Основные конструкционные материалы и их выбор
При выборе материала для изготовления оборудования должны учитываться следующие важные показатели:
- прочность;
- термостойкость;
- коррозионная стойкость;
- физические свойства (плотность, теплоемкость, теплопроводность);
- технологические характеристики;
- структура;
- стоимость.
Все перечисленные характеристики материала неразрывно связаны между собой и почти все (кроме стоимости) зависят от условий, в которых находится материал. Например:
· при изменении температуры изменяются коррозионная стойкость, обрабатываемость;
· при увеличении чистоты поверхности при механической обработке улучшается коррозионная стойкость;
· при изменении структуры материала термической обработкой изменяется коррозионная стойкость.
Поэтому, при выборе материала в процессе конструировании машин и оборудования необходимо уточнение рабочих условий (температуры, давления, характер нагрузки, состав и свойства среды, контактирующей с материалом).
Однако во многих случаях свойства материала могут вступать в противоречие друг с другом. Например:
· химически стойкий материал может оказаться недостаточно прочным или термостойким;
· прочный материал может оказаться хрупким, обладать плохой обрабатываемостью;
· прочный и химически стойкий материал может оказаться слишком дорогим.
Следует отметить, что такой показатель, как стоимость, не в полной мере характеризует материал с точки зрения экономической целесообразности его применения. Например:
|
|
· дорогой, но более прочный материал может оказаться выгоднее дешевого из-за возможности изготовления более тонкостенных и легких изделий и большей их долговечности;
· стоимость обработки дешевого материала может оказаться чрезмерно высокой, что готовое изделие получается слишком дорогим (абсорбционные гранитные башни, несмотря на низкую стоимость гранита в сравнении со сталью, обходятся дороже стальных из-за дороговизны обработки гранита).
Металлы и сплавы
Чугуны и стали
Сплавы железа с углеродом – чугуны и стали являются самыми распространенными материалами для изготовления машин и оборудования. По весу, на их долю приходится около 85-90% всего оборудования и около 50% - из чугуна.
Цветные металлы
Наиболее широко распространены для изготовления оборудования: алюминий, медь, никель, титан, тантал.
Для всех цветных металлов характерна высокая коррозионная стойкость, причем наличие примесей ее снижает, но повышает механическую прочность.
Прочность цветных металлов повышают наклепом и гартовкой (холодная обработка), при этом снижается пластичность.
|
|
Пластические свойства повышают отжигом.
Алюминий. Выпускается всего 7 марок в зависимости от чистоты. Наиболее распространены две:
АОО – 99,7 % Al
АО – 99,6 % Al
Химическая и коррозионная стойкость алюминия объясняется способностью образовывать защитную пленку из окислов.
Положительные свойства Al:
- большая теплопроводность;
- малая плотность;
- высокая пластичность;
- устойчив к воздействию азотной, фосфорной, уксусной кислот, сухого хлора и хлористого водорода, паров серы и сернистых соединений.
Отрицательные свойства Al:
- плохие литейные свойства;
- плохая обрабатываемость резанием;
- малая прочность;
- Образование защитной пленки затрудняет пайку и сварку алюминия, при этом пайка и сварка снижают коррозионную стойкость.
Медь. Выпускается всего 5 марок в зависимости от чистоты. Применяются две:
М2 – 99,7 % Cu
М3 – 99,5 % Cu
Положительные свойства Cu :
- высокая электропроводность;
- повышение прочности при низких температурах;
- высокая пластичность;
- устойчива против щелочей.
Отрицательные свойства Cu :
- не обладает стойкостью против большинства кислот и солей;
- разрушается под действием аммиака (NH3), углекислого газа (СО2), сероводорода (SO2), паров серы, сернистого ангидрида (H2S)
|
|
- посредственные литейные свойства;
- плохая обрабатываемость резанием.
Никель. Выпускается 5 марок. Применяется марка Н0 – 99,9 % Ni.
Положительные свойства Ni:
- высокая прочность;
- высокая термостойкость;
- высокая коррозионная стойкость;
- хорошая обрабатываемость и литейные свойства.
