Компоновочные схемы расположения оборудования и АТС
Рассмотрим основные из разнообразных компоновок оборудования (рисунок 2.8). Параллельное расположение оборудования вдоль трассы обслуживания. Станки могут устанавливаться как с одной, так и с двух сторон по отношению к трассе обслуживания. В общем случае один промышленный робот с двумя рабочими местами размещается перед станком для загрузки заготовок и выгрузки готовых деталей, а другой робот с одним рабочим местом - сзади станка для обслуживания его инструментом. Преимуществом такой компоновки является удобство обслуживания рабочих мест станка любыми транспортными средствами - напольными и подвесными. Однако некоторая растянутость трассы и увеличенная потребность в площадях, повышенная нагрузка на транспортные средства, потребность в их дополнительном количестве указывают на недостатки этой компоновки. Указанная компоновка может быть рекомендована для относительно небольших и средних объемов производства.
Перпендикулярное расположение оборудования вдоль трассы обслуживания. Станки могут устанавливаться как с одной, так и с двух сторон по отношению к трассе обслуживания. Достоинством этой компоновки является компактность планировки и, следовательно, меньшая потребность в производственных площадях, возможность обеспечения рабочих мест с помощью одного транспортного средства. Недостатки указанной планировки - повышенная нагрузка на транспортные средства, наличие дополнительных требований к производственным площадям и сложность организации работы на рабочих местах (рисунок 2.8).
|
|
Расположение трассы обслуживание над оборудованием. Данная компоновка, как и предыдущая, отличается максимальной компактностью, минимальной потребностью в производственных площадях. Но ограничение транспортных средств только подвесным типом, повышенная их загруженность и установка основного оборудования только в один ряд предопределяет использование данной компоновки лишь при малых и средних объемах производства.
Используются и другие виды компоновки, например, угловая и комбинированная.
1 - промышленный робот;
2 - станок с ЧПУ;
3 - транспортное средство;
4 - стол приема транспорта;
5 - стол приема готовых деталей;
6 - стол приема заготовок;
7 - тара для стружки
а) параллельное расположение оборудования вдоль трассы обслуживания; б) перпендикулярное расположение вдоль трассы обслуживания; в) расположение трассы над оборудованием.
Рисунок - 2.8 Схемы компоновки оборудования и трассы обслуживания
В практике используют следующие варианты компоновок АТНС: локальная линейная, групповая линейная, однорядная, групповая линейная многорядная, кольцевая внутренняя или наружная комбинированная (рисунок 2.9).
|
|
а) с локальными линейными транспортными линиями;
б) с линейной многорядной трассой обслуживания;
в) с кольцевой внутренней линией транспорта;
г) с кольцевой наружной линией транспорта;
д) с приводными рольгангами;
е) с конвейером
Рисунок - 2.9 Структурные схемы АТНС
Требования к автоматизированным складам и их характеристики
Компоновочные решения складских систем в общих технологических системах ГПС определяются характеристикой производственных площадей, особенностями номенклатуры хранимых грузов, массой грузопотоков, запасами хранения и оборачиваемостью грузов, объемом соответствующих партий, технологией складских работ, характером выполняемых на складе операций по приему, складированию и выдаче грузов, видом и спецификой работы транспорта по доставке и отправлению их со склада (рисунок 2.10).
Осевое расположение складов. При такой компоновке складов по отношению к линии размещения основного технологического оборудования склад может иметь некоторое боковое смещение относительно этой линии. Такая компоновка проста по исполнению, удобна в эксплуатации и предназначена для небольших объемов производства.
|
|
Перпендикулярное расположение складов. При таком варианте склады могут разметаться симметрично и асимметрично. Прием и выдача грузов осуществляется с разных торцов склада. Применяется такая компоновка для относительно небольших объемов производств.
Угловое расположение складов. Этот вариант является разновидностью компоновки с перпендикулярным расположением складов.
1 - стеллажи; 2 - трансманипулятор; 3 - прием и подготовка грузов к складированию; 4 - подготовка и выдача грузов в производство; 5 - станки; 6 - приемные маты у станков; 7 - подготовка и выдача груза со склада
а) перпендикулярное расположение складов; б) угловое расположение складов; в) сложные компоновки складских систем.
