Шлифованием центровые отврстия подвергают исправлению путём шлифования конусным кругом.
При шлифовании распространены два метода: осциллирующее шлифование , применяемое при обработке поверхностей значительной протяжённости, и врезное шлифование, применяемое при обработке коротких шеек.
В серийном и массовом производствах врезное шлифование часто выполняется по автоматическому циклу, что обеспечивает лучшее качество обработки и повышает производительность. В тех случаях, когда необходимо достигнуть точности размеров, соответствующему 5-му или 6-му квалитетам и шероховатость поверхности Ra=0,1 мкм и меньше, после чистовой шлифовальной операции шейки вала притирают.
При шлифовании размеры деталей часто контролируют в процессе обработки, т.е без остановки станка, что повышает производительность . Используют также измерительные средства активного контроля. Котор. автоматически выключает поперечную подачу при достижении заданного размера.
Описание бесцентрового шлифования.
Заготовка располагается выше осевой линии шлифовальных кругов на размер h. Подача S заготовки вдоль оси осуществляется путём поворота ведущего круга на угол α, который составляет 1-4,5 °. Благодаря этому наклону ведущий круг сообщает заготовке посредством силы трения движение подачи. Бесцентровое шлифование выполняют с продольной подачей и с поперечной подачей ( врезанием). Если вал гладкий, топрименяют шлифование с продольной подачей на проход; если же ступенчатый – шлифуют с продольной подачей до упора. Врезным бесцентровым шлифованием обрабатывают короткие буртики. Бесцентровое шлифование применяют при обработке небольших валов , при этом обеспечивается точность по 6-8-му квалитетам. Этот метод по точности несколько уступает шлифованию на кругло-шлифовальных станках.
|
|
Контроль валов.
Диаметральные размеры , длины ступеней, размеры резьб, шлицев, шпоночных пазов проверяют с помощью предельных скоб, резьбовых и шлицевых колец. Шероховатость поверхности контролируют сличением с эталоном.
Для проверки отклонения от соосности шеек ступенчатый вал укладывают базовыми шейками на призмы контрольного приспособления, а стержнем индикатора касаются пов-ти контролируемой шейки. Поворачивая вал вокруг оси, определяют биение шейки по разности показаний индикатора.
Отклонение от параллельности шлицев или шпоночного паза оси вала устанавливают по разности показаний индикатора в двух крайних положениях, базируя вал на призмах или в центрах.
В крупносерийном и массовом производствах контроль валов производят многомерным прибором с индикаторами или электроконтактными датчиками.
|
|
Технология изготовления коленчатых валов.
Коленчатые валы двигателей внутреннего сгорания явл-ся ответственными и напряжёнными деталями, работающими при воздействии динамических нагрузок, которые передаются валу через поршень и шатун при рабочем процессе двигателя, и инерционных усилий, возникающих при изменении скорости и направления движущихся масс поршней, шатунов, маховиков и др. деталей.
Коленчатые валы делают цельными или составными ( из отдельных частей – колен). В зависимости от числа и расположения цилиндров – коленчатые валы имеют разное число колен и шеек.
Основными элементами коленчатых валов явл-ся коренные и шатунные шейки, щёки, соединяющие коренные и шатунные шейки, передний и задний концы, служащие для передачи движения приводным механизмом и механизмом двигателя. В местах перехода от шеек и концов вала к щекам и фланцам имеются галтели.
Щёки коленчатых валов делают прямоугольными, круглыми или овальными. Для уменьшения массы вала на щеках в ненагруженных местах снимают фаски и скосы; шейки часто выполняют полыми. На щеках в отдельных конструкциях коленчатых валов устанавливают противовесы.
Основные технические требования, предъявляемые к коленчатым валам:
|
|
1. Коленчатые валы должны изготовляться из углеродистых сталей 35,40,50Г и легированных сталей, химический состав которых соответствует ГОСТу 4543. Марка стали оговаривается в чертеже.
2. Механические свойства валов должны соответствовать показателям, установленным ГОСТом 10158 в зависимости от марки стали и категории прочности. Обязательными показателями мех.свойств явл-ся предел текучести, относительное сужение, ударная вязкость и твёрдость. Мех. свойства материалов коленчатых валов после т/о проверяются на образцах, вырезанных из детали.
3. Твёрдость НRC шеек, подвергаемых поверхностной закалке, должна быть не менее 52 для валов, изготовляемых из стали 45 и 50Г, и не менее 48 для валов из легированных сталей. Галтели закалке не подвергаются.
4. Чистота обработки поверхности шеек диаметром до 100 мм должна быть не ниже 9 класса , а шеек диаметром более 100 мм и галтелей шеек 8-го класса; чистота обработки коренных шеек, монтируемых на подшипниках качения , должна быть 7-го класса.
5. Диаметры коренных и шатунных шеек требуется обрабатывать по 2-му классу точности. Овальность шеек диаметром до 260 мм не должна выходить за пределы поля допуска скользящей посадки 1-го класса точности, а шеек диаметром более 260 мм должна быть в пределах допуска скользящей посадки 2-го класса точности.
|
|
6. Биение коренных шеек и шейки под распределительную шестерню относительно оси вала не должна превышать 0,03 мм для валов с Ø шеек до 100 мм; 0,04 мм для валов с Ø шеек 100-180 мм; 0,05 мм для валов с Ø шеек 180-260 мм и 0,06 мм для валов больших размеров.
7. Допускается отклонение радиуса кривошипа не более ± 0,15 мм на 100 мм радиуса.
8. Смещение углов между коленами кривошипов, а также между шпоночным пазом распределительной шестерни и осью базового кривошипа допускается не более ±30´.
9. Биение торцов соединительных фланцев при жёстком креплении маховика или муфты допускается не более 0,005 мм на 100 мм Ø фланца, при прочих соединениях – не более 0,03 мм на 100 мм Ø фланца.
10. Каждый вал должен быть динамически сбалансирован. одно и двухступенчатые валы, а также валы , работающие с числом оборотов в минуту менее 1000, допускается балансировать статически. Допускаемый дисбаланс указывается в чертеже.
Требования к коленчатым валам, подвергаемым азотированию, хромированию и механическому уплотнению галтелей, указывается в чертеже.
Заготовки коленчатых валов получают свободной ковкой , штамповкой и отливкой.
Свободной ковкой получают заготовки валов крупных двигателей, выпускаемых малыми партиями, для которых нецелесообразно делать сложные и дорогие штампы. Сложная конфигурация коленчатого вала не позволяет изготовить свободной ковкой заготовку, в достаточной степени приближающуюся к конфигурации готовой детали, и при обработке шеек приходится удалять большое кол-во металла.
Заготовки валов , выпускаемых значительными сериями, в закрытых штампах. Это позволяет снизить расход металла, улучшить его структуру и снизить трудоёмкость изготовления вала в заготовительных и механических цехах.
Заготовки коленчатых валов быстроходных двигателей в серийном производстве получают штамповкой в закрытых штампах их проката последовательно в нескольких ручьях одного штампа или двух штампов. Сначала производят гибку заготовки в гибочном ручье штампа, затем штамповку в предварительном ручье. Потом производят отрезку облоя, окончательную штамповку. Фланцы на конце вала обычно штампуют в отдельной операции на горизонтально- ковочных машинах. При изготовлении заготовки коленчатых валов как одно целое с ним отковывают бруски, из которых после совместной т/о вырезают образцы для контроля механических свойств материала.
Крупные валы ( для тепловозных и стационарных двигателей) изготовляют в земляных формах: шейки их обычно отливают полыми, что позволяет избежать большой разницы в толщине стенок отливки и обеспечить более равномерную структуру материала.
Коленчатые валы небольших размеров ( для автомобильных, тракторных двигателей) отливают в оболочковых формах.
Литые заготовки коленчатых валов получают из модифицированного легированного чугуна и высокопрочного чугуна с шаровидным графитом. Литые заготовки подвергают рентгенографическому контролю для выявления внутренних скрытых раковин.
