Раздел Cилы сопротивления резанию при точении
Вопрос 21
Силы, действующие на резец.
Ответ:
В результате сопротивления металла деформированию возникают реактивные силы, действующие на режущий инструмент. Это силы упругого (PУ1 и РУ2) и пластического (PП1 и РП2) деформирования, векторы которых направлены перпендикулярно к передней и главной задней поверхностям резца.
Схема сил, действующих на резец приведена на рисунке 9.
Рисунок 9 Схема сил, действующих на резец
Наличие нормальных сил обусловливает возникновение сил трения (T1 и T2), направленных по передней и главной задней поверхностям инструмента. Указанную систему сил приводят к равнодействующей силе резанияR.
Считают, что точка приложения силы R находится на рабочей части главной режущей кромки инструмента. Абсолютная величина, точка приложения и направление равнодействующей силы резания R в процессе обработки переменны. Это можно объяснить неоднородностью структуры металла заготовки, переменной поверхностной твердостью материала заготовки, непостоянством срезаемого слоя металла (наличие штамповочных и литейных уклонов и другие), изменением углов резца, в процессе резания.
Вопрос 22
Разложение равнодействующей силы, действующей на резец, на составляющие.
Ответ:
В результате сопротивления срезаемого слоя металла деформации сжатия, трения стружки о переднюю поверхность резца и некоторых других причин возникает равнодействующая сила.
|
|
Равнодействующую силу P при обработке точением разлагается на три составляющие (рисунок 10):
- тангенциальнуюPz, направленную вертикально вниз и определяющую мощность, потребляемую главным движением станка;
- радиальнуюРy, направленную вдоль поперечной подачи, она отжимает резец и учитывается при расчете прочности инструмента и устройства механизма поперечной подачи станка;
- осевуюPx, направленную вдоль продольной подачи, она стремится отжать резец в сторону револьверного суппорта и учитывается при определении величины допустимой нагрузки на резец и механизмы станка при продольной подаче.
Рисунок 10 Составляющие равнодействующей силы
Между тремя составляющими силы резания существует примерно следующее соотношение:
Рz:Рy:Рx = 1:(0,25...0,5):(0,10...0,25).
Сила резания Р в большинстве случаев примерно на 10% больше составляющей Рz. Это позволяет многие практические расчеты производить не по силе Р, а по силе Рz.
Вопрос 23
Влияние составляющих Рx, Рy, Рz на резец, заготовку, станок.
Ответ:
Сила резания изгибает резец в вертикальной плоскости, сила
стремится оттолкнуть резец от заготовки, а сила
стремится изогнуть резец в горизонтальной плоскости и вывернуть его из резцедержателя.
|
|
Напряжения, вызванные в державке силами ,
и
, не должны повышать напряжений, допускаемых материалом державки по его прочности и жесткости. В практике, однако, принято рассчитывать резец только на плоский изгиб по силе
, не учитывая деформаций от сил
и
.
Наряду с напряжениями в державке резца сила создает большие напряжения и в режущей части инструмента — в пластинке. В зависимости от значения переднего угла пластинка может испытывать деформации изгиба и среза или деформации сжатия. Для каждого резца сила
должна быть не больше определенной величины, иначе напряжения, вызванные этой силой, достигнут предела прочности пластинки и пластинка разрушится. Это особенно важно для твердосплавных резцов из минералокерамических, алмазных материалов и эльбора Р (вследствие их большей хрупкости).
Силы ,
и
влияют на режущую часть инструмента и в том случае, когда напряжения не достигли ее предела прочности, так как чем больше эти силы, тем интенсивнее протекает износ инструмента (разрушение режущей кромки) в процессе резания.
Если на резец действует сила , то на заготовку в месте резания действует сила
, равная по величине силе
, но обратная по направлению.
|
|
Кроме скручивания заготовки, от действия силы создается момент, изгибающий заготовку в вертикальной плоскости. Для резания необходимо, чтобы момент сопротивления резанию был преодолен вращающим (крутящим) моментом станка, то есть вращающий момент станка на выбранной ступени числа оборотов был бы больше или, в крайнем случае, равен (для расчетов) моменту сопротивления резанию.
Сила изгибает заготовку в горизонтальной плоскости. При недостаточной жесткости системы СПИД эта сила может вызвать в процессе резания вибрации. Складываясь с силой
, они создают силу
, которая будет вызывать суммарный изгибающий момент, действующий на заготовку и влияющий на точность обработанной поверхности.
