Припуски могут быть симметричными и асимметричными.
Асимметричные припуски назначаются в том случае, если условия изготовления заготовок не обеспечивают одинакового качества материала и чистоты пов-ти в разных частях заготовки.
Например, пов-ти отливки, котор. находятся в верхней половине литейной формы, требуют больших припусков, т.к. на них скапливается больше засоров и шлаковых включений.
При выборе величины припуска необход. учитывать точность изготовления заготовки – допуски на размеры заготовки.
При выборе величины припусков на обработку следует исходить из тго, что припуски должны быть:
1) достаточными для получения заданной формы и раз-ров детали;
2) минимальными для сокращения расхода металла и уменьшения затрат на обработку.
При этом необходимо учитывать:
1) материал, из котор. изготавливают детали;
2) раз-ры и форму деталей;
3) способ получения загот-к и точность их изготовления;
4) точность и чистоту пов-тей обрабатываемых деталей;
5) деформацию деталей при т/о и возможную точность правки;
6) величину дефектного слоя пов-ти заготовок;
7) возможность погрешности при установке детали для обработки.
Расчёт межоперационных припусков и допусков.
Обработка многих пов-тей произв-ся за несколько операций. Некотор. пов-ти заготовок могут обрабатываться за несколько переходов. Для осуществления каждого перехода необход. снять слой матер-ла – припуск.
Минимальный межоперационный припуск должен обеспечить снятие микронеровностей пов-ти и дефектного слоя ( литейная корка у отливок, обезуглероженный слой у поковок, деформир-й слой), компенсировать отклонения формы и погрешностей.
|
|
По формулам проф. В.М.Кована минимальный межоперационный припуск Zi min определяется:
Минимальный асимметричный межоперационный припуск при последовательной обработкеп противолежащих плоских поверхностей:
Zi min =(hi -1 + Ti-1)+ (pi-1 + ∑yi) , где
hi -1 – высота микронеровностей , полученная на смежном предшествующем переходе;
Ti-1 –глубина дефектного поверхностного слоя , полученного на смежном предшествующем переходе;
pi-1 –геометрическая сумма отклонений ф-мы взаимосвязанных пов-тей обрабатываемой заготовки, возникающих на смежном переходе;
∑yi – погрешность установки на выполняемом переходе;
Минимальный симметричный межоперационный припуск при параллельной обработке противолежащих плоскостей пов-тей:
2Zi min= 2x ( (hi -1 + Ti-1) + (pi-1 + ∑ yi) )
Минимальный симметричный межоперационный припуск при обработке наружных и внутренних пов-тей тел вращения:
Zi min =(hi -1 + Ti-1)+V pi-1 + ∑yi *
Приведённые выше формулы расчёта минимального припуска Zi min относятся к обработке деталей на настроенном оборудовании методом автоматического получения заданного раз-ра.
|
|
При получении заданного раз-ра методом пробных проходов для расчёта припуска Zi min в указанную формулу вместо погрешностей установки на выполняемом переходе ∑yi вводится погрешность выверки ∑вi .
Зная минимальные припуски, можно определить промежуточные раз-ры от готовой детали до черновой заготовки.
Рис1.
Определим раз-ры при обработке плоскостей у партии заготовок. Для простоты расчёта будем иметь один переход. На рис. изображены две заготовки из партии – с наибольшим и наименьшим предельными раз-ми.
Инструмент устанавливают на определённый раз-р Сн. При обраб-ке вследствие разной глубины резания и колебания отжатий технологической системы от уmin до ymax обработанные детали в партии имеют разные раз-ры:
aimax-aimin=бi , где
aimax и aimin - максимальные и минимальные раз-ры заготовки после обработки;
бi – допуск на выполнение перехода.
Зная раз-р aimin в предыдущей ф-ле и величину минимального припуска, можно определить минимальный р-р по ф-ле:
а i-1 min= aimin+ Zi min
Максимальный раз-р заготовки определяется из формулы:
а i-1 max= а i-1 min + б i-1 или
а i-1 max= aimax+ Zi mах , где
Zi mах- максимальный припуск.
|
|
При этом Zi mах= Zi min+ б i-1- бi,
Zi mах- Zi min=б z, где б z-допуск на припуск.
