Пятый этап (Разработка операций на станках с ЧПУ. Выполнение схем технологических наладок).
а) Определение зон обработки на станках с ЧПУ, способы базирования.
В пояснительной записке студента перечисляются операции, выполняемые на станках с ЧПУ, для 1-2 операций приводятся эскизы заготовок деталей поступающих на станки с ЧПУ, где тонкими сплошными линиями определяют контуры детали, получающиеся после обработки на станке с ЧПУ, представляются размеры обрабатываемых поверхностей, их шероховатость.
Далее студенты показывают, как осуществляется обработка детали на станке с ЧПУ, т.е. разрабатывается схема обработки поверхностей.
Например, при токарной обработке детали в патроне на станке с ЧПУ может быть установлена следующая схема:
1. центрование.
2. сверление.
3. подрезание торца.
4. черновая обработка наружных поверхностей.
5. чистовая обработка наружных поверхностей.
6. нарезание резьбы и т.д.
Если припуск на черновую обработку больше наибольшей допустимой глубины резания, то черновая область обработки делится на уровни, определяется количество рабочих ходов (см. рис.5).
Рис. 5. Разделение черновой обработки на уровни.
Затем студенты должны описать способ базирования детали в данной операции, обосновать его, связать с предыдущими операциями технологического процесса.
Базирование детали на станке с ЧПУ должно обеспечивать устойчивость и жесткость установки заготовки, требуемую точность ориентации заготовки в приспособлении, кроме того базирование должно удовлетворять требованию совмещения координатных осей детали с осями координатной системы станка, что упрощает программирование и облегчает взаимную увязку нуля детали с нулем станка.
|
|
Так, при обработке на токарных станках с ЧПУ наибольшее распространение получили две схемы базирования: в центрах для деталей типа валов и в патронах для деталей типа дисков и втулок.
Базирование корпусных деталей на фрезерных и сверлильных станках с ЧПУ производится по трем точным отверстиям. В ряде случаев применяют базирование по черным базам (например, ложементы) или искусственным базам. При соответствующей подготовке базовых поверхностей установка деталей обеспечивает качественную обработку.
В пояснительной записке следует привести схему базирования детали, пояснить способы предварительной обработки базовых поверхностей и требования к ним.
Подраздел должен содержать 1-2 страницы.
Литература: [7,161-292]
б) Выбор оборудования и приспособления.
В данном подразделе пояснительной записки учащиеся должны привести краткую характеристику применяемых станков с ЧПУ (на 1-2 операции), обосновать выбор зажимных приспособлений, применяемых для установки и крепления детали на станке. Для описания станка необходимо пользоваться паспортами станков, данными справочной литературы.
|
|
При выборе приспособлений следует учитывать специфические требования, обуславливаемые особенностью программного оборудования: повышенную точность, жесткость, лишение заготовки и самого приспособления 6-ти степеней свободы, строго определенное положение базовых поверхностей заготовки и самого приспособления относительно начала координат станка, возможность подхода инструмента ко всем обрабатываемым поверхностям, возможность быстрой переналадки приспособлений.
Для выбора приспособлений следует пользоваться данными справочной специальной литературы, а также наборами «штатных» приспособлений, поставляемых вместе со станком. В данном подразделе приводится схема расположения приспособления, детали в системе координат станка, а также описывается способ крепления приспособления на станке.
Подраздел должен содержать 2-3 страницы.
в) Определение количества режущих инструментов и траектории их перемещений.
Траектория перемещения инструментов строится относительно контура детали и начинается в исходной точке, которую выбирают из условий минимизации вспомогательных ходов, обеспечения безопасности смены инструмента и удобства закрепления заготовки на станке.
|
|
Траектория инструментов должна соответствовать выбранной в п. 2.7.1. схеме обработки поверхностей детали, причем строится траектория определенной точки инструмента (например, для фрезерования центра радиуса фрез, для точения центра окружности при вершине резца и т.д.).
Рекомендуется траекторию движения инструментов изображать в масштабе 5:1 или 10:1 на миллиметровой бумаге, затем вшить в пояснительную записку. На схеме сплошными линиями указываются рабочие движения, а пунктирными – холостые. Опорные точки траектории обозначаются арабскими цифрами с числовым индексом. Цифра соответствует номеру точки, а индекс – номеру инструмента.
Стрелкой указываются направления движения. Если в обработке детали участвуют от одного до трех инструментов при небольшом количестве опорных точек, то вычерчиваются общая схема для всех инструментов. При большом числе инструментов и значительном количестве опорных точек следует вычерчивать схему движения для каждого инструмента отдельно.
Для облегчения чтения схемы движения инструментов рекомендуется использовать условные обозначения, приведенные в таблице 11. (см. далее).
|
|
Таблица 11. – Условные обозначения элементов траектории.
.7.1. ентов должна соответствовать выбраной крепления заготовки на станке.