Обработка элементов коленчатых валов.
Коленчатые валы обладают относительно небольшой жёсткостью и легко деформируются под действием радиальных и осевых нагрузок, поэтому при обработке , особенно чистовой, надо принимать меры, предотвращающие деформацию.
Обработка коленчатых валов ведётся обычно в три этапа:
черновая, чистовая и отделочная.
В том случае, когда заготовки коленчатых валов получают свободной ковкой , обработка ведётся в три этапа: обдирка, черновая, чистовая и отделочная обработка.
Черновая и чистовая обработка коренных шеек и концов крупных коленчатых валов производятся на токарных станках. Для устранения деформации вала в центрах обрабатывают только шейки, расположенные близко к концам , затем вал устанавливают этими шейками в люнеты, после чего обрабатывают другие шейки. Одновременно с этим обрабатывают торцовые поверхности, контуры и скосы щёк, т.е все поверхности , оси вращения которых совпадают с осью коренных шеек.
У валов небольших размеров коренные шейки часто обрабатывают на многорезцовых специальных токарных станках с двусторонним или центральным приводом. Вал устанавливают обработанными средней или крайними шейками во вращающийся люнет или специальные патроны. Одновременно обрабатываются часть или все свободные от зажима коренные шейки и торцовые поверхности щёк. Каждая шейка и пара щёк обрабатывается тремя призматическими резцами : два резца переднего суппорта обрабатывают торцовые поверхности щёк, галтели и прилегающие к ним части шейки, а третий резец заднего суппорта – среднюю часть шейки. Резцы работают как фасонные, с радиальной подачей. Вследстие того, что резцы расположены с двух сторон обрабатываемой шейки, уменьшается деформация вала.
Черновую и чистовую обработку производят на одинаковых станках, которые отличаются только настройкой ( размерами посадочных мест в патронах и люнетах, размером и формой резцов).
Специфической операцией при изготовлении коленчатых валов явл-ся обработка шатунных шеек и поверхностей щёк, оси которых не совмещены с осью коренных шеек.
Для обработки шатунных шеек крупных коленчатых валов широко применяют станки с вращающимся суппортом.
Коленчатый вал закрепляют коренными шейками в призмы стоек, установленных на станине станка. Совмещение оси обрабатываемой шейки с осью вращения резцов достигается путём разворота вала и смещения корпуса по направляющим в поперечном направлении. На призматических направляющих , укреплённых на кольце, которое вращается в корпусе при помощи червячной пары, перемещаются два суппорта. Подача суппортов осуществляется от эл. двигателя с редуктором через ходовые винты. Установку вала проверяют при помощи скобы, которой измеряют расстояние от вращающегося кольца до накерненного на щеке центра шейки.
Подрезание щёк производится одновременно двумя резцами, движущимися навстречу друг другу. Протачивание шейки производится резцами, установленными на размер, при движении корпуса по направляющим вдоль оси шейки.
Обтачивание шатунных шеек небольших валов при большом выпуске производится на станках с двусторонним приводом; при этом вкладыши в патронах для установки вала смещены на величину радиуса кривошипа. С одной установки обрабатывают шейки, расположенные на одной оси. Угловое положение вала в патроне при обработке крайних шатунных шеек фиксируют по базовой площадке или риске на щеке, а при обработке остальных шеек – по обработанной крайней шатунной шейке. Обработка ведётся двумя резцами с переднего суппорта иодним резцом с заднего суппорта, также при обработке коренных шеек.
Прямоугольные щёки коленчатых валов обрабатывают на вертикально- фрезерных или продольно- фрезерных станках торцовыми фрезами.
Щёки круглой формы обрабатывают на токарных станках , преимущественно с двусторонним приводом, аналогично обработке шатунных шеек. Обработку обычно ведут проходными резцами с продольной подачей.
Щёки овальной формы обрабатывают или по частям такими же способами, как и круглые щёки, или на токарно- копировальных многосуппортных станках, конструктивно подобных станкам для обработки кулачковых валов.
Шейки коленчатых валов после чистового обтачивания подвергают отделочной обработке.
Шейки очень крупных валов подвергают отделочной обработке на токарных станках одновременно с чистовым обтачиванием. Эта работа ведётся вручную рабочими высокой квалификации. Форму поверхности шеек проверяют на краску по эталонным стальным вкладышам, а размеры и взаимное положение шеек микрометрами и индикаторами.
Шлифование коренных шеек производят с установкой вала в центрах и люнетах. При шлифовании крупных валов установку люнетов проверяют путём контроля изменения расстояния
Между щеками индикаторным приспособлением. Если вал при вращении изгибается , расстояние между щеками изменяется. Допускается изменение расстояния между щеками не более 0,01-0,02 мм. Регулировкой люнетов достигается правильное положение оси вала, и в этом положении шлифуются шейки.
При шлифовании шеек на специализированных станках размеры контролируют индикаторной трёхконтактной скобой.
Шейки валов после шлифования полируют или подвергают суперфинишированию.
К шейкам коленчатого вала, вращающегося в центрах станка прижимаются абразивные бруски головок для суперфиниширования. Головки закреплены на коленчатых валах, вращающихся синхронно с обрабатываемой деталью, вследствие чего обеспечивается постоянный контакт брусков с шейками. Вращающийся от эл. двигателя эксцентриковый палец сообщает брускам возвратно- поступательные движения вдоль шейки. Работа ведётся с обильным охлаждением детали керосином.
Полирование шеек производят на подобных станках, но у них вместо абразивных брусков закреплены жимки , охватывающие шейку вала и прижимающие к обрабатываемой поверхности мелкозернистую шлифовальную шкурку.
Для подвода смазки к подшипникам в шейках и щеках коленчатых валов деталей делают отверстия. Эти отверстия имеют малый Ø (6-10 мм)и большую глубину. В мелкосерийном производстве обработку отверстий для смазки производят по кондукторам на радиально- сверлильных станках. В крупносерийном производстве и массовом для этого используют специальные станки , часто многошпиндельные , работающие с частыми отводами для удаления стружки, или автоматические линии.
Схема технологического процесса обработки коленчатого вала в условиях мелкосерийного производства ( заготовка – поковка).
