Практическая работа № 4 (2 часа)
ИЗУЧЕНИЕ КОНСТРУКЦИИ И ПРИНЦИПА ДЕЙСТВИЯ
КОЛОДОЧНЫХ ТОРМОЗОВ
Цель работы
Изучение конструкции и принципа действия колодочных тормозов; определение величин, характеризующих эффективность работы тормозных устройств.
Формируемые компетенции
ПК-4: готовность к разработке проектной и технологической документации по ремонту, модернизации и модификации ТиТТМ различного назначения и ТО, разработке проектной документации по строительству и реконструкции транспортных предприятий, с использованием методов расчетного обоснования, в том числе с использованием универсальных и специализированных программно-вычислительных комплексов и систем автоматизированного проектирования.
ПК-31: готовность к использованию знания рабочих процессов, принципов и особенностей работы транспортных и ТиТТМ отрасли и применяемого при технической эксплуатации и сервисном обслуживании оборудования.
ПК-32: готовность к использованию знания организационно-правовых основ управленческой и предпринимательской деятельности.
Теоретическая часть
Все механизмы, входящие в состав грузоподъемных машин (ГПМ), снабжают надежными тормозными устройствами: в механизме подъема они обеспечивают остановку и удержание груза в подвешенном состоянии с заданным коэффициентом запаса торможения, а в механизмах передвижения и поворота – торможение до полной остановки при заданной длине тормозного пути. Применение тормозов в подъемно-транспортных машинах гарантирует безопасность работы этих машин и повышает их производительность.
|
|
Повышение интенсивности работы ГПМ может быть достигнуто за счет снижения длительности периода торможения. Однако резкое торможение приводит к высоким динамическим нагрузкам, вызывающим потерю устойчивости, повышенный износ муфт, подшипников, ходовых и зубчатых колес, нарушению соединений и другим негативным явлениям.
Тормозной шкив рекомендуется устанавливать на быстроходном валу механизма, где действует наименьший крутящий момент и, следовательно, требуется небольшой тормозной момент. В качестве тормозного шкива может использоваться одна из полумуфт, соединяющих двигатель с редуктором. Если в механизме применена муфта с упругими элементами (втулочно-пальцевая, пружинная и т. п.), то в качестве тормозного шкива следует использовать ту полумуфту, которая находится на валу редуктора.
На рисунке 4.1 показана схема и общий вид механизма подъема (лебедки), в состав которого входит электродвигатель 1, колодочный тормоз 2, двухступенчатый цилиндрический редуктор 3 и барабан 4, на который наматывается канат 5.
|
|
![]() | ![]() |
Рисунок 4.1 – Схема и общий вид лебедки
Классификация тормозных устройств: в подъемно-транспортных машинах тормоза классифицируются по следующим признакам:
– в зависимости от конструктивного исполнения рабочих элементов: колодочные – тормоза с рабочим элементом в виде колодки, трущейся по наружной или внутренней поверхности тормозного барабана (шкива); ленточные – с рабочим элементом в виде гибкой ленты, трущейся по тормозному барабану; дисковые – с рабочим элементом в виде целого кольцевого диска или отдельных сегментных колодок; конические – устройства с рабочим элементом в виде конуса;
– по принципу действия: автоматические тормоза (с электромагнитным, электрогидравлическим или электромеханическим приводом, а также замыкаемые весом транспортируемого груза и т.п.), в которых торможение выполняется независимо от воли обслуживающего персонала и происходит одновременно с отключением двигателя механизма, на котором установлен тормоз; управляемые тормоза, замыкание или размыкание которых производится обслуживающим персоналом при воздействии на орган управления;
– по назначению: стопорные тормоза, производящие остановку механизма; спускные тормоза и регуляторы скорости, ограничивающие скорость движения в определенных пределах и действующие в течение всего периода работы соответствующего механизма;
|
|
– по характеру действия силы, управляющей тормозом: нормально замкнутые тормоза, в которых замыкание (прижатие рабочего элемента к тормозному барабану или диску) создается постоянно действующей силой (пружины, весом специального замыкающего груза и т. п.), а размыкание – одновременно с включением привода механизма за счет силы управления тормозом (при выключении привода тормоз автоматически замыкается); нормально разомкнутые тормоза, в которых рабочий элемент не соприкасается с тормозным барабаном (диском), а замыкание происходит при приложении силы управления тормозом; комбинированные тормоза, работающие в нормальных условиях как нормально разомкнутые тормоза, а в аварийных условиях – как тормоза, нормально замкнутые действием внешней замыкающей силы.