Все данные для расчёта припусков и промежуточных раз-ров берутся из нормативов. Для облегчения определения припусков пользуются опытно-статистическим методом, т.е припуск выбирают с помощью таблицы припусков, составленной на основании производственного опыта.
Величины припусков , полученные этим методом, явл-ся завышенными, т.к. они устанавливаются суммарно на весь технологический процесс и не учитывают особенности выполнения отдельных операций.
Для возможного уменьшения припусков на обработку применяют правку заготовок перед обработкой и в процессе обработки; изготавливают заготовки способом, обеспечивающим чистоту пов-ти и отсутствие поверхностных дефектов, используют приспособления и способы крепления, при котор. достигаются точность и постоянство положения деталей при обработке; производят обдирочное шлифование вместо токарной и фрезерной обработки.
Обеспечение точности параметров деталей , подвергаемых механической обработке, осуществляется снятием с поверхности слоя материала , называемого припуском.
Последовательной обработкой заготовки получают готовую деталь с заданными параметрами, обеспечивающими её качество:
|
|
- точность размеров, формы и расположения поверхностей;
-шероховатость и микротвёрдость поверхностей;
-глубину наклёпанного слоя и знак поверхностных напряжений и т.д.
Припуск есть слой материала, снимаемый с поверхности детали для обеспечения заданного качества. Величина снимаемого припуска должна быть оптимальной, обеспечивающей заданное качество при минимальном расходе материала и времени на обработку. Увеличенные припуски приводят к удалению наиболее износоустойчивых поверхностных слоёв детали. Кроме того, увеличение припусков снижает экономические показатели технологического процесса, т.к ведёт к увеличению времени обработки. Малые припуски на обработку не обеспечивают возможности удаления дефектных поверхностных слоёв металла, повышают требования к точности заготовок.
Различают припуски общие, операционные, промежуточные и припуски, снимаемые за один рабочий ход.
Операционный припуск Z, - это припуск , удаляемый при выполнении одной технологической операции.
Промежуточный припуск – удаляемый при выполнении одного технологического перехода. Определяется разностью размеров, полученных на предшествующем и выполняемом переходе.
Деление припусков на операционные и промежуточные явл-ся условным, поскольку каждый технологический переход обработки поверхности при определённых условиях может быть выделен в отдельную операцию и наоборот.
Общим припуском называется слой материала, необходимый для выполнения всей совокупности операций и переходов от заготовки до готовой детали. Он равен сумме операционных припусков:
n
Z=∑ Zi
i=1
n – число операций ( переходов).
Припуски на обработку могут быть симметричными и асимметричными.
Симметричные припуски имеют место при обработке наружных и внутренних цилиндрических и конических поверхностей вращения, а также одновременной обработке противолежащих поверхностей с одинаковыми припусками.
Асимметричный припуск будет в том случае, когда противолежащие поверхности обрабатываются независимо одна от другой.
Во всех случаях установленный минимальный припуск не должен быть меньше минимальной толщины стружки, которую может снять режущий инструмент, например, после непродолжительной работы заточенного резца минимальная толщина снимаемой стружки составляет 0,02-0,05 мм; при других видах обработки она может быть больше( фрезерование) или меньше ( абразивная обработка).
На припуск устанавливают допуск, который явл-ся разностью между наибольшим и наименьшим значениями припуска.
Значения припусков и допусков определяют промежуточные ( операционные) размеры.
Наряду с припуском в машиностроении существует понятие напуска, под которым понимают также слой материала, подлежащего удалению. Напуски увеличивают величину припусков, из-за чего возрастает трудоёмкость обработки. К напускам относятся: штамповочные и формовочные уклоны, непролитые и непрошитые отверстия, слои металла у сортового проката, различные впадины, заполняемые металлом при ковке и штамповке и т.д.