№п.п | Операция. | Оборудование. | Приспособление. | Инструмент. |
1 | Разметка заготовки для обдирки. | Разметочная плита. | Домкраты, кубики. | Рейсмус, рулетка. |
2 | Фрезерование торцов заготовки и свер- ление центровых отверстий. | Горизонтально-расточной станок. | Клинья, прихваты. | Сверло, зенковка, торцовая фреза. |
3 | Обдирка концов, коренных шеек и щёк. | Токарный 2-х суппортный станок. | Патрон, люнеты. | Резцы. |
4 | Разметка для предварительной обработ- ки контуров щёк. | Разметочная плита. | Домкраты, кубики | Рейсмус, транспор- тир, линейка. |
5 | Предварительное фрезерование кон- туров щёк по разметке. | Продольно-фрезерный станок. | Призмы, домкра- ты, прихваты. | Торцовая наборная фреза. |
6 | Разметка колен кривошипов. | Разметочная плита. | Призмы. | Рейсмус, рулетка. |
7 | Сверление отверстий в углах кривоши- пов. | Радиально- сверлильный станок. | Призмы, подстав- ки, прихваты. | Свёрла. |
8 | Долбление кривошипов. | Долбёжный станок. | Подставки, прих- ваты. | Долбёжный резец. |
9 | Обдирка шатунных шеек и щёк. | Станок с вращающимся суппортом. | Призмы, прихваты. | Резцы. |
10 | Отрезание образцов и сверление цент- ровых отверстий.Т/о , испытания образ- цов, очистка окалины. | Токарный станок. Закалоч- ные и отпускные печи, ванны для охлаждения. | Патрон, люнеты. | Резцы, свёрла. |
11 | Разметка для токарной обработки с про- веркой размеров заготовки. | Разметочная плита. | Призмы, домкра- ты. | Рейсмус, рулетка, линейка. |
12 | Обтачивание коренных шеек, фланцев, щёк,скосов с припуском 5 мм на сторон | Токарный 2-х суппортный станок. | Патрон, люнеты. | Резцы. |
13 | Обтачивание шатунных шеек, щёк с припуском 5 мм на сторону. | Станок с вращающимся суппортом. | Призмы, прихваты | Резцы. |
14 | Центрирование вала со стороны фланца. | Токарный 2-х суппортный станок. | Патрон, люнеты. | Резцы, свёрла. |
15 | Обтачивание коренных шеек и фланцев с припуском 1,5 мм на сторону, щёк с припуском 1 мм на сторону. | Токарный 2-х суппортный станок. | Патрон, люнеты. | Резцы. |
16 | Обтачивание шатунных шеек с припус- ком 2,5 мм на сторону, щёк с припуском 1 мм на сторону до окончательных раз- меров. | Станок с вращающимся суппортом. | Призмы, прихваты | Резцы. |
17 | Фрезерование контуров щёк до оконча- тельного размера. | Продольно- фрезерный станок. | Установочное. | Скоростная фреза. |
18 | Чистовое обтачивание коренных шеек и концов с припуском для шлифования 0,5 мм на сторону и чистовое обтачива- ние щёк до окончательного размера. | Токарный 2-х суппортный станок. | Патрон, люнеты. | Резцы. |
19 | Чистовая обработка шатунных шеек с припуском для шлифования 0,5 мм на сторону и чистовая обработка щёк до окончательного размера. | Станок с вращающимся суппортом. | Призмы, прихваты | Резцы. |
20 | Шлифование коренных шеек , галтелей, и буртиков щёк. | Специальный круглошлифо. станок. | Патрон, люнеты. | Шлифовальный круг. |
21 | Отрезка технологических концов, обтачи- вание фланца, центрирование. | Токарный 2-х суппортный станок. | Патрон, люнеты. | Резцы, свёрла. |
22 | Контроль размеров. | Контрольная плита. | - | - |
23 | Сверление, зенкерование, развёртывание и подрезание отверстий во фланце. | Горизонтально- расточной станок. | Кондукторы. | Свёрла, зенкеры, развёртки. |
24 | Сверление и зенкерование отверстий для смазки. | Специальный сверлильный станок. | - | Свёрла, зенкеры. |
25 | Фрезерование шпоночной канавки. | Шпоночно- фрезерный станок. | - | - |
26 | Балансировка. | Установка для статической балансировки. | Призмы. | Фреза. |
27 | Доводка галтелей и шеек после шлифова- ния. | Слесарный стенд. | Полировальники, напильники, шаберы. | |
28 | Полирование коренных и шатунных шеек | Токарный станок. | Патрон, вращаю- щийся центр. | Специальные жимки. |
29 | Окончательный контроль. | Контрольная плита. | Призмы. | Микрометры, скобы, шаблоны. |
Рис. 7.4. Совмещенный чертеж заготовки и обработанной детали с поэлемент-
ным членением припуска под обработку (номера элементов припуска даны со-
гласно последовательности обработки)
Рис. 7.4. Совмещенный чертеж заготовки и обработанной детали с поэлемент-
ным членением припуска под обработку (номера элементов припуска даны со-
гласно последовательности обработки)
Рис. 7.4. Совмещенный чертеж заготовки и обработанной детали с поэлемент-
ным членением припуска под обработку (номера элементов припуска даны со-
гласно последовательности обработки)
Рис. 7.4. Совмещенный чертеж заготовки и обработанной детали с поэлемент-
ным членением припуска под обработку (номера элементов припуска даны со-
гласно последовательности обработки)
Основные операции механической обработки.
Заготовительная .
Для заготовок из проката : рубка прутка на прессе или резка прутка на фрезерно- отрезном станке. Для заготовок , получаемых методом пластического деформирования, штамповать или ковать заготовку.
Правильная .( применяется для проката).
Правка заготовки на прессе или другом оборудовании. В массовом производстве может производиться до отрезки заготовки. В этом случае правится весь пруток на правильно- калибровочном станке.
Термическая .
Улучшение, нормализация.
Подготовка технологических баз.
Обработка торцев и сверление центровых отверстий. В зависимости от типа производства операцию производят:
- в единичном производстве подрезку торцев и центрование на универсальных токарных станках последовательно за два установа с установкой заготовки по наружному диаметру в патроне;
- в серийном производстве подрезку торцев выполняют раздельно о центрования на продольно- фрезерных или горизонтально- фрезерных станках, а центрование – на одностороннем или двустороннем центровальном станке. Применяются фрезерные полуавтоматы последовательного действия с установкой заготовки по наружному диаметру в призмы и базированием в осевом направлении по упору;
-в массовом производстве применяют фрезерно- центровальные станки барабанного типа, которые одновременно фрезеруют и центруют две заготовки без съёма их со станка.
Форму и размеры центровых отверстий назначают в соответствии с их технологическими функциями по ГОСТ 14034-74.
Для нежёстких валов ( отношение длины к диаметру более 12) – обработка шеек под люнеты.
Токарная( черновая) :
Выполняется за два установа на одной операции ( единичное производство) или каждый установ выполняется как отдельная операция.
Производится точение наружных поверхностей ( с припуском под чистовое точение) и канавок. Это обеспечивает получение точности IT12, шероховатости Ra=6,3. В зависимости от типа производства операцию выполняют:
- в единичном производстве на токарно- винторезных станках;
-в мелкосерийном – на универсальных токарных станках с гидросуппортами и станках с ЧПУ;
- в серийном – на копировальных станках, горизонтальных многорезцовых, вертикальных одношпиндельных п/автоматах и станках с ЧПУ;
- в крупносерийном и массовом – на многошпиндельных многорезцовых п/автоматах; мелкие валы могут обрабатываться на токарных автоматах.
Токарная( чистовая):
Аналогична приведённой выше. Производится чистовое точение шеек (с припуском под шлифование). Обеспечивается точность IT11…10, шероховатость Ra=3,2.
Фрезерная:
Фрезерование шпоночных канавок, шлицев, зубьев, всевозможных лысок. Шпоночные пазы в зависимости от конструкции обрабатывают дисковой фрезой ( если паз сквозной) на горизонтально- фрезерных станках. В серийном и массовом производствах для получения глухих шпоночных пазов применяют шпоночно- фрезерные п/автоматы, работающие « маятниковым» методом.
Технологическая база – поверхности центровых отверстий или наружные цилиндрические поверхности вала. При установке на наружные цилиндрические поверхности вала ( на призмы) возникает погрешность базирования, связанная с колебаниями диаметров установочных шеек вала в партии.
Шлицевые поверхности на валах чаще всего получают обкатыванием червячной фрезой на шлицефрезерных или зубофрезерных станках с установкой вала в центрах. При диаметре вала более 80 мм шлицы фрезеруют за два рабочих хода.
Сверлильная.
Сверление всевозможных отверстий.
Резьбонарезная.
На закаливаемых шейках резьбу изготавливают до термообработки. Если вал не подвергается закалке, то резьбу нарезают после окончательного шлифования шеек ( для предохранения резьбы от повреждения). Мелкие резьбы у термообрабатываемых валов получают сразу на резьбошлифовальных станках.
Внутренние резьбы нарезают машинными метчиками на сверлильных, револьверных и резьбонарезных станках в зависимости от типа производства.
Наружные резьбы нарезают:
- в единичном и мелкосерийном производствах на токарно- винторезных станках плашками, резьбовыми резцами или гребёнками;
- в мелкосерийном и серийном производствах резьбы не выше 7-ой степени точности нарезают плашками, а резьбы 6-ой степени точности – резьбонарезными головками на револьверных и болторезных станках;
-в крупносерийном и массовом производствах – гребёнчатой фрезой на резьбофрезерных станках или накатыванием.