– основные требования, предъявляемые к тормозам: достаточный тормозной момент; быстрое замыкание и размыкание; прочность и долговечность элементов тормоза; простота конструкции; удобство осмотра, регулирования и замены износившихся деталей; надежность работы; минимальный износ трущихся элементов; минимальные габариты и масса; ограниченная температура на поверхности трения, не превышающая предельную температуру для применяемого фрикционного материала.
|
|
Колодочные тормоза. В подъемно-транспортных машинах находит применение большое число разнообразных конструкций колодочных тормозов, состоящих из рычагов и двух колодок, диаметрально расположенных относительно тормозного шкива и различающихся в основном схемой рычажной системы. Наиболее широкое применение получили нормально-замкнутые двухколодочные тормоза с электромагнитами переменного тока типа ТКТ (рисунок 4.2).
Этот тормоз состоит из двух рычагов 2, 5 с шарнирно закрепленными на них тормозными колодками 1 и 3. Замыкание тормоза осуществляется усилием, которое создается основнойпружиной сжатия 11, установленной в скобе 12 над тормозным шкивом 17 и прижимающей к нему колодки 1 и 3. Левый конец пружины воздействует на левую часть скобы, связанную через рычаг 5 с правой колодкой 3; в свою очередь правый конец пружины воздействует через контргайку 8 и гайку 9 на шток 10. Гайка 14 передает усилие сжатой пружины от штока на левый рычаг 2, т. е. на левую колодку. Для нормальной работы тормоза обязательно наличие зазора между правым рычагом 5 и гайкой 7.
Размыканиетормоза происходит при подаче электрической энергии в обмотки электромагнита 4. Якорь 18 притягивается магнитным полем магнита и своим выступом надавливает на правый хвостовик штока 10. Основная пружина 11 при этом сжимается, а отход рычагов 2, 5 с колодками 1, 3 от тормозного шкива 17 обеспечивает вспомогательная сжатая пружина 13 и момент от силы тяжести электромагнита 4. Равномерность отхода обеих колодок от шкива достигается установкой винта 6. Для регулирования степени сжатия основнойпружины на штоке 10 тормоза установлены гайка 9 и контргайка 8.
Рисунок 4.2 – Двухколодочный тормоз типа ТКТ:
1 – левая тормозная колодка с накладкой; 2 – левый рычаг;
3 – правая тормозная колодка с накладкой; 4 – электромагнит;
5 – правый рычаг; 6 – регулировочный винт; 7–9, 14 – гайки; 10 – шток;
11 – основная пружина; 12 – скоба; 13 – вспомогательная пружина;
14 – гайка для регулировки зазора; 15 – указатель; 16 – шкала силы сжатия пружины; 17 – тормозной шкив; 18 – якорь; D – диаметр тормозного шкива;
l, l1 – длины плеч рычагов; α – угол обхвата шкива колодкой (α = 70°)
Для размыкания тормоза без включения электромагнита, что необходимо при замене фрикционных накладок, предусмотрена гайка 7, отводя которую вручную по резьбе на штоке 10 до упора в рычаг 5, производят перемещение штока, приводящее к дополнительному сжатию основной пружины 11 и отходу колодки от шкива. Для регулирования зазора между шкивом и колодкой и удержания рычага 2 служит гайка 14. Указатель 15 и шкала 16 предназначены для установки степени сжатия пружины на определенное усилие.
Регулировка тормоза.Процесс регулировки тормоза заключается:
– в установлении необходимого усилия в основной пружине, создающего заданный тормозной момент;
– в создании оптимального зазора между колодками и шкивом;
– в достижении равномерного отхода колодок от шкива.
1. Регулирование (осадку) пружины осуществляют вращением гаек 8 и 9 с помощью ключа при удержании штока 10 за квадратный хвостовик до тех пор, пока указатель 15, закрепленный на пружине, не совпадет с необходимым делением на шкале 16.
2. Регулирование величины зазора между колодками и шкивом производится вращением гайки 14, при помощи которой вначале освобождаются колодки, затем между колодками и шкивом закладываются пластинки или щуп толщиной, равной величине суммарного зазора на обе колодки, и прижимают колодки к пластинкам. Отвинчивая гайку 7 до упора в рычаг 5, отжать колодки и извлечь закладки, а гайку 7 возвратить в исходное положение.
3. Регулирование равномерности зазора между колодками и шкивом осуществить винтом 6, вращением которого добиваются равного, симметричного отхода колодок, а контроль производят щупом или калиброванной пластинкой.
