Определение требований к посадочным поверхностям вала и отверстия в корпусе
На эскизе подшипникового узла, вала и корпуса проставляются выбранные посадки, шероховатости и отклонения формы (рисунок 17).
Рисунок 17 – Эскиз подшипникового узла, вала и корпуса
Требования к посадочным поверхностям вала и отверстия определяются по [5].
Шероховатость поверхности выбирается по [5, таблица 3]. Для подшипника № 210 для примера шероховатость посадочной поверхности вала Rав = 1,25 мкм; для отверстия в корпусе Rаотв = 2,5 мкм; для торца вала Rат.в = 2,5 мкм.
Допуски круглости и профиля продольного сечения находятся по [5, таблица 4]. Для вала Тпр.сеч.в = 0,004 мм, для отверстия Тпр.сеч.о = 0,009 мм.
Допуск торцового биения опорного торца вала определяется по [5,таблица 5]: Тт.б = 0,025 мм.
Задача. На основе анализа условий работы подшипника в узле определить виды нагружения колец подшипников, рассчитать и выбрать посадки для установки подшипника на вал и в корпус. Вычертить схемы полей допусков выбранных посадок, эскиз подшипникового узла с обозначением выбранных посадок, эскизы отверстий в корпусе и вала с указанием шероховатости, предельных отклонений и допусков на погрешности формы. При этом принять, что вал является сплошным, а корпус толстостенным. Перегрузки не превышают 150 %. Исходные данные выбрать из таблицы 5.
Таблица 5 – Варианты заданий к задаче
Вариант | 1 | 2 | 3 | 4 | 5 | 6 | 7 | 8 | ||
Номер подшипника | 220 | 304 | 218 | 306 | 216 | 308 | 214 | 310 | ||
Класс точности | 0 | 6 | 5 | 6 | 0 | 5 | 0 | 6 | ||
Радиальная нагрузка R, кН | 13,5 | 11,0 | 36,0 | 57,6 | 5,0 | 12,5 | 28,5 | 50,4 | ||
Условие работы | Вал вращается, корпус неподвижен
|
Продолжение таблицы 5
Вариант | 9 | 10 | 11 | 12 | 13 | 14 | 15 | 16 |
Номер подшипника | 212 | 312 | 210 | 314 | 404 | 316 | 406 | 318 |
Класс точности | 0 | 5 | 0 | 6 | 0 | 6 | 5 | 6 |
Радиальная нагрузка R, кН | 3,4 | 31,2 | 24,8 | 56,0 | 3,9 | 32,0 | 27,9 | 14,0 |
Условие работы | Вал вращается, корпус неподвижен |
Допуски цилиндрических зубчатых передач
Система допусков цилиндрических зубчатых передач (ГОСТ 1643-81) устанавливает 12 степеней точности зубчатых колес. Для каждой степени точности устанавливаются независимые нормы допускаемых отклонений параметров, определяющих кинематическую точность колес и передачи, плавность работы и контакт зубчатых колес в передаче. Степень точности вновь проектируемых зубчатых передач и колес в большинстве случаев устанавливают в зависимости от окружной скорости колес (таблица А.17).
При комбинировании норм различных степеней точности нормы плавности работы колес и передач могут быть не более чем на две степени точнее или на одну степень грубее норм кинематической точности; нормы контакта зубьев (витков) не могут назначаться по степеням точности более грубым, чем нормы плавности, хотя для цилиндрических зубчатых передач допускаются на одну степень грубее.
|
|
Вид сопряжения зубьев колес в передаче определяет величину гарантированного, т. е. наименьшего из возможных в передаче, бокового зазора между нерабочими профилями зубьев. Вид сопряжения передачи выбирается по величине гарантированного бокового зазора в зависимости от межосевого расстояния.
Боковой зазор – это зазор между нерабочими профилями зубьев, который необходим для размещения смазки, компенсации погрешностей изготовления при сборке и для компенсации изменения размеров от температурных деформаций.
Ориентировочно величину гарантированного минимального бокового зазора можно определить по формуле
jn.min.расч = k × m, (17)
где k – коэффициент (для тихоходных передач (Vокр до 3 м/с) k = 0,01, для среднескоростных передач (Vокр = 3…15 м/с) k = 0,02, для быстроходных передач (Vокр св. 15 м/с) k = 0,03);
m – модуль нормируемого колеса, мм.
Для прямозубых колес межосевое расстояние определяется как
aw = (Z1 + Z2) × m / 2, (18)
|
|
где Z1, Z2 – число зубьев колес передачи.
Пример –Выполнить условие задачи 1 для зубчатой передачи: z1 = 58, z2 = 201, m = 3,5 мм,Vокр = 1,8 м/с.