Термическая.
Закалка объёмная или местная согласно чертежу детали.
Исправление центровых отверстий ( центрошлифовальная).
Перед шлифованием шеек вала центровые отверстия, которые явл-ся технологической базой, подвергают исправлению путём шлифования конусным кругом на центрошлифовальном станке за два установа или притираются.
Шлифовальная.
Шейки вала шлифуют на круглошлифовальных или бесцентрово- шлифовальных станках.
Шлицы шлифуют в зависимости от центрирования:
- при центрировании по наружной пов-ти- наружное шлифование на круглошлифовальных станках и шлифование боковых пов-тей на шлицешлифовальном п/автомате с делением;
- при центрировании по пов-ти внутреннего диаметра- шлифование внутренних пов-тей по диаметру профильным кругом.
Моечная.
Контрольная.
Нанесение антикоррозионного покрытия.
В настоящее время разработаны типовые технологические процессы м/о валов на основе разновидности их в различных типах производства.
Анализ рабочего чертежа деталей класса валов позволяет сделать следующие заключения:
-основными конструкторскими базами явл-ся ось детали и торец, от которых заданы размеры;
-двустороннее расположение ступеней с равномерным перепадом диаметров не затрудняет процесс обработки;
- в массовом и крупносерийном производстве заготовки получают методом штамповки или специального профильного проката.
Схема технологических процессов изготовления деталей класса вал:
Номер операции. | Наименование и краткое содержание операции, технологические базы. | Оборудование. |
005 | Фрезерно-центровальная. Фрезерование торцов вала и сверление центровых отверстий с двух сторон. Технологическая база –наружные поверхности двух шеек . | Фрезерно- центровальный п/автомат. |
010 | Токарная. Обтачивание поверхностей шеек вала с одной стороны и подрезание торцевых поверхностей ступеней вала. Технологическая база- центровые отверстия вала. | Токарный многорезцовый или многошпиндельный п/автомат. |
015 | Токарная. Обтачивание поверхностей шеек вала с другой стороны, а также подрезка обрабатываемых шеек вала. Технологическая база – центровые отверстия вала. | То же. |
020 | Токарная. Обтачивание поверхностей шеек вала под шлифование и окончательная подрезка торцов ступеней вала ( если отдельные торцы ступеней подлежат шлифовке, необходимо оставлять припуск под шлифовку). Технологическая база – центровые отверстия вала. | Токарный многорезцовый , гидрокопировальный , многошпиндельный . |
025 | Токарная. Обтачивание поверхностей шеек вала под шлифование и окончательная подрезка торцов ступеней вала с другой стороны. Технологическая база – центровые отверстия вала. | То же. |
030 | Контроль промежуточный. | |
035 | Термическая обработка НRСэ 41…45 | |
040 | Шлифовальная. Предварительное шлифование шеек вала в зависимости от требований чертежа по качеству поверхностей и точности обработки. Технологическая база – центровые отверстия вала. | Круглошлифовальный п/автомат. |
045 | Шлифовальная. Окончательное шлифование поверхностей шеек вала согласно размерам по рабочему чертежу и шероховатостей поверхностей. Технологическая база – центровые отверстия вала. | То же. |
050 | Моечная. | |
055 | Контроль окончательный. |
Примечание: При наличии у детали других элементов (отверстий, шпоночных пазов, резьб и т.д) их обработку производить в установленной технологической последовательности до т/о.
Тема 4.2 Технология изготовления деталей типа втулок, фланцев.
Черновая обработка цилиндрических поверхностей .
Закрепление заготовки при черновой обработке производится в зависимости от формы, размеров и назначения детали. Закрепление заготовки должно быть прочным, т.к при черновом обтачивании резцы снимают стружку больших сечений и при этом возникают значительные силы резания.
Резцы для чернового обтачивания снимают стружку больших сечений при высокой скорости резания. Поэтому резец должен быть прочным. Форма резца должна быть такой, чтобы отделение стружки происходило с возможно большей лёгкостью.
Проходные упорные резцы применяют при обработке заготовок с уступами небольших размеров. Главный угол в плане этих резцов = 90°, что способствует уменьшению вибраций в процессе работы. Для нежёстких деталей необходимо применять упорные резцы. Проходные резцы , используемые при обработке заготовок из стали и чугуна, изготовляют из быстрорежущей стали, а также из твёрдого сплава. При черновой обработке заготовок из стали по корке с неравномерным припуском и переменной нагрузкой.
Обработку заготовок из стали с небольшой глубиной резания с относительно равномерным припуском производят резцами из сплавов Т14К8, Т15К6, Т15К6Т.
При черновой обработке заготовки из чугуна с неравномерным припуском и переменной нагрузкой применяют резцы из твёрдого сплава ВК2, ВК4.
Величина переднего угла γ у быстрорежущих проходных резцов выбирается в зависимости от обрабатываемого материала, формы передней поверхности резца.
Задний угол α выполняют = 12° при подачах до 0,2 мм\об и 8° - при больших подачах.
Главный угол в плане φ для резцов , предназначенных для обтачивания ступенчатых заготовок большой длины и малого Ø , принимают = 90°. При обработке заготовок малой жёсткости φ=65°…70°, более жёстких заготовок 30°…60°. Радиус вершины резца при подаче до 0,2 мм/об – 0,5…5 мм, а при подаче свыше 0,2 мм/об – 1…3 мм.
Чистовая обработка цилиндрических поверхностей.
Закрепление детали при чистовой обработке должно быть прочным, чтобы не могло быть смещения заготовки во время обработки. При закреплении заготовки в самоцентрирующемся патроне за обработанную поверхность при требовании соосности обработанной и обрабатываемой поверхностей следует учитывать неточность патрона.
Резцы для чистового обтачивания должны давать чистую поверхность. В соответствии с этим требованием и выбирают форму.
Для получения меньшей шероховатости поверхности передний угол резца должен быть больше. Задний угол α резцов для чистовой обработки при обтачивании заготовок из стали = 12°, а при обработке заготовок из серого чугуна = 10°.
Существует два метода точения цилиндрических поверхностей.
Обтачивание методом радиальной подачи применяют при обработке коротких цилиндрических шеек канавочными и широкими резцами.
Обтачивание методом продольной подачи явл-ся наиболее распространённым методом обработки.
Обрабатываемая деталь , закрепляемая в центрах или в патроне, вращается, а резцу сообщается движение подачи.
Цилиндрические поверхности обычно обтачивают в два или несколько рабочих ходов: сначала снимают поочерёдно большую часть припуска ( до 6 мм на Ø), а затем оставшуюся часть ( до 1 мм на Ø).
Для получения необходимых размеров Ø вала пользуются лимбом поперечной подачи и устанавливают резец на заданный размер по методу пробных рабочих ходов. Обработка с применением лимбов обеспечивает точность по 8…9-му квалитетам. У большинства современных
Токарных станков имеется также продольный лимб, применение которого даёт возможность получать продольные размеры с точностью до 0,2 мм.
Поверхность тел вращения , ограничивающие элементы деталей, могут быть цилиндрическими, коническими, фасонными и торцовыми –плоскими и фасонными.
Обработка наружных поверхностей тел вращения производится на токарных револьверных и карусельных станках, на токарных автоматах и п/автоматах, многорезцовых станках, а также на станках для доводки и суперфиниширования.
Методы обработки наружных поверхностей тел вращения выбирается в зависимости от конструкций и жёсткости деталей и требований к точности и чистоте обработки.
Для достижения 5-7-го классов точности применяется однократное обтачивание , если позволяет величина припуска. При необходимости обеспечить точность 4-го класса и чистоту 5-6-го класса после чистовой обработки производят чистовое обтачивание с небольшой глубиной резания и подачей. Точность 3-го класса с чистотой 7-8-го класса обеспечивается шлифованием за одну операцию, а точность 2-го класса с чистотой 8-9-го класса – черновым и чистовым шлифованием или однократным шлифованием повышенной точности.
