Задачи для самостоятельной работы
1. Определить необходимую длину сборочного конвейера, а также скорость его движения при следующих условиях: сменная программа линии сборки 150 механизмов, шаг конвейера 2 м, на сборке занято 12 рабочих; регламентированные перерывы для отдыха в смене – 30 мин.
2. Процесс сборки изделий в цехе организован в форме «стационарного» потока при неподвижном изделии и переходах рабочих по объектам. Определить число сборочных стендов и периодичность передвижения бригад сборщиков от одного стенда к другому. Годовая программа выпуска 1200 изделий; трудоемкость работы на каждом стенде в среднем – 120 нормо-часов; состав каждой бригад – 4 человека, коэффициент выполнения норм 1,11; цех работает 22 рабочих дня в месяц в две смены по 8 ч, перерывы – 18 мин в смену.
3. Процесс сборки изделия М состоит из шести операций продолжительностью:
Операции | 1 | 2 | 3 | 4 | 5 | 6 |
Норма времени, мин | 6 | 5 | 5,2 | 6,3 | 7,2 | 5,9 |
Определить коэффициенты загрузки сборщиков по операциям, если на каждой занято по одному человеку. Как изменится суточный выпуск линии, если на операции № 5 осуществить мероприятия, которые повышают производительность труда, в результате которых норма времени уменьшится до 6 мин.
4. Коробки передач (габарит 365×265 мм) собирают на рабочем конвейере. Суточная программа запуска линии – 365 шт.; режим работы – две смены по 8 ч. На операции № 2 фактические затраты времени колеблются в пределах 0,7–1,3 от штучной нормы времени. Регламентированные перерывы составляют 30 мин в смену.
|
|
Необходимо:
1) определить такт линии;
2) рассчитать потребное число рабочих мест на линии;
3) наметить тип и определить основные параметры конвейера (шаг, рабочие зоны операций, общую длину, скорость);
4) подсчитать продолжительность цикла сборки;
5) составить схему планировки поточной линии. Технологический процесс сборки коробок передач следующий:
№ операции | Операция | Норма времени, мин | |||
1 | Завести шестерню с запрессованной в ней деталью в коробку передач | 2,5 | |||
2 | Поставить валик в отверстие коробки, надеть на валик шестерню и кольцо, продвинуть валик на место | 7,4 | |||
3 | Надеть на валик шестерню с запрессованной втулкой, напрессовать втулку | 2,3 | |||
4 | Вставить валик в коробку передач | 2,6 | |||
5 | Просверлить и нарезать два отверстия под винты в валиках и в корпусе коробки (снять с конвейера) | 5,0 | |||
6
| Нарезать два отверстия в валике и в корпусе коробки | 7,45 | |||
7 | Поставить винты | 5,1 | |||
8 | В отверстие коробки передач запрессовать наружное кольцо роликоподшипника | 5,0 | |||
9 | Контроль | 1,3 |
5. Рассчитать потребное число станков по операциям и их загрузку на линии обработки шатуна и крышки автомобильного двигателя. Годовое задание составляет 900 тыс. шт.; потери времени в работе оборудования – 7 %; линия работает в две смены по 8 ч. Технологический процесс обработки следующий:
№ | Операция | Норма времени, мин |
| |||
операции |
| |||||
| ||||||
1 | Фрезерование обеих сторон крышки и установка бобышек | 0,6 |
| |||
| ||||||
| ||||||
2 | Сверление отверстий под поршневой палец | 0,4 |
| |||
3 | Протяжка отверстия под поршневой палец | 0,3 |
| |||
4 | Фрезерование места стыка шатуна и крышки | 0,5 |
| |||
5 | Сверление отверстий для болтов | 0,5 | ||||
6 | Фрезерование бобышек для болтов | 0,4 | ||||
7 | Цековка и ценковка бобышек | 0,6 | ||||
8 | Сверление отверстия для зажимного болта | 0,5
| ||||
9 | Нарезание резьбы | 0,3 | ||||
10 | Расточка большой головки | 0,3 | ||||
11 | Контроль | 0,4 | ||||
6. Радиоприемники собирают на конвейере. Сменная программа линии – 34 радиоприемника; трудоемкость сборки приемника 5 ч 25 мин; шаг конвейера – 1,6 м; регламентированные остановки линии для отдыха рабочих – 7 %; рабочие места располагаются с одной стороны конвейера. Определить:
1) такт линии;
2) число рабочих мест;
3) скорость движения ленты конвейера;
4) общую длину конвейера.
