Технология и организация ремонта электроподвижного состава промышленного транспорта
Технологический процесс. В производственном цикле ремонта т. п. с. основным является технологический процесс, представляющий собой комплекс способов и средств восстановления с регламентированной последовательностью сочетания операций. Требования, предъявляемые к технологическому процессу ремонта: возможность восстановления заданной номенклатуры объектов; выполнение технических условий, норм и допусков с учетом требований к уровню характеристик надежности; обеспечение заданного уровня качества ремонта; прогнозирование и направленное формирование физико-механических характеристик средств восстановления для достижения заданного ресурса детали.
Основными параметрами технологического процесса восстановления являются: обеспечение направленного формирования свойств восстанавливаемой детали, точность, надежность, экономичность и производительность. К второстепенным параметрам относятся: уровень автоматизации, технологическая трудоемкость, стабильность.
Направленное формирование свойств характеризует способность назначенного технологического процесса придавать восстанавливаемой детали заранее обусловленные свойства, которые обеспечивают необходимый технический ресурс. Так, для обеспечения управления свойствами восстанавливаемого слоя необходимо: четкое формулирование технических требований к восстанавливаемой детали; обеспечение прогнозирования и направленного формирования физико-механических характеристик восстанавливаемого слоя. Таким образом, технологическое управление сводится к разработке рационального технологического процесса восстановления, мероприятий по его стабилизации, выявлению количественных параметров и активному воздействию на них с целью их улучшения на основе СТП (стандартов предприятия).
|
|
Точность технологического процесса, как один из основных критериев его качества, определяется точностью выполнения основных технологических операций: механической обработки, пригонки, монтажа, испытаний. Так, точность механической обработки восстановленной детали характеризуется коэффициентом точности
,
где ∆ — поле рассеивания отклонений любого параметра обрабатываемой детали; S — поле допуска на параметр.
В производственных условиях наиболее рациональным является метод выборочных наблюдений. При этом обследуют определенную часть деталей от партии, данные о качестве которой распространяют на всю партию. По статистическим данным обмеров строят точечную диаграмму (рис. 2). Если все значения проверяемого параметра находятся между верхней (ВКПГ) и нижней (НКПГ) контрольно-предупредительными границами, значит, точность изготовления находится в допустимых пределах. Характер изменения расположения точек на диаграмме указывает также на причину возникновения погрешностей, что позволяет наметить действенные мероприятия по их предупреждению.
|
|
Рис.2. Точечная диаграмма контроля состояния технологического
процесса обработки валика
Надежность технологического процесса — это его способность обеспечивать заданные выходные параметры, определенные технической или технологической документацией, в течение установленного времени при определенных режимах, заданных условиями производства. Надежность технологического процесса как системы характеризуется надежностью элементов — технологических операций. Так как технологическая операция является независимым элементом системы, вероятность исполнения процесса в заданных пределах (его надежность)
,
где k - общее число-технологических операций; р(Ai) - вероятность выполнения операции на заданном уровне.
Надежность технологического процесса восстановления детали т. п. с. должна находиться в пределах 0,92 — 0,97. Эффективным методом обеспечения заданного уровня надежности является стандартизация технологического процесса. Стандарт создают с целью определения системы допускаемых отклонений элементов процесса с учетом заложенных показателей качества. При соблюдении требований стандарта технологический процесс обеспечивает прогнозируемый уровень качества при запланированных расходах.
|
|
Экономичность технологического процесса восстановления узла (агрегата) определяется суммой затрат на производство демонтажа — восстановления — монтажа:
,
где Сд, СВ, См — стоимости соответственно демонтажа, восстановления и монтажа; пу — годовая программа ремонта узлов.
Назначенный технологический процесс может выполняться различными средствами. Рациональным считается такой процесс, который при прочих равных условиях обеспечивает наименьшую стоимость восстановления. При окончательном выборе варианта определяется только та часть стоимости, значение которой зависит от варианта технологического процесса. В общем случае себестоимость операций демонтажа и монтажа
,
где tшт/60 - норма штучно-калькуляционного времени, мин; Ср — заработная плата основных рабочих; 3Н— процент начисления на заработную плату; CЭО — стоимость эксплуатации оборудования; Са — отчисления на амортизацию оборудования; СИи Спр — стоимость эксплуатации и отчисления на амортизацию инструмента и приспособлений.
|
|
Стоимость восстановления детали
,
где Смт, Сэ и Сн — стоимость соответственно материалов, энергии и наладки оборудования.
Таким образом, сопоставляя расходы по вариантам намечаемых технологических процессов, можно определить наиболее экономичный из них.
Производительность технологического процесса определяют числом деталей (узлов), восстановленных за определенный период времени (смену, месяц):
,
где F — фонд рабочего времени; ∑t3 ~ время, затраченное на восстановление единицы продукции.
Повышение производительности технологического процесса достигается наиболее полным использованием фонда рабочего времени и сокращением времени на восстановление детали. При проектировании рационального трудового процесса предусматривают главным образом сокращение простоев по организационно-техническим причинам и меры по сокращению времени непроизводительной работы. Время восстановления сокращается за счет интенсификации технологического процесса, разработки и внедрения технически обоснованных норм, которые устанавливаются для конкретных условий при наиболее полном использовании средств производства, достижений науки, техники и передового опыта. Это приобретает особую значимость в период технического перевооружения промышленного железнодорожного транспорта.
Повышение производительности технологического процесса сокращает длительность производственного цикла ремонта. Это снижает простой т. п. с. в ремонте, повышает оборачиваемость оборотных средств, уменьшает незавершенное производство, улучшает использование производственных площадей и технологического оборудования.
