Характеристика способов формования обычного
Натрийкальцийсиликатного стекла
Способ формования | Рабочий интервал вязкости, Па.с | Интервал температу формования, °С | Градиент температуры между стекломассой и формующим устройством | Состояние поверхности |
Вытягивание Флоат Прокат Прессование Выдувание Моллирование Вспенивание | 103…107 103…1010 102…106 103…4.107 5.102.. 5.106 5.106.. 4.107 106…107 | 1050…700 1050…600 1150…800 1050…650 1100…750 750…650 800…700 | Незначительный >> ~800 ~600 ~500 Незначительный >> | Гладкая, огненно- полированная >> Неровная, кованая, бугристая с мелкой посечкой Кованость, мелкая посечка, швы от форм, тупые углы и грани Гладкая, огненно- полированная >> Неровная, губчатая |
Способы формования
Формование листовых стекол
Вытягивание листового стекла.
Если в текучую стекломассу погрузить конец плоского металлического листа, а затем поднимать этот лист, то стекломасса прилипнет к нему и будет вытягиваться вверх в виде плоской ленты. Однако под влиянием сил поверхностного натяжения лента стекла при вытягивании постепенно суживается по ширине и толщине, пока не превратится в нить круглого сечения. Для получения листов стекла нужно предотвратить сужение, а для этого следует оттягивать края (борты) ленты. Ленту стекла при вертикальном вытягивании формуют двумя способами: лодочным и безлодочным.
|
|
Лодочный способ. Для формования ленты стекла по этому способу используется лодочка – длинный прямоугольный керамический брус со сквозным продольным вырезом, переходящим в верхней части в узкую щель. Схема вытягивания стекла при помощи лодочки показана на рис. 3.2, а. В рабочем положении лодочка 2 погружена в бассейн со стекломассой 1, охлажденной до температуры выработки. Лодочка погружена так, что верхняя кромка щели, называемая губами лодочки, находится ниже уровня стекломассы в бассейне и на 40–50 мм ниже верхней плоскости лодочки, чтобы предотвратить затекание стекломассы через верх при погружении лодочки. В нерабочем положении лодочка свободно плавает на поверхности расплава, причем губы ее несколько возвышаются над этой поверхностью.
Рис. 3.2. Схема формования ленты стекла
способом лодочного вертикального вытягивания:
а – схема образования ленты стекла; б – схема подмашинной камеры; 1 – стекломасса;
2 – лодочка; 3 – холодильники; 4 – валики машины ВВС; 5 – бортодержатель; 6 – мост
При нажиме на лодочку сверху она погружается в стекломассу; при этом расплав выступает из щели под влиянием гидростатического напора, сцепляется с опущенной в нее металлической гребенкой – «приманкой» и оттягивается кверху с помощью валиков 4 машины вертикального вытягивания (ВВС), образуя непрерывную ленту стекла. Чтобы лента стекла не сужалась по ширине, ее края (борты) захватывают специальными приспособлениями – металлическими бортодержателями 5, а полотно ленты охлаждают с помощью холодильников 3.
|
|
Поднимаясь, стекло заходит в промежуток между парными асбестированными валиками машины ВВС, которые, сближаясь, соприкасаются с поверхностью ленты. Валики заключены в чугунную шахту. В этой шахте отформованная лента поднимаясь, охлаждается по заданному режиму – сначала медленно, затем быстрее. По выходе ленты из машины ее разрезают на листы, которые поступают на раскрой, сортировку и упаковку.