исходной точке, которую выбирают из условий минимиз
Условные обозначения | Значение обозначения |
![]() | Исходная точка |
![]() | Точка остановки инструмента или его смены |
![]() | Контрольная точка с координатами х и у |
![]() | Точка вертикального подъема на 20мм |
![]() | Точка вертикального опускания на 15мм |
![]() | Перемещение с одновременным опусканием |
![]() | Перемещение с одновременным опусканием |
![]() | Траектория рабочего хода |
![]() | Траектория холостого хода |
Одновременно с разработкой траектории перемещения определяется необходимое количество режущих инструментов, определяется их тип, ГОСТ.
Следует помнить, что количество инструментов должно соответствовать возможностям установки их на станке, инструмент должен быть точный, жесткий, следует широко применять многогранные неперетачиваемые быстросменные пластины из твердого сплава.
Для установки выбранных режущих инструментов на станке необходимо выбрать для каждого режущего инструмента вспомогательный инструмент, определить его ГОСТ.
Подраздел должен содержать 1-2 страницы.
г) Расчет координат опорных точек траектории.
В данном подразделе пояснительной записки следует подробно аналитическим методом привести расчет координат 1-2 опорных точек траектории, а также координат исходной точки обработки.
Примеры определения координат опорных точек траектории достаточно подробно рассмотрены в учебнике А.Л. Дерябина «Программирование технологических процессов для станков с ЧПУ», а координаты исходной точки выбираются произвольно с учетом возможности Ø и экономичности обработки.
Расчеты координат должны сопровождаться соответствующими схемами, выполненными по возможности на миллиметровой бумаге в масштабе 1:1 (допускаются и другие масштабы). Результаты расчета координат всех остальных опорных точек следует выполнять на специальном бланке, форма которого приведена в таблице 2.12.
Таблица 2.12. – Координаты опорных точек.
Номер опорной точки | Координаты, мм | ||
Х | У | Z | |
Подраздел 2.7.4. должен содержать 2-3 страницы.
Литература:[7]
д). Разработка расчетно-технологической карты.
Расчетно-технологическая карта является исходным документом для разработки управляющей программы. Она содержит сведения об обработанных поверхностях детали, применяемой оснастке, траектории движения инструментов, режимов обработки и другие данные.
В курсовом проекте расчетно-технологическая карта разрабатывается на одну операцию. Обычно РТК выполняется на листе формата А1. Для станков с ЧПУ различных групп оформление РТК различно. Для токарных станков с ЧПУ на расчетно-технологической карте должны быть показаны:
1. Деталь, закрепленная в приспособлении и в том виде, какой она имеет после выполнения данного инструментального перехода. Если при обработке применяется несколько инструментов, то изображается несколько эскизов детали с размерами, полученными при выполнении каждого перехода. Обрабатываемые поверхности выделяются утолщенной линией, указываются направления осей координат х и z.
2. Режущий инструмент в исходной точке с указанием базовых размеров и координат его вершины. Для каждого инструмента изображают траекторию движения его вершины.
На траектории движения обозначают опорные точки и стрелки, указывающие направление движения. Рабочие движения инструмента показывают сплошными линиями, холостые – пунктирными.
Координаты опорных точек проставляются на РТК согласно рис.6
Рис. 6. Простановка размеров координат опорных точек на РТК.
1. Приспособление для крепления детали изображают сплошными тонкими линиями, ориентируют его базовые поверхности относительно системы координат станка, на линии – выносные записывают обозначение приспособления.
2. Резцедержатель или револьверную головку для установки режущих инструментов показывают сплошными тонкими линиями в начальном положении, ориентируют их относительно системы координат станка, режущие инструменты показывают в гнездах резцедержателя или револьверной головки, цифрами показывают номера инструментов по мере включения их в работу.
3. Над основной надписью чертежа помещают две таблицы, формы которых должны соответствовать рис.7 и рис.8. В основной надписи чертежа делается запись «РТК» на обработку (название детали). Станок модели (указывается модель).
Содержание перехода | Позиция инструмента Т | t, мм | S, мм/мин | Код подачи F | Vф, мм/мин | n, об/мин | Код частоты вращения S |
Рис.7. Форма таблицы №1 на РТК.
Примечание: таблицу режимов резания достаточно выполнить на 1-2 перехода
В позиции инструмента | Т01 | Т02 | и т.д. |
Наименование и характеристика режущего инструмента. | |||
Наименование и характеристика вспомо-гательного инструмента. | |||
Настроенные размеры инструмента и корректора. |
Рис. 8. Форма таблицы №2 на РТК.
Для фрезерных станков:
1) деталь вычерчивают в первом квадрате прямоугольной системы координат, ориентируют относительно осей Х и У, расположенных параллельно осям координат станка; выбирается исходная точка обработки; контуры детали, подлежащие обработке выделяются утолщенными линиями, деталь показывают зажатой в приспособлении.
2) изображают вторую проекцию детали, которую ориентируют относительно осей Х и Z.
3) траекторию движения инструмента изображают как в плоскости Х0У, так и Х0Z, требования к изображению траектории аналогичны токарным станкам.
4) требования к изображению приспособления аналогичны токарным станкам.
5) режущий инструмент показывают в плоскости Х0Z с указанием координат его положения, рекомендуется условно инструмент показать и в плоскости Х0У.
