Изготовление полуфабрикатов теплозащитных материалов
Полуфабрикаты резиноподобных ТЗМ изготавливают на специализированных заводах методом каландрования и поставляют для получения ТЗМ в рулонах. Процесс получения ка-ландрованного полуфабриката ТЗМ состоит из следующих этапов:
изготовление резиновой смеси из компонентов в резино-смесителях или на вальцах, причем резиносмесители имеют
большую производительность;
вальцевание смеси (при изготовлении в резиносмесителях) в пластину толщиной 10...20 мм;
каландрование листов, т.е. продавливание материала в зазоры между цилиндрическими валками до получения определенной толщины.
Каландрованные листы выпускают обычно толщиной от 0,5 до 2 мм, так как более тонкие листы трудно снимать с последнего валка. При изготовлении листов с большей толщиной возможно появление воздушных пузырей вследствие недостаточного давления при большом зазоре между валками. Некоторые материалы имеют и другие ограничения по толщинам, например ТЗМ, наполненные асбоволокном, не выпускаются толщиной меньше 1 мм из-за выкрашивания асбеста.
Специфической особенностью, присущей каландрованным листам, является анизотропия свойств — каландровый эффект. Эта анизотропия возникает вследствие продольной ориентации, которой подвергается материал при проходе в зазорах между валками. Каландровый эффект зависит от температуры каландрования, скорости и фрикции валков, а также от свойств резиновой смеси. С повышением температуры каландровый эффект уменьшается, так как снижается вязкость смеси. Для снятия каландрового эффекта рекомендуется прогревать листы резиновых смесей перед формованием в термостатах при тем-ператере 60...70 °С в течение 1...4 ч. При термостатировании происходит изменение геометрических размеров листов: уменьшается длина и увеличивается толщина. Изменение толщины составляет 10... 15%, что необходимо учитывать при расчете схем набора толщин ТЗМ.
|
|
428
429
6.1. Технология изготовления корпуса РДТТ
Полуфабрикаты ТЗМ имеют ограниченный срок хранения, что связано с протеканием процессов самовулканизации и охрупчивания резиновых смесей. Пастообразные ТЗМ на основе олигомерных низковязких каучуков изготавливают на месте формования покрытий. Для изготовления используются камерные смесители, в основном периодического действия.
Наиболее широко применяют смесители со шнековым устройством. Подготовка компонентов, входящих в состав пастообразных ТЗМ, включает в себя операции измельчения и сушки порошкообразных наполнителей, а также взвешивания всех
компонентов.
Порошкообразные наполнители измельчаются в шаровых мельницах с последующим отделением крупной фракции частиц с помощью различных сит.
|
|
Влага из компонентов удаляется сушкой в термошкафах или вакуумных сушилках. Время сушки определяется экспериментально и зависит от допустимой влажности компонентов, температуры и особенностей оборудования. Режимы сушки некоторых компонентов, входящих в состав ТЗМ, представлены в табл. 6.5.
Таблица 6.5 Режимы сушки компонентов ТЗМ
Материал | Температура сушки, °С | Допустимая влажности % |
Асбоволокно Белая сажа Технический углерод Оксид цинка Древесная мука Фенольные микросферы Стеклянные микросферы | 110 150 110 110 115 100 110 | 1,0 1,0 0,2 0,2 2,5 3,0 1,0 |
Компоненты дозируются с помощью весов или дозаторов, в некоторых случаях используют объемную дозировку жидких и сыпучих материалов.
430 |
Качество полуфабриката обеспечивается равномерностью распределения компонентов материала и контролем времени
6. ПРОЦЕССЫ ИЗГОТОВЛЕНИЯ КОНСТРУКЦИЙ ИЗ КОМПОЗИТОВ
смешения, устанавливаемым экспериментально в зависимости от вязкости каучука, температуры и применяемого оборудования.
Подготовка поверхности закладных деталей и оснастки
Качество поверхности определяет прочность соединения деталей, а следовательно, и работоспособность изделия в целом. Процесс подготовки поверхности состоит из операций механической и химической обработки.
|
|
Механические методы предназначены для удаления окалины, ржавчины, заусенцев и создания требуемой шероховатости поверхности. Известно, что адгезия различных покрытий находится в прямой зависимости от истиной поверхности склеивания, определяемой шероховатостью. Существует оптимальный параметр шероховатости для разных подложек. Так, для крепления металлов и стеклопластиков с резинами необходим параметр шероховатости Rz — 20...80 мкм.
К механическим методам создания шероховатости относятся струйная обработка металлической дробью, электрокорундом или другими абразивами, зачистка шлифовальной шкуркой или металлическими щетками. Существуют дробеструйная и дробеметная обработка, которые различаются способом разгона абразива. Дробеструйные аппараты разгоняют абразив до нужной скорости сжатым воздухом. Дробе-метные аппараты, работающие на метательном эффекте, в несколько раз производительнее дробеструйных. Для цехов и участков ТЗМ, имеющих большую номенклатуру изделий, но относительно малый объем производства, преимущества дробеструйных аппаратов, т.е. простота конструкции и гибкость технологии, очевидны.
|
|
Струйную обработку применяют для деталей, толщина стенок которых выдерживает воздействие струи типа "мембрана". Для нежестких деталей поверхности зачищают шлифовальной шкуркой с зернистостью 40...110 мкм. Поверхности деталей из неметаллических материалов (пластики, резины) обрабатывают
431
6.1. Технология изготовления корпуса РДТТ
до удаления глянца. Пластмассовые детали после механической обработки пригодны к сборке.
