Расчеты по механическому участку
7.1.1 Определение потребного количества основного оборудования
Расчетное количество станков основного производства определяем по моделям станков по формуле:
где Т – трудоемкость в станкочасах, затрачиваемая на одно изделие по каждой модели станка (исходные данные).
N – годовая программа, шт.
Фо – действительный годовой фонд времени работы оборудования (используют данные таблицы А.1). Принимаем Фо = 4060 часов;
Определим количество токарно-винторезных станков 1К62
Полученное расчетное значение округляем до ближайшего большего расчетного числа станков
и определяем коэффициент загрузки:
Данный коэффициент загрузки превышает допустимые значения таблицы А.2. Поэтому в расчет вводим коэффициент использования Ки, учитывающий возможные наложенные потери. Ки = 0,9.
Тогда принятое количество станков Спр составит:
Принимаем Спр =13 станков.
Следовательно фактический коэффициент загрузки составит:
Определим количество токарно-винторезных станков 1М365
Ср = 6 станков.
Кз = 0,85 удовлетворяет требованиям таблицы А.2. Поэтому не вводим дополнительно коэффициент использования. Тогда Ср=Спр=6 станков;
Аналогично производим расчет по остальным моделям станков. Все расчеты сведем в таблицу 3.
Таблица 3 - Сводная ведомость основного оборудования.
№ п/п | Наименование и модель станка | ![]() | ![]() | ![]() | ![]() | ![]() | Высота станка, мм | Вес станка,кг |
1 | 2 | 3 | 4 | 5 | 6 | 7 | 8 | 9 |
1 | Токарно-винторезный станок 1К62 | 10,9 | 11 | 13 | 0,84 | 0,85 | 1500 | 2400 |
2 | Токарно-карусельный станок 1512 | 5,1 | 6 | 6 | 0,85 | 0,85 | 4100 | 1850 |
3 | Токарно-винторезный станок 1М635 | 5,1 | 6 | 6 | 0,85 | 0,85 | 1450 | 3600 |
4 | Токарно-револьверный станок 1Г340 | 4,1 | 5 | 5 | 0,82 | 0,82 | 1300 | 8000 |
5 | Горизонтально-расточной станок 2636Г | 5,1 | 6 | 6 | 0,85 | 0,85 | 4805 | 32500 |
6 | Горизонтально-расточной станок 2М614 | 8,6 | 9 | 10 | 0,86 | 0,90 | 2505 | 3700 |
7 | Вертикально-сверлильный станок 2Н135 | 10,9 | 11 | 13 | 0,84 | 0,85 | 605 | 1383 |
8 | Радиально-сверлильный станок 2Н55 | 8,6 | 9 | 10 | 0,86 | 0,90 | 3315 | 4700 |
9 | Горизонтально-протяжной станок 7Б35У | 2,4 | 3 | 3 | 0,86 | 0,8 | 2950 | 7500 |
10 | Вертикально-фрезерный станок 6У13П | 3,3 | 4 | 4 | 0,83 | 0,83 | 2300 | 4150 |
11 | Широкоуниверсальный станок 6М322 | 3,3 | 4 | 4 | 0,83 | 0,83 | 2500 | 3250 |
12 | Продольно-фрезерный станок 6Г605 | 2,4 | 3 | 3 | 0,80 | 0,8 | 2330 | 13950 |
13 | Зубофрезерный станок 5К310 | 6,9 | 7 | 8 | 0,86 | 0,88 | 1710 | 3500 |
14 | Зубодолбежный станок 5В12 | 6,9 | 7 | 8 | 0,86 | 0,88 | 820 | 1850 |
15 | Круглошлифовальный станок 3В161 | 4,1 | 5 | 5 | 0,82 | 0,82 | 1500 | 4500 |
1 | 2 | 3 | 4 | 5 | 6 | 7 | 8 | 9 |
16 | Внутришлифовальный станок 3А227 | 4,1 | 5 | 5 | 0,82 | 0,82 | 1650 | 2500 |
17 | Плоскошлифовальный станок 3722 | 3,3 | 4 | 4 | 0,83 | 0,83 | 2290 | 7300 |
18 | Резьбонарезной полуавтомат КТ441 | 8,5 | 9 | 10 | 0,85 | 0,9 | 1286 | 2500 |
19 | Горизонтально-фрезерный станок 6М83Г | 2,4 | 3 | 3 | 0,8 | 0,8 | 1770 | 3350 |
Всего основного оборудования | 106 | 126 | 0,84 | 0,86 |
|
|
|
|
7.1.2 Определение количества вспомогательного оборудования
7.1.2.1 Заточное отделение. Необходимое количество заточных станков в зависимости от общего количества металлорежущих станков для не поточного производства составляет 3…4% (таблица А.4). Принимаем 4 %.