Решение
Назначение степеней точности зубчатой передачи. Степень точности проектируемого колеса устанавливается в зависимости от окружной скорости колеса. Используем принцип комбинирования степеней. По окружной скорости Vокр = 1,8 м/с назначаем степень точности зубчатой передачи по плавности работы 9 (вторая цифра в обозначении колеса) (см. таблицу А.17). По рекомендациям [4] по кинематической норме точности назначаем степень такую же, как по плавности, т. е. 9, а по полноте контакта – на одну точнее. При записи степеней точности на чертеже первой записывается степень точности по нормам кинематической точности, вторая – по нормам плавности, последней – по нормам контакта зубьев, т. е. 9–9–8.
Выбор вида сопряжения по боковому зазору. Вид сопряжения передачи выбирается по величине гарантированного бокового зазора, который рассчитывается по формуле (17). Для тихоходной передачи
jn.min.расч = 0,01 × m = 0,01 ∙ 3,5 = 0,035 мм = 35 мкм.
Межосевое расстояние рассчитаем по формуле (18):
aw = (28 + 201) × 3,5 / 2 = 129,5 мм.
|
|
По рассчитанной величине jn min расч, равной 35 мкм, в зависимости от межосевого расстояния aw = 129,5 мм из таблицы А.18 выбираем вид сопряжения, причем выполняется условие jn.min.табл. ³ jn.min.расч.
Данному условию соответствует вид сопряжения Е, для которого 40 > 35 мкм. По таблице А.19 уточняем соответствие вида сопряжения и степени точности по нормам плавности работы. В девятой степени соответствия с сопряжением Е нет. Для девятой степени установлено соответствие с сопряжением С, для которого jn.min.табл = 100 мкм. Таким образом, окончательно точность зубчатой передачи будет 9 – 9 – 8 С (ГОСТ 1643-81).
Оформление чертежа цилиндрического зубчатого колеса. Рабочие чертежи зубчатых колес должны выполняться в соответствии с требованиями стандартов ЕСКД. Согласно им, на чертеже зубчатого колеса должна быть помещена таблица параметров зубчатого венца, которая состоит из трех частей: основные данные, данные для контроля, справочные данные. В строку «Степень точности…» записываются три степени точности и вид сопряжения, например 8–8–7С. Если все степени одинаковые, то пишется только одна цифра и вид сопряжения, например 7С. Пример оформления чертежа цилиндрического зубчатого колеса приведен на рисунке 18.
Рисунок 18 – Общий вид чертежа цилиндрического зубчатого колеса
Задача . По условиям работы зубчатого колеса установить степени точности по всем нормам точности, используя принцип комбинирования степеней точности, определить вид сопряжения. Исходные данные взять из таблицы 6.
Таблица 6 – Варианты заданий к задаче
Вариант | 1 | 2 | 3 | 4 | 5 | 6 | 7 | 8 |
Z1 | 32 | 48 | 55 | 40 | 36 | 28 | 46 | 38 |
Z2 | 18 | 20 | 22 | 36 | 28 | 24 | 18 | 20 |
Модуль m, мм | 5 | 3 | 2 | 4 | 5 | 3 | 2 | 4 |
Окружная скорость Vокр, м/с | 3 | 7 | 5 | 8 | 4 | 7 | 3 | 8 |
Продолжение таблицы 6
Вариант | 9 | 10 | 11 | 12 | 13 | 14 | 15 | 16 |
Z1 | 45 | 36 | 44 | 28 | 38 | 40 | 28 | 48 |
Z2 | 25 | 30 | 24 | 18 | 30 | 25 | 70 | 32 |
Модуль m, мм | 3 | 5 | 4 | 5 | 3 | 4 | 5 | 2 |
Окружная скоростьVокр, м/с | 5 | 7 | 4 | 6 | 8 | 7 | 4 | 3 |
Обозначения на чертежах
Отклонения формы и расположения поверхностей возникают в процессе обработки деталей из-за неточности и деформации станка, инструмента, приспособлений, неравномерности припуска на обработку, неоднородности материала, деформации заготовки. Для каждого вида допуска формы и расположения установлен определенный знак (таблица 7).
Таблица 7 – Условные обозначения допусков формы и расположения на чертежах
Допуск формы | Допуск взаимного расположения | ||||
Допуск прямолинейности | ![]() | Допуск перпендикулярности | ![]() | Допуск радиального или торцового биения | |
Допуск плоскостности | ![]() | Допуск параллельности | ![]() | ||
Допуск профиля продольного сечения | ![]() | Допуск наклона | ![]() | Допуск симметричности | ![]() |
Допуск цилиндричности | ![]() | Допуск соосности | ![]() | Позиционный допуск | |
Допуск круглости | ![]() | Допуск пересечения осей | ![]() |
На чертеже допуски формы и расположения указываются в рамке, которая разделена на две или три части и соединяется с рассматриваемой поверхностью линией со стрелкой. Базы обозначаются зачерненным равносторонним треугольником.
Одним из качеств поверхности является шероховатость, которая оказывает влияние на работу соединения (твердость, износостойкость, контактная жесткость и другие).
Шероховатость поверхности – совокупность неровностей с относительно малыми шагами, образующими рельеф детали и расположенными в пределах базовой длины.