7. В цехе осуществляется стационарная сборка станков. Процесс сборки синхронизирован; операции сборки осуществляются бригадами, состоящими из 5 человек каждая; трудоемкость всех сборочных операций – 220 человеко-ч.; месячная программа – 228 станков (за 23 дн.); цех работает в две смены; регламентированные перерывы и потери времени на линии составляют за месяц в среднем 10 % финального фонда времени работы линии. Определить число необходимых сборочных стендов, а также периодичность (ритм) передвижения бригад сборщиков.
8. Воздушный насос (габарит 320× 220 мм) собирают на линии с рабочим конвейером. Необходимо:
1) определить такт линии;
2) рассчитать потребное число рабочих мест на линии;
|
|
3) тип и основные параметры конвейера (шаг, рабочие зоны, длину, скорость);
4) определить длительность цикла сборки изделия;
5) составить схему планировки поточной линии.
Сменная программа для линии – 470 шт.; работа производится в одну смену. На операции № 7 фактические затраты времени колеблются в пределах 0,7–1,3 от штучной нормы; регламентированные перерывы в работе линии – 30 мин в смену. Технологический процесс общей сборки следующий:
Номер операции | Операция | Норма времени, мин | |
1 | Установить картер насоса в приспособление; вынуть опору из картера | 1,9 | |
2 | Установить в гнездо кривошип и вбить шпонку | 0,9 | |
3 | Снять картер с приспособления, ввернуть от руки перепускной клапан и ввернуть в картер пробку | 0,95 | |
4 | Поставить картер в приспособление и ввернуть пробки около отверстия под крышку | 1,0 | |
5 | Вставить в картер кривошип со шпонкой, надеть шестерню на кривошип, надеть на кривошип замочную шайбу, навернуть гайку | 3,8 | |
6 | Поставить опору кривошипа, ввернуть и затянуть три винта крепления опоры | 2,8 | |
7 | Контроль | 0,4 |
9. Определить такт непрерывно-поточной линии обработки маховика трактора, потребное число рабочих мест и степень их загрузки. Сменная программа выпуска линии – 143 шт.; технологические потери составляют в среднем 2 %; регламентированные перерывы в работе линии 6 % от продолжительности смены. Технологический процесс следующий:
Номер операции | Операция | Норма времени, мин | |
1 | Черновая обточка обода | 5,48 | |
2 | Черновая обточка ступицы | 6,1 | |
3 | Чистовая проточка обода и ступицы | 18,34 | |
4 | Сверление и нарезание резьбы девяти отверстий | 3,2 | |
5 | Зенкерование | 2,9 | |
6 | Протяжка двух шпоночных канавок | 3,0 | |
7 | Шлифование | 5,9 | |
8 | Балансировка | 5,4 | |
9 | Промывка | 3,2 |
10. Поточная линия для обработки выпускного клапана двигателя должна работать с тактом 3,8 мин. Технологический процесс обработки следующий:
Номер операции | Операция | Норма времени, мин | ||
1 | Подрезка торца и обточка диаметра головки | 1,6 | ||
2 | Центровка штока и проточка радиуса | 7,3 | ||
3 | Обдирка фасок грибка, отрезка и подрезка конца шток | 3,6 | ||
4 | Предварительное шлифование штока | 1,0 | ||
5 | Сверление отверстия в штоке | 6,2 | ||
6 | Обточка головки, окончательная проточка, | 6,1 | ||
развертка и расточка отверстия пол пробку | ||||
7 | Запрессовка пробки и расточка гнезда под наплавку твердого сплава | 1,7 | ||
8 | Наплавка стеллита | 3,0 | ||
9 | Шлифование торца, снятие фаски на торце штока, проточка фаски, предварительная и окончательная проточка радиуса шейки | 5,92 | ||
10 | Шлифование штока и фаски | 5,6 |
Определить число необходимых рабочих мест по операциям и их загрузку, а также программу, при которой будет достигнута наибольшая загрузка рабочих мест на линии.
11. На участке, работающем в одну смену, обрабатывается станина токарного станка. Технологический процесс следующий:
Номер операции | Операция | Трудоемкость, ч |
1 | Строгание | 3,5 |
2 | Расточка | 2 |
3 | Сверление отверстий | 2,5 |
Определить:
1) при какой программе в смену и с каким числом рабочих мест на операциях линия может работать как непрерывно поточная;
2) с какими межоперационными заделами работает линия, если на каждой операции имеются по два станка, а период комплектования задела равен смене, и какова при этом программа выпуска;
3) как изменятся выпуск станин и величина задела, если на операции №1 будут работать четыре станка.
