Типы и конструкции судовых устройств
Судовые устройства. Различаются общесудовые и специальные устройства.
К общесудовым относятся следующие устройства:
1. рулевое,
2. якорное,
3. швартовное,
4. буксирное,
5. леерное
6. кранцевое
7. шлюпочное
8. грузовое
9. тентовое и др.
По приводу различают:
1. электрические
2. гидравлические
3. электрогидравлические
4. паровые
5. дизельные
Конструкции арматуры судовых трубопроводов
Судовыми системами называют сеть трубопроводов с арматурой и механизмами, предназначенную для перемещения жидкостей или газов по судну.
Трубопроводы – В судовых системах они выполняются из стальных труб, которые для защиты от коррозии оцинковывают или покрывают пастой на основе бакелитового лака.
Трубы между собой соединяют с помощью сварки. Сварное соединение труб обычно выполняют встык и только в отдельных случаях внахлестку.
Там где требуется демонтаж используют разъемное соединение(с помощью фланцев)
Для уменьшения напряжений в трубах при их деформации на трубопроводах устанавливают компенсаторы. В большинстве случаев компенсаторы — это небольшой кусок изогнутой трубы. Только в длинных трубопроводах большого диаметра могут применяться компенсаторы сальникового типа.
Арматура. По конструкции и назначению всю арматуру судовых систем можно разделить на следующие группы: клапаны и клапанные коробки; краны и крановые манипуляторы; задвижки и клинкеты; захлопки.
|
|
Наиболее распространенной арматурой в судовых системах являются клапаны.
По способу соединения штока с тарелкой клапаны разделяются на запорные, невозвратные, невозвратно-запорные и невозвратно-управляемые.
В запорном клапане шток соединен с тарелкой без зазора.
Невозвратный клапан штока не имеет.
Невозвратно-управляемый клапан имеет шток, который соединен с тарелкой с зазором.
Качество изделий судового машиностроения. Показатели качества
Качество — это совокупность свойств и характеристик продукции, которые придают ей способность удовлетворять обусловленные или предполагаемые потребности
Качество изделий характеризуется рядом показателей (ГОСТ 15467–79), которые можно разделить на следующие три группы:
1) определяющие технический уровень
2) производственно-технологические
3) эксплуатационные.
Процесс изготовления начинается с изготовления деталей. Важнейшим показателем качества изделия является точность его деталей.
Точность детали характеризуют следующими параметрами:
а) допускаемые отклонения действительных размеров от номинальных;
б) допускаемые отклонения от геометрической формы (овальность, огранка, некруглость, неплоскостность, нецилиндричность, непрямолинейность и т.д.);
|
|
в) допускаемые отклонения поверхностей и осей .
г) допускаемая шероховатость поверхности (микрогеометрические отклонения).
Система качества и его контроль.
Система качественных показателей с установленными на них количественными данными и допусками, описывающая целевое назначение, получила название технических условий и норм точности на приемку готового изделия.
Стандартизация устанавливает оптимальные показатели качества, его параметрические ряды, приемы контроля и испытаний, режимы технического обслуживания, методы ремонта, нормы запасных частей и т.п.
Контроль качества включает:
1. входной контроль качества сырья
2. производственный пооперационный контроль за соблюдением установленного технологического режима, а иногда и межоперационную приемку продукции;
3. систематический контроль за состоянием оборудования
4. контроль моделей и опытных образцов;
5. контроль готовой продукции
Технологическое обеспечение качества обработки и сборки
Необходимая точность обработки может быть достигнута следующими основными методами.
а) Метод пробных рабочих ходов - заключается в индивидуальной выверке устанавливаемой на станок
|
|
заготовки, последовательного снятия стружки с короткого участка путём пробных рабочих ходов, сопровождаемых пробными замерами. Окончательная обработка производится по всей длине заготовки после корректировки положения режущего инструмента по данным пробных замеров.
Достоинства метода:
1. На неточном оборудовании можно получить высокую точность.
2. Исключается влияние износа режущего инструмента на точность, так как при проведении пробных ходов и замеров корректируется положение инструмента.
3. Исключает необходимость пользоваться сложными и дорогостоящими приспособлениями (кондукторами, поворотными и делительными головками и т.д.).
Недостатки:
1. Зависимость достигаемой точности от толщины снимаемой стружки, т.е. нет возможности внести поправку в размер меньше толщины стружки.
2. Высокая квалификация исполнителя.
3. Низкая производительность, высокая себестоимость.
Используется в единичном, мелкосерийном производстве. В серийном - "спасение брака".
б) Метод автоматического получения заданного размера - заключается в том, что партию заготовок обрабатывают на предварительно настроенном станке с установкой заготовок в приспособление без выверки их положения, а режущий инструмент при наладке станка устанавливают на определённый размер, называемый настроечным. Метод более производителен, так как обработка ведётся за один проход, а затраты времени на предвари-тельную наладку раскладываются на всю партию деталей. Применяется в серийном и массовом производстве.
|
|
Преимущества:
1. Повышение точности и снижение брака.
2. Рост производительности.
3. Низкая квалификация рабочих. Применяются также такие методы как:
1) за один проход с установкой размера по лимбу (нужное деление - пробной обработкой одной детали, или по эталону), - мелко-среднесерийное производство;
2) с использованием подналадчика, с использованием устройств, производящих измерение на ходу - автоматизированное производство.
Дата добавления: 2018-02-28; просмотров: 284; Мы поможем в написании вашей работы! |
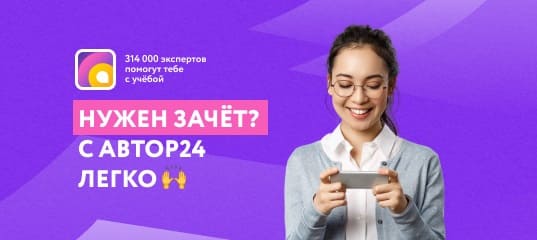
Мы поможем в написании ваших работ!