Тема 1.3 Точность механической обработки.
ТЕМА 1.1 Производственный процесс и принципы
Его организации в автотракторном производстве.
Слово «технология» (образованное из двух греческих слов techne-искусство, мастерство, умение и logos- слово , учение) означает науку , систематизирующую совокупность приёмов и способов обработки ( переработки) сырья, материалов, полуфабрикатов соответствующими орудиями производства в целях получения готовой продукции.
В состав технологии включается и технический контроль производства.
Важнейшие показатели, характеризующие технико-экономическую эффективность технологического процесса: расход сырья, полуфабрикатов и энергии на единицу продукции,
количество и качество получаемой продукции, изделий, уровень производительности труда ,
интенсивность процесса, затраты на производство, себестоимость продукции, изделий.
Продукт конечной стадии машиностроительного производства называется изделием.
Для того, чтобы превратить исходные материалы и сырьё в изделие, нужно выполнить ряд работ;
доставить материалы на предприятие, организовать их складирование и хранение, превратить ма-
териалы в заготовки, обработать эти заготовки на станках, при помощи т/о придать необходимые качества материалу деталей, собрать изделия, произвести окраску и упаковку.
В процессе изготовления деталей и сборки изделий требуется перемещать их от станка к станку и из цеха в цех, хранить их, предохранять их от коррозии, а также контролировать качество деталей на разных стадиях изготовления.
|
|
Весь комплекс работ по превращению сырья и материалов в готовое изделие называется
Производственным процессом.
Отдельные стадии производственных процессов на машиностроительном заводе осуществляется в специализированных цехах : литейных, кузнечных, заготовительных, механических, сборочных, испытательных и являются производственными процессами кузнечного, литейного, механического, сборочного цехов.
Предметом исследования и разработки в технологии машиностроения являются виды обработки, выбор заготовки, качество обрабатываемых поверхностей, точность обработки и при-
пуски на неё, базирование заготовок, способы м/о поверхностей – плоских, цилиндрических, сложнопрофильных и др; методы изготовления типовых деталей – корпусов, валов, зубчатых колёс и др; процесс сборки ( характер соединения деталей и узлов, принципы механизации и автоматизации сборочных работ); конструирование приспособлений.
Технология машиностроения постоянно обновляется и изменяется по мере развития техники Совершенствование технологии – важное условие ускорения технического прогресса в
|
|
народном хозяйстве.
Основные направления развития современной технологии: переход от прерывистых, дискретных технологических процессов к непрерывным автоматизированным, обеспечивающим увеличение масштабов производства и качества продукции; эффективное использование машин и оборудования; внедрение безотходной технологии для наиболее полного использования сырья, материалов, энергии, топлива и повышения производительности труда; создание гибких производственных систем, широкое использование роботов и роботизированных технологических комплексов в машиностроении и приборостроении.
В отечественном машиностроении с 1975 года внедряется Единая система технологической
подготовки производства. Основное назначение ЕСТПП заключается в установлении системы
организации и управления процессов технологической подготовки производства.
Внедрение ЕСТПП вводит единый порядок и системный подход к выбору и применению методов и средств технологической подготовки производства, сокращает срок освоения производства и выпуска изделий высшей категории и требуемого качества; обеспечивает организацию машиностроительного производства высокой степени гибкости, допускающую возможность непрерывного его совершенствования и быструю переналадку на выпуск новых изделий.
|
|
ЕСТПП базируется на государственных стандартах, в т.ч. на стандартах Единой системы конструкторской документации ( ЕСКД), Единой системы классификации и кодированиятехнико-экономической информации, Единой системы государственного управления качеством продукции (ЕС ГУКП), Государственной системы обеспечения единства измерений, а также на
системе стандартов безопасности труда (ССБТ) и документации, регламентирующей и регулирующей технологическую подготовку производства (ТПП).
Технологический процесс-часть производственного процесса, содержащая действия по изменению и последующему определению состояния предмета производства. Технологический процесс непосредственно связан с изменением размеров, формы или свойств материалов, обрабатываемой заготовки, выполняемым в определённой последовательности.
Технологический процесс должен обеспечить получение детали или изделия, отвечающим требованиям чертежа и ТУ, при наименьших затратах труда и материальных ресурсов. ТП определяет размеры, последовательно придаваемые деталям на разных стадиях обработки, требования к чистоте и взаимному расположению поверхностей, режимы обработки и нормы времени, а также сведения о способе получения заготовки, материале, из которого она изготовлена, и обработке её до поступления в цех.
|
|
Технология производства складывается из ряда процессов, каждый из которых характеризуется определёнными методами обработки и сборки. В структуру технологического
процесса входят операции, состоящие в свою очередь из нескольких элементов.
Так, для технологического процесса м/о основными элементами операции являются переход, рабочий ход, установ и позиция.
Под операцией понимают законченную часть технологического процесса,выполняемую на одном рабочем месте. Операция может осуществляться на одной заготовке или совместно на нескольких заготовках на одном рабочем месте одним рабочим или бригадой рабочих непрерывно ( до перехода к следующей заготовке). В операцию входят как действия,непосредст-
венно связанные с обработкой, так и необходимые вспомогательные приёмы ( переходы и ходы).
Переходом называется законченная часть операции, характеризуемая постоянством применяемого инструмента и поверхностей, образуемых обработкой или соединяемых при сборке.
Вспомогательным переходом называется законченная часть операции, не сопровождаемая обработкой, но необходимая для выполнения данной операции ( например, установка и снятие обработанной заготовки) или перехода и рабочего хода ( замена инструмента, установка инструмента, контрольный промер).
Рабочим ходом называется законченная часть перехода, состоящая из однократного перемещения инструмента относительно заготовки и сопровождаемая изменением формы, размеров, шероховатости поверхности или свойств заготовки.
Вспомогательным ходом называется законченная часть перехода, состоящая из однократного перемещения инструмента относительно заготовки, не сопровождаемая изменением формы, размеров, шероховатости поверхности или свойств заготовки, но необходимая для выполнения
рабочего хода.
Установ – часть операции, выполняемая при неизменном закреплении обрабатываемых заготовок или собираемой сборочной единицы.
Позицией называется фиксированное положение, занимаемое неизменно закреплённой обрабатываемой заготовкой или собираемой сборочной единицей совместно с приспособлением
относительно инструмента или неподвижной части оборудования для выполнения определённой части операции. Если применить поворотное приспособление, позволяющее изменять и фиксировать положение заготовки без её снятия, поворачивания и поворотного закрепления, то в этом случае обработка уступов с двух сторон буде осуществляться позиционно.
Характеристика типов производства.
В машиностроении в зависимости от программы выпуска изделий и характера изготовляемой продукции различают три основных типа производства: единичное, серийное, массовое.
Единичное производство характеризуется широкой номенклатурой изготовляемых или ремонтируемых изделий и малым объёмом их выпуска. На предприятиях с единичным производством применяют преимущественно универсальное оборудование, расположенное в цехах по групповому признаку (т.е. с разбивкой на участки токарных, фрезерных, строгальных станков и т.д). Обработку ведут стандартным режущим инструментом, а контроль – универсальным измерительным инструментом. Так как конструкции изготовляемых в единичном производстве машин нестабильны и подвергаются частым изменениям, то при обработке заготовок принципы полной взаимозаменяемости не соблюдаются ( иначе потребовалось бы большое количество специальных измерительных средств, затраты на изготовление которых чрезвычайно велики), поэтому при сборке применяют подгоночные работы.
Для предотвращения брака основные металлоёмкие дорогостоящие детали изготовляют раньше, чем сопрягаемые с ними более дешёвые детали, за счёт которых компенсируют отклонения размеров основных деталей, возникающие при их обработке.
Серийное производство характеризуется ограниченной номенклатурой изделий, изготовляемых или ремонтируемых периодически повторяющимися партиями, и сравнительно большом объёмом выпуска. В зависимости от кол-ва изделий в партии и значения коэффициента
закрепления операций различают мелкосерийное, среднесерийное и крупносерийное производство.
Коэффициент закрепления операций – это отношение числа всех различных технологических операций, выполненных или подлежащих выполнению в течение месяца, к числу рабочих мест.
К з.о = N т.о / n
Для мелкосерийного производства он составляет 20….40, для среднесерийного пр-ва 10….20.
для крупносерийного пр-ва 1….10.
На предприятиях серийного производства значительная часть оборудования состоит из универсальных станков, оснащённых как специальными, так и универсально-наладочными ( УНП) и универсально-сборными (УСП) приспособлениями, что позволяет снизить трудоёмкость и удешевить производство.
При небольшой трудоёмкости обработки или недостаточно большой программе выпуска изделий целесообразно обрабатывать заготовки партиями, с последовательным выполнением операций,
т.е.после обработки всех заготовок партии на одной операции производить обработку этой партии на следующей операции. Заготовки во время работы хранят у станков, а затем транспортируют целой партией.