Рисунок - 2.10 Компоновка складов
При создании современных гибких автоматизированных заводов большое значение приобретает разработка систем управления автоматизированными транспортно-складскими системами как предприятия в целом, так и отдельных его составляющих компонентов – цехов, участков, гибких производственных модулей.
Транспортно-накопительная система (ТНС) автоматизированного предприятия, объединенная в единое целое интегрированной системой управления, не только служит местом накопления и хранения грузов, но также организует формирование материальных потоков в технологическом цикле производства и является связующим звеном в выполнении производственного процесса. ТНС на базе средств вычислительной и микропроцессорной техники должна синтезировать автоматизированное производство в единую ГПС.
|
|
Развитие средств вычислительной и микропроцессорной техники позволяет автоматизировать подачу на общезаводской склад материалов, заготовок и комплектующих изделий, поступающих на предприятие от других организаций, затем их подачу на рабочее место и готовой продукции, от рабочего места на общезаводской склад. Появилась реальная возможность создавать не только автоматизированные системы управления (АСУ) складами и транспортом, но и микропроцессорное управление отдельными перекладчиками грузов, автоматическими транспортными тележками и бесконтактными средствами информационного обеспечения ТНС всех уровней.
К системам управления складскими операциями в гибкой производственной системе (ГПС) предъявляются специфические требования, а именно: отсутствие человека-оператора в контуре управления, наличие связи с ЭВМ верхнего уровня, повышенная надежность, модульное построение. Высокая степень автономности должна позволять им функционировать длительный период при потере связи с верхним уровнем.
Специальные требования к автоматизированным складам (АС) для ГПС изготовления ИЭТ обусловлены малыми габаритными размерами и массой изделий, большим числом типономиналов и изделий в партии, ограниченными размерами склада.
Исходя из этих условий АС для ГПС ИЭТ должны иметь при алых габаритах и грузоподъемности большое количество ячеек, рассчитанных на изделия малой массы, обеспечивать значительную скорость перемещения и точность позиционирования.
Исходя из этих требований был разработан автоматический стеллажно-тарный склад АСТС-10.
АСТС-10 имеет модульную структуру и содержит систему управления и размещенные на расстоянии до 300 м от нее складские модули. Принятая структура позволяет изменять состав АС и использовать его элементы в помещениях различной планировки без существенных конструктивных, аппаратных и программных доработок. В состав складского модуля входят два стеллажа на 512 ячеек каждый, один штабелер со стойкой питания, два механизма перемещения тары (МПТ). Стеллажи установлены параллельно на общей раме. Между ними перемещается штабелер, который может выполнять 3 вида операций: перенос тары с МПТ в стеллаж, со стеллажа на МПТ и из одной ячейки стеллажа в другую. Штабелер допускает три направления перемещения: горизонтальное перемещение тележки, вертикальное перемещение каретки и выдвижение устройства перемещения тары (УПТ), укрепленного на каретке. Привод каретки – позиционный, замкнутый по скорости и положению. Привод УПТ – цикловой, управляемый тремя бесконтактными концевыми датчиками.
Взаимодействие АС с другими элементами ГПС осуществляется посредством МПТ, представляющего собой цикловое устройство на два конечных положения. Для ускорения цикла загрузки-разгрузки используются два МПТ, установленных у стеллажей. Изделия транспортируются и хранятся в малогабаритной пластмассовой таре или кассетах.
Основные характеристики АСТС-10.
Максимальное число складских модулей 4
Габаритные размеры, мм 7710х920х3270
Число ячеек в модуле 1024
Максимальное число ячеек склада 4096
Грузоподъемность, кг 10
Размеры ячейки, мм 300х250х250
Точность позиционирования штабелера, мм +2
Цикл загрузки-выгрузки, с 40
Двухуровневая система управления автоматическим складом АСТС-10 (рисунок 2.11) состоит из стойки управления складом (СУС) и устройства управления штабелером (УУШ). Система работает в трех режимах – автоматическом, полуавтоматическом и режиме наладки.