6) содержание таблиц аналогично токарным станкам.
7 )по необходимости строится развернутая циклограмма (перемещение фрез по оси Z).
Для сверлильных станков РТК разрабатывается аналогично фрезерным станкам с обязательным построением развернутой циклограммы перемещения инструмента по оси Z.
Для обрабатывающих центров РТК разрабатывают для каждой стороны детали. В пояснительной записке к проекту в разделе 2.7.6. даются пояснения к РТК.
Раздел должен содержать 1 страницу.
е) Краткая характеристика устройства числового программного управления.
В пояснительной записке учащиеся должны привести краткую характеристику устройства числового программного управления станка, показать его возможности.
Подраздел 2.7.7. должен содержать 1 страницу.
Литература:
1. Паспорта систем УЧПУ, инструкции по программированию.
и) Составление рукописи управляющей программы.
В пояснительной записке приводится рукопись управляющей программы обработки детали на одну из операций, выполняемую на станке с ЧПУ, приводится расшифровка 10-15 кадров программы и по возможности ее распечатка.
Подраздел 2.7.8. должен содержать 1-2 листа.
к) Запись управляющей программы на программность.
В пояснительной записке приводится способ записи программы, вклеивается перфолента, дается расшифровка нескольких кадров программ.
Подраздел 2.7.9. должен содержать 1 страницу.
л)Контроль записи программы.
В пояснительной записке приводятся способы контроля программы, приводится чертеж с графопостроителя.
Подраздел должен содержать 1 страницу.
м) Нормирование операции.
В пояснительной записке учащимся следует привести определение нормы времени на одну из операций, выполняемую на станке с ЧПУ.
Запись расчетов производить в следующей последовательности.
1. Привести исходные данные для нормирования: название операции, ее содержание, модель станка, вид программоносителя, название приспособления, тип режущего инструмента, материал режущей части, геометрию заточки, количество деталей в партии, краткую характеристику организации труда, эскиз обрабатываемой детали с необходимыми размерами, допусками, шероховатостью обрабатываемых поверхностей.
2. Норма штучного времени Тшт определяется по следующей формуле:
где to – основное (машинное) время в мин.;
tвсп – вспомогательное время, мин.;
tобс – время обслуживания рабочего места, мин.;
tотд – время на отдых и личные нужды, мин.
где toa – автоматическое основное время, мин.;
tва – автоматическое вспомогательное время, мин.
где Li – длина пути, проходимого инструментом или деталью в направлении подачи при обработке I – го технологического участка с учетом врезания и перебега, мм;
Smin i – минутная подача на данном участке;
m = 1,2,3 … число технологических участков обработки;
Smin I, Li – определяются по РТК или управляющей программе.
tва = tхх + tост
где tхх – суммарное время холостых ходов, мин.;
tост – время технологических пауз (смена инструмента, поворот стола)
где l1, l2, l3 – длины холостых ходов, мм;
n и S – частота вращения и подача при проходе соответствующего участка, м/мин;
Vус – скорость ускоренных перемещений, м/мин.
Величины l, n, S – определяются по РТК или управляющей программе.
tост = 0,4 + tсм ×n + tпов., мин
где tсм – время смены инструментов по программе, мин
n – количество смен инструментов (определяется по программе)
tпов – время на поворот стола.
tсм для токарных станков – 0,1мин,
для сверлильных станков – 0,13мин,
для фрезерных станков – 0,16мин.
tпов на ¼ оборота стола – 0,4мин.
Твсп = tуст + tпер + tизм
где tуст – время на установку и снятие детали, мин.;
tпер – время остановок станка для осмотра станка, ручной смены инструмента, поворота стола вручную и т.д. мин.;
tизм – время на измерение, если оно не перекрывается временем автоматической работы станка, мин.
tуст – выбирают по нормативам в зависимости от приспособления, массы детали, габаритов станка.
tпер - определяют по управляющей программе, где запланировались технологические паузы с определенной длительностью.
tизм – определяют по нормативам в зависимости от точности контролируемых размеров и вида контрольно-мерительных устройств.
3. Определить оперативное время Топ
Топ = tо + tвсп.
4. Определить tобс, tотд в % к оперативному времени К
К = 8…10%
5. Определить штучное время Тшт.
Тшт = Топ× мин.
6. Определить подготовительно-заключительное время Тпз по нормативам.
7. Определить штучно-калькуляционное время Тшт.к
Тшт.к = Тшт +
где n – число деталей в партии.
Литература:[2],[17],[18]
Дата добавления: 2019-02-22; просмотров: 293; Мы поможем в написании вашей работы! |
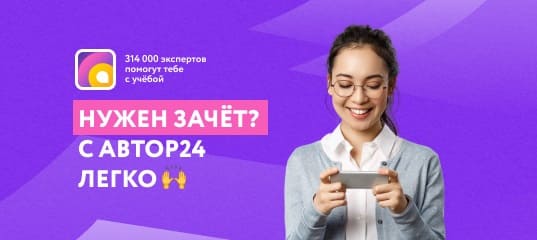
Мы поможем в написании ваших работ!