг | « | ±0,5 | +0,5 ... –1 | +0,5 ... –1,5 | – |
10.7 | Отклонение по толщине ушек кронштейнов подвески тормозных башмаков | « | ±0,5 | +0,5 ... –1 | +0,5 ... –2 | – |
10.8 | Отклонение по ширине зева проушины кронштейна подвески башмаков | « | 1,5 | 1,5 ... 2,5 | 1,5 ... 3,5 | |
10.9 | Диаметр отверстия во втулке башмака под цапфу с втулкой тормозного валика | « | 60+0,19 | 60+0,25 | 60+0,25 | |
10.10 | Износ цапфы тормозной поперечины по диаметру | « | – | 0–0,7 | 0–1,0 | Более 1,2 |
10.11 | Износ пружины тормозного цилиндра по диаметру витка | « | – | 1,5 | 2 | 3 |
10.12 | Выход штоков тормозных цилиндров | « | 75–100 | 75–100 | 75–100 | Менее 75 Более 125 |
10.13 | Износ штока тормозного цилиндра по диаметру | « | – | 2 | 2 | Более 4 |
10.14 | Толщина тормозной колодки | « | 66 | 66 | 66 | Менее 15,0 |
10.15 | Суммарный зазор вдоль оси валика в проушинах а) в сочленении траверс с рычагами б) в сочленении рычагов с головками тяг авторегуляторов в) в сочленении рычагов с корпусом авторегуляторов | « | 2 2–2,6 2 | 2–2,2 2–3 2–2,2 | 2–3 2–4 2–3 | Более 4 Более 5 Более 4 |
11. Ударно-сцепные устройства и путеочистители | ||||||
11.1 | Высота горизонтальной оси автосцепки от головки рельса | « | ![]() | 1000–1080 | 990–1080 | Менее 980 Более 1080 |
11.2 | Вертикальный зазор между хвостовиком автосцепки и ударной розеткой | « | 30±5 | 25–35 | 25–35 | Менее 25 Более 40 |
11.3 | Расстояние от упора головы автосцепки до ударной розетки | « | 75±5 | 75±5 | 80±10 | Менее 70 Более 90 |
11.4 | Высота нижней кромки путеочистителя от головки рельса | « | 150±10 | 140–160 | 120–160 | Менее 100 Более 165 |
Приложение 2.
Нормы допусков и износов электроаппаратуры электровозов ЧС2, ЧС2т, ЧС2к, ЧС6, ЧС7 и ЧС200
| ||||||
Наименование деталей и размеров | Размер, мм | |||||
№ | Тип | чертежный | допускается при выпуске из ремонта | Браковоч-ный в эксплуата-ции | ||
п/п | Капиталь-ного | Текуще-го ТР-3 | ||||
1 | 2 | 3 | 4 | 5 | 6 | 7 |
1.Общая часть | ||||||
1.1. | Толщина блокировочных сегментов в цепях управления | Все | 4 5 6 | 4,5–3 5,5–4 6,5–5 | 4,5–2,5 5,5–3 6,5–3,5 | Менее 2 « 2,5 « 3 |
1.2. | Наименьшая толщина рабочей части меди блокировочного пальца | « | – | – | 2,5 | Менее 2 |
1.3. | Допустимые отклонения от номинальных размеров валиков и осей при диаметре, мм: 5 - 10 10 - 18 18 - 30 30 - 50 | « | 0,015–0,055 0,02–0,07 0,025–0,085 0,032–0,1 | 0,015–0,15 0,02–0,18 0,025–0,21 0,032–0,25 | 0,015–0,3 0,02–0,36 0,025–0,42 0,032–0,5 | Более 0,5 « 1,1 « 1,3 « 1,6 |
1.4. | Допустимые отклонения от номинальных размеров отверстий под валики и оси при диаметре,мм 5 - 10 10 - 18 18 - 30 30 - 50 | « | 0–0,03 0–0,035 0–0,045 0–0,05 | 0–0,1 0–0,12 0–0,14 0–0,17 | 0–0,2 0–0,24 0–0,28 0–0,34 | Более 0,5 « 1,1 « 1,3 « 1,6 |