ГОСТ 2.309-73 устанавливает шесть параметров шероховатости поверхности, правила простановки шероховатости на чертежах деталей. К параметрам шероховатости относятся:
Ra – среднее арифметическое отклонение профиля;
Rz – высота неровностей по 10 точкам;
Rmax – расстояние между линией выступов и линией впадин профиля (через самую высокую и самую низкую точки);
Sm – средний шаг неровностей профиля;
S – средний шаг местных выступов профиля – среднее значение шага местных выступов профиля в пределах базовой длины;
tp – относительная опорная длина профиля – отношение опорной длины к базовой длине.
Примеры простановки допусков формы и взаимного расположения поверхностей и шероховатости поверхности приведены на рисунке 19.
Рисунок 19 – Примеры простановки допусков формы и взаимного расположения поверхностей
Допуски формы и расположения не должны превышать допуски на соответствующий размер. Если допуск формы и расположения равен допуску на размер, то он на чертеже не указывается.
Задача. Вычертить эскизы деталей, представленных на рисунке 20 без указания буквенных обозначений поверхностей. Указать на эскизах следующие допуски и параметры шероховатости, используя данные таблицы 8.
Рисунок 20 – Эскизы деталей
Таблица 8 – Исходные данные к задаче 10
Номер варианта | Допуски и параметры шероховатости |
1 | 2 |
1 | Допуск радиального биения поверхности В относительно оси детали (Т = 0,1 мм). Допуск круглости поверхности В (Т = 0,2 мм). Допуск перпендикулярности поверхности Л относительно поверхности М (Т = 0,3 мм). |
Продолжение таблицы 8
| |
1 | 2 |
1 | Шероховатость поверхности К (среднее арифметическое отклонение профиля составляет 6,3 мкм) |
2 | Допуск круглости поверхности Д (Т = 0,01 мм). Допуск симметричности паза И относительно поверхностей Л и Ж (Т = 0,1 мм). Допуск параллельности поверхности К относительно поверхности М (Т = 0,2 мм). Шероховатость поверхности З (высота неровностей по 10 точкам составляет 12 мкм) |
3 | 1 Допуск радиального биения поверхности В относительно оси детали (Т = 0,1 мм). Допуск круглости поверхности Д (Т = 0,2 мм). Допуск перпендикулярности поверхности Л относительно поверхности М (Т = 0,3 мм). Шероховатость поверхности К (среднее арифметическое отклонение профиля составляет 6,3 мкм) |
4 | Отклонение от цилиндричности поверхности В (Т = 0,03 мм). Радиальное биение поверхности А относительно В (Т = 0,02 мм). 3 Отклонение от симметричности поверхности И относительно поверхности Л (Т = 0,1 мм). 4 Шероховатость поверхности К (среднее арифметическое отклонение профиля составляет 2,5 мкм) |
5 | 1 Допуск цилиндричности поверхности А (Т = 0,05 мм). Допуск параллельности поверхности 3 относительно поверхности И (Т = 0,1 мм). Допуск плоскостности поверхности М (Т = 0,2 мм). Шероховатость поверхности К (высота неровностей по 10 точкам составляет 20 мкм) |
6 | Отклонение от круглости поверхности А (Т = 0,4 мм). Торцевое биение поверхности Б относительно поверхности В (Т = 0,1 мм). Отклонение от плоскости поверхности И (Т = 0,1 мм). Шероховатость поверхности Д (высота неровностей по 10 точкам составляет 5 мкм) |
7 | Допуск круглости поверхности Д (Т = 0,01 мм). Допуск симметричности паза И относительно поверхностей Л и Ж (Т = 0,2 мм). Допуск параллельности поверхности К относительно поверхности М (Т = 0,1 мм). Шероховатость поверхности И (высота неровностей по 10 точкам составляет 12 мкм) |
