Расчет режима и закалка стекла
Закалке подвергают пластины листового стекла толщиной не менее 6 мм размером 100×25 мм. Для испытания отбирают образцы без видимых пороков стекла (пузыри, свили и др.), не имеющие трещин и царапин, хорошо отожженные. Торцевые грани необходимо отшлифовать. Количество образцов должно быть не менее 10.
По химическому составу стекла определяют температуру закалки.
Пример. Определить температуру закалки листового стекла следующего химического состава, мас. %: 72,2 SiO2; 1,5 Al2O3; 9,1 CaO; 3,5 MgO; 13,7 Na2O.
Для расчета используют метод Охотина. T11 = 579 ; T12 = 557. Применяя метод экстраполяции, находят температуру стеклования Т12,3 = 550,4 ≈ 550°С. Температура закалки составляет 550 + 80 = 630°С. Можно определить температуру закалки как соответствующую lgη = 9 Па∙с. Согласно расчету Т9 = 636°С. Оба способа расчета дают весьма близкие значения температуры закалки.
Время закалки (τз) определяют в зависимости от толщины (δ) листового стекла: τз = (35…50)δ. Например, для листа толщиной 6 мм время закалки составит 210…300 с или 3,5…5 мин.
Механическая обработка стекла
К механической обработке стекла относятся процессы шлифовки и полировки, нанесение алмазной грани, резки, фацетирования, токарной обработки, сверления, пескоструйной обработки.
Шлифовка и полировка являются наиболее важными операциями холодной обработки стекла. Шлифовка – это процесс, при котором стекло получает определенную форму, а полировка – процесс, при котором изделие получает окончательное качество поверхности (блеск, прозрачность).
|
|
Основная часть формовочного процесса заключается в грубой шлифовке (обдирке), которая придает стеклу форму, мало отличающуюся от окончательной формы изделия.
Решающим критерием грубой шлифовки является скорость снятия слоя стекла, причем шероховатость поверхности при этом не принимается во внимание; она учитывается при последующей операции – тонкой шлифовке.
Процесс тонкой шлифовки состоит из одной или нескольких стадий для создания поверхности с минимальной шероховатостью. Тонкая шлифовка является, таким образом, переходной ступенью от грубой шлифовки к полировке.
Полированная поверхность имеет глубину неровностей, меньше длины волны видимого света. Она прозрачна, не рассеивает световых лучей и обладает совершенным блеском.
Шлифовка происходит при взаимном трении стекла и абразивного материала, чаще всего в присутствии воды. Двигающиеся острые зерна абразива разрушают поверхность стекла и создают на ней сеть царапин и трещин. При продолжении процесса из разрушенного слоя выламываются мелкие кусочки стекла, что увеличивает площадь обрабатываемой поверхности и снижает массу шлифуемого изделия.
|
|
Шлифовка производится водной суспензией абразивного порошка, которая наносится между обрабатываемым изделием и шлифовальным инструментом или при помощи круга из связанного абразива, на который поступает вода.
Интенсивность процесса шлифовки характеризуется количеством стекла, удаленного с единицы поверхности изделия. Качество поверхности определяется как степенью шероховатости, так и равномерностью снятия слоя. Скорость съема стекла определяет продолжительность процесса шлифовки, а от качества отшлифованной поверхности зависит продолжительность полировки. Интенсивность процесса и качество поверхности после шлифовки зависит от выбора абразивного материала и технологических условий.
Абразивные вещества могут быть свободными и связанными.
Свободными абразивами называют шлифовочные порошки. В качестве абразивного порошка применяют природные или синтетические материалы.
Из природных материалов для шлифовки стекла применяют алмаз, корунд, наждак, гранат и кварцевый песок. Из синтетических абразивов – электрокорунд, карбид кремния и карбид бора. Основные физико-механические свойства некоторых абразивных материалов приведены в табл. 5.1.
|
|
Таблица 5.1
Физико-механические свойства абразивных материалов
Материал | Плотность, кг/м3 | Микротвердость, МПа | Твердость по шкале Мооса | Относительная абразивная производительность |
Песок Гранат Корунд Электрокорунд Карбид кремния Алмаз | 2 600 4 050 3 700 3 900 3 200 3 500 | 11 000 14 500 22 100 20 000 33 100 100 000 | 7 7…7,5 9 9 9,2 10 | 1 2…2,5 5,5 5…6 8,7 30 |
Дисперсность является наиболее важной характеристикой свободного абразива, от которой зависит как интенсивность шлифования стекла, так и шероховатость поверхности.
При шлифовке стекла связанным абразивом применяют диски из природного песчаника и некоторые виды синтетических абразивных кругов.
Интенсивность процесса шлифовки стекла зависит от качества стекла, природы и крупности применяемых абразивных материалов, количества и плотности суспензии абразивного материала, подаваемого под шлифовальник, удельного давления шлифовальника на стекло, скорости его вращения и др.
Количество удаляемого стекла увеличивается с повышением твердости и величины зерен абразивного материала. В то же время наличие отдельных очень крупных зерен приводит к образования царапин на поверхности стекла.
|
|
Из всего количества абразива, подаваемого под шлифовальник, лишь 15…20% производят работу по шлифовке стекла, а остальной абразив сбрасывается с его поверхности при вращении шлифовальника.
Производительность процесса шлифовки увеличивается при повышении давления шлифовальника на зерна абразивного материала и частоты вращения шлифовальника. Однако необходимо контролировать величину сбрасываемого абразива, чтобы избежать его перерасхода.
Скорость процесса шлифовки существенно зависит от химического состава стекла, определяющего такие его свойства, как твердость и химическую устойчивость. В табл. 5.2 приведены данные о скорости шлифовки стекол различных составов.
Таблица 5.2
Дата добавления: 2018-08-06; просмотров: 484; Мы поможем в написании вашей работы! |
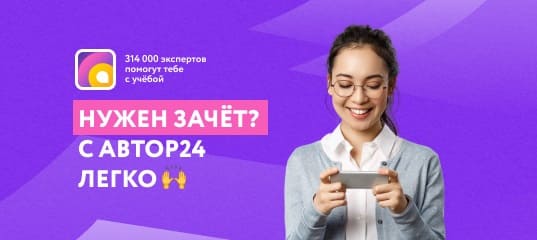
Мы поможем в написании ваших работ!