Тема 2.1 Общие сведения о приспособлениях.
Назначение и классификация приспособлений.
Приспособления, предназначенные для установки и закрепления режущего инструмента, называют вспомогательными инструментами.
При применении приспособлений в процессе обработки деталей машин:
1) повышается точность обработки вследствие правильной установки деталей, точного направления режущего инструмента, постоянства величины и направления усилия зажима;
2) повышается производительность обработки, т.к. сокращается вспомогательное время и машинное, повышаются режимы резания при надёжном и жёстком закреплении деталей;
3) облегчается труд рабочих;
4) расширяются технологические возможности использования станков и обеспечивается пр-во таких работ, котор. без приспособлений не могут быть выполнены;
5) сокращаются затраты времени на контроль элементов деталей, раз-ры или координаты котор. обеспечиваются приспособлениями.
По степени специализации приспособления можно подразделить на группы:
1) Универсальные приспособления (УП), применяемые при обработке различных деталей путём установки отдельных элементов приспособления на требуемый раз-р ( патроны, станочные тиски, делительные головки, поворотные столы и т.д).
2) Переналаживаемые многопредметные приспособления, котор. делятся на :
а) универсально-наладочные приспособления ( УНП) – универсальные или нормализованные приспособления со сменными наладками ( цанговые патроны, пневматические патроны и тиски со сменными фасонными кулачками и губками, протяжные приспособления со сменными направляющими и др); к ним так же относятся приспособления, предназначенные для обработки определённой группы деталей; такие приспособления могут быть со сменными наладками или с постоянными установочными элементами, обеспечивающими обработку разных деталей без переналадки;
|
|
б) универсально-сборные приспособления ( УСП) – специальные приспособления, собираемые из стандартных деталей, входящих в комплект этих приспособлений.
3) Специальные приспособления (СП) , предназначенные для обработки одной или группы конструктивно и технологически однородных деталей и спроектированные исходя из определённых условий обработки, формы и раз-ров заготовки и принятой схемы базирования.
В единичном и мелкосерийном производстве широко используются универсальные приспособления; специальные приспособления применяются только в тех случаях, когда без них невозможно обеспечить требуемое качество детали.
В серийном производстве наряду с универсальными приспособлениями, широко распространены переналаживаемые приспособления. Особенно целесообразно использовать универсально-сборные и универсально-наладочные приспособления, характерные для массового производства.
|
|
В массовом пр-ве и крупносерийном распространены специальные приспособления.
( в соответствии с видом обработки и типом станков, на котор. их устанавливают ) делятся на токарные, фрезерные, расточные, сверлильные, шлифовальные и т.д.
При разработке конструкции приспособлений должны соблюдаться правила выбора баз, обеспечиваться точное и стабильное взаимное положение детали и инструмента при обработке, удобство установки, снятие и контроля деталей, свободное удаление стружки, постоянство зажимного усилия и приложение его в местах, не приводящих к деформации детали, жёсткое крепление детали при обработке, а также условия , обеспечивающие безопасность работы. В приспособлении не должно быть элементов, которые . могут повредить обработанные пов-ти.
Конструкции приспособлений разнообразны, но элементы приспособлений можно разделить на группы:
1) установочные элементы, определяющие положение деталей в приспособлении;
2) зажимные элементы – механизмы и устройства для крепления деталей или подвижных частей приспособлений;
|
|
3) элементы для направления режущего инструмента и контроля его положения;
4) силовые устройства для приведения в действие зажимных элементов, ( пневматические, гидравлические,электрические, механические);
5)корпуса приспособлений, на которых крепятся все остальные элементы;
6) вспомогательные элементы, служащие для изменения положения детали в приспособлении относительно инструмента, для соединения между собой элементов приспособлений и регулирования их взаимного положения.
Установочные элементы приспособлений.
При базировании деталей плоскими поверхностями установочные элементы выполняются в виде опорных штырей и пластин.
При установке деталей с обработанной базовой поверхностью применяют штыри с плоской головкой или установочные пластины.
При установке деталей с необработанными базовыми поверхностями используют установочные штыри с сферической или рифлёной поверхностью.
Опорные штыри устанавливают по глубокой посадке непосредственно в отверстия, расточенные в корпусах приспособлений или в переходные закалённые втулки, запрессованные в корпуса приспособлений.
Опорные пластины прикрепляют к корпусу приспособления винтами. Чтобы уменьшить возможность попадания под опорные пов-ти деталей стружки, отверстия для крепления делают на срезанной части пластины.
|
|
Опорные штифты и пластины стандартизованы и изготовляются по ГОСТам 4083-57 и 4743-57.
Штыри пластины цементуют и закаливают до твёрдости HRC 54-58.
При установке в приспособления литых, кованых, штампованных заготовок применяют регулируемые опоры.
Деталь с необработанной и обработанной с невысокой точностью опорной базовой поверхностью надёжно устанавливают в приспособлении только на три опоры( три точки). При большем количестве опор установка деталей получается неопределённой , между отдельными опорами и базовой поверхностью детали может быть зазор и при зажиме возможна деформация детали. Поэтому основные три опоры должны быть размещены так, чтобы центр тяжести детали и проекции сил зажима оказались внутри треугольника, вершинами которого являются опоры.