В серийном производстве применяют так же переменно-поточную форму организации работ.
Здесь оборудование также располагают по ходу технологического процесса. Обработку производят партиями, причём заготовки каждой партии могут несколько отличаться размерами и конфигурацией, но допускают обработку на одном и том же оборудовании. В этом случае время обработки на смежных станках согласуют , поэтому движение заготовок данной партии осуществляют непрерывно, в порядке последовательности технологического процесса.Для перехода к обработке партии других деталей переналаживают оборудование и технологическую оснастку ( приспособления и инструмент).
Массовое производство характеризуется узкой номенклатурой и большим объёмом выпуска изделий, непрерывно изготавливаемых или ремонтируемых в течение продолжительного времени.
Коэффициент закрепления операций в этом типе производства принимают равным 1.
Массовое пр-во характеризуется установившимся объектом пр-ва, что при значительном объёме выпуска продукции обеспечивает возможность закрепления операций за определённым оборудованием с расположением его в технологической последовательности ( по потоку) и широким применением специализированного и специального оборудования, механизацией и автоматизацией производственных процессов при строгом соблюдении принципов взаимозаменяемости, обеспечивающих резкое сокращение трудоёмкости сборочных работ.
Высшей формой массового пр-ва является пр-во непрерывным потоком, когда длительности выполнения всех операций на технологической линии равны или кратны, что позволяет производить обработку без заделов в строго определённые промежутки времени. Интервал времени, через который периодически производится выпуск изделий определённого наименования, типоразмера и исполнения, называется тактом выпуска и подсчитывается по формуле:t= Фэ х 60 где t – такт, мин;
_______, Фэ –эффективный фонд производственного времени выпуска рабочего
n
места, участка, цеха (час),
n – годовая программа выпуска рабочего места, участка, цеха (шт).
Для выполнения операций, длительность которых не укладывается в установленный такт выпуска, используют дополнительное оборудование.
При непрерывном потоке передача с позиции на позицию (рабочее место)осуществляется непрерывно в принудительном порядке, что обеспечивает параллельное одновременное выполнение всех операций на технологической линии.
Тип производства характеризуется коэффициентом закрепления операций ( К з.о):
1= Кз.о <10 – при массовом и крупносерийном производстве;
10< Кз.о <20- при среднесерийном производстве;
20< Кз.о <40 – при мелкосерийном производстве.
Значение К з.о принимается для планового периода, равному одному месяцу.
Кз.о= О , где О –число различных операций;
Р Р – число рабочих мест , на которых выполняются различные операции.
Дифференциация и концентрация технологического процесса.
Для обработки одной и той же детали могут быть применены различные варианты ТП (технологического процесса). Существенное влияние на построение ТП оказывает тип произ-ва.
Так, в массовом и крупносерийном произ-вах ТП строится на принципе дифференциации или концентрации операций при возможно полной их автоматизации.
При использовании принципа дифференциации ТП расчленяется на элементарные операции с примерно одинаковым временем их выполнения, равным такту или кратному ему; на каждом станке выполняют определённые операции, преимущественно однопереходные или двухпереходные, например, центровка валиков, снятие фасок при доделке после обработки заготовок на автомате и т.д. В связи с этим здесь применяют специальные и узкоспециализированные станки ; специальные же приспособления для обработки предназначены для выполнения только одной операции . Часто такое специальное приспособление является частью станка .
При использовании принципа концентрации ТП предусматривает объединение операций, которые в этом случае производятся на многошпиндельных автоматах, п/автоматах, агрегатных, многопозиционных, многорезцовых станках, производящих одновременно несколько операций при малой затрате основного ( технологического) времени. Если число последовательных переходов, выполняемых на станке, значительно, то такое построение обработки называют последовательной концентрацией ТП.
Если одновременно значительное число переходов в одной операции выполняется параллельно, то такое построение обработки называют параллельной концентрацией ТП.
Параллельная концентрация связана с использованием многоинструментных станков( многорезцовых, многошпиндельных и т.д.), обеспечивающих высокую производительность; применение таких станков экономично при большом объёме выпуска продукции, характерным для крупносерийного и массового произв-ва.
Тема 1.2 Технологическая подготовка производства.
Разработка ТП входит основным разделом в технологическую подготовку производства и выполняется на основе принципов « Единой системы технологической подготовки производства»
( ГОСТ 14.001-73)
ГОСТ 14.301-83 этой системы устанавливают виды и общие правила разработки ТП, исходную информацию и перечень основных задач на этапах разработки.
Разрабатываемый ТП должен быть прогрессивным, обеспечивать производительность труда и качество деталей, сокращение трудовых и материальных затрат на его реализацию, уменьшение
Вредных воздействий на окружающую среду.
ТП разрабатывают на основе имеющегося типового или группового ТП. По технологическому классификатору формируют технологический код . По коду изделие относят к определённой классификационной группе и действующему для неё типовому или групповому ТП. При отсутствии соответствующей классификационной группы ТП разрабатывают как единичный, с учётом ранее принятых прогрессивных решений в действующих единичных ТП.
Важным этапом разработок является нормирование труда на выполнение процесса; определение разряда работ и обоснование профессий исполнителей для выполнения операций в зависимости от сложности этих работ; расчёт норм расхода материалов, необходимых для реализации процесса. В ходе разработок определяются требования охраны труда.
Целесообразность использования средств вычислительной техники при проектировании ТП определяется в соответствии с требованиями стандартов ЕСТПП. На завершающем этапе разработок выбирают оптимальный вариант ТП и рассчитывают его экономическую эффективность на основе существующих методик. При оформлении ТП по стандартам ЕСТД проводят нормоконтроль документации, согласование и утверждение в установленном порядке.
Базовой исходной информацией для проектирования ТП служат: рабочие чертежи, технические требования, регламентирующие точность , параметр шероховатости поверхности и др. требования качества; объём годового выпуска изделий, определяющий возможность организации поточного производства. Для поточного выпуска необходимо рассчитать такт выпуска.Для непоточного произв-ва важно знать ритмичность выпуска изделий и объём серий.
При проектировании необходимо изучить и использовать руководящую и справочную информацию. Рукововодящая информация предопределяет подчинённость принимаемых решений государственным и отраслевым стандартам, учёт принятых перспективных разработок.
К справочной информации относятся опыт изготовления аналогичных изделий, методические материалы и нормативы, результаты научных исследований.
Для разработки ТП обработки детали требуется предварительно изучить её конструкцию, функции, выполняемые в узле, механизме, машине, проанализировать технологичность конструкции и проконтролировать чертёж. Рабочий чертёж детали должен иметь все данные, необходимые для исчерпывающего и однозначного понимания при изготовлении и контроле детали, и соответствовать действующим стандартам.
Технологичность конструкции детали анализируют с учётом условий её производства, рассматривая особенности конструкции и требования качества как технологические задачи изготовления. Выясняют возможные трудности обеспечения параметров шероховатости поверхности, размеров, форм и расположения поверхностей, делают увязку с возможностями методов окончательной обработки, возможностями оборудования и метрологических средств.
Размеры элементарных поверхностей деталей (ширины канавок и пазов, резьбы, фасок и т.д) должны быть унифицированы.Ограничения при проектировании могут возникнуть, например, в случае слишком близкого расположения осей отверстий у деталей, невозможности сквозного прохода инструмента.
Анализируют специальные технические требования (балансировку, подгонку по массе, т/о, покрытия и т.д), предусматривают условия их выполнения в ТП и место проверки. Изменения утверждают в установленном порядке и вносят ( отдел гл.конструктора) в рабочие чертежи и технические требования на изготовление.
Для количественной оценки технологичности конструкции применяют показатели, предусмотренные ГОСТ 14.202-73. Показатели, характеризующие трудоёмкость, материалоёмкость, унификацию конструкции элементов детали, требования к точности изготовления, дают конкретные представления при сравнении с аналогичными деталями, принятыми в качестве базовых.
Заготовку выбирают исходя из минимальной себестоимости готовой детали для заданного годового выпуска. Чем больше форма и размеры заготовки приближаются к форме и размерам готовой детали, тем дороже она в изготовлении. Но тем проще и дешевле её последующая мех. обработка (м/о) и меньше расход материала. Задача решается на основе минимизации суммарных затрат средств на изготовление заготовки и её последующую обработку.
При выборе заготовки следует учитывать, что руководящим положениям об экономии материалов, создании безотходной и малоотходной технологии и интенсификации ТП в машиностроении отвечает тенденция использования более точной и сложной заготовки. Для таких заготовок требуется более дорогая технологическая оснастка в заготовительном цехе ( сложные штампы и комплекты модельной оснастки), затраты на которую могут оправдать себя лишь при достаточно большом объёме годового выпуска заготовок.
Размеры, припуски на обработку и механические свойства материала, поступающих на обработку заготовок должны соответствовать величинам, принятым при проектировании и изложенным в утверждённых ТУ ( технических условиях).