При обработке деталей из цветных металлов точности 2-го класса можно достигнуть тонким обтачиванием. Особо точные детали, с допусками 1-го класса и точнее и чистотой до 12-го класса, обрабатываются путём тонкого шлифования с малыми припусками, а также притиркой и суперфинишированием.
На токарных станках может производиться обтачивание наружных цилиндрических , конических, торцовых и фасонных поверхностей, растачивание , сверление, рассверливание, зенкерование и развёртывание отверстий, нарезание наружных и внутренних резьб, отрезка.
Длинные детали обрабатываются в центрах, короткие в патроне, на центровой, консольной оправках или в центрах, если они являются базой для дальнейшей обработки.
Для установки детали в центры токарного станка в торцах детали должны быть сделаны центровые отверстия . Центровые отверстия выполняются по ОСТу 3725 с углом 60° . У простых деталей центровые отверстия без защитной фаски, у крупных и сложных деталей с длительным циклом – с защитной фаской под углом 120° или с предохранительной выточкой и резьбой в цилиндрическом отверстии.
Центрование производится комбинированными центровыми свёрлами или спиральными свёрлами и коническими зенковками.
На токарных станках целесообразно выполнять операции получистовые с точностью 4-5-го классов, а чистовую обработку производить на шлифовальных станках.
При обработке деталей типа поршней двигателей производят тонкое обтачивание при небольшой глубине резания и малой подаче, обеспечивающее 2-й класс точности и чистоту обработки 7-8-го класса. Для этого применяют стали с жёсткими шпинделями, смонтированными на точных подшипниках и хорошо пригнанными по направляющим суппорта.
Обработку ступенчатых и фасонных деталей целесообразно производить на токарных станках, используя копировальные устройства.
Технология производства цилиндров.
Цилиндры , например, гидросистем, изготовляют с внутренним Ø 50…280 мм при отношении длины к диаметру 4…12. Заготовками для цилиндров служат горячекатаные стальные трубы. Наиболее распространены цилиндры с внутренним Ø 80…140 мм. Зеркало большинства цилиндров обрабатывают с точностью , соответствующему 8-му квалитету при шероховатости Rа= 0,63…0,16 мкм.
Трубы разрезают на заданную длину на фрезерно- отрезных станках, обтачивают на многорезцовых токарных п/автоматах. Поверхности отверстий обрабатывают в три перехода: черновое растачивание, чистовое растачивание и раскатывание отверстия.
Растачивают отверстия на специальных расточных станках инструментом с двухрезцовыми пластинами из твёрдого сплава Т15К6. Припуск под чистовое растачивание оставляют 0,5…0,8 мм., под раскатывание 0,02…0,04 мм.
Раскатывание выполняют многороликовой раскаткой. При раскатывании отверстий больших Ø самоподача инструмента из-за его значительной массы затрудняется , приходится применять подачу от механизма станка.
Обтачивание фасонных поверхностей тел вращения на токарных, револьверных и карусельных станках, на автоматах и п/автоматах производится тремя основными способами:
1) Вершиной резца, который перемещаясь по заданной кривой относительно оси вращения и на заданном от неё расстоянии, определяет форму и размеры поверхности;
2) Лезвием фасонного резца, который перемещаясь перпендикулярно или под углом к оси вращения , врезается в деталь и придаёт ей соответствующую форму и размеры;
3) Методом обкатки при качении дискового инструмента по образующей.
Обработка поверхности по копиру производится на токарных станках , оснащённых копировальными приспособлениями, при помощи гидрокопировальных или электрокопировальных устройств, а также на станках с программным управлением, у которых требуемая траектория движения резца обеспечивается заданными программой скоростями поперечной и продольной подач.
При использовании копировальных устройств автоматизируется процесс обработки фасонных поверхностей; функции рабочего заключаются в замене обрабатываемых деталей и настройке станка.
При обработке конических поверхностей , кроме указанных способов обработки фасонных поверхностей, могут быть использованы:
1) Обтачивание фасонными резцами;
2) Обтачивание при повороте верхних салазок суппорта на угол α, равный половине угла при вершине конуса детали;
3) Обработка при смещении заднего центра; при этом ось вращения детали располагается под углом к направлению движения суппорта. Величина смещения h определяется в зависимости от угла α конуса и длины l детали : h=l·tgα. Этим способом обрабатывают пологие конические поверхности;
4) Обработка при помощи копирной линейки, которая явл-ся нормальной принадлежностью к некоторым станкам.
Для обтачивания выпуклых и вогнутых сферических поверхностей применяют приспособления, обеспечивающие движение острия резца по окружности.
Обработка наружных поверхностей тел вращения абразивными инструментами.
Шлифованием можно легко выдержать допуски по 1-2 му классу точности. При правильном подборе абразивного инструмента и режимов работы обеспечивается чистота поверхности 8-9 го класса, а при тонком шлифовании 10-го класса.
Шлифование наружных поверхностей тел вращения производится на круглошлифовальных и бесцентрово-шлифовальных станках.
На круглошлифовальных станках обработка деталей ведётся в центрах или центровых оправках. Обработка в патроне и консольных оправках производится редко, т.к. при обработке детали, закреплённой на вращающемся шпинделе, его биение, овальность шеек, неточности и зазоры в подшипниках влияют на точность изделия.
Деталь при шлифовании устанавливается в неподвижные центры станка и при помощи хомутика приводится во вращение. Стол станка, на котором установлена передняя и задняя бабки, перемещается по направляющим станины. Поперечная подача осуществляется путём перемещения бабки шлифовального круга в направлении , перпендикулярно к линии центров. На круглошлифовальных станках шлифование производится тремя методами:
1) Шлифованием с продольной подачей; так шлифуют обычно длинные детали; поперечная подача шлифовального круга при предварительной обработке составляет 0,02-0,1 мм; при окончательной 0,005-0,01 мм на двойной ход; продольная подача при предварительной обработке составляет 0,3-0,8 ширины круга на оборот детали, при окончательной обработке 0,2-0,3 ширины круга;
2) Однократным шлифованием установленным кругом; применяется при обработке коротких деталей; в этом случае почти весь припуск снимается за один проход при небольшой подаче, равной 1-5 мм на оборот детали;
3) Шлифование врезанием или методом поперечной подачи; такое шлифование явл-ся наиболее производительным методом шлифования точных изделий; этим методом шлифуют поверхности, ширина которых не больше ширины круга: шейки валов, кольцевые выступы и т.д. Поперечная подача в начале шлифования составляет 0,02-0,08 мм на оборот изделия, при приближении к окончательному размеру уменьшается до 0,005-0,01 мм и затем прекращается.
Для шлифования врезанием шлифовальный круг должен быть хорошо выправлен алмазом или другим инструментом для правки.
В процессе шлифования в результате правки шлифовального круга и его износа размер детали при постоянной настройке станка изменяется. Вследствие этого возникает необходимость в остановке
станка для измерения детали, что связано со значительной затратой времени.
Для контроля деталей в процессе шлифования применяются индикаторные трёхконтактные скобы . По показаниям индикатора судят о размере детали. Кроме индикаторных скоб , применяются электроконтактные, индукционные , пневматические и др. приборы, которые при достижении определённого размера детали включают световой сигнал или механизм отвода шлифовального круга.
При шлифовании длинных нежёстких валов используют люнеты обычно с двумя кулачками ( поддерживающим и упорным). Кулачки делают из твёрдых пород дерева, текстолита или пластмасс.
Обработка на бесцентрово- шлифовальных станках при вращении детали, поддерживаемой линейкой ( ножом) между двумя абразивными кругами: шлифующим и ведущим. Шлифующий круг вращается с числом оборотов , обеспечивающим нормальную скорость резания ( 25-35 м/ сек), ведущий круг с числом оборотов, обеспечивающим окружную скорость вращения детали ( 20-40 м/ мин).