Сила прижимает заготовку к переднему центру (или стремится сдвинуть заготовку в осевом направлении при креплении ее в патроне) и создает момент который «вывертывает» заготовку из центров.
Сила резания , будучи наибольшей и совпадая с направлением скорости резания, через резец действует на суппорт и станину. Сила
через заготовку действует на центры и заднюю бабку. По этой силе производится расчет ответственных деталей станка и мощности, затрачиваемой на резание (а, следовательно, расчет и необходимой мощности электродвигателя станка).
|
|
Радиальная сила действует через резец на суппорт и станину, а сила
через заготовку — на шпиндель, центры и заднюю бабку станка. По этой силе производится расчет станка на жесткость и расчет радиального давления на подшипники шпинделя.
Сила подачи действует через резец на механизм подачи станка, а сила
через заготовку—на шпиндель и его опоры в осевом направлении. Сила
преодолевается механизмом подачи станка, а потому в основном по ней и рассчитываются детали коробки передач фартука и упорные подшипники шпинделя, а также мощность, необходимая для осуществления движения подачи. Таким образом, силы, действующие в процессе резания, нужно знать для правильного расчета и конструирования режущего инструмента, станков и приспособлений, для расчета жесткости системы СПИД и мощности, затрачиваемой на резание, а также для правильной эксплуатации станка, инструмента и приспособлений.
Вопрос 24
Влияние различных факторов на величину Рx, Рy, Рz.
Ответ:
При токарной обработке глубина резания (ширина среза) оказывает большее влияние на силы резания, чем подача (толщина среза). При этом сила Рz пропорциональна глубине резания и возрастает медленнее, чем подача. Например, если увеличивать подачу в два раза, сила Рz увеличится лишь на 70% . Это объясняется тем, что ширина среза почти не влияет на усадку стружки; с увеличением же толщины среза усадка снижается.
С увеличением угла резания инструмент труднее внедряется в обрабатываемый материал, возрастает пластическая деформация, а значит увеличиваются силы резания; причем в большей мере повышаются силы Рy и Рx. Если с увеличением угла резания на 1° сила Рz увеличится в среднем на 1%, то силы Рy и Рx- на 4-5%.
С увеличением главного угла в плане, при постоянных значенияхглубины резания и подачи увеличивается толщина среза, а следовательно, снижается усадка стружки и силаРz. Но эта зависимость справедлива при обработке стали резцом с нулевым радиусом закругления вершины и обработке чугуна резцом с любым радиусом закругления вершины. При обработке стали резцом с нулевым радиусом закругления вершины сила Рzуменьшается с увеличением главного угла в плане до 60°, затем, с дальнейшим увеличением главного угла в плане, она возрастает. Увеличение силы Рzобъясняется тем, что при главном угле в плане больше 60° резко возрастает длина криволинейного участка лезвия, у которого усадка больше, чем у прямолинейного участка.
Главный угол в плане оказывает значительное влияние на соотношение сил Рy ,Рx. С увеличением w возрастает сила Рx и уменьшается сила Рy . Поэтому при недостаточно жесткой системе станок – деталь - инструмент во избежание вибраций работают резцами с большим главным угломв плане.
Угол наклона главного лезвия в пределах от -5 до +5° не оказывает заметного влияния на силы резания. С увеличением положительного значения угла силы Рz и Рy возрастают, а силаРx уменьшается. При этом значительно повышается сила Рy.
С увеличением радиуса закругления вершины резца силаРz возрастает, так как увеличивается длина криволинейного участка лезвия, а вместе с этим — и усадка стружки. Увеличение радиуса закругления равносильно уменьшению главного угла в плане на закругленном участке лезвия, что приводит к уменьшению силыРx и увеличению силы Рy. С увеличением радиуса закругления от 0,5 до 5 мм при обработке стали сила Рzвозрастает на 27%, сила Рy - на 200%; при обработке чугуна силаРzвозрастает на 18%, сила Py - на 60%. Таким образом, увеличение радиуса закругления вершины резца приводит к значительному увеличению силы Рy.
Вспомогательный угол в плане и задний угол не оказывают значительного влияния на силы резания.
