Принципы создания гибких производственных систем
Поскольку технологические комплексы с применением роботов наиболее широко распространены в промышленности, рассмотрим организационно – технологические основы создания ГПС в машиностроении и приборостроении, на которые приходится большая часть мирового парка роботов [1].
При создании промышленных ГПС необходимо обеспечить:
– сквозную унификацию конструкций, технологических процессов, управляющих программ, плановых групп заготовок и деталей;
– специализацию цехов, участков, линий и рабочих мест под плановые группы деталей;
– подетальное планирование с учетом полной загрузки обрабатывающих участков;
– автоматизацию подготовки и управления ходом производства.
Как отмечалось ранее, наиболее полно эти требования можно реализовать при групповой технологии.
При определении специализации цехов, технологических участков, линий и рабочих мест проводят классификацию и кодирование деталей и технологических процессов. На их основе осуществляют группирование. На первом этапе детали группируются по общности конструктивно – технологических признаков (основа для специализации цехов, участков), на втором – по общности технологических процессов и операций (основа для специализации линий и рабочих мест).
Рассмотрим алгоритм группирования деталей по технологическим процессам. Пусть имеется множество деталей, каждая из которых описывается цепочкой операций. Вначале все детали упорядочиваются по длине цепочки. Самая длинная принимается за основной лидер. Для остальных деталей проверяется возможность включения маршрутов в основной лидер.
|
|
Рис. 5 Объединение лидеров на основе графа – лидера [6]
Наиболее длинная цепочка из оставшихся принимается за второй лидер и т.д. Эти лидеры изображаются в виде графов. В дальнейшем их можно объединить для создания многопредметных поточных линий. На рис. 5 и 6 изображены примеры объединения графов-лидеров.
Так как Г2 Г1, и Г
Г1: Г1 то граф Гг является общим и по нему может быть организован технологический процесс для трех типов деталей (см. рис. 5).
В исходных графах Г} и Г2 (см. рис. 6) удаляются оригинальные вершины (операции) с, е, f, при этом получаются усеченные графы и
. Затем объединяются усеченные графы и восстанавливаются удаленные вершины и связи. Получается общий граф Г.
Рис. 6 Объединение лидеров с введением дополнительных
вершин и связей [6]
В этих графах под вершинами понимаются операции, а под дугами – материальные потоки. Такой подход является ориентировочным. Для уточнения результатов и выбора окончательного варианта технологической линии необходимо моделирование ГПС, что будет рассмотрено в дальнейшем.
|
|
Остановимся на вопросе определения размеров партий деталей в условиях гибкого производства при их группировании методом пакетирования. Сущностью метода является объединение различных типов деталей в «суточный пакет». Критерии для объединения – близость размеров, общность материала.
Критерий целесообразности пакетирования – сравнение затрат времени на обработку деталей в ГПС и на универсальных станках [6]:
(1)
где Тп п , Тнз , T шт –соответственно время подготовки производства, подготовительно – заключительное время, штучное время изготовления детали, индекс 1 относится к универсальным станкам, индекс 2 – к ГПС; п – число деталей в партии.
Если левая часть выражения (1) больше правой, то выгодно использовать ГПС [6]:
(2)
При пакетной обработке с учетом количества наименований деталей в пакете Рпак :
(3)
Пусть, например, ,
ч. Определим минимальное число деталей в партии, при котором целесообразно использовать ГПС без пакетирования и с пакетированием. Получается: по выражению (2.2) n min=7 деталей, по выражению (2.3) – nmin=2 детали.
|
|
Выбор технологического оборудования. Как показано в [4], для ГПС при выборе основного и вспомогательного технологического оборудования может быть применен принцип двухуровневого проектирования. Его сущность состоит в том, что множеству технологических процессов необходимо поставить в соответствие набор единиц оборудования с учетом заданных критериев качества функционирования ГПС. При этом на первом уровне проектирования (виртуальном) рассмотрение осуществляется в терминах абстрактных элементов оборудования, а на втором (физическом) уровне учитываются доступные единицы оборудования с конкретными характеристиками.