Методы определения припусков на обработку.
Существует два метода определения припусков: опытно- статистический и расчётно-аналитический.
Следствием первого метода явл-ся разработка таблиц для определёния общих и операционных припусков. Таблицы составлены на основе обобщения систематизации производственных данных передовых заводов и некоторые из них стандартизованы. Например, на отливки –ГОСТ 26645-85, штампованные поковки – ГОСТ 7505-89 и др. Табличные значения припусков во избежание брака , завышены и не учитывают конкретных условий обработки ( последовательности выполнения операций, схем базирования и др). В связи с этим был разработан профессором В.М. Кованом – расчётно- аналитический метод. Он основан на учёте конкретных условий выполнения технологического процесса обработки путём анализа и выявления фактров, влияющих на величину припуска. К таким факторам относятся:
-величина микронеровностей поверхности Rz;
-глубина дефектного слоя поверхности h;
-пространственные отклонения поверхностей Δ. К пространственным отклонениям относятся коробление и кривизна поверхности, эксцентричность оси отверстия, несовпадение положения осей и др;
-погрешности установки заготовки ε.
Припуск на обработку должен быть таким, чтобы при его снятии устранялись дефекты обработки, и дефекты поверхностного слоя, полученные при предшествующей обработке, а также погрешности установки обрабатываемой заготовки при выполняемой обработке. Из факторов, влияющих на величину припусков Rz, h, Δ относятся к предшествующей обработке , и им присваивается индекс i-1,ε относится к выполняемой обработке и имеет индекс i.
С учётом изложенного минимальный промежуточный припуск на выполняемыйпереход в общем виде можно определить по формуле:
_ _
Z imin =( Rz i -1 + h i -1 )+│Δ i -1 +ε i │
Пространственные отклонения и погрешности установки представляют собой векторы, т.к они имеют не только величину, но и направление. Их суммируют по правилам сложения векторов. При обработке плоских поверхностей имеем коллинеарные векторы: - -
│Δ i-1 +ε i │=Δ i-1 +ε i ,
При обработке поверхности вращения , когда невозможно предвидеть направление векторов суммирование производится по правилу квадратного корня:
- - 2 2
│Δ i-1 +ε i │=√ Δ i-1 + ε i
Минимальный припуск на обработку плоскостей определяется по формуле:
Z imin =(Rz i-1 +h i-1 )+( Δ i-1 + ε i )
Для поверхностей вращения припуск обычно считается сразу на диаметр:
2 2
2Z imin =2((Rz i-1 +h i-1 )+√ Δ i-1 + ε i )
Из общих формул расчёта припусков могут быть получены частные формулы для конкретных случаев обработки, например:
- при обработке цилиндрических поверхностей заготовки, установленной в центрах, погрешность установки отсутствует:
2Z imin =2( Rz i -1 + h i -1 + Δ i -1 );
- при обработке отверстий плавающей развёрткой и при протягивании не устраняетсясмещение увод оси; в этом случае также отсутствует погрешность установки:
2Z imin =2( Rz i -1 + h i -1 )
-при обработке , целью которой явл-ся лишь уменьшение шероховатости поверхности( полирование, суперфиниширование), минимальный припуск определяют по формуле:
2Z imin =2 Rz i ;
- при шлифовании заготовок после их т/о поверхностный слой должен быть сохранён; следовательно, в расчётных формулах будет отсутствовать слагаемое h i -1.
Составляющие расчётной формулы минимального припуска приведены в технических справочниках в зависимости от конфигурации и размеров заготовки, материала, метода получения, способа установки на станке.
Действительные припуски на обработку в партии заготовок будут колебаться вследствие колебаний размеров заготовок, а также твёрдости их материалов.
Можно записать зависимость для минимального и максимального припусков наружных поверхностей:
Z imin = а min -b min;
Z imax = а max –b max.