Стабильность характеристик качества заготовок существенно влияет на протекание ТП. В автоматизированном произ-ве при этом создаются условия для осуществления статистически управляемого ТП ( ГОСТ 15895-77), обеспечивающего получение деталей с заданными параметрами качества при минимальных затратах времени на регулирование хода ТП.
Применение прогрессивных заготовок со стабильными характеристиками качества явл-ся важным условием организации гибкого автоматизированного производства, требующего быстрой переналадки оборудования, оснастки.
При низкой точности размеров заготовок, увеличенных припусках, больших колебаниях твёрдости материала, плохом состоянии необработанных баз нарушается безотказность работы приспособлений, ухудшаются условия работы инструментов, снижается точность обработки, возрастают простои оборудования.
Выбор заготовки после соответствующих технико-экономических обоснований оформляют назначением класса точности по соответствующему ГОСТу на заготовки и указанием на чертеже заготовки технологических баз. После определения припусков на обработку на чертеже заготовки наносят общие припуски и обозначают отверстия, которые образуются в результате обработки, а в заготовке отсутствуют.
Маршрутную технологию разрабатывают, выбирая технологические базы и схемы базирования для всего ТП.
Выбирают две системы баз- основные базы и чёрные базы, используемые для базирования при обработке основных баз.
Всю м/о распределяют по операциям, и т.о., выявляют последовательность выполнения операций и их число; для каждой операции выбирают оборудование и определяют конструктивную схему приспособления.
На первых одной-двух операциях при базировании по чёрным базам обрабатывают основные технологические базы. Затем, выполняют операции формообразования детали до стадии чистовой обработки(точность 7-9-го квалитета). Далее осуществляют операции местной обработки на ранее обработанных поверхностях ( фрезеруют канавки и лыски, нарезают резьбу и зубья, сверлят отверстия). Затем выполняют отделочную обработку основных, наиболее ответственных поверхностей (точность 7-го квалитета); при необходимости за этим следует дополнительная обработка самых ответственных поверхностей с точностью 6-7-го квалитетов и параметрам шероховатости поверхности Ra=0,32 мкм и менее.
Построение маршрутной технологии во многом зависит от конструктивно-технологической особенности детали и требований точности, предъявляемых к её основным, наиболее ответственным поверхностям. Для основных поверхностей с учётом точности выбранной заготовки и достижимых коэффициентов уточнения при обработке, выбирают методы обработки, назначают число и последовательность выполняемых переходов, определяют содержание операций. Место обработки менее ответственных пов-тей определяется конкретными условиями и не является принципиально важным.
Если обработку этих пов-тей по расположению и видам применяемых инструментов можно вписать в основные операции, то её включают в состав этих операций в качестве переходов, выполняемых на черновой и чистовой стадиях обработки.
Деление всего объёма обработки на операции, выбор оборудования, формирование операций по содержанию зависят также от условий произв-ва.
В поточном пр-ве штучное время любой операции должно соответствовать такту выпуска, а для этого в некоторых случаях требуется применять специальные приспособления, инструментальные наладки и станки. Наиболее точные станки используют дл чистовой и отделочной обработки, выделяемой в отдельные операции. Чтобы избежать трудоёмких переустановок крупногабаритных и тяжёлых заготовок, черновую и чистовую обработку таких заготовок выполняют за одну операцию. Такое же построение маршрутной технологии характерно для любых деталей в мелкосерийном производстве. Во всех случаях выполнения черновой и чистовой обработки за одну операцию рекомендуется сначала провести черновую обработку всех поверхностей, а затем выполнить чистовую обработку тех. Поверхностей, для которых она необходима. В маршрутной технологии в процессе обработки предусматривается контроль с целью технологического обеспечения заданных параметров качества обрабатываемой детали.Технолог устанавливает объект контроля и его место, обращая внимание на операции, при которых точность обеспечивается наиболее трудно, назначает методы и средства контроля, выдаёт задание на их конструирование.
Операционную технологию разрабатывают с учётом места каждой операции в маршрутной технологии.
К моменту проектирования каждой операции известно, какие поверхности и с какой точностью были обработаны на предшествующих операциях, какие пов-ти и с какой точностью нужно обрабатывать на данной операции.
Проектирование операций связано с разработкой их структуры, с составлением схем наладок, расчётом настроечных размеров и ожидаемой точности обработки, с назначением режимов обработки, определением норм времени и сопоставлением её с тактом работы (в поточном произ-ве).При расчётах точности и проверке производительности может возникнуть необходимость в некоторых изменениях маршрутной технологии, выбора оборудования, содержания операции или условий её выполнения.
Операционная технология позволяет выдать задание на конструирование специального оборудования, средств механизации и автоматизации, на разработку средств технологического оснащения и метрологического процесса.
Технологический процесс должен обеспечить получение детали или изделия, отвечающим требованиям чертежа и ТУ, при наименьших затратах труда и материальных ресурсов. ТП должен содержать все данные , необходимые для подготовки производства и изготовления детали ( изделия). Кроме схемы обработки, методов крепления и базирования, применяемого оборудования и оснастки, ТП определяет размеры , последовательно придаваемые деталям на разных стадиях обработки, требования к чистоте и взаимному расположению поверхностей, режимы обработки и нормы времени , а также сведения о способе получения заготовки, материале, из которого она изготовлена, и обработке её до поступления в цех.
Основным документом , на основании которого ведётся обработка ТП, явл-ся рабочие чертежи изделия и ТУ на его изготовление.
Под технологичностью конструкции понимают степень учёта при конструкторском оформлении элементов машин факторов, влияющих на трудоёмкость обработки, производительность труда, соблюдение заданных допусков и в конечном итоге на стоимость изделия.
При проверке технологичности деталей надо согласовывать с конструкторами способы простановки размеров, требования к точности и взаимному расположению отдельных элементов, исключить из конструкции элементы, затрудняющие подвод и выход инструмента, а также формы, очерченные сложными кривыми и излишние требования к точности и чистоте обработки.
Необходимыми материалами для разработки ТП явл-ся данные об оборудовании: каталоги и паспорта.
Последовательность разработки ТП:
1.Определяют такт выпуска или размеры партии.
2.Определяют вид и размеры заготовки и величину припуска на обработку.
3.Устанавливают технологический маршрут- рациональную последовательность выполнения операций.
4.Выбирают способы установки заготовки, базовые пов-ти и способы закрепления заготовки на каждой операции.
5.Назначают станки для выполнения всех операций.
6.Выбирают универсальные приспособления и принципиальные схемы специальных приспособлений.
7.Расчленяют операции на переходы и проходы, устанавливают операционные размеры, допуски и припуски.
8.Подбирают типы и размеры режущего инструмента.
9.Устанавливают режимы резания, производят техническое нормирование и расчёты экономичности выбранной схемы ТП.
10.Определяют технологические карты.
Оформление технологической документации.
( См. ГОСТ 3.1102-81; ГОСТ 3.1118-82).
Для м/о при единичном и мелкосерийном производстве оформляют маршрутно- технологические карты, в которых указывается материал, размер заготовки, порядок выполнения операций и краткое их содержание, тип оборудования, разряд работы и норма времени.
При крупносерийном и массовом производствах ТП оформляется в виде комплекта карт, состоящие из операционных карт м/о, в которых подробно, по переходам изложено содержание операции; указаны режимы резания, режущие и измерительные инструменты; вычерчен эскиз детали с размерами, необходимые для выполнения операции, а также указаны материал и твёрдость детали, приспособления, норма времени , цех, тип ,№ станка.
Кроме операционных карт, составляется сводная технологическая карта. В ней кратко излагается содержание операции, указываются станок, на котором она выполняется и операционные нормы времени.
К документации ТП относятся также карта технологического контроля и сводная инструментальная карта. В картах технического контроля указываются, какие размеры и каким инструментом проверяется процент деталей, подвергаемых контролю и особые технические требования.
Инструментальные карты содержат перечень оснастки, применяемой при изготовлении детали, и служат для подготовки производства и учёта оснащённости ТП изготовления данной детали.
Для подготовки производства изделия составляют сводные ведомости технологической оснастки, в которых заносятся специальные приспособления, режущие, измерительные и вспомогательные инструменты, штампы, модели, прессформы.
В массовом производстве на отдельные операции с большим кол-вом переходов разрабатывают карты наладки , в которых даются схемы наладки, указывается инструмент, режимы обработки ит.д.
Для расчета норм времени на каждую операцию составляют нормировочные карты. Эти карты
Служат для учёта трудоёмкости процесса, расчёта численности рабочих и загрузки оборудования.
Выбор станков.