Титан.
Положительные свойства Ti:
- высокая коррозионная и химическая стойкость;
- малая плотность (в 2 раза меньше чем у стали);
- хорошая обрабатываемость и литейные свойства;
- при температуре > 200oC способен поглощать газы;
Отрицательные свойства Ti:
- не стоек против серной кислоты (H2SO4);
- дороже в 8-10 раз высоколегированной стали.
Сплавы на основе цветных металлов
Применяются в основном для частей машин, подверженных истиранию: подшипники, шестерни).
Латуни – сплав меди с цинком.
При содержании цинка до 20% сплавы называются томпаками; при содержании Zn 20-55% - латунями.
Обозначение: Л68 (68% меди, остальное – цинк).
ЛН 65-5 (65% меди, 5% никеля, остальное – цинк).
Бронзы – сплав меди с оловом, кремнием, марганцем, бериллием.
Бр.ОЦ 8-4 – оловянистая бронза (8% олова, 4% цинка, остальное – медь).
Бр.ОС 8-12 – свинцовистая бронза (8% олова, 12% свинца, остальное – медь)
|
|
Бр. ОФ 10-1 – фосфоритная бронза (10% олова, 1% фосфора, остальное – медь)
Бр. АЖ 9-4 – алюминиево-железная бронза (9% алюминия, 4% железа)
Бр. АЖН 10-4-4 – алюминиево-железо-никелевая бронза
Бр. КМц 3-1 – кремнистая бронза (3% кремния, 1% марганца)
Баббиты – сплавы на основе олова (Sn) или свинца (Pb)с добавлением 8-16 % сурьмы (Sb), < 6 % меди (С u), < 1% натрия или калия.
Припои – служат для соединения металлических изделий.
Мягкие припои (t плавления 183-280ОС) – сплав олова с цинком:
ПОС-40 (припой оловянисто-свинцовый с 40 % олова); ПОС-30
Серебряные припои (t плавления 740-830ОС)
ПСр-12 (12 % серебра, 40 % меди, остальное – цинк); ПСр-25; ПСР-45
Твердые припои (t плавления 850-885ОС)
ПМЦ48 (припой медноцинковый с 48 % меди, остальное – цинк); ПМЦ54.
Неметаллические материалы
Неорганические материалы
Горные породы
Граниты и андезиты. Применяют для изготовления абсорбционных башен, резервуаров.
Асбест. Применяют для изготовления огнестойких, кислотоупорных прокладок.
Органические материалы
Дерево
Используется главным образом древесина хвойных пород – сосны, ели, лиственницы. Применяют для изготовления простейших аппаратов, лопастей вентиляторов для аэродинамических испытаний.
Резины
Резина – продукт, получаемый в результате термической обработки (вулканизации) натурального или синтетического каучука с серой.
при введении в каучук 2-4 5 серы – мягкая резина;
при введении в каучук 25-40 % серы – твердая резина или эбонит.
Тепловая стойкость резин невысокая – до 80оС. Специальные теплостойкие силиконовые резины выдерживают до 300оС.
Под действием света мягкая резина теряет эластичные свойства и растрескивается.
Сырая листовая резина служит для гуммирования аппаратов и трубопроводов.
Гуммирование – покрытие внутренних поверхностей защитным слоем резины для предохранения от действия коррозии и эрозии.
Эбонит применяется как конструкционный материал для изготовления небольших аппаратов и деталей (почти полностью вытеснен пластмассами).
Пластические массы
Обладают высокой коррозионной стойкостью и достаточно большой прочностью, малым удельным весом. С этой точки зрения они являются прекрасными заменителями дорогих цветных металлов и сплавов.
Пластические массы представляют собой органические высокомолекулярные соединения естественного или искусственного происхождения. Во время изготовления к ним добавляют наполнители, пластификаторы, красители для придания необходимых свойств – прочности, эластичности, цвета, температуры размягчения.