Учитывая, что
а max = а min + Т а,
b max = b min + Т b ,
получим Z imax = а min + Т а - b min – Т b = Z imin + Т а – Т b ,
где Та – допуск на размер заготовки;
Тb – допуск на выполняемый размер.
После вычислений минимального и максимального общего припуска рассчитывается припуск номинальный. Для наружного размера:
n
Z ном =∑ Z imin + е i заг – е i дет ,
i -1
где е i заг – нижнее отклонение размера заготовки;
е i дет –нижнее отклонение размера детали.
Величина номинального припуска необходима при конструировании штампов, пресс-форм, моделей, стержневых ящиков, приспособлений и т.д.
Расчёт минимальных и максимальных промежуточных припусков на обработку производят для определения расчётных размеров обрабатываемой поверхности по всем технологическим переходам от готовой детали до исходной заготовки.
Величина операционного допуска принимается в соответствии с экономической точностью метода обработки, используемого на данном этапе обработки.
Допуски на размеры , выполняемые на операциях окончательной обработки, выбирают в соответствии с экономической точностью метода обработки и в том случае, если по чертежу требуется меньшая точность выдерживаемого размера. Такая необходимость возникает в тех случаях, когда целью окончательной обработки явл-ся достижение малой шероховатости поверхности, а не высокой точности размера. Достоинством этого принципа явл-ся обеспечение окончательной обработки при малых колебаниях припуска в следствие уменьшения допуска на выполняемый размер. Вследствие увеличения колебания припуска снижается производительность окончательной обработки.
Если размер , координирующий положение обрабатываемой на данной операции поверхности, отсчитывается от другой, необработанной поверхности заготовки, то допуск на этот размер принимается ниже экономической точности обработки:
Т =Тзаг +Тобр ,
2
где Тзаг – допуск размера заготовки;
Тобр – допуск, соответствующий экономической точности метода обработки.
Тема 1.7. Базы и базирование.
Перед обработкой заготовка должна быть установлена на станке в строго определённое положение. Отклонение фактически достигнутого положения заготовки или изделия при установке от требуемого называется погрешностью установки. Она состоит из погрешности базирования, погрешности положения заготовки и погрешности её закрепления.
Для правильной надёжной установки и закрепления заготовки необходимо и достаточно устранить шесть степеней свободы её возможного перемещения, т.е наложить шесть двусторонних геометрических связей.
Базирование – это придание заготовке или изделию требуемого положения относительно выбранной системы координат, т.е ориентирование заготовки.
База – это поверхность или выполняющее ту же ф-цию сочетание поверхностей, ось, точка, принадлежащая заготовке или изделию и используемая при базировании.
Базы подразделяются :
1. По назначению.
Конструкторская база – база, используемая для определения положения детали или сборочной единицы в изделии.
Основная база – конструкторская база, принадлежащая данной детали или сборочной единице и используемая для определения её положения в изделии.
Вспомогательная база – конструкторская база, принадлежащая данной детали или сборочной единице и используемая для определения положения присоединяемого к ним изделия.
Технологическая база – база , используемая для определения положения заготовки или изделия в процессе изготовления и или ремонта. На эту базу заготовка устанавливается при обработке.
Измерительная база – база, используемая для определения относительного положения заготовки или изделия и средств измерения. От неё производится измерение детали.
2. По лишаемым степеням свободы.
Установочная база –база , лишающая заготовку или изделие трёх степеней свободы- перемещения вдоль одной координатной оси и поворотов вокруг двух других осей.
Направляющая база- база, лишающая заготовку или изделие двух степеней свободы – перемещения вдоль одной координатной оси и поворота вокруг другой оси.
Опорная база- база, лишающая заготовку или изделие одной степени свободы – перемещения вдоль одной координатной оси и поворота вокруг оси.
Двойная направляющая база-база, лишающая заготовку или изделие четырёх степеней свободы- перемещения вдоль двух координатных осей и поворотов вокруг них.
Двойная опорная база- база, лишающая заготовку или изделие двух степеней свободы- перемещений вдоль двух координатных осей.
