Характеристики клеев и клеевых соединений для склеивания элементов оправки
Показатель | К-153 | Водорастворимый на основе эпокситриа- зольной смолы (ЭТС) |
Жизнеспособность, ч (порции до 3 кг) Время отверждения, ч, при температуре 15...35 °С, не менее Прочность при сжатии отвержденного клея, МПа, не менее Прочность склеивания материала оправок при отрыве, Мпа Размываемость оправки горячей водой Характер разрушения оправки | 0,5 16 30 5-8 Не размывается Разрушение по материалу оправки | 0,5 24 20 5-7 Размывается Разрушение по материалу оправки |
В соответствии с принципом установки элементов оправки на валу используют торцевое или радиальное базирование, которое исключает взаимные перекосы торцевых поверхностей
фланцев корпуса, днищ, цилиндрических элементов. Для устранения люфтов, зазоров цилиндрических элементов применяют их клиновое соединение с втулками 6, приваренными на валу.
В конструкцию оправки (см. рис. 6.5) входят элементы 3 и 8, обеспечивающие изготовление в одном технологическом процессе УС ("юбок"). Эти узлы изготавливают после намотки основной СО корпуса в форме второго кокона ("ложного" днища) методом спирально-кольцевой намотки с подкреплением тканью. После отверждения "ложные" днища отрезаются, в результате чего формируются "юбки" (см. рис. 6.4).
Для обеспечения требуемых геометрических размеров оправки необходима ее механическая обработка после окончательной сборки.
|
|
Песчано-полимерная часть оправки после отверждения намотанной СО вымывается на специальных вертикальных стендах при подаче пара (Т = 90...100 °С) в течение 4...5 ч либо воды с температурой более 80 °С под напором в течение 1...2 ч. Технологическая схема изготовления оправки показана на рис. 6.6.
Рис.6.6. Технологическая аппаратурная схема изготовления оправки |
Приготовление формовочной смеси
418
27*
419
6.1. Технология изготовления корпуса РДТТ
При выборе типа оправки исходят из того, что допустимые радиальные давления от усилий технологического натяжения ЛПФ при намотке не должны превышать 20 % рабочего давления в корпусе двигателя, а допустимые радиальные деформации при намотке составляют 0,5 мм. Композиционные составы, используемые для изготовления вымываемых оправок, приведены в табл. 6.4. Общий вид оправки показан на рис. 6.7.
Рис.6.7. Общий вид оправки для намотки корпуса РДТТ
Таблица 6.4 Рецептура и физико-механические свойства песчано-смоляных оправок
Свойства | Материал | оправки |
Содержание выплавляемой оправки, | ||
масс, доля | ПВС 2-3 Песок 100 | ЭТС-15 УП 605-3 Песок 100 Бура-3 |
Режим термообработки: | ||
температура, °С | 90-120 | 110-150 |
время, ч | 3 | 8 |
Прочность при сжатии, МПа: | ||
при температуре 20 °С | 27 | 100-130 |
при температуре 150 °С | 5 | 25-26 |
Модуль упругости, ГПа: | ||
при сжатии | 8,5 | 20-22 |
при растяжении | 10,1 | 18,8 |
Время гидролитической деструкции образца разме- | ||
ром 1,5 х 1 х 1 см2, мин, при температуре 100 °С | 10 | 17 |
6. ПРОЦЕССЫ ИЗГОТОВЛЕНИЯ КОНСТРУКЦИЙ ИЗ КОМПОЗИТОВ
|
|
Технологические режимы намотки
Технологический режим формования определяется рядом параметров, которые обусловливают качество производимых корпусов. К таким параметрам относятся: технологическое натяжение ЛПФ при намотке; контактное давление формования (контактное давление на наматываемую поверхность); температура ЛПФ; скорость намотки ленточного полуфабриката; температурно-влажностные характеристики, запыленность и загазованность производственного помещения.
