Раздел Физические основы процесса резания
Вопрос 15
Типы стружки. Приемы стружкодробления.
Ответ:
Одно из первых исследований процесса стружкообразования выполнено русским ученым Иван Августович Тиме в 1870 году. Им, в частности, предложена классификация стружек, которая оказалась настолько удачной, что сохранилась и до настоящего времени. Согласно этой классификации по внешнему виду и внутреннему строению при резании конструкционных сталей стружка бывает следующих типов: сливная, элементная, суставчатая и надлома.
Сливная стружка (рисунок 6, а) представляет собой непрерывную ленту, которая в зависимости от условий схода по передней поверхности инструмента может быть прямой, спиральной или в виде хаотических завитков. Прирезцовая сторона стружки I, прилегающая к передней поверхности инструмента, гладкая, блестящая, а внешняя сторона 2 - в виде мелких, постоянно чередующихся зубчиков. Цвет стружки в зависимости от температуры резания изменяется от серебристо-белого и желтого до матово-серого и синего. Форма и размеры поперечного сечения стружки по всей длине постоянны, что свидетельствует о стабильности деформации, происходящей при образовании такой стружки. Сливная стружка встречается при резании пластичных металлов в основном на больших скоростях, малых и средних подачах, а также при положительных передних углах инструмента.
Элементная стружка (рисунок 6, б) (иногда ее называют стружкой скалывания) состоит из отдельных элементов (кусочков) металлаI, не связанных или слабо связанных между собой прирезцовым слоем. Каждый элемент стружки при его формировании претерпевает значительную деформацию и становится в 2...3 раза тверже по сравнению с исходной твердостью обрабатываемого материала. Вследствие этого срезаемый слой, проходя через так называемую поверхность скалывания mn, теряет свою пластичность и разрушается с определенной периодичностью. Элементная стружка образуется при резании хрупких металлов (чугун, бронза и другие), а также при резании на невысоких скоростях пластичных металлов, при больших толщинах срезаемого слоя, малых передних углах, высокой твердости обрабатываемых металлов и других условиях, затрудняющих пластическую деформацию.
|
|
а - сливная; б - элементная; в - суставчатая; г– надлома
I - металл
Рисунок 6 Типы стружек, образующихся при резании металлов
Суставчатая стружка (рисунок 6, в) является переходной от элементной стружки к сливной. Она состоит из отдельных суставов 1, связанных между собой. Такой вид стружки часто встречается при резании высоколегированных сталей и титановых сплавов.
Стружка надлома (рисунок 6, г) состоит из отдельных не связанных между собой кусочков, имеющих различные размеры и форму; она встречается при резании весьма хрупких материалов или некоторых металлов, склонных к налипанию на передние поверхности инструментов. При этом скол отдельных кусочков металла происходит по поверхностиmn, часто располагаемой ниже поверхности резания.
|
|
На практике при резании пластичных металлов (сталей и сплавов) и особенно на высоких скоростях чаще всего встречается сливная стружка. Образование элементной стружки характеризуется периодическим изменением параметров процесса стружкообразования при формировании каждого элемента, что весьма затрудняет его изучение. Поэтому сначала рассмотрим более простой и удобный для исследования процесс сливного стружкообразования при прямоугольном, свободном резании.
В настоящее время металлообрабатывающая промышленность располагает различными средствами воздействия на форму и размеры стружки, которые базируются на кинематическом (прерывистом) и некинематическом (непрерывном) методах. Некинематический метод дробления стружки основан на создании условий, обеспечивающих изменение механических свойств и возникновение дополнительных местных напряжений в сечении стружки при неизмененных кинематических параметрах процесса резания. Некинематический метод включает в себя способы, оказывающие механическое и физическое воздействие на процесс стружкообразования. Кроме того, дробление стружки может достигаться путем подбора соответствующих режимов резания, создания специальных марок сталей и сплавов для заготовок и разработки технологических режимов их термической обработки.
|
|
К механическим способам дробления стружки следует отнести:
- специальные типы заточек передней грани режущего инструмента, такие как выкружки, порожки, круглые, секторные и продольные лунки, отрицательные фаски на главной и вспомогательной режущих кромках, которые обеспечивают необходимый характер завивания стружки, и принудительное направление ее на обрабатываемую поверхность заготовки .