Безлодочное вытягивание. По такому способу лента стекла формуется со свободной поверхности стекломассы (рис. 3.3). Необходимые для формования ленты вязкости получают путём охлаждения определенного участка зеркала стекломассы 1 между подвесными огнеупорными элементами 2 (блоками). В стекломассу на глубину 70–120 мм погружают огнеупорное тело 6, направленное вдоль оси машины. Его назначение – быть экраном для излучения глубинного расплава и тем самым усиливать охлаждение потоков стекломассы, движущихся с обеих сторон к луковице над его поверхностью. Кроме того, луковица становится более устойчивой благодаря смачиванию стекломассой твердой поверхности.
|
|
Рис. 3.3. Схема формования ленты стекла
способом безлодочного вертикального вытягивания:
1 – стекломасса; 2 – L-блок; 3 – холодильник; 4 – валики машины БВВС;
5 – луковица; 5 – центральное погруженное тело
Оттягивают ленту кверху, как и при лодочном способе, при помощи асбестированных валиков машины БВВС (безлодочного вертикального вытягивания стекла). Поверхность стекломассы и ленты стекла в подмашинной камере при безлодочном способе вытягивания подвергают более интенсивному охлаждению, чем при лодочном. Благодаря высокоразвитой поверхности охлаждения по этому способу можно формовать ленту при более высоких температурах стекломассы по сравнению с лодочным способом. Края ленты удерживают бортоформующими приспособлениями с механическим приводом.
Прокат. Листовое стекло можно прокатывать на неподвижной плоскости при помощи катящегося вала (первый способ) или между двух валков, вращающихся навстречу друг другу (второй способ). Первый (самый старый) из этих способов – периодический; второй – непрерывный.
|
|
При периодическом прокате порцию стекла выливают на охлаждаемый металлический стол и прокатывают валом, катящимся по столу и разравнивающим стекло.
При непрерывном способе стекломасса поступает в промежуток между двумя цилиндрическими металлическими валками, вращающимися навстречу друг другу. Прокатываемой ленте стекла сообщается поступательное движение. Толщину стекла регулируют расстоянием между валками, а скорость проката – изменением скорости вращения валков. Во избежание прилипания ленты стекла к поверхности валков их охлаждают изнутри водой; охлаждение не должно быть слишком сильным, чтобы на ленте не образовались поверхностные трещины (посечки).
Слой стекломассы толщиной 75–80 мм поступает из выработочной части печи к прокатным валам машины по сливному брусу 9 по сливной линейке 8, расположенной между сливным брусом и нижним прокатным валом и закрепляемой на станине машины. Высоту слоя стекломассы, поступающей к машине, регулируют подъемным шибером. Лента стекла при выходе из прокатных валов поступает сначала на приемную чугунную плиту, охлаждаемую водой, затем на приемный наклонный роликовый конвейер из асбестовых валов и далее для отжига в электрический лер. Полые прокатные валы машины изготовляют из легированной стали. Внутри они охлаждаются водой, которая подается через трубу.
Для нормального процесса прокатки необходимо некоторое натяжение ленты, которое создается за счет небольшого превышения (5–10%) скорости вращения валиков лера по сравнению со скоростью прокатных валков.
При повышении температуры стекломассы и температуры поверхности прокатных валов поверхность ленты стекла становится более гладкой, но уровень этих температур лимитируется прилипанием ленты стекла к валам и затеканием стекломассы в промежутки между сливной линейкой и валами.
Способом непрерывного проката изготовляют гладкое и узорчатое стекло, а также стекло, армированное металлической сеткой. В толще армированного стекла параллельно его поверхности находится металлическая сетка, что делает его безопасным, так как при разбивании осколки стекла удерживаются на сетке и стекло, даже при большом количестве трещин, сохраняет свою форму и не выпадет из рамы. Это свойство армированного стекла позволяет применять его для устройства фонарей промышленных зданий и остекления помещений с повышенными требованиями к безопасности и огнестойкости остекления.
Армированное стекло изготавливается толщиной 5,5 мм с допуском ±0,7 мм. Проволочная сетка с толщиной проволок 0,35–0,45 мм должна располагаться на расстоянии не менее 1,5 мм от поверхности стекла и не более 20 мм от края. Существуют два способа подачи металлической сетки в стекломассу. По одному из них металлическая сетка подается сверху (рис. 3.4), по другому – снизу (рис. 3.5).