Правильный выбор оборудования – один из важнейших факторов успешного выполнения ТП. При выборе оборудования необходимо, кроме вида обработки ( токарная, шлифовальная и т.д), учитывать:
- характер производства;
-метод достижения заданной точности при обработке;
-необходимую сменную ( или часовую) производительность станка;
-соответствие станка размерам детали;
-мощность станка и её соответствие требованиям обработки;
-возможность обеспечения требуемой точности и чистоты обработки;
-удобство управления и обслуживания станка при обработке детали( удобство измерения, удаление стружки, подвод СОЖ);
-размеры станка;
-стоимость станка;
-возможность оснащения станка высокопроизводительным приспособлением и средствами механизации и автоматизации;
-кинематические данные станка ( число оборотов, величина и усилие подачи и т.д).
В единичном и мелкосерийном производстве выбирают универсальные станки ( станки общего назначения). В массовом и крупносерийном производстве выбирают специализированные и определённого назначения станки.
Однако, важнейшим фактором , определяющим выбор станка, явл-ся экономичность обработки: получение заданной производительности и точности при наименьших затратах.
Нормирование технологического процесса.
Существует три метода нормирования: опытно-статистический, суммарно-сравнительный и расчётно-аналитический.
Самым прогрессивным методом нормирования явл-ся расчётно- аналитический.
По этому методу техническая норма времени определяется на основе анализа ТП и учитывает кинематические и эксплуатационные возможности станка, прочность и стойкость инструмента, величину партии обрабатываемых деталей, средства , которыми оснащён процесс ( приспособления, измерительные инструменты, подъёмные и загрузочные средства и т.п).
Техническая норма штучного времени может быть определена:
Тш=То+Тв+Тто+Тоо+Тп, мин , где
То-основное ( машинное) время, в течение которого инструмент врезается в деталь, обрабатывает заданную поверхность и выходит из процесса резания;
Тв- вспомогательное время, необходимое на установку и снятие детали, включение и выключение станка, подвод и отвод инструмента, измерение детали и др. переходы, выполняемые рабочим и не вызывающие изменения размеров, формы и качества детали; сумма То+Тв – называется оперативным временем.
Тто – время технического обслуживания, затрачиваемое на установку, снятие и замену притупившихся инструментов, на заправку шлифовальных кругов, смазку и подналадку станка, уборку стружки в процессе работы и т.д.
Тоо- время на организационное обслуживание, затрачиваемое на подготовку станка к работе в начале смены, получение инструмента, заготовок и заданий, уборку станка в конце смены и передачи его сменщику; время на организационное обслуживание Тоо принимается в % к оперативному времени ( 5-6%);
Тп- время на отдых и физические потребности исчисляются в % к оперативному времени; при выполнении тяжёлых работ время Тп принимается большим, чем при выполнении лёгких работ.
Для расчёта загрузки оборудования и определения себестоимости обработки деталей пользуются калькуляционным временем:
Тк=Тш+Тпз , мин
N
Тпз –подготовительно- заключительное время, т.е время, затрачиваемое на подготовку и наладку станка для обработки данной партии деталей, получение необходимой оснастки, документации, а также на сдачу обработанных деталей, документации и оснастки;
n – кол-во деталей в партии.
Величина, обратная технической норме времени, называется нормой выработки.
Q=1 шт/ч,
Т
Т –норма времени,в час или
Q =420 шт/смена,
Т
420 – время смены в мин,
Т- норма времени в мин.
Определение нормы расхода материалов.
Основанием для расчёта норм расхода материала явл-ся чертёж заготовки, ТП и чертёж детали.
При определении нормы расхода материала на детали, изготовляемые из проката , надо учитывать не только длину заготовки, равную длине детали с припуском на обработку, но и расход материала на отрезку ( резцом, пилой и т.д), а также отход в случае некратности длины прутка длине заготовки и остаток, необходимый для зажима прутка при отрезке.
При расчёте норм расхода материала на детали , получаемые из листового металла, надо пользоваться картами раскроя металла и учитывать массу отходов, которые нельзя использовать для других деталей.
При определении нормы расхода материала на детали, изготовляемые из поковок или штамповок, необходимо учитывать . кроме массы заготовки, расход метала на угар, облой и клещевые концы, составляющий 15-25% массы заготовки.
Основанием для определения нормы расхода литых заготовок служит чертёж литой заготовки или чертёж детали с учётом припусков на чертёж литой заготовки или чертёж детали с учётом припусков на обработку и всех предусмотренных технологией отливки приливов, которые не удаляются в литейном цехе. В связи со сложностью конфигурации большинства отливок и многих штамповок и значительными допусками на толщину стенок нормы расхода металла для их изготовления уточняются путём взвешивания нескольких десятков заготовок из разных партий.
Тема 1.3 Точность механической обработки.
Под точностью обработки понимают степень соответствия обработанной детали прототипу, изображённому на чертеже. Точность обработки влияет на эксплуатационные качества и долговечность машин и приобретает большое значение при увеличении их скорости и удельных нагрузок. Кроме того, требуемая точность изготовления детали влияет на построение ТП, выбор припусков, трудоёмкость обработки деталей и сборки машин. Повышение точности обеспечивает взаимозаменяемость деталей.
В условиях единичного и мелкосерийного производства необходимая точность деталей достигается методом пробных проходов , т.е. снятием припуска при последовательных проходах под контролем измерительного инструмента. Такой метод не применяют при крупносерийном и массовом производстве, как неэкономичный. В серийном и массовом производстве требуемая точность детали достигается методом автоматического получения размеров. Станки предварительно настраивают на заданный размер, т.е рабочими звеньями станка, приспособления и инструмента придаётся определённое , конечное взаимное положение, которое и обеспечивает автоматическое получение требуемого размера детали.
Под точностью обработки понимают степень соответствия обработанной детали требованиям чертежа и ТУ.
Точность детали слагается из точности выполнения размеров, формы, относительного положения поверхностей детали и шероховатости поверхностей.
Под точностью формы поверхности понимают степень приближения её к геометрической форме.
Например, плоские поверхности могут иметь отклонения формы в виде непрямолинейности, т.е отклонения проверяемой поверхности в заданном направлении от прилегающей прямой.
Цилиндрические поверхности в поперечном сечении могут иметь отклонения от прилегающей окружности: овальность, огранку; в продольном сечении : бочкообразность, седлообразность, конусообразность, изогнутость. Относительное положение поверхности определяется обычно параллельностью, перепендикулярностью или симметричностью её относительно других поверхностей или осей.
Для проектирования технологического процесса , гарантирующего достижение этой точности, необходимо знать и учитывать погрешности , возникающие при обработке.
Основными причинами погрешностей обработки на металлорежущих станках следующие:
1) собственная неточность станка, например, непрямолинейность направляющих станины и суппортов, непараллельность или неперпендикулярность направляющих станины к оси шпинделя, неточности изготовления шпинделя и его опор и т.д;
2) деформация узлов и деталей станка под действием сил резания и нагрева;
3) неточность изготовления режущих инструментов и приспособлений и их износ;
4) деформация инструментов и приспособлений под действием сил резания и нагрева в процессе обработки;
5) погрешности установки заготовки на станке;
6) деформация обрабатываемой заготовки под действием сил резания и зажима, нагрева в процессе обработки и перераспределения внутренних напряжений;
7) погрешности, возникающие при установке инструментов и их настройке на размер;
8) погрешности в процессе измерения, вызываемые неточностью измерительных инструментов и приборов, их износом и деформациями, а также ошибками рабочих в оценке показаний измерительных устройств.
Собственная точность станков ,т.е точность их в ненагруженном состоянии, установлена ГОСТом для всех основных типов станков. По мере износа собственная точность станка уменьшается. Особое значение имеет износ подшипников и шеек шпинделей, а также направляющих станин. Биение шпинделя с овальной шейкой приводит к получению овальности у обтачиваемой заготовки. В следствие износа направляющих у токарного станка возникает , например, непрямолинейное движение суппорта, что приводит к искажению формы обтачиваемой цилиндрической заготовки.
В процессе обработки под действием сил резания узлы станка деформируются. Это вызывается неточностями пригонки стыковых поверхностей отдельных сопрягаемых элементов узлов. В результате таких деформаций могут получаться погрешности формы и относительного положения обрабатываемой поверхности. Величина упругой деформации тем больше, чем больше силы резания и меньше жёсткость узлов станка.
Большое значение вопросы точности приобретают при автоматизации произ-ва.
Каждая деталь ограничена комплексом поверхностей, часть из которых подвергается м/о. Потому, говоря о точности, подразумевают следующие понятия:
1. Точность выполнения размеров отдельных поверхностей детали, (ф вала или отверстия, угол и длина конуса, глубина отверстия или паза), котор. Регламентируются допусками, указанными в чертежах.
2. Точность выполнения формы поверх-тей, под котор. подразумевается степень соответствия их формам, заданным в чертеже.
Погрешности формы весьма разнообразны:
Предельные отклонения от формы для плоскостей и цилиндрических поверхностей приведены в ГОСТе 10356-63.
Цилиндрические поверхности могут иметь овальность, гранёность,бочкообразность,корсетность, кривизну и конусность.
