Изготовление сопловых раструбов и насадков
Для изготовления выходных раструбов рдхх широко используют УУКМ. Каркасы раструбов в основном производят в соответствии со следующими технологиями: ткане-выкладочная прошивка, намоточная и технология ткачества (табл. 6.10). Тканевыкладочная прошивная технология и применяемое оборудование были рассмотрены в гл. 3. Для намотки раструбов используют универсальное намоточное оборудование и те же процессы, что и для намотки корпусов двигателей. Аналогичные процессы применяют и для изготовления сопловых насадков жидкостных ракетных двигателей.
6. ПРОЦЕССЫ ИЗГОТОВЛЕНИЯ КОНСТРУКЦИЙ ИЗ КОМПОЗИТОВ
Таблица 6.10
УУКМ для изготовления раструбов РДТТ
Конструкция соплового насадка ЖРД, изготавливаемая из УУКМ, представлена на рис. 6.17, а структурная схема технологического процесса его изготовления — на рис. 6.18.
Намотка — один из самых совершенных процессов изготовления высокопрочных армированных оболочек, позволяющий получать оболочки вращения сложной формы и реализовывать с высокой точностью большое количество схем армирования.
446
447
6.2. Технология изготовления конструкций сопла
6. ПРОЦЕССЫ ИЗГОТОВЛЕНИЯ КОНСТРУКЦИЙ ИЗ КОМПОЗИТОВ
Рис. 6.17.Конструктивная схема насадка
При намотке изделий конической формы ткаными лентами из волокнистых материалов слои армирующего материала располагаются не только параллельно образующей, но также па-раллельно и под различными углами к оси изделия.
|
|
Технологический процесс спиральной намотки "сухим" способом для рассматриваемого случая заключается в следующем. Волокнистый армирующий материал перед формованием предварительно пропитывают связующим (в данном случае бакелитовым лаком ЛБС-2) на пропиточных машинах, которые обеспечивают качественную пропитку и требуемое равномерное содержание связующего в препреге за счет регулирования вязкости связующего в процессе пропитки.
Насадок выполняют способом двухзаходной намотки, согласно которому одновременно укладываются два слоя ленты. Контактное давление формования создается путем натяжения армирующего волокнистого материала.
С целью получения оптимальной геометрии намотки используют метод зонной намотки на универсальном намоточном станке. После завершения процесса намотки оболочку по внешней поверхности утягивают фторопластовой лентой. Отверждение углепластика является частью технологического
Рис. 6.18.Структурная схема технологического процесса изготовления насадка
448
29-243
449
29* |
6.2. Технология изготовления конструкций сопла
процесса, который должен обеспечить заданные требования по физико-механическим характеристикам.
|
|
Задавая закон изменения температуры отверждения в процессе нагрева и охлаждения, необходимо учитывать конкретные условия, вытекающие из разнородности коэффициентов ли нейного термического расширения материалов изделия, ее геометрии, теплопроводности применяемой формообразующей оснастки, типа применяемого связующего, интенсивности теп-лопритока нагревательных устройств. Вместе с тем, технологические режимы отверждения должны обеспечивать бездефектную структуру материала и конструкции с наименьшими затратами энергетических ресурсов. Необходимо также, чтобы температура отверждения обеспечивала оптимальные характе ристики всех материалов и по всей толщине изделия.
С учетом вышесказанного применяют следующий режим отверждения оболочки. Изделие помещают в газостат. После проверки его работоспособности поднимают давление до значения 400 кПа в течение 1 ч при температуре до 120 °С. При этих параметрах изделие выдерживают еще 1 ч. Происходит предварительное отверждение, после чего давление доводят до значения 650 кПа, а температуру до 160 °С, и изделие выдерживают еще 2 ч. Установку отключают. После остывания до нормальной температуры изделие извлекают из установки, снимают с оправки и подвергают термической обработке.
|
|
Режим термической обработки осуществляется за несколько этапов: подъем температуры до 100 °С со скоростью 100 °С/ч, выдержка при этой температуре 2 ч; до 250 °С со скоростью 20 °С/ч, выдержка — 2 ч; до 400 °С со скоростью 20 °С/ч, выдержка — 4 ч; до 600 °С со скоростью 50 °С/ч, выдержка -2 ч; подъем температуры до 1000 °С со скоростью 200 °С/ч.