1.5. | Допускаемые зазоры в шарнирах при диаметре отверстий, мм 5 - 10 10 - 18 18 - 30 30 - 50 | « | 0,015–0,085 0,02–0,105 0,025–0,13 0,032–0,15 | 0,015–0,25 0,02–0,3 0,025–0,35 0,032–0,42 | 0,015–0,5 0,02–0,6 0,025–0,7 0,032–0,84 | Более 1 « 2,2 « 2,6 « 3,2 |
2.Токоприемники 10РР2, 10РР5, 17РР, 17РР2 и SP6 M/ CM | ||||||
2.1. | Толщина накладок полоза: медных металлокерамических | Все | 6 7,8 | 6–5 7,8–6 | 6–5 7,8–5 | Менее 2,5 « 2,5 |
2.2. | Отклонение верхней поверхности полоза от горизонтали на длине 1м: при установке токоприемника на выверенных тумбах в цехе при установке на крыше электровоза | « | - – | 0–5 0–10 | 0–5 0–10 | - Более 20 |
2.3. | Смещение центра полоза относительно центра основания токоприемника поперек оси электровоза в пределах рабочей высоты | « | – | 0–10 | 0–10 | Более 15 |
2.4. | Зазор между валиком и отверстием в силуминовых деталях | « | 0,03–0,08 | 0,03–0,1 | 0,03–0,2 | Более 1 |
2.5. | Наибольший осевой зазор в любом шарнире рамы | « | – | 0,5 | 0,8 | Более 1 |
2.6. | Вогнутость полоза на длине 1 м прямолинейной части | « | – | 0–2 | 0–2 | Более 5 |
2.7. | Зазор между накладками на полозе со стороны контактной поверхности медных и металлокерамичес-ких пластин, не более | « | 1 | 1 | 1 | Более 1 |
3.Быстродейст-вующие выключатели 12НС, 12НС3 и 1 VPD3 | ||||||
3.1. | Толщина подвижного контакта в рабочей части контактной поверхности | Все | 50+0,5 | 50–47 | 50–44 | Менее 40 |
3.2. | Длина неподвижного контакта по нижней грани | « | 121 | 121–119 | 121–119 | Менее 116 |
3.3. | Раствор контактов | « | 26±2 | 28–24 | 28–22 | Более 32 Менее 20 |
3.4. | Наибольшее горизонтальное смещение силовых контактов относительно друг друга | « | 0,5 | 0,5 | 0,5 | Более 1 |
3.5. | Зазор между вилкой (отключающим рычагом) и упором якоря отключающего электромагнита во включенном положении выключателя | « | 3 | 3–2,5 | 3–2 | – |
3.6. | Зазор между планками изоляционной тяги и шпильки отключающей вилки во включенном положении выключателя | « | 5 | 5–3 | 5–3 | Менее 3 |
3.7. | Площадь прилегания правого рога дугогасительной камеры к неподвижному контакту, не менее, % | « | 80 | 80 | 80 | Менее 80 |
3.8. | Раствор контактов правого рога дугогасительной камеры, не более | « | – | 8 | 8 | Более 8 |
3.9. | Зазор между стенкой дугогасительной камеры и силовыми контактами | « | – | 1–1,5 | 1–1,5 | Менее 1 |
3.10. | Толщина стенок дугогасительной камеры в месте разрыва контактов | « | 6+0,3 | 7,5–5 | 7,5–4 | Менее 3 |
3.11. | Зазор между вилкой (отключающим рычагом) и упором на подвижном контакте в отключенном положении выключателя | « | 3 | 3–2,5 | 3–2 | – |
3.12. | Нажатие главных контактов, Н (кгс) | « | 600(60) | 600(60) | 600–570 (60–57) | Менее 570 (57) |
4.Главные контроллеры (переключатели) 17 КН и 18КН | ||||||
4.1. | Толщина контактов | Все | 8±0,2 | 8,2–7 | 8,2–6 | Менее 4 |
