Интенсификация процесса стекловарения
Высокую единичную производительность любых установок, в том числе стекловаренных печей, экономически наиболее выгодно получать путем интенсификации технологического процесса и увеличения выхода продукции с единицы производственной площади.
Повышение эффективности стекловарения связано, прежде всего, с его интенсификацией. Способы интенсификации можно подразделить на три группы:
− термические;
− физико-химические;
− гидродинамические.
Основная роль в интенсификации стекловарения принадлежит термическим способам.
Главный метод интенсификации варки стекла — увеличение количества теплоты, передаваемой шихте и стекломассе в зоне варки. В пламенных печах, где сверху в шихту и стекломассу поступает 60–70 % всего воспринимаемого ими количества теплоты, это достигается увеличением теплового напряжения1 с соответствующим повышением температуры печи. Очень большое значение имеет организация факелов, которые должны покрывать 80 % площади отапливаемой части печей и максимально приближаться к поверхности шихты и стекломассы в зоне варки. Для этого увеличивают ширину влетов горелок ванных печей и уменьшают ширину простенков между ними; придают определенный наклон поду и понурому своду горелок; практикуют подачу газа в горелки через несколько сопел, подведенных снизу или установленных в стенах горелок.
Во избежание уноса шихты пламенными газами при приближении факелов к ее поверхности увеличивают размеры загрузочных карманов в продольном направлении и располагают над ними ряд выносных загрузочных арок, чтобы создать как бы форкамеры, обогреваемые излучением и газами печи, где шихта успевает нагреваться и превратиться в спек до момента поступления в печь.
|
|
Увеличивают теплоотдачу от факела пламени, прежде всего, путем повышения его температуры. Для этого улучшают смешивание газа и воздуха путем вдувания воздуха под давлением в сопла газовых горелок. Кроме того, для повышения температуры пламени воздух для горения нагревают до максимально высокой температуры; в последние годы для этих целей добавляют к воздуху кислород.
Теплоотдачу от факела повышают также увеличивая его излучательную способность (светимость). Факел горения природного газа несветящийся – прозрачный. Светимость факела повышают путем поддержания в горелках зоны варки коэффициента избытка воздуха не более 1,06–1,08 (для сохранения в нем светящихся частиц сажистого углерода).
С повышением средней температуры в зоне варки на 10° удельный съем стекломассы с отапливаемой части печи возрастает на 4—5 %. Несмотря на то что для повышения температуры в печи приходится увеличивать общий расход топлива, удельный его расход снижается, так как с данной площади печи снимают больше стекломассы.
|
|
Мощное средство интенсификации процесса стекловарения –электрический подогрев стекломассы в зоне варки. Электроподогрев позволяет наряду с увеличением количества теплоты, переносимого сыпочным потоком в зону провара шихты, повысить температуру стекломассы в квельпункте и усилить сыпочный цикл потоков, облегчить осветление расплава и снизить общий расход теплоты в печи. Он особенно эффективен при варке стекол с низкой лучепрозрачностью, в этом случае его применение позволяет увеличить съем стекломассы на 50– 60 %.
В последние годы в связи с появлением высокоустойчивых огнеупорных материалов для кладки бассейнов ванных печей температуру стекломассы в них повышают также путем тепловой изоляции дна и стен бассейна ниже уровня стекломассы.
Увеличить количество теплоты, поступающей в стекломассу в зоне варки, можно также с помощью ее бурления воздухом в местах расположения куч шихты: поднимающиеся пузыри раздвигают шихту и пену и открывают поверхность расплава, увеличивая проникновение теплоты в стекломассу. Подъем пузырей активизирует обмен стекломассы под шихтой. Благодаря этому ускоряются провар зерен песка и гомогенизация расплава.
|
|
В проточных печах для получения тарного, строительного и технического стекла бурление используют и для облегчения гомогенизации стекломассы; в этих целях расплав бурлят в зоне квельпункта. Воздух подводят с помощью корундовых сопел в жароупорных чехлах, установленных в дне печей; его расход составляет порядка 0,1 м3/ч. Воздух очищают от влаги, масла и пыли и подают импульсно с частотой 12–20 пузырей/мин. Оптимальный диаметр пузырей 120–200 мм.
Физико-химические способы интенсификации можно разделить по стадиям технологического процесса приготовления шихты и варки стекла.
На стадии приготовления шихты интенсификация стекловарения может быть осуществлена путем замены одного из компонентов шихты более активным, уплотнения шихты (брикетирования, гранулирования), использования специальных, например, гидротермальных способов приготовления шихты.
