Раздел Операция «Резьбонарезание»
Вопрос 51
Методы получения резьбы.
Ответ:
В промышленности применяются следующие способы получения резьб:
- лезвийная обработка резанием;
- абразивная обработка;
- накатывание;
- выдавливание прессованием;
- литьё;
- электрофизическая и электрохимическая обработка.
Наиболее распространенным и универсальным способом получения резьб является лезвийная обработка резанием. К ней относятся:
- нарезание наружных резьб плашками;
- нарезание внутренних резьб метчиками;
- точение наружных и внутренних резьб резьбовыми резцами и гребенками;
- резьбофрезерование наружных и внутренних резьб дисковыми и червячными фрезами;
- нарезание наружных и внутренних резьб резьбонарезными головками;
- вихревая обработка наружных и внутренних резьб.
Накатывание является наиболее высокопроизводительным способом обработки резьб, обеспечивающим высокое качество получаемой резьбы. К накатыванию резьб относятся:
- накатывание наружных резьб двумя или тремя роликами с радиальной, осевой или тангенциальной подачей;
- накатывание наружных и внутренних резьб резьбонакатными головками;
- накатывание наружных резьб плоскими плашками;
- накатывание наружных резьб инструментом ролик-сегмент;
- накатывание (выдавливание) внутренних резьббесстружечными метчиками.
К абразивной обработке резьб относится шлифование однониточными и многониточными кругами. Применяется для получения точных, в основном ходовых резьб.
|
|
Выдавливание прессованием применяется для получения резьб из пластмасс и цветных сплавов. Не нашло широкого применения в промышленности и применяется в основном в единичном производстве нестандартных изделий..
Литье (обычно под давлением) применяется для получения резьб невысокой точности из пластмасс и цветных сплавов.
Электрофизическая и электрохимическая обработка (например, электроэрозионная, электрогидравлическая) применяется для получения резьб на деталях из материалов с высокой твердостью и хрупких материалов, например твердых сплавов, керамики.
Вопрос 52
Нарезание резьбы резцами и гребенками.
Ответ:
Треугольную резьбу часто нарезают на токарно-винторезных станках резьбовыми резцами, т. е. резцами обычного типа, заточенными под требуемым углом (60° для метрической резьбы и 55° — для дюймовой). Получение профиля резьбы обеспечивается соответствующим профилем резьбового резца, который должен быть заточен очень точно, и правильной установкой резца относительно детали: резец должен быть расположен строго перпендикулярно оси станка, так как в противном случае резьба получится косой; кроме того, передняя поверхность резца должна быть расположена на высоте центров станка. При другом ее положении резьба будет нарезана с неправильным углом.
|
|
Высокие требования, предъявляемые к заточке резцов и сохранению правильного профиля, привели к внедрению в производство фасонных резьбовых резцов — призматических,«круглых (дисковых). У этих резцов размеры элементов профиля резьбы выдерживаются более точно, чем у обычных, так как такие резьбовые резцы затачиваются по передней поверхности, а отшлифованные при изготовлении задние (боковые) поверхности сохраняют профиль неизменным.
Для улучшения качества поверхности резьбы часто применяют пружинные державки.
При нарезании резьбы одним резцом режущая кромка его вследствие быстрого притупления теряет форму, поэтому рекомендуется черновые ходы производить одним резцом с менее точным профилем, а чистовые ходы — чистовым резцом.
При нарезании резьбы на производстве широко применяются твердосплавные резьбовые резцы со специальной заточкой, значительно повышающие режимы резания.
При скоростном нарезании резьбы происходит небольшое искажение ее профиля: угол профиля нарезаемой резьбы получается всегда больше угла при вершине резца на 30'-1°30'. Поэтому рекомендуется в этих условиях применять резцы с углом профиля, равным углу профиля нарезаемой резьбы, уменьшенному на 1°. Например, для нарезания метрической резьбы с углом профиля 60° угол профиля чистового резца принят 59°.
|
|
Применяют также нарезание резьбы за один проход, используя одновременно три резца, оснащенных твердым сплавом и в совокупности напоминающих гребенку; черновой резец 1 имеет угол профиля 70°, получистовой резец 2 — 65° и чистовой резец 3 — 59°.
Нарезание резьбы резцом производится за много ходов в зависимости от требуемой точности, диаметра резьбы и твердости материала нарезаемой детали.
Необходимо заметить, что применение высоких скоростей резания при нарезании наружной и внутренней резьб в упор, в тех случаях когда на станке нет специальных автоматических упоров, ограничивающих ход суппорта, часто приводит к браку детали. Происходит это потому, что при большом числе оборотов шпинделя рабочий не всегда успевает отвести резец по окончании прохода.
Значительно облегчается работа, когда для быстрого отвода резца используются специальные устройства, особенно автоматические.
В крупносерийном и массовом производстве, а также и в специализированном серийном производстве резьбу часто нарезают на станках, работающих по автоматическому циклу.
|
|
Нарезание прямоугольной и трапецеидальной резьб является более сложной работой в сравнении с нарезанием треугольных резьб. Резьбы прямоугольного и трапецеидального профиля изготовляют как однозаходными, так и многозаходными. При нарезании таких резьб для установки резцов по углу подъема винтовой линии токари применяют специальные державки.