3. По характеру проявления.
Скрытая база – база заготовки или изделия в виде воображаемой плоскости, оси или точки.
Явная база – база заготовки или изделия в виде реальной поверхности, разметочной риски или точки пересечения рисок.
Схема базирования – схема расположения опорных точек на базах заготовки или изделия.
Все опорные точки на схеме базирования изображаются условными знаками и нумеруются порядковыми номерами, начиная с базы, на которой располагается наибольшее кол-во опорных точек.
Положение любой поверхности заготовки может быть определено только относительно других поверхностей, условно принимаемых за координатные. Абсолютно твёрдое свободное тело имеет относительно координатных осей шесть степеней свободы. Эти шесть степеней свободы сводятся к трём возможным перемещениям вдоль трёх осей координат и трём возможным вращениям относительно тех же осей, т.е положение тела определяется шестью координатами относительно трёх координатных плоскостей. Любая координата лишает твёрдое тело одной степени свободы.
Точность соблюдения раз-ров деталей при обработке в значительной степени зависит от их установки относительно рабочих органов станка и режущего инструмента. Положение детали при обработке определяется её поверхностями, которыми деталь устанавливается на стол станка или в приспособление.
Базами называются поверхности деталей, определяющие её положение при установке.
Конструкторские базы – это линии или точки на чертеже, от которых конструктор задаёт раз-ры и взаимное положение других линий, соответствующих поверхностям детали или их осям.
Производственные (технологические) базы подразделяют на установочныеи измерительные.
База, используемая для определения положения заготовки или изделия в процессе изготовления или ремонта называется технологической базой.
Установочные базы бывают опорные и проверочные.
Опорная установочная база – это поверхность, при контакте которой с установочными элементами приспособления деталь ориентируется в нужном направлении с требуемой точностью.
Различают опорные установочные базы на основные и вспомогательные.
Основная опорная установочная база –это сочетание поверхностей, при соприкосновении которых с др.деталями в собранном узле или механизме определяется взаимное положение деталей.
Вспомогательными опорными установочными базами называются пов-ти , используемые для установки деталей при обработке, но не определяющие положение обработанной детали относительно др.деталей при их соединении в узел . Вспомогательными опорными установочными базами называют также пов-ти, специально обрабатываемые для установки детали в процессе изготовления ( центровые углубления в валах)
Проверочная установочная база – это сочетание поверхностей или разметочных рисок, по котор. выверяется положение обрабатываемой детали на станке при установке без приспособления.
Измерительной базой называют пов-ть , от котор. производят отсчёт раз-ров при измерении детали или по отношению к котор. проверяют правильность положения других пов-тей.
Сборочной базой называют пов-ть, по котор. деталь ориентируется по отношению к другим деталям в собранной машине. Если эти поверхности используют как установочные опорные базы в процессе обработки деталей, то они явл-ся в то же время установочными базами.
Для того ,чтобы ориентировать деталь при обработке в определённом положении, необходимо лишить её всех шести степеней свободы, т.е исключить возможность перемещения в трёх взаимно перпендикулярных направлениях и вращательного движения вокруг трёх взаимно перпендикулярных осей.
Точка, символизирующая одну из связей заготовки или изделия с избранной системой координат, называется опорной точкой. Все опорные точки на схеме базирования изображают условными знаками и нумеруют порядковыми номерами, начиная с базы, на которой располагается наибольшее число опорных точек
При наложении в какой либо проекции одной опорной точки на другую изображается одна точка, около которой проставляются номера совмещённых точек.
Рис.
Установка детали при обработке определяется правилом шести точек, каждая из которых лишает деталь одной из шести точек свободы.
На рис. показана установка призматической детали.
Три опоры детали в плоскости хоу лишает её трёх степеней свободы – перемещения вдоль оси z и вращения вокруг осей х и у . Плоскость хоу называется установочной
Две опоры детали в плоскости xoz лишают – перемещение вдоль оси х и вращения вокруг оси z . Плоскость xoz называется направляющей. Опора детали в плоскости у oz , котор. называется
упорной, лишает деталь шестой степени свободы – перемещения вдоль оси у.