Рис. 3.4. Схема формования армированного стекла при подаче сетки сверху:
1 – стекломасса; 2 – металлическая сетка; 3 – валик для направления сетки;
4 – прокатные валки; 5 – лента стекла; 6 укатывающий валик;
7 – печь для отжига стекла; 8 – сливная линейка; 9 – порог
Рис. 3.5. Схема формования армированного стекла при подаче сетки снизу
1 – печь отжига; 2 – лента стекла; 3 – валки конвейера; 4, 19 – прокатные валы;
5 – опорная труба; 6 – шамотный шибер; 7 – обогреваемая стенка из жароупорной стали;
8 – шамотная стенка; 9, 10 – шиберы; 11– стекломасса; 12 – сливной порог; 13 – сливная линейка; 14–16 – направляющие валики; 17 – выравнивающие вальцы; 18 – рулон сетки
При верхней подаче сетки она перед прокаткой листа подвергается продолжительному воздействию горячей стекломассы, что вызывает появление пузырей на границе «металл–стекломасса». При нижней подаче сетка защищена от излучения стекломассы огнеупорным дном устройства и соприкасается с горячей расплавленной стекломассой перед прокаткой значительно меньше времени, чем при первом способе. Скорость прокатки 150–250 м/ч. После прокатки армированное стекло отжигается в лере, длина которого зависит от скорости проката. Общее время отжига и охлаждения не превышает 30–40 мин.
Армированное стекло также изготовляют с узорчатой поверхностью и цветное. За рубежом наряду с обычным изготовляется полированное армированное стекло.
Прокатывая стекло и загибая его края в форме швеллера или коробки, получают профильное стекло. Этот метод используют и для производства коврово-мозаичных плиток.
Растекание (флоат-способ). В настоящее время производство полированного листового стекла путем его механической обработки (шлифования и полирования) на конвейерных линиях заменен новым способом – непрерывной огневой полировкой пластичной ленты стекла на расплаве металла, так называемым флоат-способом. Механической обработкой на периодически действующих станках продолжают пользоваться в производстве изделий технического назначения.
Патент на флоат-способ принадлежит Хилу и Хичкоку (США, 1902 г.). В практику он был внедрен в 1959 г. в патентном варианте фирмы «Пилкингтон» (Англия) и в течение короткого времени получил широкое распространение во всех технически развитых странах мира.
Производительность одной установки составляет оптимально порядка 42 млн. м2 стекла в год в условном 2-мм исчислении. Этой производительности отвечает средний суточный съем стекломассы с ванной печи более 600 т и удельный съем до 2500 кг/сутки с 1 м2 отапливаемой площади при коэффициенте использования стекломассы 0,9. Толщина вырабатываемого стекла 2,5–19 мм.
Схема формования ленты стекла флоат-способом показана на рис. 3.6. Флоат-ванна имеет длину от 45 м; ее ширина для наиболее распространенной ширины ленты 3,05–4,06 м (с бортами) в начале составляет 7 м, а в остальной части 4–4,5 м. Ванна футерована огнеупорным материалом, стойким к воздействию расплавленного олова, и заключена в металлический кожух. Глубина слоя олова в ванне 40–100 мм, масса олова, содержащегося в ванне, около 120 т. Боковые стены и свод ванны также выполнены из специально предназначенных для них огнеупоров. Ванна по длине разделена перегородками 2, 3 на три части, в каждой из которых поддерживают свой тепловой и газовый режим. По трубам 4 под свод ванны непрерывно подают смесь азота и водорода для защиты олова от окисления и для предотвращения образования пленки оксида олова на нижней поверхности ленты стекла.