Применение для нарезания резьбы гребенок сокращает время нарезания и, таким образом, увеличивает производительность резьбонарезания. При нарезании резьбы гребенкой работа резания распределяется между несколькими зубьями; для этой цели концы зубьев стачиваются от одного края гребенки к другому, так что глубина резания постепенно увеличивается. Особенно целесообразно и экономично i применять гребенки при изготовлении больших партий одинаковых деталей.Гребенки нельзя применять при нарезании деталей, у которых резьба доходит до выступа или буртика, так как часть резьбы, находящаяся ближе к буртику, не получит полного профиля. Для точных резьб гребенки не применяются, так как они не могут дать высокой точности; их можно использовать только для предварительного нарезания.
Гребенки бывают плоские, тангенциальные и дисковые с кольцевыми и винтовыми канавками. Плоские гребенки применяются для нарезания треугольной резьбы с малым углом подъема: тангенциальные — для нарезания треугольной резьбы с большим углом подъема; они снабжены резьбой, обратной по отношению к резьбе обрабатываемой детали; если эта деталь должна иметь левую резьбу, то резьба гребенки — правая, и наоборот.
Круглые (дисковые) гребенки, так же как и круглые (дисковые) резцы, имеют то преимущество, что они затачиваются только по передней поверхности, допускают большое число переточек и, значит, имеют большой срок службы; благодаря этому они удобны в эксплуатации.
Вопрос 53
Нарезание резьбы метчиками и плашками.
Ответ:
Внутренние метрические резьбы диаметром до 50 мм часто нарезают метчиками. Обычно применяют машинные метчики, что позволяет нарезать резьбу за один рабочий ход. Для нарезания резьбы в деталях из твердых и вязких материалов применяют комплекты, состоящие из двух или трех метчиков. В комплекте из двух метчиков первый (черновой) выполняет 75 % всей работы, а второй (чистовой) доводит резьбу до требуемого профиля. В комплекте из трех метчиков первый (черновой) выполняет 60 % всей работы, средний (получистовой) — 30 % и третий (чистовой) — 10 %. Метчики в комплекте различают по длине заборной части, наибольшая длина заборной части у чернового метчика. В отверстиях с прерывистой поверхностью, имеющей пазы (канавки), резьбу нарезают метчиками с числом канавок, не кратным числу пазов на обрабатываемой поверхности. В этих же целях и для нарезания глубоких отверстий длиной более двух диаметров применяют метчики с винтовыми канавками. Направление винтовой канавки метчика должно быть таким же, как и у нарезаемой резьбы (правая канавка для правой резьбы, левая — для левой). Для нарезания коротких сквозных метрических резьбØ1,5—8 мм и длиной, равной 1,5—2,0 диаметра, применяют бесканавочные метчики, которые обладают большей прочностью, чем обычные, и обеспечивают более высокое качество резьбы.
При нарезании коротких сквозных резьб в деталях из вязких материалов применяют метчики с расположением зубьев в шахматном порядке. Преимущество таких метчиков заключается в том, что в процессе их работы снижается трение, улучшается процесс стружкообразования и облегчается подвод смазочно-охлаждающей жидкости. При установке метчика в револьверную головку на его хвостовик надевают и закрепляют винтом кольцо, вместе с которым метчик устанавливают в патрон для плашек. Скорость резания для нарезания резьбы метчиками в стальных заготовках;
— в чугунных, бронзовых и алюминиевых заготовках. Нарезание резьбы производят с охлаждением эмульсий или маслом.
Для нарезания наружной резьбы на винтах, болтах, шпильках и других деталях применяют плашки. Участок детали, на котором необходимо нарезать резьбу плашкой, предварительно обрабатывают. Диаметр обработанной поверхности должен быть несколько меньше наружного диаметра резьбы: на 0,1—0,2 мм для метрической резьбы диаметром 6—10 мм, на 0,12—0,24 мм для резьбы диаметром 11 —18 мм, на 0,14—0,28 мм для резьбы диаметром 20—30 мм. Для образования захода резьбы в начале нарезаемой поверхности снимают фаску, соответствующую высоте профиля резьбы. Плашку устанавливают в плашкодержатель (патрон), который закрепляют в пиноли задней бабки или в гнезде револьверной головки. При нарезании резьбы скорость резания для стальных, и
для чугунных и
для латунных заготовок.
Вопрос 54
Фрезерование резьбы.
Ответ:
Фрезерование наружной и внутренней резьб производят дисковыми и гребенчатыми, или групповыми, фрезами. При нарезании дисковыми резьбовыми фрезами инструмент устанавливают под углом, равным углу подъема нитки нарезаемой резьбы. Резьбы с крупным шагом нарезают коническими профильными фрезами или цилиндрическими концевыми фрезами с поочередной обработкой одной, а затем другой стороны нитки.
Трапецеидальные и прямоугольные резьбы с крупным шагом фрезеруют дисковыми фрезами предварительно, а чистовые переходы делают резьбовым резцом за несколько рабочих ходов.
Короткие наружные и внутренние резьбы с треугольным профилем фрезеруют гребенчатыми, или групповыми, фрезами. Гребенчатая резьбовая фреза представляет собой как бы несколько дисковых резьбовых фрез, соединенных торцами вместе. Такие фрезы называют групповыми. Продольные канавки, а, следовательно, и режущие кромки у таких фрез расположены параллельно их оси. Зубы фрезы делают затылованными для облегчения их заточки. Длину групповой фрезы обычно берут на 2…3 нитки больше длины нарезаемой резьбы.