4.2. | Раствор на нулевой позиции, не менее | « | 14 | 14 | 14 | Менее 13 |
4.3. | Раствор контактов на позициях | « | Согласно требованиям к развертке (см. приложение № 7) | |||
4.4. | Наибольшее поперечное смещение контактов относительно друг друга во включенном положении | « | – | 0,5 | 1,0 | Более 2 |
4.5. | Толщина стенки и перегородки дугогасительной камеры | « | 6+0,3 | 7,5–5 | 7,5–4 | Менее 3 |
4.6. | Смещение роликов подвижного контакта за край кулачковой шайбы, не более | « | – | – | 1 | Более 1 |
4.7 | Смещение половинок кулачковых шайб относительно друг друга, не более | « | – | – | 1 | Более 1 |
4.8. | Притирание силовых контактов не менее | « | 1 | 1 | 1 | Менее 1 |
4.9. | Нажатие силовых контактов не менее, Н (кгс) | « | 80(8) | 80(8) | 80(8) | Менее70 (7) |
5. Пневматические привода 15NP и PHV2 | ||||||
5.1. | Внутренний диаметр цилиндра пневматического привода | Все | 72+0,03 | 72,2 | 72,3 | – |
5.2. | Наибольший зазор между цилиндром и поршнем привода | « | – | 0,5 | 0,5 | – |
5.3. | Наибольший зазор в шарикоподшипни-ках главного вала пневматического привода | « | – | 0,2 | 0,2 | – |
6. Реверсоры 18МР, 18МР2 | ||||||
6.1. | Толщина контактной части силового сегмента | Все | 6 | 6–5 | 6–4,5 | Менее 4 |
6.2. | Толщина силового пальца в контактной части | « | 5 | 5–4 | 5–3,5 | Менее 3 |
6.3. | Наименьший диаметр сегментов | « | 138 150 | 137 149 | 136 148 | Менее 135 « 147 |
6.4. | Нажатие силовых пальцев на сегмент, Н (кгс) | « | 25(2,5) | 25(2,5) | 22–25 (2,2–2,5) | Менее 22 (2,2) |
6.5. | Провал силовых пальцев | « | 2 | 2 | 2–2,5 | Менее 2 |
6.6. | Износ скользящих втулок подшипника | « | – | 0,1 | 0,2 | Более 0,5 |
7. Реверсоры 1 PPD26, 3 PPAD3 | ||||||
7.1 | Толщина ножа в месте соприкосновения | Все | 8 | 8–7 | 8–6,5 | Менее 6 |
7.2 | Толщина пружинных контактов в месте соприкосновения | « | 4 | 4–3,8 | 4–3,7 | Менее 3,5 |
7.3 | Провал пальцев | « | 1 | 1 | 1 | Менее 0,5 |
8. Разъединитель 7FC, 7 FC3 и OSD4 | ||||||
8.1. | Толщина ножа в рабочей части | Все | 10 | 10–8,5 | 10–8,0 | Менее 7,5 |
8.2. | Толщина пружинящих контактов в месте соприкосновения с ножом | « | 3 | 3–2,5 | 3–2,2 | Менее 2 |
8.3. | Нажатие пружинящих контактов, Н (кгс) | « | 50(5) | 50–48 (5–4,8) | 50–45 (5–4,5) | Менее 40(4) |
9. Контроллер косвенного управления IKNDI, 1 KND3 и 1 KND4 | ||||||
9.1. | Раствор контактов | Все | 4 | 4 | 4–3,5 | Менее 3 |
9.2. | Износ контактов | « | – | 0,5 | 1 | Более 1,2 |
9.3. | Износ сегментов на кулачках | « | – | 0,2 | 0,3 | Более 0,5 |
9.4. | Износ роликов кулачковых выключателей | « | – | 0,05 | 0,1 | Более 0,15 |
9.5. | Зазор в шарикоподшипни-ках | « | – | 0,1 | 0,15 | – |
10. Переключатель тормоза PPD15, 1PPD14, 3PPD14, PPD12 | ||||||
10.1. | Износ ролика сегмента | Все | – | 0,2 | 0,3 | Более 0,5 |