![]() |
Рис. 3.6. Флоат-ванна для производства стекла толщиной до 6,5 мм
(продольный разрез и план)
Защитная атмосфера создает в полости ванны небольшое (30–50 Па) избыточное давление и удаляется в конце ванны. Смесь, подаваемая в горячую часть ванны, содержит водорода до 8 % по объему, а поступающая в концевые части – до 15% водорода. В смеси должно содержаться по объему не более 0,0001 % кислорода, не более 0,0001 % соединений серы или углерода, не более 0,001 г/м3 механических примесей или паров воды при точке росы 60°С. Азот и водород готовят на отдельных установках, размещаемых на заводе, и смешивают на специальной станции. Расход смеси – до 1250 м3/ч.
Под сводом ванны и внутри олова установлены электрические нагреватели 5, 6, 7 (см. рис. 3.6), с помощью которых поддерживают необходимые температуры стекломассы по длине и ширине ванны. Дно металлического кожуха ванны охлаждают воздухом. По бокам флоат-ванны устроены смотровые окна, которые используют также для выполнения операций по передвижению ленты во время пуска установки. После флоат-ванны размещено роликовое тянульное устройство 8, которое непрерывно оттягивает ленту из ванны и передает ее в печь отжига.
Температуру стекломассы 1 в сливном канале перед отсекающим шибером измеряют с помощью термопары, погруженной в стекломассу на 20–25 мм, ее поддерживают около 1080°С и регулируют с точностью ±1°С при помощи автоматической системы вдувания холодного воздуха в начале студочной части печи. На сливном лотке температура стекломассы около 1050°С. Под сливной лоток, расположенный примерно на 70 мм выше поверхности олова в ванне, затекает стекломасса, образуя своеобразную лужу 9 (как бы горизонтальную луковицу), из которой формуется лента стекла. Эта лужа нужна для того, чтобы полотно ленты формовалось только из верхних слоев расплава, не контактировавших с материалом лотка; нижние же слои, контактировавшие с лотком, поступают на образование бортов.
Стекломасса перестает растекаться на расстоянии от лотка порядка 4,5 м; здесь лента достигает равновесной толщины при температуре 1025°С равно приблизительно 6,5 мм. Для получения ленты толщиной меньше равновесной ее принудительно растягивают Чтобы полотно ленты не сузилось чрезмерно при оттягивании, ленту растягивают в ширину роликами 10–15, установленными сверху под углом около 10° к оси ленты и придерживающими борта. В зоне роликов температура ленты 950–900°С. После охлаждения до температуры порядка 600 °С лента выходит из флоат-ванны и передается на роликовый конвейер печи отжига.
составляет 5–10 т/сут.
Формование стеклоизделий
Ручное выдувание. Основной принцип ручного выдувания состоит в том, что стеклодув с помощью стеклодувной трубки набирает расплавленную стекломассу на конец трубки, подготавливает пульку и выдувает массу в форму. В настоящее время при ручном выдувании изделий повсеместно используют трубку-самодувку (рис. 3.9). Основное ее отличие от ранее применяемых трубок состоит в том, что выдувание осуществляют с помощью резинового баллона путем его нажатия и возврата в прежнее положение. Формы для выдувания делают преимущественно из металла, однако в ряде случаев их делают из дерева, огнеупорного материала и др.
Прессование. Стекло прессуют при помощи формы, определяющей внешнюю конфигурацию изделия, и пуансона, создающего давление на стекло и оформляющего изделие изнутри. При прессовании поверх формы накладывают кольцо, которое задерживает стекломассу в форме и оформляет край изделия. Схема прессования изделий в форме показана на рис. 3.10.
Этот способ прост и производителен, но изделия получаются с кованой и матовой поверхностью. Прессованием вырабатывают главным образом изделия бытового назначения (стаканы, пивные кружки, салатницы и т. п.) или изделия для строительства (стеклоблоки, архитектурные детали). Изделия сложной формы прессуют в раскрывных формах.
На ручных прессах давление создают при помощи рычага, перемещающего керн, в полуавтоматических и автоматических прессах используют сжатый воздух. Самые крупные и тяжелые прессы – гидравлические. К концу прессования давление повышают в связи с увеличением вязкости стекла. Толщина стенок изделий зависит от величины зазора между керном и формой, а распределение стекла в форме – от температуры стекломассы, давления при прессовании и равномерности отбора теплоты отдельными частями формы.