8 | Допуск радиального биения поверхности А относительно оси поверхности В (Т = 0,2 мм). Допуск круглости поверхности Д (Т = 0,1 мм). Допуск перпендикулярности поверхности Ж относительно поверхности М (Т = 0,25 мм). Шероховатость поверхности З (среднее арифметическое отклонение профиля составляет 0,32 мкм) |
9 | Отклонение от цилиндричности поверхности А (Т = 0,01 мм). Радиальное биение поверхности Д относительно поверхности В (Т = 0,02 мм). Отклонение от симметричности поверхности И относительно поверхности Ж (Т = 0,2 мм). Шероховатость поверхности З (среднее арифметическое отклонение профиля составляет 0,63 мкм) |
10 | Допуск цилиндричности поверхности В (Т = 0,05 мм). Допуск параллельности поверхности И относительно поверхности З (Т = 0,1 мм). Допуск плоскостности поверхности М (Т = 0,2 мм). Шероховатость поверхности К (высота неровностей по 10 точкам составляет 40 мкм) |
Продолжение таблицы 8
1 | 2 |
11 | Отклонение от круглости поверхности Д (Т = 0,2 мм). Торцевое биение поверхности Г относительно поверхности В (Т = 0,5 мм). Отклонение от плоскостности поверхности З (Т = 0,2 мм). Шероховатость поверхности А (высота неровностей по 10 точкам составляет 12,5 мкм) |
12 | Допуск круглости поверхности А (Т = 0,1 мм). Допуск симметричности паза И относительно поверхностей Л и Ж (Т = 0,3 мм). Допуск торцевого биения поверхности Г относительно оси детали (Т = 0,05 мм). Шероховатость поверхности З (высота неровностей по 10 точкам составляет 40 мкм) |
13 | Отклонение от цилиндричности поверхности В (Т = 0,02 мм). Радиальное биение поверхности А относительно поверхности В (Т = 0,04 мм). Отклонение от симметричности поверхности И относительно поверхности Л (Т = 0,3 мм). Шероховатость поверхности К (среднее арифметическое отклонение профиля составляет 1,25 мкм) |
14 | Допуск цилиндричности поверхности В (Т = 0,05 мм). Допуск параллельности поверхности К относительно поверхности М (Т = 0,25 мм). Допуск плоскостности поверхности К (Т = 0,3 мм). Шероховатость поверхности А (высота неровностей по 10 точкам составляет 20 мкм) |
15 | Отклонение от цилиндричности поверхности Д (Т = 0,01 мм). Радиальное биение поверхности Д относительно поверхности В (Т = 0,05 мм). Отклонение от симметричности поверхности И относительно поверхности Ж (Т = 0,1 мм). Шероховатость поверхности В (среднее арифметическое отклонение профиля составляет 1,25 мкм) |
16 | Отклонение от круглости поверхности Д (Т = 0,2 мм). Торцевое биение поверхности Г относительно поверхности В (Т = 0,2 мм). Отклонение от плоскостности поверхности З (Т = 0,2 мм). Шероховатость поверхности А (высота неровностей по 10 точкам составляет 10 мкм) |
Список литературы
1 Палей, М. А. Допуски и посадки: справочник в 2 ч. / М. А. Палей. – 8-е изд., перераб. и доп. – Санкт-Петербург. : Политехника, 2001. – Ч. 1. – 576 с.
2 Палей, М. А. Допуски и посадки: справочник в 2 ч. / М. А. Палей. – 8-е изд., перераб. и доп. – Санкт-Петербург. : Политехника, 2001. – Ч. 2. – 608 с.
3 ГОСТ 2.403-75. Правила выполнения чертежей цилиндрических зубчатых колес. – Москва. : Изд-во стандартов, 1982. – 11 с.
4 ГОСТ 1643-81. Передачи зубчатые цилиндрические. Допуски. – М Москва. : Изд-во стандартов, 1981. – 65 с.