10.2. | Износ цапф и ролика включателя | « | – | 0,2 | 0,3 | Более 0,5 |
10.3. | Толщина контактов включателя VKADI | « | 1,5 | 1,5–1,2 | 1,5–1 | Менее 0,7 |
11. Контроллеры машиниста 12KR, 20KR, IKRD3, KRD17 | ||||||
11.1. | Высота контакта контактного пальца с наплавленной частью | Все | 9 | 9–8 | 9–7,5 | Менее 7 |
11.2. | Высота наплавленной части у контактного пальца | « | 4 | 4–3 | 4–2,5 | Менее 2 |
11.3. | Толщина медных сегментов | « | 4 | 4–3 | 4–2,5 | Менее 2 |
11.4. | Толщина подвижного контакта переключающего устройства | « | 1,5 2 | 1,5–1 2–1,5 | 1,5–0,8 2–1,2 | Менее 0,5 Менее 0,7 |
11.5. | Раствор контактов (кратчайшее расстояние от пальца до сегмента) | « | 4 4 | 4 4 | 4–1,5 4–3 | Менее 1 Менее 3 |
11.6. | Износ роликов кулачковых выключателей | « | – | 0,2 | 0,3 | Более 0,5 |
11.7. | Износ сегментов на кулачках | « | – | 0,2 | 0,3 | Более 0,5 |
11.8. | Нажатие контактов, Н (кгс) | « | 3,5(0,35) | 3,5(0,35) | 3,5–3 (0,35–0,3) | Менее 2(0,2) |
11.9. | Толщина контактов | « | 2 | 2–1,5 | 2–1 | Менее 0,5 |
12. Электропневма-тические контакторы 6SPI, ISVAD4, ISVAD5, SVD3, SVD6, 1 SVD3, 3 SVAD4, 2 SVAD4, 2 SVAD5, 3 SVAD6, 2 SVAD6, SVAD11, 9 SVAD7, SVAD7, SVAD9 | ||||||
12.1. | Толщина дугогасительных контактов | SVD3, SVD6 6SP1 ISVAD4, ISVAD5 2SVAD, 3SVAD4 1SVD3 2SVAD5, 3SVAD6 2SVAD6, SVAD11 9SVAD7, SVAD7 SVAD9 | 6 12±0,2 6 10 | 6 12,2–9 6 10-7 | 6–4 12,2–7 6–5 10-6 | Менее 3 « 5 « 3 « 5 |
12.2. | Раствор силовых (мостиковых) контактов | 6SP1 SVD3, SVD6 SVAD4, SVAD9 Остальных | 26±1 20±1 16±0,5 16±1 | 25–27 19–21 15,5–16,5 15–17 | 25–29 19–23 15–17 15–19 | Менее 24 Более 32 Менее 15 Более 26 Менее 12 Более 20 Менее 12 Более 20 |
12.3. | Наибольшее поперечное смещение дугогасительных контактов во включенном положении | Все | – | 0,5 | 1 | «1,5 |
12.4 | Раствор дугогасительных контактов | Все | 20±1 | 19–21 | 19–21 | Менее 23 Более 28 |
12.5. | Нажатие силовых контактов, Н ( кгс) | 2SVAD4 1SVAD5 SVD3, SVD6 остальных | 90(9) 60(6) 35(3,5) 80–100 (8–10) | 85–95 (8,5–9,5) 58–62 (5,8–6,2) 35–32 (3,5–3,2) 80–100 (8–10) | 85–95 (8,5–9,5) 58–62 (5,8–6,2) 35–30 (3,5–3) 80–100 (8–10) | Менее 85(8,5) Менее 58(5,8) Менее 35(3,5) Менее 80(8) |
12.6 | Толщина серебряных напаек мостиковых контактов | Все | 1,6 | 1,5–1,3 | 1,5–1,2 | Менее 1,0 |
12.7 | Нажатие дугогасительных контактов, Н (кгс) | SVD3, SVD6 2SVAD4, 1SVAD5 остальных | 25–35 (2,5–3,5) 28–32 (2,8–3,2) 28–38 (2,8–3,8) | 25–35 (2,5–3,5) 28–32 (2,8–3,2) 28–38 (2,8–3,8) | 25–35 (2,5–3,5) 28–32 (2,8–3,2) 28–38 (2,8–3,8) | Менее 25(2,5) Менее 28(2,8) Менее 28(2,8) |
12.8 | Наибольшее поперечное смещение мостиковых контактов во включенном положении | Все | – | 0,5 | 1 | Более 1 |
12.9 | Внутренний диаметр привода | 6SP1 SVD3, SVD6, 1SVD3 остальных | 60+0,045 40 80 | 60,15 40,15 80,15 | 60,25 40,25 80,25 | Более 60,35 « 40,35 « 80,35 |