Шлифовальный круг имеет цилиндрическую форму; ведущий круг при шлифовании методом поперечной подачи – цилиндрическую форму, при шлифовании на проход – форму гиперболоида вращения, у которого линия линия соприкосновения с деталью прямая.
Напроход шлифуют цилиндрические детали; врезанием –цилиндрические, конические и фасонные диски, длина которых меньше ширины круга. При шлифовании ступенчатых и фасонных деталей методом врезания шлифовальный круг заправляется по контуру, соответствующему контуру детали.
Бесцентрово- шлифовальные станки обеспечивают высокую производительность , стабильность размеров и чистоты поверхности обрабатываемой детали.
Притирка поверхностей применяется в тех случаях, когда необходимо обеспечить высокую точность размеров и чистоту поверхности детали. Притирка производится чугунными или медными притирами с притирочными пастами, состоящими из мелкозернистого абразивного порошка, смешанного с парафином, маслом, керосином, олеиновой кислотой и др. жидкостями.
Механическая притирка коротких деталей ( например, поршневые пальцы, толкатели, детали топливной аппаратуры) производится на притирочных станках. Они снабжены двумя вращающимися чугунными дисками ( один диск может быть неподвижен), закреплёнными в шпинделях. Между дисками расположен сепаратор; в него устанавливают детали в таком положении, при котором их оси скрещиваются с радиусом диска под углом 5-15°. Это обеспечивает некоторое скольжение деталей при качении по дискам и интенсифицирует процесс притирки.
Припуски на притирку невелики (0,005-0,02мм). При нормальных припусках и соответствующей подготовке детали притирка осуществляется быстро, обеспечивается очень высокая чистота поверхности ( до 14-го класса) и высокая точность.
Суперфиниширование применяется для отделочной обработки шлифовальных поверхностей, придания им чистоты 12-14-го классов. Суперфиниширование производится на токарных станках, оснащённых специальными приспособлениями или на специальных станках абразивными брусками зернистостью 400-600.
Бруски , прижатые к поверхности вращающейся детали, совершают короткие возвратно- поступательные движения и снимают шероховатости. Продукты износа брусков частицы металла смываются струёй керосина , которая подаётся в зону обработки и одновременно охлаждает деталь. При суперфинишировании совершенно не устраняются погрешности формы детали, поэтому они до
этой операции должны быть очень точно обработаны. Припуск на суперфиниширование составляет 0,003-0,015 мм.
Полирование поверхностей применяется для придания им высокой чистоты при невысоких требованиях к точности детали. Полирование производится эластичными кругами, на которые нанесена абразивная паста. Круги, вращаясь с высокой окружной скоростью ( до 40 м/ сек) , прижимаются к обрабатываемой поверхности. Полировальные круги изготовляют из войлока, фетра, бязи , парусины и кожи.
К втулкам относят детали, образованные наружными и внутренними пов-ми вращения, имеющими одну общую прямолинейную ось при отношении длины цилиндрической части к наибольшему наружному диаметру более 0,5 и менее или равное 2.
Технологические задачи при обработке втулок заключаются в достижении концентричности наружных и внутренних пов-тей и перпендикулярности торцев к оси отверстия. При изготовлении тонкостенных втулок возникает дополнительная задача закрепления заготовки и её обработки без деформаций.
Основные схемы базирования.
Технологические маршруты обработки втулок в зависимости от их точности и конфигурации строятся по одному из трёх вариантов.
1.Обработка наружных пов-тей, отверстий и торцев за один установ.
Применяется для изготовления мелких втулок, не обработанных термически, из прутка или трубы на токарно- револьверных автоматах, одношпиндельных или многошпиндельных токарных автоматах. Технологическая база – наружная пов-ть и торец прутка.
2.Обработка всех пов-тей за два установа или за две операции с базированием при окончательной обработке наружной пов-ти по отверстию ( обработка от центра к периферии). Применяется в тех случаях, когда точность внутреннего отверстия задана чертежом выше, чем наружной пов-ти. В этом случае порядок черновых переходов строго не регламентируется. При чистовой обработке сначала обрабатывается отверстие. Обработанное отверстие принимается за технологическую базу ( при помощи оправки) и окончательно обрабатывается наружная пов-ть.
3. Обработка всех пов-тей за два установа или за две операции с базированием при окончательной обработке по наружной пов-ти ( обработка от периферии к центру). Применяется в тех случаях, когда точность наружных пов-тей по чертежу выше, чем у внутреннего отверстия. Порядок черновых переходов – любой. При чистовой обработке сначала обрабатывается наружная пов-ть. Эта пов-ть принимается за технологическую базу ( в патроне) и обрабатывается внутреннее отверстие.
При выборе схемы базирования следует отдавать предпочтение базированию по отверстию ( обработка от центра к периферии).
Основные операции механической обработки.
Обработка за один установ.
Токарная.
Подрезка торца у прутка, подача прутка до упора, зацентровка торца под сверление, сверление отверстия, точение черновое наружной пов-ти со снятием фасок на свободном торце, точение канавок, предварительное развёртывание, окончательное развёртывание, отрезка. При обработке втулки из трубы вместо сверления производят зенкерование или растачивание отверстия. Выполняется на токарно- револьверном , одношпиндельном или многошпиндельном токарном автомате.
Сверлильная.
Снятие фасок с противоположного торца втулки на вертикально- сверлильном или токарном станке.
Сверлильная.
Сверление отверстий , нарезка резьбы на вертикально – или радиально- сверлильном станке. В зависимости от заданной точности могут быть отдельными операциями.
Моечная.
Контрольная.
Нанесение антикоррозионного покрытия.
Обработка от центра к периферии.
Заготовительная.
Резка заготовки из проката, трубы или штамповка.
Токарная.
В зависимости от типа производства выполняется за одну операцию и два установа ( единичное) или за две операции ( серийное и массовое).
Первый установ ( базирование по наружной пов-ти и торцу в патроне)- подрезка свободного торца, сверление и зенкерование или растачивание отверстия ( с припуском под шлифование), растачивание канавок и фасок.
Второй установ ( базирование по отверстию и торцу на оправке) – подрезка второго торца , точение наружных пов-тей ( с припуском под шлифование), точение канавок и фасок.
В зависимости от типа производства операции выполняются :
-в единичном – на токарно- винторезных станках;
-в серийном – на токарно-револьверных станках и станках с ЧПУ;
-в массовом – на токарно- револьверных , одношпиндельных или многошпиндельных токарных полуавтоматах.
Сверлильная.
Сверление, зенкерование, нарезка резьбы. Производится на вертикально-сверлильных, радиально- сверлильных станках, сверлильных станках с ЧПУ, агрегатных станках.
Термическая.
Закалка согласно чертежу.
Внутришлифовальная.
Шлифование отверстия на внутришлифовальном станке.
Деталь базируется по наружному диаметру и торцу в патроне.
Круглошлифовальная.
Шлифование наружных пов-тей и торцев на круглошлифовальном или торцекруглошлифовальном станках.
Технологическая база – отверстие ( на оправке).
Моечная.
Контрольная.
Нанесение антикоррозионного покрытия.
Тема 4.3 Технология изготовления корпусных деталей.
К группе корпусных деталей относятся картеры коробок передач, редукторов, главных передач, остов двигателя, фундаментные рамы, блоки, головки цилиндров, корпусы насосов , кожухи маховиков и др.
Корпусные детали определяют взаимное положение узлов и основных деталей двигателя, которые монтируются на их внешних и внутренних поверхностях , а также надёжность и долговечность работы этих узлов и деталей. Они воспринимают нагрузки , возникающие в процессе работы двигателя – динамические усилия от давления газов, инерционные усилия от движущихся частей , давления воды и масла в охлаждающих и смазочных полостях.
Корпусные детали имеют обычно сложную форму , поверхности, отверстия, расположенные в разных плоскостях , фасонные , внутренние полости, сложные каналы, рёбра, перегородки и т.д.
