Мокрое (адсорбционное) пылеулавливание. Схема насадочного скруббера.
Мокрая очистка газа желательна в тех случаях, когда необходимо охлаждение газа независимо от его очистки. Путем смачивания и поглощения частиц пыли жидкостью достигается высокая степень извлечения пыли из газа.
При охлаждении влажного газа водяные пары конденсируются на содержащихся в нем пылинках, вследствие чего увеличивается масса пылинок и облегчается выделение их из газа. Выделение пыли в мокрых пылеуловителях происходит под действием сил тяжести (при прямолинейном движении газа через аппарат) или под действием сил инерции (при резком изменении направления газового потока), или под действием центробежных сил (при вводе газа в аппарат с большой скоростью по касательной к внутренней поверхности аппарата). В последнем случае достигается наиболее тщательная очистка газа от пыли. Смачивание и поглощение пыли водой производится при стекании воды пленкой по внутренним стенкам аппарата, при разбрызгивании воды по всему объему аппарата или комбинированным способом.
Предварительную очистку газов (в сочетании с охлаждением их) проводят в полых скрубберах-башнях круглого или прямоугольного сечения (рис.8.8).
Запыленный газ движется в скруббере снизу вверх, поглощающая жидкость распыляется форсунками, которые устанавливаются на разных уровнях; при этом все сечение скруббера перекрывается распыляемой жидкостью. Скорость газа в поперечном сечении полого скруббера не должна превышать 1-1,5 м/с.
|
|
Рис.8.6. Струйный скруббер Вентури
Несколько лучшая, чем в полых скрубберах, очистка газа достигается в скрубберах с насадкой. В качестве насадки используют кусковой кокс и кварц. Орошение насадки производится через распределительные устройства. Скорость газа в насадочных скрубберах составляет 0,8-1,25 м/с. Кроме полых и насадочных скрубберов, в качестве гидравлических пылеуловителей используют центробежные скрубберы, струйные скрубберы Вентури и пенные пылеуловители.
Центробежный скруббер работает следующим образом. Запыленный газ поступает в аппарат через патрубок по касательной к стенке корпуса и приобретает интенсивное вращательное движение. Под действием центробежной силы частицы пыли отбрасываются к стенкам скруббера и смываются пленкой воды, стекающей по стенкам. Орошающая вода распределяется по стенкам через сопла. Очищенный газ удаляется через верхнее отверстие.
Достоинства центробежного скруббера: 1) высокая степень очистки в поле центробежных сил при турбулентном движении газа и жидкости; 2) низкое гидравлическое сопротивление; 3) простота конструкции и экономичность эксплуатации.
|
|
Одним из эффективных аппаратов для мокрой газоочистки является струйный скруббер Вентури (рис. 8.6).
Вода вводится в трубу 1 через отверстия в ее горловине 2 под избыточным давлением 0,3-1 атмосферы и тонко распыляется движущимся с большой скоростью потоком газа, который протягивается через установку при помощи вентилятора. Скорость газа в горловине составляет 60-70 м/с и более. В расширенной части трубы скорость потока снижается, тонко распыленная жидкость увлажняет и поглощает частицы пыли. Вследствие этого капельки жидкости укрупняются и могут быть выделены из газового потока в циклонном сепараторе 3. Вода отделяется от шлама в отстойнике 4 и вновь подается в скруббер. В скруббере Вентури удается удалить из газа до 99% тонкодисперсной пыли (0,5-1,5 мкм).
Высокая степень очистки топочных газов достигается в пенном пылеуловителе (см. рис.8.7).
Рис.8.7. Пенный пылеуловитель
Газы поступают через патрубок 1 и, проходя через мелкие отверстия решетки 2, вспенивают воду, подаваемую через штуцер 3. Благодаря значительной поверхности пена хорошо поглощает частицы золы. Отделившиеся от газа частицы золы уходят с водой, основная часть которой (≈80%) удаляется в виде пены через регулируемый порог 4. Остальная вода сливается через решетку, а также испаряется и уносится в виде брызг газами.
|
|
Рис.8.8. Схема скруббера
Подвижное пенное состояние жидкости обеспечивается при скорости восходящего потока газа 0,7-3,5 м/с. Расход жидкости при этом составляет 0,2-0,3 л/м3 очищенного газа.
Электрофильтры.
