Точность в машиностроении. Способы достижения точности
Характеристики качества поверхности. Геометрические характеристики.
Основной геометрической характеристикой качества поверхностного слоя является шероховатость поверхности.
Шероховатость поверхности представляет собой геометрический след кромки режущего инструмента, оставленный в материале заготовки, и искаженный пластическими деформациями, сопутствующими процессу формообразования поверхности.
Принято шероховатость поверхности характеризовать отношением Sm к высоте неровностей Rz (<50).
По ГОСТ 25142–82 шероховатость поверхности — это совокупность неровностей поверхности с относительно малыми шагами, выделенная с помощью базовой длины.
Базовая длина l – длина базовой линии, используемая для выделения неровностей, характеризующих шероховатость поверхности.
Значения базовой длины выбираются из следующего ряда: 0,01; 0,03; 0,08; 0,25; 0,80; 2,5; 8,0; 25 мм.
Для количественной оценки шероховатости поверхности по стандарту установлены следующие шесть параметров: Ra, Rz, R max, Sm, S, tp.
1. Ra – среднее арифметическое отклонение профиля, определяется как среднее арифметическое из абсолютных значений расстояний точек измеренного профиля до его средней линии в пределах базовой длины:
2. Rz – высота неровностей профиля по десяти точкам, определяется суммой средних арифметических абсолютных отклонений точек пяти наибольших минимумов H min i и пяти наибольших максимумов H max i профиля в пределах базовой длины:
|
|
3. R max – наибольшая высота неровностей профиля, определяется как расстояние между линией выступов и линией впадин профиля в пределах базовой длины. Линия выступов и линия впадин — линии, эквидистантные средней линии профиля и проходящие соответственно через наивысшую точку выступов и через низшую точку впадин измеренного профиля.
4. Sm – средний шаг неровностей профиля — это среднее арифметическое значение шага неровностей профиля в пределах базовой длины:
5. S – средний шаг неровностей профиля по вершинам — среднее арифметическое значение шага неровностей профиля по вершинам в пределах базовой длины.
6. tp – относительная опорная длина профиля — это отношение опорной длины профиля к базовой длине, выраженное в процентах:
Опорная длина профиля определяется суммой длин отрезков вi в пределах базовой длины, отсекаемых на задание уровне p в материале выступов профиля линией, эквидистантной средней линии. Значения уровня р выбираются в процентах от Rmax.
Волнистость поверхности — это совокупность периодически чередующихся возвышенностей и впадин, образующих неровности поверхности с шагом, большим базовой длины, принятой при измерении шероховатостей.
|
|
Волнистость поверхности характеризуется следующим отношением:
Макроотклонения – это отклонения формы поверхности. В отличие от шероховатости, которая рассматривается как погрешность формы малых участков поверхности, макрогеометрические отклонения поверхности является единичными на протяжении всей рассматриваемой поверхности. Обычно макроотклонения характеризуются следующим отношением : L/H>1000.
К макрогеометрическим погрешностям можно отнести: конусообразность, бочкообразность, седлообразность, овальность и др. Эти погрешности соизмеримы с погрешностями размеров всей детали.
Схемы обработки точением
Обтачивание наружных цилиндрических поверхностей выполняют проходными резцами с продольной подачей, гладкие валы, — при установке заготовки в центрах.
Центровые отверстия обрабатывают на токарных, револьверных, сверлильных и двусторонних центровальных станках. Для центрования применяют типовые наборы инструмента — комбинированные центровочные сверла, а также спиральные сверла и конические зенковки.
Центровые отверстия являются, как правило, установочными базами, и поэтому от точности их исполнения зависит и точность обработки остальных поверхностей заготовки.
|
|
В полые заготовки после подрезки торца и обработки отверстия с двух сторон вводят пробки или оправки с зацентрованными отверстиями или на кромке отверстия снимают конические фаски, используемые в качестве технологических баз с последующим удалением их при отделочной обработке.
Ступенчатые валы обтачивают по схемам деления припуска на части или деления длины заготовки на части. В первом случае обрабатывают заготовки с меньшей глубиной резания, однако общий путь резца получается большим и резко возрастает То.
Во втором случае припуск с каждой ступени срезается сразу за счет обработки заготовки с большой глубиной резания. При этом Т0 уменьшается, но требуется большая мощность привода станка.
Нежесткие валы рекомендуется обрабатывать упорными проходными резцами, с главным углом в плане = 90°. При обработке заготовок валов такими резцами радиальная составляющая силы резания Ру = 0, что снижает деформацию заготовок.
Подрезание торцов заготовки выполняют перед обтачиванием наружных поверхностей. Торцы подрезают подрезными резцами с поперечной подачей к центру или от центра заготовки. При подрезании от центра к периферии поверхность торца получается менее шероховатой.
|
|
Обтачивание скруглений между ступенями валов – галтелей выполняют проходными резцами с закруглением между режущими кромками по соответствующему радиусу с продольной или поперечной подачей.
Точение канавок выполняют с поперечной подачей канавочными или фасонными резцами, у которых длина главной режущей кромки равна ширине протачиваемой канавки. Широкие канавки протачивают теми же резцами сначала с поперечной, а затем с продольной подачей.
Обработку отверстий в валах выполняют соответствующими инструментами, закрепляемыми в пиноли задней бабки. На рисунке слева показана схема сверления в заготовке цилиндрического отверстия.
Точность в машиностроении. Способы достижения точности
Точностью изделия в машиностроении называют степень соответствия заранее установленному образцу. Под точностью детали понимается степень соответствия реальной детали, полученной механической обработкой заготовки, по отношению к детали, заданной чертежом и техническими условиями на изготовление, т.е. соответствие формы, размеров, взаимного расположения обработанных поверхностей, шероховатости поверхности обработанной детали требованиям чертежа.
Следовательно, точность понятие комплексное, включающее всестороннюю оценку соответствия реальной детали по отношению к заданной.
При работе на металлорежущих станках применяют следующие методы достижения заданной точности:
· обработка по разметке или с использованием пробных проходов путем последовательного приближения к заданной форме и размерам; после каждого прохода инструмента производится контроль полученных размеров, после чего решают какой припуск необходимо снять; точность в этом случае зависит от квалификации рабочего, например токаря или фрезеровщика;
· обработка методом автоматического получения размеров, когда инструмент предварительно настраивается на нужный размер, а затем обрабатывает заготовки в неизменном положении; в этом случае точность зависит от квалификации наладчика и способа настройки;
· автоматическая обработка на копировальных станках и станках с программным управлением, в которых точность зависит от точности действия системы управления.
Дата добавления: 2018-04-05; просмотров: 580; Мы поможем в написании вашей работы! |
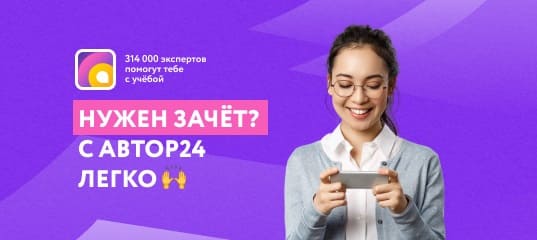
Мы поможем в написании ваших работ!