На рисунке 4.3 показан общий вид колодочного тормоза.
Рисунок 4.3 – Общий вид колодочного тормоза ТКТ-100
Параметры колодочных тормозов всех типов стандартизированы. В таблицах 4.1 и 4.2 приведены основные геометрические параметры и допустимые значения тормозного момента для тормозов типа ТКТ.
Таблица 4.1 – Геометрические параметры тормозов типа ТКТ
Размеры, мм | ТКТ-100 | ТКТ-200/100 | ТКТ-200 | ТКТ-200(300) | ТКТ-300 |
D | 100 | 200 | 200 | 300 | 300 |
B | 70 | 90 | 90 | 140 | 14 |
l | 200 | 340 | 340 | 480 | 480 |
l1 | 100 | 170 | 170 | 240 | 240 |
Таблица 4.2 – Допустимый тормозной момент для тормозов типа ТКТ
Тип тормоза | Допустимый тормозной момент [T Т], Н·м, при ПВ, % | ||
25 | 40 | 100 | |
ТКТ-100 | 20 | 20 | 11 |
ТКТ-200/100 | 40 | 40 | 22 |
ТКТ-200 | 160 | 160 | 80 |
ТКТ-200/300 | 240 | 240 | 120 |
ТКТ-300 | 500 | 500 | 120 |
Проверочный расчет колодочного тормоза. Тормозной момент, создаваемый двухколодочным тормозом, равен сумме тормозных моментов, развиваемых каждой колодкой.
В современных конструкциях тормозов для устранения сил, изгибающих тормозной вал, стремятся использовать тормоза с прямыми рычагами (см. рисунок 4.2). При этом тормозные моменты, создаваемые каждой колодкой, одинаковы и не зависят от направления вращения тормозного шкива. Общий тормозной момент двухколодочного тормоза при прямых рычагах рассчитывается по выражению
![]() | (4.1) |
где f – коэффициент трения между накладкой колодки и тормозным шкивом (см. таблицу 4.3); F з – сила, замыкающая тормоз, Н; D – диаметр тормозного шкива, мм; l1, l – длины плеч рычагов, мм (см. рисунок 4.2), мм; η – КПД рычажной системы тормоза, равный 0,90…0,95 и учитывающий потери на трение в шарнирах рычажной системы (большие значения соответствуют шарнирам, имеющим смазку).
Давление между шкивом и колодкой тормоза должно удовлетворять условию
![]() | (4.2) |
где р – удельное давление между шкивом и колодкой, Н/мм2; А к – площадь рабочей поверхности одной тормозной колодки, мм2, вычисляемая по формуле
![]() | (4.3) |
где α – угол обхвата шкива одной колодкой, равный 70°; В – ширина тормозной колодки, мм; [р] – допускаемое удельное давление, Н/мм2, принимаемое по таблице 4.3.
Таблица 4.3 – Допускаемое давление [р] и коэффициент трения
В колодочных тормозах
Материалы трущихся поверхностей | f | [р], МПа |
Чугун и сталь по чугуну | 0,15 | 1,5 |
Сталь по стали | 0,20 | 0,2 |
Тормозная асбестовая накладка по чугуну и стали | 0,35 | 0,3 |
Кроме указанного, следует проверить колодки тормоза на нагрев по удельной мощности трения:
![]() | (4.4) |
где v 0 – расчетная окружная скорость на ободе шкива, м/с, определяемая по формуле
![]() | (4.5) |
где v – действительная окружная скорость на ободе шкива, м/с; с 0 – коэффициент безопасности, равный 1,1…1,2; [А] – допускаемое значение удельной мощности, принимаемое в пределах 1,5…2,0 МН/(м·с).
Действительная окружная скорость на ободе шкива рассчитывается из соотношения
![]() | (4.6) |
где n – частота вращения тормозного шкива, мин-1.
Дата добавления: 2018-10-27; просмотров: 854; Мы поможем в написании вашей работы! |
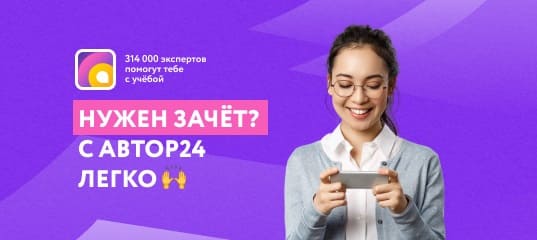
Мы поможем в написании ваших работ!