Затем отключают нагрев установки путем плавного снижения напряжения с последующим отключением питания установки. Охлаждают печь с изделием до температуры 40 °С со скоростью естественного охлаждения, и после этого изделие извлекают из печи при включенной вытяжной вентиляции.
Изотермический процесс насыщения оболочки насадка пи-роуглеродом заключается в следующем. Оснастку подготавливают для насыщения каркаса и устанавливают нагреватель. Конические заготовки-каркасы устанавливают по обеим сто-
450
6. ПРОЦЕССЫ ИЗГОТОВЛЕНИЯ КОНСТРУКЦИЙ ИЗ КОМПОЗИТОВ
ронам нагревателя до взаимного упора торцами. Наносят разделительный слой из целлофана и бумаги на внутреннюю полость заготовок. Вырезанными из угольной ткани лентами заполняют внутренние полости заготовок путем обмотки нагревателя. Установкой переходников на нагреватель обеспечивают соосность каркаса относительно стержня нагревателя. Просверливают в каркасе под термопару отверстие диаметром 10 мм (см. гл. 3).
|
|
Далее нагреватель помещают в печь, в которую подают газ (пропан, метан и др.).
При температуре 1000 °С и положении индикатора термопары на отметке "0" по шкалам перемещения термопары начинают отсчитывать время насыщения. В процессе изотермического насыщения углеродный каркас нагревается за счет излучения углеродного кожуха-сердечника индукционной печи. Газообразный углеводород вводят во внутреннюю полость формуемого тела и он заполняет кожух, насыщая при этом нагретый каркас. Для измерения температуры в зонах охлаждения углерода устанавливают скорость перемещения термопары 0,25 мм/ч. Перемещение термопары корректируют так, чтобы за 8 ч процесса перемещение термопары равнялось 2 мм.
Длительность процесса насыщения составляет 72 ч при температуре не выше 1100 °С. После этого отключают нагрев установки путем плавного снижения напряжения, подаваемого на нагреватель, с последующим отключением питания установки. Заготовку охлаждают в печи в газовой среде до температуры 40 °С со скоростью естественного охлаждения печи. Отключают вакуумный насос, подают воздух, осуществляют полное отключение установки, открывают камеру и извлекают готовое изделие.
Следует отметить, что изотермический процесс приводит к равномерному осаждению углерода на волокнистой поверхности. Получаемая в процессе насыщения плотность УУКМ равна 1,4 г/см2. По завершении цикла процесса насыщения на изделии образуется поверхностная корка, которую удаляют механическим путем.
С целью противоокислительной защиты используют покрытие на основе карбида кремния, удовлетворительно работающее в диапазоне температур 1000... 1400 °С.
451
6.2. Технология изготовления конструкций сопла
Вместе с изделием данный технологический процесс проходят контрольные образцы.
"Кровельная" намотка теплозащиты соплового раструба
|
Способ "кровельной" намотки используют для нанесения жестких ТЗМ. При этом ТЗП формируют отдельно от защищаемой конструкции, а намотку соплового раструба ведут на технологическую оправку-имитатор поверхности изделия. Схема ориентирования волокон в таких ТЗМоптимизирована по минимуму эрозионного уноса массы материала покрытия и минимуму теплопроводности в сторону стенки раструба. Высокоскоростные и высокотемпературные потоки газообразных продуктов сгорания твердого топлива, содержащие конденсированную фазу и истекающие в расширяющуюся часть сопла, вызывают интенсивный унос массы ТЗМ, волокна в котором расположены параллельно защищаемой стенке конструкции. При этом унос углепластика будет существенно больше уноса стеклопластика вследствие их теплофизических и физико-ме ханических свойств. Если же волокна расположены перпендикулярно защищаемой поверхности, то унос массы будет мини мальным.