5 ГОСТ 3325-85. Подшипники качения. Поля допусков и технические требования к посадочным поверхностям валов и корпусов. Посадки. – Москва. : Изд-во стандартов, 1985. – 21 с.
Приложение А
(справочное)
Таблица А.1 – Допуски и отклонения калибров для размеров до 500 мм (ГОСТ 24853-81)
Квалитет | Обозначение допусков | Интервал размеров, мм | ||||||||||||
До 3 | Св.3 до 6 | Св. 6 до 10 | Св. 10 до 18 | Св.18 до 30 | Св. 30 до 50 | Св. 50 до 80 | Св. 80 до 120 | Св. 120 до 180 | Св. 180 до 250 | Св. 250 до 315 | Св. 315 до 400 | Св. 400 до 500 | ||
Размер и допуски калибров, мкм | ||||||||||||||
6 | z | 1 | 1,5 | 1,5 | 2 | 2 | 2,5 | 2,5 | 3 | 4 | 5 | 6 | 7 | 8 |
y | 1 | 1 | 1 | 1,5 | 1,5 | 2 | 2 | 3 | 3 | 4 | 5 | 6 | 7 | |
а, а1 | 0 | 0 | 0 | 0 | 0 | 0 | 0 | 0 | 0 | 2 | 3 | 4 | 5 | |
z1 | 1,5 | 2 | 2 | 2,5 | 3 | 3,5 | 4 | 5 | 6 | 7 | 8 | 10 | 11 | |
y1 | 1,5 | 1,5 | 1,5 | 2 | 3 | 3 | 3 | 4 | 4 | 5 | 6 | 6 | 7 | |
Н, Нs | 1,2 | 1,5 | 1,5 | 2 | 2,5 | 2,5 | 3 | 4 | 5 | 7 | 8 | 9 | 10 | |
H1 | 2 | 2,5 | 2,5 | 3 | 4 | 4 | 5 | 6 | 8 | 10 | 12 | 13 | 15 | |
Hр | 0,8 | 1 | 1 | 1,2 | 1,5 | 1,5 | 2 | 2,5 | 3,5 | 4,5 | 6 | 7 | 8 | |
7 | z, z1 | 1,5 | 2 | 2 | 2,5 | 3 | 3,5 | 4 | 5 | 6 | 7 | 8 | 10 | 11 |
y, y1 | 1,5 | 1,5 | 1,5 | 2 | 3 | 3 | 3 | 4 | 4 | 6 | 7 | 8 | 9 | |
а, а1 | 0 | 0 | 0 | 0 | 0 | 0 | 0 | 0 | 0 | 3 | 4 | 6 | 7 | |
Н, Н1 | 2 | 2,5 | 2,5 | 3 | 4 | 4 | 5 | 6 | 8 | 10 | 12 | 13 | 15 | |
Нs | – | – | 1,5 | 2 | 2,5 | 2,5 | 3 | 4 | 5 | 7 | 8 | 9 | 10 | |
Нр | 0,8 | 1 | 1 | 1,2 | 1,5 | 1,5 | 2 | 2,5 | 3,5 | 4,5 | 6 | 7 | 8 | |
8 | z, z1 | 2 | 3 | 3 | 4 | 5 | 6 | 7 | 8 | 9 | 12 | 14 | 16 | 18 |
y, y1 | 3 | 3 | 3 | 4 | 4 | 5 | 5 | 6 | 6 | 7 | 9 | 9 | 11 | |
а, а1 | 0 | 0 | 0 | 0 | 0 | 0 | 0 | 0 | 0 | 4 | 6 | 7 | 9 | |
Н | 2 | 2,5 | 2,5 | 3 | 4 | 4 | 5 | 6 | 8 | 10 | 12 | 13 | 15 | |
Н1 | 3 | 4 | 4 | 5 | 6 | 7 | 8 | 10 | 12 | 14 | 16 | 18 | 20 | |
Нр | 1,2 | 1,5 | 1,5 | 2 | 2,5 | 2,5 | 3 | 4 | 5 | 7 | 8 | 9 | 10 | |
9 | z, z1 | 5 | 6 | 7 | 8 | 9 | 11 | 13 | 15 | 18 | 21 | 24 | 28 | 32 |
y, y1 | 0 | 0 | 0 | 0 | 0 | 0 | 0 | 0 | 0 | 0 | 0 | 0 | 0 | |
а, а1 | 0 | 0 | 0 | 0 | 0 | 0 | 0 | 0 | 0 | 4 | 6 | 7 | 9 | |
Н | 2 | 2,5 | 2,5 | 3 | 4 | 4 | 5 | 6 | 8 | 10 | 12 | 13 | 15 | |
Н1 | 3 | 4 | 4 | 5 | 6 | 7 | 8 | 10 | 12 | 14 | 16 | 18 | 20 | |
Нр | 1,2 | 1,5 | 1,5 | 2 | 2,5 | 2,5 | 3 | 4 | 5 | 7 | 8 | 9 | 10 |
Таблица А.2 – Шероховатость рабочих поверхностей калибров
Квалитет точности контролируемой детали | IT6, IT7, IT8 | IT9, IT10, IT11 |
Шероховатость поверхности калибра Ra, мкм | 0,08 | 0,16 |
Таблица А.3 – Шарикоподшипники радиальные однорядные (ГОСТ 8338-85)
Обозначение подшипника | Размер, мм | Обозначение подшипника
| Размер, мм | ||||||
D | d | r | В | D | d | r | В | ||
Легкая серия | 310 | 110 | 50 | 3 | 27 | ||||
210 | 90 | 50 | 2 | 20 | 311 | 120 | 55 | 3 | 29 |
211 | 100 | 55 | 2,5 | 21 | 312 | 130 | 60 | 3,5 | 31 |
212 | 110 | 60 | 2,5 | 22 | 313 | 140 | 65 | 3,5 | 33 |
213 | 120 | 65 | 2.5 | 23 | 314 | 150 | 70 | 3,5 | 35 |
214 | 125 | 70 | 2,5 | 24 | 315 | 160 | 75 | 3,5 | 37 |
215 | 130 | 75 | 2,5 | 25 | 316 | 170 | 80 | 3,5 | 39 |
216 | 140 | 80 | 3 | 26 | 317 | 180 | 85 | 4 | 41 |
217 | 150 | 85 | 3 | 28 | 318 | 190 | 90 | 4 | 43 |
