Расчёт спусковой массы ПЛ. Расчёт трудоёмкости
3.1 Расчёт спусковой массы ПЛ
3.1.1 Масса обшивки ПК на длине одной шпации определяется по формуле
Mобш=π·dпк·l·t1·ρ, т (3.1)
где, dпк – диаметр прочного корпуса, м;
l – длина шпации, м;
t1 – толщина обшивки, м;
ρ – плотность материала, 7,85 т/м3;
mобш=3,14·10,9·0,65·0,052·7,85=9 т.
3.1.2 Масса шпангоута определяется по формуле
mшп=Vшп·ρ, т (3.2)
где, Vшп – объём шпангоута, м3;
ρ – плотность материала, 7,85 т/м3;
mшп=0,91·7,85=7 т.
3.1.3 Масса цилиндрической вставки определяется по формуле
mцв=(mобш+mшп)·Lцв/l, т (3.3)
где, mобш – масса обшивки ПК, т;
mшп – масса шпангоута, т;
Lцв – длина цилиндрической вставки, м;
l – длина шпации, м;
mцв=(9+7)·48,1/0,65=1203 т.
3.1.4 Масса сферической части 1 отсека определяется по формуле
mсфер. 1 отс.=(mобш+mшп)·k·0,7, т (3.4)
где, mобш – масса обшивки ПК, т;
mшп – масса шпангоута, т;
k – количество шпангоутов, шт.;
0,7 – коэффициент расчёта массы оконечностей ПК;
mсфер. 1 отс.=(9+7)·8·0,7=91 т.
3.1.5 Масса конической части 4 отсека определяется по формуле
Mкон. 4 отс.=(mобш+mшп)·k·0,7, т (3.5)
|
|
где, mобш – масса обшивки ПК, т;
mшп – масса шпангоута, т;
k – количество шпангоутов, шт.;
0,7 – коэффициент расчёта массы оконечностей ПК;
Mкон. 4 отс.=(9+7)·8·0,7=91 т.
3.1.6 Масса 5 и 6 отсеков определяется по формуле
Mкон. 5 и 6 отс.=(mобш+mшп)·(k5+k6)·0,7, т (3.6)
где, mобш – масса обшивки ПК, т;
mшп – масса шпангоута, т;
k5, 6 – количество шпангоутов 5 и 6 отсеков, шт.;
0,7 – коэффициент расчёта массы оконечностей ПК;
Mкон. 5 и 6 отс.= (9+7)·(20+20)·0,7=455 т.
3.1.7 Масса легкого корпуса определяется по формуле
mлк=mобш·Lmax·0,18, т (3.7)
где, mобш – масса обшивки ПК, т;
Lmax – максимальная длина ПЛ, м;
0,18 – коэффициент расчёта массы ЛК;
mлк= 9·108·0,18=177 т.
3.1.8 Масса поперечных переборок определяется по формуле
mпп=mобш·n·0,4, т (3.8)
где, mобш – масса обшивки ПК, т;
n – количество поперечных переборок, шт.;
0,4 – коэффициент расчёта массы поперечных переборок;
mпп= 9·5·0,4=18 т.
3.1.9 Масса ограждения выдвижных устройств определяется по формуле
|
|
mву=mлк·0,1, т (3.9)
где, mлк – масса легкого корпуса, т;
0,1 – коэффициент расчёта массы ограждения выдвижных устройств;
mлк= 177·0,1=18 т.
3.1.10 Масса внутренних конструкция определяется по формуле
mвк=mпк·0,1, т (3.10)
где, mпк – масса ПК, т;
0,3 – коэффициент расчёта массы внутренних конструкций;
mвк= 1858·0,3=557 т.
3.1.11 Масса механизмов, систем и оборудования определяется по формуле
mмех=mкорп·0,1, т (3.11)
где, mкорп – масса корпуса, т;
2,5 – коэффициент расчёта массы внутренних конструкций;
mмех=2609·2,5=6523 т.
3.1.12 Сумма спусковой массы ПЛ составляет
Мпл=1203+91+91+455+18+177+18+557+6523=9133 т
3.2 Расчёт трудоёмкости
3.2.1 Расчёт трудоемкость производится по удельным нормативам трудоёмкости и представлен в таблице 4.1.