Электрический метод очистки является наиболее совершенным. Электрофильтры обеспечивают высокую степень очистки, достигающую 99%, имеют небольшое гидравлическое сопротивление, имеют возможность отделения частиц размером менее 10 мкм. В электрофильтрах можно очищать химически агрессивные газы и газы с относительно высокой температурой. Электрофильтры делятся на две группы: трубчатые и пластинчатые. Последние могут быть вертикальными и горизонтальными.
Трубчатый электрофильтр представляет собой камеру, в которой установлены осадительные электроды, выполненные в виде круглых или шестигранных труб. В качестве коронирующих электродов служат проволоки, натянутые по оси осадительных труб.
В пластинчатом электрофильтреосадительные электроды
представляют собой параллельные гладкие металлические листы или натянутые на рамы сетки, между которыми подвешены коронирующие электроды в виде проволок.
|
|
Действие электрофильтра основано на ионизации газа за счет искрового разряда, возникающего под действием приложенного электрического напряжения U.
При напряжении U=65 - 70 кВ под действием электрического поля молекулы газа ионизируются, разделяются на положительно заряженные ионы и электроны,
которые начинают перемещаться вдоль силовыхлинийэлектростатическогополя, напряжение частиц при соударении с инертными молекулами газа расщепляет и их, газ полностью ионизируется. При этом наблюдается потрескивание и слабое свечение газа (корона) вокруг проводника, который носит названиекоронирующего
Рис. 8.5.Схема электрофильтра 1-проволока (стержень); 2-осадительный электрод; 3-проходной электрод; 4-заземление |
,
осадительному электроду (рис. 8.5).
Осадительный электрод присоединяется к положительному полюсу, а к коронирующему электроду через проходной изолятор 3 подводится постоянный ток отрицательного знака, потому что отрицательно заряженные ионы движутся с большей скоростью (в 1,37 раза), чем положительные. При движении в запыленном газе или тумане отрицательные ионы сообщают заряд пылинкам или капелькам жидкости и увлекают их к осадительным электродам. Подойдя к осадительному электроду, частицы пыли отдают ему свои заряды и оседают на нем.
Осевшие частицы сбрасываются с осадительного электрода под действием собственной тяжести или при встряхивании.
Положительно заряженные электроды имеют заземление 4. Объем и сечение камеры электрофильтра определяют исходя из того, что практически время пребывания газа в камере принимают равным 2-3,5 с.
Такая продолжительность считается достаточной для осаждения пыли на осадительном электроде.
Электрофильтры работают только на постоянном электрическом токе, так как при переменном токе заряженные частицы быстро меняют направление своего движения, вследствие чего часть их не успевает осесть на электродах и выносится с газом из электрофильтра. Питание электрофильтров существляется постоянным током высокого напряжения (40-75 кВ).
Пластинчатые питатели.
Пластинчатые питатели применяются для равномерной подачи материалов в камнедробилки, в дробильные вальцы и т. п. машины.
Различают питатели тяжелого типа, предназначенные для подачи материала в кусках размером до 1300 мм, и нормального типа для подачи кусков размером до 400—500 мм. Питатели тяжелого типа допускают падение на них материала со сравнительно большой высоты.
Пластинчатый питатель (рис. 186) представляет собой непрерывную ленту из звеньев / с бортами 2 в звеньях, соединенных между собой стяжками (пальцами) 3, на концах которых установлены ролики 4, входящие во впадины приводных 5 и натяжных 6 звездочек. Лента натягивается при посредстве двух винтов 7 и поддерживается верхними 8 и нижними 9 барабанами.
Привод питателя состоит из электродвигателя, клиноременной передачи, редуктора, цепной передачи, передающей вращение звездочке 10 и далее через зубчатую цилиндрическую передачу 11 приводному валу 12.
Питатели устанавливаются наклонно, при этом стандартный угол принят равным 15°. Бункер для питателя изготовляется с таким расчетом, чтобы задняя его стенка имела угол наклона в 55°, а боковые стенки — 48°. Величины углов могут несколько отклоняться от указанных с тем, однако, условием, чтобы угол пересечения задней и боковой стенок был бы не меньше угла естественного откоса.
Основными размерами пластинчатого питателя являются ширина ленты и высота бортов.
Выбор размеров ленты производится с учетом потребной производительности и объемной массы материала, величины рабочей скорости, размеров кусков материала, степени равномерности питания и зависящего от нее коэффициента заполнения сечения ленты.
