Оформление технологической документации на станки с ЧПУ.
После разработки операций, выполняемых на станках с ЧПУ студентам следует оформить технологическую документацию.
Разрабатываются:
- карты технологического процесса;
- операционные карты,
- карты наладки инструмента,
- карты эскизов,
Все эти документы разрабатываются на специальных бланках и в соответствии с ГОСТ 3.1418-82.
Литература : ГОСТ 3.1418-82.
Шестой этап (Разработка операций на станках с ручным управлением. Оформление технологической документации.)
Разработка операций на станках с ручным управлением.
Операции разрабатываются на основе принятого маршрутного технологического процесса, схемы базирования и закрепления детали на операции, сведений о точности и шероховатости поверхностей до и после обработки на данной операции, припусков на обработку, размера партии деталей (в зависимости от типа производства).
Рекомендуется следующий порядок разработки операции:
1) Наименование операции, номер операции.
Наименование и номер операции берется из задания и разработанного маршрута обработки в разделе 3 данной контрольной работы.
2) Эскиз операции
При разработке операционного эскиза окончательно устанавливается, какие поверхности заготовки будут обрабатываться на данной операции.
Выполняется эскиз с размерами и шероховатостью обработки, получаемыми после выполнения операции. Размеры указывают с предельными отклонениями, обрабатываемые поверхности нумеруют арабскими цифрами и выделяют сплошной линией (в два раза толще сплошной линии по ГОСТ 2303-68). Номер обрабатываемой поверхности проставляют в окружности 6 - 8 мм и соединяют выносной линией с изображением этой поверхности. Для обозначения баз и зажимных усилий пользуются условными знаками в соответствии с ГОСТ 3.1107-81, приведенными в литературе [3,65-68], [4,218-220]
|
|
План операции по переходам
План операции по переходам зависит от того на каком оборудовании она выполняется.
При разработке последовательности и содержания переходов необходимо стремиться к сокращению времени обработки за счет рационального выбора числа переходов, совмещения основного и вспомогательного времени, выбора средств технологического оснащения.
Операции могут быть с последовательным, параллельным и последовательно–параллельным выполнением переходов в зависимости от расположения заготовки относительно режущих инструментов. По числу устанавливаемых заготовок операции делятся на одноместные и многоместные, а по числу инструментов на одно- и многоинструментальные.
Технологическая база.
Технологическая база для операции была определена в разделе 1, на данном этапе необходимо подробно описать теоретическую схему базирования и схему установки детали на станке. Схему установки указать на операционном эскизе.
|
|
Оборудование (обоснование и краткая характеристика)
Выбор станков произведен при выполнении третьего этапа.
Приспособление для установки и зажима детали.
Выбор приспособлений производится в зависимости от вида обработки, типа станка и типа производства по справочникам [27], [29].
Для крупносерийного и массового производства характерно применение высокопроизводительных специальных приспособлений, снабженных быстродействующими зажимными устройствами. В серийном и единичном производстве применяют в основном универсальные и универсально-наладочные приспособления.
Выбранные приспособления должны обеспечить: правильную установку детали, повышение производительности за счет сокращения вспомогательного времени, надежность и безопасность работы, расширение технологических возможностей станка; автоматическое получение точности обработки; экономичность обработки.
В пояснительной записке должны быть указаны : тип приспособления, наименование и назначение, краткая техническая характеристика, позволяющая определить правильность и обоснованность выбора.
|
|
Режущий инструмент (характеристика, материал, геометрия, ГОСТ)
Для каждого перехода операции выбирают режущий инструмент.
Порядок выбора режущего инструмента и основные рекомендации по выбору:
1) Тип режущего инструмента устанавливается в соответствии с видом механической обработки на данной операции (или переходе) и требуемой точности и шероховатости обрабатываемой поверхности.
2) Выбирают материал режущей части инструмента в зависимости от физико-механических свойств обрабатываемого материала и характера обрабатываемой поверхности.
3) Сравнительные эксплуатационные свойства и назначение основных инструментальных материалов даны в таблицах приложения [19]. Рекомендации по выбору абразивного инструмента приведены в справочнике [27]. Определяют форму и габаритные размеры режущего инструмента в зависимости от формы и размеров обрабатываемой поверхности, типа и характеристики станка, на котором производится обработка.
Чаще всего применяются резцы прямоугольного сечения с соотношениями высоты и ширины 1,25 и 1,6 при ширине 10 – 40 мм. Для чистовой и получистовой обработки рекомендуется применять резцы с соотношением 1,6; для черновой обработки – 1,25.
|
|
Квадратная форма используется для расточных, автоматно-револьверных резцов и в других случаях, когда при прямоугольном резце недостаточно расстояние от опорной поверхности резца в резцедержателе до линии центра станка.
Круглая форма используется для расточных и резьбовых резцов, она дает возможность поворачивать резцы в резцедержателе.
Размеры сечения и длина резцов нормализованы. Длина устанавливается с учетом размеров головки резца, вылета из резцедержателя, числа зажимных винтов в резцедержателе и расстояния между ними.
4) Диаметр мерного инструмента (сверл, зенкеров, разверток, протяжек и др.) определяют исходя из промежуточных размеров обработки, и уточняют по ГОСТам.
При черновом фрезеровании применяют фрезы с крупными зубьями, а фрезы с мелкими зубьями – только при чистовом фрезеровании. Диаметр фрезы выбирается в зависимости от глубины резания по справочнику [16]. При фрезеровании цилиндрическими фрезами ширина фрезы должна быть больше ширины обрабатываемой поверхности на 2 – 5 мм.
При определении размеров шлифовального круга предпочтение следует отдавать кругам большего размера, так как удельная нагрузка на зерне круга при этом уменьшается и износ круга замедляется. Максимальные размеры круга определяются по паспортным данным станка.
Необходимо определить геометрические параметры режущей части инструмента в зависимости от физико-механических свойств обрабатываемого материала, материала инструмента и жесткости системы СПИД.
Рекомендуемые параметры геометрии режущей части различных инструментов приведены в табл. 26 – 34 справочника [16].
5) По каталогам, альбомам, ГОСТам, справочникам подбирается нормализованный режущий инструмент в соответствии с установленными параметрами.
Дата добавления: 2019-02-22; просмотров: 1505; Мы поможем в написании вашей работы! |
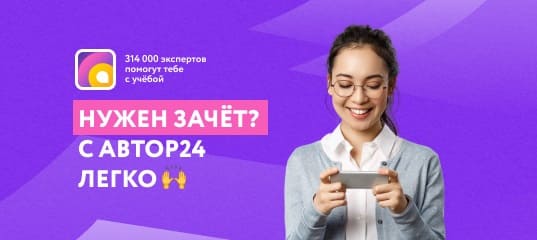
Мы поможем в написании ваших работ!