Влияние материала режущей части инструмента на силы резания связано с изменением коэффициента трения. Если для быстрорежущего резца принять силы резания за 100%, то для твердосплавного они составят 90-95%, а для минералокерамического – 88-90%.
С износом инструмента увеличиваются площади контакта на его рабочих поверхностях, возрастает радиус округления лезвия, а вместе с ним и угол резания. Все это приводит к увеличению сил резания, причем особенно увеличиваются силы, действующие на заднюю поверхность. Поэтому при работе изношенным резцом сильно возрастают силы Рy и Рz. Они достигают величины силы Рzи даже могут быть больше ее. Увеличением силы Рy можно объяснить появление или усиление вибраций при работе тупым инструментом.
Влияние смазочно-охлаждающей жидкости на уменьшение сил резания тем больше, чем активнее жидкость. При обработке пластичных металлов сила Pzуменьшается с применением водного раствора электролита на 3—5%, эмульсии - на 7-12%, осерненного масла - на 15-20%. Силы Рy и Рx уменьшаются примерно в 1,5 раза больше, чем сила Рz. Это объясняется тем, что они в большей степени, чем сила Рz, зависят от силы трения на передней поверхности.
Раздел Операция «Сверление»
Вопрос 25
Характеристика процесса сверления.
Ответ:
Сверление представляет собой процесс удаления металла для получения отверстий. Процесс сверления включает два движения: вращение инструмента V (рисунок 11) или детали вокруг оси и подачу S вдоль оси. Режущие кромки сверла срезают тонкие слои металла с неподвижно укрепленной детали, образуя стружку, которая, скользя по спиральным канавкам сверла, выходит из обрабатываемого отверстия.
Рисунок 11 Схема резания при сверлении
Сверло является многолезвийным режущим инструментом. В резании участвуют не только два главных лезвия, но и лезвие перемычки, также два вспомогательных, находящихся на направляющих ленточках сверла, что очень усложняет процесс образования стружки. При рассмотрении схемы образования стружки при сверлении хорошо видно, что условия работы режущей кромки сверла в разных точках лезвия различны. Так, передний угол наклона режущей кромки у (рисунок 12),расположенный ближе к периферии сверла (сечение А—А), является положительным. Режущая кромка работает в сравнительно легких условиях.
Рисунок 12 Образование стружки при сверлении
Передний угол наклона режущей кромки, расположенный дальше от периферии, ближе к центру сверла (сечение В—В), является отрицательным. Режущая кромка работает в более тяжелых условиях, чем расположенная ближе к периферии.
Резание поперечной режущей кромкой (сечение С—С) представляет собой процесс резания, близкий к выдавливанию. При сверлении по сравнению с точением значительно хуже условия отвода стружки и подвода охлаждающей жидкости; имеет место значительное трение стружки о поверхность канавок сверла, трение стружки и сверла об обработанную поверхность; вдоль режущей кромки возникает резкий перепад скоростей резания — от нуля до максимума, в результате чего в различных точках режущей кромки срезаемый слой деформируется и срезается с разной скоростью; вдоль режущей кромки сверла деформация различна — по мере приближения к периферии деформация уменьшается. Эти особенности резания при сверлении создают более тяжелые по сравнению с точением условия стружкообразования, увеличение тепловыделения и повышенный нагрев сверла. Если же рассматривать процесс стружкообразования на отдельных микро участках режущей кромки, то упругие и пластические деформации, тепловыделение, наростообразованне, упрочнение, износ инструмента здесь возникают по тем же причинам, что и при точении. На температуру резания при сверлении скорость резания имеет большее влияние, чем подача.
Вопрос 26
Элементы и углы спирального сверла.
Ответ:
Наиболее распространенным и имеющим универсальное назначение является спиральное сверло. Сверло состоит из рабочей части, конусного или цилиндрического хвостовика, служащего для закрепления сверла, а лапки, являющейся упором при удалении сверла. Рабочая часть сверла представляет собой цилиндрический стержень с двумя спиральными или винтовыми канавками, по которым удаляется стружка.
Элементы спирального сверла показаны на рисунке 13.
Рисунок 13 Элементы спирального сверла
Режущая часть заточена по двум коническим поверхностям, имеет переднюю и заднюю поверхности и две режущие кромки, соединенные перемычкой под углом 55°. На цилиндрической части по винтовой линии проходят две узкие ленточки, центрирующие и направляющие сверло в отверстии. Ленточки значительно уменьшают трение сверла о стенки обрабатываемого отверстия. Для уменьшения трения рабочей части сверла в сторону хвостовика сделан обратный конус. Диаметр сверла уменьшается на каждые 100 мм длины на 0,03—0,1 мм.