Плоскости могут иметь выпуклости, вогнутости, скрученности и др. искажения. Например,
профиль поверх-ти зуба шестерни или нитки резьбы могут быть отклонены от теоретической формы эвольвенты или спирали и т.д.
Неточность формы пов-тей оказывает большое влияние на работоспособность машины. Допускаемая величина отклонения формы пов-ти нередко задаётся частью допуска на её размер.
3. Точность взаимного расположения поверхностей деталей.
Погрешности взаимного расположения поверхностей деталей даже при правильных размерах и форме могут привести к нарушениям работы детали в машине.
К таким погрешностям относятся несоосность шеек вала или наружной и внутренней пов-ти полой детали ( эксцентриситет), непараллельность или неперпендикулярность оси цилиндрической поверхности к её торцу, ошибки углового расположения поверх-ти ( шатунных шеек коленчатого вала, зубьев шестерён), непараллельность и неперпендикулярность плоских пов-тей (( верхней, нижней и торцовой пов-тей блока) и т.п.
Предельно допустимые отклонения от теоретической формы, размеров или взаимного расположения пов-тей, оговорённое чертежом, называется допуском.
Величина допустимого отклонения назначается из условий работы и сопряжения деталей в соот-
ветствии с ГОСТами.
Классы точности определяют величину допускаемых отклонений, а посадки – характер соединений и величину зазоров и натягов между сопрягаемыми поверх-ми.
Точность, заданная чертежом, может быть обеспечена разными технологическими методами.
В условиях единичного произ-ва точность взаимного положения поверх-тей обеспечивается выверкой , а точность размеров – пробными проходами – последовательным снятием стружки и пробными промерами в начале каждого прохода; при этом точность в значительной степени зависит от квалификации рабочего.
В условиях мелкосерийного произ-ва для обеспечения размеров обработанной детали применяется установка по лимбу, нужное деление которого определяется пробной обработкой первой детали или по эталону.
В серийном и массовом произ-ве точность обеспечивается предварительной настройкой станка, приспособления и инструмена, т.е. способом автоматического получения заданных размеров; при этом установка детали в приспособлении обеспечивает взаимное положение поверх-тей, а установка инструментов относительно обрабатываемой детали – точность размеров.
При обработке деталей на автоматических станках и автоматических линиях применяются измерительные и регулирующие устройства( подналадчики), котор. В случае выхода детали за пределы допуска, автоматически подналаживают станок на заданный размер. Такие устройства называют устройствами с обратной связью.
При использовании мерных режущих инструментов ( свёрла, зенкера, развёртки, протяжки, мерные фрезы и резцы, фасонные инструменты) точность раз-ров обрабатываемых поверх-тей зависит от раз-ров и состояния инструмента и правильности его установки.
Основные причины, вызывающие погрешности при обработке деталей:
1. геометрические погрешности станка, допущенные при его изготовлении или вызванные износом его деталей;
2. упругие деформации технологичской системы станок- приспособление-инструмент-деталь под действием сил резания;
3. погрешности установки заготовок на станок;
4. размерный износ инструмента;
5. погрешности настройки станка на выполняемый размер;
6. температурные деформации отдельных элементов системы станок- приспособление-инструмент-деталь;
7. погрешности, связанные с внутренними напряжениями в материале заготовки.
В результате суммирования перечисленных погрешностей детали в процессе обработки получаются с отклонениями от заданных раз-ров. Эти погрешности могут быть систематическими и случайными.
Систематические погрешности возникают в силу вполне определённых причин и остаются постоянными или закономерно изменяются .К постоянным систематическим погрешностям можно отнести погрешности формы деталей, вызываемые геометрическими погрешностями станка на размер при обработке одной партии заготовок. Примером могут служить погрешности, вызываемые износом режущего инструмента. В большинстве случаев при выборе ТП можно учесть влияние указанных погрешностей и принять меры для их устранения.
Случайные погрешности возникают в рез-те действий множества различных не связанных между собой причин. К ним относятся погрешности , вызванные разной твёрдостью заготовок или неравномерным припуском на обработку, изменением усилия зажима детали в приспособлении и т.д.
В результате влияния систематических и случайных погрешностей размеры обрабатываемых деталей будут переменными .Это явление носит название рассеивание размеров.
Величину постоянных систематических погрешностей можно определить расчётным путём.
Можно рассчитать погрешность формы обработанной детали, связанную с геометрическими погрешностями станка ( погрешностями от биения шпинделя). Однако, во многих случаях, когда действует несколько факторов, в том числе и случайные, расчёт затрудняется и делается неточным.В таких случаях используют статистический метод определения погрешностей.
При использовании специальных методов обработки может быть достигнута очень высокая точность с отклонениями от заданных размеров в десятых и сотых долях микрона. Однако при проектировании ТП необходимо учитывать , что повышение точности станка, инструмента, приспособления, применение высококвалифицированного труда и увеличение затраты времени вызывает увеличение стоимости обработки. Поэтому для каждого вида оборудования устанавливается точность обработки, достижимая при высокой производительности труда и низкой стоимости обработки- экономическая точность обработки.
Экономическая точность обработки является величиной условной. Она характеризуется средними отклонениями размеров обрабатываемых деталей, получаемыми с наименьшими затратами труда и средств в конкретных производственных условиях. Незначительные изменения технологии и производственных условий вызывают изменение экономической точности обработки.
Например, при переходе от обработки запорного конца иглы распылителя в цанговом зажиме к обработке в призме точность повышается в 5-10 раз без существенного увеличения затрат.
Технологический процесс может быть устойчивым или неустойчивым, налаженным или разлаженным, вследствие чего качество деталей может получаться однородным или неоднородным.
Детали однородного качества имеют незначительные колебания, в то время как детали неоднородного кач-ва характериз-ся большими колебаниями размеров, формы или свойства.
С помощью кривых распределения исследуют точность обработки законченного технологического процесса. При этом не учитывается последовательность обработки заготовок, т.к. все заготовки данной партии перемешиваются, и систематические постоянные и переменные погрешности не отделяются от случайных, и влияние как тех, так и других выражается в общем виде как рассеивание размеров.
Статистический метод исследования точности обработки с построением точечных диаграмм свободен от этих недостатков и позволяет исследовать технологический процесс ТП значительно глубже, чем метод кривых распределения; при этом оказывается возможным разделить влияние случайных и систематических погрешностей ( как постоянных, так и изменяющихся).
Несколько образцов, взятых для измерения сразу после обработки, называют пробой. Для того, чтобы пробы могли быть сравнимы между собой, число деталей в них каждый раз должно быть одинаковым.
Чтобы подналадка процесса обработки была сведена к min и производилась как можно реже, необходимо стремиться использовать полный р-р поля допуска от наладки до наладки. Для этого работу после наладки начинают с р-ра , противоположного тому, котор. определяет момент остановки процесса для очередной наладки станка, а не со среднего раз-ра, расположенного где-то около середины поля допуска, и тем более не с раз-ра, близкого к границе допуска, на котор. необход. остановить станок для очередной наладки.
Допуски формы и расположения поверхностей деталей машин и приборов, термины, определения, относящиеся к основным видам отклонений, стандартизованы ГОСТом 24642 – 81*.
В основу нормирования и систему отсчета отклонений формы и расположения поверхностей положен принцип прилегающих поверхностей и профилей, элементов, деталей, сборочных единиц (узлов). Все отклонения и допуски подразделяются на три группы: формы; расположения; суммарные – формы и расположения.
Общие термины и определения
Профиль—это линия пересечения поверхности с плоскостью или заданной поверхностью. Различают профили номинальной и реальной поверхностей.
Нормируемый участок - это участок поверхности или линии, к которому относится допуск на отклонение формы или расположение элемента. Нормируемый участок должен задаваться размерами, определяющими его площадь, длину или угол сектора (в полярных координатах). Если нормируемый участок не задан, то допуск или отклонение формы или расположения должен относиться ко всей поверхности или длине рассматриваемого элемента.
База - элемент детали (или выполняющее ту же функцию сочетание элементов), определяющий одну из плоскостей или осей системы координат
по отношению к которой задается допуск расположения или определяется отклонение расположения рассматриваемого элемента. Базами могут быть, например, базовая плоскость, базовая ось, базовая плоскость симметрии.
Комплект баз - совокупность двух или трех баз, образующих систему координат, по отношению к которой задается допуск расположения или определяется отклонение расположения рассматриваемого элемента.
Прилегающая плоскость и прилегающая прямая - плоскость или прямая, соприкасающаяся с реальной поверхностью или профилем и расположенная вне материала детали так, чтобы отклонение от нее наиболее удаленной точки соответственно реальной поверхности или профиля в пределах нормируемого участка имело минимальное значение (рис. 2.15, а).
Прилегающая окружность - это окружность минимального диаметра, описанная вокруг реального профиля (для наружной поверхности вращения), или максимального диаметра, вписанная в реальный профиль (для внутренней поверхности вращения) (рис. 2.15, б и в).