Где Сз.о – станки заточного отделения.
Принимаем Сз.о = 5 шт.
Рассчитанное общее количество универсальных станков для заточки распределяется по типам (таблица А.4).
Принимаем:
-универсально-заточный станок –2 шт.;
-станок для заточки сверл – 1 шт.;
-заточной специализированный для твердо-сплавных резцов – 2 шт.
7.1.2.2 Отделение по ремонту технологической оснастки.
Необходимое количество станков составляет 3,5% от общего числа обслуживаемых основных станков (таблица А.3).
;
где Срто – станки отделения ремонта технологической оснастки.
Срто = 5 шт.
Принимаем по типам станков (таблица А.5)
|
|
-токарно-винторезный станок – 2 шт.;
-универсально-фрезерный станок – 1 шт.;
-вертикально-сверлильный станок – 1 шт.;
-универсально-шлифовальный станок – 1 шт.
7.1.2.3 Отделение по ремонту оборудования.
Количество станков составляет 2,5% от общего числа обслуживаемых станков (таблица А.3)
где Ср.о – станки отделения ремонта оборудования.
Ср.о = 5 шт. при Кз = 0,65.
Принимаем по типам станков (таблица А.6)
- токарно-винторезный станок – 2 шт.;
- вертикально-фрезерный станок – 1 шт.;
- универсально-шлифовальный станок – 1 шт.;
- вертикально-сверлильный станок – 1 шт.
7.1.3 Рабочий состав механического участка и определение его численности.
Общее количество рабочих механосборочного цеха составляет:
а) производственные рабочие;
б) вспомогательные рабочие;
в) ИТР и служащие;
г) уборщики производственных и бытовых помещений.
7.1.3.1 Количество рабочих-станочников определяем исходя из принятого количества станков по формуле
,
где Фо – действительный годовой фонд времени работы единицы оборудования в час при 2-х сменной работе Фо = 4060 (таблица А.1);
Спр – количество принятого производственного оборудования. Спр = 126 станков.
Фр –эффективный годовой фонд времени рабочих в час. Фр = 1840 часов (таблица А.7);
|
|
Км – коэффициент многостаночного обслуживания. Км = 1,3 (таблица А.8);
(Кз·Ки)ср – коэффициенты соответственно загрузки и использования оборудования. При укрупненных расчетах для единичного, мелкосерийного и серийного производства Кз.·Ки = 0,85; (таблица А.2).
чел.
Принимаем Рпр =182 чел.
7.1.3.2 Число слесарей мехучастков принимаем 3-5% от числа станочников. Принимаем 4%.
чел. принимаем 8 чел.
Общее число производственных рабочих по механическим участкам цеха составляет:
чел.
7.1.3.3 Количество вспомогательных рабочих от числа производственных рабочих для среднесерийного производства составляет 20-25% (таблица А.9). Принимаем 22%.
чел. Принимаем 42 чел.
7.1.4 Определение площади механических участков цеха
Площадь механических участков цеха складывается из основной и вспомогательной площади и площади складских помещений цеха.
7.1.4.1 Производственная площадь для основного и вспомогательного оборудования рассчитывается по удельной площади (S уд) одного станка (с учетом проходов, проездов, нормативных расстояний между станками, между станками и колоннами и стенами с учетом размещения инструментальных шкафов, верстаков, контрольных плит, тары с заготовками и деталями, приведенными в таблице А.11.
