Расчет предельных и исполнительных размеров калибров и выбор универсальных измерительных средств
Калибры являются контрольными инструментами для определения годности деталей. С помощью калибров можно установить, находится ли действительный размер детали между наибольшим и наименьшим предельными размерами или нет, т. е. годная деталь или бракованная.
Для контроля отверстий используют калибры-пробки, а для контроля валов – калибры-скобы. В комплект калибров входят проходной (ПР) и непроходной (НЕ) калибры. Деталь считается годной, если проходной калибр проходит в проверяемую деталь под действием собственного веса или усилия, равного ему, а непроходной – не проходит.
По назначению калибры делятся на рабочие и контрольные. В процессе изготовления рабочих калибров-скоб используются контрольные калибры: К – ПР, К – НЕ, а калибр К – И – для контроля износа проходной скобы в процессе ее эксплуатации. Схемы контроля калибрами-пробками и калибрами-скобами представлены на рисунках 11, а и 13, а.
Расчет калибров для контроля отверстий
С помощью проходной пробки проверяют наименьший предельный размер отверстия Dmin, а непроходной – наибольший предельный размер Dmах, т. е. эти размеры являются номинальными для проходной и непроходной пробок.
а)
б)
Рисунок 11 – Схемы контроля отверстия калибрами-пробками (а) и расположения полей допусков калибра-пробки (б)
|
|
В качестве исполнительных размеров, т. е. размеров, проставляемых на чертежах, калибров-пробок принимается их наибольший размер, допуск задается в «минус», как для основного вала.
Пример 1 –Рассчитать исполнительные размеры калибров-пробок для контроля отверстия Ø16Н8 .
Решение
Максимальный предельный диаметр отверстия
Dmax = D + ES =16 + 0,027 = 16,027 мм.
Минимальный предельный диаметр отверстия
Dmin = D + EI = 16 + 0 = 16,000 мм.
Допуски на изготовление калибров нормируются по ГОСТ 24853-81.
Для определения предельных и исполнительных размеров пробок из таблицы указанного стандарта (таблица А.1) выписываем численные значения параметров Н, y, z по квалитету 8 и диаметру 16 мм: Н = 3 мкм = 0,003 мм; y = 4 мкм = 0,004 мм; z = 4 мкм = 0,004 мм.
Строим схему полей допусков калибра-пробки, на которой указываем поле допуска контролируемого отверстия Н8, и проставляем все найденные допуски (рисунок 11, б). Эта схема применима для расчета калибров-пробок с номинальными размерами до 180 мм.
Определяем предельные и исполнительные размеры пробок ПР и НЕ из ГОСТ 24853-81 по формулам:
DПР min = Dmin + z – H / 2 = 16 + 0,004 – 0,003 / 2 = 16,0025 мм;
DПР max = Dmin + z + H / 2 = 16 + 0,004 + 0,003 / 2 = 16,0055 мм;
DПР изн = Dmin – y = 16 – 0,004 = 15,996 мм.
|
|
Исполнительный размер проходной пробки
DПР исп = DПР max = 16,0055 -0,003 мм;
DНЕ max = Dmax + H / 2 = 16,027 + 0,003 / 2 = 16,0285 мм;
DНЕ min = Dmax – H / 2 = 16,027 – 0,003 / 2 = 16,0255 мм.
Исполнительный размер непроходной пробки
DНЕ исп = DНЕ max = 16,0285-0,003 мм.
Вычерчиваем эскиз рабочей пробки, на котором указываем исполнительные размеры, шероховатость рабочих поверхностей и маркировку (рисунок 12). Шероховатость выбираем по таблице А.2. Маркировка калибра содержит диаметр контролируемого отверстия с полем допуска и квалитетом точности, предельные отклонения контролируемого отверстия, товарный знак завода-изготовителя.
Рисунок 12 – Эскиз калибра-пробки
Дата добавления: 2019-03-09; просмотров: 6974; Мы поможем в написании вашей работы! |
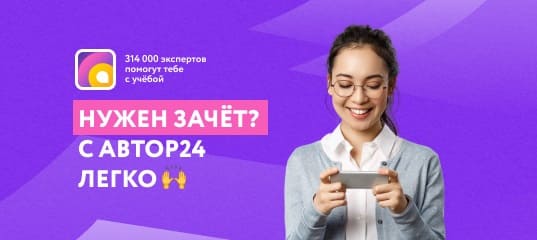
Мы поможем в написании ваших работ!