- различные типы стружкозавивающих и стружколомающих устройств, являющихся препятствием на пути движения сходящей стружки, вызывая ее дополнительную деформацию и снижение пластических свойств;
- опережающую пластическую деформацию обрабатываемой поверхности, получаемую за счет нанесения прямозубой, винтовой или косозубой накаткой рисок, ослабляющих сечение стружки и являющихся концентраторами напряжений;
|
|
- предварительную подготовку обрабатываемой поверхности заготовки путем нанесения стружкоразделительной канавки или локального физического воздействия (высоко или низкотемпературного, а также деформационного воздействий).
К способам физического воздействия на процесс резания, обеспечивающим дробление стружки, относятся электроискровой разряд, следующий за основной механической обработкой и создающий интенсивное тепловое воздействие, разрушающее стружку; предварительный периодический подогрев зоны резания с нанесением стружкоразделительных канавок кратковременным импульсом тока плазматрона; электродуговое распределение стружки, подаваемой в ориентированном состоянии в зону термического влияния дуги.
Более надежное и эффективное дробление стружки при возможных изменениях режимов резания и механических свойств обрабатываемого материала в процессе обработки высокопрочных, жаропрочных материалов и пластичных сплавов возможно только кинематическими способами, когда создаются колебательные движения инструмента или заготовки в направлении подачи .
Вопрос 16
Явление наклепа.
Ответ:
При обработке металлов резанием деформации подвергается не только срезаемый слой, но и поверхностный, образовавшийся на детали после прохода резца. Под влиянием этих деформаций изменяются механические свойства поверхностного слоя: увеличивается его твердость и уменьшается пластичность, то есть он становится более хрупким. Такое изменение механических свойств в результате пластических деформаций в холодном состоянии называется или наклепом.
Схема образования наклепа приведена на рисунке 7.
Рисунок 7 Схема образования наклепа
Таким образом, стружка, полученная от пластичного материала, раза в 1,5-2 тверже, чем сам металл.
В процессе резания деформации подвергается не только срезаемый металл, но и наружный слой поверхности на некоторой глубине h. Дело в том, что режущая кромка любого инструмента в действительности не так остра, как это кажется невооруженному глазу. Под микроскопом на ней видны зазубрины и некоторый радиус закругления ρ. Даже у тщательно заточенного инструмента ρ = 0,01- 0,03 мм. Такое закругление режущей кромки препятствует ее врезанию в срезаемый слой. В результате некоторая часть металла подминается закруглением, вызывая пластические деформации в поверхностном слое обрабатываемой заготовки. Вот почему твердость наружного слоя обработанной заготовки (детали) иногда намного выше твердости нижележащих слоев: при обработке алюминия на 90-100%, латуни на 60-70%, мягкой стали на 40-50%.
аклепанный слой имеет разную глубину при различных способах обработки. Так, при обычных условиях обработки заготовок из стали средней твердости глубина наклепанного слоя получается при черновой обработке резцом 0,4-0,5 мм, при чистовой - только 0,04-0,06 мм, а при полировании - 0,02-0,04 мм.
На глубину наклепа значительное влияние оказывают условия работы и режим резания. Она уменьшается с увеличением скорости резания и растет с увеличением толщины среза. Затупленный резец дает в 2-3 раза большую глубину наклепа, чем острый, так как тупой резец труднее внедряется в срезаемый слой.