Углы спирального сверла приведены на рисунке 14.
Рисунок 14 Углы спирального сверла
Режущая часть сверла изготовляется из инструментальных сталей в твердых сплавов. Как и резец, сверло имеет передний и задний углы (рисунок 14). Передний угол γ(сечениеБ-Б)в каждой точке режущей кромки является величиной переменной. Наибольшее значение уголγимеет на периферии сверла, наименьшее—у вершины сверла. Вследствие того что сверло во время работы не только вращается, но и перемещается. вдоль оси, действительное значение заднего углаαотличается от угла, полученного при заточке. Чем меньше диаметр окружности, на которой находится рассматриваемая точка режущей кромки, и чем больше подача, тем меньше действительный задний угол.
Действительный же передний угол в процессе резания соответственно будет больше угла, замеренного после заточки. Чтобы обеспечить достаточную величину заднего угла в работе(в точках режущей кромки, близко расположенных к оси сверла), а также угла заострения зуба вдоль оси всей длины режущей кромки, задний угол делается: на периферии 8—14°, а у середины 20-27°, задний угол на ленточках сверла равен 0°.
Кроме переднего и заднего углов сверло характеризуется углом наклона винтовой канавки , углом наклона поперечной кромки
, углом при вершине
, углом обратной конусности
.
Вопрос 27
Элементы режимов резания при сверлении.
Ответ:
Элементами режима резания при сверлении являются скорость резания и подача.
Скорость резания при сверлении представляет собой условно окружную скорость сверла относительно обрабатываемой детали и подсчитывается по формуле:
,
где - диаметр сверла, мм;
- число оборотов детали в минуту.
При сверлении углеродистой стали средней твердости, серого чугуна и бронзы сверлами из быстрорежущей стали Р9, Р18 скорость резания можно принимать ; при сверлении углеродистой стали средней твердости сверлами, оснащенными пластинкой твердого сплава ВК8, скорость резания достигает
.
Подача - величина перемещения сверла за один оборот детали в . Подача сверла на токарном станке производится обычно вручную; наряду с этим при сверлении применяют и механическую подачу. При сверлении сверлами диаметром от 6 до 30 мм величина механической подачи должна быть следующей: для углеродистой стали средней твердости от 0,1 до 0,35
; для чугуна - от 0,15 до 0,5
.
Вопрос 28
Силы резания при сверлении.
Ответ:
При сверлении в срезании стружки принимают участие два главных лезвия и перемычка. На каждом из главных лезвий действует сила резания, условно приложенная к точке режущей кромки, лежащей на радиусе . Эту силу резания раскладывают на:
Pz – касательная сила, касательная к окружности, на которой лежит точка приложения равнодействующей силы резания;
Py– радиальная сила, проходящая через ось сверла;
Px– осевая сила, параллельная оси сверла.
На другом главном лезвии действует аналогичная система сил.
Силы резания при сверлении приведены на рисунке 15.
Рисунок 15 Силы резания при сверлении
Силы резания, действующие на перемычке, представляют только осевой силой Pxп(две другие силы, лежащие в плоскости, перпендикулярной оси сверла, во внимание не принимают, так как их влияние на силовые характеристики при резании невелико).
На каждую ленточку (вспомогательную кромку) действуют сила Pzл, направленная по касательной к окружности диаметром D, и осевая Pxл, направленная вдоль оси сверла (обе эти силы по характеру своему – силы трения).
Сумма проекций сил, действующих вдоль оси сверла, на осьх называют осевой силой при сверлении. По ней рассчитывают на прочность детали механизма подачи станка.
Измерения показывают, что 80% общего момента резания приходится на долю главных режущих кромок, 8% – на поперечную кромку и 12% – на трение стружки о сверло и ленточки об обработанную поверхность.
Вопрос 29
Формы заточки сверла.
Ответ:
Задняя поверхность сверла изнашивается в результате трения о поверхность резания, передняя - в результате трения об образующуюся стружку. Затупившееся сверло в процессе работы издает характерный скрипящий звук, свидетельствующий о необходимости его переточки.