Рис. 7 Граф, соответствующий структурно – технологической схеме
обработки i – го типа деталей: индексу отвечает типу
склада (АС), транспортного средства (ТР),
технологического оборудования (ТО) [6]
На виртуальном уровне для каждого типа деталей в соответствии со структурно – технологической схемой его обработки строят графы Г, в вершинах которого находятся обобщенные характеристики операций (складские, транспортные, обрабатывающие), а дуги обозначают направления движения материальных потоков (рис. 8). Множество оборудования К lm является ограниченным из – за конечного числа типови наличных единиц т каждого типа оборудования. Задача выбора оборудования сводится к поиску такого графа из множества К lm , чтобы накрыть все графы Г i . При выборе основного технологического оборудования (ОТО) необходимо сформировать требования, распределить технологические операции по гибким производственным модулям и определить состав ОТО. На основе анализа структурно – технологических схем обработки деталей формируется матрица, устанавливающая для каждой операции набор требований к ОТО, определяющих параметры рабочего пространства, скорость, мощность, подачу, размеры партий деталей и т.п. Далее производят распределение технологических операций по гибким технологическим модулям (ГТМ). При этом в последовательностях обозначений типов оборудования для реализации техмаршрутов обработки отдельных деталей (например Т1,С1,Ф1: токарная – сверлильная – фрезерная; индексы обозначают ряды оборудования) отыскивают повторяющиеся фрагменты, которые целесообразно обрабатывать в общих ГТМ.
|
|
Пусть, например, последовательности обработки трех групп деталей имеют вид:
В связи с наличием общих фрагментов целесообразно обработку вести в ГТМ: ГТМ1: ; ГТМ2:
; ГТМ3:
; ГТМ4:
, т.е. необходимо пять типов ГТМ.
При выборе состава ОТО учитывают функциональное назначение оборудования и трудоемкость обработки деталей. Остановимся на выборе вспомогательного технологического оборудования (ВТО). Наиболее важной частью ВТО для ГПС является автоматизированная транспортно – складская система (АТСС), в которую входят общая транспортная система, система складов и локальные транспортные системы ГПМ. При выборе общей транспортной системы на виртуальном уровне составляется граф (рис. 9), заданный техмаршрутами перемещения материальных ценностей, в вершинах которого находятся гибкие модули (ГСМ – складские, ГКМ – контрольные, ГМО – удаления отходов).
Далее составляется матрица, устанавливающая связь между перемещениями и требованиями к ним, на основе которых выбираются транспортные средства на физическом уровне проектирования.
При выборе системы складов составляется таблица: составляющие материального потока-требования к складам, на основании которой определяются типы складов.
Выбор локальных транспортных систем ГПМ производят на основе графа, аналогичного графу рис. 8, только в его вершинах располагают элементы ГПМ (см. рис. 2) – станки, накопители, системы удаления отходов и т.п. После составления и анализа таблицы «Перемещения – требования к ним» выбирают технические средства (роботы, манипуляторы, толкатели и т.п.).
Наиболее полная классификация роботизированных ГПС приведена в [5] в зависимости от признаков: тип подразделения, вид технологического процесса, компоновка, тип управления и др.
Рассмотрим наиболее типичные структурно-компоновочные схемы роботизированных ГПС для технологических процессов, где роботы применяются на вспомогательных операциях (механообработка, холодная штамповка, кузнечно-штамповочное производство), а также на основных технологических операциях (сборка, сварка, нанесение покрытий). Будем называть гибким роботизированным производственным комплексом (ГРПК) подразделение ГПС (модуль, линия, участок, цех), в котором используются промышленные роботы.
Рис. 8 Граф общей транспортной системы [6]
В случаях, когда используются транспортные роботы с расположением их над оборудованием или оборудование размещается в нескольких уровнях, получается объемная компоновка.