Разные металлы имеют неодинаковую способность к наклепу. Чем пластичнее обрабатываемая сталь и меньше ее твердость, тем большее повышение твердости она получит после обработки. Встречаются такие металлы, которые при невысокой твердости отличаются чрезвычайно большой способностью к наклепу. Их твердость в процессе резания настолько возрастает, что нередко механическая обработка становится невозможной. К ним, например, относится кремнемарганцовая сталь, содержащая 13% марганца, и некоторые другие стали. Хрупкие металлы - чугун, бронза и др. не наклепываются. Наклеп - следствие пластической деформации обрабатываемого металла: чем больше деформация, тем больше наклеп. Следовательно, на образование наклепа, как и на усадку стружки, должна влиять величина переднего угла.
Так, с увеличением переднего угла деформации срезаемого слоя обработанной поверхности уменьшаются, следовательно, степень и глубина наклепа резко снижаются. Например, при угле γ=5° глубина наклепанного слоя примерно в 2-3 раза больше, чем при угле γ=45°.
Вопрос 17
Явление нароста.
Ответ:
При обработке пластичных металлов резанием на передней поверхности инструмента образуется слой металла, который называют наростом. Это сильно деформированный металл, структура которого отличается от структур обрабатываемого металла и стружки.
Образование нароста объясняется тем, что геометрическая форма инструмента не идеальна с точки зрения обтекания ее металлом. При некоторых условиях обработки силы трения между передней поверхностью инструмента и частицами срезанного слоя металла становятся больше сил внутреннего сцепления, и при наличии определенных температурных условий металл прочно оседает на передней поверхности инструмента.
В процессе обработки резанием размеры и форма нароста непрерывно меняются в результате действия сил трения между отходящей стружкой и внешней поверхностью нароста. Частицы нароста постоянно уносятся стружкой, увлекаются обработанной поверхностью заготовки, иногда нарост целиком срывается с передней поверхности инструмента и тут же вновь появляется. Схема образования нароста приведена на рисунке 8.
Рисунок 8 Схема образования нароста
Объясняется это тем, что нарост находится под действием силы трения, сил сжатия и силы растяжения. С изменением размеров нароста меняется соотношение действующих сил. Когда сумма сил сжатия и растяжения становится больше силы трения, то происходят разрушение и срыв нароста. Частота срывов нароста зависит от скорости резания и может достигать нескольких сотен в секунду.
Нарост существенно влияет на процесс резания и качество обработанной поверхности заготовки, так как при его наличии меняются условия стружкообразования.
Положительное влияние нароста заключается в том, что при наличии его меняется форма передней поверхности инструмента, что приводит к увеличению переднего угла, следовательно, к уменьшению силы резания. Вследствие высокой твердости нарост способен резать металл. Нарост удаляет центр давления стружки от режущей кромки, в результате чего уменьшается износ режущего инструмента по передней поверхности. Нарост улучшает теплоотвод от режущего инструмента.
Отрицательное влияние нароста заключается в том, что он увеличивает шероховатость обработанной поверхности. Частицы нароста, внедрившиеся в обработанную поверхность, при работе детали с сопрягаемой деталью вызывают повышенный износ пары. Вследствие изменения наростом геометрии режущего инструмента меняются размеры обрабатываемой поверхности в поперечных (диаметральных) сечениях по длине заготовки и обработанная поверхность получается волнистой. Вследствие изменения переднего угла инструмента изменяется сила резания, что вызывает вибрацию узлов станка и инструмента, а это, в свою очередь, ухудшает качество обработанной поверхности.
Вопрос 18
Тепловые явления при резании.
Ответ:
Теплота является одним из основных факторов, влияющих на резание.
Теплообразование оказывает двойное воздействие на резание. С одной стороны, интенсивное тепловыделение облегчает деформирование материала срезаемого слоя, способствует образованию пограничного слоя на контактных поверхностях стружки и заготовки, вследствие чего уменьшается износ инструмента и повышается качество обработанной поверхности. С другой стороны, тепловое воздействие на режущее лезвие инструмента приводит к изменению структуры и физико-механических свойств инструментального материала (снижению его твердости). Температура в зоне главной режущей кромки достигает 800-1000 °С. Это приводит к потере режущих способностей инструмента и ускоренному изнашиванию.