Выбор рационального варианта технологического процесса восстановления производят в два этапа с последующей оптимизацией принятого решения:
1. Назначают варианты технологических процессов, обеспечивающих необходимый технический ресурс с учетом производственных возможностей предприятия.
2. Выбирают из них наиболее экономически целесообразный. Оптимизацию технологического процесса по экономическому критерию производят следующим образом.
Математическая модель оптимизации для узла или локомотива в целом
,
где Э — экономический эффект, руб.; F (l) — доходы в эксплуатации после внедрения нового технологического процесса, руб.; ∫р(l) —затраты на ремонт и эксплуатацию, руб.
Каждую из этих функций можно выразить через основные составляющие:
,
где C1 и С2 — себестоимость единицы выполненной локомотивом работы до и после внедрения нового технологического процесса, руб./т∙км; ∑ Qili — работа, выполненная локомотивом за межремонтный период, т∙км; ∆Сk и ∆СЭКС - дополнительные затраты соответственно на повышение качества, руб., и содержание локомотива в эксплуатации, руб./тыс. км; Lp — межремонтный период, тыс. км.
Условие оптимизации обеспечивается, если
,
где ЕН — нормативный коэффициент эффективности на промышленном транспорте.
Таким образом, назначенный технологический процесс считается оптимальным по экономическому критерию, если экономическая и техническая эффективность отремонтированного узла (локомотива) имеет наибольшее значение по отношению к произведенным затратам на ремонт. Технологический процесс разрабатывают с использованием технической, технологической документации и документации общего назначения, руководствуясь ей, как действующей документацией отрасли. Ниже приведен перечень рекомендуемой действующей документации:
· технический паспорт локомотива;
· Инструкция по освидетельствованию, ремонту и формированию колесных пар локомотивов и электросекций ЦТ/2306;
· Инструкция по эксплуатации и уходу за аккумуляторными батареями;
· указания «Об устранении причин ослабления бандажей» 373 ЦТЭ/73-Т;
· Инструкция по содержанию и ремонту автосцепного устройства подвижного состава железных дорог 3181-ЦВ;
· Технические указания по изготовлению и ремонту листовых рессор локомотивов ЦТРП-59, М., Транспорт, 1963;
· Технологическая инструкция на формирование, проверку, ремонт и эксплуатацию резинометаллических амортизаторов буксовых поводков локомотивов и электросекций ТИ 175;
· Инструкция по техническому обслуживанию, ремонту и испытанию тормозного оборудования локомотивов и моторвагонного подвижного состава ЦТ/3549;
· Инструкция по содержанию и ремонту роликовых подшипников локомотивов и моторвагонного подвижного состава ЦТ/2361;
· Инструктивные указания по сварочным работам при ремонте тепловозов, электровозов и моторвагонного подвижного состава ЦТ теп/251;
· Технические указания по контролю шариковых подшипников локомотивов и моторвагонного подвижного состава широкой колеи И-025Р-64, разработанные ПКТБ ЦТВР;
· Инструкция по магнитному контролю ответственных деталей локомотивов и моторвагонного подвижного состава в депо и на ремонтных заводах ЦТ/2303; Инструкция по техническому содержанию устройств автоматической локомотивной сигнализации и автостопов ЦШ/2471;
· Инструкция по эксплуатации и ремонту локомотивных скоростемеров СЛ-2 и СЛ-2М и приводов к ним ЦТ/3004;
· Временная технологическая инструкция по применению эпоксидных компаундов при ремонте деталей локомотивов КЛ-192;
· Технологическая инструкция на осмотр, ремонт и проверку счетчиков киловатт-часов постоянного тока типов Д-600М и СКВТ-Д621 с добавочным резистором типа Р-600 и наружным шунтом 150ШС ТИ 18;
· Руководство по заводскому ремонту аппаратов АЛСН РР-27-71; Технологическая инструкция по очистке от загрязнений и нанесению защитного электроизоляционного покрытия на поверхность стеклопластиковых изоляторов при ремонте электроподвижного состава ТИ 237;
· указания «О ремонте и сборке колесно-моторных блоков» ЦТ теп/248; технологические карты ремонта на все виды оборудования тяговых агрегатов, разработанные НИС ДИИТ1;
· Правила текущего ремонта тяговых агрегатов ПЭ2М, ОПЭ1А, ОПЭ2 (НИС ДИИТ);
· Правила ремонта электрических машин тяговых агрегатов (НИС ДИИТ); Технологические указания по наплавке гребней бандажей колесных пар аустенитными сталями (НИС ДИИТ);
· Технологические указания по ремонту автосцепного оборудования СА-ЗМ (НИС ДИИТ);
· Правила технической эксплуатации железнодорожного транспорта предприятий Министерства черной металлургии СССР;
· приказ № 415 «О совершенствовании технического обслуживания, ремонта и эксплуатации локомотивов на предприятиях Министерства черной металлургии СССР»;
· Дизель 84Н-26/26. Основные данные для ремонта (разработаны Коломенским тепловозостроительным заводом);
· Дизель ЗА-6Д49. Техническое описание и инструкция по эксплуатации (Внешторг, 1973);
· книга ремонта локомотива;
· журнал технического состояния локомотива;
· книга регистрации непланового ремонта локомотивов.
Дата добавления: 2018-08-06; просмотров: 459; Мы поможем в написании вашей работы! |
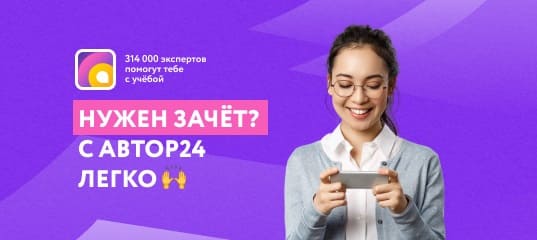
Мы поможем в написании ваших работ!