13. Электропневма-тические контакторы ПК 19 (ПК120), ПК 21 (ПК121) | ||||||
13.1 | Толщина силового контакта (у пятки) | Все | 10 ![]() | 9,8-10,2 | 5-10,2 | Менее 3,5 |
13.2 | Раствор силовых контактов | Все | 24-27 | 24-27 | 24-27 | Менее 24, Более 32 |
13.3 | Наибольшее поперечное сечение силовых контактов относительно друг друга во включенном состоянии | Все | 1 | 1 | 2 | Более 2 |
13.4 | Допускаемое уменьшение от номинальных размеров валиков и осей при диаметре: от 5 до 10 от 10 до 18 | Все | 0,015-0,055 0,02-0,07 | 0,015-0,055 0,02-0,07 | 0,015-0,3 0,02-0,36 | Более 0,5 Более 1,1 |
13.5 | Допускаемое увеличение от номинальных размеров отверстий под валики и оси при диаметре: от 5 до 10 от 10 до 18 | Все | 0,03 0,035 | 0,03 0,035 | 0,2 0,24 | Более 0,5 Более 1,1 |
13.6 | Допускаемые зазоры в шарнирах при диаметре отверстий: от 5 до 10 от 10 до 18 | Все | 0,015-0,085 0,02-0,105 | 0,015-0,085 0,02-0,105 | 0,015-0,5 0,02-0,6 | Более 1,0 Более 2,2 |
13.7 | Суммарное перемещение подвижного контакта по вертикали за счет слабины в валиках | Все | - | - | 2,5 | 2,5 |
13.8 | Максимальный зазор между штоком поршня и отверстием для него в цилиндре, не более | Все | 0,1 | 0,1-0,5 | 0,1-0,6 | Более 1 |
13.9 | Внутренний диаметр цилиндра пневматического привода | Все | 45+0,05 | 45-45,45 | 45-45,6 | Более 45,7 |
13.10 | Ход клапана электромагнитного включающего вентиля | Все | 0,9 | 0,9 | 0,7-1,1 | 0,6-1,2 |
13.11 | Толщина стенки лабиринтно-щелевых дугогасительных камер | Все | 5,5-7 | 5-7,5 | 4-7,5 | Менее 3 |
13.12 | Износ стенок дугогасительных камер, не более, % | Все | - | - | 25 | 50 |
13.13 | Зазор между стенкой дугогасительной камеры и подвижными деталями контактора, не менее | Все | - | 1 | 1 | Менее 1 |
13.14 | Допустимый обрыв жил шунта, не более, % | Все | - | - | 10 | Более 10 |
13.15 | Допускаемое отклонение длины пружины, не более, % | Все | - | - | 5 | Более 5 |
14. Электропневма-тические контакторы 1КП-016М-05 К220 | ||||||
14.1 | Раствор главных контактов | Все | 22±3 | 19-25 | 19-25 | - |
14.2 | Раствор вспомогательных контактов | Все | 8±2 | 6-10 | 6-10 | - |
14.3 | Провал главных контактов | Все | 4,5-9,0 | 4,5-9,0 | 4,5-9,0 | - |
14.4 | Провал вспомогательных контактов | Все | 2,5-5,5 | 2,5-5,5 | 2,5-5,5 | - |
14.5 | Нажатие главных контактов, Н (кгс) | Все | 7-10 (0,72-1,02) | 7-10 (0,72-1,02) | 7-10 (0,72-1,02) | - |
14.6 | Нажатие вспомогательных контактов конечное, Н (кгс), не менее | Все | 0,8 (0,081) | 0,8 (0,081) | 0,8 (0,081) | - |
14.7 | Суммарный износ главных контактов по толщине | Все | - | - | 0-4 | Более 4 |
14.8 | Суммарный износ вспомогательных контактов по толщине | Все | - | - | 0-2 | Более 2 |
14.9 | Толщина стенки продольно – щелевых дугогасительных камер | Все | 6 | 5-7,5 | 4-7,5 | Менее 3 |