Рис 3.10. Схема прессования изделия в форме
1 – капля стекломассы; 2 – пресс-форма; 3 – ограничительное кольцо;
4 – керн; 5 – изделие; 6 – поддон
Механизированные способы изготовления изделий из стекла. Созданные в последнее время поточно-механизированные линии производства изделий из стекла отличаются высокой производительностью. Для формования изделий используют автоматические стеклоформующие машины, по способу формования подразделяющиеся на прессовые, прессовыдувные и выдувные.
В качестве прессовых машин наибольшее распространение получил отечественный автоматический 12-ти позиционный пресс АПП-12. Этот автомат предназначен для изготовления различных изделий из бесцветного и цветного стекла (стаканов, мелких вазочек, пепельниц, салатников и др.). Рабочие органы машины приводятся в движение при помощи сжатого воздуха. Наряду с этой машиной используются пресс-автоматы «Линч», а также роторный автомат АРП-10.
Из прессовыдувных машин наибольшее распространение получил автомат «Гортфорд-28», отличающийся высокой производительностью. Он используется главным образом для изготовления стаканов. Автомат имеет 12 рабочих секций, в состав которых входят все необходимые механизмы для прессовыдувания изделий.
В качестве выдувных машин на отечественных стекольных заводах все еще широко применяется карусельный автомат ВС-24. Он состоит из шести секций, в каждой из которых имеются четыре выдувные трубки и четыре чистовые формы. Принцип питания машины – вакуумный. Автомат ВС-24 служит для изготовления тонкостенных стаканов различного назначения, блюдец для чая и варенья.
В производстве сортовой посуды используют также выдувные машины с капельным питанием. В качестве таковой, прежде всего, следует назвать автомат ВР-24, на котором изготовляют колбы для термосов, стаканы, сосуды для изделий на ножке.
Наряду со стеклоформующими автоматами технологические линии по производству сортовой посуды включают механические конвейеры для транспортировки изделий, отжигательные печи, оборудование для отрезки колпачка, обработки края и шлифовки дна изделия.
Формование стекловолокна
Штапельное волокно. Для производства теплоизоляционных изделий, используемых в массовом строительстве, применяют утолщенное волокно диаметром 10–13 мкм, вырабатываемое способом вертикального раздува паром (ВРП). Применявшийся ранее способ горизонтального раздува паром (ГРП) не используется, так как он давал более грубое волокно (15–20 мкм) с большим количеством корольков. Центробежно-фильерно-дутьевой (ЦФД) и другие способы выработки ультратонкого, супертонкого и тонкого волокон предназначаются для производства теплоизоляционных изделий специального назначения.
Схема установки для производства штапельного волокна способом ВРП с последующим изготовлением полужестких теплоизоляционных плит показана на рис. 3.11. Шихта из бункеров 1 конвейером 2 подается к загрузчику 3 и далее в стекловаренную печь 4. Хорошо проваренная стекломасса из печи поступает в питатели 5, откуда она вытекает в виде нескольких струй диаметром 2–7 мм. Пар или сжатый воздух под давлением 6–10 МПа при помощи дутьевого устройства 6 воздействует на вытекающие струи стекла, расчленяет их и увлекает образующиеся волокна в вертикальную камеру волокнообразования 7. В этой камере установлен сетчатый конвейер, на который волокна оседают равномерным слоем. Меняя скорость движения конвейера, можно регулировать толщину слоя стекловолокна. Под конвейером установлен вентилятор, создающий разрежение, которое способствует притягиванию волокон к его сетке. В камере волокнообразования при помощи распылителя 8 разбрызгивается синтетическая смола, например фенолформальдегидная, составляющая 3,5–10% массы волокна.