В ГРПК механообработки промышленные роботы выполняют типичные операции установки и снятия деталей в ОТО. В простейших схемах применяется цикловое управление ПР, в более сложных случаях – дискретное позиционное управление. Важной здесь является проблема ориентации деталей. Для ее разрешения используются ориентирующие устройства и адаптивные ПР. Естественно, в таких комплексах используются роботизированные складские, транспортные, контрольно – измерительные и другие комплексы.
Рис. 9 Схема ГРПК (технологической линии) с линейной компоновкой;
ОТО – основное технологическое оборудование; ПР – промышленный робот;
М – магазин выдачи заготовок, приема изделий [6]
Рис. 10 Схема ГРПК (технологического участка) с
замкнутой компоновкой [6]
Рис. 11 Схема ГРПК (технологического участка) с компоновкой
по площади: С – склад; МПР – мобильный промышленный робот;
Т – трасса мобильного ПР [6]
Компоновка оборудования в холодной штамповке требует применения для операций загрузки-разгрузки ОТО более быстродействующих, чем в механообработке, ПР, поскольку цикл работы пресса равен нескольким секундам. Зачастую вместо одного быстродействующего робота применяют два манипулятора (один – на загрузку, другой – на выгрузку) с простым цикловым управлением.
При организации автоматизированного кузнечно – прессового производства возникают по сравнению с холодной штамповкой задачи, связанные с транспортировкой, загрузкой и выгрузкой заготовок, смазкой и обдувкой, штампов, снятием облоя с детали. В этом случае промышленные роботы выполняют функции кузнецов.
Остановимся кратко на компоновке роботизированных комплексов сборки и сварки. При автоматизации процессов сборки структурно – компоновочные схемы зависят как от серийности производства, так и от числа роботов, задействованных в комплексе. В связи с этим создаются как специальные сборочные автоматы в массовом производстве с использованием простейших манипуляторов для выполнения вспомогательных операций, так и сборочные комплексы на базе универсальных и специализированных роботов для выполнения основных операций, наконец – ГПК, в которых все сборочные операции выполняются одним универсальным ПР. На рис. 12 приведена схема компоновки ГРПК сборки катушек индуктивности. Гибкие роботизированные комплексы, получившие применение в сварочном производстве, основаны на реализации точечной, дуговой и электронно – лучевой сварки. Для выполнения точечной сварки используются ПР, у которых рабочими органами являются сварочные клещи. Управление такими роботами – дискретное позиционное. При дуговой сварке обеспечивается непрерывное перемещение электрода по сложной траектории. Управление роботами – адаптивное. Электронно – лучевая сварка требует перемещения электронного пучка либо изменения положения рабочего стола. Управление роботами – адаптивное.
Рис. 12 Схема ГРПК сборки катушек индуктивности:
РС – роторный стол; ПР – промышленный робот; ВБ – вибробункер;
БК – блок контроля; Н – накопитель изделий [6]
На рис. 12 – 14 показаны примеры компоновок ГРПК дуговой сварки. В случае, когда оснастка для сборки и фиксации свариваемого изделия находится на позиционере постоянно, применяются двухпозиционные столы (рис. 12) или два раздельных манипулятора, взаимодействующие с одним ПР (рис. 13).
Если оператор справляется с обслуживанием нескольких роботов, возможна схема компоновки, изображенная на рис. 14.
Дата добавления: 2018-11-24; просмотров: 347; Мы поможем в написании вашей работы! |
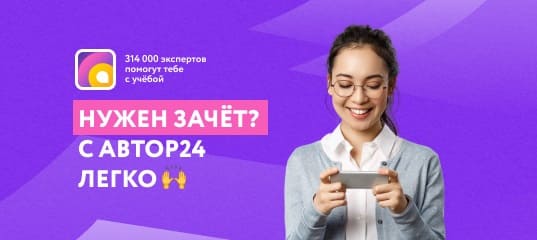
Мы поможем в написании ваших работ!