Производственная программа и ее расчет
Производственная программа - календарный план использования производительных сил с целью осуществления выпуска продукции и услуг в ассортименте и объемах, востребованных товарным спросом и потребностями внутрикорпоративной кооперации, по установленной технологии, однозначно задающей ресурсные потребности.
Целью расчета производственной программы является максимально полное удовлетворение ранжированного спроса путем выбора из альтернативных вариантов производства, технологий при ресурсных ограничениях с учетом переходящих планов за пределами горизонта планирования и существующих обязательств.
Расчет производственной программы производится как для одного предприятия или выделенного подразделения, так и для группы предприятий, осуществляющих согласовано свою производственную деятельность в рамках единой системы планирования.
Производственная программа разрабатывается по предприятию в соответствии с установленными сроками реализации продукции потребителям. Для серийного производства планирование выпуска продукции на протяжении года производится с учетом незавершенного производства на всех стадиях производственного процесса и изменения номенклатуры запускаемых в производство изделий. В целях достижения полной и равномерной загрузки оборудования и рабочих мест предприятие имеет возможность разрабатывать различные варианты производственной программы выпуска продукции во времени.
|
|
Расчет производственной программы производится в едином алгоритмическом блоке вычислений с расчетами следующих планов:
· отгрузка покупателям и заказчикам;
· закупка у поставщиков и подрядчиков;
· движение МТЦ на складах и обеспеченность страховым запасом;
· движение запасов в незавершенном производстве.
Вариант производства определяется выбором из системы альтернатив:
· периоды производства;
· оборудование и установки;
· трудовые ресурсы;
· спецификации и сметы затрат;
· карты замены;
· варианты, технологии изготовления.
Расчет производится с учетом повременных и удельных затрат определяемых в сметах, спецификациях при наличии производительных, материальных и сервисных ресурсных ограничений.
Точение на многорезцовых станках
Довольно большое количество деталей, обрабатывающихся в центрах, специальных патронах и на оправках, со значительным числом ступеней диаметров, обтачивается в автомобильном производстве среднего масштаба на многорезцовых токарных станках.
Основной принцип конструкции многорезцовых станков заключается в том, что они снабжены двумя основными суппортами, способными нести каждый по несколько резцов (откуда и принято их название). Передний суппорт имеет обычно лишь продольную механическую подачу, а задний—поперечную. Некоторые модели этих станков имеют еще
|
|
и дополнительные подачи, например, механическую поперечную подачу не только заднего, но и переднего суппорта. Передний суппорт, таким образом, предназначен для продольного точения рядом установленных проходных резцов, а задний — для поперечной обточки и подрезки также целым рядом подрезных, широких или фасонных резцов.
Подачи на один оборот, соответственно условиям обточки, могут быть различны, у обоих суппортов. Многорезцовые станки большей частью не имеют коробок скоростей и подач, как и большинство станков высокой производительности, предназначенных для работы при постоянном режиме резания. При переналадке станка на другую операцию изменение чисел оборотов и подачи могут быть, однако, изменены путем смены соответствующих пар шестерен в передаче движения к шпинделю и суппорту. Чаще всего на многорезцовых станках обработка ведется за два раза: один станок обдирает деталь, другой—проходит «начисто» и заканчивает поверхности, которые не могли быть обработаны на первом станке.
|
|
В случае сложной формы детали иногда приходится ставить на обдирку по два станка (при выполнении сложного контура детали).
Обычно обработка передним и задним суппортом производится одновременно для сокращения времени, если контур и характер обработки это позволяют. В случае, если одна из операций значительно короче другой, то продолжительность всей обработки определяется временем более длительной операции.
Однако в случаях, когда поперечный суппорт должен работать после продольного, продолжительность обработки будет равна суммарному времени проходов (или их неперекрывающихся частей) обоих суппортов. Так, например, если на поперечном суппорте будут стоять широкие или сложной формы фасонные резцы, то часто бывает необходимо их пускать лишь после того, как поверхность уже будет пройдена соответствующими обдирочными резцами продольного суппорту.
12 Основные понятия и определения технологических процессов
Технологический процесс – это часть производственного процесса, содержащая целенаправленные действия по изменению и (или) определению состояния предмета труда.
Технологическая операция – это законченная часть технологического процесса, выполняемая на одном рабочем месте. Операция связана с выполнением законного объема работы и является основным элементом производственного планирования и учета.
|
|
Установка представляет собой часть операции, выполняемую при одном закреплении изделия.
Позиция – часть операции, выполняемая при неизменном положении изделия относительно рабочих органов оборудования, при этом деталь, заготовка занимает неизменно закрепленное положение.
Технологические процессы и операции по организации производства делятся.
Единичный технологический процесс – представляет процесс изготовления и ремонта изделия одного наименования, типоразмера и исполнения, независимо от типа производства.
Типовой технологический процесс – изготовление группы изделий (деталей) с общими конструктивными технологическими признаками.
Групповой технологический процесс – изготовление группы изделий с различными конструктивными, но общими технологическими признаками.
Характеристика технологического процесса (операции), цикл – это интервал времени от начала до конца периодически повторяющейся технологическая операция не зависимо от числа одновременно изготовляемых изделий.
Технологические нормы.
Технологическая норма – регламентированное значение показателя технологического процесса.
Норма времени – регламентированное время выполнения некоторого объема работ в определенных производственных условиях одним или несколькими исполнителями одной квалификации.
Единица нормирования – количество производственных объектов или число работающих, на которое устанавливается технологическая норма.
Норма выработки – регламентированный объем работ, который должен быть выполнен в единицу времени в определенных организационно-технических условиях одними или несколькими исполнителями соответствующей квалификации.
Расценка – размер вознаграждения работнику за единицу объема выполненной работы.
Дата добавления: 2018-04-05; просмотров: 380; Мы поможем в написании вашей работы! |
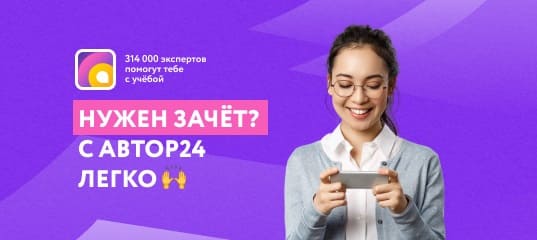
Мы поможем в написании ваших работ!