Рабочая скорость ленты принимается для питателей тяжелого типа в пределах 0,05—0,25 м/сек, а для питателей нормального типа — 0,025— 0,15 м/сек.
Производительность пластинчатого питателя с брртами подсчитывается по формуле
кг/ч, (750)
гдеВ— расстояние между бортами, м;
h— высота бортов, м;
v—скорость движения ленты, м/сек;
γо6— объемная масса материала, кг/м3;
ψ — коэффициент заполнения сечения ленты, ψ=0,75—0,8.
При выборе ширины ленты необходимо учитывать величину наибольшего размера поступающих кусков. Если количество особо крупных кусков не превышает 10% от общей массы, то рекомендуется ширину ленты принимать равной примерно 1,8—2,5 размера наибольших кусков.
Высота бортов практически принимается равной (0,06—0,09) В.
Суммарное тяговое усилие на пластинчатом питателе равно
Wo6щ=W1+W2+W3 н, (751)
где W1 — сопротивление движению груженой ветви, н;
W2— сопротивление движению холостой ветви, н;
W3— сопротивление движению при перегибе цепей на приводных и натяжных роликах.
Для наклонно установленного питателя получим
н, (752)
где q1 — сила тяжести материала, приходящаяся на 1 пог. м ленты, н/м;
q2— сила тяжести 1 пог.мленты, н/м;
L— длина питателя, м;
β — угол установки питателя, град;
ω — коэффициент тяги;
(7б3)
k— коэффициент, учитывающий сопротивление движению от трения реборд роликов о направляющие, k=l,5;
f— коэффициент трения скольжения в ступице ролика, f=0,25;
d— наружный диаметр втулки ролика, м;
μ — коэффициент трения качения роликов по направляющим, μ=0,001 м.
D— диаметр ролика, м;
н, (754)
н.
Мощность электродвигателя будет равна
вт, (755)
где v— скорость движения ленты, м/сек;
η — к. п. д. привода.
Рис. 187. Яшичный подаватель
Второй тип пластинчатого питателя — ящичный, подаватель, применяемый на керамических заводах для приема глины из автосамосвалов или и вагонеток и последующей равномерной подачи ее в перерабатывающие машины,— представлен на рис. 187. Он состоит из пластинчатой ленты 1, ящичного корпуса 2, ведущего 3 и натяжного 4 валов, вала 5 с билами у приводного устройства. Корпус питателя представляет собой сварной каркас прямоугольной формы, обшитый с внутренней стороны металлическими листами. В вертикальных направляющих корпуса установлены шиберы 6, разделяющие корпус на три отсека.
В каждый из отсеков подается по одному компоненту (глина, песок, опилки и т. п.). Шиберы по высоте устанавливаются с таким расчетом, чтобы нижний обрез его вместе с лентой образовывал окно для прохода материала. При этом учитывается, что первое по ходу окно должно пропустить определенное количество массы из первого отсека, второй шибер устанавливается так, чтобы в образованное им окно прошла вся масса, поступающая из первого отсека, плюс порция из второго отсека и т. д.
Пластинчатый транспортер состоит из двух бесконечных тяговых пластинчато-роликовых цепей, к которым приварены плоские поперечные пластины 7. Для предотвращения просыпания массы пластины расположены таким образом, что перекрывают друг друга, а вдоль корпуса подавателя укреплены резиновые полосы, перекрывающие зазор между лентой и корпусом. На ведущем и натяжном валах закреплены по две звездочки для тяговых цепей.
Для разбивания крупных комьев глины служат билы 8.
Привод ящичного питателя осуществляется от электродвигателя через редуктор, клиноременную передачу 9, зубчатую передачу 10 и кулисно-храповой механизм 11. В новейших конструкциях привод выполняется без кулисно-храпового механизма.
Ящичные питатели изготовляются с расстоянием между центрами приводного и натяжного валов в 3,5 и 5 м.
Дата добавления: 2018-04-15; просмотров: 428; Мы поможем в написании вашей работы! |
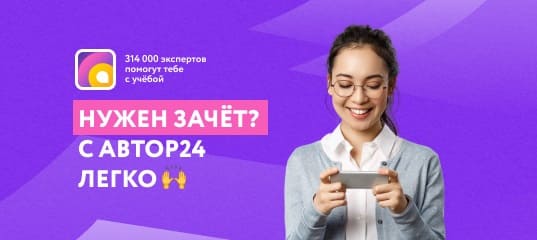
Мы поможем в написании ваших работ!