Все пластические массы делятся на две группы:
- Термопласты характеризуются способностью размягчаться при нагревании и снова отвердевать при последующем охлаждении, причем этот процесс можно многократно повторять.
- Реактопласты во время нагревания сначала нагреваются и плавятся, а при дальнейшем нагреве до определенной температуры необратимо затвердевают и становятся нерастворимыми.
Фенопласты. Представляет собой фенолформальдегидную смолу. Относится к реактопластам. Необратимо отвердевает при t=120-170оС.
В зависимости от наполнителя фенопласты различаются на:
Фаолит – фенопласт с асбестом. Изготавливаются емкости, колонны, насосы, трубы.
Графолит – фенопласт с графитом, пропитанным бакелитовым лаком. Применяется для изготовления теплообменных поверхностей.
Текстолит (стеклотекстолит) – листы хлопчатобумажной или стеклянной ткани, пропитанные фенолформальдегидной смолой, прессованные при t=110оС и Р=12 МПа. Применяется для изготовления деталей, несущих механические нагрузки. Коррозионная стойкость невысокая.
Асбовинил. Получается путем смешивания лака этинол с асбестом. Относится к реактопластам. Необратимо отвердевает при t=40-130оС. Используется для изготовления труб, для футеровки аппаратов. По свойствам близок к фаолиту.
Винипласт. Получается в процессе полимеризации хлорзамещенных производных этилена. Относится к термопластам. Применяется для изготовления аппаратов и их футеровки. Не применяется при высоких давлениях из-за хрупкости, особенно при низких температурах.
Акрипласт (плексиглас, органическое стекло). Получается в результате полимеризации метилового эфира метакриловой кислоты. Относится к термопластам. Используется для изготовления прозрачных аппаратов, работающих при комнатных температурах и для смотровых стекол. Размягчается при t=100-120оС.
Стиропласт (полистирол). Получается в результате полимеризации стирола. Относится к термопластам. Применяется для защитного покрытия стенок аппаратуры методом напыления на нагретую поверхность. Является хорошим теплоизолятором.
Этиленопласт (полиэтилен). Получается в результате полимеризации газа этилена в присутствии катализатора. Относится к термопластам. Применяется для футеровки аппаратов.
Стеклопластики. Получаются в результате полимеризации полиэфирных смол, усиленных стеклянным волокном. Полимеризация осуществляется при комнатных температурах при небольшом подогреве и может быть проведена без давления. Изготавливаются аппараты большого размера.
Эпокси-смолы. Относятся к реактопластам. Применяются для смеси с другими пластиками для повышения их прочности и химической стойкости.
Фторопласт. Получается полимеризацией тетрафторэтилена. Диапазон рабочих температур –200-+250оС. По химической стойкости превосходит все пластмассы и металлы. Изделия из фторопласта получают спеканием порошка при t=360-380оС в плотную белую массу. Применяют для изготовления труб, прокладок, различные детали, обкладочные листы.
Лекция № 7
Безмоментная теория оболочек вращения.
Оболочка – тело, ограниченное двумя параллельными поверхностями, причем одно из измерений которого (толщина) значительно меньше двух других.
Срединная поверхность – геометрическое место точек, равноотстоящих от внешней и внутренней поверхностей оболочки.
Оболочка вращения (симметричная оболочка) – оболочка, срединная поверхность которой образована вращением какой-либо плоской линии вокруг оси, лежащей в ее плоскости. Для таких оболочек действующая нагрузка также считается симметричной, т.е. не изменяется по дуге окружности.
При прочностных расчетах рассматривают главные сечения оболочки: меридиональное и перпендикулярное меридиану. Этим сечениям соответствуют два главных радиуса кривизны оболочки: R1 – радиус кривизны меридиана в данной точке и R2 – радиус кривизны сечения, перпендикулярного меридиану. Радиусы R1 и R2 являются функцией угла q между нормалью к срединной поверхности и осью симметрии.
Теория расчета, основанная на предположении равномерного распределения напряжений по толщине стенки, называется безмоментной или мембранной теорией оболочек. При таком предположении отсутствует изгиб стенки оболочки.