Резьбу групповой фрезой нарезают за 1,25 оборота нарезаемой заготовки. Это делается для того, чтобы перекрыть место врезания фрезы. При нарезании резьбы заготовка при каждом обороте должна продвинуться в осевом направлении на один шаг нарезаемой резьбы.
Профиль зубьев фрезы должен быть одинаковым с профилем нарезаемой резьбы. Ось гребенчатой фрезы устанавливают параллельно оси нарезаемой заготовки.
Применение резьбовых гребенчатых фрез особенно целессобразно при нарезании резьбы, расположенной у галтелей, буртиков и т. п., а также резьбы, доходящей до дна глухих отверстий, так как в таких случаях только с помощью фрезерования можно обеспечить полную резьбовую нитку вплоть до буртика или до дна отверстия. Фрезерование гребенчатыми фрезами широко применяют при нарезании резьбы на деталях из вязких и твердых сталей, когда нарезание резьбы плашками или резьбонарезными головками не может обеспечить требуемую шероховатость поверхности на резьбе или же вызывает быстрое изнашивание инструмента.
Вопрос 55
Методы нарезания резьбы.
Ответ:
В зависимости от типа резьбы (каков ее профиль, размеры, внутренняя или наружная, цилиндрическая или коническая), характера производства, требований к ее качеству применяют различные методы и инструменты для ее нарезания.
При нарезании резьбы используют следующие методы:
1) копирования, при котором профиль режущих кромок инструмента (резьбового резца, метчика, плашки, резьбонарезной головки, накатной плашки, абразивного круга) совпадает с профилем впадины или витка резьбы;
2) центроидногоогибания, при котором линии, называемые центроидами и связанные соответственно с инструментом и заготовкой, в процессе нарезания резьбы катятся друг относительно друга без скольжения, при этом профиль резьбы получается как огибающая различных положений режущих кромок инструмента, профиль которых отличается от профиля нарезаемой резьбы; примером инструмента, работающего по этому методу, служит обкатный резец;
3) бесцентроидногоогибания, при котором профиль резьбы получается как линия, огибающая различные последовательные положения режущих кромок инструмента (дисковой фрезы, абразивного круга и др.), но при этом центроиды у инструмента и заготовки отсутствуют; профиль витка инструмента отличается от профиля впадины нарезаемой резьбы.
Для нарезания резьбы применяют следующие инструменты: резьбовые резцы (стержневые, призматические однониточные и гребенчатые, круглые однониточные и гребенчатые); метчики; плашки; винторезные головки с плашками или круглыми гребенками; резьбонарезные фрезы (дисковые и гребенчатые); головки для скоростного резьбофрезерования; накатные плашки и ролики; шлифовальные круги (однониточные и многониточные); обкатные резцы.
Вопрос 56
Накатывание резьбы.
Ответ:
Накатывание резьбы основано на использовании пластических свойств металлов, формирование резьбы происходит за счет перераспределения элементарных объемов заготовки, причем ее исходный объем остается приближенно постоянным.
Под влиянием пластической деформации при накатывании резьбы изменяются физико-механические свойства поверхностного слоя; образуется наклеп, повышающий твердость и прочность; создаются остаточные сжимающие напряжения; видоизменяется форма и ориентация кристаллов. Образующийся при накатывании наклеп поверхностного слоя, напряжения сжатия способствуют повышению циклической прочности резьбовых соединений. Процесс накатывания резьбы по сравнению с обработкой резанием более производителен. Накатывание резьбы можно осуществлять на углеродистых, легированных, нержавеющих сталях, на медных, алюминиевых, титановых сплавах, если их относительное удлинение не меньше 12%, а твердость HRC < 35. В отдельных случаях можно накатывать резьбу при меньшей пластичности и большой твердости металла (относительное удлинение не меньше 8%, а твердость — до 40 HRC), но стойкость резьбонакатного инструмента при этом резко снижается.
В настоящее время используют три способа накатывания резьбы:
а) с тангенциальной подачей инструмента на накатываемую заготовку;
б) с радиальной подачей инструмента на накатываемую заготовку;
в) с продольным перемещением заготовки или инструмента.
При тангенциальной подаче в качестве инструмента используют плоские плашки, два ролика разных диаметров, вращающиеся плашки (ролик) и неподвижный сектор (или секторы).
При радиальной подаче в качестве инструмента применяют один, два или три ролика равного диаметра. При продольном перемещении, основанном на принципе самозатягивания заготовки или инструмента в процессе накатывания, в качестве инструмента используются ролики, установленные на специальных станках или в резьбонакатных головках, которые используют на универсальных металлорежущих станках.
Раздел Операция «Протягивание»
Вопрос 57
Характеристика протягивания и его особенности.
Ответ:
Протягивание— высокопроизводительный метод обработки внутренних и наружных поверхностей, обеспечивающий высокую точность формы и размеров обрабатываемой поверхности. Протягивают многолезвийным режущим инструментом — протяжкой при ее поступательном движении относительно неподвижной заготовки (главное движение).