14.10 | Толщина перегородки продольно- щелевых дугогасительных камер | Все | 5 | 4-5,3 | 3-5,3 | Менее 2 |
14.11 | Ширина щели продольно – щелевых камер | Все | - | - | 4 | 4 |
15. Электропневма-тические контакторы 1КП-006-18 | ||||||
15.1 | Раствор главных контактов | Все | 28-32 | 28-32 | 28-32 | - |
15.2 | Раствор дугогасительных контактов при полностью включенном контакте | Все | Не менее 4,0 | Не менее 4,0 | Не менее 4,0 | - |
15.3 | Нажатие главных контактов, Н (кгс),не менее (начальное-конечное) | Все | 40-127 (4,1-12,9) | 40-127 (4,1-12,9) | 40-127 (4,1-12,9) | - |
15.4 | Допустимое боковое смещение дугогасительных контактов | Все | 1 | 1 | 1 | - |
15.5 | Суммарный износ главных контактов по толщине | Все | - | - | 2 | Более 2 |
15.6 | Суммарный износ дугогасительных контактов по толщине | Все | - | - | 3 | Более 3 |
15.7 | Толщина стенки продольно – щелевых дугогасительных камер | Все | 6 | 5-7,5 | 4-7,5 | Менее 3 |
15.8 | Толщина перегородки продольно- щелевых дугогасительных камер | Все | 5 | 4-5,3 | 3-5,3 | Менее 2 |
15.9 | Ширина щели продольно – щелевых камер | Все | - | - | 4 | 4 |
16.Электромаг-нитные контакторы 6SM, 23SM, 31SM3, 42SM,43SMI, VO3 c-009, V13 c-005, SMD7, 23 SMD8, SMD11, 4 SMD17,2 SMD20 | ||||||
16.1 | Толщина силовых контактов | 6SM остальных, кроме V03c-009,V13c-005 | 8+0,2 6+0,2 | 8,2–7 6,2–5 | 8,2–6 6,2–4 | Менее 4 « 3 |
16.2. | Раствор силовых контактов | 6SM 23SM, 31SM, 31SM3, 43SM1; SMD7, 2SMD8, 42SM V03c-009,V13c-005 SMD11, 4SMD17,2SMD20 | 18–20 16±1 13±0,5 1,8±0,2 6+1 | 8–20 15–17 1,6–2,0 6–7 | 18–25 14–18 1,6–2,5 6–7,5 | Менее 17 Более 26 Менее 14 Более 19 Менее 1,5 Более 3,0 Менее 5,0 Более 8,0 |
16.3. | Наибольшее поперечное смещение силовых контактов относительно друг друга | Все | – | 0,5 | 1 | Более 2 |
16.4. | Толщина стенки дугогасительной камеры | 6SM остальных | 5 4 | 6,5–5 5,5–4 | 6,5–4,5 5,5–3,5 | Менее 4 « 3 |
16.5. | Зазор между дугогасительным рогом и дугогасительной камерой | Все | 3 | 3 | 3 | « 3 |
16.6. | Раствор блок-контактов | 6SM V03c-009,V13c-005 остальных | 3 1 2 | 3 1 2 | 3 1 2 | « 3 « 0,8 « 2 |
16.7. | Провал блокировочных контактов | Все, кроме V03c-009,V13c-005 | 1,5 | 1,5 | 1,5 | « 1,5 |
16.8. | Нажатие блокировочных контактов, Н (кгс) | « | 0,55–0,6 (0,055–0,06) | 0,55–0,6 (0,055–0,06) | 0,55–0,6 (0,055–0,06) | 0,5(0,05) |
17. Мостиковые блокировочные контакты реле, выключателей, разъединителей | ||||||
17.1. | Высота контактов | Все | 1,5+0,1 | 1,6–1,2 | 1,6–0,8 | Менее 0,5 |
17.2. | Раствор контактов | « | 1,5 | 1,5–2,5 | 1,5–2,5 | « 1,2 |
17.3. | Провал контактов | « | 2±0,5 | 1,5–2,5 | 1,5–2,5 | « 1 |
17.4. | Нажатие на контактный мостик, Н (кгс) | « | 0,45–0,5 (0,045–0,05) | 0,45–0,5 (0,045–0,05) | 0,45–0,5 (0,045–0,05) | « 0,3(0,03) |