Рисунок 2.11 Структурная схема СУ
Основы построения ГПС
Степень автоматизации производственных процессов определяется уровнем развития техники и технологии, организации производства и управления его стадиями. Как известно [1], тип производства можно установить по коэффициенту закрепления операций Кзо, определяемому для планового периода (например один месяц) как отношение числа операций к числу рабочих мест, на которых они выполняются. Наряду с К30 находит применение коэффициент серийности производства, определяемый как отношение числа видов продукции к числу технологических линий при ее производстве. Для непрерывного производства K 30 = 1, для дискретного К30 > 1. В зависимости от значения этого коэффициента различают следующие типы производства [1 – 3]:
– массовое (К30 =1 – 3);
– крупносерийное (Кю = 3 – 10);
– среднесерийное (К30 =10 – 30);
– мелкосерийное (К30 = 30 – 40);
– единичное (К30 > 40).
В каждом из этих типов имеются свои особенности и ограничения при управлении материальными потоками. При преобразовании продуктов производства в производственной системе можно условно выделить подсистемы: обрабатывающие, хранения и транспортные. Обрабатывающие подсистемы выполняют основные и вспомогательные технологические операции (механообработка, литье, обжиг, запрессовка, сборка, упаковка). Подсистемы хранения накапливают заготовки, полуфабрикаты, изделия, инструмент, оснастку и т.п. Транспортные подсистемы осуществляют перемещение материальных потоков (изделий, инструментов, оснастки, отходов). К транспортным подсистемам относятся роботы, которые производят операции перемещения и манипулирования.
При управлении производственными процессами следует иметь в виду, что в случае непрерывного производства его динамика определяется в первую очередь функционированием обрабатывающих подсистем, вопросы перемещения и складирования материальных продуктов отходят на второй план. В дискретном же производстве особую роль приобретают проблемы организации перемещения материальных потоков, синхронизации работы всех основных и вспомогательных видов оборудования.
Внедрение автоматизации в первую очередь в массовое производство объясняется тем, что затраты на создание специализированного дорогостоящего оборудования оправдывались только при выпуске больших партий изделий. По мере развития науки итехники потребовались расширение номенклатуры выпускаемой продукции, ускорение темпов ее освоения при сокращении циклов жизни изделий и снижении серийности. Организация такого производства привела к необходимости применения универсального оборудования и быстрой его переналадки при переходе к новым видам продукции, обеспечения высокой производительности и требуемого качества изделий. Пришлось также учитывать усложнение управления производством при дефиците высококвалифицированных специалистов. Выход из этого положения был найден в создании гибких производственных систем – адаптивных человеко–машинных комплексов, способных быстро перестраиваться на выпуск новой продукции.
Гибкая автоматизация прошла несколько этапов. Первый этап (1960 – 1970–е г.г.) связан с появлением промышленных роботов, обрабатывающих центров, микропроцессоров, разработкой принципов технологии будущего.
Второй этап (1980 – е г.г.) – это создание гибких модулей, линий, участков.
Третий этап (1990 – е г.г. и далее) – разработка и реализация заводов – автоматов с гибкой технологией и интегрированных гибких производственных комплексов и систем.
Однако необходимо учитывать, что гибкие производственные системы наиболее эффективны при размерах партий деталей (Р) в несколько сотен и при номенклатуре изделий (N) от единиц до сотен (рис. 1).
|
Рис. 1 Области эффективного применения различных видов
автоматизации производства [4]
Модульность. Принцип модульности состоит в использовании при проектировании ГПС отдельных модулей для обработки, транспортировки, складирования, контроля, при создании управляющих комплексов и программного обеспечения.
В соответствии с ГОСТ 26228 – 85. «Гибкие производственные системы. Термины и определения», ГПС — это «совокупность в различных сочетаниях оборудования с ЧПУ, роботизированных технологических комплексов, гибких производственных модулей, отдельных единиц технологического оборудования и систем обеспечения их функционирования в автоматическом режиме в течение заданного интервала времени, обладающая свойством автоматизированной переналадки при производстве изделий произвольной номенклатуры в установленных пределах значений их характеристик».
Наименьшей единицей ГПС является гибкий производственный модуль (ГПМ). ГПМ – это единица технологического оборудования для производства изделий произвольной номенклатуры в установленных пределах значений их характеристик с программным управлением, автономно функционирующая, осуществляющая все функции, связанные с изготовлением, имеющая возможность встраивания в ГПС. В структуру ГПМ могут входить наряду с основным технологическим оборудованием система управления, манипулятор, накопители, система удаления отходов (рис. 2).
Рис. 2 Структура ГПМ [4]
На базе ГПМ создаются гибкие автоматизированные линии (ГАЛ), далее – гибкие автоматизированные участки (ГАУ), гибкие автоматизированные цехи (ГАЦ), гибкие автоматизированные заводы (ГАЗ).