Кроме того, с повышением температуры инструмента увеличиваются его размеры, что вызывает снижение точности обработки. Нагрев жестко закрепленной обрабатываемой заготовки ведет к изменению ее размеров и деформациям, что также влияет на точность обработки.
Тепловыми явлениями при резании необходимо управлять так, чтобы выделяющаяся теплота облегчала резание и не снижала стойкости инструмента и точности обработки. Погрешности обработки заготовки, возникающие вследствие тепловыделения, необходимо учитывать при наладке станков, особенно автоматов и полуавтоматов. Для определения погрешностей нужно знать температуру инструмента и заготовки в процессе резания.
При резании металлов затрачивается работа на пластические и упругие деформации в срезаемом слое и в слое, прилегающем к обработанной поверхности и поверхности резания, а также на преодоление трения по передней и задней поверхностям резца.
Работа, затрачиваемая на пластические деформации, составляет около 80% всей работы резания, а работа трения — около 20%. Примерно 85—90% всей работы резания превращается в тепло.
Образующееся тепло поглощается стружкой – 50 -86%, резцом –10-40%, обрабатываемой деталью – 3-9% и около 1% тепла рассеивается в окружающей среде излучением.
На величину температуры в зоне резания оказывают влияние физико-механические свойства обрабатываемого материала, режимы резания, геометрические параметры инструмента и применение смазочно-охлаждающей жидкости.
При обработке стали выделяется больше тепла, чем при обработке чугуна. Чем выше предел прочности σв и твердость обрабатываемого материала, тем выше температура в зоне контакта инструмента с деталью.
С увеличением подачи температура в зоне резания повышается, но менее интенсивно, чем при увеличении скорости резания. Еще меньшее влияние на температуру оказывает глубина резания.
С увеличением угла резания δ и главного угла в плане φ температура в зоне резания возрастает, а с увеличением радиуса закругления резца r уменьшается.
Применение смазочно-охлаждающей жидкости существенно уменьшает температуру в зоне резания.
Высокая температура в зоне резания оказывает непосредственное влияние на износостойкость инструмента, состояние обрабатываемого материала, качество обработанной поверхности детали и производительность процесса резания.
Вопрос 19
Износ резцов. Критерии износа.
Ответ:
При трении любых тел трущиеся поверхности изнашиваются. Величина износа и интенсивность его образования зависят от материала трущихся тел, действующего давления на поверхностях трения, вида смазки, температуры в зоне трения и других факторов.
При резании температура достигает 1000-1200° С, площадки контакта трущихся поверхностей инструмента, стружки и обрабатываемой заготовки небольшие, и следовательно, даже при небольших силах резания, давление на поверхностях трения довольно высокое . Высокая температура в зоне резания является причиной структурных изменений в материале режущего инструмента. При работе резцами, оснащенными пластинками твердого сплава, высокая температура в зоне резания не вызывает структурных изменений в твердом сплаве, но является причиной приваривания (прилипания) сходящей стружки к передней поверхности инструмента. Непрерывно движущаяся стружка вырывает микрочастицы твердого сплава и с большой интенсивностью изнашивает переднюю поверхность.
Высокое давление в местах контакта режущего инструмента и обрабатываемого материала затрудняет проникновение смазочно-охлаждающей жидкости, а значит трение на контактных площадках можно считать близким к сухому трению.
В результате трения стружки о переднюю поверхность резца на последней образуется лунка. На главной задней поверхности, трущейся о поверхность резания, образуется шероховатая площадка, не имеющая заднего угла.
В зависимости от вида обрабатываемого материала, его состояния и условий обработки преобладающим может быть износ по передней или задней поверхности резца. При точении деталей из пластичных (вязких) металлов (сталь, вязкая латунь) с большими скоростями резания и толщиной срезаемого слоя, превышающей 0,1-0,2 мм, преобладающим будет износ по передней поверхности резца.