Принцип протягивания заключается в том, что размер каждого последующего зуба протяжки больше предыдущего, при этом каждый зуб срезает с обрабатываемой поверхности заготовки стружку небольшой толщины, вследствие чего обработанная поверхность имеет малую шероховатость. Несмотря на сравнительно низкую скорость резания при протягивании, этот метод является высокопроизводительным вследствие большой суммарной длины одновременно работающих режущих лезвий.
Протяжки являются сложным и дорогостоящим специальным инструментом. Поэтому экономическая эффективность от их применения может быть достигнута только при условии их применения в массовом или крупносерийном производстве, либо при нормализации формы и размеров обрабатываемых поверхностей в мелкосерийном производстве.
Движение резания при протягивании - прямолинейное, реже -круговое или винтовое. Наиболее распространенной является схема протягивания с прямолинейным движением. Для осуществления процесса резания заготовке и инструменту сообщается относительное поступательное движение. При этой поступательное движение протяжки является главным движением резания.
Протяжки подразделяют на внутренние и наружные. Внутренние протяжки предназначены для обработки отверстий, то естьзамкнутых поверхностей, а наружные - для обработки незамкнутых поверхностей. Кроме этого, к протяжным инструментам относятся прошивки и круглые протяжки, применяемые для обработки тел вращения.
Работа протяжки может быть уподоблена работе ряда строгальных резцов, смещенных относительно друг друга на небольшую величину, которая называется подъемом и определяет толщину снимаемого каждым зубом слоя металла.
При протягивании заготовка своей торцовой поверхностью опирается на приспособление станка и остается неподвижной. Передняя направляющая часть протяжки вставляется в предварительно просверленное отверстие заготовки и присоединяется к тяговому патрону станка.
Протягиванием могут обрабатываться поверхности как свободно расположенные относительно базовых поверхностей заготовки, так и связанные с ними определенным допуском (линейным или угловым). В соответствии с этим различают два метода протягивания.
Метод свободного протягивания должен обеспечить только точне размеры обрабатываемой площади поверхности, независимо от его расположения относительно базовых поверхностей.
Метод координатного протягивания различных поверхностей заготовок должен обеспечить не только соблюдение допуска на выдерживаемый размер, но и точное взаимное расположение базовой и обрабатываемой поверхностей, которое обеспечивается рациональной конструкцией приспособления для установки заготовки.
При обработке отверстий наблюдается явление «разбивания» отверстия, заключающееся в отклонение получаемого размера от ожидаемого. Величина, «разбивания» зависит от качества изготовления протяжки и предварительного отверстия в заготовке, размеров детали и инструмента, состава СОЖ и не соосности предварительного отверстия и протяжки.
Следует отметить, что при обработке тонкостенных деталей может иметь место «усадка» отверстия. Величина «разбивания» и «усадки» определяется экспериментально и учитывается при изготовления и проектировании протяжки.
Вопрос 58
Части внутренней протяжки, ее углы.
Ответ:
Внутренняя протяжка состоит из нескольких элементов. Схема внутренней протяжки приведена на рисунке 26.
Рисунок 26 Схема внутренней протяжки
Хвостовик 1 протяжки служит для соединения протяжки посредством патрона с рабочей кареткой протяжного станка. Конструкция хвостовика зависят от типа протяжки и конструкции патронов.
Шейка 2 и переходный конус 3 связывают хвостовую и направляющую части. На шейку обычно наносится маркировка протяжки. Для отдельных типов хвостовиков, а также для шпоночных иплоских протяжек шейку не выделяют, а делают за одно целое с хвостовиком. Форма поперечного сечения шейки такая же, как и у хвостовиков. Диаметр шейки обычно на 0,3-1,0 мм меньше диаметра хвостовой части. Длину шейки выбирают с таким расчетом, чтобы вставленная в заготовку протяжка легко присоединялась к тяговому патрону, когда он находится в исходном положении, т.е. в наибольшей близости к столу станка. Передняя направляющая часть 4 протяжки служит для установки обрабатываемой заготовки на протяжку перед протягиванием и для направления и центрирования протяжки относительно оси протягиваемой заготовки. Размер и форма поперечного сечения передней направляющей части соответствуют размеру и форме поперечного сечения заготовки до протягивания.