Замена части карбоната натрия раствором NaOH ускоряет процесс варки стекла благодаря тому, что водный раствор NaOH обволакивает зерна песка, и силикатообразование начинается при более низких температурах, чем при использовании одного карбоната натрия.
|
|
Интенсифицирующий эффект при использовании уплотненной шихты обусловлен:
− увеличением поверхности соприкосновения между частицами сырьевых материалов;
− повышенной теплопроводностью шихты по сравнению с сыпучей, что способствует лучшему проникновению тепла в ее массу;
− возможностью использования очень мелких фракций песка.
Одним из способов интенсификации стекловарения является применение гидротермальной шихты, которая обладает высокой дисперсностью, химической однородностью и чистотой. Плотность гидротермальной шихты в зависимости от химического состава составляет 500–700 кг/м3. При влажности 20–25% и давлении 5–10 МПа без применения специального связующего можно получить шихту плотностью 1500–1700 кг/м3 в виде брикетов.
Механизм образования стекломассы из гидротермальных шихт отличается от механизма варки обычных стекольных шихт. В первом случае стадия силикатообразования в основном завершается в процессе получения шихты, а растворение кварца в расплаве протекает иначе, чем при варке обычной шихты. Остаточный кремнезем в гидротермальных шихтах находится в тонкодисперсном состоянии и равномерно распределен в массе силикатных компонентов шихты. Повышенная реакционная способность гидротермальных шихт обусловлена тем, что их основными составляющими являются аморфные гидросиликаты щелочных и щелочноземельных металлов в смеси с аморфным кремнеземом. Ускорению процесса стеклообразования способствует однородность гидротермальных шихт, а также присутствие в гидросиликатах связанных молекул воды, удаляющихся только в процессе варки.
Интенсификация стекловарения может быть достигнута также при введении в состав шихты химических ускорителей.
Гидродинамические способы интенсификации заключаются в применении перемешивания и бурления для ускорения взаимодействия компонентов расплавов и гомогенизации стекломассы.
В стекловаренных ванных печах с высокими удельными съемами стекломассы производственный (рабочий) поток подавляет конвективную циркуляцию, вследствие этого в них необходимо гомогенизировать стекломассу принудительно. В больших ванных печах листового стекла в последнее время для принудительной гомогенизации используют перемешивание стекломассы в выработочных отделениях печей с помощью механических мешалок. Последние имеют в большинстве случаев форму вертикального пропеллера с лопастями, погруженными в стекломассу. Мешалки делают из термостойких и стеклоустойчивых огнеупоров и вводят в полость печей с помощью водоохлаждаемых штырей, проходящих через свод и приводимых во вращение механизмом, позволяющим изменять направление вращения и число оборотов. Мешалки устанавливают в ряд по ширине рабочего потока на глубину до 200–250 мм ниже поверхности расплава и сообщают им вращение со скоростью 9–16 мин–1. Перемешивание устраняет химическую и температурную неоднородность стекломассы
Формование
Основы процесса
Превращение стекломассы в стеклянные изделия – формование или выработка – может осуществляться разнообразными способами. Из стекла можно изготовлять мельчайшие изделия (бисер, миниатюрные электронные лампочки, тончайшее стекловолокно диаметром в доли микрона) и изделия больших размеров и массы (витринные стекла площадью 15–20 м2, диски для телескопов диаметром несколько метров, высокие стеклянные колонны и т. д.).
Возможность формования стекломассы в пластичном состоянии связана, прежде всего, с особенностями изменения ее вязкости в зависимости от температуры. Как мы уже знаем, готовая текучая стекломасса по мере охлаждения становится пластичной. Пластичность расплава позволяет ему принять заданную форму; затем полученное изделие охлаждают, и приданная ему форма фиксируется в процессе затвердевания изделия.
Интервал температур, при которых стекло отформовывают, называют интервалом формования или выработки. В этом интервале вязкость стекла изменяется от 102 до 107 Па∙с, изделие полностью отвердевает при вязкости, равной 1012 Па-с.
Температуры и вязкости, соответствующие выработке, зависят от состава стекла и способа формования. Так, например, вязкость при вытягивании листового стекла составляет 103,5 Па∙с, вязкость при выдувании тарных изделий – 102,2 Па∙с, при прессовании — 102,7 Па∙с. Скорость изменения вязкости стекломассы во времени (скорость затвердевания), зависящая от состава и цвета стекла, определяет необходимое время формования и производительность выработки изделий.
Во всех случаях скорость и продолжительность этого процесса обусловлены двумя его стадиями.
Формообразование– придание пластической стекломассе требуемой конфигурации формуемого изделия в результате приложения внешних сил, характер действия которых обусловлен видом изделия и применяемым способом его формования.
Фиксация формы– закрепление конфигурации отформованного стеклоизделия в результате его твердения, характер которого обусловлен видом стекла, изделия и применяемым способом охлаждения.