218 | 160 | 90 | 3 | 30 | 319 | 200 | 95 | 4 | 45 |
219 | 170 | 95 | 3,5 | 32 | 320 | 215 | 100 | 4 | 47 |
220 | 180 | 100 | 3,5 | 34 | Тяжелая серия | ||||
Средняя серия | 404 | 72 | 20 | 2 | 19 | ||||
304 | 52 | 20 | 2 | 15 | 405 | 80 | 25 | 2,5 | 21 |
305 | 62 | 25 | 2 | 17 | 406 | 90 | 30 | 2,5 | 23 |
306 | 72 | 30 | 2 | 19 | 407 | 100 | 35 | 2,5 | 25 |
307 | 80 | 35 | 2,5 | 21 | 408 | 110 | 40 | 3 | 27 |
308 | 90 | 40 | 2,5 | 23 | 409 | 120 | 45 | 3 | 29 |
309 | 100 | 45 | 2,5 | 25 | 410 | 130 | 50 | 3,5 | 31 |
Таблица А.4 – Допустимые интенсивности радиальных нагрузок на посадочные поверхности вала
Диаметр d, мм | Допустимое значение Рr при посадке на вал, Н/мм | |||
js5, js6 | к5, к6 | m5, m6 | n5, n6 | |
Cв. 18 до 80 | 0–300 | 300–1400 | 1400–1600 | 1600–3000 |
Cв. 80 до 180 | 0–600 | 600–2000 | 2000–2500 | 2500–4000 |
Cв. 180 до 360 | 0–700 | 700–3000 | 3000–3500 | 3500–6000 |
Cв. 360 до 630 | 0–900 | 900–3500 | 3500–4500 | 4500–8000 |
Таблица А.5 – Допустимые интенсивности радиальных нагрузок на посадочные поверхности корпуса
Диаметр D, мм | Допустимое значение Рr при посадке на вал, Н/мм | ||||
св. | до | К6, К7 | М6, М7 | N6, N7 | Р7 |
50 | 180 | 0–800 | 800–1000 | 1000–1300 | 1300–2500 |
180 | 360 | 0–1000 | 1000–1500 | 1500–2000 | 2000–3300 |
360 | 630 | 0–1200 | 1200–2000 | 2000–2600 | 2600–4000 |
630 | 1600 | 0–1600 | 1600–2500 | 2500–3500 | 3500–5500 |
Таблица А.6 – Предельные отклонения внутренних колец подшипников (ГОСТ 520-89)
Интервал диаметров d, мм | Класс точности подшипника | Интервал диаметров d, мм | Класс точности подшипника | ||||||
0 | 6 | 5 | 4 | 0 | 6 | 5 | 4 | ||
Нижнее предельное отклонение, мкм | Нижнее предельное отклонение, мкм | ||||||||
Св. 2,5до 10 | –8 | –7 | –5 | –4 | Св. 50 до 80 | –15 | –12 | –9 | –7 |
Св. 10 до 18 | –8 | –7 | –5 | –4 | Св. 80 до 120 | –20 | –15 | –10 | –8 |
Св. 18 до 30 | –10 | –8 | –6 | –5 | Св. 120 до 180 | –25 | –18 | –13 | –10 |
Св. 30 до 50 | –12 | –10 | –8 | –6 | |||||
Примечание – Верхние предельные отклонения ES = 0 |
Таблица А.7 – Предельные отклонения наружных колец подшипников (ГОСТ 520-89)
Интервал диаметров D, мм | Класс точности подшипника | Интервал диаметров D, мм | Класс точности подшипника | ||||||
0 | 6 | 5 | 4 | 0 | 6 | 5 | 4 | ||
Нижнее предельное отклонение, мкм | Нижнее предельное отклонение, мкм | ||||||||
Св. 2,5 до 6 | –8 | –7 | –5 | –4 | Св.80 до 120 | –15 | –13 | –10 | –8 |
Св. 6 до 18 | –8 | –7 | –5 | –4 | Св. 120 до 150 | –18 | –15 | –11 | –9 |
Св. 18 до30 | –9 | –8 | –6 | –5 | Св. 150 до 180 | –25 | –18 | –13 | –10 |
Св. 30 до50 | –11 | –9 | –7 | –6 | Св. 180 до 250 | –30 | –20 | –15 | –11 |
Св. 50 до 80 | –13 | –11 | –9 | –7 | Св. 250 до 315 | –35 | –25 | –18 | –13 |
Примечание – Верхние предельные отклонения еs = 0 |
Таблица А.8 – Поля допусков для отверстий корпусов и валов при местном нагружении колец подшипников
Нагружение | Диаметр отверстия | Корпус стальной или чугунный | Для валов | |
неразъемный | разъемный | |||
Спокойное или с умеренными толчками и вибрацией. Перегрузка до 150 % | < 80 | Н6, H7 | Н6, H7, H8 | h5, h6, g5 |
80–260 | G6, G7 | g6, f6, jS6 | ||
С ударами и вибрацией. Перегрузка до 300 % | < 80 | JS6, JS7 | JS6, JS7 | h5, h6 |
80–260 | Н6, H7 | g5, g6 |