Прилегающий цилиндр - это цилиндр минимального диаметра, описанный вокруг реальной поверхности (для наружной поверхности вращения), или максимального диаметра, вписанный в реальную поверхность (для внутренней поверхности вращения).
Прилегающий профиль продольного сечения цилиндрической поверхности – две параллельные прямые, соприкасающиеся с реальным профилем (двумя реальными образующими, лежащими в продольном сечении) и расположенные вне материала детали так, чтобы наибольшее отклонение точек образующих профиля имело минимальное значение (рис. 2.16).
Общая ось - это прямая, относительно которой наибольшее отклонение осей нескольких рассматриваемых поверхностей вращения в пределах длины этих поверхностей, имеет минимальное значение (рис. 2.17, а). Для двух поверхностей общей осью является прямая, проходящая через оси рассматриваемых поверхностей в их средних сечениях (рис. 2.17, б).
К отклонениям формы относятся отклонения прямолинейности, плоскостности, круглости, профиля продольного сечения и цилиндричности.
Отклонения формы плоских поверхностей. Отклонение от плоскостности определяют как наибольшее расстояние D от точек реальной поверхности до прилегающей плоскости в пределах нормируемого участка (рис. 2.20, а). Частными видами отклонений от плоскостности являются выпуклость (рис. 2.20, б) и вогнутость (рис. 2.20, в). Отклонение от прямолинейности (см. рис. 2.15, а) определяют как большее расстояние D от точек реального профиля до прилегающей прямой.
Таблица 2.7
Допуски формы и расположения и их условные знаки
Группа допусков | Вид допуска | Знак | Группа допусков | Вид допуска | Знак |
| Прямолинейности | Суммарные допуски формы и расположения | Радиального биения |
| |
Плоскостности | Торцового биения | ||||
Круглости | Биения в заданном направлении | ||||
Профиля продольного сечения | Полного радиального биения |
| |||
Цилиндричности | Полного торцового биения | ||||
| Параллельности | ||||
Перпендикулярности | Формы заданного профиля |
| |||
Наклона | |||||
Соосности | |||||
Симметричности | Формы заданной поверхности |
| |||
Позиционный | |||||
Пересечения осей |
А) б) в)
А) б) в) г) д)
Е) ж)
Кроме нанесения отклонений формы и расположения на чертеже иногда применяют текстовые записи в случаях, когда условные обозначения слишком затемняют чертеж или не раскрывают полностью технических требований к изготовлению детали. В текстовой части дается краткое наименование заданного отклонения и буквенное обозначение или наименование параметра (например, поверхности), для которого задаются отклонение и его числовая величина. Если допускаемое отклонение относится к расположению поверхностей, то показываются еще и базы, относительно которых задано отклонение.
Допуск плоскостности | Допуск плоскостности поверхности не более 0,06 мм | |
Допуск прямолинейности | Допуск прямолинейности поверхности не более 0,25 мм на всей длине и не более 0,1 мм на длине 300 мм | |
Допуск цилиндричности, круглости и профиля продольного сечения | Допуск цилиндричности поверхности А не более 01 мм, круглости не более 0,004 мм, профиля продольного сечения не более 0,004 мм | |
Допуск параллельности | Допуск параллельности общей оси отверстий относительно поверхности А не более 0,01 мм | |
Допуск перпендикулярности и плоскостности | Б А | Суммарный допуск перпендикулярности и плоскостности поверхности Б относительно поверхности А 0,2 мм |
Допуск соосности | Б А | Допуск соосности поверхностей А и Б Æ 0,2 мм (допуск зависимый в диаметральном выражении) |
Допуск симметричности (в диаметральном выражении) | Допуск симметричности поверхностей Б относительно оси отверстия Т 0,04 мм | |
Допуск наклона | Б 30о А | Допуск наклона порверхности Б относительно поверхности А 0,1 мм |
Допуск пересечения осей (в радиусном выражении) | А | Допуск пересечения осей отверстий Т/2 0,06 мм |
| ||
![]() ![]() | A 4 отв.Æ… | Позиционный допуск осей отверстий А Æ 0,2 мм (допуск зависимый) |
Допуск полного радиального биения | В А Б А Б | Допуск полного радиального биения поверхности В относительно общей оси поверхностей А и Б 0,1 мм |
Допуск торцового биения | А Б | Допуск торцового биения поверхности Б относительно оси поверхности А 0,1 мм на диаметре 50 мм |
Допуск формы заданной поверхности | А | Допуск формы заданной поверхности А Т 0,02 |
Тема 1.4 Качество поверхности детали.
Обработанные поверхности не явл-ся идеально гладкими; они имеют шероховатости, величина форма котор. зависит от метода обработки, формы и состояния инструмента, а так же от свойств материала обрабатываемой детали. Величина шероховатости, или как её называют, микрогеометрия поверхности, характеризует чистоту обработки.
Качество обработанной поверхности характеризуется также физико-механическими свойствами поверхностного слоя, котор. во время обработки под действием давления при резании,трения инструмента о поверхность детали и пластических деформаций изменяется и отличаются от св-в необработанных поверхностей.
От чистоты и качества пов-ти зависят износостойкость трущихся поверхностей, усталостная прочность, устойчивость против коррозии, надёжность неподвижных посадок.
Шероховатостью поверхности согласно ГОСТу 25142 - 82 называют совокупность неровностей поверхности с относительно малыми шагами, выделенную с помощью базовой длины. Базовая длина l — длина базовой линии, используемой для выделения неровностей, характеризующих шероховатость поверхности. Базовая линия (поверхность) — линия (поверхность) заданной геометрической формы, определенным образом проведенная относительно профиля (поверхности) и служащая для оценки геометрических параметров поверхности.
Шероховатость поверхности оказывает существенное влияние на эксплуатационные свойства поверхностного слоя, следовательно, детали в целом. К показателям, характеризующим эксплуатационные свойства поверхностного слоя, относятся: действительное напряжение на поверхности двух взаимодействующих тел и, как следствие, контактная жесткость; прочность деталей из-за концентрации напряжений в отдельных рисках на поверхности; характер процесса трения между сопрягаемыми поверхностями в паре трения; изменение посадки в процессе сборки (с натягом) или при эксплуатации (с зазором); антикоррозионная стойкость повехностей; плотность и герметичность соединений; адгезионная способность к гальваническим и лакокрасочным покрытиям; декоративные свойства; удобство содержания поверхностей в чистоте и т. п..
Числовые значения шероховатости поверхности определяют от единой базы, за которую принята средняя линия профиля т, т. е. базовая линия, имеющая форму номинального профиля и проведенная так, что в пределах базовой длины среднее квадратическое отклонение профиля до этой линии минимально. Систему отсчета шероховатости от средней линии профиля называют системой средней линии.
Если для определения шероховатости выбран участок поверхности длиной l, другие неровности (например, волнистость), имеющие шаг больше l, не учитывают.
Длина оценки L - длина, на которой оценивают шероховатость. Она может содержать одну или несколько базовых длин l. Числовые значения базовой длины выбирают из ряда: 0,01; 0,03; 0,08; 0,25; 0,80; 2,5; 8; 25 мм.
Параметры шероховатости. Согласно ГОСТу 2789 – 73* шероховатость поверхности изделий независимо от материала и способа изготовления можно оценивать следующими параметрами (рис. 2.11):
Рис. 2.11. Профилограмма поверхности
1. Среднее арифметическое отклонение профиля Ra - среднее арифметическое из абсолютных значений отклонений профиля в пределах базовой длины:
,
где l — базовая длина; n — число выбранных точек профиля на базовой длине; у — расстояние между любой точкой профиля и средней линией (отклонение профиля).
2. Высота неровностей профиля по десяти точкам Rz — сумма средних абсолютных значений высот пяти наибольших выступов профиля и глубин пяти наибольших впадин профиля в пределах базовой длины:
или
,
где
определяются относительно средней линии, а hi max, hi min –относительно произвольной прямой, параллельной средней линии и не пересекающей профиль.
3. Наибольшая высота неровностей профиля Rmax — расстояние между линией выступов профиля и линией впадин профиля в пределах базовой длины.
4. Средний шаг неровностей профиля Sm — среднее арифметическое значение шага неровностей профиля в пределах базовой длины:
,
где Smi — шаг неровностей профиля, равный длине отрезка средней линии, заключенного между точками пересечения смежных выступов и впадин профиля со средней линией.
5. Средний шаг неровностей профиля по вершинам S — среднее арифметическое значение шага неровностей профиля по вершинам в пределах базовой длины:
,
Si — шаг неровностей профиля, равный длине отрезка средней линии, заключенного между проекциями на нее наивысших точек двух соседних местных выступов профиля.