При необходимости придать детали большую устойчивость против опрокидывающих или деформирующих её усилий применяют вспомогательные опоры- подводимые или самоустанавливающиеся.
Подводимые опоры- домкратики устанавливают на корпусе приспособления и подводят в установочную пов-ть детали.
При базировании деталей наружными цилиндрическими поверх-ми применяют призмы. Для устранения влияния погрешностей изготовления призмы и базовой цилиндрической пов-ти призму при достаточной длине детали делают из двух узких частей или с выемкой в средней части. Наиболее распространены призмы с углом 90 град.
Для базирования заготовок по внутренним цилиндрическим пов-тям применяют оправки или установочные пальцы. Пальцы запрессовывают в корпус приспособления или, если требуется частая замена пальцев, прикрепляют к корпусу винтами либо гайками. Чтобы облегчить установку детали на конце пальцев делают фаски или скругления.
Часто при обработке деталей типа корпусов, плит, рам и картеров, установка заготовок осуществляется на два цилиндрических отверстия с параллельными осями на перпендикулярную к ним плоскость. В этом случае заготовку устанавливают на два пальца и плоскость, причём один из пальцев имеет двусторонние срезы. Ось, проходящая через цилиндрические пояски срезанного пальца, должна быть перпендикулярна оси, проходящей через центры отверстия заготовки.
При базировании по отверстию и плоскости палец делают срезанным. Срез пальцев позволяет компенсировать погрешность в расстоянии между осями базовой плоскостью и отверстием вследствие возникновения дополнительного зазора.
При обработке тяжёлых деталей, а также при обработке деталей на автоматических линиях, установленные пальцы выполняют выдвижными, их вводят в базовые отверстия после установки детали на плоскость.
Зажимные элементы и силовые устройства приспособлений
Зажимные элементы должны обеспечить надёжный контакт обрабатываемой детали с установочным элементами и препятствовать нарушению его под действием возникающих при обработке усилий, быстрый и равномерный зажим всех деталей и не вызывать деформации и порчи пов-тей закрепляемых деталей.
Зажимные элементы подразделяются:
По конструкции – на винтовые, клиновые, эксцентриковые, рычажные, рычажно-шарнирные ( применяются также комбинированные зажимные элементы – винторычажные, эксцентрико-рычажные и т.д).
По степени механизации – на ручные и механизированные с гидравлическим , пневматическим, электрическим или вакуумным приводом.
Зажимные мех-мы могут быть автоматизированными.
Винтовые зажимы используют для непосредственного зажима или зажима через прижимные планки, либо прихваты одной или нескольких деталей. Недостатком их является то, что для закрепления и открепления детали приходится затрачивать много времени.
Эксцентриковые и клиновые зажимы , также как винтовые, позволяют закреплять деталь непосредственно или через прижимные планки и рычаги.
Наибольшее распространение получили круговые эксцентриковые зажимы. Эксцентриковый зажим является частным случаем клинового зажима , причём для обеспечения самоторможения угол клина не должен превышать 6-8 град. Эксцентриковые зажимы изготовляют из высокоуглеродистой или цементуемой стали и термически обрабатывают до твёрдости HRC55-60. Эксцентриковые зажимы относятся к быстродействующим зажимам, т.к. для зажима необход. повернуть эксцентрик на угол 60-120 град.
Рычажно- шарнирные элементы применяются в качестве приводных и усилительных звеньев зажимных механизмов. По конструкции они делятся на однорычажные, двухрычажные ( одностороннего и двустороннего действия – самоцентрирующие и многозвенные). Рычажные механизмы не обладают самотормозящими свойствами . Наиболее простым примером рычажно-шарнирных мех-мов является прижимные планки приспособлений, рычаги пневматических патронов и т.д.
Пружинные зажимы применяют для зажима изделий с небольшими усилиями , возникающие при сжатии пружины.
Для создания постоянных и больших зажимных усилий, сокращения времени зажима, осуществления дистанционного управления зажимами применяют пневматические, гидравлические и другие приводы.
Наиболее распространёнными пневматическими приводами явл-ся поршневые пневматические цилиндры и пневматические камеры с упругой диафрагмой , стационарные, вращающиеся и качающиеся.
Пневматические приводы приводятся в действие сжатым воздухом под давлением 4-6 кг/см.² При необходимости применения малогабаритных приводов и создания больших зажимных усилий используют гидравлические приводы, рабочее давление масла в котор. достигает 80 кг/см².
Усилие на штоке пневматического или гидравлического цилиндра равно произведению рабочей площади поршня в квадратных см. на давление воздуха или рабочей жидкости. При этом необходимо учитывать потери на трение между поршнем и стенками цилиндра, между штоком и направляющими втулками и уплотнениями.
Электромагнитные зажимные устройства выполняют в виде плит и планшайб. Они предназначены для закрепления стальных и чугунных заготовок с плоской базовой поверхностью при шлифовании или чистовом точении.
