Экспериментальное определение удельной теплоемкости
Сущность экспериментального измерения удельной тепло емкости методом "смешения" состоит в равномерном прогреве (или охлаждении) испытуемого образца материала известной массы до заданной температуры и измерении путем калори-метрирования поглощенного (или отданного) количества теп лоты, отнесеннного к одному градусу температуры нагрева или охлаждения образца к единице массы.
В калориметрический сосуд до определенного уровня, обес печивающего покрытие ртутного шарика термометра, наливают дистиллированную воду ст = 1 Дж/(кг-К). Массу т воды, численно равную ее тепломкости, следует определить с точ-ностью до 0,1 г.
Калориметрический сосуд с водой помещают в наружным сосуд калориметрической установки и проверяют центровку мешалки. При работе мешалка не должна задевать стенок калориметрического сосуда, термометра и крышки калориметра.
Взвешенный с точностью до 0,01 г образец материала встав ляют в медную трубку, которую устанавливают в термостате или криостате (см. рис. 5.21 или 5.22). Процесс нагревании воды или охлаждения охлаждющей смесью необходимо контролировать ртутным или спиртовым термометром соответст венно.
С момента закипания воды (или достижения охлаждающей смесью требуемой температуры) образец следует выдерживать при этой температуре в течение одного часа. Этого времени достаточно для полного равномерного прогрева образца до заданной температуры.
|
|
За 15...20 мин до окончания термостатирования или крио статирования образца необходимо включить мешалку калори метра и замерить температуру воды в калориметрическом сосуде. Измерение следует начинать при температуре воды и калориметре на 2...3 °С ниже или выше комнатной. Изменении температуры воды в калориметре при работающей мешали следует фиксировать по показаниям калориметрического тер мометра через каждые 3...5 мин и заносить в таблицу.
5. МЕТОДЫ ИСПЫТАНИЙ И КОНТРОЛЬ КАЧЕСТВА КОНСТРУКЦИИ
|
По окончании часовой выдержки образца в термостате (или криостате) необходимо открыть крышку калориметра, зафиксировать начальную температуру Т0 воды в калориметре, остановить мешалку, быстро переложить из медной трубки в калориметр термостатированный или криостатированный образец и отметить этот момент времени θ в таблице для последующего определения точки А при построении графиков рис. 5.23 и рис. 5.24. Закрыть крышку калориметра и сразу после сбрасывания образца включить мешалку и продолжать измерения температуры через 2...3 мин в течение 10...15 мин, а после скачка температуры — через 5 мин в течение 40...45 мин. На этом калориметрический опыт заканчивается.
|
|
Рис. 5.24.График расчета с криостатированного образца |
Рис. 5.23.График расчета ст термостатированного образца
Для нахождения основного результата калориметрического опыта (калориметрической разности температуры ∆T) по данным таблицы на миллиметровую бумагу следует нанести точки для построения графиков (см. рис. 5.23 и 5.24) соответственно для случаев термостатированного или криостатированного образцов. По экспериментальным точкам нужно провести линии, отметить начало скачка температуры (точка А) и на графиках определить точку В, соответствующую моменту достижения равновесной температуры θ калориметра с образцом в конце опыта.
386
25*
387
5.7. Определение тешгофизических свойств КМ
5. МЕТОДЫ ИСПЫТАНИЙ И КОНТРОЛЬ КАЧЕСТВА КОНСТРУКЦИЙ
Искомую калориметрическую разность (скачок температуры) ∆Т= T0 -θследует отсчитывать в масштабе по графику как расстояние между точками А и В.
Согласно формуле, численное значение средней удельной теплоемкости испытуемого образца материала на основании данных калориметрического опыта равно
где ∆Т= T0 -θ — калориметрическая разность температур, °С; Т0 — температура воды в калориметре в момент погружении образца, °С; θ — температура в калориметрическом стакат после наступления теплового равновесия между калориметром и испытуемым образцом материала, °С; С — теплоемкость воды в калориметре, кал/°С; т — масса образца материала, г; Ткконечная температура нагрева или охлаждения образца перед погружением его в калориметр, °С.
|
|
Относительная погрешность измерений не должна превышать 2...3 %.
Статистическую обработку результатов испытаний материалов с определением средних арифметических значений удельной теплоемкости, среднеквадратичных отклонений и коэффициентов вариации следует проводить по известным формулам. Окончательные результаты испытаний представляют в виде
где Хсm — среднее арифметическое значение удельной теплоём-кости; S — среднеквадратичное отклонение.
Определение теплопроводности
Образец представляет собой диск диаметром 12 + 0,1 мм и толщиной 4 ± 0,1 мм. Допускается применение образцов толщиной 6 ±0,1 мм при условии предварительной тарировки прибора по образцам-эталонам толщиной 6 мм. При невозможности изготовления образцов номинальных толщин допускает-
388
ся применение образцов толщиной от 2 мм и более с доведением толщины до номинальной путем приклеивания металлического диска с диаметром, равным диаметру образца.
|
|
Теплопроводность оценивают как среднюю величину по измерениям на серии образцов, взятых от партии материала. Количество образцов должно быть не меньше шести.