Подача ленты
Рис. 6.19. Схемы "кровельной" намотки абляционного покрытия на технологическую оправку: 1 — конструктивная или технологическая оправка для намотки; 2 — цапфы крепления оправки; 3 — наматываемое покрытие
Вместе с тем теплопроводность при такой схеме укладки волокон, особенно углеродных, будет максимальной. Приве денные на рис. 6.19 углы укладки тканой ленты из углеродных
6. ПРОЦЕССЫ ИЗГОТОВЛЕНИЯ КОНСТРУКЦИЙ ИЗ КОМПОЗИТОВ
волокон приняты как результат рассмотренного компромисса, а также с учетом сдвиговых характеристик в КМ и технологичности такой намотанной конструкции. Схему укладки слоев материала при такой намотке называют "рыбья чешуя", а саму технологию намотки — "кровельной", обеспечивающей расположение слоев с нахлестом по направлению движения набегающего потока газов. При формировании покрытия на поверхности защищаемой конструкции процесс намотки начинают с малого диаметра оправки, задавая требуемый угол укладки ленты и располагая плоскость ленты параллельно оси изделия. Такая схема намотки позволяет осуществить сильное натяжение лент при намотке и не только обойтись без технологических роликов, но и получить более плотную структуру материала покрытия, чем в случае намотки на маложесткую конструкцию изделия. Кроме того, структура намотанного покрытия может быть улучшена, если намотку вести не на цельнометаллическую технологическую, а на разжимную оправку, размеры которой будут изменены в процессе отверждения материала покрытия. Увеличение контактных давлений формования материала благоприятно скажется на улучшении свойств последнего. По окончании процесса отверждения материала отформованную оболочку покрытия снимают с оправки, механически обрабатывают и вклеивают в защищаемую конструкцию.
Схема "кровельной" намотки ориентирована на применение препрегов в виде лент, задающих волокнистую структуру покрытия. При этом однонаправленные ленты можно использовать при их возможно меньшей ширине, согласованной с кривизной наматываемой поверхности так, чтобы не вызвать недопустимых складок и нарушений текстуры материала из-за разной длины пути укладки обеих кромок одной ленты на профилированной оправке. Для некоторого снижения остроты проявления этого фактора применяют подогрев препрега и используют в препреге нити, например, из лавсановых волокон с удлинением до 7 % вместо стеклянных, углеродных и асбестовых, у которых удлинение только 2...3 %. При нанесении покрытий из асбо-, стекло- и углепластиков наиболее часто используют тканые ленты шириной 15...80 мм. Ткани сатинового плетения характеризуются большей гибкостью и высокими формующими свойствами, позволяющими обматывать оболоч-
452
453
6.2. Технология изготовления конструкций сопла
ки большей крутизны. В отличие от них ткани полотняного плетения можно использовать на оболочках малой кривизны, в этом случае натяжение при намотке должно быть более сильным.
Свойство формуемости тканых лент при рассматриваемой схеме намотки может быть улучшено, если одну из кромок ленты еще до начала намотки снабдить насечками, надрезами, вырезами, увеличивающими способность к деформации лент до 20...30 %. Созданы и специальные ткани, легко деформирующиеся по профилю оправки. Структура таких тканей имеет по ширине две зоны: одну обычной текстуры с удлинением 2...3 %, а другую — с текстурой повышенной деформативности (30 %).
Технологические параметры укладки ТЗМ по схеме "кровельной" намотки следующие: скорость намотки равна 2,5... 15,0 м/мин, натяжение лент 5... 10 Н/см от ширины и не превышает 20 % от разрывной нагрузки на ленту. Шаг намотки в зависимости от ширины используемой ленты составит 2,0...3,5 мм/об.
Дата добавления: 2018-05-02; просмотров: 1171; Мы поможем в написании вашей работы! |
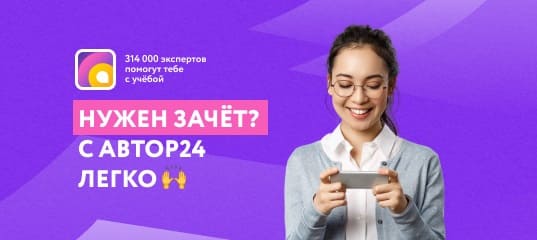
Мы поможем в написании ваших работ!