12. На линии с распределительным конвейером обрабатывается картер воздушного насоса (габарит 320×140 мм, масса за готовки – 9 кг).
Необходимо:
1) определить такт линии;
2) рассчитать потребное число рабочих мест по операциям и их загрузку;
3) составить схему планировки поточной линии;
4) составить таблицу распределения разметочных знаков конвейера;
5) наметить тип и основные параметры конвейера (шаг, комплект разметочных знаков, длину и скорость).
Суточная программа для линии – 734 шт., линия работает в две смены по 8 ч. Технологический процесс следующий:
№ п/п | Операция | Оборудование | Норма времени, мин | |
1 | Фрезеровать плоскость фланца | Вертикально-фрезерный, тип 612 | 5,2 | |
2 | Сверлить семь отверстий во фланце | Вертикально-сверлильный одношпиндельный, тип 2135А | 1,35 | |
3 | Зенкеровать отверстия со стороны привода | Вертикально-сверлильный | 4,0 | |
одношпиндельный, тип 2135А | ||||
4 | Развернуть два отверстия | Вертикально-сверлильный одношпиндельный, тип 2135А | 3,7 | |
5 | Фрезеровать горец | Горизонтально-фрезерный, тип 665 | 2,7 | |
6 | Цековать торцы | Сверлильный одношпиндельный, тип 213С | 1,3 | |
7 | Сверлить два отверстия | Сверлильный одношпиндельный, тип 221С | 1,25 | |
8 | Контроль | – | 0,7 |
13. На линии с распределительным конвейером обрабатывается корпус коробки передач (габариты 365× 295 мм; масса заготовки 35 кг). Необходимо:
1) определить такт линии;
2) рассчитать потребное число рабочих мест и их загрузку;
3) составить схему планировки ниточной линии;
4) наметить тип и рассчитать основные параметры конвейера (шаг, комплект разметочных знаков, общую длину, скорость);
5) составить таблицу распределения разметочных знаков конвейера. Суточная программа для линии – 263 шт.; линия работает в две смены по 8 ч. Технологический процесс следующий:
№ | Операция | Норма времени, мин | |
1 | Фрезеровать плоскость прилегания к коробке скоростей | 11,5 | |
2 | Фрезеровать плоскость прилегания к крышке коробки скоростей | 11,5 | |
3 | Шлифовать обе плоскости | 3,6 | |
4 | Рассверлить семь отверстий | 3,7 | |
5 | Нарезать резьбу | 7,5 | |
6 | Сверлить четыре отверстия | 3,7 | |
7 | Нарезать резьбу | 3,8 | |
8 | Контроль | 1,8 |
14. На линии с распределительным конвейером обрабатывается ведущая шестерня (длина 297 мм, диаметр 118 мм; масса заготовки – 4 кг). Необходимо:
1) определить такт линии и потребное число рабочих мест и их загрузку;
2) наметить тип и основные параметры конвейера (шаг, период, общую длину, скорость);
3) составить таблицу распределения номеров конвейера;
4) составить схему планировки поточной линии;
5) рассчитать цикл обработки деталей.