Форма заточки оказывает влияние на стойкость сверла и скорость резания. Различают следующие формы заточки сверл: нормальную одинарную и двойную заточку, заточку с подточкой перемычки, с подточкой ленточки и другие.
а - одинарная (нормальная); б - одинарная с подточкой перемычки;
в - одинарная с подточкой перемычки и ленточки; г - двойная с подточкой перемычки; д - двойная с подточкой перемычки и ленточки
Рисунок 16 Основные формы заточки сверл
При двойной заточке на заборном конусе сверла образуется вторая затылованная часть, имеющая угол при вершине . Стойкость сверла с двойной заточкой при обработке стали увеличивается в 2,5—3 раза по сравнению со сверлом с нормальной заточкой.
Подточка ленточки производится на длине 1,5- 4 мм путем снятия затылка под углом 6-8° и образования узкой фаски шириной 0,2-0,3 мм, необходимой для предотвращения защемления и поломки сверла. С такой заточкой стойкость сверла при обработке вязких сталей увеличивается в 2-3 раза.
Подточка перемычки состоит в образовании дополнительных выемок у вершины сверла с обеих сторон вдоль его оси на длину 3-15 мм, после чего длина перемычки сокращается. При этом значительно уменьшается сила подачи, а стойкость сверла увеличивается в 1,5 раза.
Вопрос 30
Основные типы сверл.
Ответ:
Сверла можно разделить на несколько типов.
Цилиндрические спиральные сверла - данный тип имеет обычную цилиндрическую спиральную форму, и такие сверла чаще всего применяются в бытовых нуждах. Изготавливают цилиндрический тип сверла, как правило, из быстрорежущей стали.
Конические сверла - данные сверла, чаще всего используются на специальных, узкопрофильных сверлильных станках. В таком сверле, его хвостовая часть выполнена в форме конуса Морзе 1-5. С помощью данного конуса сверло устанавливается в станок. Назначение таких типов сверл – они необходимы для проделывания больших отверстий, включая размеры, достигающие30 мм.
Корончатые сверла - необходимы для проделывания достаточно больших диаметров. Если, используя конический тип сверла, можно проделать отверстие лишь до 30 мм, то используя корончатые сверла, можно проделывать отверстия значительно больше чем 30 мм. Кроме того, что данное сверло используется для сверления металла, его также можно использовать для проделывания отверстий в бетоне, но только при условии, что сверло сделано не из быстрорежущей стали, а имеет режущую часть из твердых сплавов.
Ступенчатые сверла - основной задачей данного типа сверла является проделывание достаточно больших отверстий. Но, в отличие от остальных видов сверлнасадок, в данном случае ступенчатое сверло является универсальным – с его помощью также можно проделывать и небольшие отверстия необходимого диаметра.
Плоские или перовые сверла - данные сверла необходимы для просверливания крупных по диаметру глубин и отверстий.
Сверла для глубокого сверления – являются разновидностью винтовых сверл, их удлиненной версией с наличием двух винтовых каналов;
Кольцевые или пустотелые сверла – они преобразуют в стружку только определенную узкую часть обрабатываемого материала;
сверла одностороннего резания – имеют направляющую и используются для работ, требующих высокой точности исполнения, подразделяются на пушечные и ружейные;
Центровочные сверла – специально предназначены для сверления так называемых центровых отверстий в деталях.
Для обработки различных материалов могут использоваться сверла, которые являются универсальными в своем применении или узкоспециализированные, к которым относятся:
- сверла для работы с древесиной;
- сверла для работ с хрупкими материалами – керамикой и стеклом;
- сверла для работы с твердыми материалами и подходящие для дрелей ударного типа и перфораторов – они работают с кирпичом, бетоном и камнем;
- сверла для работы с металлами и их различными сплавами.
Дата добавления: 2018-02-28; просмотров: 1416; Мы поможем в написании вашей работы! |
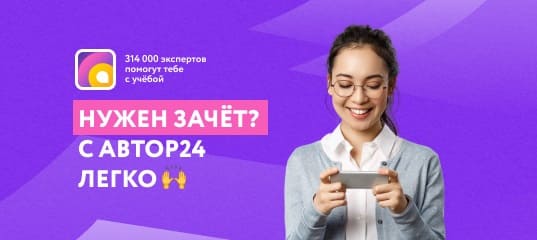
Мы поможем в написании ваших работ!