Кроме струйной обработки, а также в комбинации с нейдля тонкостенных деталей и деталей из некоторых сплавов применяют химические методы подготовки поверхности, на пример травление для титана, вольфрама и молибдена. После травления обязательна промывка деталей и сушка.
Обработанные поверхности деталей подвергают обезжириванию с целью удаления масляных и других загрязнений. Процесс обезжиривания основан на коллоидно-химическом растворении загрязнений в органических растворителях (бензине, ацетоне, трихлорэтилене) или эмульгировании в растворах едких щелочей. Характеристики органических растворителей представлены в табл. 6.6.
Таблица 6.6 Свойства органических растворителей
Раство- | Плотность, г/см3 | Температура | Температура | Лету- | Основные |
ритель | кипения, °С | замерзания, °С | честь, % | особенности | |
Ацетон | 0,791 | 56,2 | -17,8 | 2,1 | Удовлетворительная очищающая способность Опасность воспламенения |
Бензин | 0,722 | 80,0 | - | 3,5 | То же |
Бензол | 0,879 | 80,0 | -11,0 | 3,0 | Высокая токсичность |
Дихлор- | Хорошая очищающая | ||||
этан | 1,260 | 83,5 | — | 4,1 | способность |
Трихлор- | Недостаточная | ||||
этилен | 1,480 | 87,3 | — | 3,8 | стабильность |
Хлорис- | Хорошая очищающая | ||||
тый ме- | способность | ||||
тилен | Экологическое | ||||
(фреон) | 1,340 | 40,0 | - | 1,8 | воздействие |
Четырех- | Отличная очищающая | ||||
хлорис- | способность | ||||
тый угле- | Высокая токсичность | ||||
род | 1,590 | 76,5 | - | 4,0 | |
Уайт- | Низкая очищающая | ||||
спирит | 0,795 | 165 | - | - | способность |
6. ПРОЦЕССЫ ИЗГОТОВЛЕНИЯ КОНСТРУКЦИЙ ИЗ КОМПОЗИТОВ
В последнее время большое внимание уделяют разработке и применению водных моющих средств. Водные составы по сравнению с органическими растворителями дешевле, они негорючие, нетоксичные, однако длительность обезжиривания водными составами значительно выше.
В мелкосерийном производстве наиболее широко в силу простоты и универсальности распространен метод обезжиривания протиркой салфетками, смоченными растворителями, с последующей сушкой в условиях цеха. Время сушки зависит от материала и составляет для металлов 10... 15 мин, для пластмасс — 30...40 мин. В серийном производстве применяют механизированные способы обезжиривания окунанием, струйным обезжириванием и т.д.
Подготовленные к склеиванию поверхности имеют ограниченное время до нанесения клея, например: для стальных деталей не более 12 ч, для деталей из коррозионно-стойкой стали и титановых сплавов не более 24 ч, для деталей из алюминиевых сплавов не более 6 ч, для деталей из резины не более 48 ч, для стекло-, асбо-, углепластиков не более 96 ч. Для увеличения времени хранения подготовленных поверхностей используют их специальную защиту (консервацию) с помощью пленок, прорезиненных тканей, специальных клеевых подслоев. В этих условиях время хранения деталей может быть увеличено до 30 сут, а иногда и более.
Для склеивания деталей из резины на основе неполярных каучуков разработан метод подготовки поверхности путем ультрафиолетового облучения. Суть метода состоит в окислительных процессах, происходящих в поверхностных слоях материалов под воздействием образующегося при ионизации воздуха озона. В качестве источника излучения используют ртутно-кварцевые лампы. Условия облучения (мощность лампы, время облучения, расстояние до источника) устанавливают экспериментально путем испытания склеиваемых образцов.
Марки резин и рекомендуемые клеевые композиции для склеивания резины и металлов приведены в табл. 6.7.
432
28-243
433
6.1. Технология изготовления корпуса РДТТ
Таблица 6,7
Дата добавления: 2018-05-02; просмотров: 547; Мы поможем в написании вашей работы! |
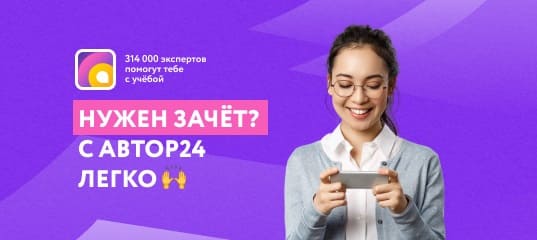
Мы поможем в написании ваших работ!