Длина берется равной 0,75-1,0 длины протягивания, что обеспечивает размещение и центрирование заготовки. Излишняя длина нежелательна, так как при этом увеличивается расстояние до первого зуба и общая длина протяжки. Задняя направляющая часть 7 препятствует перекосу заготовки на протяжке и повреждению обработанной поверхности и зубьев в момент выхода последних зубьев калибрующей части из отверстия. Плоские шпоночные протяжки выполняются, как правило, без задней направляющей. Длина задней направляющей принимается 0,5-1,0 длины протягивания. У очень длинных и тяжелых протяжек задняя направляющая имеет также опорную цапфу 8, за которую протяжка поддерживается люнетом скользящим по направляющим корыта протяжного станка. Цапфа необходима для поддержания и центрирования протяжки при обратном ходе станка перед началом работы. Часто протяжка имеет задний хвостовик такой же формы и размеров, как и передний хвостовик, служащий для захвата протяжки патроном каретки обратного хода станка при работе на станках с полуавтоматическим или автоматическим циклом. Если протяжка должна быть определенным образом ориентирована (например, для попадания в шлицы, прорезанные предыдущей протяжкой), задняя замковая часть снабжается плоским срезом. Режущая часть 5 протяжки, служащая для срезания припуска, оставленного под протягивание, состоит из ряда последовательно расположенных режущих зубьев, каждый из которых срезает слой металла определенного сечения. По величине подачи режущие зубья могут быть разделены на черновые, переходные и чистовые. Число режущих зубьев зависит от величины припуска, принятой подачи на зуб и выбранной схемы резания. Калибрующая часть 6 протяжки состоит из небольшого числа зубьев, размеры и форма которых одинаковые и соответствуют форме и размерам готового отверстия. Назначение калибрующей части следующее: зачистка поверхности после режущих зубьев, обеспечение стабильности получаемых размеров и замена режущих зубьев, постепенно теряющих размер вследствие переточки. Профиль зубьев и стружечных канавок у калибрующей части такой же, как и у режущей. Режущие кромки калибрующих зубьев имеют прямую ленточку, которая предназначается для сохранения размеров протяжки при переточках. Шаг калибрующих зубьев равен шагурежущих зубьев; у протяжек для точных отверстий шаг калибрующих зубьев составляет 60-70% от шага режущих зубьев. Число калибрующих зубьев равно 4-8.
Углы внутренней протяжки приведены на рисунке 27.
Рисунок 27 Углы внутренней протяжки
Передние и задние углы протяжки измеряют в плоскости, перпендикулярной к главному режущему лезвию. Передний угол γ (5-20°) выбирают в зависимости от свойств обрабатываемого материала, задний угол α (1-4°) - в зависимости от класса точности обработки.
Вопрос 59
Элементы режимов резания при протягивании.
Ответ:
Определение элементов режимов резания при протягиваниивыполняется в следующей последовательности.
Определяется глубина резания
Определяется периметр резанияпо формуле:
где – периметр резания, который равняется длине обрабатываемого контура заготовки;
– количество зубьев в секции протяжки;
– наибольшее количество зубьев, которые одновременно режут;
где – длина обрабатываемой поверхности;
– шаг режущих зубьев.
Шаг режущих зубьев зависит от высоты зуба
:
где – подача на зуб;
– длина протягивания;
– поправочный коэффициент (увеличивается с увеличением
).
Получив значения , необходимо проверить, чтобы количество зубьев
, которые одновременно принимают участие в работе, было не меньшее двух и чтобы шаг не был кратный
.
Дале величину округляют к ближайшему значению нормального ряда шагов протяжки: 4, 5, 6, 8, 10, 12, 14, 18, 20, 22, 25 мм. Полученное значение
округляют к ближайшему целому числу.
Скорость резания , определяется в зависимости от свойств обрабатываемого материала. Устанавливается 4 группы скоростей резания.
К I группе скоростей резания относится обработка углеродистой (НВ197-269), хромистой (НВ187-229) сталей, к II группе – углеродистой (НВ187-197), хромистой (НВ156-187), хромоникелевой (НВ187-269), к III группе–углеродистой (НВ156-187), хромистой (НВ269-321), хромоникелевой (НВ156-187), к IМ группе – углеродистой стали (< НВ156).
Вопрос 60
Схемы резания при протягивании.
Ответ:
Различают следующие схемы резания:
- по способу деления припуска по толщине и ширине - одинарная и групповая;
- по способу формирования обработанной поверхности - профильная, генераторная и комбинированная.
Схемы резания при протягивании приведены на рисунке 28.
а - одинарная; б - групповая; в - профильная; г - генераторная; д – комбинированная
Рисунок 28 Схемы резания при протягивании
Одинарная схема резания (рисунок 28, а) характерна тем, что каждый зуб протяжки срезает припуск определенной толщины по всему периметру обрабатываемого отверстия за счет того, что диаметр каждого последующего зуба больше диаметра предыдущего на величину , где
- подъем или подача на зуб.
Так как кольцевая стружка недопустима, то для деления стружки по ширине на режущих кромках необходимо делать стружкоделительные канавки V-образной формы, которые располагают в шахматном порядке при переходе от одного зуба к другому. Стружкоделительные канавки имеют глубину 0,4... 1,0 мм и ширину 0,6...1,2 мм в зависимости от диаметра протяжки. Снимаемые каждым зубом стружки получаются в виде отдельных частей с ребром жесткости толщиной 2az за счет того, что на участке канавки предыдущего зуба стружка не снимается. Ребро жесткости ухудшает свертываемость стружки в канавках между зубьями, из-за чего приходится значительно снижать величину подачи на зуб. Это приводит к нежелательному увеличению длины протяжки.
Стружкоделительные канавки прорезают шлифовальным кругом при небольшом (2...3°) поднятии заднего центра протяжки для создания заднего угла по дну канавки. При этом ослабляются режущие кромки зубьев в точках К пересечения канавок с задней поверхностью. Это приводит к более интенсивному износу зубьев на этих участках и, соответственно, к снижению стойкости протяжки.