Сменная расчетная программа для линии – 298 шт. Технологический процесс следующий:
Номер операции | Операция | Норма времени, мин | |
1 | Фрезерование торца | 1,6 | |
2 | Предварительная обточка | 4,7 | |
3 | Обточка конуса | 1,5 | |
4 | Окончательная обточка | 4,7 | |
5 | Нарезание десяти шлицев | 4,65 | |
6 | Предварительное шлифование шейки | 1,5 | |
7 | Фрезерование резьбы | 3,1 |
15. Рассчитать основные параметры поточной линии механической обработки цилиндров тракторного двигателя: программу; такт, число рабочих мест на операциях и их загрузку. Годовое задание по выпуску тракторов 50 тыс. шт. Число цилиндров для одного двигателя 4 шт. Число запасных частей составляет 20 % от общего числа цилиндров, идущих на сборку. Нормальный остаток собранных двигателей на складе перед главным конвейером – 2 тыс. шт.; фактический остаток к началу планируемого года – 3 500 шт.; нормальный запас готовых цилиндров на сборке 15 тыс. шт.; фактический остаток готовых цилиндров 5 тыс. шт. Режим работы – две смены по 8 ч; потери времени в использовании станков 5 %. Технологический процесс следующий:
Номер операции | Операция | Оборудование | Норма времени, мин | |
1 | Черновая расточка | Специальный станок | 3,2 | |
2 | Черновая обточка | Токарный полуавтомат | 2,0 | |
3 | Чистовая расточка | Специальный станок | 2,5 | |
4 | Сверление десяти отверстий | Агрегатный станок | 0,7 | |
5 | Фрезерование двух | Специальный станок | 1,0 | |
плоскостей | ||||
6 | Нарезание десяти отверстий | Агрегатный станок | 0,4 | |
7 | Развертывание отверстия | Специальный станок | 2,2 | |
8 | Чистовая токарная обточка | Токарный | 1,35 | |
полуавтомат | ||||
9 | Контроль | – | 1,9 |
16. Произвести предварительную синхронизацию технологического процесса ручной сборки методом комбинирования операций и определить потребное число рабочих. Такт поточной линии 5 мин. Продолжительность операций следующая:
Номер операции | 1 | 2 | 3 | 4 | 5 | 6 | 7 |
Норма времени, мин | 3,2 | 2,6 | 1,7 | 4,3 | 2,5 | 3,2 | 1,9 |
Последовательность расположения операций № 1–5 может быть выбрана произвольно; операции № 6 и 7 должны выполняться последовательно в конце обработки.
17. Произвести предварительную синхронизацию технологического процесса сборки, определить потребное число рабочих и разработать регламент их работы, если линия должна работать в две смены по 8 ч. Для выполнения суточного задания 240 шт. продолжительность операций следующая:
Номер операции | 1 | 2 | 3 | 4 | 5 | 6 | 7 | 8 | 9 | 10 | 11 | 12 |
Время, мин | 3 | 1 | 4 | 0,7 | 1,3 | 1 | 0,9 | 2,0 | 1,9 | 3,9 | 8 | 4 |
18. На прямоточной линии механического цеха обрабатывается деталь со следующими нормами времени по операциям:
Номер операции | 1 | 2 | 3 | 4 | 5 | 6 |
Штучное время, мин | 4,05 | 7,6 | 5,4 | 1,35 | 0,67 | 1,46 |
Каждый станок работает на удовлетворение только сменной потребности цеха, которая определяется 200 деталями. Действительный фонд работы станков в смену принимается равным 400 мин. Рассчитать потребность в оборудовании по операциям, построить план-график работы поточной линии и определить величину межоперационных оборотных заделов.
19. На прямоточной линии обрабатывается ведущая шестерня. Необходимо:
1) определить такт линии, потребное число рабочих мест на операциях и их загрузку;
2) составить план-график работы оборудования и рабочих на линии;
3) определить штат рабочих, учитывая возможные совмещения, и установить регламент работы для рабочих-совместителей;
4) рассчитать величину заделов;
5) построить график изменения межоперационных оборотных заделов. Суточная программа для линии – 400 шт.; линия работает в две смены; период комплектования задела – 2 ч. Технологический процесс следующий:
Номер операции | Операция | Норма времени, мин |
1 | Фрезерование торцов | 2,2 |
2 | Предварительная обточка | 4,6 |
3 | Обточка конуса | 1,8 |
4 | Окончательная обточка | 3,0 |
5 | Нарезание зубьев шестерни | 11,4 |
6 | Предварительное шлифование шейки | 2,4 |
7 | Фрезерование резьбы | 0,6 |
20. На сборочный конвейер детали поступают с трех линий механической обработки. Сборочная линия работает в одну смену с тактом 12 мин. Две питающие линии подают детали непрерывно с тактами r1 = 18 мин; r2 = 6 мин. Третья линия – прямоточная – подает на сборку детали 2 раза в смену; работая в одну смену, она полностью удовлетворяет потребности сборочной линии. Определить максимальную величину межлинейных оборотных заделов по каждой из трех деталей и установить сменность работы поточных линий.
21. В литейном цехе на формовочно-заливочном конвейере отливается крышка масляного насоса при продолжительности смены 8 ч. Сменная программа выпуска – 3 720 шт.
В одну опоку формуются четыре детали. Размер опок: верх 540× 540× 200 мм, низ 540× 540× 100 мм.