Магнитные зажимные устройства могут быть выполнены в виде призм, служащих для закрепления цилиндрических заготовок. Появились плиты, у которых в качестве постоянных магнитов используют ферриты. Эти плиты отличаются большой удерживающей силой и меньшим расстоянием между полюсами.
Вакуумные зажимные устройства работают по принципу непосредственной передачи атмосферного давления закрепляемой заготовке. Эти устройства могут применяться для закрепления заготовок из различных материалов с плоской или криволинейной базовой поверхностью при выполнении операции отделки или чистовой обработки.
Элементы для направления режущего инструмента и контроля его положения.
Для направления инструмента при обработке деталей на сверлильных и расточных станках применяются неподвижные и вращающиеся кондукторные втулки.
Неподвижные кондукторные втулки делятся на постоянные, сменные, быстросменные и специальные.
Кондукторные втулки изготовляют из инструментальных и цементуемых сталей и термически обрабатывают до высокой твёрдости (HRC 60-64).
Постоянные втулки делают с буртиками и без буртиков. Эти втулки применяют в кондукторах, предназначенных для обработки небольших партий деталей.
Сменные втулки применяют при обработке отверстия одним инструментом. При износе их легко заменить . Сменные втулки устанавливают во втулки гнезда, запрессованные в корпус приспособления.
Быстросменные втулки используют при обработке отверстия последовательно несколькими инструментами разных размеров ( сверлом, зенкером, развёрткой и т.д_.
Специальные втулки применяются при малом расстоянии между осями отверстий, при сверлении отверстия в наклонной поверхности и т.д.
Для направления борштанг в расточных приспособлениях применяют неподвижные и вращающиеся втулки.
Неподвижные направляющие втулки изготовляют из стали или бронзы. Однако, нерегулярная смазка и попадание мелкой стружки между втулками и борштангой приводит к повреждению и износу их рабочих поверхностей. Для устранения этого недостатка в расточных приспособлениях применяются вращающиеся направляющие втулки. Эти втулки вращаются в бронзовых или стальных подшипниках скольжения, шариковых, роликовых или игольчатых подшипниках качения.
Эти подшипники защищены от попадания грязи, стружки и эмульсии и имеют устройства для смазки. Направляющие втулки могут иметь пазы для прохода инструмента и шпоночные пазы или шпонки, вследствие чего втулки вращаются вместе с борштангой.
Вспомогательные элементы и корпусы приспособлений.
К вспомогательным элементам приспособлений относятся делительные механизмы, механизмы для перемещения элементов приспособлений, детали для соединения отдельных частей и узлов приспособлений и др.
Делительные устройства служат для правильного углового или линейного перемещения деталей. Основными элементами делительных устройств явл-ся делительные диски или линейки (плиты), фиксаторы, червячные пары, зубчатые рейки с шестернями и наборы шестерён.
Делительные диски изготавливают в виде круглой плиты с делениями , пазами или втулками, расположенными по окружности. Делительные линейки представляют собой призматические плиты, на одной их граней которых на определённом расстоянии расположены пазы или втулки.
В качестве делительных дисков и линеек могут быть использованы корпусы поворотной или передвижной части приспособлений. Фиксаторы изготовляют в виде цилиндрических, конических или призматических пальцев, конец котор. входит в пазы или втулки делительного диска. Фиксатор точно подгоняется к направляющему отверстию или пазу и вводится в делительный диск под действием пружины, реечных или эксцентриковых механизмов.
Червячные пары, рейки с шестернями и наборы шестерён применяют для поворота или перемещения подвижной части приспособления, иногда их используют как делительные устройства.
К вспомогательным элементам приспособлений относятся выталкиватели, защёлки и замки, а также подъёмные механизмы, обеспечивающие выполнение специальных технологических приёмов.
Корпус является основной частью приспособления, на котором крепятся все остальные элементы. Он воспринимает все усилия, действующие на деталь при её обработке и закреплении. Корпусы приспособлений делают литыми из чугуна СЧ 12-28, сварными из стали Ст3 или сборными из отдельных элементов, скреплённых болтами. Для обеспечения достаточной жёсткости корпусов без значительного увеличения массы они имеют рёбра жёсткости.
При конструировании корпусов приспособлений необходимо учитывать удобство установки и зажима детали, удаления стружки, а также условия, обеспечивающие точность их установки и закрепления на станке. Наиболее распространены чугунные литые корпуса; однако с ними конкурируют корпусы сварные, обеспечивающие достаточную прочность и жёсткость и не требующие для изготовления моделей.
Тема 2.2 Конструкция приспособлений.
Дата добавления: 2022-01-22; просмотров: 49; Мы поможем в написании вашей работы! |
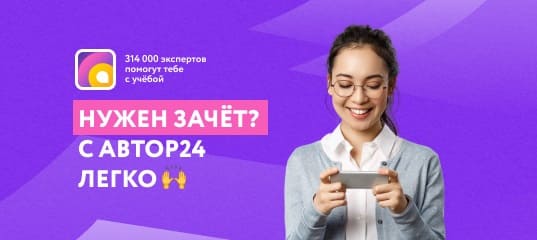
Мы поможем в написании ваших работ!