![]() |
3.11. Схема установки
для производства штапельного волокна способом ВРП
Смола покрывает волокна тончайшим слоем и они становятся эластичными и химически устойчивыми. При последующей подпрессовке верхним сетчатым конвейером и термической обработке стекловолокна в камере полимеризации 9 при температуре 130–170°С смола склеивает волокна друг с другом и делает стекловолокно полужестким. Ленту толщиной 30–50 мм, выходящую из камеры полимеризации, разрезают на плиты заданных размеров. Производительность технологической линии 50 тыс. м3 полужестких плит в год. Длина линии 50 м.
Непрерывное волокно. Вытягивание волокна из расплава может осуществляться механическими устройствами, воздухом или паром
Механическое вытягивание осуществляют с помощью барабана, съемных бобин, вытяжных валков и прядильной головки; вытягивание воздухом или паром производят с помощью дутьевой головки (рис. 3.12).
Струйный питатель – изогнутая электрообогреваемая трубка, для отбора расплава с заданного уровня и регулируемой его подачи в сосуд. Выбор диаметра струйного питателя производится при условии равенства дебитов фильерного и струйного питателей.
Диаметр непрерывного стеклянного волокна, получаемого различными способами, колеблется от 3 до 100 мкм. Для текстильной переработки применяют волокна диаметром 3…14 мкм.
Рис. 3.12. Производство непрерывных волокон:
1 – ванная печь; 2 – струйный питатель; 3 – фильерный питатель;
4 – вытяжные валки; 5 – съемная бобина
Работа 3.1.Расчет и оценка выработочных
Характеристик тарных стекол
В последнее время в связи с использованием для производства стеклянной тары высокопроизводительного стеклоформующего оборудования (секционные автоматы типа IS, AL и др.) при проектировании и оптимизации химических составов тарных стекол большое внимание уделяют оценке их выработочных характеристик.
Показателем интенсивности работы стеклоформующего оборудования является сравнительная скорость стеклоформующих машин (СССМ), рассчитываемая по формуле, %:
, (3.1)
где ТЛит – характеристическая температура Литтлтона (lgη = 6,65 Па∙c); Тg – температура стеклования (lgη = 12,3 Па∙c).
Для отечественных и зарубежных стекол этот показатель изменяется от 102 до 110, большинство современных линий работает со скоростью 107–108 %.
Температурный интервал формования (ТИФ), °С:
ТИФ = (TЛит –Tg). (3.2)
Для большинства тарных стекол этот показатель превышает 160°С.
Индекс кристаллизации (ИК), °С:
ИК = ТИФ – 160. (3.3)
Температура капли (ТК)соответствуетзначению lgη = 2 Па∙ c.
Для усредненного состава бесцветного тарного стекла, мас.%: 72,2 SiO2; 2,2 Al2O3; 0,10 Fe2O3; 10,1 CaO; 0,9 MgO; 13,9 Na2O; 0,6 K2O значения выработочных характеристик следующие: CCCМ = 107, ТИФ = 175, ИК = 15, ТК = 1184.
В табл. 3.2 представлены химические составы отечественных и зарубежных тарных стекол, выработочные характеристики которых следует определить и оценить с точки зрения возможности использования высокопроизводительного стеклоформующего оборудования, опасности кристаллизации при формовании, эффективности процесса варки стекла и формования стеклоизделий. Составы стекол для расчета можно также подбирать по справочным данным, периодической литературе, проектировать самостоятельно.
Таблица 3.2
Дата добавления: 2018-08-06; просмотров: 1622; Мы поможем в написании вашей работы! |
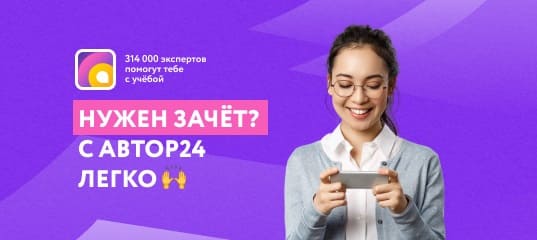
Мы поможем в написании ваших работ!