6. Относительная опорная длина профиля tр — отношение опорной длины профиля к базовой длине:
,
где hр - опорная длина профиля — сумма длин отрезков bi, отсекаемых на заданном уровне р в материале профиля линией, эквидистантной средней линии т в пределах базовой длины (см. рис. 2.11):
.
Опорную длину профиля определяют на уровне сечения профиля р, т. е. на заданном расстоянии между линией выступов профиля и линией,
|










Числовые значения параметров шероховатости Ra, Rz, Rmax, Sm, S и tp приведены в ГОСТе 2789 – 73*.
Обозначение шероховатости на чертежах. ГОСТ 2.309 – 73* устанавливает обозначения шероховатости поверхностей и правила нане-
сения их на чертежах изделий.
На рис. 2.13 приведена структура обозначения шероховатости. При обозначении шероховатости только по параметру применяют знак без полки.
Примеры обозначения шероховатости на чертежах приведены на рис. 2.14. В обозначении числового значения
параметра Ra символ не указывается (см. рис. 2.14).
а) б) в)
Рис. 2.14. Примеры обозначения шероховатости на чертежах
Если параметры Rа, Rz, Rmax определены на базовой длине в соответствии с ГОСТом 2789 – 73*, то эти базовые длины не указываются в требованиях к шероховатости (рис. 2.14, б).
При необходимости дополнительно к параметрам шероховатости поверхности устанавливаются требования по направлению неровностей поверхности (табл. 2.5), а также по способу или последовательности способов получения (обработки) поверхности. При этом способ обработки указывают только в случаях, когда он является единственно приемлемым для получения требуемого качества поверхности.
Таблица 2.5
Направления неровностей поверхности по ГОСТу 2789 – 73*
Типы направления неровностей | Схематическое изображение | Условное обозначение | ||
![]() ![]() ![]() ![]() ![]() ![]() ![]() | ||||
![]() ![]() ![]() ![]() ![]() ![]() ![]() ![]() | ||||
![]() ![]() ![]() ![]() ![]() ![]() | ||||
![]() ![]() ![]() ![]() ![]()
![]() | ||||
![]() ![]() ![]() ![]()
![]() ![]() ![]() ![]() | ||||
![]() ![]() ![]() ![]() ![]() ![]() ![]() ![]() ![]() ![]() ![]() |
При указании двух и более параметров шероховатости поверхности значения параметров записывают сверху вниз в следующем порядке: высота неровностей профиля, шаг неровностей профиля, относительная опорная длина профиля (рис. 2.14, а).
Таблица 2.5
Влияние микрогеометрии пов-ти на износостойкость трущихся деталей объясняется тем, что при скольжении одной пов-ти относительно др, происходит разрушение выступающих частей гребешков, отрыв частиц металла в результате сваривания их в местах точечного контакта при нарушении целостного масляного слоя.
В начале процесса приработки деталей износ происходит быстро вследствие усиленного истирания верхних гребешков; затем износ происходит медленно. Он вызывается разрушением трущихся поверхностей в рез-те абразивного действия частиц, образующихся при разрушении гребешков, пыли и грязи, попадающих вместе со смазкой, а также электрохимическими процессами.
Уменьшение микронеровности при обработке повышает износостойкость пов-тей. Микрогеометрия пов-ти оказывает значительное влияние на усталостную прочность, т.к. имеющиеся на пов-ти детали риски вызывают концентрацию напряжений и могут привести к разрушению детали. Например, при наличии рисок от обработки на образцах из конструкционной, углеродистой стали их прочность снижается до 20%, а на образцах из легированных сталей – почти вдвое.
Понижение коррозионной стойкости грубо обработанных деталей объясняется тем, что впадины между гребешками, в котор. Сосредотачивается влага, явл-ся очагами распространения коррозии в теле детали.
Величина шероховатости влияет на надёжность неподвижных посадок, т.к. при разрушении выступов гребешков, по котор. Определяется р-р деталей, может уменьшиться расчетный натяг.
В отдельных случаях пов-ти деталей обрабатывают с повышенной частотой для обеспечения хорошего внешнего вида или для подготовки к гальваническим покрытиям.
Шероховатость поверхности определяется одним из следующих параметров:
а) средним арифметическим отклонением профиля Ra, которое равно среднему значению расстояний ( у1,у2,у3,……уn) точек измеренного профиля до его средней линии m.
б) высотой неровностей Rz, котор. Равна среднему расстоянию между находящимися в пределах базовой длины пятью высшими точками выступов с пятью низшими точками впадин, измеренному от линии, параллельной средней линии профиля:
Rz=( h1+ h3+….. h9)-( h2+ h4+….. h10)
5
Базовая длина согласно ГОСТу 2789-73 принимается в пределах 0,08-8 мм для разных классов точности.
Установлено 14 классов чистоты поверхности, для котор. Максимальные числовые значения шероховатости Ra и Rz соответствуют определённым базовым длинам. На этой базовой длине осуществ-ся измерение шероховатости поерхности, котор. должно производиться в направлении наибольшего значения параметра Ra или Rz.
ГОСТ 2789-73 устанавливает следующие параметры шероховатости:
Ra- среднее арифметическое отклонение профиля (Ra = 400…..0,008 мкм);
Rz – высота неровностей профиля по десяти точкам (Rz = 1600….0,025 мкм);
Sm- средний шаг неровностей (Sm=12,5….0,002 мм);
l–длина профиля.
Параметр Ra является предпочтительным.
В соответствии с ГОСТ 2.309-73 для обозначения шероховатости поверхностей, вид обработки котор. не установлен, применяется знак .
Шероховатость пов-ти, образуемой удалением слоя металла, например, точением, сверлением, фрезерованием, шлифованием, травлением и др. обозначают знаком , а шероховатость пов-ти, образуемой без удаления слоя металла, например, литьём, штамповкой и пр, а также не обрабатываемой по данному чертежу - знак .
Значение параметра шероховатости указывают: для параметра Ra без символа, например,
а для остальных параметров – после соответствующего символа, например .
При необходимости указания кроме параметра вида обработки базовой длины, условного обозначения направления неровностей применяют знак с полкой, например,
Волнистость поверхности представляет собой совокупность периодически чередующихся возвышенностей и впадин с отношением L=50….1000
h
Волнистость является следствием вибрации технологической системы, а также неравномерности процесса резания.
Оценку чистоты поверхности можно производить двумя методами: качественным и количественным.
При качественном методе обработанную поверхность сравнивают с образцом-эталоном визуально, путём ощупывания или сопоставления обработанной поверхности с эталоном под микроскопом. Этим методом можно определять чистоту пов-ти не выше 7-8-го класса.
При количественной оценке применяют оптико-механические профилографы ( для замера чистоты поверхностей 3-10-го классов, точность измерения 0,1-0,2 мкм), электродинамические, пьезоэлектрические и индуктивные профилометры ( для оценки чистоты в пределах 5-12-го классов), двойной микроскоп Линника ( для замеров средней высоты гребешков пов-тей 3-8 классов) и микроинтерферометр Линника (позволяющий измерить неровности для контроля в пределах 10-14 классов чистоты)
На оптико-механических и электрических приборах высота неровностей определяется путём контакта измерительной иглы с с проверяемой поверхностью.
Классы шероховатости поверхности по ГОСТ 2789.
Класс | Обозначение | Ra (мкм) | Rz(мкм) | Базовая длина l,мм |
1-й 2-й 3-й | V1 V2 V3 | 80 40 20 | 320 160 80 | 8 |
4-й 5-й | V4 V5 | 10 5 | 40 20 | 2,5 |
6-й 7-й 8-й | V6 V7 V8 | 2,5 1,25 0,63 | 10 6,3 3,2 | 0,8 |
9-й 10-й 11-й 12-й | V9 V10 V11 V12 | 0,32 0,16 0,08 0,04 | 1,6 0,8 0,4 0,2 | 0,25 |
13-й 14-й | V13 V14 | 0,02 0,01 | 0,1 0,05 | 0,08 |
Для классов 6-12 основной является шкала Ra (мкм), а для классов 1-5и 13-14 –шкала Rz(мкм).
Некоторые методы обработки, которые обеспечивают следующие классы шероховатости поверхности по ГОСТ 2789.
Точение,строгание, растачивание: Классы шероховатости
Черновое 1-4-й
Чистовое 4-7-й
Тонкое 7-9-й
Фрезерование (цилиндрическое)
Черновое 2-5-й
Чистовое 5-7-й
Тонкое 6-8-й
Шлифование:
Предварительное 6-7-й
Чистовое 8-9-й
Тонкое 9-10-й
Притирка:
Грубая 8-9-й
Средняя 9-10-й
Тонкая 10-13-й
Под волнистостью поверхности понимают совокупность периодически повторяющихся неровностей, у которых расстояния между смежными возвышенностями или впадинами превышают базовую длину l. Волнистость занимает промежуточное положение между отклонениями формы и шероховатостью поверхности. Условно границу между различными порядками отклонений поверхности можно установить по значению отношения шага Sw к высоте неровностей Wz. При (Sw/Wz)< 40 отклонения относят к шероховатости поверхности, при 1000 ³(Sw/Wz) ³40 — к волнистости, при (Sw/Wz) > 1000 —к отклонениям формы.