При установке цилиндрической детали на призме, поверхности призмы лишает деталь четырёх степеней свободы – перемещения в направлении осей х и z и вращения вокруг этих же осей. Возможность перемещения вдоль оси у и вращения вокруг этой оси исключается наличием
упора в торец и шпоночный паз или заменяющий эти упоры силой трения, возникающей при зажиме.
Существует два способа установки деталей при обработке :
1.Установка с выверкой непосредственно на станке. Такая установка применяется при обработке деталей в единичном и мелкосерийном произ-ве и выполняется рабочим по чертежу детали. При этом не обеспечивается высокая точность и равномерное распределение припусков.
Установка с выверкой может осуществляться по необработанным и обрабртанным поверх-м , а также по разметочным рискам.
Выверка по обработанным пов-тям обеспечивает наиболее высокую точность установки заготовок при обработке ( от +- 0,1 до +- 0,3 мм, в завис-ти от раз-ров заготовки). При выверке по необработанным пов-тям точность установки ниже ( от +-1,5 до +-3,0 мм). Для повышения точности выверки необраб-х заготовок использ-ся разметочные риски, котор. наносятся на деталь для облегчения выверки, проверки пригодности загот-к к обработке, указания границ обработки( припусков), контроле сложных деталей, установки накладных кондукторов и расточных приспособлений.
2.Установка без выверки в приспособлении, в котор. положение детали определ-ся установочными элементами приспособления. Такая установка деталей примен-ся в крупносерийном и массовом произ-ве.При этом обеспечивается высокая точность и сокращается время, затрачиваемое на установку детали.
Погрешности установки деталей.
Погрешность установки- отклонение фактического положения заготовки или изделия от требуемого.
Погрешности установки детали при обработке суммируются из погрешностей базирования, погрешностей закрепления, погрешностей положения детали вследствие неточного изготовления приспособления, износа его установочных элементов, а также ошибок установки приспособления на станок.
Погрешностью базирования ∑б называется разность предельных расстояний итзмерительной базы относительно установленного на размер инструмента. Если при обработке детали технологическая установочная база не совпадает с измерительной, возникает погрешность базирования.
Для того, чтобы исключить погрешность базирования, необходимо совмещать установочную и измерительные базы или пересчитывать допуски, предусмотренные чертежом и назначать более жёсткие допуски.
Погрешностью закрепления ∑з называется разность между наибольшими и наименьшими расстояниеми измерительной базы относительно установочного на раз-р инстр-та, вызванная смещением обрабатываемой заготовки под действием усилия зажима. Эта разность может иметь очень малую величину, если величина смещения велика, но постоянна.
Погрешность положения заготовки ∑пр вызывается неточностью изготовления приспособления, износа его установочных элементов, а также неточностью установки приспособления на станок. Эти неточности учитываются при проектировании приспособлений, периодически контролируются и устраняются при ремонте оснастки.
Погрешности ∑б,∑з,∑пр представляют собой поля рассеяния случайных величин, распределение котор.можно (приближённо) считать подчиняющимися нормальному закону распределения.При этом в общем виде погрешность установки Е как суммарное поле рассеяния
2 2 2
выполняемого раз-ра определяется из ф-лы : ∑у=√∑б +∑з+∑пр
Основные правила выбора баз:
1. Совмещать установочную и измерительную базы, чтобы исключить погрешности базирования.
2. Во всех случаях, когда это возможно, надо использовать в кач-ве технологических измерительных баз пов-ти, являющиеся конструктивными базами.
3. Необходимо соблюдать принцип постоянства баз, т.е использовать одни и те же базы при большом числе операций, или обрабатывать возможно большее кол-во пов-тей с одной установки для сохранения точности взаимного расположения пов-тей деталей, котор. обраб-ся в разных операциях.
4.В качестве базовых следует применять пов-ти наибольшей протяжённости для повышения точности установки детали.