Процесс формования любого стеклоизделия начинается со стадии его формообразования и завершается стадией фиксации формы изделия, которая продолжается по существу в течение всего хода процесса формования. Поэтому в общем виде процесс формования характеризуется следующими условиями:
V1 ≥ V2 и t1 ≤ t2 ,
где V1, V2, t1 и t2 –скорость и время первой и второй стадии процесса формования соответственно.
Практически формообразование изделия осуществляется значительно быстрее, чем фиксация его формы. Поэтому часть времени (t2 – t1)затрачивается только на охлаждение и твердение изделия и является непроизводительной. На практике стремятся к максимально возможному увеличению скорости фиксации формы и сокращению за счет этого продолжительности всего процесса формования.
Для определения и регулирования в нужном направлении продолжительности всего процесса формования и отдельных его стадий необходимо, прежде всего, знать характер температурного изменения вязкости, а также скорость охлаждения и твердения стекломассы (формуемого изделия) и возможные технологические способы изменения этих параметров.
Скорость твердения стекломассы характеризуется скоростью нарастания вязкости при её охлаждении, а, следовательно, зависит, прежде всего, от хода кривой lgη = f(t), то есть от температурного градиента вязкости (Δη/Δt).
Из рис. 3.1 следует, что «длинные» стекла характеризуются более пологим ходом кривой вязкости, а следовательно, меньшим температурным градиентом вязкости (Δη/Δt1) , и обладают меньшей скоростью твердения, тогда как «короткие» стекла с более крутым ходом кривой вязкости и большим температурным градиентом вязкости (Δη/Δt2) твердеют значительно быстрее.
Однако температурный градиент вязкости не учитывает фактор времени. Количественно скорость твердения стекломассы выражается интенсивностью нарастания вязкости со временем при охлаждении стекла, то есть временным градиентом вязкости (Δη/Δτ), значения которого определяются ходом кривой твердения стекломассы lgη = f(τ).
Таким образом, скорость твердения стекломассы в процессе формования стеклоизделия обусловлена температурным и временным градиентами вязкости.
Наибольшее влияние на скорость охлаждения стекломассы в процессе её формования оказывают: масса и поверхность формуемого изделия, удельная теплоемкость стекла, начальная и конечная температуры стекломассы (стеклоизделия), интенсивность лучеиспускания поверхности стекломассы, теплопрозрачность стекломассы, температура внешней (контактной) охлаждающей среды (форм, пуансонов, прокатных валков и др.), с которыми стекломасса соприкасается в процессе формования.
В отличие от бесцветных окрашенные стекла обладают пониженной теплопрозрачностью. Для таких стекол наблюдается замедленное охлаждение и твердение внутренних слоев при одновременном очень быстром охлаждении и твердении наружного поверхностного слоя. По силе влияния на уменьшение теплопрозрачности окрашивающие оксиды располагаются в следующий ряд: СoO > CuO > FeO > Mn2O3 > Cr2O3.
Важную роль в процессе формования стекломассы играет также ее поверхностное натяжение. Оно может действовать положительно или отрицательно в зависимости от способа формования. Благодаря этому свойству удается выдуть без формы тонкостенный круглый пузырь – заготовку будущего изделия, ограничить растекание стекломассы по поверхности какого-либо материала, получить гладкую поверхность стекла при его огневой полировке. Однако при вытягивании или прессовании стекла поверхностное натяжение вызывает деформацию изделий – сужение вытягиваемых листов, закругление углов и ребер изделий.
Важнейшие способы формования стеклянных изделий — вытягивание, прокатка, растекание, литье, выдувание, прессование и центробежное формование (табл. 3.1).
Тепловой режим процесса формования должен быть таким, чтобы изделие до момента затвердевания успело приобрести окончательную форму и размеры. При выработке изделий необходимо, чтобы формующие приспособления оставляли как можно меньше отпечатков и следов на поверхности изделий, а для этого стекло при выработке не должно ни прилипать к формующей поверхности, ни переохлаждаться ею.
В температурной области формования обычно наиболее сильно проявляется склонность стекол к кристаллизации. Поэтому необходимо достигнуть максимально допустимой при формовании скорости охлаждения и твердения стекломассы и ориентироваться на применение более «коротких» стекол. Практически осуществить режим формования более «длинных» стекол значительно проще, чем «коротких», однако при этом замедляется скорость формования и снижается производительность стеклоформующих машин.
Таблица 3.1
Дата добавления: 2018-08-06; просмотров: 979; Мы поможем в написании вашей работы! |
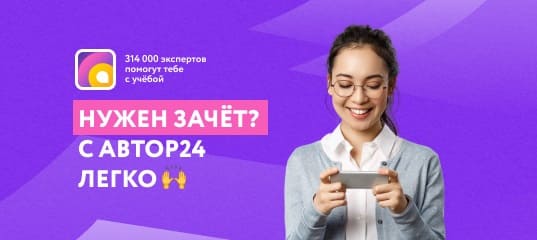
Мы поможем в написании ваших работ!