Параметры волнистости установлены рекомендацией СЭВ (РС 3951 - 73).
Высота волнистости (рис. 2.27, а) Wz = (1/5)×(W1+W2+W3+W4+W5).
![]() ![]() ![]() ![]() ![]() |
Наибольшая высота волнистости Wmax — расстояние между наивысшей и наинизшей точками измеренного профиля в пределах длины Lw, измеренное на одной полной волне.
Средний шаг волнистости (рис. 2.27, б) .
Размерный анализ.
Качество изготовления и сборки деталей обеспечиваются правильной простановкой размеров на рабочих и сборочных чертежах. В большинстве случаев отдельные раз-ры , отнесённые к одной или к группе деталей, находятся во взаимосвязи друг с другом; изменение одного из размеров влияет на один или несколько других размеров.
Размерной цепью называется совокупность р-ров (звеньев), образующих замкнутый контур и отнесённых к одной детали или к группе деталей.
Звеном размерной цепи называется один из раз-ров, образующих размерную цепь.
Различают следующие виды размерных цепей:
1) с линейными размерами и параллельными звеньями; к ним относится большинство размерных цепей.
Рис.
2)с линейными размерами и непараллельными звеньями; к этой группе может быть отнесён любой многоугольник, если каждая сторона его задана линейным размером, причём если спроектировать все размеры А-Е на одну ось, то эту группу можно свести к первому виду размерных цепей;
Рис.
3) с угловыми размерами; для этого вида цепей характерны детали с несколькими отверстиями, равномерно расположенными по окружности, если расстояния между центрами отверстий заданы в угловых единицах, а также детали, требующие при обработке деления окружности на равное число частей , например, зубчатые и червячные колёса, фрезы и т.п; из-за трудности точного измерения угловых величин угловые размерные цепи часто заменяют линейными с непараллельными звеньями; контроль размеров возможен с помощью калибров для межцентровых расстояний.
Рис.
4) пространственные, звенья которых расположены в непараллельных плоскостях; такие размерные цепи встречаются очень редко и для их решения проектируют все раз-ры на одну плоскость.
Наименьшее число звеньев размерной цепи равно трём .
Все звенья размерной цепи подразделяют на две группы: составляющие звенья и замыкающее звено.
Замыкающим звеном называют звено, получаемое в процессе изготовления и измерения последним. Получение того или иного звена в качестве замыкающего зависит от порядка обработки заготовок или сборки деталей.
Так, при обработке ступенчатого вала ( рис.1), чтобы звено В было обработано последним,
Нужно сначала отрезать заготовку размером А, затем, обтачивая вал в размере малого диаметра d, выдержать в пределах заданной точности размер Б, и тогда размер В получится последним.
Если в качестве замыкающего звена нужно иметь общий размер ступенчатого вала по длине А, то в этом случае заготовку берут несколько большей длины, чем размер А. В начале обтачивают меньшую ступень вала на длину В, а затем отрезают готовую деталь, выдерживая размер Б. Общая длина вала при этом будет замыкающим звеном, имеющим размер А.
Т.о, меняя порядок обработки, можно в качестве замыкающего звена получить любое звено размерной цепи.
Звено размерной цепи , изменение котор. вызывает изменение исходного звена (для его решения и используется размерная цепь) или замыкающего звена, называется составляющим.
Составляющие звенья размерной цепи подразделяются на две группы: увеличивающие и уменьшающие.
Увеличивающим называют такое звено, которое при своём увеличении увеличивает размер исходного или замыкающего звена.
Уменьшающее звено при своём увеличении уменьшает размер исходного или замыкающего звена.Так, если у ступенчатого вала (рис.!) принять в качестве замыкающего звено В, то звено А будет увеличивающим, а звено Б – уменьшающим.
Правильность размерного расчёта зависит от правильности нахождения увеличивающих и уменьшающих звеньев.
Общее правило для нахождения увеличивающих и уменьшающих звеньев заключается в составлении уравнения номинальных размеров, связывающего все члены размерной цепи, и решения его относительно номинального раз-ра замыкающего звена. Тогда все члены правой части уравнения со знаком «+» будут увеличивающими звеньями, а со знаком «-»
Уменьшающими.
При решении размерных цепей возникает две задачи: прямая и обратная.
При прямой задаче по допускам составляющих звеньев находят допуск замыкающего звена.
При обратной задаче по допуску замыкающего звена определяют допуск составляющих звеньев.
Для решения прямой задачи на максимум и минимум возьмём простейшую размерную цепь, рис.1 с замыкающим звеном В, в котором А- является увеличивающим , а Б- уменьшающим звеном.
Из рис.1 видно, что А=Б+В, отсюда В=А-Б.
В общем случае для любого числа звеньев размерной цепи уравнение номинальных размеров будет В=ЕА-ЕБ.
Т.о, номинальный раз-р замыкающего звена В равен сумме номинальных раз-ров всех увеличивающих звеньев А без суммы номинальных раз-ров всех уменьшающих звеньев Б.
Из рис.1 видно, что предельные значения замыкающего звена В зависят от предельных значений составляющих звеньев А и Б:
Вб= Аб-Бм; Вм=Ам-Бб ; где
Аб,Бб,Вб и Ам,Бм,Вм – наибольшие и наименьшие значения звеньев.
Вычтя почленно второе уравнение из первого, найдём :
Вб-Вм=(Аб-Бм)-(Ам-Бб),
раскрыв скобки и переставив члены, получим:
Вб-Вм=(Аб-Ам)+(Бб-Бм),
но разность предельных раз-ров есть допуск на это размер , следовательно,
б В=б А+ б В.
Отсюда для любой размерной цепи с числом звеньев n , обозначив бз допуск замыкающего звена, имеем :
б з = ∑ бn
Т.о, допуск замыкающего звена размерной цепи равен сумме допусков всех составляющих звеньев. Приведённое уравнение явл-ся основным уравнением размерного анализа, из которого вытекают два правила:
1. В качестве замыкающего звена в размерной цепи надо выбирать самое грубое ( с точки зрения эксплуатации) по точности звено, чтобы для него можно было назначить суммарный допуск всей размерной цепи. Это правило основано на том, что в замыкающем звене, поскольку оно явл-ся последним в процессе изготовления , накапливаются погрешности предшествующей обработки всех составляющих звеньев.
2. Для облегчения решения размерной цепи необход. проектировать цепи с наименьшим числом звеньев.Это правило иногда называют правилом короткой размерной цепи и обосновывают тем, что при большом числе размеров(10…15) в замыкающем звене получается такой большой допуск, что ни на одно из звеньев размерной цепи его назначить нельзя.
Недостаточно знать номинальный размер и допуск замыкающего звена, следует найти и его отклонения:
ΔВА= Аб-А; ΔНА=Ам-А; где
ΔВА – верхнее отклонение р-раА;
Аб - наибольший предельный р-р;
ΔНА – нижнее отклонение р-ра А;
Ам- наименьший предельный р-р, следовательно , Аб=А+ΔВА; Ам=А+ΔНА
И для остальных звеньев размерной цепи ( рис.1) можно написать аналогичные уравнения, т.е всего шесть вспомогательных уравнений.
Уравнение максимума замыкающего звена имеет вид:
Вб=Аб-Бм
Заменив каждый член этого уравнения соответственно одним из вспомогательных уравнений, получим: В+ΔВВ = А+ΔВА – Б -ΔНБ ;
Вычтя из него почленно уравнение номинальных размеров В=А-Б, получим …ВВ=..ВА-…НБ
Для любой размерной цепи с каким угодно числом звеньев уравнение верхнего отклонения замыкающего звена имеет вид ΔВВ= ∑ ΔВА – ∑ΔНБ
Т.о, верхнее отклонение замыкающего звена равно разности сумм верхних отклонений всех увеличивающих звеньев и нижних отклонений всех уменьшающих звеньев.
Уравнение минимума замыкающего звена имеет вид Вм= Ам-Бб
Заменив члены этого уравнения вспомогательными уравнениями, получим ΔНВ=∑ΔНА –∑ΔВБ
Дата добавления: 2022-01-22; просмотров: 110; Мы поможем в написании вашей работы! |
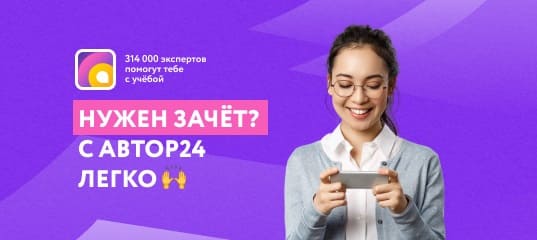
Мы поможем в написании ваших работ!