Таблица А.9 – Допускаемые погрешности измерений
В микрометрах
Номинальный размер | Квалитет | |||||||||||
5 | 6 | 7 | 8 | 9 | 10 | |||||||
IT | δиз | IT | δиз | IT | δиз | IT | δиз | IT | δиз | IT | δиз | |
1 | 2 | 3 | 4 | 5 | 6 | 7 | 8 | 9 | 10 | 11 | 12 | 13 |
До 3 | 4 | 1,4 | 6 | 1,8 | 10 | 3,0 | 14 | 3,0 | 25 | 6 | 40 | 8 |
Св. 3 до 6 | 5 | 1,6 | 8 | 2,0 | 12 | 3,0 | 18 | 4,0 | 30 | 8 | 48 | 10 |
Св. 6 до 10 | 6 | 2,0 | 9 | 2,0 | 15 | 4,0 | 22 | 5,0 | 36 | 9 | 58 | 12 |
Св. 10 до 18 | 8 | 2,8 | 11 | 3,0 | 18 | 5,0 | 27 | 7,0 | 43 | 10 | 70 | 14 |
Св. 18 до 30 | 9 | 3,0 | 13 | 4,0 | 21 | 6,0 | 33 | 8,0 | 52 | 12 | 84 | 18 |
Св. 30 до 50 | 11 | 4,0 | 16 | 5,0 | 25 | 7,0 | 39 | 10,0 | 62 | 16 | 100 | 20 |
Св. 50 до 80 | 13 | 4,0 | 19 | 5,0 | 30 | 9,0 | 46 | 12,0 | 74 | 18 | 120 | 30 |
Св. 80 до 120 | 15 | 5,0 | 22 | 6,0 | 35 | 10,0 | 54 | 12,0 | 87 | 20 | 140 | 30 |
Окончание таблицы А.9
1 | 2 | 3 | 4 | 5 | 6 | 7 | 8 | 9 | 10 | 11 | 12 | 13 |
Св. 120 до 180 | 18 | 6,0 | 25 | 7,0 | 40 | 12,0 | 63 | 16,0 | 100 | 30 | 160 | 40 |
Св. 180 до 250 | 20 | 7,0 | 29 | 8,0 | 46 | 12,0 | 72 | 18,0 | 115 | 30 | 185 | 40 |
Св. 250 до 315 | 23 | 8,0 | 32 | 10,0 | 52 | 14,0 | 81 | 20,0 | 130 | 30 | 210 | 50 |
Св. 315 до 400 | 25 | 9,0 | 36 | 10,0 | 57 | 16,0 | 89 | 24,0 | 140 | 40 | 230 | 50 |
Св. 400 до 500 | 27 | 9,0 | 40 | 12,0 | 63 | 18,0 | 97 | 26,0 | 155 | 40 | 250 | 50 |
Примечание – IT – допуски размеров, мкм; δиз – допускаемые погрешности измерений, мкм |
Таблица А.10 – Техническая характеристика штангенциркулей (ГОСТ 166-80)
Тип, модель | Диапазон измерения, мм | Показание нониуса, мм | Допускаемая погрешность при отсчёте по нониусу, мм, не более | Тип, модель | Диапазон измерения, мм | Показание нониуса, мм | Допускаемая погрешность при отсчёте по нониусу, мм, не более |
ШЦ-I ШЦ-II ШЦ-II | До 125 До 150 До 250 | 0,1 0,05 0,05 | ± 0,1 ± 0,1 ± 0,1 | ШЦ-III ШЦ-III ШЦ-III | До 160 До 400 250–630 | 0,1 0,1 0,1 | ± 0,1 ± 0,1 ± 0,1 |
Таблица А.11 – Технические характеристики микрометров (ГОСТ 6507-78)
Тип, модель | Диапазон измерения, мм | Цена деления, мм | Допускаемая погрешность для приборов класса точности 2, мм, не более | Тип, модель | Диапазон измерения, мм | Цена деления, мм | Допускаемая погрешность для приборов класса точности 2, мм, не более |
МК-25 МК-50 МК-75 МК-100 МК-125 МК-150 МК-175 | 0–25 25–50 50–75 75–100 100–125 125–150 150–175 | 0,01 0,01 0,01 0,01 0,01 0,01 0,01 | ± 0,004 ± 0,004 ± 0,004 ± 0,004 ± 0,005 ± 0,005 ± 0,005 | МК-200 МК-225 МК-250 МК-275 МК-300 МК-400 МК-500 | 175–200 200–225 225–250 250–275 275–300 300–400 400–500 | 0,01 0,01 0,01 0,01 0,01 0,01 0,01 | ± 0,005 ± 0,006 ± 0,006 ± 0,006 ± 0,006 ± 0,008 ± 0,010 |
Таблица А.12 – Технические характеристики микрометров рычажных (ГОСТ 6507-78)
Тип, модель | Диапазон измерения, мм | Цена деления, мм | Допускаемая погрешность, мм, не более | Тип, модель | Диапазон измерения, мм | Цена деления, мм | Допускаемая погрешность, мм, не более |
МР-25 МР-50 МР-75 МР-100 МРИ-125 МРИ-150 | 0–25 25–50 50–75 75–100 100–125 125–150 | 0,02 0,02 0,02 0,02 0,02 0,02 | ± 0,003 ± 0,003 ± 0,003 ± 0,003 ± 0,005 ± 0,005 | МРИ-200 МРИ-250 МРИ-300 МРИ-400 МРИ-500 | 150–200 200–250 250–300 300–400 400–500 | 0,02 0,02 0,02 0,02 0,01 | ± 0,006 ± 0,006 ± 0,006 ± 0,006 ± 0,008 |