где S уд – удельная площадь, приходящаяся на 1 станок;
Спр – принятое количество оборудования.
7.1.4.2 Производственная площадь для основного оборудования.
По таблице А.11 нормы удельной площади основного оборудования на 1 станок весом до 10 тн составляет 20 м2, весом 10 … 30 тн – 45 м2.
По принятому количеству основного оборудования (таблица 3) определяем количество станков весом до 1…10 тн – 117 шт; весом 10 … 30 тн – 9 шт.
Тогда общая производственная площадь S равна
где S осн.о – площадь, занятая под основным оборудованием;
Спр.о – принятое количество соответственно основного оборудования, шт.
S уд – удельная площадь.
Производственная площадь на одного слесаря-ремонтника составляет 4м2, а для 8 чел.
;
Тогда производственная площадь мехучастка составляет
7.1.5 Определение площадей вспомогательных отделений механических участков цеха
Площади вспомогательных отделений цеха определяют исходя из удельной площади на один станок S уд (таблица А.11).
7.1.5.1 Заточное отделение (S з.о)
где C з.о – количество станков заточного отделения;
S удз.о – удельная площадь на 1 станок заточного отделения S уд = 12 м2;
7.1.5.2 Отделение по ремонту оборудования (Sр.о)
;
C р.о – количество станков отделения ремонта оборудования;
S уд.р.о – удельная площадь на 1 станок отделения ремонта оборудования.
7.1.5.3 Отделение по ремонту технологической оснастки (S рто)
;
C рто – количество станков отделения ремонта технологической оснастки;
S удрто – удельная площадь на 1 станок отделения ремонта технологической оснастки.
7.1.5.4 Площадь контрольного отделения (Sк.о).
Площадь контрольного отделения составляет 3-5% от площади станочного отделения. Принимаем 3%.
7.1.5.5 Общая площадь вспомогательных площадей равна
7.1.5.6 Общую площадь механического участка определяют как сумму его производственных и вспомогательных площадей.
;
7.1.6 Определение площади для цехового склада материалов и заготовок, готовых изделий
Площадь склада определяем, исходя из необходимости хранения определенного количества запаса металла, заготовок, полуфабрикатов или деталей.
где m – масса соответственно заготовок, материалов, готовых изделий, обрабатываемых в цехе в течение года;
Т – нормативный запас хранения на складе (таблица А.12).
Принимаем Т = 8 суток;
D – число календарных дней в году;
q – средняя грузонапряженность площади склада т/м2 (таблица А.12).
Принимаем q = 3 т/м2;
Ки – коэффициент использования площади склада, учитывающий проходы и проезды; Ки = 0,35 для стеллажных складов.
Определим общий вес расходуемых материалов;
На одно изделие
.
Тогда .
7.1.7 Определение площади инструментально-раздаточной кладовой (ИРК)
Площадь инструментально-раздаточной кладовой определяется по числу обслуживаемых складом рабочих мест. Для расчета размера площади склада служит показатель, который выражает размер площади склада в м2, приходящийся на 1 металлорежущий станок (таблица А.13) обслуживаемого в цехе в 2 смены; для серийного производства этот показатель равен 0,5 м2
В расчет вводим металлообрабатывающие станки всех отделений цеха, в том числе станки вспомогательного отделения цеха
.
шт.
Тогда
Для хранения инструмента одного обслуживающего слесаря принимается еще 0,15 м2.
Площадь склада приспособлений принимается равной 0,3м2 для серийного производства на 1 станок
Общая площадь ИРК равна
Дата добавления: 2019-01-14; просмотров: 162; Мы поможем в написании вашей работы! |
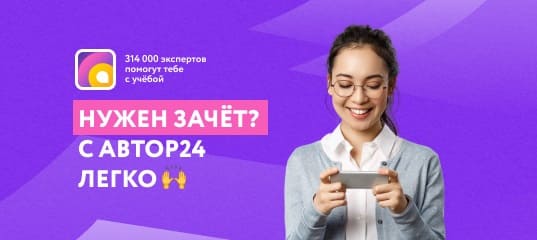
Мы поможем в написании ваших работ!