Таблица 4.1 – Расчёт трудоёмкости
Наименование | Масса, т | Удельная трудоёмкость, нормо-ч | Трудоёмкость, нормо-ч | ||
Изготовление деталей корпуса | 9 133 | 25 | 228 325 | ||
Сборка и сварка секций корпуса | 9 133 | 80 | 730 640 | ||
Формирование корпуса на стапеле | 9 133 | 75 | 684 975 | ||
Изготовление труб | 186 | 900 | 167 193 | ||
Монтаж механизмов и трубопроводов | 2 136 | 86 | 183 726 | ||
Достройка | 372 | 74 | 27 494 | ||
Испытания | 1 858 | 10 | 18 577 | ||
Изделия машиностроения, 15% | - | - | 306 140 | ||
Итого
| 2 347 070 |
Стапельное расписание. Размещение производства на стапеле
4.1 Стапельное расписание
Стапельное расписание является графической характеристикой загрузки построечных мест и достроечных набережных.
Стапельное расписание составляют в виде ленточных графиков с разбивкой цикла постройки ПЛ на следующие периоды:
а) Заготовительный – совокупность работ цехов верфи и машиностроения, объединенная системой планово-учетных единиц (цехо-этапы, технологические комплекты) в пределах между типовыми событиями: «Начало изготовления деталей» и «Закладка на стапеле первого по счету блока произведена».
б) Стапельный – совокупность работ цехо-этапов и технологических комплектов между типовыми событиями: «Закладка на стапеле произведена» и «Спуск ПЛ на воду осуществлен».
в) Достроечный – совокупность работ между типовыми событиями: «Спуск осуществлен» и «Швартовные испытания (ШИ) начаты».
|
|
г)Сдаточный – совокупность работ между типовыми событиями («ШИ начаты» и «Приемный акт подписан»).
При расчете стапельного расписания продолжительность (в %) периодов для модульно – агрегатного метода постройки принимаем следующим образом: заготовительный – 30%, стапельный - 60%, достроечно-сдаточный – 10%.
Стапельное расписание представлено в приложении В. Продолжительность постройки представлена в таблице 4.1.
Таблица 4.1 – Продолжительность постройки ПЛ
№ заказа | Продолжительность постройки (мес.) | ||||
Общая | Периоды | ||||
Заготовительный | Стапельный | Достроечный | Сдаточный | ||
1 | 39 | 11,7 | 23,4 | 2,7 | 1,2 |
2 | 32 | 9,6 | 19,2 | 2,2 | 1 |
3 | 32 | 9,6 | 19,2 | 2,2 | 1 |
4 | 32 | 9,6 | 19,2 | 2,2 | 1 |
5 | 32 | 9,6 | 19,2 | 2,2 | 1 |
6 | 32 | 9,6 | 19,2 | 2,2 | 1 |
4.2 Размещение производства на стапеле
Схема размещения производства дает представление о размещении ПЛ на стапеле в процессе постройки всей серии заказов.
При разработке схемы необходимо учитывать следующие условия:
а) расположение ПЛ на схеме: нос - справа, корма - слева. При этом головной заказ размещается у выводных ворот кормой к воротам;
б) по стенкам строительного дока (эллинга) должны быть предусмотрены стационарные построечные эстакады (ширина не менее 3 м), на всех ярусах которых размещаются слесарно-станочное оборудование, сварочные установки, коммуникации, испытательные стенды;
в) между выводными воротами и кормой ПЛ предусмотреть зазор 12-20 м (мертвая зона для работы большегрузных кранов);
г) расстояние от стенки дока до обшивки наружного корпуса ПЛ должно быть не менее 3 м (при отсутствии построечной эстакады);
д) габариты сборочно-монтажных единиц (модулей) принимать равным 0,6 от длины отсека, в который они загружаются через открытый торец;
е) при проведении ГИ ПК предусмотреть зоны безопасности - 15 м в нос и корму от испытываемого объема;
ж) для монтажа гребных валов (движительного комплекса) предусмотреть в кормовой части площадку размерами: L = 10 м. Аналогичная зона должна быть предусмотрена в носовой части для монтажа технических изделий.
Схема размещения производства на стапеле представлена в приложении Г.
Дата добавления: 2018-04-15; просмотров: 525; Мы поможем в написании вашей работы! |
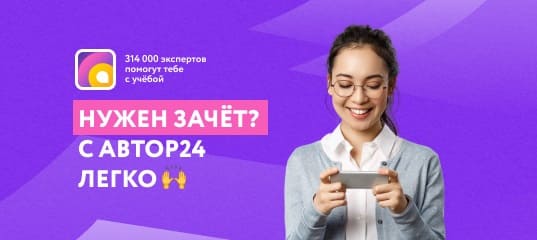
Мы поможем в написании ваших работ!