Измерения следует проводить на приборе типа "Лямбда" или его аналогах. Прибор предназначен для определения теплопроводности стационарным методом при комнатной температуре. Диапазон измеряемых значений теплопроводности 0,1... 2,5 Вт/(м-К). Погрешность измерения ±5%.
Образцы для измерения теплопроводности должны поступать в воздушно-сухом состоянии. Для кондиционирования влажных образцов перед испытанием их прогревают при температуре 50...70 °С в течение 25...35 мин с последующим охлаждением и выдержкой в эксикаторе над влагопоглотителем в течение 2...3 ч.
Перед проведением измерений торцевые поверхности образца должны быть смазаны тонким слоем смазки типа ЦИАТИМ.
|
Вычислить средние значения теплопроводности материала по п образцам (п > 5): |
|
Окончательный результат измерений представить в виде |
|
389 |
Для каждого образца в соответствии с порядком проведения измерений следует определить по показаниям прибора значение теплопроводности λi. При отличии толщины h образца от номинальной hном следует пересчитать отсчитанные по прибору значения λiизм по соотношению
5.8. Неразрушающие методы контроля деталей и узлов из КМ
где λ — среднее арифметическое значение; S — среднеквад-ратичное отклонение.
5.8. Неразрушающие методы контроля деталей и узлов из композитов
Структурные дефекты и их влияние на свойствакомпозитом
Оптимальные для конкретных условий эксплуатации физи-ко-механические и теплозащитные свойства композитов прак-тически полностью достигаются формированием заданной структуры и зависят от степени ее соответствия расчетным параметрам. Поэтому наличие структурных нарушений (дефек-тов) может стать решающим фактором, определяющим рабо тоспособность конструкций.
Важной особенностью структурных дефектов слоистых и пространственно-армированных композитов является то, что наряду с дефектами, присущими традиционным материалам (трещины, раковины, поры, рыхлоты, посторонние включении и т.д.), могут образовываться дефекты, характерные только для данного вида материала, связанные с особенностями структуры армирующего каркаса и методом формирования матрицы. При чем дефекты, возникающие на разных этапах изготовления, существенно различаются.
На стадии изготовления каркасов возникают дефекты, спя занные с отклонениями от расчетных параметров структуры: направления укладки армирующих нитей и жгутов, периодич ности расположения структурных элементов, расстояния между жгутами и пакетами жгутов, объемного содержания жгутов в каждом направлении армирования.
Дефекты, которые образуются на этапе формирования матрицы, связаны в основном с отклонениями от расчетного распределения плотности конечного материала, хотя и не исключены нарушения структуры армирующего каркаса, возникаю щие на различного рода подготовительных операциях. На этом этапе возможно образование вследствие нарушения технологи ческих режимов пропитки или насыщения таких дефектов, как раковины, рыхлоты и трещины.
5. МЕТОДЫ ИСПЫТАНИЙ И КОНТРОЛЬ КАЧЕСТВА КОНСТРУКЦИЙ
Дефекты типа "посторонние включения", обычно металлического характера, могут образовываться на каждом этапе изготовления.
Таким образом, на основании проведенных исследований удалось определить характер влияния различных видов структурных дефектов на физико-механические и теплозащитные свойства композиционных материалов.
Наличие различного шага укладки наполнителя вдоль координатных осей может являться одной из причин отличия расчетных значений упругих констант от реальных характеристик материала.
Наличие искривленных волокон в ортогонально-армированных материалах существенно снижает их жесткость при растяжении и сжатии. Создание предварительного натяжения арматуры при изготовлении каркасов способствует некоторому увеличению модулей упругости и прочности в направлении натяжения за счет исключения случайных искривлений жгутов, однако чрезмерное натяжение в одном направлении может вызвать нарушение ортогональности в других.
Уменьшение числа армирующих жгутов в каком-либо направлении, обычно вследствие их припусков или обрывов, приводит к снижению прочности при растяжении.
Повышенная пористость оказывает заметное влияние на модуль упругости в трансверсальном направлении, где содержание волокон мало, а влияние матрицы на формирование жесткости указанного направления весьма значительно.
Дата добавления: 2018-05-02; просмотров: 790; Мы поможем в написании вашей работы! |
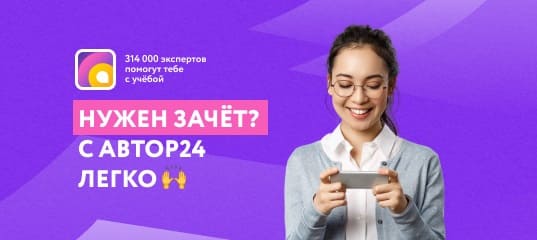
Мы поможем в написании ваших работ!