Гибкость. Важнейшим свойством и принципом создания ГПС является гибкость. Это сложная характеристика системы. Она включает техническую, технологическую и организационную составляющие.
При этом следует иметь в виду, что техническая гибкость обеспечивается избыточностью основного оборудования, разнообразием инструментов, универсальностью схватов роботов, зажимных приспособлений и т.п. Ее увеличение возможно за счет модернизации технологического оборудования или его замены.
Технологическая гибкость связана с минимизацией времени и других затрат на перенастройку ГПС. Сложность в увеличении технологической гибкости состоит в организационно – плановом обеспечении последовательности смены инструмента и оснастки при переходе на новые партии изделий. На эту гибкость влияет наличие систем автоматизации подготовки техпроцессов, подготовки управляющих программ, проектирования, разработки и изготовления приспособлений, переналадки оборудования.
Технологическая гибкость находится во взаимосвязи с организационной. Организационную гибкость подразделяют на стратегическую, тактическую и оперативную. Стратегическая гибкость определяется на длительный период: на год или время выпуска продукции, тактическая – на месяц, декаду, оперативная – при формировании сменно – суточных заданий.
При обеспечении гибкости учитываются организационно – технологические подходы при унификации элементов производства. Дискретное производство может быть организовано по технологическому, предметному или смешанному принципам. Разновидностью последнего является групповое производство, сочетающее предметную специализацию подразделений и унифицированную организацию технологических процессов.
При гибкой автоматизации по мере перехода от массового производства к единичному меняются элементы производственной системы в соответствии с табл. 3.
Таблица 3
Зависимость элементов производственной системы от типа производства [1]
Элементы производства | Производство | ||
Массовое | Серийное | Единичное | |
Технология | Единичная | Единичная, групповая | Единичная, групповая |
Структура организации производственного процесса | Поточные линии | Поточные линии, предметно – замкнутые участки | Технологические участки |
При проектировании ГПС необходимо в каждом конкретном случае сопоставлять увеличение гибкости с ростом затрат на создание ГПС.
Системность. Современная ГПС входит важнейшей составной частью в более сложную систему – интегрированный производственный комплекс (ИПК), представляющий собой органическое объединение автоматизированной системы управления производством (АСУП), автоматизированной системы научных исследований (АСНИ), системы автоматизированного проектирования (САПР), автоматизированной системы технологической подготовки производства (АСТПП) и ГПС.
Структура ИПК представлена на рис. 3.
При создании ИПК важно соблюдать следующие моменты: учет места и роли каждой подсистемы в общей структуре системы; иерархию построения системы; внутренние и внешние связи всех подсистем.
Важнейшей особенностью ИПК является интеграция подсистем на основе единого информационного обеспечения всех процессов. В связи с этим возникло понятие интегрированного компьютеризованного производства СА D /САМ/САЕ и МНР (МНР II ) систем. Первое понятие – СА D ( Computer Aided Design ) / САМ ( Computer Aided Manufacturing ) / САЕ ( Computer Aided Engineering ) – обозначало комплекс программных средств компьютерного проектирования, подготовки производства и инженерных расчетов. Второе – MRP – (М aterials Requirement Planning ) – «планирование потребностей в материалах», а позднее М R Р (М anufacturing Recource Planning – управление производственными ресурсами) – стало обозначением комплекса задач управления финансово-хозяйственной деятельностью предприятия.
Рис. 3 Интегрированный производственный комплекс:
СУ – системы управления [4]
К середине 90 – х гг. в XX в. появилось осознание необходимости создания интегрированной информационной системы, поддерживающей весь жизненный цикл изделия [2]. По определению, приведенному в стандарте ISО 2004 – 1, жизненный цикл продукции – это совокупность процессов, выполняемых от момента выявления потребности общества в определенной продукции до момента удовлетворения этой потребности и утилизации продукции. Впервые работы по созданию интегрированных систем, поддерживающих жизненный цикл продукции, были начаты в оборонном комплексе США. Предполагалось, что реализация новой концепции, получившей обозначение CALS (Computer Aided Logistic Support – компьютерная поддержка процесса поставок), позволит сократить затраты на организацию информационного взаимодействия государственных учреждений с частными фирмами в процессах формализации требований, заказа, поставок и эксплуатации военной техники. Доказав свою эффективность, концепция последовательно совершенствовалась, дополнялась и, сохранив существующую аббревиатуру (С ALS), получила более широкую трактовку – Continuous Acquisition and Life Cycle Support – непрерывные поставки и информационная поддержка жизненного цикла продукции.