Рассмотрим тонкостенную оболочку вращения произвольной формы толщиной стенки s, нагруженную внутренним давлением Р.
Выделим в стенке бесконечно малый элемент, ограниченный двумя меридиональными сечениями, расположенными под углом d j и двумя сечениями, перпендикулярными к мередиану, расположенными под углом d q (часть угла q).
Примем следующие допущения:
- прямые, перпендикулярные к срединной поверхности до деформации, остаются такими же и после деформации;
- в плоскостях, параллельных срединной поверхности, нормальные напряжения s r (радиальные) незначительны и ими можно пренебречь;
- напряжения в оболочке постоянны по толщине стенки.
На гранях выделенного элемента возникают меридианальное s m и тангенциальное (окружное) s t напряжения, вектор которых направлен по нормали к соответствующей грани.
Т.к. напряжения равномерно распределены по толщине стенки, это позволяет легко определить силы, приложенные к граням.
Нормальные силы U, расположенные в плоскости кривизны меридиана:
. (1)
Нормальные силы T, расположенные во второй плоскости кривизны
. (2)
К выделенному элементу приложена также внешняя нагрузка от давления на стенку, представляющая собой силу, направленную по нормали к срединной поверхности выделенного элемента:
. (3)
Под действием этих сил элемент находится в равновесии. Для составления уравнения равновесия спроецируем указанные силы на направление нормали к выделенному элементу.
Длина дуги меридиана:
Длина дуги кольца:
Заменяя ввиду малости синусы их аргументами и пренебрегая бесконечно малыми членами второго порядка, получим
/ :
. – уравнение Лапласа (4)
В уравнении Лапласа содержится два неизвестных s t и s m . Поэтому необходимо еще одно уравнение. Для этого рассмотрим условие равновесия зоны оболочки, отсеченной нормальным коническим сечением.
Просуммируем по контуру меридиональную силу U:
.
Эта сила должна быть равна силе газового давления на оболочку:
Запишем условие равновесия в проекции сил на ось вращения оболочки:
,
учитывая, что из-за малой толщины стенки R ср » r , из уравнения равновесия найдем меридиональное напряжение:
,
Из рисунка r = R 2 × sin q , тогда получим
. (5)
Уравнения (4) и (5) являются основными уравнениями безмоментной теории оболочек, исходя из которых, получают расчетные зависимости для определения главных напряжений в оболочках любой формы, при соответствующих значениях главных радиусов кривизны.
Применим формулы (4) и (5) для наиболее часто применяющихся форм оболочек.
Сферическая оболочка .
(6)
Из формулы (6) можно получить формулы для вычисления толщины стенки или допускаемого давления [Р] c учетом условия прочности.
Цилиндрическая оболочка.
,
.
Из уравнения (4)
.
Из уравнения (5)
.
Т.е. тангенциальные напряжения в цилиндрической оболочке в 2 раза больше меридиональных, поэтому они принимаются за расчетные напряжения.
Коническая оболочка.
,
.
Из уравнения (5)
Из уравнения (4)
.
Т.е. в конической оболочке за расчетные принимаются также тангенциальные напряжения. Причем напряжения в конической оболочке увеличиваются к основанию.
Эллиптическая оболочка (эллипсоид вращения).
Обозначим a и b – полуоси эллипса. Главные радиусы кривизны имеют максимальное значение в вершине купола и равны:
,
тогда
Лекция № 8
Дата добавления: 2018-09-23; просмотров: 1829; Мы поможем в написании вашей работы! |
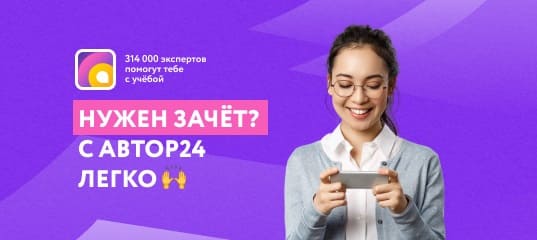
Мы поможем в написании ваших работ!