При точении деталей из хрупких металлов (чугун, бронза, алюминиевокремнистые сплавы) изнашивается главным образом задняя поверхность резца, находящаяся в непрерывном контакте с поверхностью резания и подвергающаяся повышенному абразивному действию со стороны обрабатываемого материала. На переднюю поверхность действует получающаяся стружка надлома, но она не оказывает такого сильного истирающего действия как стружка скалывания или сливная, получающиеся при обработке вязких металлов.
Износ в процессе работы резца происходит следующим образом. В начале работы на передней поверхности резца появляется лунка и фаска, а на задней поверхности - небольшая изношенная площадка. При дальнейшей работе ширина лунки В увеличивается, а ширина фаски уменьшается, увеличивается и изношенная площадка на задней поверхности. Когда ширина фаски приближается к нулю, наступает выкрашивание и прорыв режущей кромки; изношенные площадки на передней и задней поверхностях соединяются. В этот момент обычно происходит резкое увеличение изношенной площадки на задней поверхности и резец теряет свою режущую способность, для восстановления которой его необходимо переточить (снять изношенный слой с передней и задней поверхностей). Таким образом, решающим является износ по задней поверхности, так как от его величины в основном зависит точность и шероховатость обработанных поверхностей, а также режущая способность инструмента.
Для определения момента снятия режущего инструмента со станка и отправки его в переточку существуют принятые критерии износа:
1. Резкое возрастание радиальной силы резания и осевой силы (силовой критерий).
2. Изменение внешнего вида поверхности резания - появление блестящей полоски при обработке деталей из стали или темных пятен (чешуек) при обработке деталей из чугуна.
3. Определенная геометрическая величина износа инструмента (оптимальный износ).
4. Увеличение шероховатости обработанной поверхности при чистовой обработке (технологический критерий).
Вопрос 20
СОТС, их влияние на процесс резания.
Ответ:
Смазачно-охлаждающие технологические средства (СОТС) – это веществапредназначенные для смазки поверхностей трения, охлаждения режущего инструмента и обрабатываемой заготовки, облегчения процесса деформирования металла, своевременное удаление из зоны резаниястружки и продуктов износа инструмента, а также для временной защиты изделий и оборудования от коррозии. Благодаря этому СОТС в значительной мере определяют экономичность и надежность работы многочисленны и разнообразной металлообрабатывающей техники, а именно: увеличивают стойкость режущего инструмента, улучшают качество изделий, снижают силы резания и потребную мощность.
К СОТС относятся.
1. Смазочно-охлаждающие жидкости (СОЖ):
а) вода с небольшой
добавкой веществ, препятствующих коррозии станка и детали (на
пример, соды);
б) эмульсии, представляющие собой растворы в воде специальных эмульсолов и паст, то есть растворы специальных мыл в воде;
в) масла растительные (льняное, сурепное, касторовое), минеральные (индустриальное-20) и осерненные (сульфофрезол– масло индустриальное-20 с добавкой 2...3 % серы);
г) специальные (например, смесь керосина и масла).
2. Распыленные жидкости.
3. Газообразные среды.
4. Твердые смазки.
Применение СОТС оказывает благоприятное действие на процесс резания металлов, значительно уменьшает износ режущего инструмента, повышает качество обработанной поверхности и снижает затраты энергии.
Применение СОТС препятствует образованию нароста у режущей кромки инструмента и способствует удалению стружки и абразивных частиц из зоны резания.
Дата добавления: 2018-02-28; просмотров: 908; Мы поможем в написании вашей работы! |
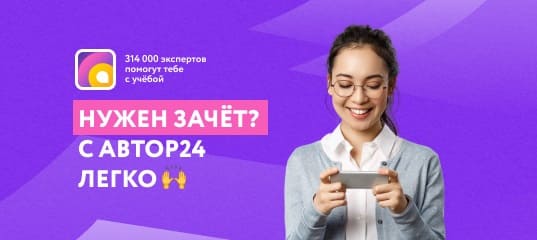
Мы поможем в написании ваших работ!