5. Для деталей, у котор. некоторые поверх-ти не обрабатываются, в качестве черновых баз ( баз на первой операции) нужно принимать необработанные пов-ти. На черновую базу разрешается устанавливать деталь только один раз.
6. Для деталей, обрабатываемых полностью, в качестве черновой базы принимаются пов-ти с наименьшим припуском на обработку.
7.В случае необходимости следует искусственно увеличить раз-ры технологических баз или делать специальные технологические базы.
8. Технологические установочные базы надо выбирать так, чтобы обеспечить жёсткость установки и отсутствие деформаций деталей от усилий зажима и сил, возникающих в процессе обработки.
Погрешности базирования в приспособлениях.
Погрешность установки ∑у – одна из составляющих суммарной погрешности выполняемого раз-ра детали. Она возникает при установке обрабатываемой заготовки в приспособлении и складывается из погрешности базирования ∑б, погрешности закрепления ∑з и погрешности положения заготовки ∑пр, зависящей от неточности приспособления и определяемой ошибками изготовления и сборки его установочных элементов и их износа при работе.
Погрешность настройки станка Δн возникает при установке режущего инструмента на раз-р, а так же вследствие неточности копиров и упоров для автоматического получения заданных раз-ров на детали.
Погрешность обработки Δобр, возникающая в процессе изготовления детали на станке, объясняется:
1) геометрической неточностью станка;
2)деформацией технологической системы под действием сил резания;
3) неточностью изготовления и износом режущего инструмента и приспособления;
4) температурными деформациями технологической системы.
Для получения годных деталей суммарная погрешность при обработке на станке должна быть меньше допуска б на заданный раз-р детали. Это условие выражается неравенством ∑у+Δн+Δобр = б
Погрешностью базирования ∑б называют разность предельных расстояний измерительной базы относительно установленного на заданный раз-р детали режущего инструмента. Погрешность базирования возникает, когда технологическая установочная база обрабатываемой заготовки не совмещена с измерительной.
При разработке ТП для каждой операции выбирают исходные базы и проставляют исходные раз-ры, а так же базы для ориентирования заготовки. При неправильном выборе баз заметно увеличивается вспомогательное время на установку и снятие заготовки, усложняется конструкция приспособления.
Разработка схемы базирования при фрезеровании паза.
При фрезеровании паза шириной h выдержать размеры а и в и обеспечить параллельность оси паза, относительно поверхности Б, а дно паза – относительно основания А.
Рис. Схема базирования.
За основную базу предпочтительно брать пов-ть, которая обеспечивает заготовке устойчивое положение в приспособлении даже при базировании только одной этой базы. Наиболее полно такому требованию отвечает плоская пов-ть заготовки, располагающаяся снизу и обладающая достаточной протяжённостью. Если у заготовки такой пов-ти нет, выбирают другую пов-ть достаточной протяжённости – боковую плоскую пов-ть, цилиндрическое отверстие либо цилиндрическую наружную пов-ть.
На выбор основной базы влияет так же точность исходных раз-ров и допускаемых отклонений расположения обрабатываемой пов-ти.За основную следует принимать базу, от которой заданы наиболее точные исходные раз-ры. На первой операции , когда у заготовки ещё нет ни одной обработанной пов-ти, за основную базу приходится принимать необработанную пов-ть, на следующих – обработанную с наименьшей шероховатостью.
Дата добавления: 2022-01-22; просмотров: 103; Мы поможем в написании вашей работы! |
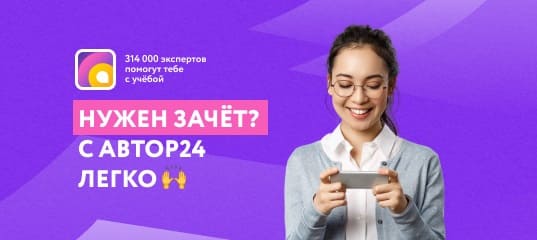
Мы поможем в написании ваших работ!