Схема группового резания (рисунок 28, б) отличается от вышеописанной тем, что все режущие зубья делятся на группы или секции, состоящие из 2...5 зубьев, в пределах которых зубья имеют одинаковый диаметр. Припуск по толщине делится между группами зубьев, а по ширине - между зубьями группы благодаря широким выкружкам, выполненным в шахматном порядке. Каждый зуб снимает отдельные части припуска участками режущей кромки, где нет выкружек. При этом благодаря большой ширине выкружек снимаемая стружка не имеет ребер жесткости, хорошо скручивается в канавках между зубьями, даже при увеличении толщины среза до 0,3...0,4 мм при обработке стали и до 1,0...1,2 мм - при обработке чугуна. За счет этого при групповой схеме резания возможно существенное сокращение длины режущей части протяжки.
Широкие выкружки на зубьях обеспечивают увеличение угла стыка выкружек и режущих кромок до 130...150°, что в сочетании с задними углами 4...6° на вспомогательных режущих кромках, полученными при вышлифовываниивыкружек, обеспечивает повышение стойкости протяжек в 2-3 раза по сравнению с одинарной схемой резания.
При проектировании протяжек с групповой схемой резания последний зуб в группе, не имеющий выкружек и выполняющий роль зачистного, делают с занижением на 0,02...0,04 мм по диаметру относительно других зубьев. Это необходимо, чтобы избежать образования кольцевых стружек, возможных при упругом восстановлении обработанной поверхности после прохода прорезных зубьев.
Недостатком групповой схемы резания является повышенная трудоемкость изготовления протяжки по сравнению с одинарной схемой.
Форма режущих кромок зубьев протяжки определяется принятой схемой формирования обработанной поверхности.
При профильной схеме (рисунок 28, в) контур всех режущих кромок подобен профилю протягиваемого отверстия. При этом в окончательном формировании обработанной поверхности принимают участие только последние зубья, а остальные служат для удаления припуска. При сложной форме отверстий использование такой схемы нецелесообразно, так как усложняет изготовление протяжки. Профильная схема в основном применяется при формировании простых по форме поверхностей, например, круглых или плоских.
При использовании генераторной схемы (рисунок 28, г) форма режущих кромок не совпадает с формой обработанной поверхности, которая формируется последовательно всеми зубьями. В этом случае упрощается изготовление протяжки путем шлифования напроход всех зубьев абразивным кругом одного профиля. Однако при этом на обработанной поверхности возможно появление рисок (ступенек) вследствие погрешностей заточки зубьев, что ухудшает качество обработанной поверхности.
При высоких требованиях к шероховатости обработанной поверхности рекомендуется использовать комбинированную схему (рисунок 28, д), при которой два-три последних режущих и калибрующие зубья работают по профильной, а остальные - по генераторной схеме.
Раздел Операция «Шлифование»
Вопрос 61
Характеристика процесса шлифования.
Ответ:
Шлифование представляет собой процесс сверхскоростного резания, осуществляемого большим количеством абразивных зерен, расположенных по периферии или торцовой поверхности шлифовального круга.
Результатом резания отдельного абразивного зерна шлифовального круга, удаляющего мелкую стружку, является царапина на обрабатываемой поверхности. Поэтому процесс резания при шлифовании можно рассматривать как суммарное царапание обрабатываемой поверхности абразивными зернами. Свойственное процессу шлифования высокое качество обрабатываемой поверхности достигается благодаря наличию на поверхности инструмента огромного числа царапающих зерен; поэтому царапины не только плотно размещены, но и многократно перекрываются.
Процесс резания при шлифовании отличается следующими особенностями.
Шлифовальный круг имеет не сплошную, а прерывистую режущую кромку, так как абразивные зерна находятся друг от друга на некотором расстоянии.
Процесс шлифования заключается в очень тонком срезании отдельными зернами - резцами материала детали.
Зерна круга в отличие от резцов имеют неправильную округленную в вершинах геометрическую форму и произвольно расположены в круге, поэтому нет определенных значений углов заточки, а передний угол, как правило, имеет отрицательное значение. Так, у зерен электрокорунда, зернистостью 80 имеются закругления на вершинах радиусом до 0,014 мм, а у зерен зернистостью 40-0,012 мм. В момент, предшествующий врезанию, абразивные зерна интенсивно скользят по металлу, вызывая большое тепловыделение, приводящее к высокой мгновенной температуре.
В процессе шлифования под влиянием увеличивающейся нагрузки на затупившиеся зерна последние могут выкрашиваться или раскалываться. При этом обнажаются новые острые кромки зерен. Таким образом, в отличие от резца круги могут самозатачиваться.
Снятие стружки зерном происходит за очень незначительное время (0,0001-0,00005 с), т. е. практически мгновенно, но благодаря большому количеству зерен процесс стружкообразования протекает для всего круга непрерывно.
Высокая твердость и термостойкость абразивных зерен, а также увеличение пластичности обрабатываемого материала из-за местного нагрева в зоне контакта круга с деталью дают возможность обрабатывать очень твердые материалы (стальные закаленные детали, твердые сплавы, высокотвердые чугуны и др.).
Высокая температура в зоне контакта абразивного зерна и детали приводит к интенсивному нагреву поверхности, образовавшейся риски. После выхода зерна из зоны контакта начинается охлаждение, но поверхность не успевает полностью охладиться до тех пор, пока в работу вступает новое зерно. Можно считать, что новое зерно начинает резание при температуре примерно 600° С.