Обработка корпусных деталей производится с высокой точностью.
Корпусные детали можно разделить на две основные разновидности: призматические и фланцевые.
Корпуса призматического типа, например корпус коробки передач, блок цилиндров двигателя, характеризуются большими наружными поверхностями и расположением отверстий на нескольких осях.
У корпусов фланцевого типа базовыми поверхностями служат торцовые поверхности основных отверстий и поверхности центрирующих выступов или вытачек.
Корпусные детали выполняют литыми из серого чугуна, реже из стали. Отливки получают чаще всего литьём в песчаные формы. До отправки в механический цех у отливок удаляют литники и прибыли, очищают поверхность , контролируют размеры, качество поверхности, твёрдость и др.
Для корпусных деталей характерно наличие базовых поверхностей, а также основных и крепёжных отверстий. Базовые поверхности корпуса стыкуются с другими узлами или агрегатами данной машины.
Основные отверстия предназначены для монтажа опор валов . Точность диаметральных размеров основных отверстий соответствует 7-му квалитету, реже 8-му квалитету, шероховатость поверхности Rа=2,5…0,63 мкм. Межосевые расстояния основных отверстий выдерживают согласно стандарту с допусками, обеспечивающими необходимую точность работы зубчатых и червячных передач ( обычно 8-я степень точности).
Отклонения отверстий от соосности устанавливают в пределах половины допуска на диаметр меньшего отверстия.
Базовые поверхности обрабатывают с допускаемыми отклонениями о прямолинейности 0,05…0,2 мм на всей длине и с шероховатостью 4…0,63 мкм.
Базирование корпусных деталей выполняют с учётом их конструктивных форм и технологии изготовления.
Если конфигурация корпуса не позволяет эффективно использовать его поверхности для базирования, то обработку целесообразно выполнять в приспособлении – спутнике. При установке заготовки в спутнике могут быть использованы черновые или искусственно созданные вспомогательные базовые поверхности, причём, заготовка обрабатывается на различных операциях при постоянной установке в приспособлении, но положение самого приспособления на разных операциях меняется
Технологический маршрут обработки корпусов .
При обработке заготовок корпусов неразъёмного типа, например, корпуса коробки передач, маршрут состоит из трёх этапов обработки:
1) Базовых поверхностей ( наружной пов-ти и установочных отверстий);
2) Основных отверстий и поверхностей;
3) Крепёжных и других мелких отверстий.
Каждый этап обработки может включать несколько операций, в т.ч . черновые и чистовые.
Для разъёмных корпусов, например, корпусов редукторов, предусмотрены обработка поверхностей разъёма отдельных частей корпуса, поверхностей крепёжных отверстий, предназначенных для соединений отдельных частей, дополняемая обработкой отверстий под контрольные штифты и их установка; обработка поверхностей основных отверстий; обработка поверхностей крепёжных и др. мелких отверстий.
В единичном производстве заготовки корпусов обрабатывают на универсальном оборудовании без специальных приспособлений.
В серийном и массовом производствах для установки заготовок применяют приспособления. При обработке без приспособлений производится предварительная разметка заготовок. В этом случае определяют контуры детали, учитывая рациональное распределение припусков на обработку, а также устанавливают положение соей отверстий. По разметочным рискам выверяют заготовку при её установке на станке.
Обработка наружных поверхностей заготовок осуществляется строганием, фрезерованием, протягиванием, точением и шлифованием.
Строгание поверхностей применяют в единичном и мелкосерийном производстве на продольно- строгальных станках Строгание отличается низкой производительностью , но обеспечивает боле высокую точность , чем фрезерование.
Наибольшее распространение при обработке поверхностей получило фрезерование. Заготовки небольших корпусов в единичном и мелкосерийном производствах обрабатывают на консольно- фрезерных станках с поворотными столами. Это позволяет обработать с одной установки четыре поверхности заготовки.
В серийном производстве заготовки корпусов , имеющих форму параллелипипеда, обрабатывают на продольно- фрезерных станках. Наибольший эффект получают при использовании многоместных приспособлений и при работе несколькими инструментами.
Обдирочное шлифование поверхностей производят торцом сборного сегмента шлифовального круга со снятием припуска до 4…5 мм. Торцовые поверхности корпусов, имеющих конфигурацию тел вращения , протачивают на токарно- карусельных станках или на расточных станках с применением головок с подрезными пластинами или цековок.
У заготовок корпусных деталей небольших размеров , например коробок передач, поверхности обрабатывают протягиванием, используя прогрессивные конструкции протяжек. Протягивание обеспечивает шероховатость поверхности Rа =1,25…0,32 мкм, малое отклонение от плоскостности ( 0,005 мм на длине 300 мм) и точность размера в пределах 6-го квалитета.
Торцовое фрезерование в два прохода ( черновое и чистовое) обеспечивает шероховатость Rа =2,5…1,25мкм, отклонение от плоскостности 0,03 мм на длине 300 мм и точность размера в пределах 11-го квалитета.
Для достижения более высокой точности применяют шлифование поверхностей, а в единичном и мелкосерийном производствах – строгание и шабрение.
Общее направление последовательности обработки конструкций корпусных деталей:
1) Черновая обработка базовых и сопрягаемых плоских поверхностей в мелкосерийном производстве – по разметке, в крупносерийном производстве и массовом производится от черновой базы;
2) Обработка базовых отверстий;
3) Черновое растачивание посадочных отверстий под подшипники коленчатого вала, распределительного вала, гильзы и агрегаты.
4) Промежуточное старение и предварительные гидроиспытания.
5) Чистовая обработка плоскостей.
6) Обработка базовых отверстий, сверление и нарезание резьбы в отверстиях, необходимых для крепления деталей, обработка которых ведётся в сборе с корпусными деталями.
7) Получистовая и чистовая обработка посадочных отверстий.
8) Сверление и нарезание резьбы в отверстиях для крепления узлов, обработка масляных каналов и т.п.
9) Слесарные и мелкие м/о и окончательные гидравлические испытания.
При обработке корпусных деталей важное значение имеет правильный выбор и подготовка баз, обеспечивающих постоянство установки деталей относительно инструментов и рабочих органов станка на всех операциях. Наиболее часто в качестве установочных баз при обработке корпусных деталей принимают плоскости достаточно большой протяжённости и два отверстия, расположенные на возможно большом расстоянии. Если по эксплуатационным и конструктивным особенностям в детали не имеется таких отверстий, их часто делают специально в качестве базовых. У блоков и фундаментных рам в качестве установочных баз обычно выбирают плоскости разъёма или плоскости лап и отверстия для крепления, а в качестве черновой базы также отверстия под гильзы цилиндров и гнёзда подшипников. У головок цилиндров в качестве черновых баз выбирают плоскости разъёма и отверстия для клапанов или камеры сгорания. У других корпусных деталей при выборе баз необходимо учитывать равномерное распределение припусков на обработку .
Обработка основных отверстий.
В зависимости от конфигурации , размеров детали и программы выпуска основные отверстия обрабатывают на расточных и агрегатных многошпиндельных станках на токарно- карусельных , вертикально- и- радиально- сверлильных станках.
На расточных станках обрабатывают заготовки корпусов коробчатой формы в единичном и серийном производствах. В условиях крупносерийного и массового производств применяют многошпиндельные агрегатные станки.
Заготовки корпусов фланцевого типа обрабатывают на токарно- карусельных станках. Отверстия в корпусах небольших и средних размеров в серийном производствк могут быть обработаны на вертикально- или радиально- сверлильных станках путём последовательной установки нескольких инструментов ( например, для сверления, зенкерования и развёртывания) в быстросменных патронах.
Для обработки отверстий на вертикально-сверлильных станках используют также шестишпиндельные поворотные головки. В качестве режущего инструмента применяют однорезцовые, двухрезцовые и регулируемые блоки, а также зенкеры и резцовые головки, имеющие 4…8 ножей. Резцовые головки более производительны по сравнению с другим расточным инструментом.