В период 1990 – 2000 г.г. в мире был выполнен ряд проектов, направленных на апробацию и внедрение принципов CALS в различных отраслях промышленности [3], в частности, в фирмах: Airbus (проектирование и технологическая подготовка производства), Rolls Royce, General Motors и Hughes Aircraft (интеграция разработки и изготовления изделий). В настоящее время в мире действуют более 25национальных организаций, координирующих развитие CALS – технологий. Развитие этой концепции вызвало появление новой формы проектов – «виртуальных предприятий».
Алгоритм системотехнического синтеза ИПК. Исходя из системного подхода к конечной цели проектирования ИПК, заключающейся в выборе технологического оборудования и организации его работы, укрупненный алгоритм системотехнического синтеза ИПК может иметь вид, представленный на рис. 4 [4]. Кратко рассмотрим содержание каждого блока алгоритма. При формировании исходных требований на проектирование ИПК определяются области использования ГПС, ограничения на ресурсы, цель и задачи, входные и выходные параметры. Результатом этой процедуры является техническое задание на разработку ИПК.
Рис. 4 Алгоритм системотехнического синтеза ИПК
Разработка организационной структуры и производственного процесса чаще всего должны вестись параллельно. Организационная структура определяет состав подсистем и взаимодействие их между собой. При ее создании учитывают как новые необходимые подразделения, обеспечивающие автоматизацию производства, так и уже имеющиеся на производстве, требующие модернизации. Разработка производственного процесса осуществляется на основе анализа возможной номенклатуры изделий, определения основных характеристик технологии их обработки, типов оборудования, оснастки, инструмента и т.п. Результаты этих двух процедур служат основанием для построения функциональной структуры ИПК.
Функциональная структура представляет собой схему материальных и информационных потоков в ИПК. При этом выделяются уровни управления и взаимодействия между ними. Результатом этого этапа является описание параметров материальных и информационных потоков для всех элементов схемы ИПК.
Анализ этих потоков дает возможность приступить к разработке информационной и технологической структуры, а также алгоритмической модели ИПК. При создании алгоритмической модели описывают движение материальных и информационных потоков на формализованных языках, составляют расписание работы оборудования, разрабатывают планы оперативно – календарного планирования и управления, алгоритмы диспетчирования и управления оборудованием.
При реализации процедур выбора оборудования ИПК широко используют моделирование для оценки различных вариантов оборудования с учетом его технических, экономических и других показателей.
При разработке программного обеспечения для всех подсистем ИПК используют модульный принцип и требования концепции CALS к общности информационных ресурсов на основе Internet – технологий.
Наконец, этап оценки эффективности необходим для сопоставления соответствия технико – экономических показателей созданного ИПК (ГПС) исходным требованиям на проектирование.
Рассмотренный алгоритм является приближенным, поскольку некоторые процедуры связаны с другими и последовательность их осуществления может изменяться.
Реализацию проекта по созданию ИПК (ГПС), включающего этапы: техническое задание, технический проект, рабочие документы, изготовление, монтаж и внедрение, можно представить в виде сходящейся спирали. На начальном этапе составляются укрупненные структуры ИПК в нескольких вариантах. По мере продвижения к окончанию проектирования отбрасываются ненужные решения с учетом соответствующих критериев.
В дальнейшем будут более подробно рассмотрены организационно-технологические основы проектирования ГПС, модели материальных потоков и алгоритмы планирования и управления производством.
Дата добавления: 2018-11-24; просмотров: 573; Мы поможем в написании вашей работы! |
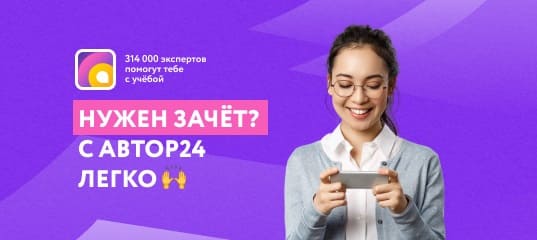
Мы поможем в написании ваших работ!