Таким образом, в процессе шлифования резание осуществляется при высокой температуре детали, тогда как резание резцами или фрезами - при значительно более низкой. Это обстоятельство приводит к необходимости учитывать при шлифовании физико-механические свойства стали и чугунов при температуре 600° С, а не в холодном состоянии.
При высоких температурах материал имеет меньшую твердость и прочность и потому обрабатываемость его более легкая, чем холодного материала.
Ряд легирующих элементов способствует сохранению высоких механических свойств в нагретом состоянии, т. е. делает сталь более жаропрочной. Наиболее эффективными элементами, повышающими жаропрочность, являются вольфрам, молибден, кремний, титан. Поэтому стали, легированные этими элементами, шлифуются труднее углеродистых конструкционных сталей.
Вопрос 62
Виды абразивного инструмента.
Ответ:
Абразивные инструменты характеризуются формой и размерами, шлифовальным материалом, его зернистостью, связкой, твердостью, точностью, неуравновешенностью, а алмазные и эльборовые инструменты также и концентрацией зерен в рабочем слое.
Различают следующие виды абразивного инструмента:
1) Шлифовальный круг – абразивный инструмент в виде твердого тела вращения, предназначенный для шлифования. Лепестковый шлифовальный круг – шлифовальный круг, состоящий из радиально расположенных и жестко закрепленных на одной из торцевых сторон шлифовальных листов.
2) Шлифовальная головка – шлифовальный круг с глухим отверстием для крепления.
3) Абразивный брусок – абразивный инструмент в виде твердого тела, предназначенный для обработки без вращения вокруг своей оси.
4) Абразивный шевер – абразивный инструмент в виде твердого тела, имеющий форму зубчатого колеса.
5) Притир – абразивный инструмент в виде твердого тела на поверхности которого абразивные зерна находятся в закрепленном и незакрепленном связкой состоянии.
6) Полировальный круг – абразивный инструмент в виде твердого тела вращения, предназначенный для абразивного полирования.
7) Шлифовальная шкурка – абразивный инструмент на гибкой основе с нанесенном на нее слоем или несколькими слоями шлифовального материала, закрепленного связкой.
8) Лепестковый шлифовальный круг – шлифовальный круг, состоящий из радиально расположенных и жестко закрепленных на одной из торцевых сторон шлифовальных листов.
8) Шлифовальный лист, шлифовальный диск, лента, конусы, цилиндры, бобины.
10) Абразивное тело – абразивный инструмент предназначенный для виброабразивной обработки.
Вопрос 63
Схема шлифования.
Ответ:
Шлифование — технологический способ обработки металлов, позволяющий получать на деталях поверхности высокого качества с высокой точностью размеров. Признаком, позволяющим квалифицировать шлифование как один из способов обработки резанием, является образование стружки, срезаемой в процессе обработки.
Различают следующие основные схемы шлифования:
1. Наружное круглое шлифование (рисунок 29), при котором шлифовальный круг 1вращается вокруг оси , совершая главное движение
. Цилиндрическая заготовка 2вращается вокруг оси
, параллельной оси
, совершая движение
. Наружные поверхности круга и заготовки взаимно касаются по образующей
. Линейные скорости точек шлифовального круга и заготовки, лежащие на линии
, могут быть направлены в одну сторону или навстречу друг другу. Но во всех случаях скорости точек, принадлежащих кругу, по значению намного больше скорости точек заготовки. Заготовке сообщается возвратно-поступательное движение продольной подачи
. По окончании цикла возвратно-поступательного движения продольной подачи действует прерывистое движение поперечной подачи
, сообщаемое шлифовальному кругу или заготовке. Наружным круглым шлифованием можно обрабатывать и конические поверхности: в этом случае наружная поверхность шлифовального круга «заправляется» на необходимый угол наклона образующей обрабатываемого конуса или оси вращения круга и заготовки пересекаются под тем же углом.
Рисунок 29 Наружное круглое шлифование
2. Внутреннее круглое шлифование (рисунок 30), при котором шлифовальный круг 1 и обрабатываемая заготовка 2 вращаются вокруг параллельных осей и
совершая соответственно движения
и
. Наружная поверхность круга касается внутренней цилиндрической поверхности заготовки. Движения продольной
и поперечной
подач происходят так же, как при наружном круглом шлифовании, и приложены обычно к шлифовальному кругу. Возможна также обработка внутренних конических поверхностей.
Рисунок 30 Внутреннее круглое шлифование
3. Плоское шлифование (рисунок 31) главное движение резания . Наружная цилиндрическая поверхность круга каса-ется обрабатываемой заготовки2 по линии
. В процессе резания заготовке сообщается возвратно-поступательное движение подачи
. В промежутках между возвратно-поступательными движениями заготовки шлифовальному кругу сообщается прерывистое движение
поперечной подачи. После обработки плоскости шлифовальному кругу сообщается движение вер-тикальной подачи
. Обработка всей плоскости повторяется до тех пор, пока значение суммарной вертикальной подачи не будет равно припуску на обработку данной поверхности шлифованием.