Технологическое натяжение предназначено для создания натяжения в гибкой вантовой системе формируемой оболочки с целью придания ей конструктивной жесткости и прочности, а также для создания технологического натяга в системе станок - приспособление - оправка — ЛПФ, без которого невозможно обеспечить ни кинематические, ни динамические условия намотки арматуры на оправку по заданным траекториям, ни добиться устойчивости и повторяемости результатов намотки. Технологическое натяжение определяется методом формования, кривизной формуемой поверхности, типом ЛПФ, спецификой оборудования и другими факторами. Для каждого конкретного случая оно зависит от типа материала, его определяют расчетом и уточняют экспериментально. Например, для стеклопластиков практически используемые значения натяжения Т0 лежат в диапазоне 0,1 ТP < Т0 < 0,2 ТP где Т0 - натяжение, а ТP - разрывная сила ЛПФ.
|
|
Контактное давление формования предназначено для создания натяга в технологической системе оболочка — оправка, т.е. на границе контакта наматываемого ЛПФ и формующей поверхности оправки (а затем на границе ранее сформированных слоев стенки оболочки). Контактное давление обеспечивает уплотнение наматываемой структуры, заданную ей плотность, отжим избытка связующего и вымывание воздушных включений (в "мокром" способе формования), слипания и адгезию связующего (при "сухом" методе формования). Контактное давление зависит от тех же факторов, что и Т0, и не должно быть ниже 0,049 МПа. Наибольшее его значение ограничивается только опасностью передавливания хрупких армирующих волокон и разрушения технологической оправки.
|
|
420
421
6.1. Технология изготовления корпуса РДТТ
Для создания и управления технологическим натяжением используют различные технологические приемы и устройства: торможение ЛПФ при помощи регулируемых тормозных устройств, создание натяга в волокнах с помощью разжимных, надувных оправок и т.п. (см. гл. 2). Создавать контактное давление и управлять им можно с помощью специальных при-катных устройств, посредством обжимных, наружных рубашек (канаты, ленты), внешнего гидростатического давления и т.п. При малых и средних диаметрах корпусов необходимые значения контактного давления N можно обеспечить с помощью создаваемого технологического натяжения:
q=(N-T0)/R (6.1)
где R — радиус криволинейной поверхности.
С увеличением диаметра формуемых изделий значение контактного давления при оптимальном значении T0 снижается и требуются обязательные дополнительные устройства для его поддержания на требуемом уровне. Так, например, при намотке крупногабаритных корпусов из органопластика применение прикатных роликов позволяет повысить прочность органоплас-тиковых стенок на 5...8%, а модуль упругости — на 4—5%.
Температура формования Tф является параметром режима формования, с помощью которого управляют свойствами ЛПФ в процессе намотки оболочки корпуса. Варьируя Tфизменяют агрегатное состояние и вязкость связующего, регулируют его адгезионные и аутоадгезионные свойства, уменьшают пористость и увеличивают плотность изготавливаемой конструкции. Нагревание ЛПФ осуществляют с помощью контактного обогреваемого ролика, газодинамических и радиационных (инфракрасных) нагревателей и т.д. Оптимальная температура формования зависит в каждом конкретном случае от рецептуры применяемого связующего, его технологического состояния, силовых параметров режима формования, скорости намотки.
Скорость намотки характеризуется принятым методом формования, кинематической схемой намотки, совмещенностью операций формирования ЛПФ и намотки заготовки изделия, возможностями намоточного оборудования. Для отечественно-
6. ПРОЦЕССЫ ИЗГОТОВЛЕНИЯ КОНСТРУКЦИЙ ИЗ КОМПОЗИТОВ
го оборудования при "мокрой" намотке оболочек наибольшая скорость подачи ЛПФ составляет 24 м/мин.
Дата добавления: 2018-05-02; просмотров: 798; Мы поможем в написании вашей работы! |
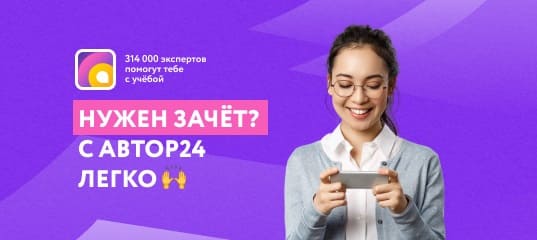
Мы поможем в написании ваших работ!