Технологический процесс содержит следующие операции:
Номер операции | Операция | Норма времени, мин | |
1 | Формовка верха | 1,3 | |
2 | Формовка низа | 0,92 | |
3 | Простановка стержней | 0,42 | |
4 | Сборка формы | 0,66 | |
5 | Заливка формы | 3,0 | |
6 | Охлаждение формы | 2,0 | |
7 | Выбивка | 1,0 | |
8 | Разъем и подготовка опок | 0,33 |
Определить:
1) такт и ритм линии;
2) потребное число оборудования и рабочих по операциям;
3) длину рабочих зон на каждой операции и общую длину линии;
4) скорость движения конвейера;
5) длительность цикла изготовления отливки на конвейере.
22. В литейном цехе на формовочно-заливочном конвейере отливается из ковша экскаватора. Сменная программа выпуска 640 шт.; продолжительность смены 8 ч. На конвейере выполняются следующие операции:
Номер операции | Операция | Норма времени, мин | |
1 | Формовка низа | 1,33 | |
2 | Формовка верха | 1,33 | |
3 | Простановка стержней | 0,66 | |
4 | Сборка формы | 0,58 | |
5 | Заливка формы | 2,0 | |
6 | Охлаждение формы | 4,0 | |
7 | Выбивка | 0,33 | |
8 | Разъем и подготовка опок | 0,5 |
Формуется 8 шт. в опоку. Размер опок: верх 712× 460× 200 мм, низ 712× 460× 150 мм. Определить:
1) такт и ритм линии;
2) потребное число оборудования и рабочих по операциям;
3) длину рабочих зон каждой операции и общую длину линии;
4) скорость движения конвейера;
5) длительность цикла изготовления отливки на конвейере.
23. На участке поточной обработки валика возникают межоперационные оборотные заделы. Определить их максимальную величину и построить график суммарного задела. Период комплектования задела – 2 ч. Линия работает с тактом 8 мин. Нормы времени по операциям следующие:
Номер операции | 1 | 2 | 3 | 4 | 5 | 6 |
Штучное время, мин | 4 | 6 | 8 | 4 | 6 | 12 |
Список использованной литературы
1. Гатилин Н.Ф. Проектирование поточных линий. - М.: Пищевая промышленность, 1975. – 374 с.
2. Дунаев П.Ф., Леников О.П. Конструирование узлов и деталей машин : Учеб. Пособие для техн. спец. вузов. – 5 изд. перераб. и доп. – М.: Высшая шк., 1998. – 447 с.
3. Ерохина С.А., Карпа А.В. Проектирование и расчет подъёмно – транспортирующих машин сельскохозяйственного назначения– М. : Колос, 1999. – 228 с.
4. Зуев Ф.Г., Лотков Н.А., Левачев Н.А., Паргентанян Г.В. Курсовое проектирование по механизации погрузочно-разгрузочных, транспортных и складских работ. Учебное пособие для вузов – М.:Колос, 1995. – 416 с.
5. Ивашков И.И. Монтаж, эксплуатация и ремонт подъемно-транспортных машин: Учебник для машиностроительных вузов. – М.: Машиностроение, 1981. – 335 с.
6. Изместьева А .Я., Юдина Л.П., Умняков П.Н. Проектирование предприятий швейной промышленности: Учебник для ВУЗов- М.: Легкая промышленность, 1983. -264 с.
7. Плавинский В.И. Машины непрерывного транспорта. – М:, «Машиностроение», 1969. - 720 с.
8. Пучкова Л.И., Гришин А.С. Проектирование предприятий с основами САПР. – М.:Колос, 1994. – 224 с.
9. Спиваковский А.О., Дьячков В.К. Транспортирующие машины: Учеб. пособие для машиностроительных вузов. – 3-е изд., перераб. – М.: Машиностроение, 1983. – 487 с.
Дата добавления: 2020-04-08; просмотров: 1015; Мы поможем в написании вашей работы! |
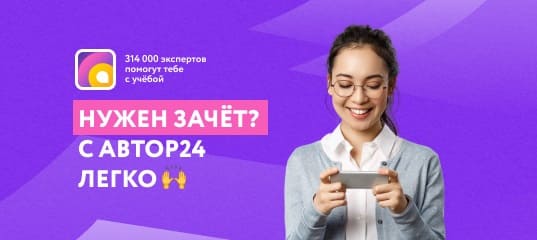
Мы поможем в написании ваших работ!