Рисунок 31 Плоское шлифование
Торцовое шлифование(рисунок 32), при которых шлифовальный круг 1 вращается вокруг оси , совершая движение
. Касание заготовки2с кругом происходит не по линии, как в предыдущих схемах, а по плоскости. Заготовке сообщается возвратно-поступательное движение продольной подачи
, а в промежутках между этими движениями шлифовальному кругу или заготовке сообщается прерывистое движение поперечной подачи
. Так же, как приплоском шлифовании внешней цилиндрической поверхностью круга, значение суммарной поперечной подачи равно припуску на шлифование.
Рисунок 32 Торцовое шлифование
Вопрос 64
Маркировка абразивного инструмента.
Ответ:
Все абразивные инструменты имеют свою маркировку. В маркировке абразивного инструмента указывается природа абразивного материала, размер его зерен (зернистость) и зерновой состав (содержание основной фракции), твердость инструмента, природа и свойства связки, класс точности и класс неуравновешенности круга.
Так, например, маркировка абразивного:
2SA16 ПСМ2 8К8 БЗ,
может быть расшифрована следующим образом:
25А – шлифовальный материал-электрокорунд белый,
16 – зернистость (160-200 мкм.),
П – зерновой состав (содержание основной фракции 55%),
СМ2 – твердость круга,
8 – номер структуры,
К8 – связка керамическая,
Б – класс точности,
3 – класс неуравновешенности круга.
Кроме этого на абразивном круге указывается обозначение его формы, размеры и максимальная окружная скорость (скорость резания) в метрах в секунду.
В качестве шлифовальных материалов применяются:
- на основе кристаллической окиси алюминия Al2O3–нормальный электрокорунд (марки 13А, 14А и 15А), электрокорунд белый (23А, 24А,25А), хромистый электрокорунд (33А и 34А), монокорунд (43А, 44А);
- на основе карбида кремния SiC – карбид кремния черный (53С, 54С, 55С) и карбид кремния зеленый (63С, 64С);
- природный алмаз (А1, А2, А3, А5, А8);
- синтетический алмаз (АС2, АС4, АС6, АС15, АС20).
В зависимости от размера зерен шлифовальные материалы делятся на четыре группы: шлифзерно (2000…160 мкм), шлифпорошки (125…40 мкм), микро- шлифпорошки (63…14 мкм) и тонкие микропорошки (10…3 мкм). В номере зернистости размер зерен основной фракции указывается в сотых долях миллиметра.
Содержание основной фракции обозначается буквенными индексами; В (высокое), П (пониженное), Н (низкое) и Д (допустимое).
Твердость абразивного инструмента зависит от прочности связки и характеризует способность связки удерживать зерна шлифовального материала. Установлены семь степеней твердости инструментов: весьма мягкие (ВМ1, ВМ2), мягкие (М1, М2, М3), среднемягкие (СМ1, СМ2), средние (С1, С2), среднетвердые (СТ1, СТ2, СТ3), твердые (Т1, Т2), весьма твердые (ВТ) и чрезвычайно твердые (ЧТ).
Номер структуры круга показывает объемное содержание шлифовального материала. С увеличением номера от 1 до 16 содержание шлифовального материала уменьшается, а объем пор увеличивается.
Связки абразивных инструментов могут быть: керамические (К1-К10), бакелитовые (Б, Б1…Б4), вулканитовые (В, В1…В5), металлические (М1, МК, МВ1), глифталевые (Г) и другие.
Шлифовальные круги изготавливаются трех классов точности (АА, А и Б) и четырех классов неуравновешенности (1, 2, 3 и 4).
При шлифовании вращательное главное движение резания всегда придается режущему инструменту — шлифовальному кругу. Скорость его является скоростью резания, измеряемой, в отличие от всех других видов обработки резанием, в метрах в секунду. По форме обрабатываемой поверхности шлифование может быть плоским или круглым.
Вопрос 65
Элементы режимов резания при шлифовании.
Ответ:
Основными элементами режима резания при шлифовании являются окружная скорость круга , окружная скорость заготовки
, глубина резания
и подача
.
Скоростью резания при шлифовании называют линейную скорость на наибольшей окружности шлифовального круга
где – диаметр круга;
– частота вращения.
Скоростью перемещениязаготовки при плоском шлифовании называют скорость перемещения стола, а при круглом шлифовании — окружную скорость заготовки.
Поперечной подачей при плоском шлифовании называют перемещение точки круга вдоль оси за один оборот, а продольной подачей при круглом – ее перемещение за двойной ход заготовки.
Глубиной резания при шлифовании называют слой металла между обработанной и обрабатываемой поверхностью, снимаемый за один рабочий ход.
В зависимости от технологических параметров обработки, материала заготовки и оборудования можно с помощью справочных данных назначить окружную скорость шлифовального круга, глубину срезаемого слоя и подачу.
Дата добавления: 2018-02-28; просмотров: 661; Мы поможем в написании вашей работы! |
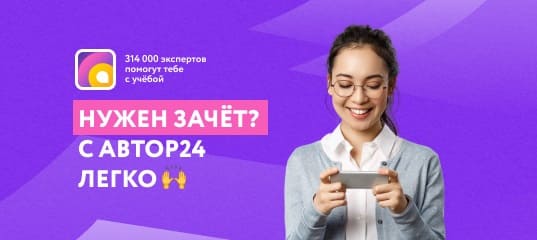
Мы поможем в написании ваших работ!