Таблица А.13 – Технические характеристики скоб с отсчетным механизмом (ГОСТ 11098-75)
Скоба | Тип, модель | Диапазон измерения, мм | Цена деле-ния, мм | Допускае-мая погреш-ность, мм, не более | Скоба | Тип, модель | Диапазон измерения, мм | Цена деления, мм | Допускае-мая погреш-ность, мм, не более |
Рычаж-ная | СР-25 СР-50 СР-75 СР-100 СР-125 СР-150 | 0–25 25–50 50–75 75–100 100–125 125–150 | 0,02 0,02 0,02 0,02 0,02 0,02 | ± 0,002 ± 0,002 ± 0,002 ± 0,002 ± 0,002 ± 0,002 | Инди-катор-ная | СИ-50 СИ-100 СИ-200 СИ-300 СИ-400 СИ-500 | 0–50 50–100 100–200 200–300 300–400 400–500 | 0,01 0,01 0,01 0,01 0,01 0,01 | ± 0,008 ± 0,008 ± 0,010 ± 0,010 ± 0,012 ± 0,012 |
Таблица А.14 – Техническая характеристика нутромеров
Нутромер | Тип, модель | Диапазон измерения, мм | Допускаемая погрешность, мм, не более | Нутромер | Тип, модель | Диапазон измерения, мм | Допускаемая погрешность, мм, не более |
Индика-торный (ГОСТ 868-82) | НИ 10 НИ 18 НИ 50Л НИ 100 НИ 160 НИ 250 НИ 450 | 6–10 10–18 18–50 50–100 100–160 160–250 250–450 | ± 0,012 ± 0,012 ± 0,015 ± 0,018 ± 0,018 ± 0,018 + 0,022 | С измери-тельными головками (ГОСТ 9244-75) | 153 116 103 104 105 109 154 155 156 | 1,5–2,0 2–3 3–6 6–10 10–18 18–50 50–100 100–160 160–260 | ± 0,0018 ± 0,0018 ± 0,0018 ± 0,0018 ± 0,0035 ± 0,0035 ± 0,004 ±0,004 ±0,004 |
Таблица А.15 – Технические характеристики нутромеров микрометрических (ГОСТ 10-75)
Тип, модель | Диапазон измерения, мм | Допускаемая погрешность, мм, не более | Тип, модель | Диапазон измерения, мм | Допускаемая погрешность, мм, не более |
НМ 50-75 НМ 75-175 | 50–75 75–175 | ± 0,004 ± 0,006 | НМ 75-600 НМ 150-1250 | 75–600 150–1250 | ± 0,015 ± 0,020 |
Таблица А.16 – Требования к базовым отверстиям насадных зубчатых (червячных) колёс
Степень точности | Точность отверстия (ГОСТ 25347-82) | Шероховатость отверстия Ra, мкм |
3-5 | Н4, Н5 | 0,32–0,63 |
6-7 | Н6, Н7 | 0,63–1,25 |
8 и выше | Н7, Н8 | 1,25–2,5 |
Таблица А.17 – Зависимость степеней точности по нормам плавности работы передачи от окружной скорости
Степень точности по норме плавности | 6 | 7 | 8 | 9 |
Окружная скорость V, м/c | Св. 10 до 15 | Св. 8 до 10 | Св. 2 до 8 | До 2 |
Шероховатость рабочей поверхности зубьев Ra, мкм | 0,63 | 1,25 | 3,2 | 6,3 |
Таблица А.18 – Норма бокового зазора (показатель jn min – гарантированный боковой зазор) ГОСТ 1643-81
Вид сопряжения |
Класс отклонений межосевого расстояния | Межосевое расстояние, аw | ||||||||
До 80 | От 80 до 125 | От 125 до 180 | От 180 до 215 | От 215 до 250 | От 250 до 315 | От 315 до 400 | От 400 до 500 | От 500 до 630 | ||
В микрометрах | ||||||||||
H E D C B A | I II III IV V VI | 0 30 46 74 120 190 | 0 35 54 87 140 220 | 0 40 63 100 160 250 | 0 46 72 115 185 290 | 0 52 81 130 210 320 | 0 57 89 140 230 360 | 0 63 97 155 250 400 | 0 70 110 175 280 440 | 0 80 125 200 320 500 |
Таблица А.19 – Соответствие вида сопряжения степени точности по нормам плавности цилиндрических зубчатых колес
Вид сопряжения | H | E | D | C | B | A |
Степень точности по нормам плавности | 3–7 | 3–7 | 3–8 | 3–9 | 3–11 | 3–12 |
Приложение Б
(справочное)
Дата добавления: 2019-03-09; просмотров: 1397; Мы поможем в написании вашей работы! |
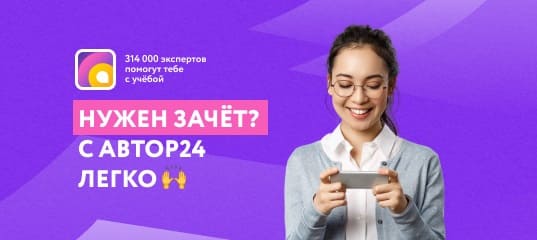
Мы поможем в написании ваших работ!