Для обработки отверстий диаметром до 400 мм с точностью по 7-му или 8- му квалитетам основной операцией явл-ся развёртывание.
При изготовлении отверстий точность их взаимного расположения обеспечивается двумя способами: 1) установка заготовки в специальном приспособлении;
2) Использование универсальных способов координации положения инструмента.
В единичном и мелкосерийном производствах при изготовлении корпусов высокой точности применяют координатно- расточные станки . В этих станках инструмент устанавливают либо непосредственно в шпинделе, либо в концевой оправке. Координация шпинделя относительно оси отверстия обеспечивает погрешность межосевых расстояний не более 5 мкм, а погрешность размеров и геометрической формы отверстий – не более 2…3 мкм.
В мелкосерийном производстве при обработке в корпусах отверстий без применения специальных приспособлений установку шпинделя можно выполнить с использованием координатного шаблона, в котором отверстия расположены с координатами, соответствующему заданному расположению осей отверстий детали. Шаблон можно устанавливать непосредственно на заготовку или на стол станка.
При растачивании по координатному шаблону шпиндель устанавливают с помощью центроискателя по отверстию шаблона, затем снимают центроискатель, закрепляют в шпинделе режущий инструмент и растачивают отверстие в заготовке через отверстие в шаблоне. Отверстия в шаблоне должны быть на 2…3 мм больше соответствующих отверстий в заготовке. Применение шаблона обеспечивает погрешность установки шпинделя не более 0,05 мм.
В серийном и массовом производстве распространена обработка отверстий в приспособлениях с направлением инструмента кондукторными втулками. Обрабатывать отверстия с направлением инструмента кондукторными втулками можно на горизонтально- расточных агрегатных, вертикально- сверлильных и радиально- сверлильных станках. Если отверстия выполняют с применением кондуктора , погрешность зависит от точности кондуктора и расточной скалки и от зазоров между скалкой и кондукторным втулками.
Обработка крепёжных и других отверстий.
Эти отверстия обрабатывают сверлением, зенкерованием, цекованием, развёртыванием.
В единичном производстве отверстия сверлят по разметке.
В серийном и массовом производстве применяют различные кондукторы – коробчатого типа , накладные.
Для обработки отверстий с разных сторон применяют поворотные кондукторы. В серийном и единичном производствах корпусные заготовки массой до 30 кг обрабатывают на вертикально- сверлильных станках, а заготовки массой свыше 30 кг- на радиально- сверлильных станках.
В крупносерийном и массовом производствах обработка выполняется на многошпиндельных агрегатных станках.
При контроле корпусных деталей производят проверку размеров диаметров основных отверстий и их геометрической формы, а также отклонений от прямолинейности и взаимного положения поверхностей корпуса.
Размеры Ø отверстий обычно контролируют предельными калибрами и реже микрометрическими или индикаторными штихмассами.
Правильность геометрической формы отверстий проверяют индикаторными и рычажными нутромерами или пневматическим ротомером.
Для контроля отклонения от соосности обычно используют контрольные оправки. Отклонение от соосности в крупногабаритных корпусах проверяют оптическими методами.
Отклонение от параллельности осей и межцентровое расстояние проверяют измерением расстояний между внутренними образующими контрольных оправок при помощи индикаторного нутромера, штихмасса или блока концевых мер, либо расстояний между внешними образующими контрольных оправок при помощи микрометра или штангенциркуля. Зная диаметры оправок рассчитывают межцентровое расстояние.
Отклонение от перпендикулярности осей отверстий устанавливают при повороте оправки с индикатором из положения 1 в положение 2 , отстоящее одно от др. на расстоянии L.
Отклонение от перпендикулярности торцовой поверхности корпуса относительно оси отверстия проверяют контрольной оправкой с индикатором, фиксированной от осевого перемещения угольником.
Для контроля точности положения осей отверстий в одной плоскости расположенных под углом , применяют два контрольных калибра.
При контроле деталей в крупносерийном и массовом производствах используют специальные контрольные приборы для комплексной проверки деталей по многим параметрам тонности.
Схема технологического процесса обработки фундаментной рамы.
№№ | Операция. | Оборудование. | Приспособление. | Инструмент. |
1 | Проверка размеров и разметка для предварительной обработки. | Разметочная плита. | Домкраты, кубики. | Штангенрейсмус, линейка. |
2 | Предварительное фрезерование технологических платиков и нижней пов-ти лап. | Продольно- фрезерный станок. | Подставки и прижимные планки. | Торцовая наборная фреза Ø 300 мм. |
3 | Предварительное фрезерование верхней плоскости и боковых сторон. | То же. | То же. | Торцовая наборная фреза Ø300 мм и концевая фреза Ø250 мм. |
4 | Предварительное строгание замка. | Продольно-строгальный станок мод. 7А256 | То же. | Строгальные резцы, правый и левый. |
5 | Растачивание опор под коленчатый вал и предварительное фрезерование торца. | Горизонтально- расточной станок мод. 265В. | Подставка, люнеты. | Борштанга, расточные резцы, торцовая фреза. |
6 | Искусственное старение, очистка, гидравлические испытания, грунтовка. | Термическое, очистное, окрасочное оборудование. | -- | -- |
7 | Разметка для окончательной обработки. | Разметочная плита. | Домкраты, кубики. | Штангенрейсмус, линейка. |
8 | Окончательное строгание нижней пов-ти лап. | Продольно-строгаль- ный станок мод. 7А256 | Подставки и прижимные планки. | Резцы. |
9 | Окончательное строгание верхней плос- кости, замка и боковых пов-тей. | То же. | То же. | Резцы. |
10 | Разметка для сверления отверстий. | Разметочная плита. | Домкраты, кубики. | Штангенрейсмус, линейка. |
11 | Сверление и нарезание отверстий на верхней пов-ти, в лапах, днище, на боковых пл-тях и в замке. | Радиально- сверлильный станок. | Накладные кондукторы. | Свёрла, зенкеры, метчики. |
12 | Сборка рамы с крышками коренных подшипников. | - | Специальная подставка, контрольная плита, приспособление для крепления крышек. | Шабер, набор слесарного инструмента. |
13 | Предварительное растачивание опор коленчатого вала и окончательное подрезание торцов опор. | Горизонтально- расточной станок мод. Н-165Д. | Расточное приспособление. | Борштанга, резцы. |
14 | Окончательное растачивание опор, подрезание торцов упорного подшипника. | То же. | То же. | То же. |
15 | Фрезерование торцовых поверхностей и сверление отверстий в торцах. | Горизонтально- расточной станок мод. Н-125Д. | Накладные кондукторы, контрольный вал. | Торцовая фреза, свёрла. |
16 | Сверление и подрезание мелких отверстий. | Переносный радиально- сверлильный станок. | Подставка. | Сверло, метчики. |
17 | Слесарная: зачистка заусенцев, опиловка острых кромок, фрезерование пазов для фиксации подшипников. | Переносный фрезерный станок. | -- | Напильник, шабер, фреза. |
18 | Окончательный контроль. | Контрольная плита. | Контрольный вал. | Шртангенрейсмус, индикатор, калибры. |
Тема 4.4 Технология изготовления зубчатых колёс.
Дата добавления: 2022-01-22; просмотров: 111; Мы поможем в написании вашей работы! |
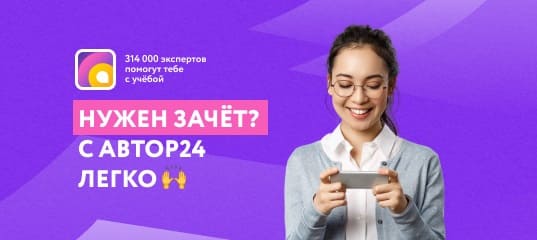
Мы поможем в написании ваших работ!