Технологические методы обеспечения повышения качества поверхности
Классификация:
1. Методы упрочняющей обработки поверхности предназначены для:
а) улучшения физико-механических свойств;
6) повышения твёрдости поверхностного слоя;
в) снижения влияния концентраторов напряжения;
г) повышения предела выносливости.
В результате обработки в поверхностном слое возникают деформационное упрочнение и остаточные напряжения (сжатия или растяжения).
Рассмотрим методы повышения качества поверхности.
1) Дробеструйное деформационное упрочнение - для деталей сложной формы. Повышает в 10 - 12 раз срокслужбы рессор, пружин.
Чеканка - для упрочнения частей ступенчатых валов, сварных швов, зубчатых колес и др.
Обкатывание (раскатывание) роликами и шариками. Дорнование и калибровка отверстия.
4) Обработка стальными щётками - упрочняется слой на глубину 0,04.0,06 мм. Высотные параметрыRa, Rz, Rmax снижаются в 2 - 4 раза.
5) Гидроабразивная обработка. Недостаток - малая глубина наклёпа.
б) Выглаживание алмазным инструментом. Увеличивается в 2 - 4 раза опорная поверхность при той жешероховатости, что и у шлифования, полирования, суперфиниширования (инструмент - алмаз, сапфир, ко-рунд).
Электромеханическая обработка (ЭМО), анодно-механическая и др.
Упрочнение взрывом (пустотелые валы, сварные соединения, лопатки турбин и др.)
Поверхностная закалка - для среднеуглеродистьгх и легированных сталей и чугунов S= 1,5...2 мм. Нагрев - ТВЧ.
Химико-термическая обработка (цементация, азотирование, цианирование, нитроцементация, борирование и т. д.); т.е. насыщение поверхности различными химическими элементами одновременно с термическим воздействием на него.
|
|
Наплавка и напыление металлов - на поверхности появляются растягивающие напряжения, что несколько снижает предел выносливости.
Электроискровое легирование. (Анод - легирующий материал, катод - легируемая поверхность)
Ионно-плазменное напыление.
Преимущества:
прочное сцепление с диффузией легирующего материала;
легирование в строго указанных местах радиусам от 0,5 мм и более;
отсутствие термического воздействии на слой основного металла.
2. Методы повышения коррозионной стойкости поверхностей.
I. Легирование материалов - добавление в сплавы специальных элементов (хром, алюминий, никель и
т.д.).
II. Нанесение на поверхность покрытий:
а) металлических (цинковое, хромовое, никелевое, кадмиевое);
6) неметаллических (неорганических) - анодирование, оксидирование, воронение;
в) неметаллических (органических) - лакировочные, пластмассовые, резиновые, битумные;
г) смазка.
III. Специальные методы:
1) Вибрационное обкатывание - микрорельеф создаётся за счёт вдавливания инструмента, при этом рисунок микрорельефа становитсярассматриваемым.
|
|
2) Применение инструментов из алмаза иди эльбора - позволяет создавать поверхности с оптимальныймикрогеометрией, увеличивая контактную жёсткость.
3) Электрохимические и электрофизические методы.
Электроэрозионная обработка
Электроимпульсная
Электрохимическая
Электромеханическая обработка
Комбинированная или анодно-механическая обработк
Абразивно-жидкостное полирование
Ультразвуковая обработка
Способ окончательной обработки поверхности зависит от технических требований, предъявляемых к готовой детали. С учётом этих требований окончательным способом обработки может быть черновая, чистовая или финишная обработка.
Черновая обработка точением, фрезерованием, сверлением заканчивается изготовлением поверхностей с Ra и 80.. .20 мкм и точностью JT 11 - 14.
Чистовая обработка точением, фрезерованием, зенкерованием, развертыванием, шлифованием заканчивается JT 6 - 9; Ra и 1,25 мкм.
Финишная (шлифование, финиширование, хонингование, полирование, притирка, выглаживание, накатывание) позволяет обеспечить Ra1,25 мкм и менее; JT5. Качество поверхности, получаемое после соответствующего способа обработки, приводится в таблицах.
|
|
ЕСКД, стадии проектирования, виды конструкторских документов
Проектирование изделий судового машиностроения выполняется обязательно в соответствии ЕСКД
ЕСКД (Единая система конструкторской документации)- комплекс стандартов, устанавливающих взаимосвязанные нормы и правила по разработке, оформлению и обращению конструкторской документации, разрабатываемой и применяемой на всех стадиях жизненного цикла изделия (при проектировании, изготовлении, эксплуатации, ремонте и др.).
Стадии разработки
1. Техническое предложение
2. Эскизный роект
3. Технический проект
4. Рабочая конструкторская документация
a. Опытного оброца
b. Серийного или единичного производства
c. Серийного(массового) производства
К конструкторским документам (именуемым в дальнейшем словом "документы") относят графические и текстовые документы, которые в отдельности или в совокупности определяют состав и устройство изделия и содержат необходимые данные для его разработки или изготовления, контроля, приемки, эксплуатации и ремонта.
Виды:
1. Чертеж детали
2. Сборочный чертеж
3. Чертеж общего вида
4. Теоретический чертеж
5. Габаритный чертеж
|
|
6. Электромонтажный чертеж
7. Монтажный чертеж
8. Упаковочный чертеж
9. Схема
10. Спецификация
11. Ведомость спецификаций
12. Ведомость ссылочных документов
13. Ведомость покупных изделий
14. Ведомость разрешения применения покупных изделий
15. Ведомость держателей подлинников
16. Ведомость технического предложения
17. Ведомость эскизного проекта
18. Ведомость технического проекта
19. Пояснительная записка
20. Технические условия
21. Программа и методика испытаний
22. Таблица
23. Расчет
24. Эксплуатационные документы
25. Ремонтные документы
26. Инструкция
Дата добавления: 2018-02-28; просмотров: 551; Мы поможем в написании вашей работы! |
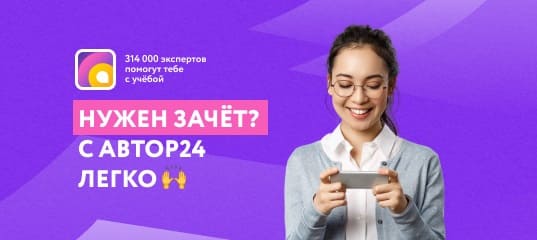
Мы поможем в написании ваших работ!