17.5. | Наибольшее поперечное смещение контактов относительно друг друга во включенном положении | « | – | 0,5 | 1 | Более 1 |
18. Реверсивный переключатель ПТ-022 | « | |||||
18.1 | Раствор главных контактов | « | 17 | 17 | 17 | Менее 17 |
18.2 | Толщина главного подвижного контакта | « | 12—0,5 | 10-12 | 8-12 | Менее 7 |
18.3 | Износ главного подвижного контакта | « | - | - | 3,5 | Более 4,5 |
18.4 | Износ цилиндрической поверхности кулачковой шайбы, не более | « | - | - | 3 | Более 4 |
18.5 | Биение окружности кулачковых шайб, не более | « | - | - | 1 | Более 2 |
18.6 | Увеличение внутреннего диаметра цилиндра по износу, не более | « | - | - | 1 | Более 1,5 |
18.7 | Наибольший зазор между цилиндром и поршнем привода | « | - | - | 0,6 | Более 0,8 |
19. Реле РПН-496 | ||||||
19.1 | Раствор размыкающих контактов | « | 2,0-2,5 | 2,0-2,5 | 2,0-2,5 | Менее 2, Более 3,5 |
19.2 | Раствор замыкающих контактов | « | 2,5-3,0 | 2,5-3,0 | 2,5-3,0 | Менее2,5, Более 5 |
19.3 | Провал замыкающих контактов | « | 1-1,5 | 1-1,5 | 1-1,5 | Менее1,0, Более 1,5 |
19.4 | Провал размыкающих контактов | « | 1,5-2 | 1,5-2 | 1,5-2 | Менее 1,5 , Более 2 |
20. Реле РНН-497 | ||||||
20.1 | Раствор замыкающих контактов | « | 2,0-2,5 | 2,0-2,5 | 2,5- 3,0 | Менее 2,5, Более 5,0 |
20.2 | Провал замыкающих контактов | « | 1,0-1,5 | 1,0-1,5 | 1,0-1,5 | Менее 1,0, Более 1,5 |
21. Электромаг-нитное реле РП-280 | ||||||
21.1 | Рабочий воздушный зазор под якорем | « | 3,5 | 3,5 | 3,5 | Более 4 |
21.2 | Раствор контактов | « | 2,5-3,5 | 2,5-3,5 | 2,5-3,5 | Менее 2,5, Более5,5 |
21.3 | Провал контактов | « | 1,5-2,5 | 1,5-2,5 | 1,5-2,5 | Менее1,5, Более3,0 |
21.4 | Толщина контактных накладок | « | 1,2-0,12 | 1,2-0,12 | 1,2-0,12 | Менее 0,2 |
22. Электромагнитное реле РТ-067 | ||||||
22.1 | Толщина контактных накладок | « | 1,2-0,12 | 1,2-0,12 | 1,2-0,12 | Менее 0,2 |
22.2 | Раствор контактов | « | 3,5-5 | 3,5-5 | 3,5-5 | Менее 3,5, Более 7 |
22.3 | Провал контактов | « | 1,5-3 | 1,5-3 | 1,5-3,5 | Менее1,5, Более 3 |
23. Электромагнитное реле РДЗ-068, РДЗ-068-01 | ||||||
23.1 | Раствор контактов | « | 4-5 | 4-5 | 4-5 | Менее 4, Более 6,5 |
23.2 | Провал контактов | « | 1,5-2 | 1,5-2 | 1,5-2 | Менее1,5, Более 2 |
23.3 | Толщина контактных накладок | « | 1,2-0,12 | 1,2-0,12 | 1,2-0,12 | 0,2 |
24. Реле РП472 | ||||||
24.1 | Раствор контактов | « | Не менее 4 | Не менее 4 | Не менее 4 | Менее 4, Более 6 |
25. Вентиль электромагнит-ный VTM2 | ||||||
25.1 | Ход якоря вентиля (клапана) | « | 1,7±0,15 | 1,7±0,15 | 1,85-1,1 | Менее 1, Более 1,9 |
25.2 | Ход клапана | « | 1,0 ±0,15 | 1,0 ±0,15 | 1,15-0,7 | Менее 0,6, Более 1,2 |
Приложение 3
Дата добавления: 2019-02-12; просмотров: 446; Мы поможем в написании вашей работы! |
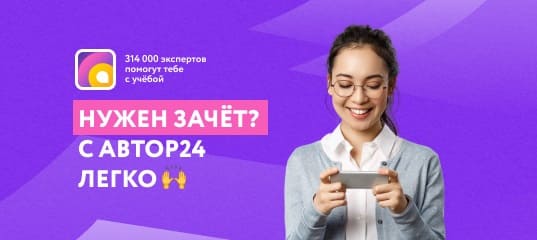
Мы поможем в написании ваших работ!